Идродинамика, воздушная система, схема распределения воздуха, воздух на горение, содорегенерационный котел, степень восстановления, развитая система управления
Вид материала | Доклад |
Содержание3. Обстоятельства модернизации срк 4.2. Моделирование CFD 4.3. Результаты моделирования 4.4. Выбор решения 4.5.2. Опыт по эксплуатации |
- Курсовая работа по дисциплине: Экономическая теория по теме: "Кредит и кредитная система", 552.22kb.
- Темы рефератов икурсовых работ общие. Система государственного управления: основные, 90.41kb.
- Методические указания му 1 09 Издание официальное Москва, 2009 Федеральная служба, 178.43kb.
- Лекция № Система распределения, 61.69kb.
- Лекция 2 Экономическая система, как объект кибернетики, 70.17kb.
- Управления и сигнализации по gsm каналу далее, 23.15kb.
- 1. Общие положения, 29.3kb.
- Лекция Рациональное использование и охрана воздушного бассейна. Основные источники, 148.72kb.
- Школа как педагогическая система и объект научного управления, 71.64kb.
- Конспект урока по естествознанию в 5 классе Тема: «Воздух», 109.22kb.
| Международный научно-практический семинар «Энерготехнологические котлы и выпарные станции ЦБП» |
Матти Салмела
Metso Power Oy, Финляндия
Модернизация СРК
1. ВВЕДЕНИЕ
Доклад рассматривает в свете примера подготовку к модернизации СРК с помощью компьютерного моделирования, а также ее успешность
2. КЛЮЧЕВЫЕ СЛОВА
CFD = computational fluid dynamics (компьютерная гидродинамика), воздушная система, схема распределения воздуха, воздух на горение, содорегенерационный котел, степень восстановления, развитая система управления.
3. ОБСТОЯТЕЛЬСТВА МОДЕРНИЗАЦИИ СРК
Обычно СРК становится рано или поздно узким местом производства на целлюлозном заводе. СРК является дорогой установкой для приобретения и содержания. На целлюлозном заводе с одной производственной линией невозможно трогать элементы СРК, работающие под давлением, без останова производства завода. Также на заводе с двумя или несколькими производственными линиями простой СРК вызывает значительные потери производства.
Большие расходы по простою СРК и обеспечение выгоды, извлекаемой из модернизации, заставили использовать все расчетные методы, с помощью которых можно гарантировать экономичность модернизации. Компания Metso Power (бывшая Tampella/Kvaerner) уже почти 20 лет применяет цифровую гидродинамику (CFD, компьютерная гидродинамика) для проектирования новых содорегенерационных и энергетических котлов, а также модернизации котлов.
При модернизации СРК не всегда речь идет только о повышении мощности. Часто повышение мощности осуществляется в связи с необходимыми работами по техобслуживанию и из-за их запускающего импульса.
На СРК высокого давления образование трещин в трубах из композитных материалов привело к использованию труб из углеродистой стали в средней части пода. В углеродистой стали не образовываются трещины, но она коррозирует. На стадии монтажа оценили безопасный срок службы в 10 лет. Первые из них были заменены после ок. 15 лет эксплуатации. В связи с модернизацией пода обычно модернизируются также воздушные системы в части первичного и вторичного воздуха.
4. ПРИМЕР
4.1. Исходное положение
При обследовании состояния СРК на заводе с одной производственной линией обнаружили, что его под из углеродистой стали требует замены. СРК был также узким местом производства завода. Новый под и повышение производительности были необходимыми.
Лица, отвечающие за эксплуатацию СРК, хотели в то же время изменить технологический процесс так, чтобы щелоковые форсунки переместили на один ярус ниже, что, со своей стороны, вызвало бы также перемещение яруса верхнего вторичного воздуха и горелок, включая горелку для сжигания крепких неконденсирующихся газов, ниже.
4.2. Моделирование CFD
Чтобы найти наиболее экономичное решение для модернизации пода и обеспечения дополнительной производительности, компанией Metso Power было выполнено моделирование СFD. Основными вариантами явились:
1. Линия обрезки пода находится выше существующего яруса вторичного воздуха. Для новых нижних частей экранов подвод вторичного воздуха предусмотрен только на фронтовом и заднем экранах вместо прежних 4-х экранов. Ярус верхнего вторичного воздуха и отметка горелок, а также отметка щелоковых форсунок остаются по-прежнему.
