Технология прямого
Вид материала | Документы |
- Реферат по дисциплине управление маркетингом на тему стратегии прямого маркетинга, 240.21kb.
- Технология прямого, 498.19kb.
- Технология прямого сращивания пластин кремния и технологические маршруты изготовления, 689.61kb.
- Н. Г. Осенний 2012 г. Расписание, 59.13kb.
- Московский Государственный Университет пищевых производств Ю. А. Косикова методические, 725.64kb.
- Прикладнаямеханика лекция, доц. Воложанинов С. С. 2/150, 47.06kb.
- Программа вступительного экзамена по специальности 05. 27. 06 «Технология и оборудование, 81.6kb.
- Отчет о результатах самообследования основной образовательной программы по специальностям:, 1627.98kb.
- Рабочая программа и методические указания к выполнению контрольной работы для заочной, 305.14kb.
- Программа преддипломной практики студентов специальности 1-36 01 01 «Технология машиностроения», 336.91kb.
4.5. Проектирование оборудования для имплантации ионов легких газов в подложки полупроводников большого диаметра
Производство структур КНИ (для специализированных ИС и микросенсоров), а также многослойных структур для элементов микроэлектромеханических систем является стратегической задачей для многих высокотехнологичных и наукоемких отраслей. Ключевой проблемой формирования структур КНИ методом газового скалывания на отечественных предприятиях является разработка и изготовление специализированного оборудования, отвечающего ужесточающимся требованиям микроэлектронного производства. Поэтому создание технологического высокопроизводительного, надежного оборудования для имплантации ионов водорода в подложки большого диаметра является актуальной задачей. В настоящее время существует несколько направлений научных разработок на основе которых возможно создание специализированного оборудования для получения структур методом газового скалывания. Наиболее перспективные методы используют имплантацию ионов водорода (или ионов легких газов) с использованием имплантеров, а также внедрение ионов с использованием эффективной системы Plasma Immersion Ion Implantation (PIII), позволяющей получать структуры КНИ низкой стоимости и с высокой производительностью.
На основе научных работ радиационно-ускорительного центра РУЦ МИФИ [42–52] и ИТЭФ проводятся работы по проектированию и созданию макетного источника ионов водорода с энергиями 30 – 150 кэВ для имплантации протонов в подложки полупроводников большого диаметра (150 – 200 мм) с целью получения структур КНИ большого диаметра. К источнику протонов предъявляются следующие основные требования:
- повышенное, близкое к 100%, содержание в пучке атомарных ионов водорода;
- стабильность энергии протонов не ниже ±2 % при среднем токе пучка до 1 мА;
- большой срок службы, высокая надежность и стабильность работы, обеспечивающие конкурентоспособность имплантера по сравнению с известными аналогами;
- нечувствительность к продуктам крекинга масла;
- возможность формирования равномерного (не хуже ±5%) поля облучения на мишени диаметром до 100 – 150 мм.
Для выбора прототипа источника водородных ионов имплантера проведены работы по адаптации имеющихся у исполнителя инжекторов ионов к поставленным задачам, включающим проектирование, изготовление и макетные испытания следующих типов источников: дуоплазмотрона, источника Пеннинга с холодным катодом, электронно-ионного источника плазменно-пучкового типа, ВЧ инжектора (рабочей частотой 36 МГц), СВЧ инжектора (рабочей частотой 2450 МГц).
На основе анализа полученных результатов определен прототип источника и выполнены необходимые конструктивные доработки, а также рассмотрен вопрос об использовании "электронного душа" для нейтрализации объемного заряда облучаемых пластин.
Для получения тонких слоев кремния заданной толщины необходимо отработать методику (технологию) режимов имплантации ионов водорода (гелия) и последующей термообработки, контроля состояния облучаемых пластин. В распоряжении авторов имеется ускорительная техника, квалифицированный персонал, методики исследования дефектной структуры твердых тел методами атомно-силовой микроскопии, просвечивающей электронной микроскопии, атомно-ионной микроскопии и позитронной и мюониевой спектроскопии.
