Обеспечение производства ЭВМ базовые понятия (сапр/астпп/саит)
Вид материала | Документы |
- Лекция №3 Базовые технологии проектирования сапр/астпп/саит, 46.62kb.
- 05. 13. 12 Системы автоматизации проектирования (машиностроение), 22.99kb.
- Оренбургский государственный университет вопросы для вступительного экзамена в аспирантуру, 61.82kb.
- Тема: Предмет, задачи, базовые понятия финансового менеджмента, 423.89kb.
- Программное обеспечение ЭВМ, 209.59kb.
- Лекция Программное обеспечение ЭВМ. Классификация и развитие, 218.8kb.
- Учебно-методический комплекс по дисциплине конструкторско-технологическое обеспечение, 848.93kb.
- План 1 ЭВМ в управлении производством. 2 Гибкие производственные системы, 326.3kb.
- Лекция: Информационное обеспечение ис: Информационное обеспечение ис. Внемашинное информационное, 314.22kb.
- Сапр 1 Общие положения, 684.54kb.
1. Выбор конструктивного использования компонентов и создание топологии.
На правильную работу электронных схем (систем) влияет технология монтажа компонентов на коммутационном поле, способы размещения и соединения компонентов между собой. Необходимо учитывать межплатные соединения. Для снижения уровня помех компоненты должны группироваться по уровню мощности и рабочим частотам. Печатные проводники должны иметь как можно меньше изгибов и быть более короткими, т.к. в длинных проводниках образуются различные паразитные помехи (емкостные и индуктивные), а также может возникать эффект резонанса. Необходимо выделять отдельные слои для проводников «земля» и «питание», а также контролировать ширину печатных проводников и зазоры между ними. Для предотвращения повреждения компонентов статическими зарядами, которые возникают при соприкосновении рук с печатной платой, проводники и компоненты располагают на достаточном расстоянии от краев платы. целесообразно, если позволяет пространство платы, рядом с сигнальными проводниками проводить защитные проводники, обеспечивающие утечку заряда на землю.
2. Производственные дефекты компонентов
- Закоротка контактов конденсаторов гибридной микросхемы.
- Различные перемычки.
Для устранения этих дефектов производится испытание компонентов на воздействие температуры пайки, чтобы выявить и отбраковать изделия с избыточной паяльной пастой.
3. Экранирование системы
Применяется для снижения воздействия электромагнитных помех. Принцип работы экрана состоит в поглощении или отражении электромагнитных и электростатических полей. На низких частотах магнитное поле поглощается, на высоких – отражается. Для защиты от низкочастотных магнитных полей рекомендуется использовать экраны из немагнитных материалов (алюминий, медь и т.д.). материалы с высокой магнитной проницаемостью (железо, железоникелевые сплавы) используются для защиты от высокочастотных электромагнитных полей. Магнитная проницаемость этих материалов снижается с ростом частоты, поэтому они эффективны на высоких частотах.
Для экранирования экран должен быть сплошным вокруг всей системы или устройства. Допускается наличие отверстий диаметром, не превышающем λ/2, где λ – минимальная длина волны сигнала. В противном случае, отверстия играют роль щелевых антенн. Разъемы на плате так же могут выполнять роль антенн и их рекомендуется закрывать поглощающим материалом. Все изолирующие материалы должны иметь достаточную диэлектрическую прочность. Необходимо экранировать кабели, соединяющие данную систему с другой. При этом оплетка кабеля должна иметь качественный контакт с корпусом. Для складирования электронных модулей необходимо использовать пластиковые пакеты с детализированным покрытием, которое имеет высокую стойкость к воздействию высокой температуры и влажности.
4. Оценка предотвращения тепловых повреждений
На начальном этапе проектирования необходимо наряде с анализом электронной схемы проводить тепловой анализ проекта т.к. в системе существуют тепловые потоки от переходов в окружающую среду. Предельная температура переходов для полупроводниковых устройств общего назначения составляет 150ºС. Чем ниже рабочая температура перехода, тем выше надежность устройства. Снизить температуру переходов во время работы устройства можно с помощью специальных теплоотводов, охлаждающих вентиляторов или отверстий для естественной вентиляции. Эти меры применяются и для охлаждения других элементов схемы (конденсаторов, транзисторов, резисторов, реле и т.д.). Дополнительными испытаниями на тепловую нагрузку могут быть электрические нагрузки, которые должны быть выявлены в начале процесса проектирования.