2. По сравнению с предыдущим вариантом линия обрезки повышается на панелях, у которых существующие сопла верхнего вторичного воздуха и пусковые горелки, включая горелку крепких неконденсирующихся газов, а также отверстия для щелоковых форсунок перемещаются ниже и ненужные отверстия заделываются.
4.3. Результаты моделирования
На рис. 1. видно моделированное положение, когда, кроме расположения и размера отверстий для подвода воздуха, горелок и щелоковых форсунок, другие параметры сохраняются постоянными. Схема распределения воздуха и параметры щелока остаются по-прежнему. Между вариантами нет значительной разницы в вертикальных скоростях, вариант 1 кажется самым хорошим.
На рис. 2. приведены профили температур с теми же самыми предпосылками в тех же самых разрезах. Опять вариант 1 является чуть более хорошим.
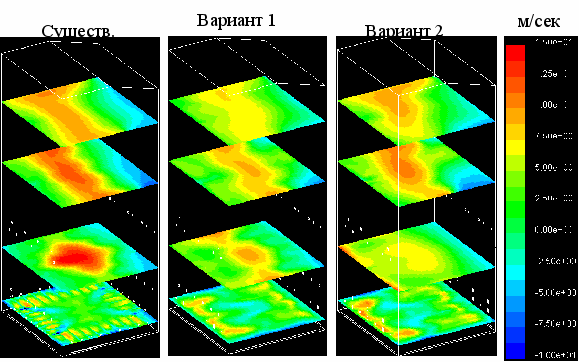
Рис. 1. Вертикальные скорости
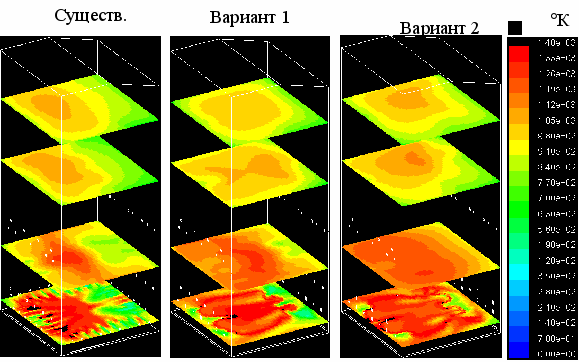
Рис. 2. Профили температур
4.4. Выбор решения
Недостатком моделирования является то, что для сравнения исходные данные могут быть изменены только в части геометрии. В действительном котле для каждой геометрии требуется также оптимизация эксплуатационных параметров. Они будут отличаться от картины моделирования. Путем изменения схемы распределения воздуха и, например, температуры впрыскивания щелока вариант 2 несомненно стал бы более конкурентоспособным. В данном случае моделирование было выполнено для существующей геометрии котла при подходящих эксплуатационных параметрах. Если бы такого не сделали, было бы трудно сравнить результаты между собой. Из-за большой длительности выполнения расчетов, требуемых для разных случаев, оптимизация эксплуатационных параметров для каждого случая стоила бы слишком много.
Несмотря на ограничения, моделирование четко показал, что дополнительные инвестиции, необходимые для варианта 2, не окупаются по сравнению с вариантом 1. Заказчик решил выбрать вариант 1.
4.5. Реализация
4.5.1. Монтаж
При проведении тендера на модернизацию котла решающую роль часто играет монтаж. Участникам тендера обычно приходится предоставлять одинаковые технологические гарантии. Решение тендера принимается на основе цены. Срок монтажа и вызываемые этим потери производства решают много. Во время останова завода были проведены и другие модернизации. Монтаж нового пода СРК отличался по своей продолжительности очень мало от монтажа следующей по продолжительности модернизации при этом останове. Сокращение срока монтажа принесло пользу также исполнителю монтажа.
Для обеспечения того, чтобы монтируемые блоки совместились друг с другом и дефектов проектирования не было, контрольная сборка пода котла была выполнена на заводе компании Metso Power в г. Лапуа, Финляндия. Части были перевезены на место монтажа возможно большими блоками. Травление пода было проведено на месте монтажа перед монтажом.
