Разработка ресурсосберегающей технологии и технических средств для производства и комплексного использования семян льна-долгунца в условиях северо-западного региона российской федерации
Вид материала | Автореферат |
- Дирекция Северо-Западного регионального отделения рст приступает к реализации комплексного, 39.24kb.
- Реферат отчета о научно-исследовательской работе по теме: «Разработка и внедрение ресурсосберегающей, 76.5kb.
- Рабочая программа повышения квалификации «Технология производства и переработки с/х, 741.27kb.
- 2-я научно – практическая конференция кардиохирургов Северо-Западного региона России, 56.04kb.
- 2-я научно практическая конференция кардиохирургов Северо-Западного региона России, 53.04kb.
- Морская пехота в великой отечественной войне 1941 1945, 782.91kb.
- Технических средств и процессов, 579.76kb.
- «Качество и конкурентоспособность в промышленности и науке» перспективы использования, 189.65kb.
- Разработка ресурсосберегающей технологии получения и использования никелевого концентрата, 307.93kb.
- 1. Состав и структура клеточной стенки, 171.34kb.
На примере Вологодской области по важнейшим факторам (теплообеспеченности, средней декадной температуре воздуха, числу ясных и пасмурных дней, относительной влажности воздуха, гидротермического коэффициента) определена наилучшая зона производства семян.
На основе данных метеорологических условий вегетационного периода юго-западной зоны области пришли к выводу – продолжительность активной вегетации (123…158 дн.) позволяет получать качественные семена (количество ФАР = 1769С).
Имея современные районированные сорта льна-долгунца с коротким вегетационным периодом можно получать урожай семян и льноволокна на европейском уровне. Так сорта «Лидер», «Восход» по урожайности семян (8…9 ц/га) и льноволокна (17,5…18,5 ц/га) превосходят европейский сорт «Мерилин» с урожаем семян 7,5 ц/га и льноволокна 16,25 ц/га.
Имея данные о сорте льна с учетом вегетационного срока специалисты могут выбрать направление специализации, вариант ресурсосберегающей технологии уборочных работ.
В
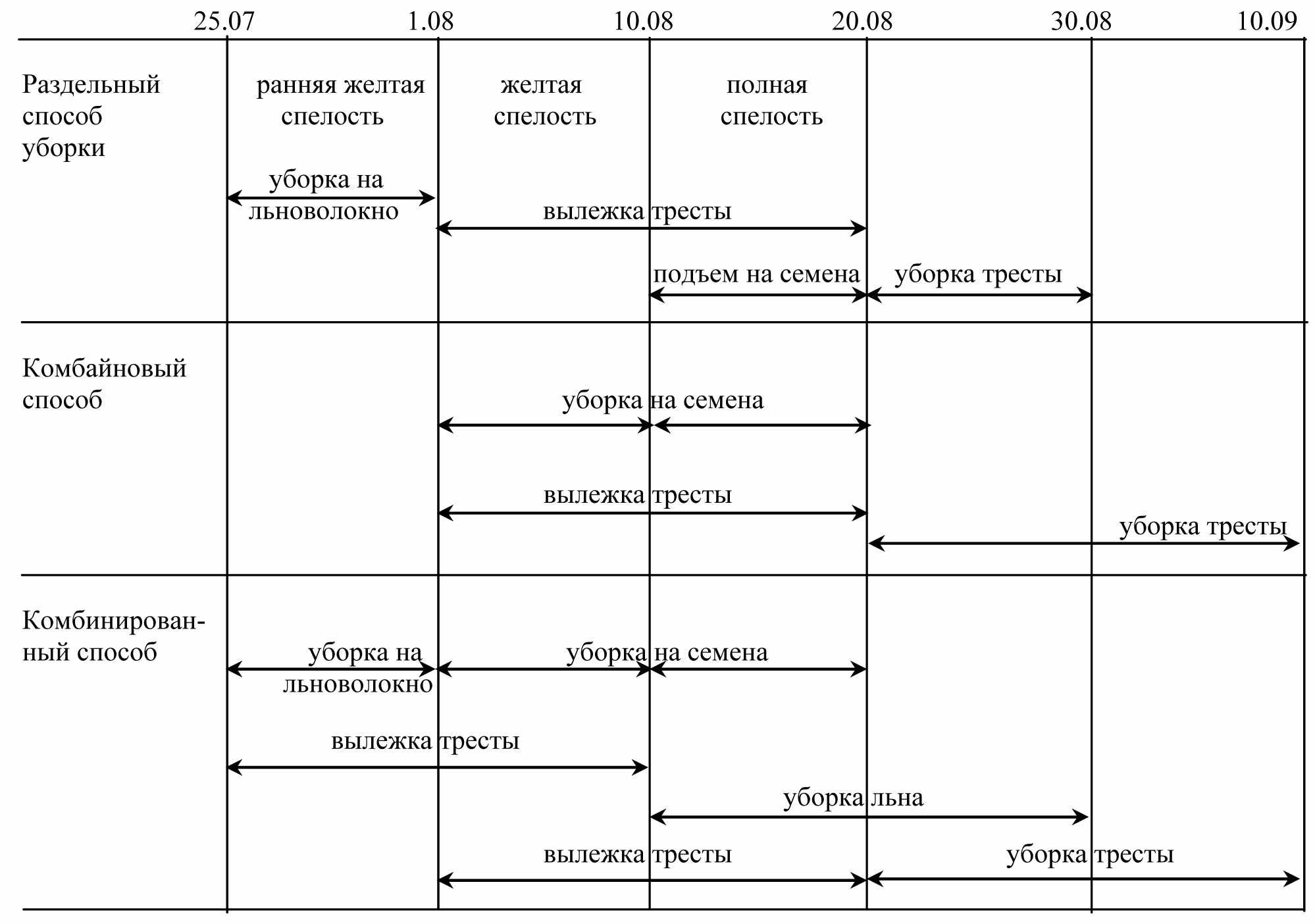
Рис. 1. Сроки уборки льна-долгунца при различных способах уборки (при посеве до 5 мая)
Из рисунка 1 видно, что при раздельном способе уборки льна в стадии ранней желтой спелости уборку льна можно начинать с 20…25 июля. Продолжительность уборки должна составлять не более 8…9 дней. Тогда вылежка льносоломки будет длиться 16 дней (до 20…25 августа). Заканчиваться уборка может 10 сентября, т.е. в более благоприятных условиях.
