Повышение износостойкости гильз цилиндров двигателей путем обоснования параметров анодно-механического хонингования
Вид материала | Автореферат |
- Повышение надежности дизельных двигателей путем оптимизации регулировочных параметров, 211.56kb.
- Повышение эффективности диагностирования цилиндропоршневой группы автомобильных двигателей, 268.3kb.
- Повышение эффективности хонингования сферических поверхностей деталей из нержавеющих, 255.56kb.
- Федеральное агентство по образованию федеральное государственное учреждение среднего, 38.08kb.
- Повышение твердости, теплостойкости и износостойкости цементированной хромоникелевой, 134.07kb.
- Технологическое обеспечение и повышение износостойкости втулок из градиентных композиционных, 307.97kb.
- Повышение эффективности выращивания молодняка крс путем оптимизации параметров и режимов, 251.61kb.
- Д. М. Медведев одноступенчатое технологическое обеспечение износостойкости цилиндрических, 106.33kb.
- Выбор рациональных параметров конструкции опор газотурбинных двигателей с межроторными, 218.67kb.
- Курсовая работа по дисциплине : " техническая эксплуатация автомобилей., 578.1kb.
На правах рукописи
ШАЙХУТДИНОВ РАФИС РАШИТОВИЧ
Повышение износостойкости гильз цилиндров
двигателей путем обоснования параметров
анодно-механическОГО ХОНИНГОВАНИЯ
Специальность 05.20.03 - Технологии и средства технического
обслуживания в сельском хозяйстве
АВТОРЕФЕРАТ
диссертации на соискание ученой степени
кандидата технических наук
Казань – 2010
Работа выполнена в ФГОУ ВПО «Казанский государственный аграрный
университет» на кафедре «Ремонт машин»
Научный руководитель: кандидат технических наук, доцент
Фасхутдинов Хасан Салахович
Официальные оппоненты: доктор технических наук, профессор
Ильин Владимир Кузьмич
доктор технических наук, профессор
Лопарев Аркадий Афанасьевич
Ведущая организация: – ФГОУ ВПО «Чувашская государственная
сельскохозяйственная академия»
Защита состоится 2 июля 2010 года в 13 часов 00 минут на заседании диссертационного совета Д220.035.02 при ФГОУ ВПО «Казанский государственный аграрный университет» по адресу: 420011, г. Казань, Учебный городок Казанского ГАУ, УЛК ИМ и ТС, ауд.213.
С диссертацией можно ознакомиться в библиотеке Казанского ГАУ (УЛК ИМ и ТС, читальный зал).
Автореферат разослан «29»_мая____ 2010 года
Размещен на сайте: www.kazgau.ru «31»_мая____ 2010 года
Ученый секретарь
диссертационного совета Галиев И.Г.
ОБЩАЯ ХАРАКТЕРИСТИКА РАБОТЫ
Актуальность работы. Повышение надежности машин и увеличение их ресурса имеют большое значение в современных экономических условиях. Энергетической основой мобильных сельскохозяйственных процессов является двигатель внутреннего сгорания (ДВС), на долю которого приходится до 36…52% от общего количества отказов. Долговечность и эффективность работы автотракторных двигателей в значительной мере определяется износостойкостью деталей цилиндропоршневой группы (ЦПГ). Износ деталей ЦПГ приводит к снижению тягово-мощностных показателей работы двигателя, росту расхода топливо смазочных материалов, загрязнению окружающей среды. Нарушения в работе ЦПГ оказывают влияние на работу других сборочных единиц двигателя, ускоряя их изнашивание. Ресурс капитально отремонтированного двигателя составляет 35…40% от ресурса нового двигателя. Одной из дорогих и быстроизнашивающихся деталей ЦПГ является гильза цилиндра (ГЦ). Интенсивность изнашивания ГЦ после капитального ремонта в 2…3 раза выше, чем у новых гильз. Поэтому разработка и совершенствование способов восстановления и увеличения ГЦ ресурса являются актуальными.
Работа выполнена в соответствии с планом НИР Казанского ГАУ; с Программой развития приоритетных направлений в Республике Татарстан до 2010 года.
Цель работы. Повышение износостойкости гильз цилиндров двигателей путем обоснования параметров анодно-механического хонингования.
Объект исследования. Объектом исследования является процесс анодно-механического хонингования гильз цилиндров двигателя ЗМЗ-511.10.
Предмет исследований. Закономерности рабочего процесса анодно-механического хонингования и образования микрорельефа поверхности, а также изменения физико-механических свойств материала.
Методика исследований. Теоретические исследования выполнены с использованием основных законов теплотехники, а также расчетно-конструктивных методов и методов физического моделирования. Экспериментальные исследования проводились на специальных стендах с использованием методов планирования эксперимента. Результаты эксперимента обрабатывались с помощью известных компьютерных программ и методов математической статистики.
Научная новизна работы. Разработка метода получения износостойкого маслоемкого микрорельефа поверхности с нанесением антифрикционного покрытия, математической модели формообразования микрорельефа поверхности.
Практическая ценность работы. Возможность использования полученных теоретических и экспериментальных результатов при анодно-механической обработке гильз цилиндров. По сравнению с типовым абразивным хонингованием разработанная технология анодно-механического хонингования металлическим инструментом с нанесением антифрикционного покрытия позволяет увеличить маслоемкость зеркала гильз цилиндров, за счет образования лунок, уменьшить их износ на 20-25%, сократить время приработки, повысить производительность труда. Полученные результаты используются учебном процессе для студентов Института механизации и технического сервиса Казанского ГАУ. Технологический процесс анодно-механического хонингования и опытные образцы хонинговальных головок испытаны и внедрены в НПО «Агросервис» и Бугульминском ПАТП РТ.
Апробация. Основные положения диссертационной работы были доложены на научных конференциях профессорско-преподавательского состава и аспирантов Казанского ГАУ (Казань, 1998-2010г.г.); на Всероссийской агропромышленной выставке «Золотая осень» (Москва, 10-14 октября 2003 г.); на технических советах ОАО «Татсельхозтехника» РТ (Казань, 1998-2000г.г.); на Международной научно-практической конференции «Совершенствование технологий, средств механизации и технического обслуживания в АПК» (Чебоксары, 24-27 декабря 2003 г.); научной конференции ФГОУ ВПО «Московский ГАУ» (Москва, 2003 г.).
Основные положения, выносимые на защиту:
1.Метод повышения износостойкости за счет увеличения маслоемкости путем получения лунок на поверхности деталей с последующим нанесением антифрикционного покрытия.
2. Математическая модель формообразования микрорельефа
3.Результаты лабораторно-производственных исследований, эксплуатационных испытаний ГЦ, обработанных анодно-механическим и абразивным хонингованием.
4. Технология анодно-механического хонингования и результаты технико-экономической оценки.
Публикации. Основное содержание диссертации, результаты исследований отражены в 13 статьях, в том числе в 2 статьях центральных журналов рекомендованных ВАК и в трудах международных симпозиумов и конференций (5 статей), получено 2 патента РФ на изобретение № 2242337 и № 2242338, 1 свидетельство на полезную модель № 23586. Результаты работы отмечены бронзовой медалью и дипломом 3-й степени Всероссийской агропромышленной выставки «Золотая осень» (Москва, октябрь 2003 г.);
Структура диссертации. Диссертация состоит из введения, пяти глав, выводов и предложений, списка литературы и приложений. Содержание работы изложено на 162 страницах машинописного текста, список литературы содержит 189 наименований, в том числе 12 на иностранном языке.
ОСНОВНОЕ СОДЕРЖАНИЕ РАБОТЫ
Во введении обоснованы актуальность проблемы, цель, объект, предмет и методы исследований. Приведена научная новизна, практическая ценность и апробация работы, реализация результатов диссертационных исследований, изложены основные положения, выносимые на защиту.
В первой главе приведены результаты состояние вопроса и задачи исследования. Рассмотрены условия работы и причины износов гильз цилиндров, проанализированы существующие способы ремонта и пути повышения долговечности гильз цилиндров, а также работы по анодно-механической обработке в целом, и электрохонингованию, в частности.
Проблемам надежности и долговечности двигателей внутреннего сгорания посвящены работы М.А. Григорьева, Н.С. Ждановского, С.В. Венцеля, Д.Н. Гаркунова, Г.И. Суранова, И.Б., Гурвича, И.А. Мишина, Н.Н. Пономарева, Б.М. Асташкевича, В.Г. Занребина, М.Н. Ерохина, В.В.Стрельцова, Е.А. Пучина, В.Ф. Карпенкова, В.К. Ильина и др.
Анализ литературных источников показал, что основными причинами малого ресурса гильз после ремонта являются: низкое качество обработки поверхностей деталей не обеспечивающее удовлетворительные условия смазки, плохая приработка деталей после ремонта, уменьшение твердости поверхности. Традиционное абразивное хонингование не обеспечивает достаточной маслоемкости поверхности, способствует её шаржированию, что снижает износостойкость деталей ЦПГ.
В связи с этим возникает необходимость в разработке и применении более прогрессивных способов обработки поверхностей. Одним из таких способов является анодно-механическая обработка (АМО). Метод анодно-механического хонингования (АМХ) (чаще всего его называют - электрохимическим) был предложен Н.Н. Гусевым и В.Н. Гусевым в 1947 году и является разновидностью способа анодно-механической обработки.
