Курсовой проект по дисциплине «Физико-химические основы защиты металлов от коррозии» на тему «Разработка технологических схем для нанесения гальванических защитных покрытий и изучения их свойств»
Вид материала | Курсовой проект |
- Методическая разработка урока химии по теме: «понятие о коррозии металлов, способы, 159.91kb.
- Vi методы защиты от коррозии металлов и сплавов, 783.92kb.
- Реферат На тему: Коррозия металлов, 45.45kb.
- «Электрохимические методы защиты металлов от коррозии», 282.48kb.
- «Вызов», 86.73kb.
- Урок в 9-м классе по теме "Коррозия", 149.58kb.
- План-конспект открытого урока по химии в 10 классе. Учитель химии: Берцева, 103.65kb.
- Кандидатские диссертации по проблеме защиты металлов от коррозии с помощью смазочных, 22.96kb.
- Контрольная работа По дисциплине физико-химические свойства и методы контроля качества, 77.41kb.
- Физические свойства вакуумно-плазменных покрытий для режущего инструмента, 338.06kb.
МИНИСТЕРСТВО ОБРАЗОВАНИЯ И НАУКИ УКРАИНЫ
Национальная металлургическая академия Украины
КАФЕДРА ПОКРЫТИЙ, КОМПОЗИЦИОННЫХ МАТЕРИАЛОВ И ЗАЩИТЫ МЕТАЛЛОВ
Курсовой проект
по дисциплине «Физико-химические основы защиты металлов от коррозии»
на тему
«Разработка технологических схем для нанесения гальванических защитных покрытий и изучения их свойств»
Вариант 7
Выполнила:
ст. гр. МК-06
Зельманчук Е.Н.
Проверила:
к.т.н., доц. Гальченко Г.Ю.
Днепропетровск, 2010
Реферат
Курсовой проект содержит:
- листов – 34;
- таблиц – 1;
- рисунков – 2.
-
В работе рассмотрен процесс нанесения покрытия на детали тормозных и топливных систем автомобилей сплавом системы «цинк-никель» во избежание атмосферной коррозии, а также подготовка поверхности под покрытие.
Гальваническое покрытие, обезжиривание, травление, травильный шлам, декапирование, сушка, промывка, цинк-никель, стационарная ванна, подвесочное устройство, электролит, анод, катод, методы контроля, регенерация, нейтрализация.
Индивидуальное задание
Получение цинкникелевых покрытий на трубах диаметром 12 мм, длиной 3 м, используемых для изготовления тормозных и топливных систем автомобилей. Количество труб – 300 штук.
Содержание
ВВЕДЕНИЕ……………………………………………………….……………..5
1. НАЗНАЧЕНИЕ ПОКРЫТИЯ И ВЫБОР ЕГО ТОЛЩИНЫ…….……….6
2. РАЗРАБОТКА ТЕХНОЛОГИЧЕСКОГО ПРОЦЕССА………….……….8
2.1 Технологический процесс………………….………………….…………8
2.1.1 Обезжиривание и травление…………………………….………..9
2.1.2 Промывка………………………………...………………..………9
2.1.3 Снятие травильного шлама……………………………….……..10
2.1.4 Активация (декапирование)………………………………..…….10
2.1.5 Нанесение покрытия………………………………………..……..11
2.1.3 Сушка……………………………………………………….……..14
2.2 Методы контроля качества покрытия……….....……………….……...16
2.2.1 Методы контроля толщины покрытий………………….………16
2.2.2 Методы контроля прочности сцепления покрытий…….……...17
2.2.3 Методы контроля пористости покрытий……………….………18
2.2.4 Методы контроля пластичности покрытий……………….……18
2.2.5 Методы контроля защитных свойств покрытий………….……19
2.3 Расчет расхода воды на промывочные операции……….……….……..20
2.4 Регенерация отработанных растворов, нейтрализация сточных вод…22
3. ВЫБОР ОБОРУДОВАНИЯ…………………………………………………24
3.1 Выбор подвески………………………………………………………...24
3.2 Расчет основных величин………………………………………………25
4. ИЗУЧЕНИЕ ЗАЩИТНЫХ СВОЙСТВ ПОКРЫТИЯ…………………….30
ЗАКЛЮЧЕНИЕ…………………………………………………………………33
ЛИТЕРАТУРА……………………………….…………………………………34
Приложение А
Приложение Б
ВВЕДЕНИЕ
Применение гальванических (металлических) покрытий является одним из наиболее распространенных методов защиты изделий от коррозии в машиностроении. Качество металлических покрытий во многом определяет качество изделий, их долговечность, работоспособность и надежность в эксплуатации. Гальванические покрытия служат не только средством защиты от коррозии, но также и способом повышения износостойкости деталей, электропроводности и других важнейших свойств поверхности.
Из металлических покрытий в мировой практике наиболее широко применяют цинковое. В последние годы в связи с возросшими экологическими требованиями особенно актуальным стал поиск покрытий из сплавов на основе цинка, обладающих в 3-10 раз большей коррозионной стойкостью по сравнению с цинковыми нелегированными покрытиями, способных служить альтернативой токсичным кадмиевым покрытиям.
Одним из способов повышения коррозионной стойкости и улучшения физико-механических свойств цинковых покрытий является легирование их различными металлами. Легированные цинковые покрытия состоят из коррозионностойких сплавов на основе цинка, которые в процессе эксплуатации покрываются устойчивыми защитными пленками сложного состава. В связи с этим коррозионная стойкость легированных цинковых покрытий значительно выше, чем нелегированных.