В случае недополучения фонометрический активной радиации (ФАР) в период вегетации, применив активную вентиляцию льновороха (подогретым или неподогретым воздухом) в течение 5…8 дней, можно добиться созревания семян. Такие семена можно использовать на семенные или технические цели.
Основополагающим технологическим процессом получения семян является процесс отделения коробочек льна от стеблей. От уровня его совершенства зависит величина урожая, размер потерь, качество льнопродукции, трудоемкость и энергоемкость сушки и обработки льновороха.
Научным обоснованием конструктивных параметров и режимов работы очесывающих устройств в разное время занимались М.М. Шлыков, М.Н. Летошнев, П.Ф. Прибытков, П.К. Шрамко, Г.А, Хайлис, Л.Ю. Гурвич, Н.Н. Быков.
Отсутствие общей теории процесса очеса не дает возможности разрабатывать более эффективную технологию очеса, совершенствовать рабочие органы. Исследованиями Черникова В.Г., Хайлиса Г.А., Порфирьева С.Г. заложены основы теории очеса стеблей и отдельных важных узлов льнокомбайна.
Исследованиями Хайлиса Г.А., Быкова Н.Н., Катченкова С.А., Петухова Б.С., Зинцова Л.Н. и др. были установлены значительные потери семян при работе льнокомбайна.
Отсюда можно сделать вывод, что применяемый способ очеса в льнокомбайне ЛК-4А не вполне отвечает современным требованиям и нуждается в улучшении или замене на более прогрессивный.
Иные очесывающие устройства для льна применяются на Западе. Так фирмой Union (Бельгия) для отделения коробочек от стеблей используется комбинированный способ очеса, обеспечивающий иной состав льновороха (см. рис. 2).
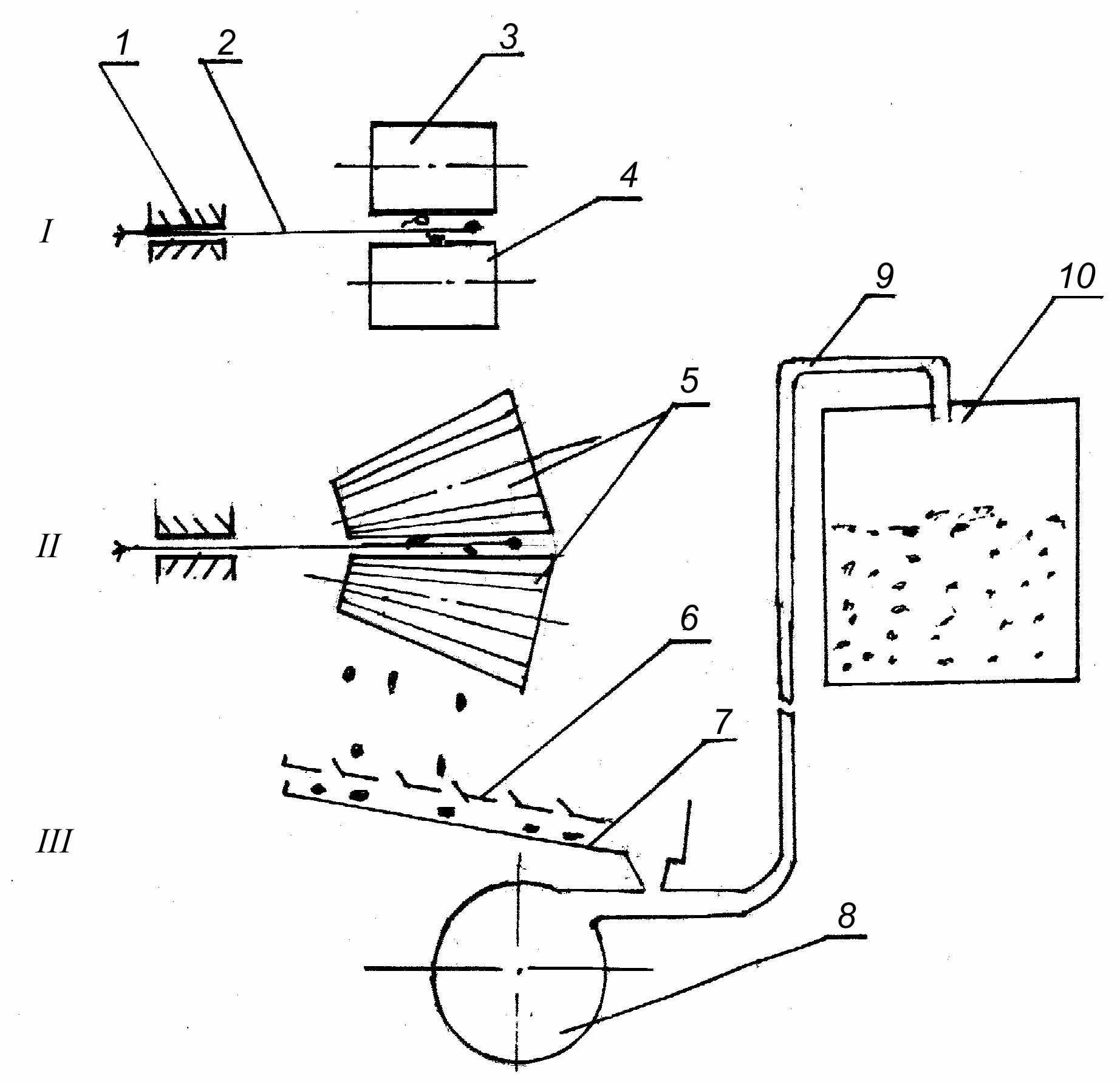
Рис. 2. Схема очесывающего
устройства подборщика-очесывателя U-22:
1 – зажимной транспортер; 2 – лента льна; 3 – регулируемый плющильный барабан; 4 – нижний барабан; 5 – очесывающие валы; 6 – решето; 7 – желоб; 8 – вентилятор; 9 – воздуховод; 10 – бункер
Процесс отделения коробочек от стеблей проходит в несколько этапов.
На первом этапе зажатая горизонтальным транспортером (1) лента льна (2) с головками проходит через регулирующую щель, образуемую плющильными валиками (3, 4). Величина щели (1,5…2 мм) обеспечивает сохранность семян и образование трещин.
На втором этапе верхняя часть стеблей движется между двумя конусными рифлеными очесывающими валами (5), имеющими зазор 2…3 мм, подвергается изгибу, с помощью которого происходит отрыв плющеных коробочек.
