Комитетом Российской Федерации по машиностроению и Госгортехнадзором России листом утверждения от 15. 05. 96/17. 06. 96, введенное в действие с 01. 06. 96 Изменение n 2 внесено юридическим бюро кодекс
Вид материала | Кодекс |
- Правила устройства и безопасной эксплуатации паровых и водогрейных котлов утверждены, 3359.45kb.
- Утверждено Госгортехнадзором России 24. 11. 99 постановление n 85 Срок введения в действие, 246.71kb.
- Пб 10-115-96 правила устройства и безопасной эксплуатации сосудов, работающих под давлением, 2564.63kb.
- Акционерное Общество "Роскоммунэнерго", 1055.75kb.
- Российская федерация федеральный закон о введении в действие лесного кодекса российской, 297.26kb.
- Российской федерации, 41.45kb.
- Принят Государственной Думой 17 июля 1998 года Одобрен Советом Федерации 17 июля 1998, 5092.85kb.
- Типовая инструкция по безопасному ведению работ для персонала котельных рд 10-319-99, 973.52kb.
- Типовая инструкция по безопасному ведению работ для персонала котельных (рд 10-319-99), 1051.44kb.
- Гражданский кодекс российской федерации часть четвертая, 2804.9kb.
6.2. Документация
6.2.1. К сосудам должна прилагаться следующая документация:
паспорт и приложения согласно требованиям Правил;
инструкция по монтажу и эксплуатации;
ведомость запасных частей;
приложения согласно требованиям настоящего стандарта;
чертежи быстроизнашивающихся деталей (по требованию заказчика);
акт о проведении контрольной сборки или контрольной проверки размеров, схема монтажной маркировки, сборочные чертежи в трех экземплярах (для сосудов, транспортируемых частями);
эксплуатационная документация;
техническая и сопроводительная документация на комплектующие изделия (электродвигатели, редукторы, насосы и др.).
Примечания.
1. К сосудам, на которые Правила не распространяются, допускается прилагать паспорт по форме согласно требованиям обязательного приложения 28.
2. Инструкция по монтажу и эксплуатации должна быть составлена разработчиком сосуда.
3. К деталям и сборочным единицам, поставляемым по кооперации, следует прилагать удостоверение о качестве.
6.2.2. Сопроводительная документация на сосуды для экспорта должна соответствовать ГОСТ 2.601, "Положению о порядке составления, оформления и рассылки технической и товаросопроводительной документации на товары, поставляемые для экспорта" МВЭС СССР, ГОСТ 2.901.
(Измененная редакция, Изм. N 2).
6.2.3. На чертеже, поставляемом с паспортом сосуда, предприятие-изготовитель должно указать перечень транспортных блоков (частей).
7. МАРКИРОВКА, КОНСЕРВАЦИЯ И ОКРАСКА.
УПАКОВКА, ТРАНСПОРТИРОВАНИЕ И ХРАНЕНИЕ
7.1. Маркировка
7.1.1. Сосуды должны иметь табличку, соответствующую требованиям ГОСТ 12971.
На сосудах наружным диаметром не более 325 мм табличку допускается не устанавливать. В этом случае необходимые данные наносятся на корпус сосуда.
7.1.2. Табличка размещается на видном месте.
Табличка крепится на приварном подкладном листе, приварной скобе, приварных планках или приварном кронштейне.
7.1.3. На табличку должны быть нанесены:
наименование или товарный знак предприятия-изготовителя;
наименование или обозначение (шифр заказа) сосуда;
порядковый номер сосуда по системе нумерации предприятия-изготовителя;
расчетное давление, МПа;
рабочее или условное избыточное давление, МПа;
пробное давление, МПа;
допустимая максимальная и (или) минимальная рабочая температура стенки, °С;
масса сосуда, кг;
год изготовления;
клеймо технического контроля.
Примечание. Для теплообменных аппаратов и сосудов с несколькими полостями следует расчетное, рабочее и пробное давления и допустимую рабочую температуру стенки указывать для каждой полости.
7.1.4. На наружной поверхности стенки сосуда должна быть нанесена маркировка:
наименование или товарный знак предприятия-изготовителя;
порядковый номер по системе нумерации предприятия-изготовителя;
год изготовления;
клеймо технического контроля.