В последние годы в мировой практике все большее распространение получают процессы цинкования труб в легированном расплаве цинка. При этом чаще всего в качестве легирующих элементов используют Мg, Ni, Аl, Тi.
1 НАЗНАЧЕНИЕ ПОКРЫТИЯ И ВЫБОР ЕГО ТОЛЩИНЫ
Надежность и долговечность работы машин и механизмов во многом определяются эффективностью защиты металлических поверхностей от коррозии. В связи с бурным развитием автомобилестроения возникла необходимость в долговременной защите труб, которые используются в тормозных и топливных системах автомобилей. В мировой практике для этих целей нашли широкое применение металлические покрытия, и в первую очередь цинковое.
Легирование цинковых покрытий другими металлами позволяет значительно улучшить их свойства – защитную способность, механическую прочность, способность к свариванию, окрашиванию лакокрасочными материалами.
По сравнению с чистым цинком цинкникелевые покрытия обладают значительно большей коррозионной стойкостью, что обосновывает выбор его для нанесения на трубы, используемые для изготовления тормозных и топливных систем автомобилей. В Японии цинкникелевые покрытия труб стали широко применяться с 1982 года.
Состав и свойства автомобильных топлив определяют скорость коррозионного поражения системы питания автомобиля. Коррозионная агрессивность автомобильных топлив зависит, главным образом, от количества содержащихся сернистых соединений и их строения. Наибольшее влияние на скорость коррозии оказывают сероводород и элементарная сера.
В настоящее время наиболее широко используют тормозные жидкости на гликолевой основе. Наличие водной фазы в таких жидкостях создает благоприятные условия для возникновения и протекания коррозионных процессов. Жидкости на гликолевой основе являются довольно коррозионно-агрессивными по отношению к другим металлам и сплавам.
Вода в топливе способствует образованию шламов, которые в летний период приводят к засорению трубопроводов, фильтров двигателя, затрудняет запуск двигателя, а в зимнее время может привести к образованию кристаллов льда, из-за чего возможно прекращение подачи топлива в двигатель. Исследования состава и коррозионной агрессивности водных отстоев показало, что одним из наиболее коррозионно-агрессивных компонентов примесей, содержащихся в отстоях, являются ионы хлора, присутствующие в количествах вполне достаточных, чтобы вызвать коррозионное поражение топливных ёмкостей [1].
Выбор толщины наносимого цинкникелевого покрытия проводится согласно ГОСТ 9.303-84. Толщина покрытия, равная 6 мкм, обеспечивает необходимую степень защиты труб, используемых для изготовления тормозных и топливных систем автомобилей при их эксплуатации и долгосрочной службе.
При оптимальной степени легирования (10-15% Ni) однофазные (γ-фаза) покрытия сплавом Zn-Ni обладают в 3-10 раз большей коррозионной стойкостью по сравнению с цинковыми нелегированными покрытиями и являются самыми коррозионноустойчивыми среди сплавов на основе металлов подсемейства железа. Микротвердость покрытий Zn-Ni при 72-88% Zn – 330 кг/мм2, что примерно вдвое выше твердости цинковых покрытий [2].
Итак, для защиты труб, используемых для топливной и тормозной систем автомобилей, наносим цинкникелевое покрытие (88% Zn+12%Ni) толщиной 6 мкм.
2 РАЗРАБОТКА ТЕХНОЛОГИЧЕСКОГО ПРОЦЕССА
При выборе способа и электролита для получения цинкникелевого покрытия руководствуются требованиями, предъявляемыми к покрытию по равномерности, декоративности, чистоте, твердости, величинам внутренних напряжений и пластичности. Определяющими факторами являются также скорость осаждения, зависящая от средней катодной плотности тока, выхода по току и рассеивающей способности электролита. Большое влияние на качество покрытия оказывает подготовка поверхности.
2.1 Технологический процесс
Перед электролитическим цинкованием обычно применяются химические и электрохимические методы подготовки поверхности (обезжиривание, травление, декапирование) и очень редко – механические (шлифование, полирование, галтовки).
Тщательная подготовка поверхности является основным условием получения качественного покрытия. Наличие на поверхности покрываемого металла жировых и оксидных пленок уменьшает силу взаимодействия покрытия с основным металлом, что препятствует их хорошему сцеплению. По своему характеру и прочности связи с основным металлом все загрязнения делятся на два вида:
- загрязнения, не связанные химически с основным металлом – масла, эмульсии, механическая пыль;
- загрязнения, представляющие собой результат химического взаимодействия метало с окружающей средой – оксиды, соли и другие продукты коррозии.
Первый вид загрязнений обычно удаляют путем обезжиривания, чаще всего в щелочных растворах, второй – травлением в растворах кислот [1].
2.1.1 Обезжиривание и травление