На третьем этапе оторванные плющеные головки и свободные семена опускаются на решето (6), проваливаясь через него, попадают в желоб (7), а затем в приемник вентилятора (8) и по воздуховоду (9) оказываются в бункере (10).
Такое устройство комбинированного очесывающего аппарата почти не имеет путанины, что повышает эффективность сушки семян.
Ранее уже отмечалось, что в работе льноуборочной техники наблюдаются значительные потери семян. Однако до сих пор отсутствует методика определения потерь льнопродукции. В данной работе мы предлагаем дать объективную оценку потерь льнопродукции в течение уборочного цикла.
По нашему мнению, при групповой работе комбайнов качество убранного поля должно оцениваться по количеству оставшихся в поле семян, неочесаных головок в стеблях ленты с площади 1 м2 поля.
Перед уборкой определяется биологическая урожайность:
а) льносоломки БУсл =10 000 Мст Кст Кос Кз (14)
б) льносемян БУс =10 000 Мс Г Кст Кп Кос (15)
где Мст – масса стебля без головок, г; Кст – количество стеблей на 1 м2; Кос, Кз– коэффициенты полноценности стеблей, потерь; Мс – масса 1000 семян, г; Кп – коэффициент выхода зрелых семян в головке (Кп = 4…8,3); Г – головчатость стебля.
Величину потерь льносоломки (Плс ) определим из выражения:
Плс=10 000(Кст.п – Кф) Мст (16)
где Кст.п, Кф – количество стеблей на 1 м2 до и после уборки, шт.
Размер потерь семян (Псл ) определим по формуле
Псл=10 000 Кз Мс (Кс + КгКп). (17)
Общий размер потерь урожая определим из выражения:
Побщ=10 000 [(Кст.п – Кф) Мст + Кз Мс (Кс + КгКп)]. (18)
Тогда относительная общая величина потерь (Потн) определяется из выражения:
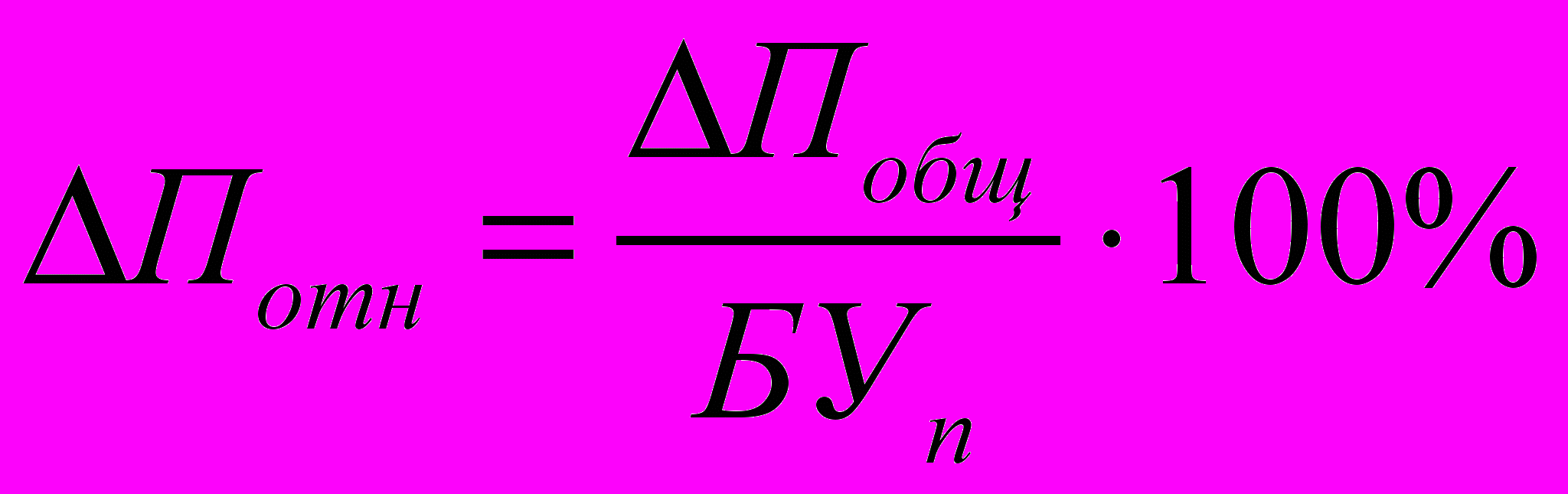
В процессе работы льноуборочного комбайна ЛК-4А, да и разработанного нового ЛТ-1,65 неизбежны потери семян и льноволокна из-за несовершенства работы очесывающего аппарата.
В проведенных в течение ряда лет исследованиях работы льнокомбайнов производственных условиях нами было установлено, что происходят большие потери семян и стеблей льна. Например, потери семян льна составляют от 23 до 43% от выращенного урожая семян.
Изучив динамику движения семян и головок льна в очесывающем барабане с целью снижения отхода стеблей льна в путанину и снижения потерь семян льна при очесе стеблей льна нами проведено усовершенствование очесывающего барабана льнокомбайна (рис. 3).