Маркировка сосудов с толщиной стенки корпуса 4 мм и более наносится клеймением или гравировкой, а с толщиной стенки менее 4 мм - гравировкой или несмываемой краской. Маркировка заключается в рамку, выполненную атмосферостойкой краской, и защищается бесцветным лаком (тонким слоем смазки). Глубина маркировки клеймением или гравировкой должна быть в пределах 0,2-0,3 мм.
Качество и цвет маркировки должны соответствовать ГОСТ 26828.
Примечание. Допускается наносить маркировку на пластину, приваренную к корпусу сосуда рядом с табличкой.
7.1.5. Шрифт маркировки должен соответствовать ГОСТ 26.020 для плоской печати и ГОСТ 26.008 для ударного способа.
7.1.6. Кроме основной маркировки, следует:
а) выполнить по две контрольные метки вверху и внизу обечайки под углом 90° на неизолируемых вертикальных сосудах, не имеющих специальных приспособлений для выверки вертикальности их на фундаменте;
б) нанести монтажные метки (риски), фиксирующие в плане главные оси сосуда, для выверки проектного положения его на фундаменте;
в) нанести несмываемой краской отличительную окраску на строповые устройства;
г) прикрепить (или отлить) стрелку, указывающую направление вращения механизмов, при этом стрелку необходимо окрасить в красный цвет несмываемой краской;
д) нанести монтажную маркировку (для негабаритных сосудов, транспортируемых частями);
е) нанести отметки, указывающие положение центра масс на обечайке сосудов, при этом отметки расположить на двух противоположных сторонах сосуда;
ж) указать диаметр отверстий под регулировочные болты несмываемой краской вблизи от одного из отверстий (при наличии регулировочных болтов в опорной конструкции сосуда).
Примечание. Отметки центра масс выполняются по черт. 12 ГОСТ 14192. Причем, если координаты центра тяжести изделия и груза, отправляемого без упаковки в тару, совпадают, то Знак нанести 1 раз с двух сторон, а если не совпадают, то Знак нанести 2 раза с двух сторон. При этом к Знаку, определяющему координаты "Центра масс", дополнительно нанести буквы "ЦМ".
(Измененная редакция, Изм. N 2).
7.1.7. Маркировка отгрузочных мест должна наноситься по ГОСТ 14192.
7.1.8. На транспортируемых частях негабаритных сосудов должно быть указано:
обозначение сосуда;
порядковый номер по системе нумерации предприятия-изготовителя;
обозначение транспортируемой части.
7.1.9. На каждом сосуде, поставочном блоке, негабаритных частях сосуда должны быть указаны места крепления стропов, положение центра тяжести. Должны быть предусмотрены и поставлены предприятием-изготовителем устройства в соответствии с технической документацией, обеспечивающие установку в проектное положение сосуда в собранном виде или поставочного блока.
7.2. Консервация и окраска
7.2.1. Консервации и окраске подлежат сосуды, принятые отделом технического контроля.
7.2.2. Консервация металлических неокрашенных поверхностей сосудов, поставляемых в полностью собранном виде, а также негабаритных поставочных частей, комплектующих деталей и сборочных единиц, входящих в объем поставки, должна проводиться в соответствии с требованиями ГОСТ 9.014 и обеспечивать защиту от коррозии при транспортировании, хранении и монтаже в течение не менее 24 месяцев со дня отгрузки с предприятия-изготовителя.
7.2.3. Консервация сосудов должна проводиться по технологии предприятия-изготовителя с учетом условий транспортирования и хранения по ГОСТ 9.014.
7.2.4. Методы консервации и применяемые для этого материалы должны обеспечивать возможность расконсервации сосудов в сборе и транспортируемых блоков (узлов) без их разборки.
Марки консервационных материалов выбираются в каждом отдельном случае в зависимости от условий эксплуатации сосудов и должны отвечать требованиям РТМ 26-02-52, РТМ 26-02-66, ГОСТ 9.014.
Примечание. Если по условиям эксплуатации требуется обезжиривание, которое невозможно выполнить без разборки сборочных единиц, то требование о безразборной расконсервации на эти сосуды не распространяется.