Вопросам электрохимического хонингования посвящены работы Б.И. Кана, Ю.Н. Петрова, С.С. Некрасова, Л.Л. Шора, И.Е. Фрагина, И.Н. Верховецкого, И.Д. Кейбаша, А.А. Ягуткина, В.Г.Сафронова, В.В. Веричева, Э.И. Плиско, А.П. Лавриненко, В.Ф. Карпенкова и др. Однако в этих работах исследовался процесс съема металла электрохимическим растворением с последующим удалением продуктов растворения абразивной обработкой. Применение же анодно-механической обработки гильз цилиндров с электроэрозионной составляющей освещено слабо.
Исходя из проведенного анализа литературных данных в данной работе поставлены следующие задачи:
1.Теоретически обосновать применение анодно-механического хонингования обеспечивающего повышение износостойкости гильз цилиндров.
2.Исследовать влияние различных факторов процесса анодно-механического хонингования на съем металла и качество обрабатываемой поверхности, а также обосновать рациональные режимы обработки.
3.Разработать технологию анодно-механического хонингования и конструкции устройств для его осуществления.
4.Провести исследования физико-механических свойств и структуры материала обработанной поверхности, а также сравнительные испытания на износостойкость гильз цилиндров, обработанных анодно-механическим и абразивным хонингованием.
5.Внедрить результаты исследований в производство и провести оценку их технико-экономической эффективности.
Во второй главе рассмотрены теоретические предпосылки для анодно-механического хонингования с целью увеличения износостойкости обработанной поверхности.
Предлагается применить металлические хонинговальные бруски из меди, латуни, стали или чугуна, что позволит использовать не только электрохимическую, но и электроэрозионную составляющие процесса АМО, и исключить шаржирование поверхности. Применение электрод-инструмента (ЭИ) из меди или латуни также позволит нанести антифрикционный слой.
Как известно, при анодно-механической обработке съем металла происходит за счет электроэрозионных и электрохимических явлений. В любом режиме в межэлектродном промежутке протекают соответствующие электрохимические процессы, поскольку рабочей жидкостью является электролит. Электрические разряды, возникающие между электродами и обусловливающие электроэрозию, можно рассматривать как отдельные источники тепла быстродвижущиеся по поверхности электрода-заготовки. При этом тепло распространяется вглубь металла по законам теплопроводности. Глубина проникновения тепла будет зависеть от мощности электрического разряда, скорости движения электродов, свойств окружающей среды и т.д. Вокруг быстродвижущейся точки образуются температурные зоны сферической формы. В той зоне, где нагрев достигает температуры плавления и выше, металл плавится частично испаряется и, удаляясь потоком рабочей жидкости и электрод-инструментом, образует лунки. В последующих нижележащих зонах происходит изменение структуры. В зоне, где температура достигает температуры закалки и выше появляется так называемый «белый» слой, который характеризуется низкой травимостью, высокой твердостью и износостойкостью. Используя эти свойства «белого» слоя, можно повысить ресурс гильз цилиндров.
Образовавшиеся на обработанной поверхности эрозионные лунки удерживают частички смазочного материала, тем самым, повышая маслоемкость и, как следствие, износостойкость поверхности.
Частное решение дифференциального уравнения теплопроводности для нашего случая (быстродвижущегося точечного источника тепла) которое выражает величину температуры на различных расстояниях от теплового источника и можно определить из известной формулы:
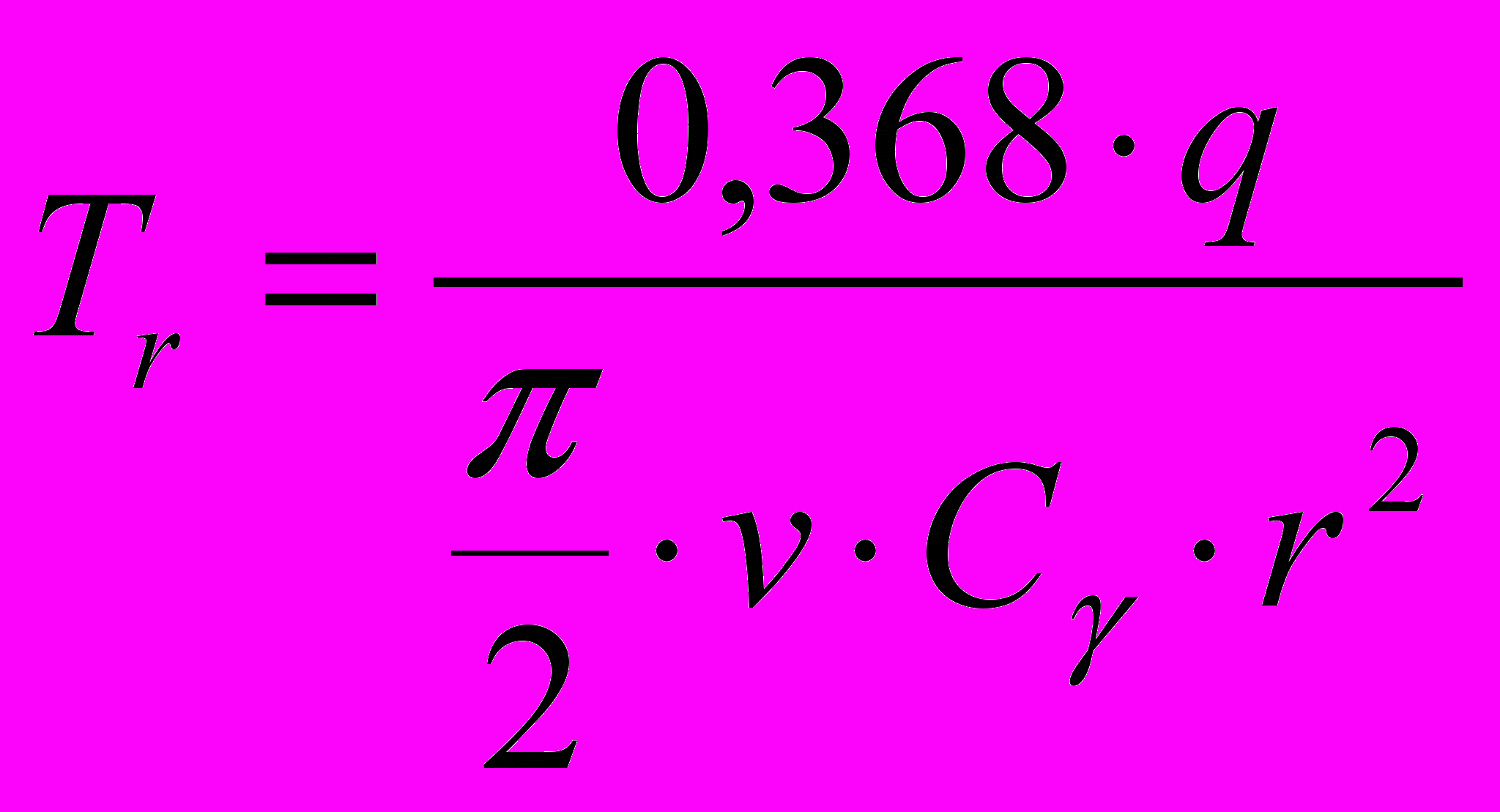
где Tr – максимальная температура на удалении r от теплоисточника, °С;
q - интенсивность точечного теплоисточника, кал/с; v - скорость движения теплоисточника, м/с; Cγ - объемная теплоемкость обрабатываемого металла, кал/м3 ·°С; r - радиус изотермической сферы, м.
