IV. обесфеноливание сточных вод
Вид материала | Лекция |
- Методы очистки сточных вод, 28.89kb.
- Охрана производственных сточных вод и утилизация осадков, 327.09kb.
- Контроль различных форм азота в процессе очистки сточных вод, 76.68kb.
- Очистка сточных вод, 34.57kb.
- Вопросы к зачету по дисциплине «Водоотведение и очистка сточных вод» для специальности, 19.74kb.
- Реферат установка для очистки сточных вод, 11.06kb.
- Ном переработка сбросов и бытовых и промышленных отходов в г. Москве, 167.96kb.
- Физико-химические методы очистки сточных вод с применением коагулянтов1, 44.5kb.
- Математическая модель процесса адсорбции при очистке сточных вод тэс от нефтепродуктов, 99.07kb.
- Рабочая программа по курсу "Очистка городских сточных вод", 207.77kb.
ЛЕКЦИЯ 3
IV. ОБЕСФЕНОЛИВАНИЕ СТОЧНЫХ ВОД
4.3. Технология парового метода обесфеноливания сточных вод
Паровой метод обесфеноливания сточных вод в сочетании с мокрым тушением кокса и замкнутым циклом фенольных вод или с биологической доочисткой получил на отечественных коксохимически заводах широкое распространение. Обесфеноливающая установка предназначена для удаления основной части фенолов из надсмольной воды и сепараторной воды смолоперегонного цеха (при наличии этого цеха на заводе), прошедшей обработку в аммиачной колонне, с получением фенолятов установленного качества в соответствии с требованиями технических условий. Степень обесфеноливания сточных вод на установке должна быть не менее 85%, остаточное содержание фенолов в обработанной воде должно составлять не более 0,2 г/л.
Сущность этого метода заключается в том, что из сточной воды, нагретой до 100–102°С, фенолы выдуваются большим количеством острого водяного пара, а затем смесь пара и фенолов пропускают через нагретый до 102–103°С поглотительный раствор щелочи, который взаимодействует с фенолами с образованием фенолятов.
Основным аппаратом паровой установки является обесфеноливающий скруббер, состоящий из верхней испарительной части с деревянной хордовой насадкой, в которой из воды выдуваются фенолы, и нижней поглотительной части, имеющей металлическую спиральную насадку, в которой из пара раствором едкого натра фенолы и крезолы связываются в феноляты и крезоляты натрия по уравнениям:
С5Н6ОН + NaOH C6H5ONa +Н2О;
C6H4(CH3)OH + NaOH C6H4(CH3)ONa + H2O
(в малом количестве образуются крезолиты и другие соли натрия). Эта смесь фенолят и крезолят называется фенолятами.
Очищенный водяной пар снова используется для обесфеноливания воды в верхней части скруббера, т.е. находится в замкнутом цикле.
Следовательно, в обесфеноливающем скруббере сочетаются два процесса: десорбция фенолов из воды в пар и абсорбция (хемосорбция) фенолов из пара ще-лочно-фенолятным раствором. Сочетание двух процессов в одном аппарате позволяет многократно использовать регенерированный (обесфеноленный) водяной пар для десорбции (отгонки) фенолов из сточной воды, а щелочной раствор для получения продукта заданного качества. Водяной пар циркулирует по схеме: десорбция фенолов из воды – абсорбция фенолов из пара щелочью – десорбция фенолов из воды. Процесс десорбции фенолов из сточной воды циркулирующим водяным паром и адсорбция фенолов из циркулирующего пара раствором щелочи влияют один на другой и каждый из них в свою очередь зависит от многих факторов.
Достоинства парового метода состоят в компактности установки, простоте аппаратурного оформления, возможности автоматизации процесса; в процессе обесфеноливания вода не соприкасается с реагентами, при повышенном расходе щелочи наличие многоступенчатого орошения позволяет применить паровой метод для обесфеноливания сточных вод с содержанием фенолов менее 1,5 г/л; образующиеся фенолята не содержат механических примесей, по необходимости установка может работать с перегрузкой.
Однако паровой метод имеет и существенные недостатки: невозможно достигнуть полного обесфеноливания сточной воды; часть фенолов теряется в дистилляционной аммиачной колонне перед обесфеноливанием воды, потери фенолов могут достигать 15–25% от их ресурсов в воде. Наличие остатков аммиака перед обесфеноливанием снижает степень обесфеноливания воды.
Полученные паровым методом обесфеноливания сточных вод фенолята натрия перерабатываются для получения чистых продуктов путем ректификации.
4.4. Технология экстракционных методов обесфеноливания
сточных вод
Экстракционные методы обесфеноливания сточных вод пригодны для извлечения фенолов из довольно концентрированных вод, содержащих более 2 г/л фенолов. Суть методов состоит в том, что фенолсодержащая вода смешивается с каким-нибудь жидким растворителем, в котором фенолы растворяются легче, чем в воде, сам же растворитель в воде не растворяется, в результате чего после обработки жидкости распадаются на два слоя, легко разделяющихся декантацией. Один слой состоит из обесфеноленной воды, второй представляет собой растворитель с поглощенными из воды фенолами, откуда они извлекаются либо отгонкой растворителя, либо переводом фенолов в феноляты путем обработки раствора едкой щелочью. В обоих случаях освобожденный от фенолов растворитель снова идет на промывку – экстракцию воды от фенолов.