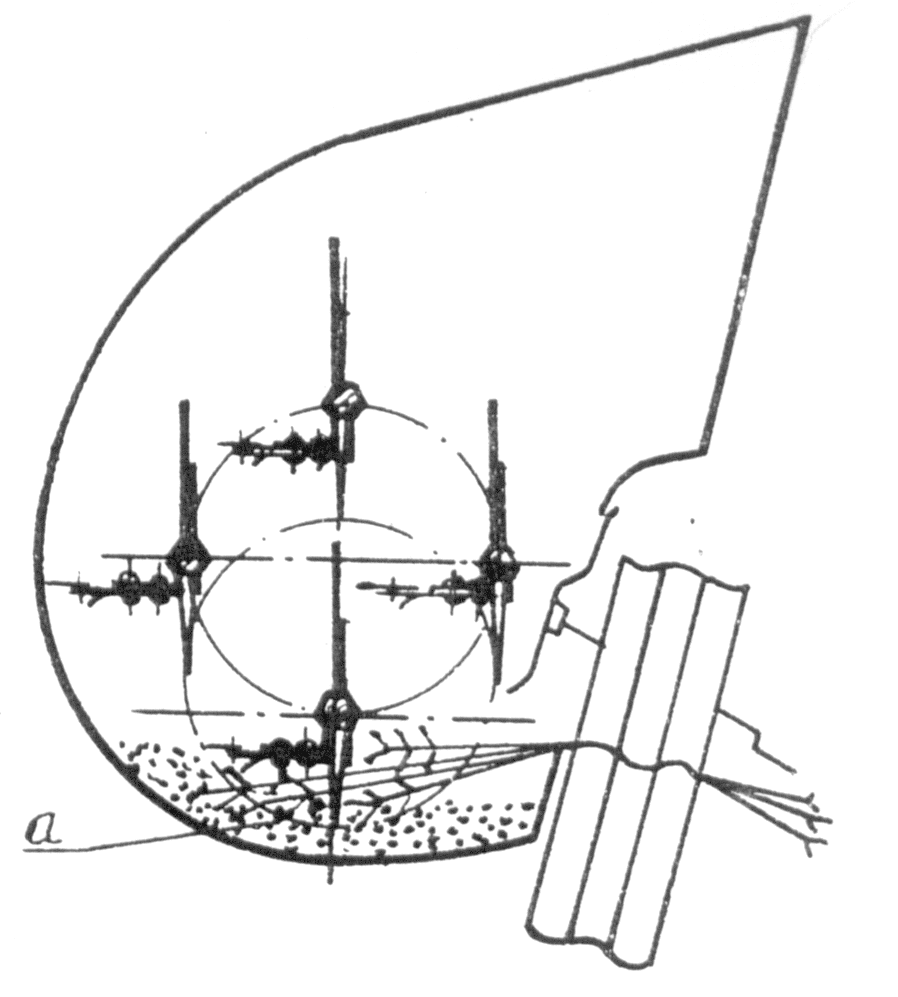
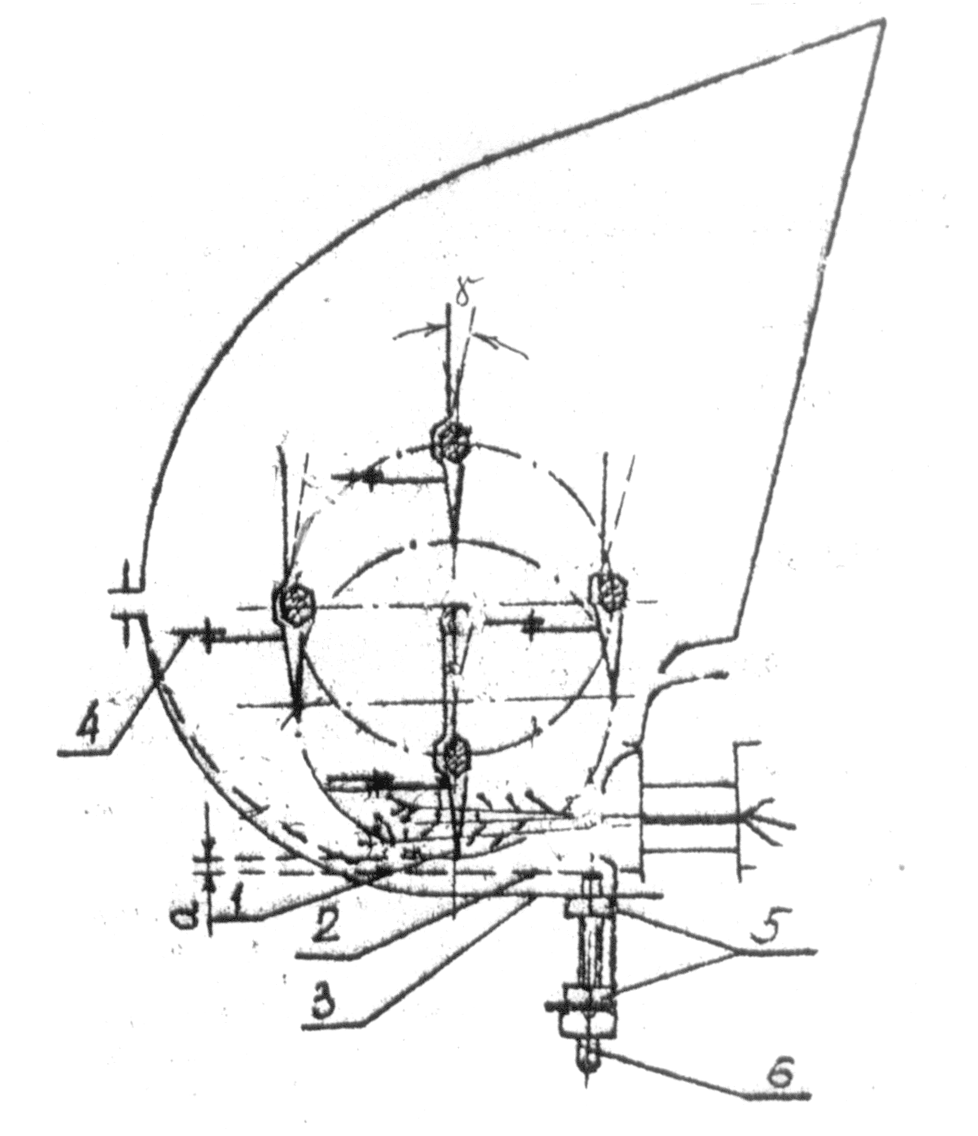
а) заводской б) модернизированный
Рис. 3. Принцип действия очесывающего аппарата
1 – гребенка; 2 – регулируемое днище;
3 – корпус; 4 – ремень прорезиненный; 5 – гайка регулировочная; 6 – шпилька
Предложена конструкция барабана с регулируемым днищем (2), которое изготовляется из листовой стали толщиной 2…2,5 мм и в верхней части кожуха барабана крепится болтами.
В нижней части регулируемого днища привариваются две шпильки М8 (6) длиной 110 м с регулируемыми гайками (5) и вставляются в отверстия днища кожуха барабана.
Для лучшего прилегания регулируемого днища к боковым стенкам барабана приклепываются уплотнения из прорезиненного ремня. Такая конструкция днища позволяет отрегулировать необходимый зазор (а) между днищем и зубьями гребня. Семенные коробочки захватываются зубьями барабана и перемещаются на выкидной транспортер.
Для лучшей транспортировки головок и семян прорезиненные ремни (4) заменяются более толстыми (4…6) мм и удлиненными на 40 мм.
Гребенки очесывающего барабана (рис. 4) срезаются на 2/3 ширины под углом 18…20º. Это обеспечивает постепенный прочес головок, снижает отход стеблей в путанину.