Из равенства (1) можно определить радиус изотермической сферы r c
температурой Tr по формуле:
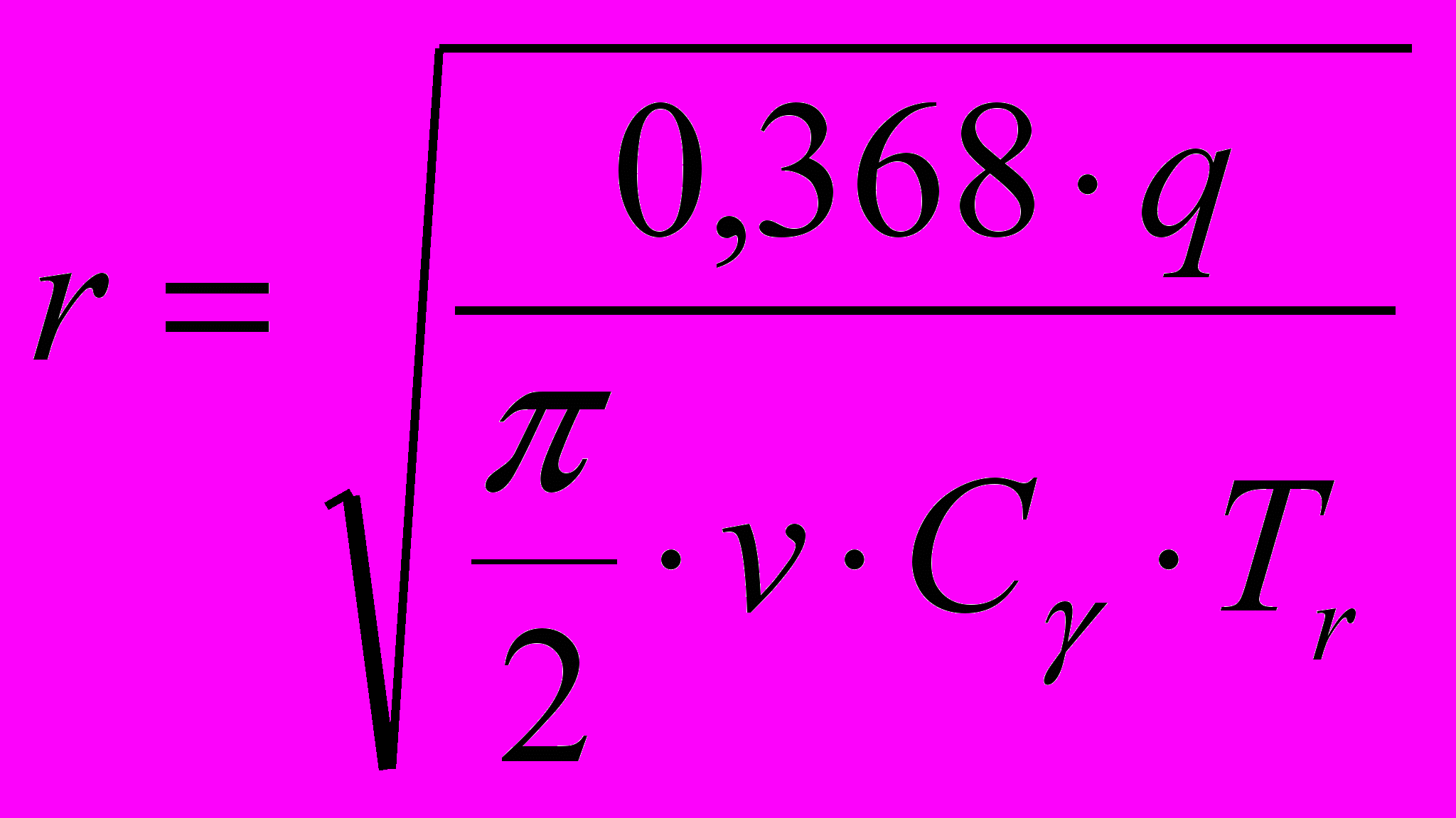
Интенсивность точечного теплоисточника (разряда) можно определить по формуле:
q = 0,24 · Ip ·Up , (3)
где Iр - величина рабочего тока, A;
Uр - величина рабочего напряжения, В;
Формула (2) подразумевает, что в единицу времени возникает один разряд на всей площади межэлектродном контакте. Однако в нашем случае хонинговальный брусок контактирует с поверхностью гильзы одновременно в нескольких точках и образуется так называемый «сеточный контакт» (рисунок 1). Поэтому необходимо учитывать общее количество точечных теплоисточников возникающих в контакте. При прочих равных условиях количество точек контакта будет увеличиваться с ростом удельного давления в контакте электродов и снижением плотности электролита. Следовательно, электрическую мощность, выделенную в контакте нужно разделить на число одновременно возникающих разрядов np.
Число одновременно возникающих разрядов np можно определить по формуле:
np = Np ·Fк , (4)
где Np – удельное число одновременных разрядов на единицу площади контакта, ед./ м2; Fк - площадь контакта электрод-инструмента с поверхностью детали в данный момент времени, м2.
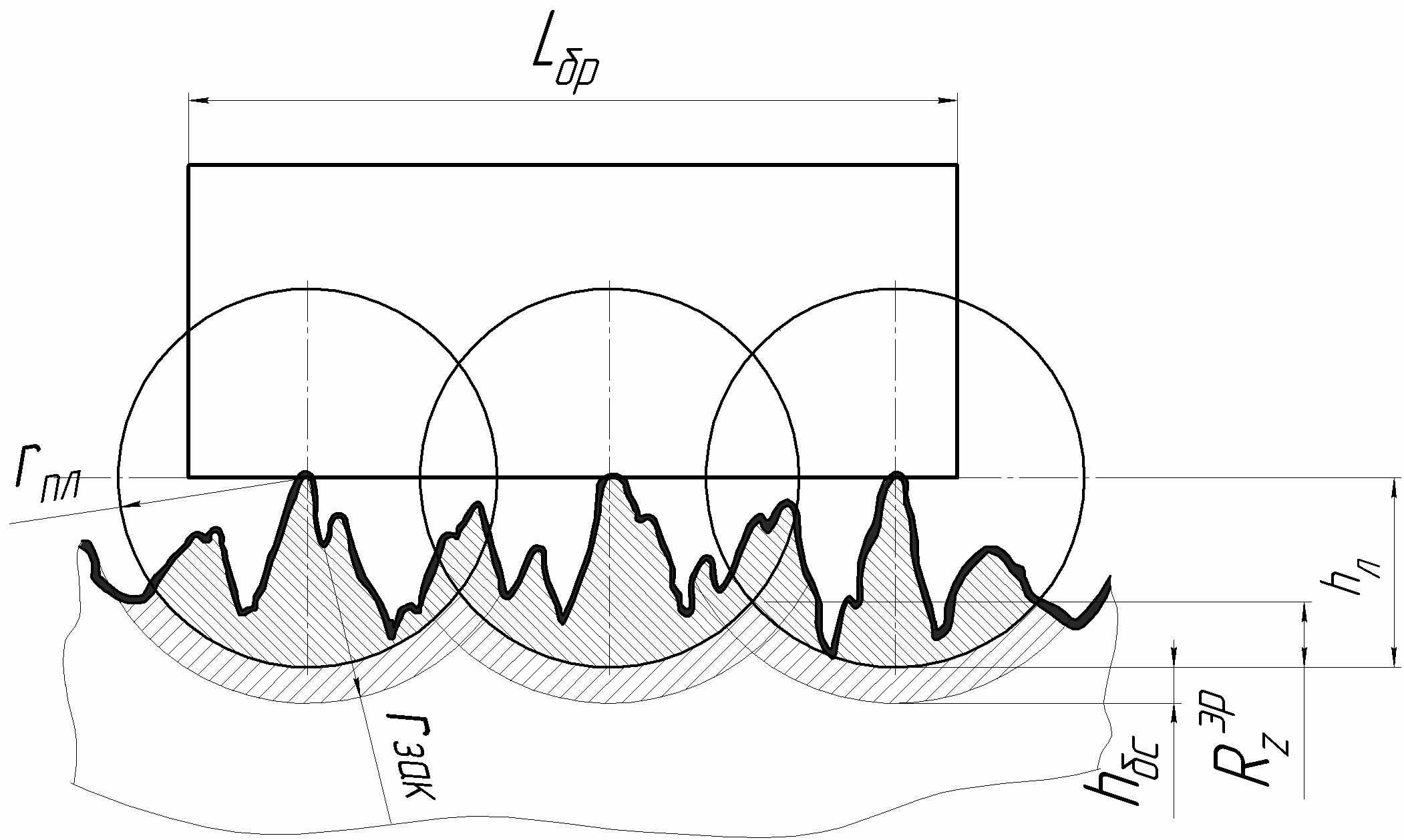
Рисунок 1- Схема контактирования электродов при АМХ.
Удельное число одновременных разрядов на единицу площади контакта Np можно определить опытным путем при изучении микроструктуры обработанной поверхности.
Тогда интенсивность точечного теплоисточника примет следующий вид:
q = 0,24 · Ip · Up/ Np ·Fк . (5)
Глубина образовавшейся лунки hл будет равна радиусу rпл изотермической сферы нагретой до температуры плавления Тпл (hл=rпл).