Целесообразно применять одновременное травление и обезжиривание, что достигается добавлением в травильный раствор синтанола ДС-10 или сульфанола НП-3.
Рекомендуемый состав для одновременного травления и обезжиривания, г/л:
кислота серная техническая 150-250
ингибитор КИ-1 3-5
синтанол ДС-10 или сульфанол НП-3 3-5
Минеральные масла и смазки плохо удаляются при нормальной температуре. Повышение температуры интенсифицирует процесс удаления жиров, но одновременно ускоряет процесс травления. При наличии на металле жировой пленки и окалины травление может происходить неравномерно, что скажется на внешнем виде поверхности металла. В предложенном составе для одновременного травлении и обезжиривания температуру можно повышать до 60 0С. В нем хорошо удаляются с поверхности металла штамповочные и консервационные смазки, минеральные масла. Продолжительность обработки не должна быть длительной во избежание наводораживания металла. Одновременное обезжиривание и травление может осуществляться в стационарных ваннах и струйным методом. На поверхности деталей при травлении образуется и удерживается шлам, который не растворяется и плохо смывается при последующей промывке в воде.
2.1.2 Промывка
Цель промывки – тщательное удаление с поверхности кислых и щелочных растворов, образовавшихся от предыдущих операций, с тем чтобы в последующую ванну не вносить примеси других веществ. Метод каскадно-противоточной промывки является одним из наиболее эффективных и экономичных. Основан на принципе встречного движения вещества и растворителя, в нашем случае адсорбированного деталью слоя раствора из воды. Устанавливаются три промывочные ванны, свежая вода поступает сначала в первую ванну, из нее переливается во вторую, затем в третью, оттуда – в канализацию. Детали с пленкой адсорбированного раствора промывают сначала в третьей, затем во второй, потом в первой ванне. При этом детали с пленкой концентрированного раствора смываются более загрязненной водой, а по мере разбавления этой пленки – более чистой водой. Это позволяет поддерживать достаточно большую разность концентраций загрязнений между пленкой на детали и подаваемой водой и существенно уменьшить расход воды.
2.1.3 Снятие травильного шлама
Для снятия травильного шлама используют раствор следующего состава: натра едкий, технический марки ТР 50-100 г/л. Обработку ведут при температуре раствора 50-80 0С в течении 1-3 мин. Травильный шлам удаляют химическими либо механическими способами (щетками, дробью, шлифованием) [2,4].
2.1.4 Активация (декапирование)
Активация (декапирование) является завершающей стадией подготовки поверхности перед нанесением гальванических покрытий. При недлительном хранении и транспортировке на поверхности деталей, обезжиренных и протравленных, образуется тонкая пленка окислов, ухудшающая прочность сцепления покрытия с основным металлом. Легкое протравливание металла в слабом растворе кислоты с целью снятия этой пленки и выявления его структуры называется декапированием.
Декапирование проводят в растворе H2SO4 (50-100 г/л) при температуре 15-30 0С в течении 15-60 с. После декапирования детали быстро и тщательно промывают в проточной воде.
После декапирования в результате протравления поверхность металла становится очень активной и легко окисляемой, поэтому детали следует покрывать немедленно защитным покрытием [3,4].
2.1.5 Нанесение покрытия
Осаждение сплавов производят из электролитов, содержащих одновременно ионы нескольких металлов. Соотношение количества металлов в сплаве зависит от концентрации соответствующих металлов в электролите, плотности тока и температуры. Цинкникелевые сплавы обычно осаждают из цианистых, сульфатных, хлоридных, сульфаматных, пирофосфатных и других электролитов. Наиболее широко в промышленности применяют сульфатные и хлоридные электролиты, которые позволяют получать цинкникелевые покрытия в широком диапазоне содержания компонента (Ni) в сплаве при плотностях тока до 100 А/дм2.
Цианистые электролиты малопроизводительны, токсичны. Цианидные электролиты, несмотря на то, что обладают рядом уникальных гальванотехнических характеристик, обусловленных химической, адсорбционной и структурной особенностями как цианид-ионов, так и цианидных комплексов металлов, имеют ограниченные перспективы применения для получения цинкникелевых покрытий. Из цианидных электролитов осаждаются цинкникелевые покрытия только со степенью легирования до 3% Ni, которые по защитной способности не очень сильно превосходят нелегированные. Кроме того, производства, связанные с цианидами, по мере усиления природно-охранных требований, сохранятся только у финансово мощных компаний.
Процесс получения покрытия цинк-никель из кислого электролита отличается определенными сложностями, что делает его менее удобным для применения в промышленных условиях. Цинковые аноды растворяются в кислых хлористых электролитах, вызывая трудности с контролированием концентрации цинка в растворе.