Р
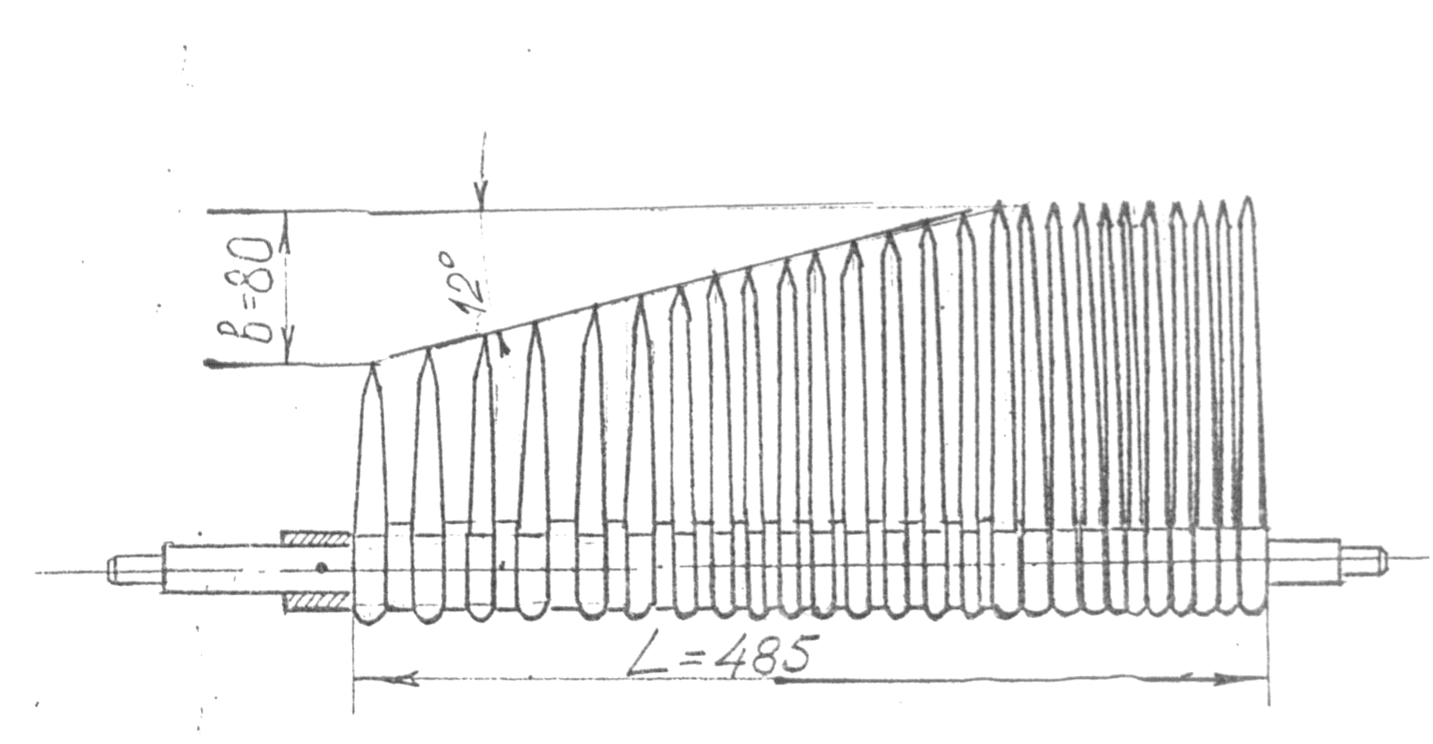
с переменной длиной зуба
Производственные исследования потерь семян и стеблей льна-долгунца проводились в колхозе «Шексна» Шекснинского района Вологодской области.
В результате исследований были обнаружены следующие каналы потерь: потери в зоне теребильных секций, потери в зоне выкидного транспортера, потери в ленте вытеребленных стеблей.
Основные потери семян, головок и стеблей льна наблюдаются в результате действия гребневого очесывающего барабана ЛК-4А.
Результаты исследований представлены в табл. 1.
Таблица 1
Сравнительные потери льнопродукции при работе комбайнов ЛК-4А
Ф., и., о. механизатора | Повторность | Количество стеблей на 1 м ленты | Величина потерь | Количество недоочесанных головок | Потери головок | Количество свободных семян | Всего потерь, кг/га | ||
стеб- лей | % | сверху ленты | под лентой | ||||||
1. Портнов Н. | 1 | 1840 | 230 | 16 | 67 | 6 | 78 | 572 | 65 |
| 2 | 2001 | 124 | 8,6 | 227 | 8 | 217 | 959 | 160,3 |
| 3 | 2022 | 282 | 13,9 | 49 | 4 | 126 | 813 | 82,9 |
в среднем | | 1954 | 212 | 10,8 | 114 | 6 | 140 | 781 | 102,5 |
2. Соловьев А. | 1 | 1677 | 337 | 20,0 | 221 | 17 | 140 | 766 | 132,2 |
| 2 | 1607 | 383 | 23,8 | 182 | 26 | 252 | 804 | 155,4 |
| 3 | 1693 | 401 | 23,7 | 206 | 14 | 186 | 916 | 146,5 |
в среднем | | 1659 | 374 | 22,5 | 203 | 19 | 193 | 928 | 144,8 |
3. Ботин В. (переоборудованный комбайн) | 1 | 2037 | 102 | 6,9 | 0 | 7 | 0 | 52 | 4,2 |
2 | 2018 | 116 | 5,7 | 12 | 5 | 17 | 38 | 10,52 | |
3 | 1998 | 132 | 6,6 | 17 | 8 | 22 | 42 | 3,1 | |
в среднем | | 2017 | 116 | 5,8 | 9 | 7 | 10 | 44 | 8,2 |
Вывод: из приведенных данных (табл. 1) видно, что величина потерь стеблей на непереоборудованных комбайнах колеблется от 8,6 до 23,8 %, а семян – от 65 до 160 кг/га. Переоборудование льнокомбайна снижает потери стеблей в 2…3 раза, а семян – в 12…17,6 раза.
Были проведены исследования определения потерь семян и головок льна при транспортировке льновороха до пункта сушки.
Для этого по брезенту проезжал трактор с нагруженным льноворохом прицепом. Подсчитывали размер потерь с площади 2,2 м2.