Исходя из необходимости получения радиационно-стойких ИС, целесообразно получать структуры КНИ с толщиной изолированного монокристаллического слоя кремния в диапазоне от 0,1 до 1 мкм, изолирующего оксида от – 0,1 до 10 мкм. Состав изолятора – аморфный SiO2; многокомпонентное стекло (например бариево-алюмо-силикатной системы BaO–Al2O3–SiO2); SiO2 – Si3N4, алюмонитридная керамика и т.д. Для аналоговых ИС толщина изолированного монокристаллического кремния должна составлять величину от 1 до 30 мкм, толщина слоя изолированного монокристаллического кремния от 1 до более 100 мкм необходима для элементов микромеханических датчиков, таких как акселерометры и микромеханические гироскопы. При этом технологические процессы получения исходных структур (КНИ) могут быть принципиально похожими.
4.6. Особенности процесса сращивания пластин кремния с использованием данных о выделении паров воды
Существует множество методов связывания монокристаллических подложек. Это, в первую очередь, термокомпрессионный метод связывания, осуществляемый при высоких температурах с приложением внешнего давления к соприкасающимся очищенным поверхностям подложек. При создании специальных приборов и устройств используются методы связывания через слои диоксида кремния, различных оксидов металлов, стеклообразных промежуточных слоев и т.д. Особый интерес представляет метод сращивания стандартных пластин кремния с нанесенными слоями диоксида кремния посредством химических реакций между гидроксилированными и гидратированными поверхностями пластин [1–4]. Далее рассмотрены особенности метода сращивания стандартных пластин кремния во влажных условиях по данным о выделении паров воды [9–15].
Имеются значительные трудности получения структур КНИ посредством технологического роста слоев кремния, например, на сапфире и диоксиде кремния, связанные с несоответствием постоянных решеток применяемых материалов, в результате чего получаются некачественные слои кремния. Выше отмечалось, что в последние годы появилась новая технология получения качественных слоев изолированного кремния, заключающаяся в сращивании двух стандартных пластин и последующем утончении одной из них до требуемой толщины слоя монокристаллического кремния. Процесс сращивания отличается сложностью и заключается во взаимодействии двух гидратированных и гидроксилированных поверхностей SiO2 [20,21]. Физико-химическая модель сращивания, предложенная в работе [21], включает три последовательные стадии (рис.4.3).
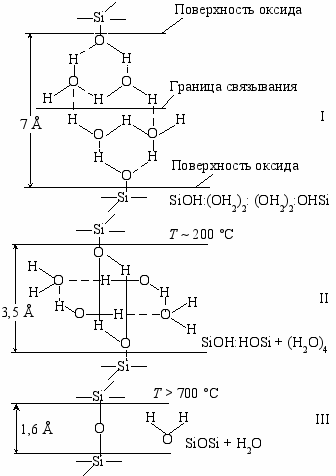
Рис.4.3. Физико-химическая модель сращивания стандартных пластин кремния
На первой стадии при соприкосновении двух гидратированных поверхностей образуются водородные связи между кислородом и водородными атомами адсорбированных молекул воды (четыре молекулы воды могут образовать водные кластеры (циклические тетрамеры)). Максимальная энергия связи, свойственная циклическим тетрамерам, составляет величину примерно 10 ккал/моль в расчете на одну молекулу воды, что соответствует 0,43 эВ. Это в 3 раза больше, чем прочность связи для "гидроксиловой" воды в димере, которая равна примерно 3 ккал/моль. Вследствие этого энергетически выгодно отделение водных кластеров от SiOH-групп с образованием новых SiOH – OHSi связей. При температурах выше 700 C кластеры воды распадаются. При этом единичные силанольные связи могут образовывать SiOSi связи с выделением молекул воды.