Высокой коррозионной стойкостью обладают цинкникелевые покрытия, содержащие 15-25% Ni. По отношению к стали получаемые покрытия являются катодными. Для осаждения таких сплавов применяют аммиакатный электролит с выходом по току 93-96%. Однако основным недостатком такого электролита является неустойчивость, так как из него улетучивается аммиак. Наибольшей защитной способностью обладают цинкникелевые покрытия, состоящие из γ-фазы с 10-16% Ni.
Поэтому для нанесения на трубы цинкникелевого покрытия используем сульфатный электролит следующего состава, г/л:
цинк сернокислый 150
никель сернокислый 350
натрий сернокислый 60
Режим осаждения:
- рабочая плотность тока при перемешивании, А/дм2…………30-50
- температура, 0С…………………………………………………..50
- перемешивание (проток электролита), м/с……………….…….1
- фазовый состав покрытия……………………………………….. γ-фаза
Сульфат цинка и сульфат никеля являются компонентами, содержащими осаждаемые металлы – цинк и никель. Сульфат натрия добавляется для увеличения электропроводности раствора.
Приготовление сульфатного электролита осуществляется следующим способом: все компоненты растворяют в воде в отдельных емкостях при температуре 60-70 0С, после этого заливают через фильтр в рабочую ванну [1,4].
Неполадке в работе ванны нанесения цинкникелевого покрытия представлены в таблице 1 [2,3].
Таблица 1
Основные неполадки в работе ванны
Характер неполадок | Причина неполадок | Способ устранения |
Образование крупнокристаллических покрытий и наростов на острых кромках и углах деталей | Защелачивание электролита; повышенная плотность тока; пониженное содержание солей цинка и никеля |
|
Шероховатость покрытия | Накопление в электролите механических примесей | Отфильтровать электролит |
Образование «пузырей» в покрытии (отслаивание) | Чрезмерное наводороживание металла при подготовительных операциях; пониженная кислотность |
|
Частичное покрытие деталей сплавом при хорошем качестве покрытия | Недостаточное обезжиривание деталей; детали взаимно экранируются на подвеске; отсутствие контакте подвески со штангой |
|
- Сушка
Способ сушки – в сушильном шкафу или сушильной камере с циркуляцией нагретого воздуха. Температура 60-110 0С для высыхания.
Для сушки деталей в гальванических цехах применяют сушильные шкафы с паро- или электрообогревом, центрифуги, сжатый воздух, опилки, горячую воду и т.п.
Сушильный шкаф состоит из стального каркаса, к которому прикреплены стальные листы. Между листами проложена теплоизоляционная прокладка (асбест, стекловата и т.п.). Обогрев производится путем искусственной циркуляции горячего воздуха. Циркуляция осуществляется вентилятором, который нагнетает воздух, нагретый в калориферах, в нижнюю часть шкафа. Воздух, проходя через детали вверх, просушивает их и всасывается вентилятором и направляется вновь через калориферы вниз. Свежий воздух поступает в установку через патрубок всасывающего отверстия вентилятора. Удаляемый воздух выбрасывается через воздуховод, снабженный дроссельной заслонкой для регулирования поступления свежего воздуха [3,5].
Технологический процесс представлен на рис. 1.
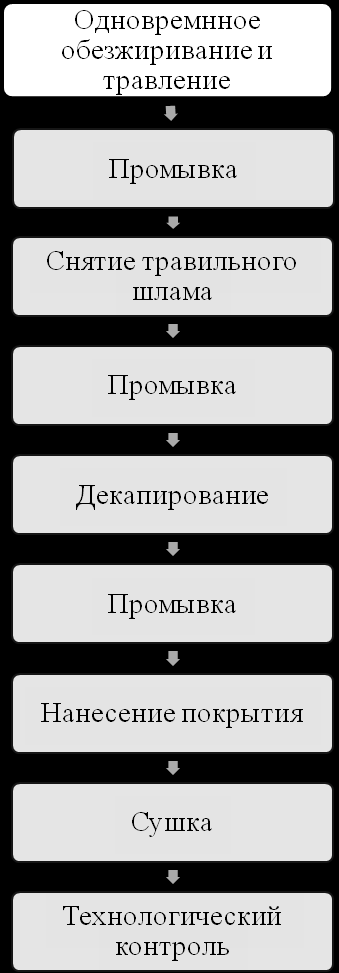
Рис. 1. Технологический процесс нанесения цинкникелевого покрытия
2.2 Методы контроля качества покрытия
Контроль качества покрытия проводят согласно ГОСТ 9.302-88. Контроль качества покрытий проводят на наружной поверхности детали, на доступных участках, не имеющих накатки, удаленных от резьбы, отверстий.
Перед проведением контроля толщины, пористости, защитных и функциональных свойств покрытий детали с покрытиями выдерживают до температуры помещения, в котором проводят контроль, и обезжиривают этиловым спиртом или пастой из окиси магния. После обезжиривания пастой детали промывают дистиллированной водой и высушивают фильтровальной бумагой или на воздухе.
- Методы контроля толщины покрытий
Профилометрический метод
Метод основан на измерении уступа, образованного краем покрытия с основным металлом, с помощью металлографических микроскопов. Метод применяют для однослойных покрытий, если значение шероховатости основного металла Rа не превышает 25 % толщины покрытия. Относительная погрешность метода ±10 %.
Уступ для измерения толщины покрытия может быть получен в процессе нанесения покрытия изоляцией любым способом участка основного металла или растворением участка покрытия с предварительной изоляцией остальной поверхности покрытия. Толщину покрытия измеряют после удаления изоляционного материала.
Раствор для снятия покрытия имеет такой состав:
кислота соляная (плотность 1,19 г/см3) 500 см3/дм3
уротропин 5 г/дм3
Толщину покрытия (Н) в микрометрах вычисляют по формуле