На тепловую нагрузку влияет температура окружающей среды. Для предотвращения влияния рассчитывается рабочий диапазон, а также проводятся тепловые испытания компонентов и всего устройства в целом.
5. Особенности теплового анализа проекта
Тепловой анализ проекта является неотъемлемым этапом проектирования, который выполняется в самом начале процесса проектирования, т.к. на более поздних стадиях проекта наличие теплового воздействия может вызвать пересмотр всего проекта.
- Первым и наиболее важным моментом является выбор таких элементов, которые соответствуют рабочему диапазону температур в заданном техническом задании.
- Равномерное размещение тепловыделяющих элементов на коммутационном поле.
- Установка теплоотводов и организация вентиляции.
К другим рекомендательным действиям по обеспечению нормального теплового режима относят:
- Чувствительный к нагревающим элементам электролитические конденсаторы и полупроводниковые приборы необходимо размещать отдельно от интенсивных источников тепла, таких как проволочные резисторы, мощные диоды, транзисторы, регуляторы напряжения, устанавливаемые на теплоотводах.
- Вокруг теплоотводов должны быть созданы хорошие условия для циркуляции воздуха.
- Необходимо иметь ввиду, что интенсивность охлаждения теплоотвода тем выше, чем больше площадь его поверхности.
- При необходимости можно делать вентиляционные отверстия, диаметр которых не должен приводить к источнику помех.
- Расчет тепловыделения необходимо производить для более жестких условий эксплуатации.
- Необходимо учитывать, что установка теплоотводов и вентиляторов сама по себе поглощает внутреннее пространство устройства, что приводит к ухудшению условий вентиляции.
- Требования к охлаждению должны определяться назначением оборудования и степенью его надежности.
- Расчет тепловых процессов в системе производится с помощью автоматизированных систем, которые обладают необходимыми средствами для моделирования тепловых режимов.
- Как правило, проводится съемка рабочего макета печатной платы с помощью тепловизоров в условиях предельной нагрузки с целью выявления наиболее тепловыделяющих частей и их распределения по площади платы.
При разработке платы необходимо учитывать как тепловые воздействия, возникающие при работе схемы, так и тепловые воздействия, которым будет подвергаться плата или устройство в процессе пайки.
6. Способы оценки надежности и качества функционирования
электронного оборудования
Надежность изделия необходимо прогнозировать до его запуска в производство. Для прогнозирования необходимы следующие данные:
- Обеспеченность инструкциями, измерительными приборами и испытательными стендами.
- Контроль качества материалов, полуфабрикатов и деталей, поставляемых внешними поставщиками.
- Классификация дефектов и качественных характеристик выпускаемых изделий.
- Систематический выборочный контроль изделий по показателям качества.
- Контроль над особыми устройствами и видами производства.
- Наблюдение за нестандартными материалами и учет статуса их годности.
- Проведение специальных испытаний без разрушения испытываемых изделий.
При сопоставлении запланированного качества определенного конструкторско-технологической документацией и качество готового изделия, соответствующая классификация дефектов определяется регламентирующими документами: технологическими инструкциями (карты, маршруты) и инструкциями по приемке изделий, т.е. их проверке, контролю и аттестации. Таким образом формируются требования к стандартизованному уровню качества.
К числу основных стандартизованных оценок качества относят:
- Допустимый процент дефектов на одно изделие, если оно сложное или дефектных изделий на партию из 100 штук, если изделие простое.
- Уровень среднего выходного качества, которое устанавливают на основе расчета плана выборочного контроля или ускоренных испытаний
- Допустимое число взвешенных дефектов, приходящихся на одно изделие.
Для расчета причинных оценок используют:
- Статистические данные за некоторые предшествующие периоды для расчета средних значений параметров качества и обоснования стандартизованных норм.
- Данные, накопленные в процессе опытов, исследований или испытаний для расчета норм качества для изделий и аналогов.
- Значение параметров, характеристик, технические требования, предъявляемые к качеству изделий, в т.ч. данные анализа затрат на обеспечение качества.