В работах [20,21] отмечается, что при комнатной температуре энергия связи двух осушенных гидратированных поверхностей пластин, обусловленная ОН связями молекул Н2О, составляет величину примерно 85 эрг/см2. При температуре выше 300 С возникают Н-связи за счет ОН-групп поверхности SiO2, а (Н2О)4 распадается и молекулы Н2О диффундируют от места сращивания. Предполагается, что имеются две Н-связи на одно место сращивания; при этом получается структура, не имеющая места в воде, но возможная для поверхностных ОН-групп. Если взять как наиболее вероятную энергию связи в водном димере, то получим для прочности связи величину 2х6,1 ккал/моль, соответствующую поверхностной энергии сращивания 634 эрг/см2 в случае, если все силанольные группы связаны друг с другом. В области очень высоких температур (вплоть до 800 С) идет дальнейшее удаление воды и образование связей SiOSi. Технология сращивания включает стадию осушки пластин при 50 С перед непосредственным сращиванием. Это очень важная стадия, так как она позволяет избежать обильного образования пузырьков воды на поверхности сращивания. Отметим, что образующиеся пузырьки исчезают сами по себе за несколько недель при комнатной температуре или за более короткое время при высоких температурах.
В рамках модели работы [21] проведенные эксперименты по предварительной осушке говорят о том, что нагревание пластин перед непосредственным сращиванием состоит в десорбции Н2О с гидратированной (гидроксилированной) поверхности с освобождением пространства для развития SiOSi связей при последующих стадиях отжига. Это может оказывать существенное влияние на прочность связывания пластин кремния.