Высота неровности профиля поверхности
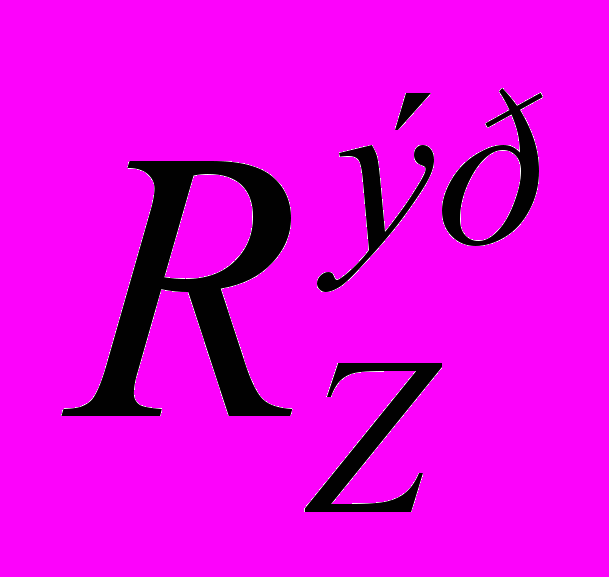
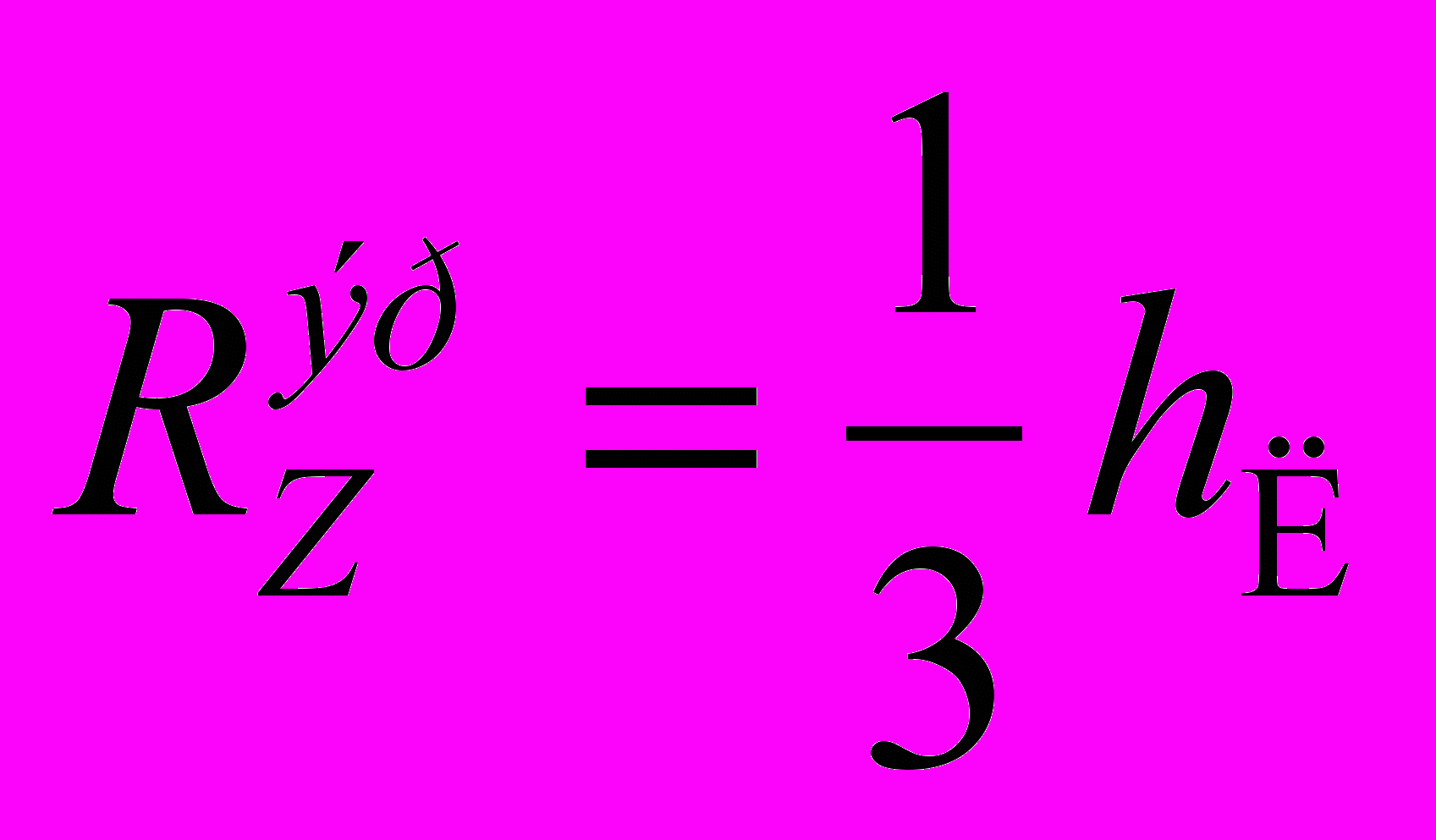
Подставляя выражения (2) и (5) в уравнение (5) получим:
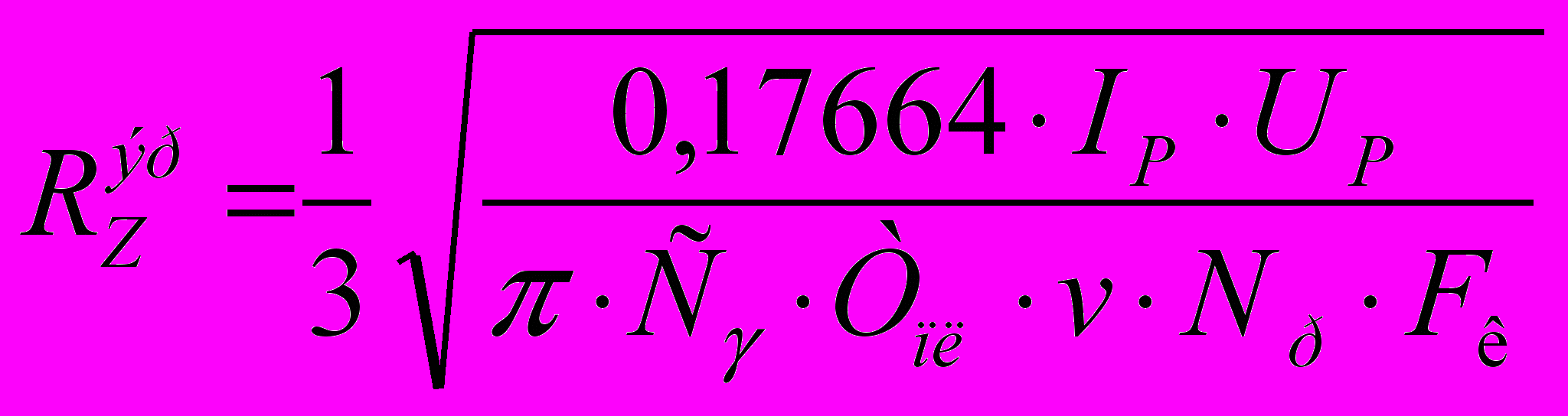
Как указывалось выше, при любом режиме происходит сглаживание поверхности детали за счет электрохимического растворения (рисунок 2). Растворение происходит основном в районе вершин сразу после образования эрозионной лунки в зоне А (рис.3). Электрохимическим растворением в зоне Б можно пренебречь так как поверхность покрывается анодной пленкой в зоне А.
![]() | ![]() |
1- обрабатываемая деталь; 2 – электролит; 3- анодная пленка; 4- брусок Рисунок 2 – Схема сглаживания поверхности при АМХ | 1- обрабатываемая деталь; 2 – брусок; 3- катодные пластины Рисунок 3 – Схематичное расположение брусков и катодных пластин |
Величину электрохимического съема
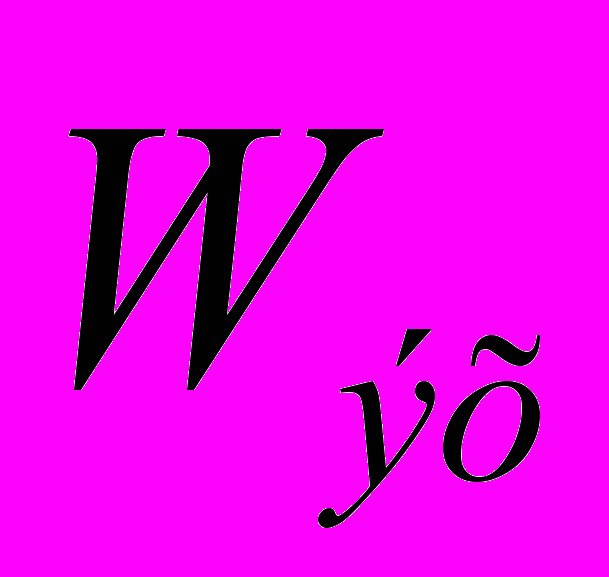
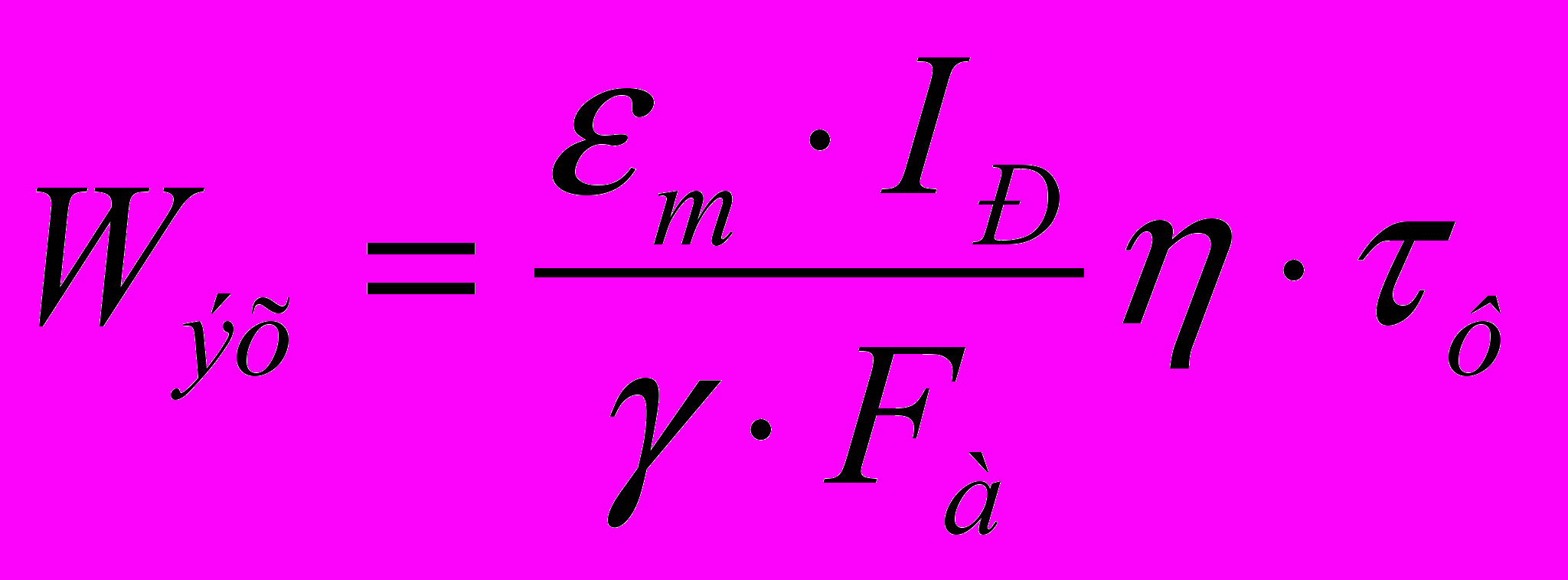
где
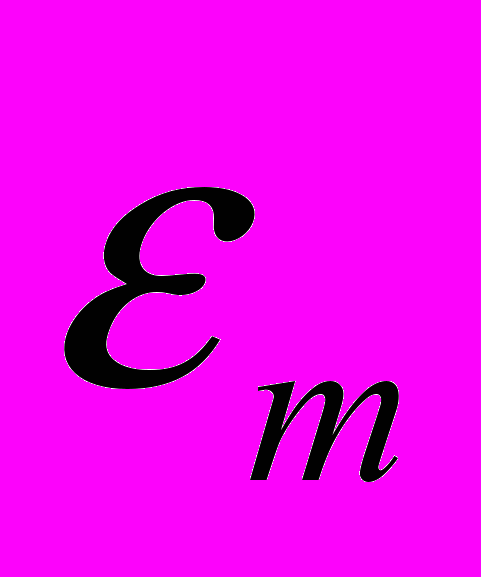
γ - плотность металла, кг/м3; Fа- площадь обрабатываемой поверхности анода-детали, м2; τф - время электрохимического растворения, с; η - выход по току.