где h — высота уступа, мм;
p — увеличение.
Метод вихревых токов
Основан на регистрации взаимодействия собственного электромагнитного поля и преобразователя поля с электромагнитным полем вихревых токов, наводимых этим преобразователем в детали и зависящих от электрофизических и геометрических параметров основного металла и покрытия. Относительная погрешность метода ±5%.
- Методы контроля прочности сцепления покрытий
Методы основаны на различии физико-механических свойств металла покрытия и основного металла.
Метод нанесения сетки царапин (метод рисок)
Метод применяют для покрытий толщиной не более 20 мкм. На поверхности контролируемого покрытия острием (твердость материала острия должна быть выше твердости покрытия) наносят не менее трех параллельных рисок с расстоянием между ними от 2 до 3 мм и перпендикулярно к ним также не менее трех параллельных рисок. Риски наносят в одном направлении острием, установленным под углом 300, глубиной до основного металла. После контроля не должно быть отслаивания покрытия между линиями и в сетке квадратов.
Метод полирования
Заключается в полировании поверхности покрытия в течении 30-60 с при окружной скорости круга 20-30 м/с. Если на поверхности имеются участки с недостаточной адгезией, то выделяемое тепло при полировании вызывает отслаивание цинкникелевого покрытия от подложки.
- Методы контроля пористости покрытий
Методы основаны на взаимодействии основного металла или металла подслоя с реагентом в местах пор с образованием окрашенных соединений.
Методы наложения паст или фильтровальной бумаги не дают достаточно надежных результатов. Поэтому, принимая во внимание анодный характер цинковых покрытий, применяют метод анодной обработки. Он заключается в том, что испытуемый образец выдерживают 30-60 с в качестве анода в электролите определенного состава. В качестве катода применяют свинец. На контролируемой поверхности подсчитывают число синих точек, соответствующих числу пор. Среднее число пор вычисляют по формуле