Масса потерь семян на 1 км пути будет равна:
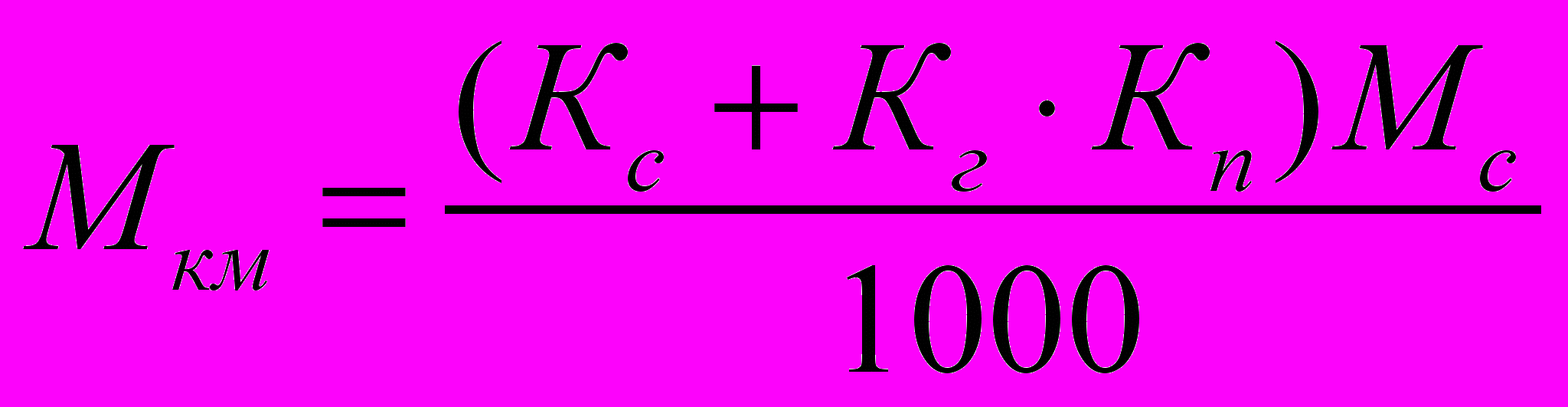
где Кс – количество семян на 1 м пути, шт.; Кг – количество головок на 1 м пути, шт.; Кп – коэффициент полноценных головок; Мс – масса 1000 семян, г.
Анализируя полученные данные, можно сделать вывод, что размер потерь при транспортировке льновороха в прицепах с уплотнением составляет примерно 0,3% урожая семян.
Однако транспортировка льновороха на неподготовленных старых прицепах может привести к необоснованным (в 3…7 раз) потерям семян, поэтому необходим ремонт прицепов, наращивание и уплотнение бортов.
Величину потерь семян льна-долгунца при работе молотилки МВ-2,5А определяли по массе семян в 1 м3, выносимой льняной мякины, из выражения:
Мс = m · Vлм , (21)
где m – содержание семян в 1 м3 льняной мякины, кг; Vлм – объем мякины с 1 га, м3.
Согласно проведенным исследованиям, 1 м3 льняной мякины имеет объемную массу, равную 82…100 кг/м3, а соотношение массы семян к массе льняной половы равно (0,75…0,8) : 1.
Зная величину урожая семян урожай льняной мякины можно определить из выражения:
Ум = 0,75 · Ус, (22)
Объем льняной мякины с 1 га определяется по формуле:
Vм = Vо · Ум , (23)
где Vо – объемная масса 1 м3 мякины, кг.
С целью исключения неквалифицированной рабочей силы при разравнивании льновороха в прицепе нами предложена установка на ЛК-4А автосцепа [а.c. 1551278] с регулируемой длиной (рис. 5).