Следовательно окончательная шероховатость будет равна:
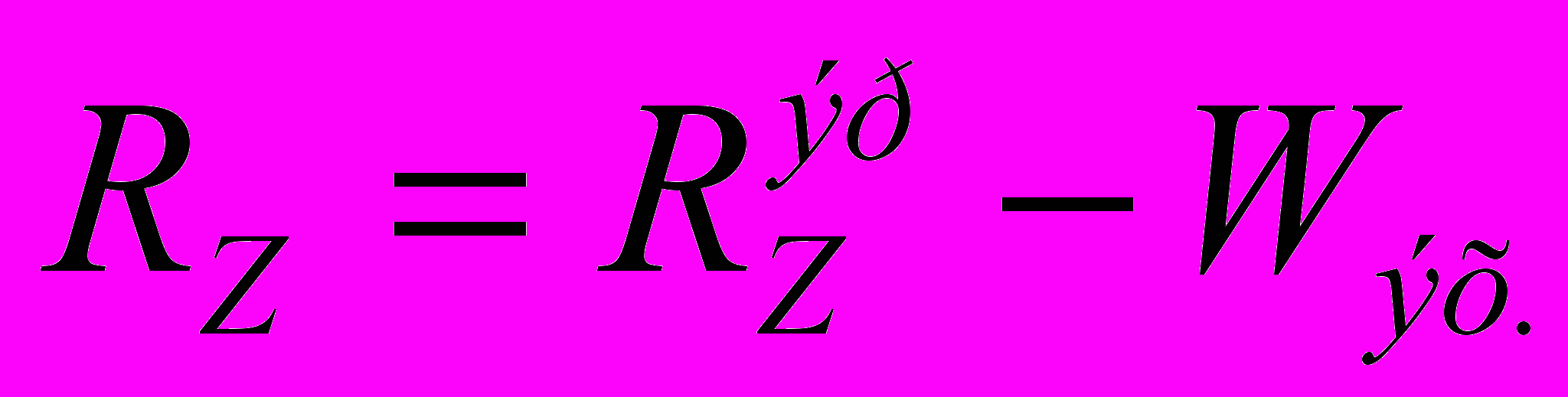
Тогда уравнение (9) с учетом выражений (7) и (8) примет вид:

Используя формулу (10) можно определить шероховатость поверхности после анодно-механического хонингования.
Высота шероховатости сильно влияет на прирабатываемость, износостойкость, маслоемкость поверхности и т.д. Зависимость износа от высоты шероховатости нелинейная и имеет вид, приведенный на рисунке 4. Поверхности со слишком малой высотой шероховатости вследствие чрезмерно большой площади контакта гладких поверхностей, и малой маслоемкости, главную роль при трении начинают играть явления адгезии и молекулярного сцепления, в результате чего образуются микрозадиры поверхностей.
![]() |
Рисунок 4 – Зависимость износа от высоты шероховатости |
В третьей главе приводится программа и методика экспериментальных исследований. Экспериментальные исследования АМХ проводились в два этапа. На первом этапе была создана лабораторная установка, реализующая процесс плоского хонингования. Образцы изготавливались из сегментов гильз цилиндров двигателя ЗМЗ-511.10 (серый чугун ИЧГ-33М). На втором этапе, на основании данных полученных при исследовании плоских образцов, проводилось хонингование целых гильз на вертикально-хонинговальном станке 3Б833, дополненным батареей выпрямителей ВСГ-3А, токоподводами и другой технологической оснасткой.
Исследования проводились с помощью квазирандомизационного метода планирования экспериментов, что дает возможность резко сократить количество необходимых опытов. Сначала проводилась основная серия для определения наиболее существенных факторов. Затем проводилась контрольная серия по изучению влияния только существенных факторов. Результаты экспериментов анализировались с помощью методов статистики. Задачей опытов было определить, как влияют отдельные факторы на среднюю высоту неровностей поверхности Rz и удельный съем металла М:
Rz=f(ρ, n, I, U , Р, Мэи), (11)
М= f(ρ, n, I, U , Р, Мэи). (12)
где ρ- плотность электролита; n - частота вращения ЭИ; I - сила тока;
U - напряжение; Р - удельное давление между электродами; Мэи - материал ЭИ.
В качестве рабочей жидкости использовались водные растворы жидкого стекла (ГОСТ 13078-81) плотностью 1,15, 1,22, 1,29, 1,36 г/см3 с добавлением глицерина. Изучение строения микроструктуры материала проводилось на микрошлифах с помощью металлографических микроскопов МИМ-7 и Эпиквант. Измерение шероховатости проводили на профилографе-профилометре Mitutoyo SJ-201P, который позволяет определять дополнительные характеристики шероховатости по зарубежным стандартам DIN EN ISO 4287:1998 и 13565-2:1998, в том числе и маслоемкость поверхности V0 , величину относительной опорной длины профиля на уровне сечения 50% - t50, уменьшенную высоту пика Rpk, основную глубину шероховатости Rk, уменьшенную глубину впадины Rvk и др. Лабораторные испытания на износостойкость проводили на машине трения 77МТ-1.
В четвертой главе приведены результаты экспериментальных исследований.
Как показывают результаты основной серии опытов наиболее существенными факторами являются напряжение и сила тока. С ростом напряжения и силы тока значительно увеличивается толщина белого слоя, шероховатость и производительность обработки. Сильное влияние этих факторов можно объяснить повышением плотности тока в межэлектродном контакте и, как следствие, ростом мощности отдельных разрядов. Плотность электролита, частота вращения и материал инструмента не являются существенными факторами. При проведении анодно-механического хонингования необходимо использовать брусковые ЭИ из меди или медьсодержащих сплавов. Износ таких инструментов в 5…7 раз меньше, чем стальных или чугунных и их применение позволяет нанести на обрабатываемую поверхность антифрикционный слой. Удельное давление в контакте между электродами также не сильно влияет на оценочные показатели. Однако от этого фактора сильно зависят рабочие значения тока и напряжения. Рациональные значения удельного давления находятся в пределах 0,1...0,15 МПа.
Для определения количества электрических разрядов Np возникающих на единице площади контакта (формула 4) необходимо измерить радиус плавления на микрошлифах (рисунок 5) и вычислив количество разрядов по следующей формуле:
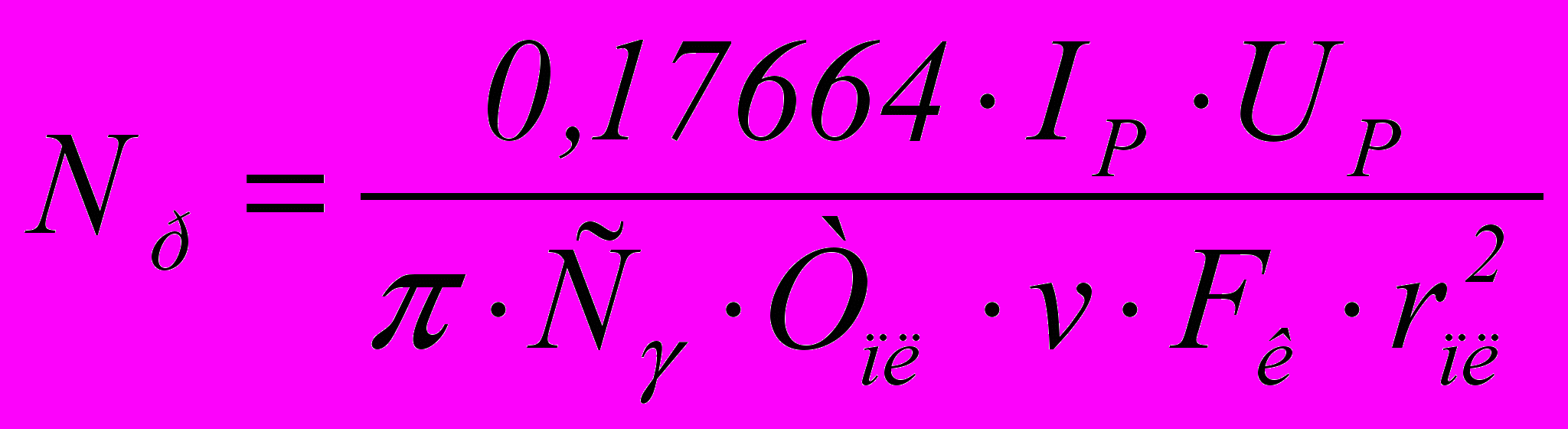
Радиус плавления определялся с помощью программы КОМПАС с учетом масштаба изображения микрошлифа.