7.2.5. Свидетельство о консервации должно включать следующие сведения:
дату консервации;
марку консервационного материала;
вариант внутренней упаковки;
условия хранения;
срок защиты без переконсервации;
срок консервации;
способы расконсервации.
Свидетельство прикладывается к паспорту сосуда, подвергнутого консервации. При этом должны применяться обозначения в соответствии с ГОСТ 9.014.
7.2.6. Поверхность сосуда (сборочной единицы) перед окраской должна быть подготовлена по документации предприятия-изготовителя и технологическим инструкциям специализированной научно-исследовательской организации с учетом требований ГОСТ 9.402.
7.2.7. Выбор системы покрытий и лакокрасочных материалов для защиты сосудов (сборочных единиц) проводится в зависимости от условий эксплуатации, категории размещения, транспортирования, хранения, монтажа, габаритов и других условий согласно РД 24.202.03.
Примечание. Окраска является защитной на время транспортирования, хранения и монтажа в течение не менее 24 мес. со дня отгрузки с предприятия-изготовителя.
(Измененная редакция, Изм. N 2).
7.2.8. Цвет покрытия выбирается в зависимости от условий эксплуатации по ГОСТ 12.4.026 и технических условий на сосуд (сборочную единицу).
На период транспортирования, монтажа и хранения цвет покрытия не нормируется.
7.2.9. При поставке негабаритных сосудов частями или габаритными блоками защитное покрытие наносится в соответствии с требованиями пп. 7.2.6, 7.2.7.
Примечание. Кромки, подлежащие сварке на монтажной площадке, и прилегающие к ним поверхности шириной 50-60 мм должны защищаться консистентной смазкой или другими материалами. Окраска кромок не допускается.
7.3. Упаковка, транспортирование и хранение
7.3.1. Упаковка сосудов должна производиться по технической документации на конкретный сосуд.
(Измененная редакция, Изм. N 2).
7.3.2. При необходимости внутренние устройства и вращающиеся механизмы должны быть закреплены для предохранения от деформации под влиянием собственной массы и динамических нагрузок при транспортировании.
7.3.3. Все отверстия, штуцера, муфты должны быть закрыты пробками или заглушками для защиты от загрязнений и повреждений уплотнительных поверхностей.
7.3.4. Отдельно отправляемые сборочные единицы, детали, запасные части должны быть упакованы в ящики или собраны в пакеты (стопы).
Вид упаковки выбирается предприятием-изготовителем, если нет других указаний в технической документации.
Ящики и способы крепления должны соответствовать ГОСТ 2991, ГОСТ 5959, ГОСТ 10198, ГОСТ 21650.
Ящики для запасных частей сосудов, предназначенных на экспорт, должны соответствовать ГОСТ 24634 или требованиям заказа-наряда.
(Измененная редакция, Изм. N 2).
7.3.5. Крепежные детали при отправке их в ящиках должны быть законсервированы согласно инструкции предприятия-изготовителя, а шпильки (болты) фланцевых соединений дополнительно упакованы в оберточную или парафинированную бумагу.
7.3.6. Техническая и товаросопроводительная документация, прилагаемая к сосудам, должна быть завернута в водонепроницаемую бумагу или бумагу с полиэтиленовым покрытием и вложена в пакет, изготовленный из полиэтиленовой пленки толщиной не менее 150 мк. Швы пакета свариваются (заклеиваются).
Для дополнительной защиты от механических повреждений пакет должен быть обернут водонепроницаемой бумагой или полиэтиленовой пленкой. Края бумаги или пленки должны быть склеены синтетическим клеем.
7.3.7. Если сосуд поставляется в виде нескольких грузовых мест, техническая документация должна упаковываться в грузовое место N 1.
7.3.8. При отгрузке сосудов без тары техническая документация должна крепиться внутри сосуда или на сосуде. При этом на сосуд наносится надпись: "Документация находится здесь".