Современная практика показывает, что:
- Общий уровень качества изделия при отсутствии стандарта примерно на 25% ниже, чем при действующим стандарте.
- Целесообразно установить стандарт используя данные предшествующих периодов в пределах до 80% от расчетного среднего значения.
- Наиболее предпочтительными для расчета стандартов представляются данные, полученные на основе опытов и испытаний. Стандарты, основанные на технических требованиях, нормах и рассчитанных ранее значениях параметров дают больший выигрыш потребителю и чрезмерно ограничивают производителя.
- Экономически выгодные оценки, нормы и стандарт качества, учитывающие минимум затрат на обеспечение качества, рассчитываются путем поиска рациональных решений в конкретных условиях производства изделий.
Надежность изделия должна обеспечиваться во время всего срока эксплуатации изделия. Динамика процесса эксплуатации изделия представляется тремя фазами:
- Отладка.
Характеризуется коротким периодом времени, резким сокращением числа отказов благодаря замене некачественных деталей и устранению ошибок сборки.
- Эффективная нормальная работа изделия.
Характеризуется длительным временем, включающим гарантийный срок безотказной работы и на этом этапе уровень отказов очень низкий и они носят случайный характер. Этот период определяет ценовую политику производителя и риск потребителя.
- Старение (период ремонта).
Характеризуется высоким уровнем отказов в связи с износом элементов, старением материалов и изменением их прочностных свойств.
Отказ на каждом этапе эксплуатации изделия описывается с помощью отдельных законов распределений случайных величин. Для описания первой фазы наиболее часто используется γ-распределение. Для второй фазы – экспоненциальное распределение, для третьей фазы – нормальное распределение или суперпозиция нормального распределения или экспоненциального распределения.
Для оценки надежности выполняется преобразование распределения для получения плотности распределения вероятностей отказов.
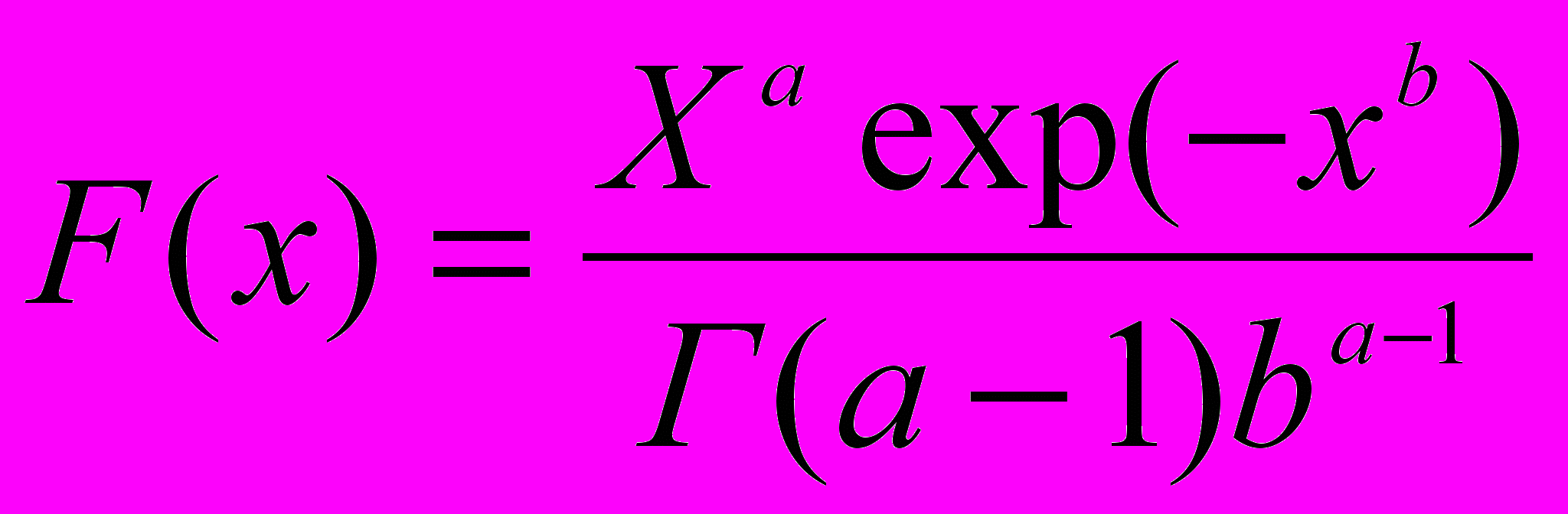
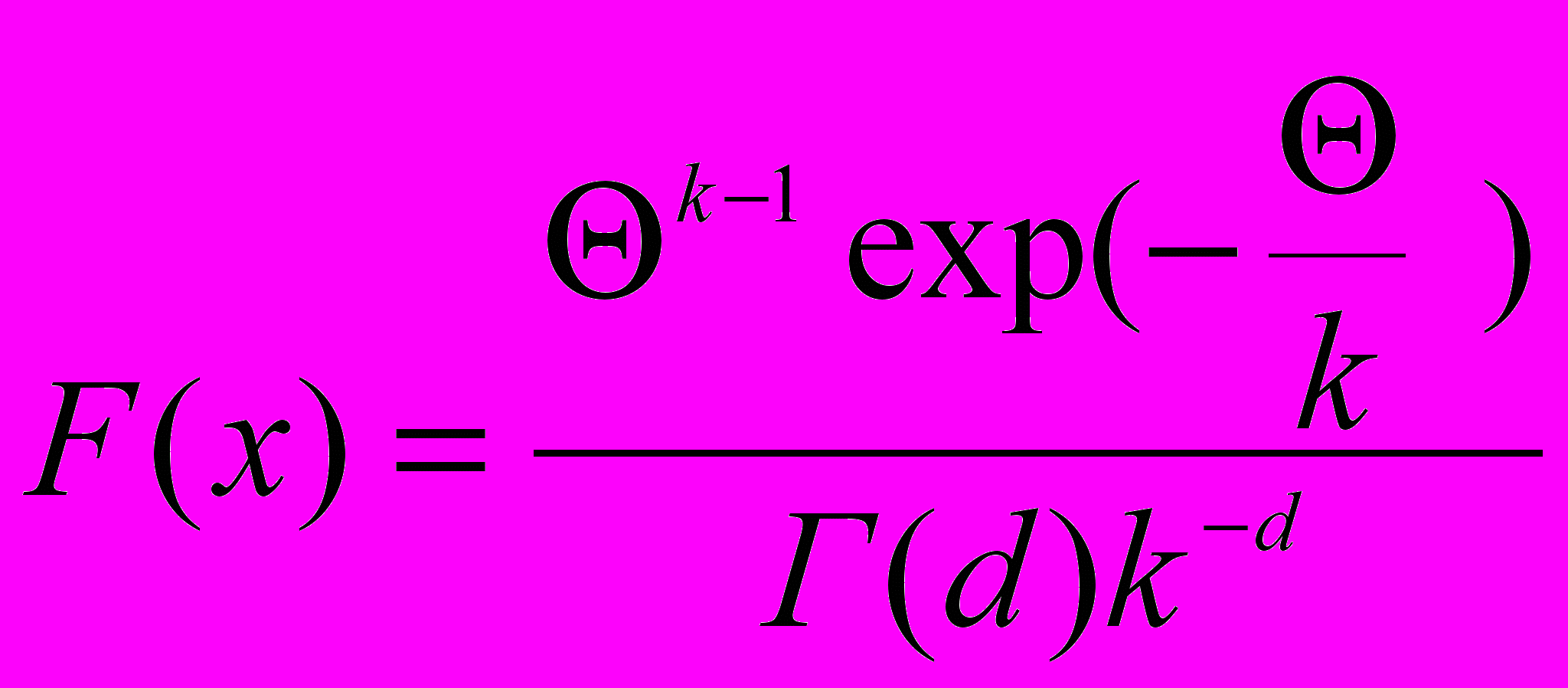
X – случайная величина
a,b – параметры распределения
Г – γ -функция
k – формообразующий параметр кривой распределения.
d – частота появления отказов
Θ – срок служб изделия.
Планом выборочного контроля изделия по сроку службы можно представить планом контроля безотказности, добавив внешнюю нагрузку и приняв в качестве допущения, что после фазы отладки следующая фаза подчиняется экспоненциальному распределению.