Процесс экстрагирования сточных вод состоит из трех стадий: приведение смеси, подлежащей экстрагированию, в тесный контакт с растворителем; разделение образовавшихся фаз; удаление и регенерация растворителя.
Выбор растворителя (экстрагента) для обесфеноливания сточных вод определяется следующими требованиями: он должен обладать высокой растворяющей способностью по отношению к фенолам; быть дешевым; не образовывать эмульсии; при взаимодействии с водой хорошо расслаиваться; не быть токсичным; не разлагаться при регенерации; достаточно полно выделять поглощенные фенолы.
До сих пор не найдено растворителя, который удовлетворял бы всем требованиям: высокой экстракционной способностью и практически полно извлекают из воды фенолы хинолин и анилин, но и сами растворяются в воде и загрязняют воду; трикрезилфосфат и феносольван являются эффективными экстрагентами, но мало доступны, так как дороги. В промышленности получили применение такие растворители, как бутилацетат, каменноугольные масла, высококипящие спирты (выкипают в пределах 170–200°С). Наибольшее применение получил бензол. Этот растворитель обладает достаточной экстракционной способностью, хорошо отделяется от сточной воды, легко освобождается от фенолов при промывке щелочью или при перегонке, химически устойчив, является продуктом коксохимического производства, имеет небольшую стоимость. В процессе экстракции сточных вод используют большие количества бензола, поэтому концентрация фенола в полученном экстракте невелика.
Выделение фенолятов из полученного экстракта (регенерация бензола) может осуществляться методом дистилляции или бензол-фенолятным методом. В промышленности получил предпочтение бензол-фенолятный метод. Он обеспечивает большую степень извлечения фенолов из сточных вод, достигающую 90–92%.
Бензол-фенолятный экстракционный метод включает следующие стадии процесса: обессмоливание воды путем ее отстаивания, фильтрования, промывки циркулирующим бензолом, который затем регенерируют дистилляцией; извлечение фенолов из сточной воды бензолом в экстракционном аппарате; предварительная промывка бензоло-щелочно-фенолятным раствором для удаления растворимых в ней кислых газов; извлечение фенолов из бензола щелочью.
Достоинствами экстракционных методов являются: высокая степень обесфеноливания воды; более высокая выработка фенолов, поскольку извлечение их из воды осуществляется до аммиачной колонны, чем исключаются потери фенолов, имеющиеся при паровом методе; более высокая степень извлечения креза-лов; практически полное извлечение из вод масел и смол.
К недостаткам экстракционных методов относят сложность технологической схемы, а также то, что большинство применяемых экстрагентов в той или иной степени растворяется в обрабатываемой воде.
Для извлечения фенолов из сточных вод в промышленности экономически выгодно применять каменноугольные масла, полученные при фракционировании каменноугольной смолы. Эти масла являются продуктами коксохимического производства, поэтому легко доступны. Каменноугольные масла могут использоваться для экстракции фенолов из аммиачной воды и из сепараторных вод смолоперегонного цеха.
Сепараторные воды смолоперегонных цехов обесфеноливают каменноугольным маслом в аппаратах периодического или непрерывного действия.
Конечное содержание фенолов в воде составляет 0,8–1,5 г/л при начальном содержании их 8–10 г/л. Степень обесфеноливания воды достигает 88–96%. Недостатком каменноугольного масла является склонность его к эмульгированию с водой, что затрудняет процесс экстракции. Интенсивность образования эмульсии зависит от рН воды, содержания в ней смол, скорости перемешивания фаз и температуры процесса. Поэтому сепараторную воду подкисляют до рН = 7,2–7,6, а затем подвергают фильтрованию в кварцевых фильтрах, что способствует разрушению водносмоляной эмульсии.
4.5. Технология биохимического метода обезвреживания
сточных вод
Сточные воды после обесфеноливания их паровым или экстракционным методом подвергают доочистке от фенолов или обезвреживанию. Доочистка, обезвреживание и использование сточных вод коксохимических предприятий является одними из главных направлений в защите окружающей среды от загрязнений.
Существует много методов обезвреживания сточных вод: адсорбционные, основанные на физико-химических свойствах поверхности твердых поглотителей – активированного угля, ионитов (природных и искусственных); окисление вод озоном; испарение фенольных вод; очистка вод от сероводорода и синильной кислоты; биохимическая очистка и др.
На коксохимических заводах страны широкое применение получили методы биохимической очистки сточных вод от фенолов и других примесей.
Биохимические методы основаны на способности микроорганизмов окислять фенолы. Конечными продуктами биохимического разложения примесей, содержащихся в сточных водах, являются соединения высшей степени окисления – диоксид углерода (СО2) и вода. Эти методы обеспечивают глубокую очистку сточных вод в результате разложения фенолов.
Для биохимической очистки фенольных вод используют микроорганизмы двух видов: активный ил (или биологическую пленку) и культуры специальных бактерий, предназначенных для разрушения определенных компонентов, загрязняющих сточные воды. Активный ил представляет собой скопление бактерий – зооглей, нитчатых, жгутиковых, корненожек, инфузорий, коловраток и др.