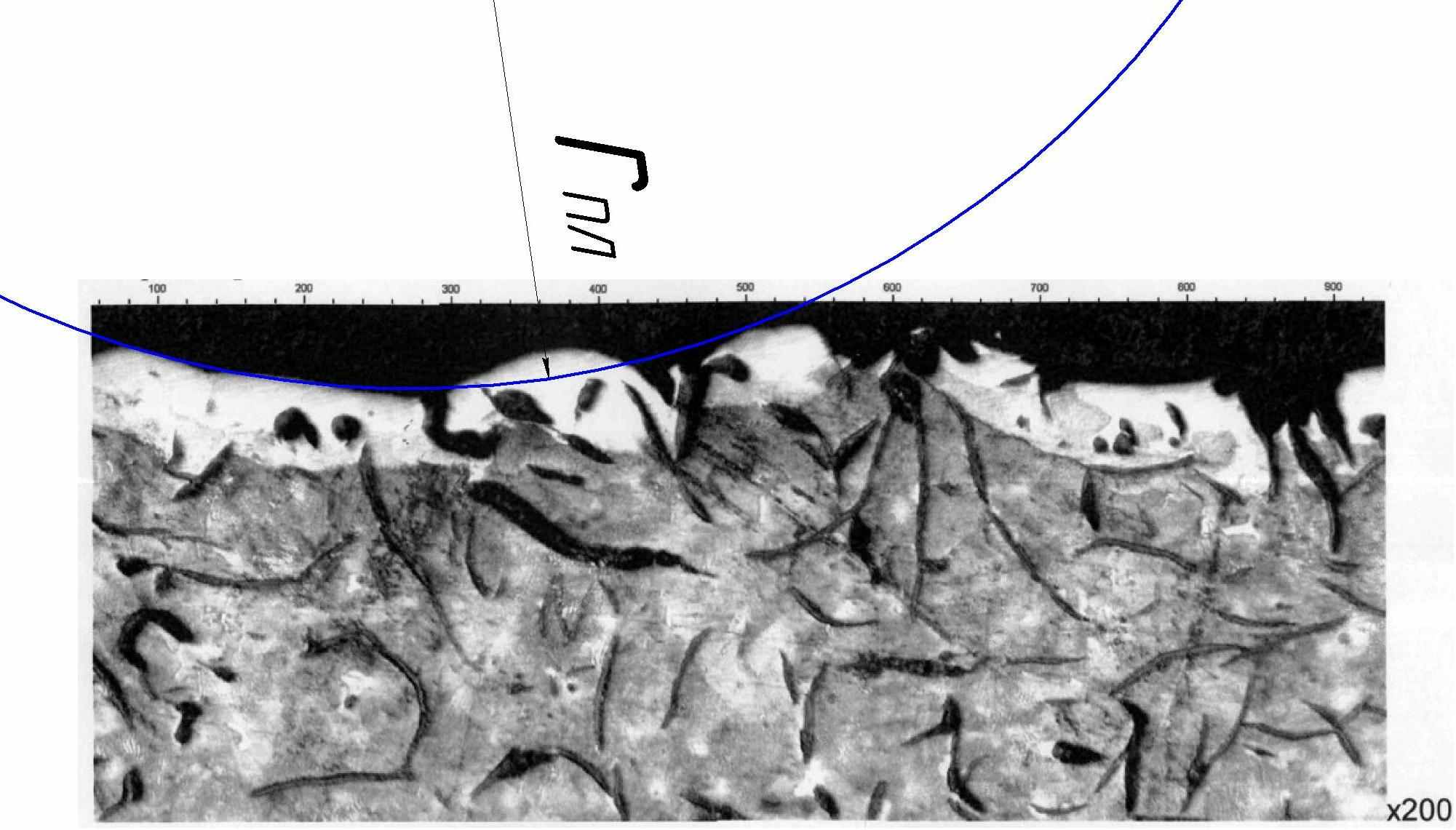
Рисунок 5 – Схема для определения радиуса плавления.
После статистической обработки получена следующая эмпирическая
зависимость удельного количества разрядов от плотности электролита ρ и удельного давления в контакте Р :
Np=3,09+61,79·P+33,33·P2 - 6,95·ρ+3,74·ρ2- 49,28· ρ·P. (14)
Исследование микротвердости поверхностного слоя показало ее увеличение до 680 МПа при исходном значении 215…250 МПа, т.е. увеличение в 2,7…3,1 раза. Однако «белый» слой имеет неравномерную толщину и сплошность, а также изобилует порами и трещинами, что связанно с перегревом металла и быстрым его охлаждением (рисунок 6).
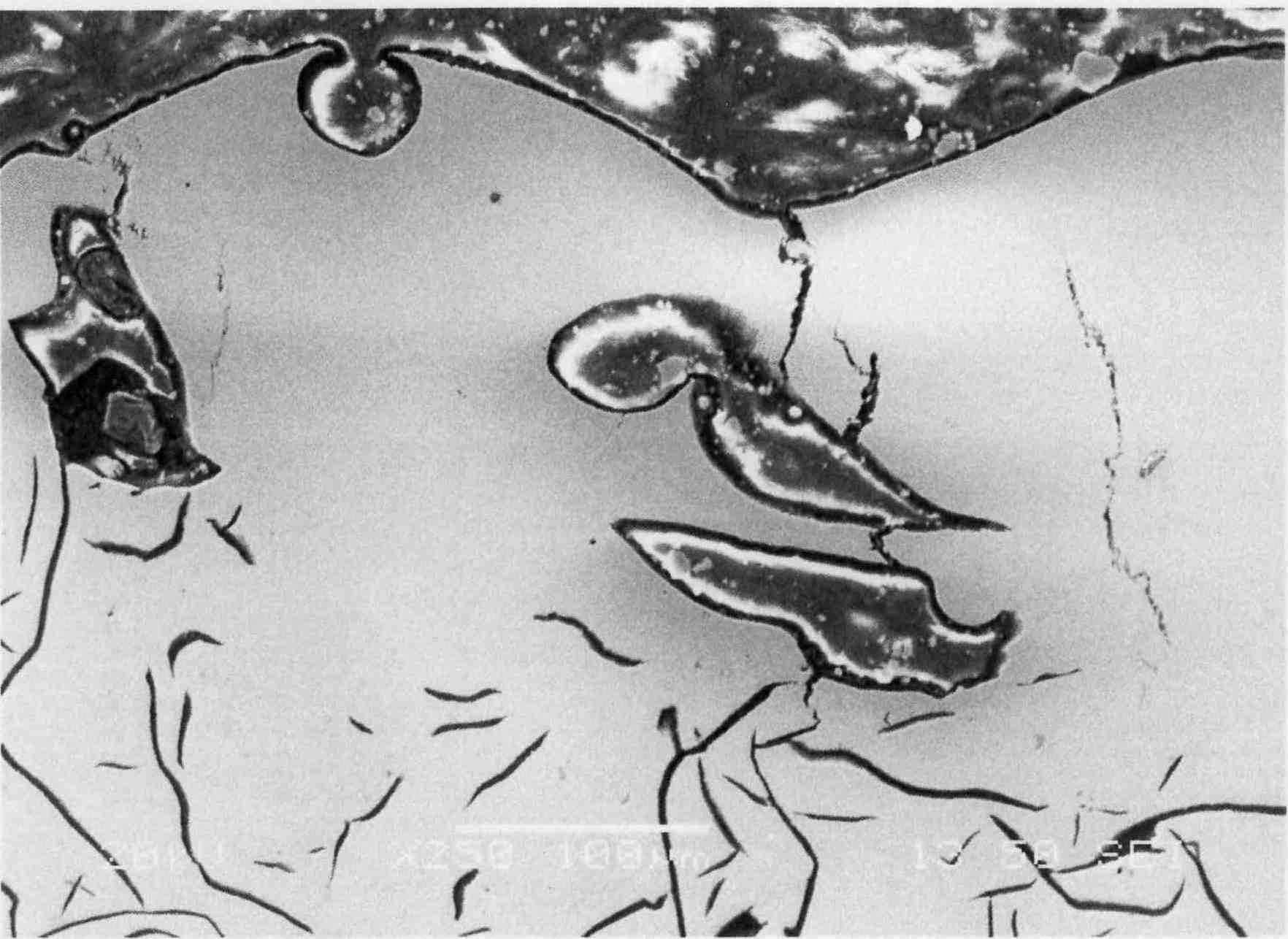
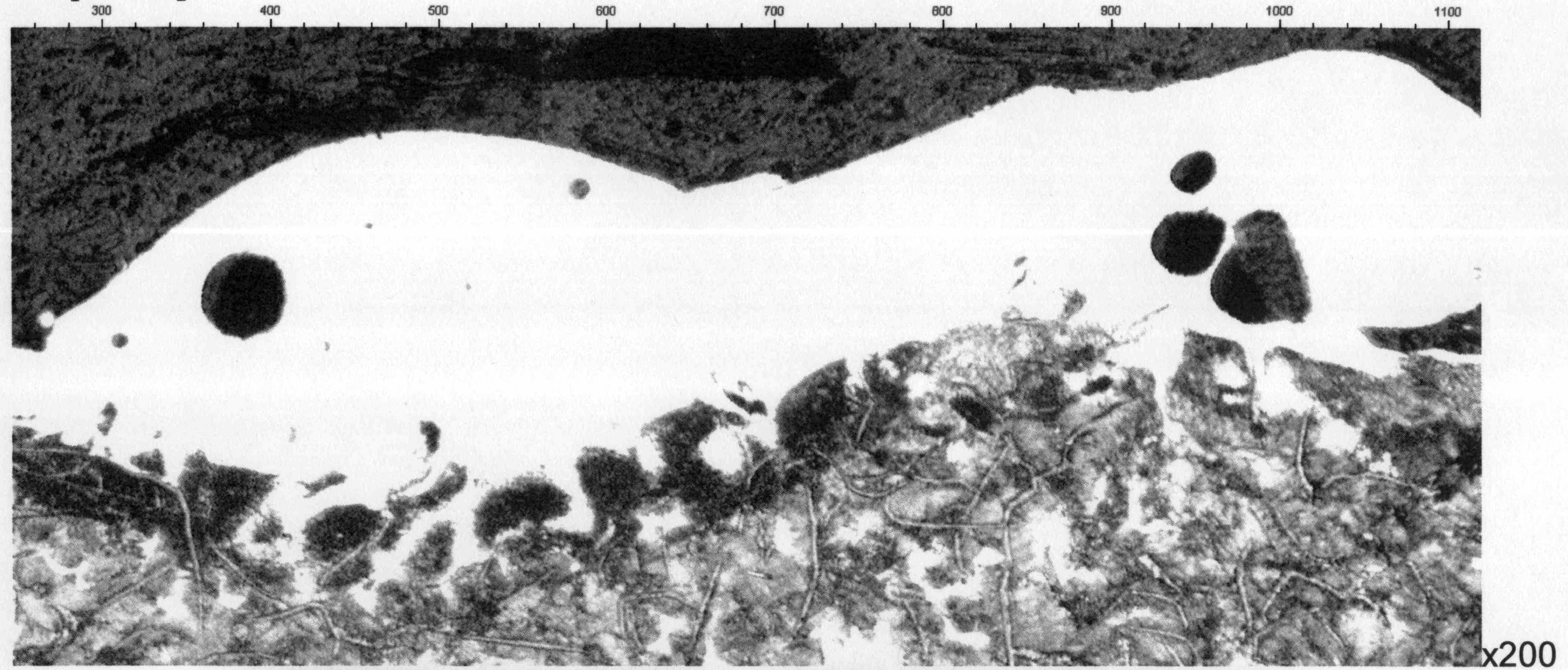
а) увеличение ×250 б) увеличение ×200
Рисунок 6 – Поверхность микрошлифов.