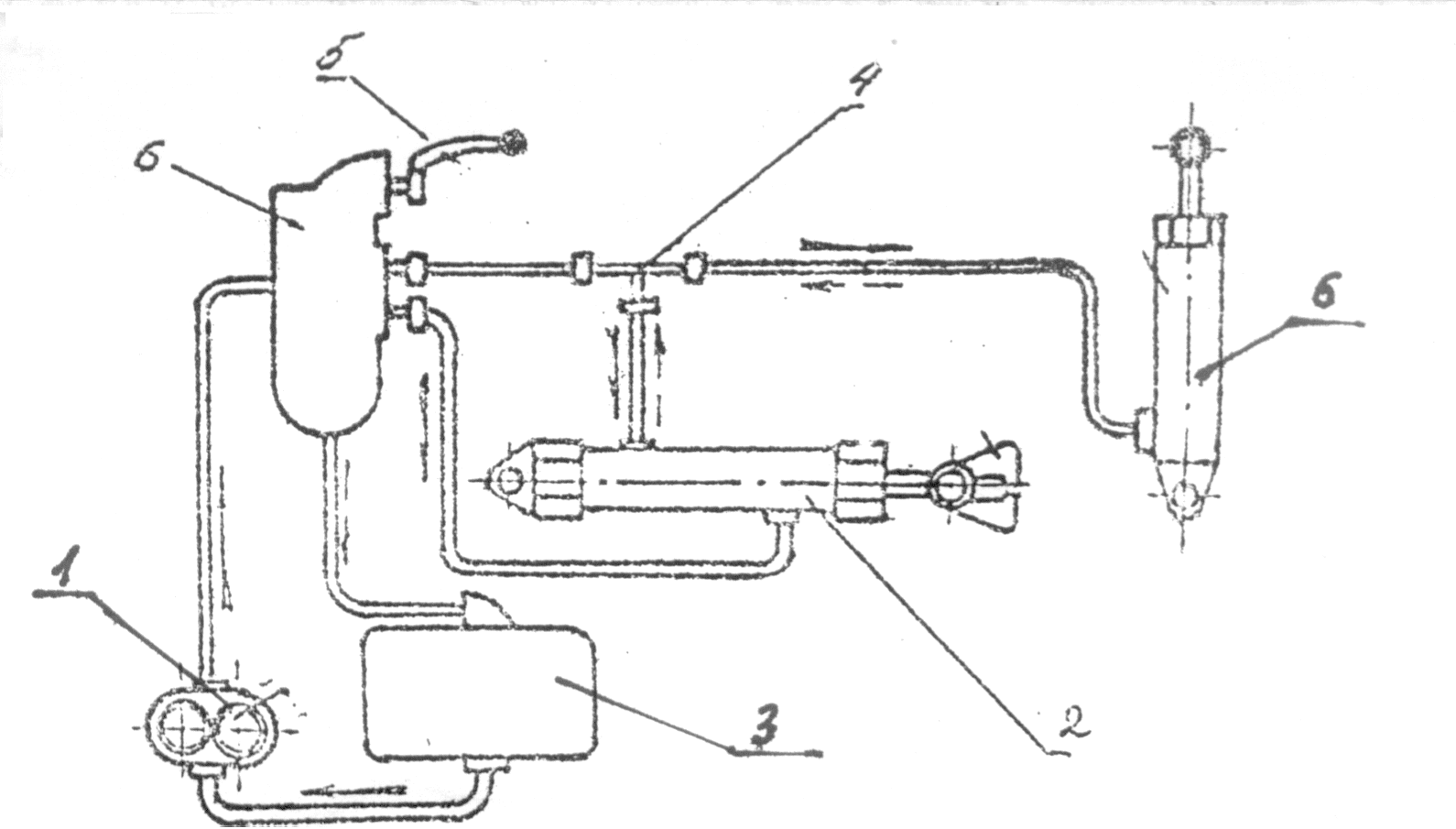
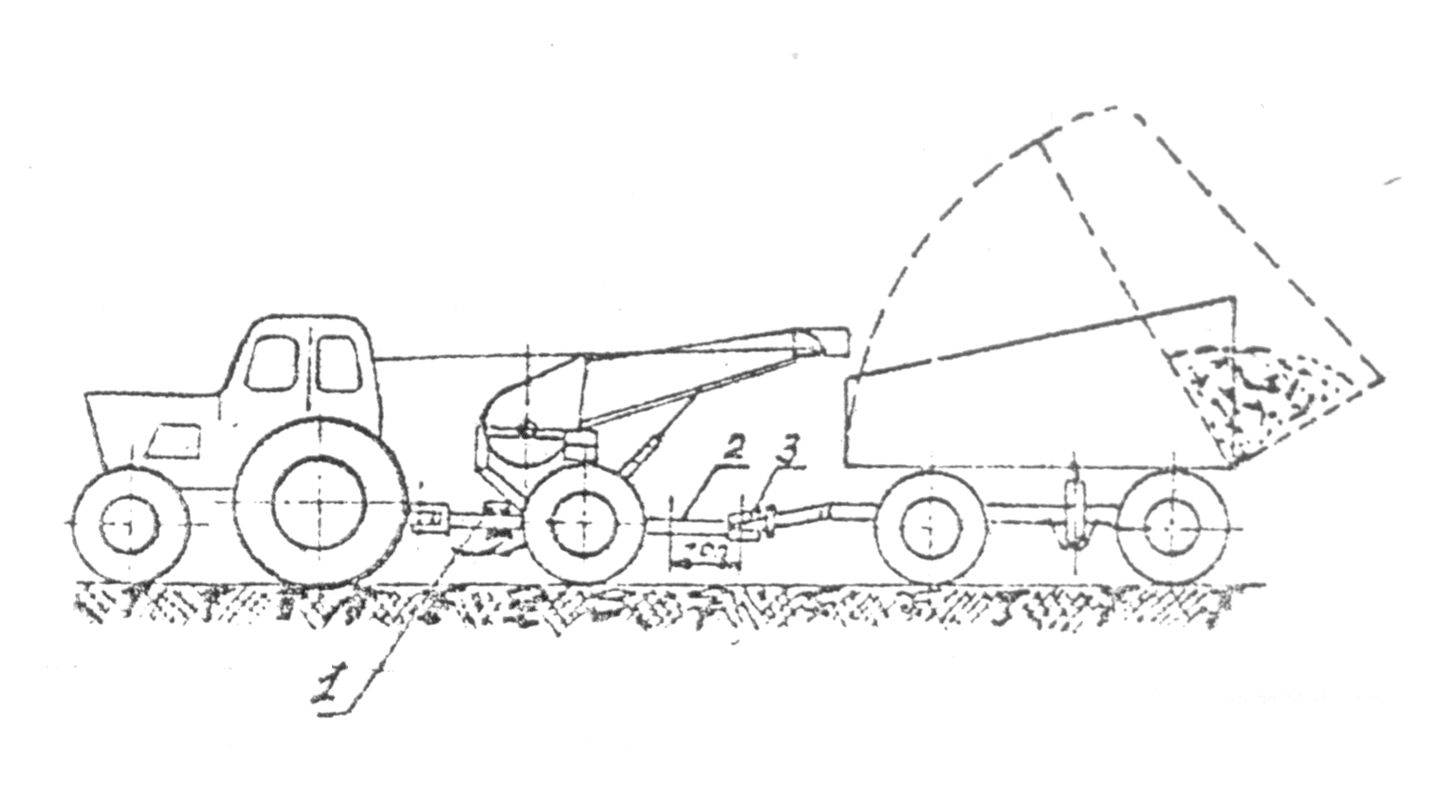
Рис. 5. Льнокомбайн с регулируемой длиной автосцепа: 1 – поперечная балка; 2 – цилиндр; 3 – автосцеп | Рис. 6. Гидросистема агрегата: 1 – насос; 2 – гидроцилиндр передвижения прицепа; 3 – гидробак; 4 – тройник; 5 – рычаг распределителя; 6 – гидроцилиндр прицепа |
Высокопроизводительное использование уборочной техники достигается на основе соблюдения общих принципов организации труда: пропорциональности, согласованности, ритмичности и поточности.
Условием непрерывной работы является равенство суточной производительности сушильного пункта (Wсп), транспортных средств (Wт) и льнокомбайнов (Wлк):
Wсп=Wт=Wлк . (24)
Для непрерывной работы льнокомбайнов необходимо условие: уборочный цикл должен быть равен транспортному:
t3.+tо.г.+tп.п.=tп.г.+tд.г.+tр.+tх.+tо.п. , (25)
где t3. , tо.г. , tп.п. – продолжительность загрузки прицепа, отцепа и прицепа пустого прицепа, ч; tп.г., tд.г. , tр , tх , tо.п. – продолжительность прицепа груженого прицепа, время доставки на льноток, разгрузки, движения трактора с порожним прицепом, отцепа пустого прицепа, ч.
Длительность рейса определена из выражения:
Тр=tз.м+tр+60L/vx+60L/vг , (26)
где tз.м – продолжительность замены прицепа, ч; vx и vг – скорости движения без груза и с грузом, км/ч; L – расстояние перевозки от поля до пункта сушки, км.