На установках с активным илом лучшие результаты обесфеноливания получаются после предварительного разбавления фенольных сточных вод технической водой или хозяйственно-бытовыми водами.
Весьма важным фактором, влияющим на эффективность обесфеноливания сточной воды биохимическими методами, является концентрация в ней, помимо фенолов, других химических веществ: цианидов, роданидов, сероводорода и др. Так как фенолы разрушаются быстрее этих соединений, то для их окисления количество кислорода, подаваемого с воздухом при аэрации биологического бассейна, оказывается недостаточным. Это приводит к накоплению в единице объема жидкости указанных примесей и достижению ядовитой для микробов концентрации, в результате чего разрушение фенолов замедляется или вовсе прекращается. Поэтому разбавление сточных вод свежей технической водой (1 : 1) снижает концентрацию примесей в единице объема жидкости и предупреждает повышение концентрации их до ядовитой для микробов. Особенно нежелательной примесью является аммиак, который окисляется значительно быстрее фенолов и при этом затрачивается большое количество кислорода. Содержание аммиака в сточной воде тормозит процесс обесфеноливания. Опыт работы биохимических установок показал, что при содержании аммиака (общего) в исходной воде в пределах 0,5–1,0 г/л конечное содержание фенолов в воде не превышает 2 мг/л. Повышение содержания аммиака в воде до 1,5 г/л приводит к увеличению фенолов до 4–5 мг/л. Следовательно, снижение содержания аммиака в сточной воде, идущей на биохимическую доочистку, повышает эффективность обесфеноливания. На коксохимических заводах широкое распространение получил биохимический метод очистки сточных вод с использованием специфических культур бактерий, он получил название микробного. Этот метод может использоваться для обесфеноливания сточных вод с большой концентрацией фенолов и других соединений.
Основным сооружением биохимической установки является биологический бассейн, в котором протекает процесс разрушения фенолов микробами. В основу микробного метода очистки сточных вод положены следующие требования:
1) основным началом, разрушающим фенолы и тиоцианаты, являются микробы специально приспособленные к разрушению этих веществ в лаборатории;
2) не допускается применение для переработки бытовых вод;
3) сточные воды с концентрацией фенолов 500–300 мг могут перерабатываться без разбавления.
Необходимыми условиями жизнедеятельности этих микробов и, следовательно, эффективности обесфеноливания сточных вод являются: тщательная предварительная очистка сточных вод от механических примесей, смолы и масел, постоянный состав сточных вод, характеризующийся величиной рН в пределах 7–8,5 и температурой 25–30°С, наличие в сточной воде солей фосфора; интенсивная аэрация сточных вод для обогащения их кислородом, содержание общего аммиака не более 2 г/л; равномерное поступление сточной воды в биологический бассейн.
Технологическая схема установки для обесфеноливания сточных вод коксохимических заводов биохимическим методом, спроектированной в Гипрококсе, приведена на рис. 7.
Сточные воды подают на биохимическую установку по двум коллекторам (отдельно для общего стока и для сточной воды аммиачного отделения). Феноль-ные воды общего стока первоначально подвергают механической очистке от взвешенных частиц, смолы и масел. Поэтому их последовательно пропускают через песколовку, отстойник и маслоотделитель. Периодически сбрасываемые сточные воды направляют в уравнительный резервуар, из которого равномерно подают на очистку.
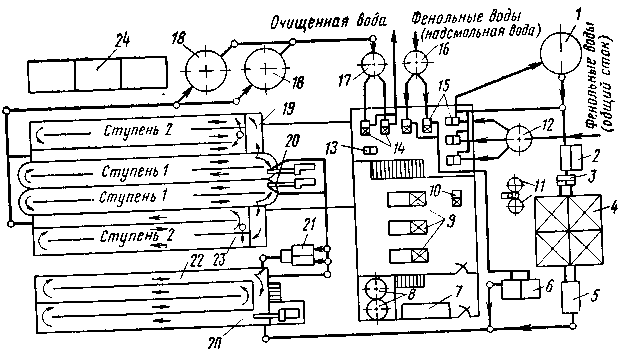
Рис 7. Технологическая схема установки для обесфеноливания сточных вод биохимическим методом:
1 – уравнительный резервуар; 2 – песколовка; 3 – распределительная камера; 4 – первичный отстойник; 5 – маслоотделитель; 6 – холодильники для охлаждения надсмольной воды; 7 – склад суперфосфата; 8 – баки для приготовления раствора суперфосфата; 9 – воздуходувки; 10 – насос для откачки смолы и масла; 11 – сборники смолы и масел; 12 – сборник фенольных вод; 15 – насосы для перекачки фенольных вод; 16 – сборник надсмольной воды; 17 – сборник очищенной воды; 18 – вторичные отстойники; 19 – биологический бассейн (из двух отделений); 20 – пропеллерные насосы; 21 – запасные емкости для фенолразрушающих и роданразрушающих микробов; 22 – усреднитель; 23 – эрлифт; 24 – дренажные площадки.