Вышесказанное позволяет сделать вывод, что получение «белого» слоя на гильзе цилиндров анодно-механическим методом нецелесообразно. Поэтому при проведении дальнейших исследований было решено проводить анодно-механическое хонингование на режимах не допускающих появления толстого «белого» слоя. В этом случае повышение износостойкости достигается образованием микрорельефа с повышенной маслоемкостью и действием антифрикционного покрытия.
Перед обработкой АМХ гильзы растачивались на станке 278Н резцами с пластинами ВК3 при подаче 0,125 мм/об, частоте вращения 315мин-1.
Числовые значения показателей шероховатости полученных с помощью профилометра Mitutoyo SJ-201P приведены в таблице 1.
Таблица 1 – Значения показателей шероховатости поверхностей
Наимено- вание показателя | Ед. измер. | Вид обработки | |||
расточка | абразивное хонинго-вание | плоско-вершинное хонинго-вание | АМХ | ||
Ra | мкм | 6,96…7,68 | 0,18…0,32 | 0,30…0,57 | 2,52…2,81 |
Rz | мкм | 38,15..67,31 | 1,98…3,14 | 2,81…5,04 | 15,76…30,29 |
t50 | % | 23…40 | 3…45 | 87…95 | 89…92 |
Rpk | мкм | 8,19…11,92 | 0,30…0,44 | 0,23…0,40 | 1,48…1, 52 |
Rvk | мкм | 4,37…9,31 | 0,14…0,61 | 1,03…2,31 | 14,31…17,97 |
Rk | мкм | 23,64…26,32 | 0,48…1,21 | 0,74…1,51 | 8,80…10,69 |
Vo | мм3/см2 | 0,012…0,027 | 0,001…0,004 | 0,016…0,024 | 0,042…0,105 |
Анализ данных таблицы 1 показывает, что двукратное АМХ позволяет получить плосковершинную поверхность с наибольшей маслоемкостью Vo порядка 0,042…0,105 мм3/см2, что в 2…4 раз выше чем после плосковершинного хонингования при практически одинаковой опорной длине профиля поверхности. Профилограммы поверхностей обработанных разными способами приведены на рисунке 7.
![]() | ![]() |
а) после расточки | б) после абразивного хонингования |
![]() | ![]() |
в) после плосковершинного хонингования | г) микропрофиль поверхности после АМХ |
Рисунок 7 - Профилограммы поверхности после различных видов обработки. |
Как видно из рисунка 7 микропрофиль поверхностей после плосковершинного хонингования (ПВХ) и АМХ представляет собой чередование относительно плоских участков и впадин для удержания смазочного материала. Такой профиль сходен с профилем, образовавшимся в ходе эксплуатации. При этом глубина впадин у поверхностей после АМХ больше, чем после абразивного хонингования и, соответственно, больше маслоемкость.
Исследования процесса анодно-механического хонингования, проведенные на целых гильзах цилиндров ЗМЗ-511.10 показали следующее. Для АМХ наиболее подходящим электролитом является водный раствор жидкого стекла плотностью 1,15…1,22 кг/м3 с добавлением 15…20% глицерина и 3…5% хлористого натрия. Рациональные значения удельного давления находятся в пределах 0,1...0,15 МПа. Наиболее рациональные режимы обработки: чистовой – напряжение 16…18В, плотность тока на электрод-инструменте 5…7А/см2; доводочной – напряжение 10…12В, плотность тока 0,5…1А/см2. Нанесение антифрикционного слоя необходимо проводить по окончании доводочной стадии обработки при отключенном технологическом токе в течение 10…15 секунд. За это время с поверхности зеркала гильзы удаляется анодная пленка и наносится медьсодержащий слой. При использовании ЭИ в виде роликов относительный износ уменьшается.
На основании математической обработки контрольной серии опытов по обработке гильз цилиндров получены следующие зависимости:
Rz== -2,93 +0,56·Up -0,0122·Uр2 +0,07·Iр -0,00023·Iр2 +0,00303Uр·Iр (13)
М= 0,14 -0,0039· Up +0,00073·Uр2-1,26·10-4 ·Iр -1,9·10-6 ·Iр2 ++1,154·10-4 Uр·Iр, (14)
Поверхности, выражающие экспериментальные зависимости шероховатости Rz и удельного съема металла М от силы тока Iр и напряжения Uр, представлены на рисунках 9и 8.
![]() | ![]() |
Рисунок 8-Зависимость шероховатости Rz от тока и напряжения | Рисунок 9-Зависимость удельного съема металла М от тока и напряжения |
Сравнительные испытания на износостойкость гильз с различной высотой шероховатости обработанных АМХ позволил выявить зависимость износа от Rz (рисунок 10) , которая имеет оптимум при 15…30 мкм.
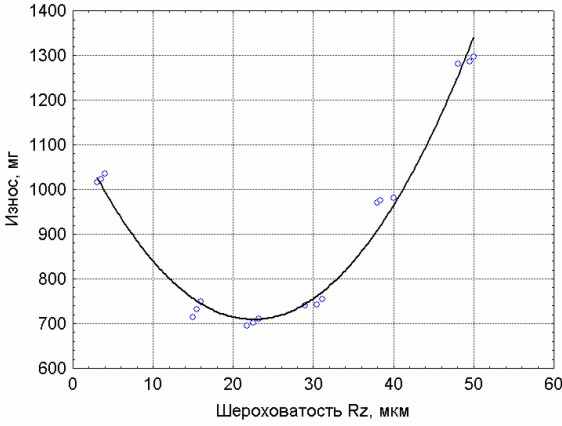
Рисунок 10 - Зависимость износа образцов от начальной высоты шероховатости.
Лабораторные испытания на износостойкость показали, что образцы после АМХ имеют больший приработочный износ т.к. высота пиков у них выше (рисунок 11а). В тоже время угол наклона β прямолинейного участка кривой износа у них меньше, чем после алмазного хонингования. Если принять время работы двигателя до ремонта 4000 ч, то износ зеркала гильзы обработанной АМХ получится меньше на 22…25% износа зеркала после абразивного хонингования U2
![]() | ![]() |
а) | б) |
а) износ после 25 испытаний; б) расчетная схема износа после 4000 часов работы двигателя; 1- абразивное хонингование; 2 – АМХ с нанесением антифрикционного покрытия; 3- АМХ без нанесения антифрикционного покрытия. | |
Рисунок 11– Зависимость износа образцов от способа хонингования. |
По окончании испытаний на износ с поверхностей трения были сняты профилограммы (рисунок 12).
![]() | ![]() |
а) | б) |
а) микропрофиль поверхности после АМХ | б) микропрофиль поверхности после ПВХ |
Рисунок 12 - Микропрофили поверхности после 25 часовых испытаний на износ.
Как видно из рисунка 12 после испытаний поверхность приобретает плосковершинный профиль с гораздо большими лунками для смазки, чем после абразивного хонингования.
Эксплуатационные испытания проводились на двигателях ЗМЗ-511.10, восстановленных в условиях НПО «Агросервис» г. Казань и Бугульминского ПАТП. После пробега в 60 тыс. км были выполнены контрольная разборка и замеры диаметров и шероховатости поверхности гильз цилиндров. Эксплуатационные испытания двигателей ЗМЗ–511.10 показали, что среднее значение износа гильз после АМХ на 20…25 % меньше износа серийных гильз. Расход моторного масла двигателя с опытными гильзами находился в пределах нормы.
В пятой главе разработана технология АМХ и приведены результаты технико-экономической оценки предлагаемой технологии. Как показывают расчеты внедрение анодно-механического хонингования позволит получить экономический эффект в размере 92436,3 руб. при программе 750 двигателей в ценах 2010 года.