Продолжительность загрузки прицепов льноворохом (tз.т) определяется из выражения:
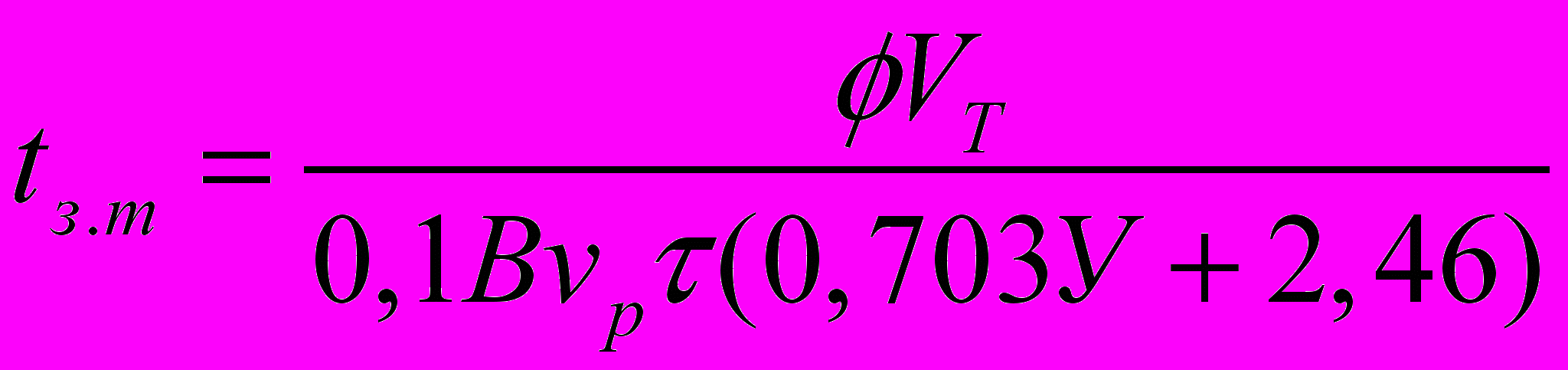
где VТ – объем прицепа, м3; – коэффициент заполнения прицепа; У – урожайность льносемян, ц/га.
Необходимое число транспортных средств определяется по формуле:

где – коэффициент использования пробега, nлк – количество комбайнов.
Исходя из условия, что количество поступающего влажного льновороха должно быть переработано на пункте сушки в течение суток, то условие выразим уравнением:
GвWлкtкKк=Wcпtc , (29)
где Gв – масса сырого льновороха с 1 га, кг/га; Wлк – производительность льнокомбайна, га/ч; tк – время работы льнокомбайна, ч; Kк – количество льнокомбайнов, шт.; Wcп – производительность пункта сушки, кг/ч; tc – время работы пункта сушки, ч.
Развернутое выражение производительности пункта сушки будет равно:

Необходимую производительность машин по переработке льновороха (Wлм) определим из выражения:
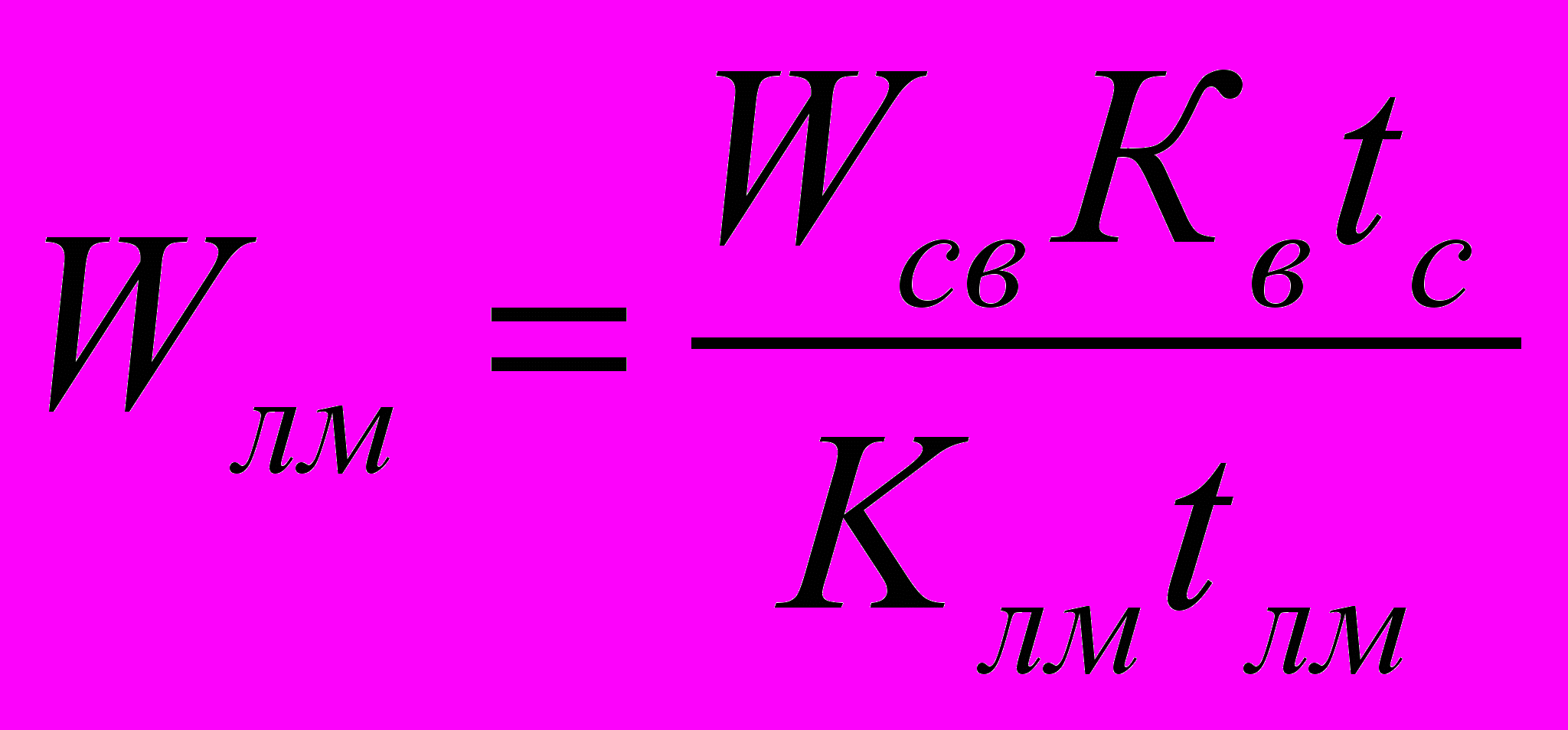
Сезонная производительность пункта сушки льновороха будет равна:

Из (33) следует, что сезонная производительность пункта сушки и переработки льновороха прямо пропорциональна производительности теплогенераторов, времени сушки и обратно пропорциональна объему влажного льновороха.