Выделенные в маслоотделителе смолы и масла откачивают в сборники для обезвоживания, а затем погружают в цистерну.
Надсмольная вода в дополнительной механической очистке не нуждается, так как ее обессмоливают в кварцевых фильтрах перед подачей в аммиачную колонну и подвергают осветлению в известковом отстойнике. Поскольку температура воды высокая (90–95°С), ее вначале охлаждают, а затем вместе с осветленной водой общего стока направляют в усреднитель. Из усреднителя сточную воду подают в биологический бассейн, в котором фенолы разрушаются микроорганизмами. По пути в бассейн к сточной воде добавляют фосфор в виде раствора суперфосфата. Доза суперфосфата, содержащего 10–12% фосфора, составляет 0,2 кг на 1 м3 сточной воды. Воздух в бассейн нагнетают воздуходувками, расположенными в здании машинно-насосного отделения, в котором установлены также насосы для перекачки сточных вод и оборудование для приготовления суперфосфата.
После очистки в биологических бассейнах сточные воды направляют во вторичный отстойник для освобождения от образующегося осадка (биомассы), а затем – на совместную очистку с бытовыми водами для создания запаса микроорганизмов, необходимого в случае выхода биологического бассейна из строя, предусмотрены специальные резервуары с фенол- и роданразрушающими микробами. Обезвоживание осадка осуществляется на дренажных площадках.
В технологической схеме трехступенчатой биохимической установки Гипрококса предусматривается на первой ступени обесфеноливание воды, на второй – удаление тиоцианидов, на третьей – доочистка сточной воды совместно с бытовыми водами.
В перспективе основным остается биохимический метод очистки сточных вод для глубокой очистки фенольных вод предусматривается дальнейшее совершенствование конструкции биологических установок, улучшение подготовки сточных вод, использование технологического кислорода для интенсификации биологических процессов, применение для обезмасливания сточных вод электрофлотации и для биохимического процесса озона, внедрение для очистки фенольных вод других более эффективных физико-химических способов, которые могут быть применены как в сочетании с биохимическим, так и самостоятельно.
V. ПРОИЗВОДСТВО СУЛЬФАТА АММОНИЯ
5.1. Сульфат аммония, его свойства. Использование сульфата аммония
Сульфат аммония [(NH4)2SO4] получают на коксохимических заводах в сульфатном отделении цеха улавливания. Исходным сырьем для получения сульфата аммония служит аммиак, содержащийся в коксовом газе.
Получение сульфата аммония основано на реакции нейтрализации аммиака серной кислотой в сатураторах или абсорберах:
2NH3 + H2SО4 — (NH4)2SО4 + q.
Сульфат аммония представляет собой белые, прозрачные кристаллы формы удлиненного ромба величиной от сотых и десятых долей миллиметра до 6–8 мм и больше. Плотность кристаллического сульфата аммония при 20°С составляет 1,768 г/см3. Насыпная масса в зависимости от крупности кристаллов и содержания влаги колеблется в пределах 780–830 кг/м3. Сульфат аммония, хорошо растворяется в воде. С повышением температуры растворимость его в воде увеличивается. Химически чистый сульфат аммония содержит 21,237% азота или 25,76% NН3.
По государственному стандарту (ГОСТ-9097-74) сульфат аммония должен характеризоваться следующими показателями:
Сорт | Высший | I | II |
Содержание азота в пересчете | | | |
на сухое вещество, % | 21,0 | 20,8 | 20,8 |
Содержание влаги, %, не более | 0,2 | 0,3 | 0,3 |
Содержание свободной H2SО4, %, не более | 0,025 | 0,050 | 0,050 |
Цвет | белый | белый или слабо окрашенный | не нормируется |
Гранулометрический состав: | | | |
содержание фракции >0,25 мм, %, не менее | 95 | 70 | не нормируется |
остаток на сите 6 мм | отсутствует | – | не нормируется |
Важным показателем качества сульфата аммония является размер кристаллов. Мелкокристаллическая структура соли с сильно развитой поверхностью является причиной повышенного содержания в ней влаги и серной кислоты, что приводит к слеживанию при хранении и срастанию ее в агломераты. Крупнокристаллическая соль менее подвержена слеживанию и равномерно распределяется в почве при использовании ее в качестве удобрения.
Сульфат аммония содержит около 24% серы, которая в виде сульфат-иона поступает в почву вместе с удобрением. Сульфат аммония является удобрением для сельскохозяйственных полей. В мировом производстве азотных удобрений на долю сульфата аммония приходится более 20% от всего производства связанного азота, в нашей стране 6–7% от всего количества выпускаемых азотных удобрений. Ценность этого удобрения обусловлена высоким содержанием азота, по сравнению с другими азотными удобрениями (чилийской селитрой NaNO3, содержащей 15–16%, норвежской селитрой Ca(NO3)2, содержащей 13–14% и естественным удобрением, содержащим 6–7% азота); азот хорошо усваивается из почвы корнями растений. Содержащаяся в сульфате аммония сера является необходимым элементом питания для многих сельскохозяйственных культур (свеклы, хлопчатника, табака и др.), поэтому сульфат аммония можно считать удобрением, содержащим питательных веществ более 45% и обладающим высокими агротехническими свойствами.