При этом возможны следующие варианты организации испытаний с целью оценки безотказности как среднего срока службы изделия:
- Испытания заканчиваются после фиксации заранее установленного срока выявления отказов. При этом используются значения приемлемого и неприемлемого сроков службы изделия для сравнения.
- Испытания заканчиваются по истечению заданного времени Т с заменой или без замены оставшихся элементов. Из нее задаются следующими параметрами:
- Объем выборки N
- Приемлемый срок службы изделия
- Установление времени проведения испытания Т
По результатам испытаний для определенного вида изделий могут составляться сводные данные для различных режимов и периодов эксплуатации. Если далее оценивается надежность изделия, относящегося к типу изделий, для которых уже составлены справочные данные по испытаниям, выбираются соответствующие показатели надежности без нового проведения испытаний, что экономит затраты при производстве изделия.
7. Отбраковочные технологические испытания
как средство повышения надежности партий интегральных микросхем.
К качеству и надежности интегральных микросхем предъявляются высокие требования независимо от их конкретного использования. Подсчитано, что при доли дефектности партии интегральных микросхем в пределах 0,01% (т.е. 100 схем на 1 млн.). Постоянный процент отказов печатных плат, на которых смонтировано 100 интегральных микросхем составляет более 9%. При дефектности партии ИС в пределах 1% выход годных печатных плат составит 63,4%. Надежности ИС при эксплуатации характеризуется кривой зависимости интенсивности отказов λ от времени.
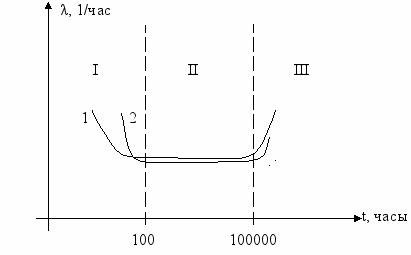
На графике:
Зона I – период приработки (ранние отказы).
Зона II – нормальная работа (случайные отказы).
Зона III – отказ/износ (поздние отказы).
Кривая 1 соответствует случаю, когда мероприятия по обеспечению надежности активно не используются, кривая 2 – когда данные мероприятия используются.
Ранние отказы, как правило, возникают вследствие конструктивно-технологических недостатков. В нормальных условиях работы этот период длится до 1000 часов.
Интенсивность отказов имеет тенденцию к уменьшению при использовании мероприятий по обеспечению надежности и совершенствованию конструкции и технологии интегральных схем.
В настоящее время общепринятыми считаются два направления увеличения надежности выпускаемых интегральных схем:
- Выявление и удаление изделий с отказами действительными и потенциальными из готовой партии до поставки потребителю.
- Устранение причины отказов за счет совершенствования конструкций и технологии изготовления, т.е. воздействия на процесс производства посредством обратной связи, т.е. передача информации от заказчиков к производственникам, что ведет к разработке бездефектной технологии. Этот метод используется чаще как наиболее эффективный. Одним из эффективных способов повышения надежности партии интегральных схем является выходной контроль партии на заводе-изготовителе, т.е. проведении отбраковочных испытаний. Считается, что случайных отказов ИС не бывает. Каждый имеет причину и является следствием приложения нагрузки.
Для того, чтобы отбраковочные испытания были эффективными необходимо знать, какие нагрузки и как они ускоряют появление отказов.
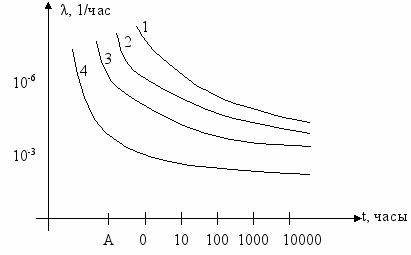
0 – момент поставки заказчику.
1 – кривая без отбраковочных испытаний
2 – только электрические испытания
3 – стабилизирующая тренировка, циклические и температурные испытания и проверка электрических параметров.
4 – тренировка в утяжеленных режимах.
На сегодня применяют такие виды отбраковочных испытаний:
- Контроль внешнего вида.
- Электрические испытания.
- Повышение рабочей температуры.
- Термоциклы.
- Вибрации.
- Одиночные удары.
- Многократные удары.
- Центрифуга.