ОБЩИЕ ВЫВОДЫ И РЕКОМЕНДАЦИИ
На основании выполненных теоретических и экспериментальных исследований можно сделать следующие основные выводы:
1. Анализ литературных источников показал, что в имеющихся работах исследовался процесс съема металла электрохимическим растворением с последующим удалением продуктов растворения абразивной обработкой. Применение же анодно-механической обработки гильз цилиндров с электроэрозионной составляющей освещено слабо.
2. Наиболее существенными факторами являются напряжение и сила тока. С ростом напряжения и силы тока значительно увеличивается толщина белого слоя, шероховатость и производительность обработки. Сильное влияние этих факторов можно объяснить и, как следствие, ростом мощности отдельных разрядов. Плотность электролита, частота вращения и материал инструмента не являются существенными факторами. Для АМХ наиболее подходящим электролитом является водный раствор жидкого стекла плотностью 1,15…1,22 кг/м3 с добавлением 15…20% глицерина и 3…5% хлористого натрия. Удельное давление в контакте между электродами также не сильно влияет на оценочные показатели, рациональные значения удельного давления находятся в пределах 0,1...0,15 МПа. Наиболее рациональные режимы обработки: чистовой режим – напряжение 16…18В, плотность тока на электрод-инструменте 5…7 А/см2; доводочный – напряжение 10…12В, плотность тока 0,5…1А/см2. Нанесение антифрикционного слоя необходимо проводить по окончании доводочной стадии обработки при отключенном технологическом токе в течение 10…15 секунд. За это время с поверхности зеркала гильзы удаляется анодная пленка и наносится медьсодержащий слой.
3. Предлагается использовать металлические электрод-инструменты в виде брусков и роликов. Это позволит использовать не только электрохимическую, но и электроэрозионную составляющую процесса АМО, получить износостойкий микрорельеф поверхности с повышенной маслоемкостью, исключить шаржирование поверхности. При проведении анодно-механического хонингования необходимо использовать бруски-электроды из меди или медьсодержащих сплавов. Износ таких электрод-инструментов ниже, чем стальных или чугунных и их применение также позволяет нанести на обрабатываемую поверхность антифрикционный слой.
4. Проведенные теоретические исследования позволили получить математическую модель, характеризующую зависимость шероховатости поверхности от электрических и механических параметров обработки.
5. Исследования физико-механических свойств показали увеличение микротвердости «белого» слоя до 680 МПа при исходном значении 215…250 МПа, т.е. увеличение в 2,7…3,1 раза. Однако «белый» слой имеет неравномерную толщину и сплошность, а также изобилует порами и трещинами. Поэтому получение «белого» слоя анодно-механическим методом оказалось нецелесообразно. Обработку гильз цилиндров следует проводить на режимах, допускающих появления «белого» слоя небольшой толщины. Лабораторные и эксплуатационные испытания показали, что износостойкость поверхности гильз цилиндров обработанной АМХ на 20…22% выше износостойкости поверхности после алмазного хонингования. Время приработки поверхности также сократилось.
6. На основе выполненных исследовании разработана технология анодно-механического хонингования, а также хонинговальные головки с металлическими брусковыми (свидетельство на ПМ № 23586) и роликовыми ЭИ (патент № 2242338), которые внедрены в НПО «Агросервис» (г. Казань) и Бугульминском ПАТП. Результаты научных исследований используются в учебном процессе ФГОУ ВПО «Казанский ГАУ». Экономический эффект от внедрения технологии АМХ составляет 92436,3 руб. при программе 750 двигателей в год.
ОСНОВНЫЕ ПОЛОЖЕНИЯ ДИССЕРТАЦИИ ОПУБЛИКОВАНЫ В СЛЕДУЮЩИХ РАБОТАХ:
В журналах, рекомендуемых ВАК:
1. Шайхутдинов, Р.Р. Результаты лабораторных исследований по упрочнению гильз цилиндров двигателей внутреннего сгорания [Текст] / Р.Р. Шайхутдинов, X.С. Фасхутдинов, М.Х. Фасхутдинов // Технический сервис в агропромышленном комплексе: вестник ФГОУ ВПО МГАУ. – Вып. 1. – М.: МГАУ, 2003. – С. 147-151.
2. Шайхутдинов, Р.Р. Методы повышения маслоемкости поверхности трения гильз цилиндров [Текст] / Р.Р. Шайхутдинов, X.С. Фасхутдинов, М.Х. Фасхутдинов // Вестник Казанского ГАУ,2010. – Вып. 2 (16). – С. 110-111.
В материалах международных, всероссийских конференций и других изданий:
3.Шайхутдинов, Р.Р. Возможности электрофизических и электрохимических способов при восстановлении деталей [Текст] / Р.Р. Шайхутдинов, X.С. Фасхутдинов // Сб. научных трудов Казанской ГСХА. – Казань: Изд-во КГСХА, 1998. – С. 90-92.
4.Шайхутдинов, Р.Р. Трудоемкость упрочняющего анодно-механического хонингования гильз цилиндров автотракторных двигателей [Текст] / Р.Р. Шайхутдинов, X.С. Фасхутдинов // Проблемы механизации сельского хозяйства: юбил. сб. науч. трудов ученых КГСХА. – Казань: Изд-во КГСХА, 2000. – С. 297-301.
5.Шайхутдинов, Р.Р. Методика проведения экспериментальных при анодно-механическом хонинговании гильз цилиндров ДВС [Текст] / Р.Р. Шайхутдинов, X.С. Фасхутдинов // Проблемы механизации сельского хозяйства: юбил. сб. науч. трудов ученых КГСХА. – Казань: Изд-во КГСХА, 2000. – С. 310-312.
6.Шайхутдинов, Р.Р. Теоретические основы обеспечения износостойкости гильз цилиндров при анодно-механическом хонинговании [Текст] / Р.Р. Шайхутдинов, X.С. Фасхутдинов // Проблемы механизации сельского хозяйства: юбил. сб. науч. трудов ученых КГСХА. – Казань: Изд-во КГСХА, 2000. – С. 312-315.
7.Шайхутдинов Р.Р., Фасхутдинов X.С. Исследование новой технологии хонингования при ремонте автотракторных двигателей [Текст] / Р.Р. Шайхутдинов, X.С. Фасхутдинов//Нива Татарстана. –2000. – №5-6.-С. 39.
8. Шайхутдинов, Р.Р. О результатах исследований упрочнения гильз цилиндров анодно-механическим способом [Текст] / Р.Р. Шайхутдинов, X.С. Фасхутдинов, М.Х. Фасхутдинов //Труды Казанской ГСХА. – Казань: Изд-во КГСХА, 2001. – Т. 70. – С.154-156
9.Шайхутдинов, Р.Р. Комбинированная обработка гильз цилиндров автотракторных двигателей [Текст] / Р.Р. Шайхутдинов, X.С. Фасхутдинов, Р.А. Андреев // Проблемы механизации сельского хозяйства: сб. науч. трудов КГСХА. – Казань, 2002. – С. 343-344.
10. Шайхутдинов, Р.Р. Влияние плотности электролита на процесс анодно-механической обработки гильз цилиндров двигателей [Текст] / Р.Р. Шайхутдинов, X.С. Фасхутдинов // Сб. науч. трудов междунар. науч.-практич. конференции, посвященной 75-летию В.И.Медведеву. ФГОУ «Чувашская ГСХА». – Чебоксары, 2003 г. – С. 135-136.
11. Шайхутдинов, Р.Р. Инструмент для анодно-механического хонингования [Текст] / Р.Р. Шайхутдинов, X.С. Фасхутдинов // Проблемы механизации сельского хозяйства: сб. науч. трудов КГСХА. – Казань, 2004 – С. 243-244.
12. Шайхутдинов, Р.Р. Анодно-механическая обработка гильз цилиндров ДВС [Текст] / Р.Р. Шайхутдинов, X.С. Фасхутдинов // Сб. науч. трудов IV междунар. науч.-практич. конференции «Автомобиль и техносфера» (ICATS, 14-16 июня 2005). – Казань, 2005 г. – С.265-266.
13. Шайхутдинов, Р.Р. О способах подвода тока при анодно-механической обработке цилиндров [Текст] / Р.Р. Шайхутдинов, X.С. Фасхутдинов, А.Н. Хисамутдинов // Труды инженерных факультетов Казанского ГАУ, посвященные 55-летию ФМСХ: Материалы науч. конференции ППС и аспирантов факультетов МСХ и ТС. –Казань: Изд-во Казанского ГАУ, 2006. – Т. 73. - с.151-154.
14. Свидетельство на полезную модель № 23586 RU U1 МПК7 В 23Н 5/06. [Текст] / Шайхутдинов P.P., Андреев Р.А., Фасхутдинов Х.С., Фасхутдинов М.Х. – 2001125573/20; заявл. 20.09.2001; опубл. 27.06.2002, Бюл. № 18.
15. Патент №2242337 RU C2 МПК7 В 23Н 5/06. Способ анодно-механи-ческого хонингования [Текст] / Р.Р. Шайхутдинов, Фасхутдинов X.С, Андреев Р.А., Фасхутдинов М.Х. – №2002124508/02; заявл. 13.09.2002; опубл. 20.12.2004, Бюл. № 35.
16. Патент № 2242338 RU C2 МПК7 B23H 5/06, С 23 С 26/00. Головка для анодно-механического хонингования [Текст] / Р.Р. Шайхутдинов, Фасхутдинов X.С, Андреев Р.А., Фасхутдинов М.Х. – №20021245509/02; заявл. 13.09.2002; опубл. 20.12.2004, Бюл. № 35.