Сульфат аммония производится на коксохимических заводах в больших количествах. На 1 т сухой шихты производство сульфата аммония (сухого) составляет 11,0–11,5 кг.
5.2. Характеристика серной кислоты, применяемой для производства сульфата аммония
В химически чистом сульфате аммония аммиак составляет 25,76%, остальные 74,24% приходятся на долю серной кислоты. На отечественных коксохимических заводах для производства сульфата аммония используется серная кислота следующих видов: башенная, контактная техническая (привозная и собственных цехов мокрого катализа); отработанная с предприятий органического синтеза; регенерированная после мойки фракций сырого бензола и других коксохимических продуктов. Качество серной кислоты нормируется ГОСТом.
Для производства сульфата аммония высшего и первого сортов используется контактная серная кислота улучшенной марки Б концентрации 92,5–94,0% с содержанием железа не более 0,015%, оксидов азота и мышьяка 0,0001%; для производства сульфата аммония второго сорта используются контактная техническая кислота концентрации 92,5%, содержащая 0,02% железа; башенная кислота марки А концентрацией 75% и содержанием 0,02% железа.
Регенерированная серная кислота цехов ректификации сырого бензола с содержанием моногидрата до 50% загрязнена органическими примесями (сульфокислотами и продуктами полимеризации). Эти примеси отрицательно влияют на ход сатураторного процесса и снижают качество сульфата аммония. Однако экономически необходимо использовать эту кислоту, как наиболее дешевую.
Кроме того, в серной кислоте содержатся и другие примеси – оксиды азота, мышьяк, хлористые соединения, свинец, кадмий, алюминий и другие, которые также влияют на работу сатуратора и качество сульфата аммония. Содержание этих примесей нормируется ГОСТом.
Большое значение для работы сульфатного отделения имеет организация приема и хранения серной кислоты. Хранение серной кислоты (75%) осуществляется в вертикальных хранилищах из углеродистой стали емкостью не более 400 м3. Хранилища снабжаются воздушками с влагоуловителями. Для регенерированной кислоты применяют хранилища с внутренней кислотоупорной футеровкой. Емкость склада серной кислоты зависит от размеров производства сульфата аммония и от того, на какой кислоте работает сульфатное отделение (на привозной или собственной). Емкость склада составляет от 15 до 20 доз суточной потребности.
Температура плавления концентрированной серной кислоты 10,3С.
5.3. Способы получения сульфата аммония
Существует три классических способа получения сульфата аммония: непрямой, прямой и полупрямой.
Сущность непрямого или косвенного способа заключается в том, что аммиак из коксового газа улавливается в аммиачных скрубберах с получением слабой скрубберной аммиачной воды. Отгонку (десорбцию) аммиака из слабой аммиачной воды проводят в дистилляционных колоннах с получением газообразного аммиака. Пары аммиака из колонн поступают в сатуратор, где он связывается серной кислотой в сульфат аммония, т.е. сульфат аммоний получается не непосредственно из газа, а путем некоторых промежуточных операций. Этот метод характеризуется значительным расходом холодной воды для улавливания аммиака в скрубберах большими потерями аммиака с обратным газом. Он не нашел промышленного применения в отечественной коксохимической промышленности. За рубежом этот метод применяется при комбинированном улавливании из газа аммиака и сероводорода.
Отличительной особенностью прямого метода является то, что перед улавливанием аммиака в сатураторе газ охлаждается до 68°С. Выделившийся из газа водяной конденсат (надсмольная вода) полностью используется для пополнения воды цикла газосборника и, таким образом, избытка надсмольной воды не получается. Весь аммиак газа улавливается в сатураторе с получением сульфата аммония. Достоинство метода состоит в уменьшении эксплуатационных расходов за счет снижения расхода пара и электроэнергии на переработку аммиачной воды. Широкое распространение этот метод не получил по следующим причинам: наличие большого количества аппаратов, работающих под разрежением, что увеличивает расход мощности нагнетателя газа; интенсивное протекание коррозионных процессов в сатураторе, что обусловливается присутствием хлористого аммония и образованием летучей соляной кислоты; недостаточная очистка газа от туманнообразной смолы, что приводит к образованию большого количества кислой смолки и загрязнению сульфата аммония; получение мелкокристаллической соли, что вызвано высокой температурой процесса; громоздкость аппаратурного оформления из-за высокой температуры газа и большого его влагосодержания.
Полупрямой метод получил широкое распространение как на отечественных коксохимических заводах, так и за рубежом. Этот метод является как бы комбинацией непрямого и полупрямого методов. Особенностью полупрямого метода получения сульфата аммония является то, что не весь аммиак, образующийся при коксовании, поступает с газом в сатуратор, а только 70–75% от его ресурсов в газе. Часть аммиака, до 25–30% от его ресурсов в газе, растворяется в надсмольной воде, образующейся при охлаждении газа в первичных холодильниках. Эта вода пepepaбатывается в аммиачном отделении с получением пароаммиачной смеси, которая направляется в сатуратор, где вместе с аммиаком из газа связывается серной кислотой. Аммиачные пары из колонны аммиачного отделения могут быть направлены в пиридиновую установку, где наряду с пиридиновыми основаниями образуется сульфат аммония – целевой продукт сульфатного отделения. Необходимость дополнительной переработки больших количеств надсмольной воды является недостатком метода, так как требует установки соответствующей аппаратуры и оборудования, больших энергетических затрат.