где Nобщ – общее число пор на контролируемой поверхности;
S – площадь контролируемой поверхности, см2.
- Методы контроля пластичности покрытий
При испытании на пластичность цинкникелевые покрытия наносят на мягкий, пластичный материал (бронзу). Образец сгибают по шаблону. Пластичность покрытия определяют по величине удлинения образца до появления трещин в покрытии и вычисляют по формуле
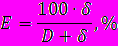
где


- Методы контроля защитных свойств покрытий
Защитную способность цинкникелевых покрытий определяют с помощью ускоренных коррозионных испытаний, в условиях, подобных атмосферной коррозии. Кроме того, данные методы позволяют выявить имеющиеся дефекты покрытий, а также их поведение в конкретных коррозионных средах. Одним из таких методов является метод испытаний при воздействии нейтрального соляного тумана.
Сущность метода заключается в ускорении коррозионного процесса повышением температуры окружающей среды и введением в атмосферу 3% раствора хлорида натрия. Распыление соляного тумана проводят в течении 15-30 минут через каждые 15-45 минут. Продолжительность испытания устанавливают в программе испытаний в соответствии с требованиями, предъявляемым к испытуемым образцам. О защитной способности покрытия судят по количеству очагов коррозии основного металла, появляющихся на 10 см длины изделия.
Метод ускоренных испытаний в камере соляного тумана можно проводить и для изделий, работающих в промышленной атмосфере. Солевой туман образуется распылением 3% раствора хлорида натрия при температуре 300 К или 5% раствора NaCl с добавкой уксусной кислоты до рН=3,2 при температуре 303 К. Распыление проводят в течении 15-30 минут. Продолжительность испытаний колеблется от 24 до 96 часов. О защитной способности покрытия судят по количеству очагов коррозии основного металла [2, 4, 6].
- Расчет расхода воды на промывочные операции
Промывочные операции имеют большое значение для качества покрытий и влияют на экономические показатели производства.
Для определения расхода воды на промывку деталей пользуются формулой (по ГОСТ 9.402-2004)