Резюмируя, еще раз подчеркнем, что модель, предложенная в работах [20,21], состоит из трехстадийного процесса сращивания с участием молекул воды. На стадии I две подложки соединяются через кластеры воды и поверхностная энергия связи составляет величину примерно 100 эрг/см2. На стадии II уже Н-связи силанольных групп связывают пластины, а на поверхности раздела присутствуют водные кластеры со средней плотностью (Н2О)4/13,35·Å2. Максимальная энергия связи на стадии II равна 634 эрг/см2. На стадии III энергия связи достигает величины 2·980 эрг/см2, где 980 эрг/см2 – поверхностная энергия связи кварца.
В работах [20,21] были проведены детальные экспериментальные исследования поверхностной энергии связи в зависимости от времени отжига и температуры. Ниже, следуя модели [20,21], посвященной кинетическому анализу поверхностной энергии связи, развита модель сращивания, основанная на выделении паров воды. Выпишем основные реакции этой модели.
SiOH:(OH2)2:(OH2)2:OHSi
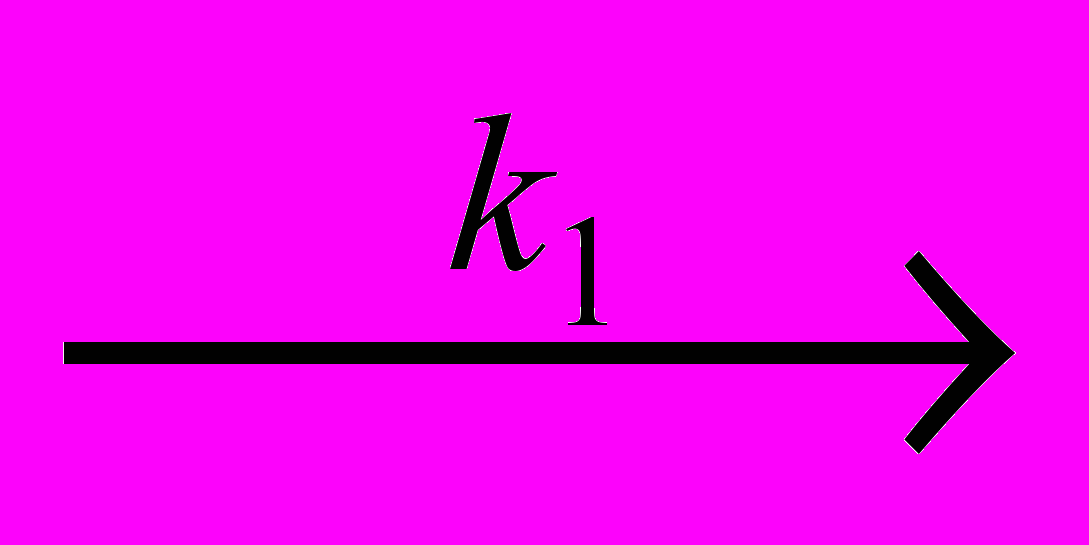
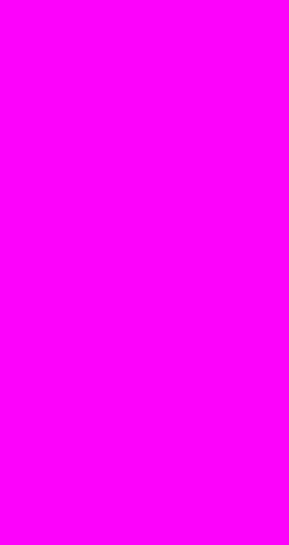
Левая и правая часть уравнения (4.2), соответствуют реакциям между стадиями сращивания I и II. Естественно, что
(Н2О)4 (Н2О)3 + Н2О (Н2О)2 + Н2О 2 Н2О . (4.3)
Кроме того,
SiOH:SiOH
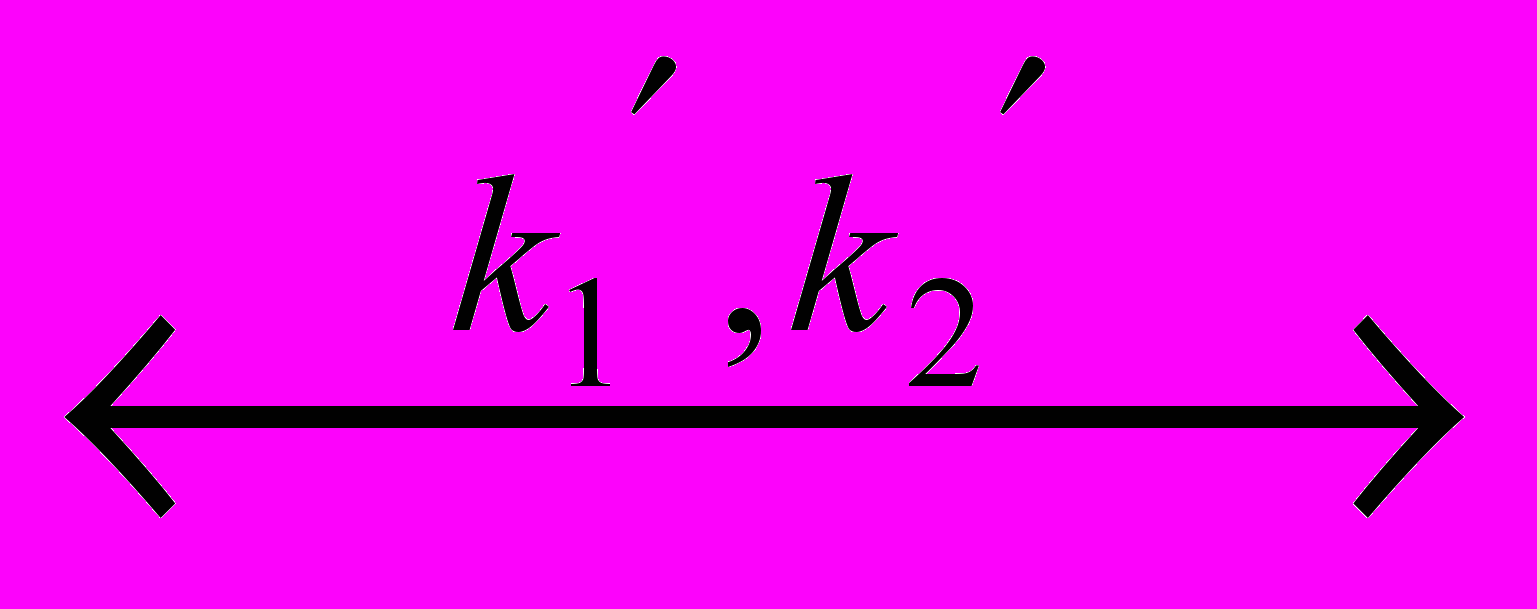
SiOH:SiOH
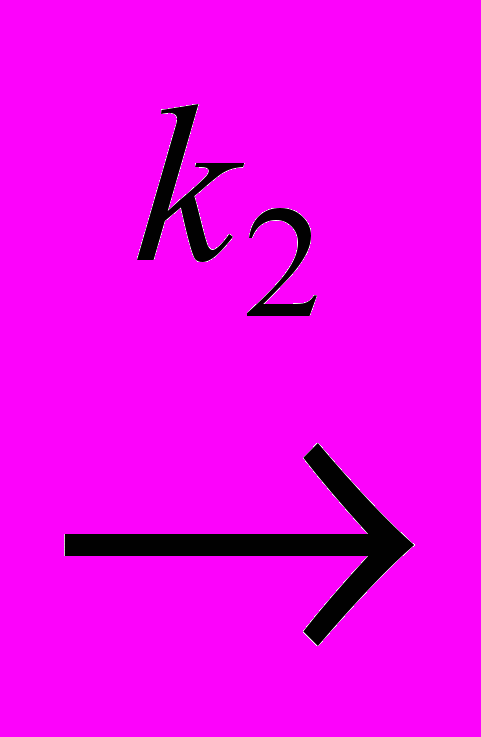
Это протекающие реакции между стадиями сращивания II и III, соответствующие процессу прямого связывания двух окисленных пластин кремния с гидроксильными группами на их поверхности (подложки А и В) (рис.4.4).