Несмотря на указанный выше недостаток, полупрямой метод наиболее распространен, так как надежен, удобен в управлении, сравнительно прост по технологической схеме и экономичен: часть аммиачных паров может применяться для получения пиридиновых оснований. Этот способ непрерывно совершенствуется.
5.4. Технология получения сульфата аммония
по сатураторному способу
В коксохимической промышленности наибольшее распространение получил полупрямой способ получения сульфата аммония с использованием сатураторов барботажного типа. Сущность процесса состоит в том, что дополнительно подогретый после нагнетателя коксовый газ, содержащий газообразный аммиак и пары из аммиачной колонны поступают в сатуратор по трубе, заканчивающейся барботажным зонтом. Зонт погружен в маточный раствор, содержащий серную кислоту. При прохождении (барботировании) газа через маточный раствор аммиак вступает в реакцию взаимодействия с серной кислотой и образует с ней конечный продукт – сульфат аммония. Процесс нейтрализации аммиака серной кислотой протекает в две ступени: сначала образуется кислая соль бисульфат аммония по уравнению
NH3 + H2SO4 — NH4HSO4.
По мере насыщения раствора аммиаком кислая соль переходит в среднюю, т.е. сульфат аммония:
NH3 + NH4HSО4 — (NH4)2SO4.
Эти реакции протекают с выделением тепла, количество которого зависит от условий ведения процесса.
Соотношение между сульфатом и бисульфатом, находящимися в растворе обусловливается его кислотностью. При очень низкой кислотности (1–2%) в растворе преобладает сульфат, который выпадает из пересыщенного раствора в виде кристаллов. При повышении кислотности раствора (выше 12–15%) средняя соль (сульфат) переходит в кислую (бисульфат), которая обладает лучшей растворимостью в воде и слабом растворе серной кислоты, чем сульфат и остается в растворенном виде, т.е. при высокой кислотности в растворе находится главным образом бисульфат аммония. По достижении пределов растворимости из раствора в первую очередь выпадают кристаллы сульфата аммония.
Так как процесс нейтрализации при производстве сульфата аммония осуществляется при непрерывном поступлении реагентов с непрерывным отбором готовой соли, то в растворе, заполняющем сатуратор, одновременно находятся бисульфат и сульфат аммония, вода и серная кислота. Этот раствор принято называть маточным раствором. Кислотность маточного раствора в сатураторе поддерживается автоматически.
Одновременно с основным процессом – улавливанием аммиака, в сатураторе протекают реакции связывания серной кислотой пиридиновых оснований, содержащихся в коксовом газе, с образованием средней соли сульфата пиридина и кислой – бисульфата пиридина.
Таким образом, в сатураторе одновременно протекает абсорбция (хемосорбция) аммиака и пиридиновых оснований и кристаллизация соли сульфата аммония. Каждый из этих процессов требует создания определенных условий, обеспечивающих высокую степень улавливания аммиака и пиридиновых оснований и получение крупнокристаллической соли сульфата аммония.
Эффективность всех этих процессов обусловливается поддержанием в сатураторе оптимальных температуры и кислотности маточного раствора, наличием центров кристаллизации соли сульфата аммония и интенсивным перемешиванием раствора в ванне сатуратора.
Технологическая схема получения сульфата аммония по полупрямому сатураторному способу приведена на рис. 8.
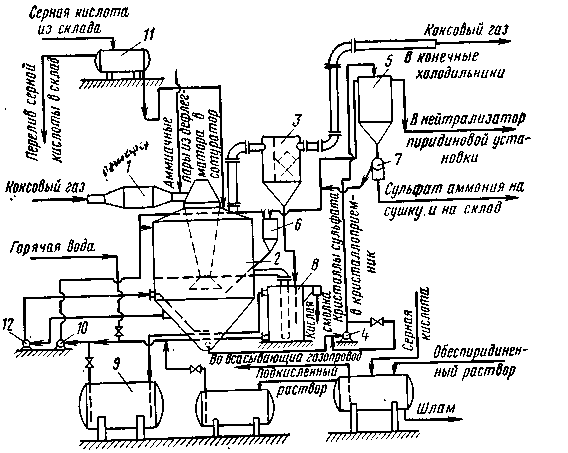
Рис. 8. Технологическая схема получения сульфата аммония по полупрямому методу:
1 – паровой подогреватель; 2 – сатуратор; 3 – кислотная ловушка; 4, 10, 12 – насосы; 5 – кисталлоприемник; 6 – кастрюля обратных токов маточного раствора; 7 – центрифуга; 8 – циркуляционная кастрюля; 9 – сборник избытка маточного раствора; 11 – напорный бак с серной кислотой
Коксовый газ, охлажденный в первичных газовых холодильниках и очищенный от туманообразной смолы в электрофильтрах подается нагнетателем в паровой подогреватель 1 сульфатного отделения. В подогревателе газ нагревается до 50–60°С и поступает в сатуратор 2 по центральной газоподводящей трубе, заканчивающейся газораспределительным зонтом, погруженным в маточный раствор ванны сатуратора на 250–280 мм.