где


n – количество ступеней промывки;

Критерий окончательной промывки


где


Для определения расхода воды на промывочные операции произведем расчет расхода воды после соответственных технологических операций.
- Рассчитаем расход воды после первой технологической операции – одновременное обезжиривание и травление:
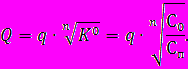
Удельный выноса раствора из ванны

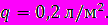
Основной компонент при одновременно обезжиривании и травлении – кислота серная техническая (см. п. 2.1.1), следовательно
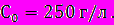

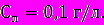

Аналогичным образом проводим расчет расхода воды после снятия травильного шлама (


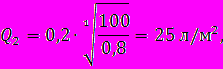
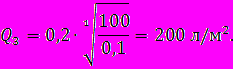
Таким образом, расход воды на промывочные операции составит:

- Регенерация отработанных растворов, нейтрализация сточных вод
Сточные воды гальванического производства содержат растворенные минеральные кислоты (серную, соляную и др.) или растворенные основания (едкий натр, едкий калий, гидроксид аммония и др.), а также растворенные соля тяжелых металлов (железа, цинка, никеля и др.). Сброс этих сточных вод в открытые водоемы или в городские канализационные сети без соответствующей обработки и очистки недопустим. Содержащиеся в производственных сточных водах химические продукты имеют значительную ценность, и их извлечение и повторное использование в производстве может дать значительный экономический эффект.
При нейтрализации сточных вод происходит удаление из них как свободных кислот и оснований, так и ионов тяжелых металлов в результате их перевода в труднорастворимые соединения.
Нейтрализация кислых сточных вод проводится с помощью различных щелочных реагентов (гидроксид кальция, натрия, магния), нейтрализация щелочных сточных вод – с помощью растворов минеральных кислот.
Нейтрализацию сточных вод, содержащих ионы тяжелых металлов (Zn, Ni), проводят до конечной величины рН в пределах 8,0-9,5 соответственно для Zn и Ni.
При нейтрализации кислых сточных вод известковым молоком, содержащим значительное количество известняка, а также растворами соды ионы цинка и никеля осаждаются в виде основных карбонатов. Последние труднее растворяются в воде, чем соответствующие гидроксиды. Поэтому при образовании основных карбонатов происходит более полное удаление из воды ионов цинка и никеля.
Нейтрализация сточных вод производится на установках непрерывного или периодического действия. В состав установки входят: усреднитель, реакционная камера (реактор), резервуары для приготовления и хранения рабочих растворов реагентов, дозировочные устройства, приборы для управления процессов очистки, отстойник для осветления обработанной воды, узел обезвоживания образующихся осадков.
Извлечение цинка. Комбинированный катионитно-анионитный метод очистки сточных вод от цинка имеет следующую схему: стоки пропускают через колонку, заполненную катионитом КУ-2 в Nа-форме, его регенерируют раствором хлорида натрия. Далее фильтрат направляют в колонку анионита АВ-17 в Сl-форме, в колонке цинк поглощается в виде анионного комплекса. Для регенерации аниоиитов используют воду. Цинк (в виде хлорида цинка) возвращается в производство [4].
- ВЫБОР ОБОРУДОВАНИЯ
- Выбор подвески
Назначение подвесочных приспособлений заключается не только в создании опоры деталей в ванне, но и в подводе к ним тока. Размеры всех подвесочных приспособлений, независимо от их типа, выбираются так, чтобы расстояние от дна ванны (или от металлического змеевика на дне) до нижнего края висящих на приспособлении деталей было не менее 100—200 мм, а расстояние от верхнего края деталей до зеркала раствора — не менее 50 мм. Необходимость зазора от низа подвесочного приспособления до дна вызвана опасностью взмучивания шлама со дна ванны и часто наблюдающимся снижением температуры около дна ванны при отсутствии перемешивании.
Подвесные крюки. Подвесной крюк подвесочного приспособления рекомендуется выполнять аналогично подвесному крюку для анода, т. е. загнутым по трем сторонам квадрата. Преимущество такого прямоугольного крюка по сравнению с загнутым по дуге круга состоит в том, что контакт со штангой осуществляется не по одной линии или точке, а по двум, что заметно улучшает условия перехода тока. Наиболее удобным, экономичным и простым для изготовления материалом подвесочных приспособлений для катодных процессов является железо (малоуглеродистая сталь). Существенным дефектом железа является его ржавление во влажном воздухе гальванического цеха. Вызванное этой коррозией повышение переходного сопротивления контактов легко устраняется предварительным покрытием всего подвесочного приспособления и, в первую очередь, его подвесных крюков каким-нибудь гальванически осажденным подходящим металлом, лучше всего никелем [7,8,9].
- Расчет основных величин
Время τ, необходимое для обработки деталей на данной операции технологического процесса, определяем по формуле

где


Для гальванических покрытий технологическое время определяется по формуле

где





Рассчитаем плотность осаждаемого сплава


Рассчитаем электрохимический эквивалент осаждаемого сплава:

Катодная плотность тока


Значения плотностей и электрохимических эквивалентов цинка и никеля взяты из справочного источника [3, табл.2, табл. 14].
Рассчитаем технологическое время:

Вспомогательное время

К перекрываемому вспомогательному времени относят время, в течение которого за период работы основной ванны выполняются некоторые операции, например: протирка деталей, изоляция, монтаж деталей на приспособление, демонтаж их. Загрузку деталей в основную ванну и выгрузку их из нее нельзя выполнять во время работы основной ванны. Поэтому время на загрузку деталей в основную ванну и выгрузку их из ванны относят к неперекрываемому вспомогательному времени. Для стационарных ванн

Примем

Таким образом, получим, что

Время, необходимое для покрытия годовой программы


где




Количество деталей П, загружаемых одновременно во все ванны, рассчитываем по формуле
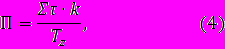
где



Определим


где





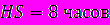

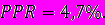
Подставив значения в формулу (5), получим

Теперь определим количество загружаемых деталей по формуле (4)

Количество ванн по покрытию определяем по уравнению
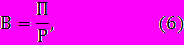
где




При определении габаритов стационарных ванн расчетным путем внутренние ее размеры (в мм) вычисляем при помощи следующих формул:

где








Ширина ванны W:

где W – ширина ванны, мм;











Высота ванны Н:

где

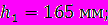







Напряжение на ванне вычисляем по формуле

где


где



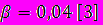



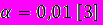


Тогда получим, что


- ИЗУЧЕНИЕ ЗАЩИТНЫХ СВОЙСТВ ПОКРЫТИЯ
Цинкникелевые покрытия все чаще применяют для замены токсичных и дорогостоящих кадмиевых и кадмийтитановых покрытий. Их преимуществом является более низкая стоимость, нетоксичность и меньшее наводороживание стальной подложки при их нанесении. При соблюдении специальных требований после нанесения цинкникелевых покрытий даже на высокопрочные стали их механические свойства не ухудшаются.
При испытаниях в камере соляного тумана в течение 3000 ч образцы с цинкникелевым покрытием показали значительно большую защитную способность, чем образцы с кадмийтитановым покрытием (рис.2).
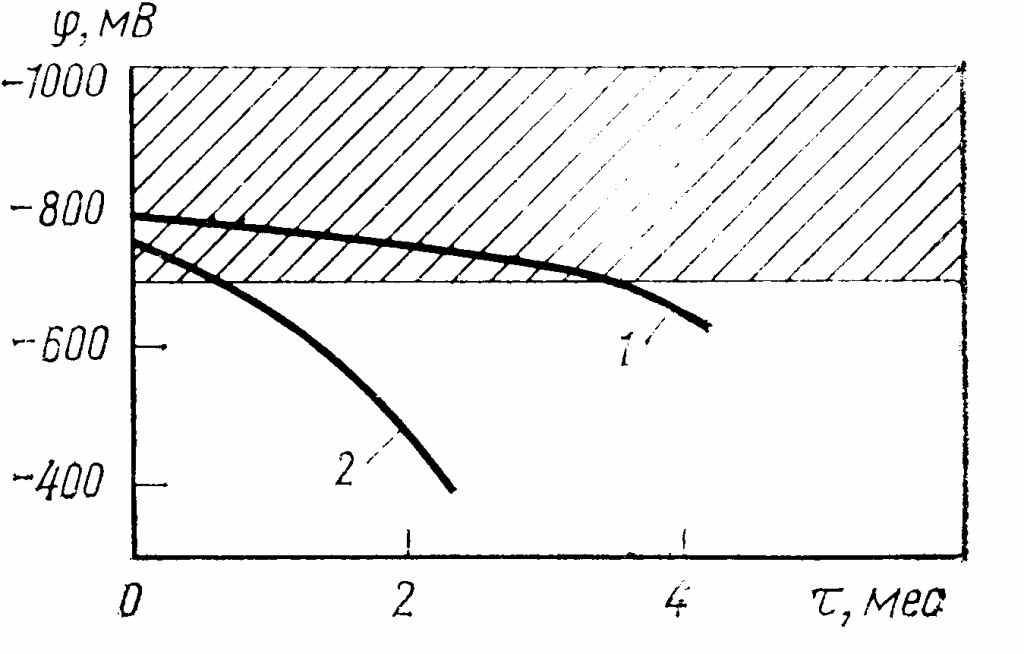
Рис. 2. Зависимость электродных потенциалов цинкникелевого (1) и кадмийтитанового (2) покрытий от продолжительности испытаний в камере соляного тумана. Заштрихована область протекторной защиты стали от коррозии
Электродный потенциал цинкникелевого покрытия после 4 мес. испытаний сдвинулся в положительную область весьма незначительно (на 100—120 мВ), в то время как протекторное действие кадмийтитанового покрытия прекратилось после испытаний в течение 14 суток. На образце с цинкникелевым покрытием толщиной 12,5 мкм первые очаги коррозии подложки появились после 7604 ч испытаний, в то время как кадмийтитановое покрытие прокорродировало почти полностью за 1848 ч.
Многочисленные экспериментальные данные указывают на то, что цинкникелевые покрытия зачастую обеспечивают более лучшую защиту изделий от коррозии в целом ряде случаев. Установлено, что при коррозионных испытаниях в камере соляного тумана при температуре 35 °С ржавчина на образцах с цинковым покрытием толщиной 12,5 мкм появляется после 72—168 ч, а на образцах с цинкникелевым покрытием той же толщины после 240—336 ч.
Методом рентгеновской фотоэмиссионной спектроскопии установлено, что белые продукты коррозии цинкникелевого покрытия, образующиеся на поверхности этого покрытия, состоят главным образом из смеси Zn(ОН)2 и ZnСO3. Слой покрытия, находящийся под слоем продуктов коррозии, обогащается никелем, что облегчает его пассивацию. При испытаниях в камере соляного тумана продолжительность периода до появления ржавчины при содержании в покрытии 10—16% Ni, оказывается наибольшей (в 6—10 раз, чем у цинкового покрытия).
Кроме того, сталь с цинкникелевым покрытием обладает лучшей способностью к точечной сварке.
При коррозионных испытаниях цинкникелевых покрытий, независимо от условий их нанесения или метода испытаний, часто наблюдается локальное коррозионное разрушение – питтинг или растрескивание покрытия. Было установлено, что в покрытиях с содержанием более 25 % Ni микротрещины появлялись в момент нанесения покрытия. В покрытиях с меньшим содержанием никеля трещины появлялись только после коррозионного воздействия агрессивной среды. Одной из причин возникновения трещин в покрытии, содержащем более 25 % Ni, является неравномерное распределение в слое покрытия цинка и никеля, причем участки с повышенным содержанием никеля являются центрами зарождения трещин. В покрытиях с меньшим содержанием легирующего компонента основной причиной растрескивания являлись высокие внутренние напряжения.
Испытания цинкникелевых (8%Ni) покрытий в средах, имитирующих пластовые воды ряда нефтеносных горизонтов, показали, что их коррозионная стойкость в этих условиях в 1,7—2,4 раза выше, чем нелегированного цинкового покрытия. Высокую коррозионную стойкость показали цинкникелевые покрытия в условиях контактной коррозии и движущейся высокоминерализованной пластовой воде. Образцы с цинкникелевым покрытием лучше противостоят и сероводородному растрескиванию по сравнению с образцами, защищенными нелегированным цинковым покрытием.
Повышенные коррозионная стойкость и защитная способность цинкникелевого покрытия обусловлены характером образующихся на его поверхности продуктов коррозии. Их формирование на этом покрытии происходит с участием никеля и его соединений, что способствует созданию достаточно плотных, прочносцепленных с покрытием защитных слоев, экранирующих доступ коррозионных агентов к поверхности покрытия.
Многослойные гальванические покрытия используют для защиты от коррозии труб диаметром 6 – 12 мм для автотракторной промышленности.
Сравнительные коррозионные испытания образцов труб диаметром 12 мм с гальваническим покрытием в камере соляного тумана показали высокие защитные свойства. Защитные свойства такого покрытия в 1,4 раза выше, чем однослойного цинкового покрытия.
ЗАКЛЮЧЕНИЕ
Перспективность использования легированных цинковых покрытий для деталей крепежа автомобильного двигателя связана с тем, что они в процессе работы двигателя испытывают нагрев до 120 0С. В этих условиях хроматированные цинковые покрытия быстро теряют свою защитную способность из-за дегидратации хроматного слоя, тогда как покрытия на основе сплавов цинка оказываются в этих условиях значительно более устойчивыми.
Хотя никель более дорогой, чем цинк, однако, благодаря тому, что небольшие добавки никеля значительно повышают срок службы оцинкованных изделий, применение цинкникелевых покрытий является экономически целесообразным.
ЛИТЕРАТУРА
- Цинкование. Справ. изд. Проскуркин Е.В., Попович В.А., Мороз А.Т. М.: Металлургия, 1988. – 528 с.
- Гальванические покрытия в машиностроении. Справочник. В 2-х томах/Под ред. М.А. Шлугера. – М.: Машиностроение, 1985.
- Ямпольский А.М., Ильин В.А. Краткий справочник гальванотехника. – Л.: Машиностроение, 1981. – 269 с.
- Гальванотехника. Справ. изд. Ажогин Ф.Ф., Беленький М.А., Галь И.Е. и др. М.: Металлургия, 1987. – 736 с.
- Оборудование гальванических цехов. Вайнер Я.В., Кушнарев Б.П. Л.: Машиностроение, 1971. – 128 с.
- Защита от коррозии. т.1 Покрытия металлические и неметаллические неорганические. – М.: Изд-во стандартов, 1990.
- Лобанов С.А. Практические советы гальванику. – Л.: Машиностроение, 1983. – 248 с.
- Мельников П.С. Справочник по гальванопокрытиям в машиностроении. – М.: Машиностроение, 1979. – 296 с.
- Дасоян М.А. Технология электрохимических покрытий. – Л.: Машиностроение, 1989. – 391 с.