7.3.9. Каждое грузовое место должно иметь свой упаковочный лист, который вкладывается в пакет из водонепроницаемой бумаги или бумаги с полиэтиленовым покрытием. Пакет дополнительно завертывается в водонепроницаемую бумагу и размещается в специальном кармане, изготовленном в соответствии с документацией, применяемой на предприятии-изготовителе. Карман крепится около маркировки груза.
К ярлыку грузов, отправляемых в пакетах и связках, должен крепиться футляр для упаковочного листа в соответствии с документацией, используемой на предприятии-изготовителе.
Второй экземпляр упаковочного листа или комплектовочной ведомости вместе с технической документацией упаковывается в грузовое место N 1.
7.3.10. Техническую документацию и второй экземпляр упаковочного листа допускается отправлять почтой. Отправка технической документации должна быть произведена в течение одного месяца после отгрузки сосуда.
7.3.11. Сосуды должны транспортироваться железнодорожным транспортом в соответствии с требованиями Министерства путей сообщения.
Допускается транспортирование автомобильным и водным транспортом.
Крепление сосудов следует производить по документации предприятия-изготовителя.
7.3.12. Транспортирование и погрузочно-разгрузочные работы должны проводиться без резких толчков и ударов в целях обеспечения сохранности оборудования и его упаковки.
7.3.13. Условия транспортирования и хранения сосудов на предприятии-изготовителе и монтажной площадке должны обеспечивать сохранность качества сосудов, предохранять их от коррозии, эрозии, загрязнения, механических повреждений и деформации.
7.3.14. Категорию и условия транспортирования и хранения сосудов в части воздействия климатических факторов внешней среды по ГОСТ 15150 следует указывать в технических условиях на конкретные сосуды. При назначении категории и условий хранения должна быть учтена сохраняемость комплектующих деталей.
8. ГАРАНТИИ ИЗГОТОВИТЕЛЯ
8.1. Предприятие-изготовитель гарантирует соответствие сосудов требованиям настоящего стандарта при соблюдении условий транспортирования, хранения, монтажа и эксплуатации.
8.2. Гарантийный срок эксплуатации - не менее 18 мес со дня ввода сосуда в эксплуатацию, но не более 24 мес после отгрузки с предприятия-изготовителя.
9. СПЕЦИАЛЬНЫЕ ТРЕБОВАНИЯ К КОЛОННЫМ АППАРАТАМ
9.1. Требования к изготовлению колонных аппаратов
9.1.1. Относительная овальность корпуса колонных аппаратов должна соответствовать требованиям п.3.3.2, если в технической документации не указаны более жесткие требования.
9.1.2. Отклонение от параллельности уплотнительных поверхностей фланцев царг после механической обработки не должно превышать 0,4 мм на 1 м диаметра (рис. 20), но не более 1 мм на диаметр D.
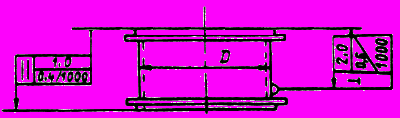
Рис. 20. Царга с фланцами
Отклонение от перпендикулярности уплотнительных поверхностей фланцев царг к образующей обечайки не должно превышать 0,6 мм на 1 м высоты царги (рис. 20), но не более 2 мм на всю высоту царги.
9.1.3. Отклонение от высоты царги с фланцами не должно превышать ±2 мм на 1 м номинального размера, но не более ±5 мм на всю высоту царги.
9.1.4. Допуск на расстояние от оси сварного шва приварки нижнего днища к обечайке до:
оси штуцера - ±10 мм;
оси люка - ±20 мм;
основания опоры - ±20 мм;
Допуск на расстояние между осями парных штуцеров для присоединения контрольных и регулировочных приборов - ±3 мм.
9.1.5. Крепежные детали внутренних устройств колонных аппаратов из углеродистых сталей должны изготавливаться из коррозионностойких материалов.
9.2. Ректификационные тарелки
9.2.1. Тарелки должны изготавливаться в соответствии с требованиями стандартов и проекта.
9.2.2. При изготовлении деталей и сборочных единиц тарелок одноименные детали и сборочные единицы определенного типоразмера должны быть взаимозаменяемыми.
9.2.3. Штампованные детали тарелок должны быть чистыми, без трещин, надрывов и заусенцев.