Срок монтажа был сокращен на 49 часов. Собственно говоря, это было точно 56,5 часов ниже графика, но из-за утечки сероводорода, независящей от поставщика, стройплощадку пришлось закрыть на 7,5 часов. По графику срок монтажа с начала демонтажа элементов, работающих под давлением, до гидроиспытания составил 12 дней 12 часов. Этот срок сократился, как указано выше. В этой связи на котле была модернизирована также защитная блокировочная система компанией Metso Automation. Эта работа была выполнена по графику, и сжигание топлива в котле было начато по плану.
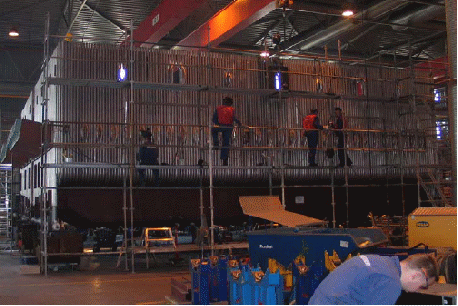
Снимок 3. Контрольная сборка пода на заводе в г. Лапуа.
4.5.2. Опыт по эксплуатации
Как опыт показывает, сравнение моделированных случаев для существующего решения при оптимизированных параметрах не дает полного представления о новых решениях. Правильным способом сравнения разных решений было бы столько далеко идущее моделирование, чтобы было возможно оптимизировать эксплуатационные параметры для каждой представленной модели. Все же, также нынешний способ обеспечивает расположение решений в порядке по превосходству.
Изменения схемы распределения воздуха были значительными по сравнению со старой схемой. В нижеследующей таблице 1 приведены схемы распределения воздуха до и после модернизации. Моделирования были выполнены на основе старой схемы распределения воздуха. Объемы верхнего и нижнего вторичных воздух были сложены. Расход верхнего вторичного воздуха является постоянной в обеих случаях. Изменения были выполнены для вторичного воздуха, схема подачи которого изменилась.
Таблица 1.
| Старая схема | Новая схема |
Первичный воздух % | 24 | 32 |
Вторичный воздух % | 47 | 50 |
Третичный воздух + слабые неконденсирующиеся газы % | 29 | 18 |
На упомянутом котле имеется система управления верхнего уровня поставки Metso Automation. Система была разработана компаниями Тampella Power и Valmet Automation в качестве новаторской работы, и она явилась первой моделью, осуществленной в центральной системе управления в Финляндии. В настоящее время сотрудничество компаний продолжается под крылом Metso.
5. ИТОГИ
Возможно экономичная эксплуатация СРК зависела от высококвалифицированных и решительных работников, инженерно-технического персонала и руководства. В настоящее время они могут применять для будущих решений результаты цифрового моделирования и для существующего положения развитые системы регулирования. Опыт и компетентность не утратили своего значения, они все еще нужны для применения результатов моделирования и усовершенствования систем регулирования. Возможности, предоставляемые информационной технологией, и, с другой стороны, ее ограничения следует понимать.
Упомянутый здесь СРК является хорошим примером новаторской работы при проектировании СРК. Благосклонность, понимание и профессиональная квалификация владельца котла обеспечили:
- первую маштабную систему суперсжигания, содержание сухого вещества более 80%;
- использование моделирования CFD на стадии приобретения нового котла и модернизации котла;
- первую систему управления верхнего уровня в центральной системе управления;
- учет будущей замены пода в опорных конструкциях котла и стеновых конструкциях котельной;
- первым сжигание крепких неконденсирующихся газов в СРК;
- первым сжигание ила с очистных сооружений сточных вод в СРК.
Самым значительным фактором экономичной эксплуатации СРК является развитая система регулирования. Механические части котла должны быть такими, чтобы система регулирования не столкнулась с механическими ограничениями. Для этого требуется моделирование CFD. С помощью него подача воздуха и щелока осуществляется так, что развитая система регулирования может управлять котлом в оптимальном режиме, стабильно на максимальной нагрузке до планового останова.