- Испытания на герметичность.
- Рентгеноскопия.
- Теплоэнерготренировка.
- Энергоциклы.
- Повышенная влажность.
Многие различные по природе дефекты приводят к одним и тем же механическим отказам. Многие одинаковые механизмы отказов ускоряются различными нагрузками, и многие различные механизмы отказов – одними и теми же нагрузками.
Термоциклы – попеременный нагрев и охлаждение. Хорошо выявляют негерметичность корпуса, а также выявляются напряженные места конструкции, склонные к образованию дефектов корпуса ИС.
Кроме тепловых и термоциклических испытаний используют механические испытания с постоянной или изменяющейся нагрузкой, которые могут выявить дефекты монтажа кристалла внутренних соединений, соединений с внешними выводами микросхемы. В общетехнических ОТУ и технических ТУ условиях как правило указывается состав обязательных отбраковочных мероприятий, их режимы и последовательность. Заводы-изготовители ИС расширяют состав испытаний в начальный период серийного производства и снижают его по мере сбора статистики. Может корректироваться вся программа испытаний, но кроме тех, которые указаны как обязательные в ОТУ и ТУ.
Состав отбраковочных испытаний ИС в отечественной промышленности
Во всех отечественных регламентирующих документах по выпуску ИС имеются указания, что в процессе изготовления должны проводиться 100%-е отбраковочные испытания. Состав этих испытаний включает до 20 видов по ОТУ, не менее 10 видов по ОТУ на ИС с приемкой заказчика и не менее 10 видов по требованию на ИС широкого применения. методика и условия испытания описаны в ОСТ.
Виды и методы отбраковочных испытаний:
Вид испытания и технологическая операция | Условия испытаний | Состав испытаний 20ОТУ/ПЗ/ШП |
1. Визуальный контроль кристалла | Увеличение кристалла в 80, 100 и 200 раз | +++ |
2. Контроль монтажа кристалла | По технической документации | +++ |
3. Контроль прочности крепления кристалла | Выборочно по две схемы от каждой установки и далее – через каждые 2 часа | +– – |
4. Контроль прочности сварного соединения | Выборочно по две схемы от каждой установки и далее – через каждые 2 часа | ++– |
5. Визуальный контроль сборки перед герметизацией | Увеличение не менее, чем в 32 раза | +++ |
Термообработка сборки перед герметизацией | 48 часов при 150 градусах | +++ |
7. Герметизация | В условиях контролируемой инертной среде | +– – |
8. Термообработка для стабилизации параметров | 24 часа при верхнем уровне температуры по ТУ | +++ |
9. испытание на воздействие температуры среды | 10 циклов от -60 до 150 ºС (верхнего значения температуры, указанного в ТУ | +++ |
10. Испытания на воздействие линейного ускорения | 30000g | + – – |
11. Контроль свободно перемещающихся частиц внутри корпуса | По ТЗ | + – – |
12. Промежуточные электрические испытания. Контроль статических параметров при нормальных климатических условиях | По ТД | +++ |
13. Электротермотренировка | 240 ч. Для МДП и 168 ч. Для биполярных схем | +++ |
14. Электротермотренировка | 72 ч. Особенности указаны в ТУ | + – – |
15. Заключительные электрические испытания. Проверка статических, динамических параметров и функционирование при нормальных климатических условиях, при пониженной рабочей температуре среды, при повышенной рабочей температуре среды | По ТД | +++ +– – +– – |
16. Рентгеновский контроль | По ТД | +– – |
17. Проверка герметичности | Только для полых корпусов | +++ |
18. Контроль внешнего вида | По ТД | +++ |
В технически обоснованных условиях по согласованию со службой контроля качества допускается иная последовательность отбраковочных испытаний, а вместо проверки статических параметров (параметров при постоянном токе) при крайних значениях температуры проводят проверку параметров при нормальных климатических условиях по нормам, обеспечивающим установленные значения параметров при критических значениях температуры. При разработке регулирующего воздействия, связанного с коррекцией состава методов или условий проведения отбраковочных испытаний, вырабатываемых на основе информации о причинах отказов ИС, учитывается взаимосвязь между причинами отказов и видами отбраковочных испытаний, с помощью которых выявляются эти виды отказов.