Подогрев газа перед сатуратором особенно необходим в момент спуска сульфатного отделения, а также для предупреждения обводнения ванны сатуратора (для повышения прихода тепла в сатуратор). Одновременно с газом в сатуратор поступает часть пароаммиачной смеси из дефлегматора аммиачного отделения. В сатураторе аммиак, содержащийся в газе и в пароаммиачной смеси и пиридиновые основания взаимодействуют с серной кислотой с образованием соответствующих солей.
Серная кислота с концентрацией 76–75% непрерывно поступает в сатуратор из напорного бака 11 по специальной трубе и распределяется по кольцевой трубе, укрепленной на газоподводящей трубе над барботажным зонтом. Таким образом, кислота подается непосредственно в зону поступления газа в маточный раствор.
Прошедший сквозь слой маточного раствора и освободившийся от аммиака и пиридиновых оснований коксовый газ через газовый патрубок направляется в кислотную ловушку 3, в которой из газа улавливаются увлеченные брызги маточного раствора. Потери аммиака в газе, уходящем из сатуратора, должны составлять не более 0,02–0,03 г/м3 и пиридиновых оснований не более 0,04–0,06 г/м3. Это достигается хорошим контактом газа и маточного раствора в ванне сатуратора.
После кислотной ловушки коксовый газ направляется в конечные газовые холодильники для охлаждения его до 25–30°С перед улавливанием бензольных углеводородов в скрубберах.
Оседающие в конической части сатуратора кристаллы сульфата аммония вместе с некоторым количеством маточного раствора кислотоупорным насосом 4 подаются в кристаллоприемник 5 для отстаивания кристаллов сульфата аммония. Через штуцер, расположенный в верхней части кристаллоприемника, маточный раствор отстоявшегося от кристаллов сульфата аммония непрерывно стекает в кастрюлю обратных токов 6 и из нее самотеком в сатуратор. Кристаллоприемник располагают выше кастрюли обратных токов, чтобы обеспечить самотек раствора.
Из нижней части кристаллоприемника 5 сгустившаяся смесь кристаллов сульфата аммония с маточным раствором самотеком поступает в центрифугу непрерывного действия 7, где кристаллы отделяются от маточного раствора и промываются горячей водой (60–70°С). Отфугованный сульфат аммония из центрифуги транспортируется на сушку, а затем на склад. Раствор после центрифуги через кастрюлю обратных токов возвращается в сатуратор.
Уровень маточного раствора в сатураторе поддерживается постоянным с помощью специального бокового штуцера (перелива), через который избыток маточного раствора отводится в циркуляционную кастрюлю 8, служащую одновременно гидравлическим затвором, исключающим возможность выхода газа из сатуратора вместе с раствором.
Вместе с маточным раствором в циркуляционную кастрюлю отводится кислая смолка, плавающая на поверхности маточного раствора в ванне сатуратора. Всплывшая на поверхность маточного раствора кислая смолка через сливной карман выводится из циркуляционной кастрюли в специальную емкость.
Для создания в ванне сатуратора равномерной концентрации кислоты и благоприятных условий для роста кристаллов соли производится непрерывная циркуляция маточного раствора циркуляционным насосом производительностью 150–200 м3/ч по схеме сатуратор–насос–сатуратор. При этом маточный раствор забирается насосом из средней зоны сатуратора и подается в его нижнюю коническую часть через специальное сопло ажитатор. Таким образом, в этой зоне сатуратора создаются интенсивные восходящие потоки маточного раствора, которые поддерживают кристаллы во взвешенном состоянии, удлиняя время их роста.
При образовании в ванне сатуратора избытка маточного раствора последний из циркуляционной кастрюли самотеком перетекает в сборник 9, откуда по мере надобности насосом 10 возвращается в сатуратор.
Перелив из сатуратора в циркуляционную кастрюлю не должен превышать 10–12 м3/ч, что обеспечивается насосом соответствующей производительности. Циркуляция раствора производится по схеме циркуляционная кастрюля–сборник–насос–кастрюля обратных токов–сатуратор–циркуляционная кастрюля или сатуратор–насос 12–сатуратор. Часть маточного раствора, отстоявшегося от кристаллов сульфата аммония, из верхней части кристаллоприемника 5 непрерывно отводится в нейтрализатор пиридиновой установки. Маточный раствор в пиридиновую установку может также отбираться из нагнетательной линии циркуляционного насоса. Количество этого раствора зависит от содержания в нем пиридиновых оснований, которое составляет 10–15 г/л и в свою очередь определяется содержанием пиридиновых оснований в коксовом газе, температурой и кислотностью маточного раствора в сатураторе. Чем выше концентрация пиридиновых оснований в маточном растворе, тем меньшее количество раствора необходимо выводить для переработки в пиридиновое отделение. Обеспиридиненный маточный раствор из пиридинового отделения поступает в реактор-подкислитель, где подкисляется серной кислотой до концентрации 10–12% и затем поступает в сборник или в циркуляционную кастрюлю 8, откуда насосом 10 подается в сатуратор.