При нагревании двух таких соединенных пластин взаимодействие двух противоположных ОН-групп приводит к образованию молекул воды и силоксановых связей ≡Si–O–Si≡.
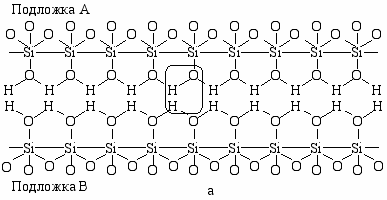
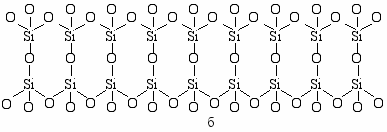
Рис.4.4. Схема процесса сращивания подложек A и B с гидроксильными группами на поверхности (а) и последующим образованием связи ≡Si–O–Si≡ (б)
В работе [5] показано, что сухая и влажно-окисленная пластины, соединенные в сухих условиях имеют несовершенную связь. С другой стороны, сухая и влажно-окисленная пластины, соединенные во влажных условиях связывание лучше. Таким образом, целесообразно проводить процесс сращивания подложек в условиях влажной атмосферы.
Энергия активации реакции (4.2) должна быть близкой к величине энергии водородной связи, равной примерно 50 мэВ. Энергия активации реакции (4.5) должна лежать в пределах от 1,8 до 2,1 эВ, так как эта реакция подобна поверхностной реакции окисления кремния.
Естественно, что
d[SiOSi]/dt=d[H2O]/dt= k2(no-[SiOSi]) = k2(no - [H2O]) (4.6)
Здесь k1 и k2 – константы скоростей реакции, no – число мест сращивания. Кроме того, согласно (4.4)
d[H2O]/dt = k1 [SiOH:SiOH] = k2 [H2O] (4.7)
Решения уравнений (4.6) и (4.7), согласно [21], позволяют описать кинетику прочности связывания и кинетику газовыделения
W = (2х980 - WB) [1 - exp(-k2t)] + WB, (4.8)
где 2·980 эрг/см2 – энергия связи пластин кремния за счет SiOSi связей, а
WB = 630 exp(-0,05 / kB·Т) [эрг/см2]. (4.9)
Здесь kB – постоянная Больцмана, Т – температура.
Нам удалось показать, что кинетика выделения паров воды во многом может описываться подобно уравнению (4.8) [24 - 26].
[H2O](t) {[no-no exp(-0,05/kB·T)] [1-exp(-k2t)]} + no exp(-0,05/kB·T) (4.10)
Из выражений (4.8) и (4.10) следует, что зависимости W и [H2O](t) симбатны. Этот теоретический вывод подтверждается качественным уровнем проведенных исследований сращивания стандартных пластин кремния различных марок. Следует, однако, отметить, что при выводе выражения (4.10) мы пренебрегли возможными процессами диссоциации воды на поверхности сращивания, поскольку этот вопрос нуждается в дальнейших экспериментальных и теоретических исследованиях. Подчеркнем, что полученное выражение (4.10) может быть использовано в качестве алгоритма моделирования и оптимизации процесса сращивания пластин кремния [15–19].