9.2.4. Сварные швы, которые перекрываются съемными деталями тарелок, в опорных деталях должны быть зачищены заподлицо с основным металлом.
9.2.5. Отклонение от перпендикулярности опорной детали тарелки, привариваемой к корпусу колонного аппарата, к оси корпуса, относительно которой установлены устройства (риски) для выверки вертикальности его на монтажной площадке, не должно превышать значений, указанных в табл. 23.
Таблица 23
Отклонение от перпендикулярности опорной детали тарелки
Тип тарелок | Внутренний диаметр колонного аппарата, мм | Отклонение перпендикулярности, мм |
Тарелки провальные | ||
Решетчатые и др. | До 2000 | ±2 |
| От 2000 до 3000 | ±3 |
Тарелки с переливами | ||
Клапанные, клапанные балластные, S-образно-клапанные, ситчатые с | До 3000 | ±3 |
отбойными элементами, центробежные | От 3000 до 6000 | ±4 |
| От 6000 и более | ±5 |
Колпачковые, ситчатые, ситчато-клапанные, жалюзийно-клапанные, с | До 3000 | ±3 |
двумя зонами контакта фаз | От 3000 до 4000 | ±4 |
| От 4000 и более | ±5 |
Результаты замеров фактических отклонений от перпендикулярности опорных деталей тарелок заносятся в формуляр, заверяемый отделом технического контроля. Формуляр прилагается к паспорту колонного аппарата.
9.2.6. Отклонение по шагу между соседними тарелками не должно превышать ±3 мм.
Отклонение по высоте нижней тарелки не должно превышать:
±3 мм от кромки нижней обечайки корпуса;
±15 мм от кромки верхней тарелки, при этом для промежуточных тарелок оно пропорционально изменяется.
9.2.7. Допуск на минимальное расстояние от сливной перегородки до вертикальной поверхности уголка приемного кармана (успокаивающей планки) - +10 мм и - 5 мм.
Допуск на расстояние от нижней кромки сливной перегородки до поверхности нижележащей тарелки при заглубленном приемном кармане - ±5 мм на 1 м длины перегородки, но не более ±15 мм на всю длину, а при отсутствии заглубленного кармана и наличии успокаивающей планки - ±5 мм.
9.2.8. Уплотнения цельнособранных тарелок и отдельных секций следует выполнять из сальниковой набивки, которая должна состоять из отдельных колец. Стык каждого отдельного кольца следует выполнять с косым срезом. Места стыков в соседних кольцах должны быть смещены по диаметру. Уплотнение секций разборных тарелок к опорной раме, если это предусмотрено стандартом или технической документацией на тарелки, должно выполняться из асбестовой ткани марки АТ-2 по ГОСТ 6102 или паронита по ГОСТ 481.
9.2.9. Попадание щелей решетчатых тарелок на опорные части не допускается.
9.2.10. Качество сборки и правильность установки каждой тарелки должны контролироваться отделом технического контроля.
9.2.11. Прогиб секции (полотна) тарелки после их установки не должен превышать 3 мм, а высота отдельных выпучин - 2 мм.
Секции (полотна) тарелки допускается изготавливать сварными, при этом швы должны быть зачищены с двух сторон заподлицо с основным металлом.
9.3. Тарелки решетчатые
9.3.1. Прогиб секций после их установки не должен превышать 2 мм на 1 м длины, но не более 3 мм на длину секции. Допускаются отдельные выпучины высотой до 6 мм и площадью не более 300х300 мм.
9.3.2. Предельные отклонения размеров щелей (рис. 21) должны быть:
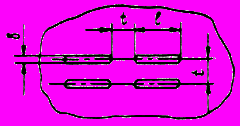
Рис. 21. Размеры щелей в решетчатых тарелках
для расстояния t между щелями

для длины

9.3.3. Расположение щелей должно соответствовать требованиям стандартов и проекта.
9.3.4. Смежные тарелки по высоте колонного аппарата должны быть повернуты в горизонтальной плоскости на 90° относительно друг друга.
9.3.5. На тарелке по кромкам щелей допускается не более 10 несквозных трещин длиной до 5 мм каждая, расположенных в разных местах секций.