Сушка сульфата аммония осуществляется в сушильной установке с «кипящим» слоем, для чего подается воздух, подогретый в калорифере. За последние годы на некоторых заводах внедрены сушилки с «кипящим» слоем с огневым обогревом. В этих сушилках подогрев воздуха осуществляется непосредственным смешением с продуктами сгорания коксового газа. Преимуществом этого метода является низкая стоимость топлива, возможность более тонкой регулировки и автоматизации процесса, получение сульфата аммония с влажностью, не превышающей требования ГОСТа к высшему сорту.
Высушенный сульфат аммония поступает на расфасовку и хранение. Показатели технологического режима работы установки характеризуются следующими данными:
-
Температура газа, С
перед газовым подогревателем
35–40
послегазовым подогревателем
53–60
после сатуратора
55–65
Температура маточного раствора,°С
53–55
Сопротивление сатуратора, кПа (мм вод. ст.)
5–6 (500–600)
Кислотность маточного раствора
4–5
Циркуляция маточного раствора
непрерывная
Заданная кислотность маточного раствора поддерживается путем непрерывной подачи в сатуратор 76%-ной серной кислоты. Состав маточного раствора характеризуется следующими показателями:
-
Плотность, кг/м3
1300–1400
Содержание, %
свободной H2SO4
4–5
NH3, г/л
150–180
(NH4)2SО4
40–48
NH4HSО4
10–15
Выполнение заданного технологического режима работы сатуратора обеспечивает высокую степень улавливания из газа аммиака и пиридиновых оснований.
Для улавливания из коксового газа аммиака и пиридиновых оснований в отечественной коксохимической промышленности наибольшее распространение получил сатуратор диаметром 6250 мм с выносной ловушкой, центральным барботажным зонтом и перемешиванием с помощью циркуляционного насоса, подающего раствор в струйное устройство – ажитатор. Для направленной циркуляции маточного раствора и сепарации кристаллов сульфата аммония по крупности применяются сатураторы, оборудованные простым (по конструкции и эксплуатации) и достаточно эффективным устройством для укрупнения соли – газлифтом. Газлифтный сепаратор представляет собой стакан диаметром 880–900 мм и высотой 1700 мм, внутри которого в нижней части расположен барботер, представляющий собой кольцо из трубы диаметром 76 мм с отверстиями. В кольцо подается сжатый коксовый газ в количестве 1% от нагрузки сатуратора по газу. Стакан устанавливается вертикально в конусной части сатуратора.
Циркуляционная кастрюля представляет собой стальной вертикальный цилиндр, внутри которого почти до дна опускается переливная труба. По этой трубе из сатуратора переливается избыток маточного раствора. В кастрюле поддерживается постоянный уровень раствора, благодаря чему создается гидравлический затвор, исключающий попадание в нее коксового газа. Высота затвора должна быть не меньше общего расчетного напора газового насоса. Из верхней части кастрюли через специальный карман выводится кислая смолка. Через нижний штуцер отводится маточный раствор для циркуляции. Таким образом, циркуляционная кастрюля выполняет три функции: служит гидрозатвором, отводит кислую смолку из ванны сатуратора и осуществляет циркуляцию маточного раствора.
Кристаллоприемник предназначен для непрерывного приема смеси кристаллов сульфата аммония и маточного раствора из сатуратора, отстаивания и накопления кристаллов и загрузки их в центрифугу.
В коксохимической промышленности для сушки сульфата аммония наибольшее распространение получили следующие сушилки: вибрационный сушильный транспортер, сушилка с направленным кипящим слоем конструкции ДПИ (Донецкого политехнического института); сушилка с кипящим слоем конструкции Гипрококса и барабанные сушилки.
Для улавливания брызг кислого маточного раствора из коксового газа, покидающего сатуратор, получили применение ловушки двух конструкций: ловушка с перегородками и ловушка с тангенцильным вводом газа. Ловушка периодически промывается водой или серной кислотой. Из нижней части ловушки раствор отводится в циркуляционную кастрюлю.
Сатураторный способ получения сульфата аммония имеет некоторые достоинства, но и существенные недостатки: высокое сопротивление газовому потоку при прохождении его через сатуратор в ловушку; недостаточная управляемость процессом кристаллизации, в результате чего получаемый сульфат аммония обладает недостаточно выраженной кристаллической структурой; невозможность вести улавливание аммиака при низких температурах и при минимальной и постоянной кислотности маточного раствора; одновременное улавливание из газа аммиака и пиридиновых оснований затрудняет ведение процесса кристаллизации в нужном направлении; периодическое искусственное изменение кислотности ванны сатуратора затрудняет осуществление автоматизации процесса и др.
Сатураторные установки постоянно совершенствуются: применяют сатураторы с разветвленной линией барботажа и эффективными ажитаторами для перемешивания маточного раствора в ванне сатуратора. Для получения крупнокристаллического и одинакового по размеру сульфата аммония устанавливают кристаллоприемники с классификаторами.