Чинні методичні вказівки розроблено відповідно до вимог дсту 3008-95 „Документація. Звіти в сфері науки І техніки. Структура І правила оформлення
Вид материала | Документы |
- Реферат (при необхідності), 348.6kb.
- 1 Вимоги до структури й оформлення кваліфікаційних робіт розроблено на базі Основних, 383.62kb.
- Дипломний, 697.2kb.
- Державний стандарт україни документація. Звіти у сфері науки І техніки структура, 449.89kb.
- Розроблено на підставі дсту 3008-95 «Документи. Звіти у сфері науки І техніки. Структура, 147.61kb.
- Стандарт університету, 259.5kb.
- И авторефератам дисертаций, 319.62kb.
- Государственный стандарт украины документация. Отчеты в сфере науки и техники структура, 478.5kb.
- Міністерство освіти та науки україни національний технічний університет “Харківський, 548.54kb.
- Основні вимоги до рефератів аспірантів (здобувачів), 28.39kb.
Додаток Б
Міністерство освіти і науки України
Вінницький національний технічний університет
Інститут автоматики, електроніки та комп’ютерних систем
управління
Кафедра електроніки
ТЕХНОЛОГІЯ ВИГОТОВЛЕННЯ СЕНСОРА ВОЛОГОСТІ
НА ОСНОВІ ТРАНЗИСТОРНОЇ СТРУКТУРИ
З ВІД’ЄМНИМ ОПОРОМ
Пояснювальна записка
з дисципліни ”Технологічні основи електроніки”
до курсової роботи за спеціальністю
“Електронні прилади та пристрої”
08-05.ТОЕ.013.00.000 ПЗ
Керівник курсової роботи
к.т.н., доц. Прокопова М. О.
( прізвище та ініціали)
________________________________
(підпис)
”___” ____________200_ р.
Розробив студент гр. ЕП-06
_____________Звягін О. С.
(підпис, прізвище та ініціали)
”___” ____________200_ р.
Вінниця ВНТУ 200_
Додаток В
Міністерство освіти і науки України
Вінницький національний технічний університет
Інститут автоматики, електроніки та комп’ютерних систем
управління
ЗАТВЕРДЖУЮ
Зав. кафедри ЕЛ, проф., д.т.н.
______________ В. С. Осадчук
(підпис)
„___” ______________ 200_ р.
ІНДИВІДУАЛЬНЕ ЗАВДАННЯ
на курсову роботу з дисципліни „ Технологічні основи електроніки ”
студенту Звягіну О. С. факультету ФЕЛТ групи ЕП-06
ТЕМА: “Технологія виготовлення сенсора вологості на основі транзисторних структур з від’ємним опором ”
Вихідні дані:
- гібридна технологія;
- напруга живлення, Uж = 5В;
- напруга керування, Uк = 5В.
Зміст ПЗ до курсової роботи
Індивідуальне завдання
Анотація
Вступ
1. Аналіз теоретичної бази сенсорів вологості
2. Конструкція та принцип роботи сенсора вологості на основі транзисторної структури з від’ємним опором
3. Технологія виготовлення сенсора вологості та розрахунок основних параметрів
Висновки
Перелік посилань
Дата видачі ”____” _________ 200_ р. Керівник _________________
(підпис)
Завдання отримав _________
(підпис)
Додаток Г
ЗМІСТ
АНОТАЦІЯ……………………………………………………………….… | 4 |
ВСТУП………………….…………………………………………………... | 5 |
1 АНАЛІЗ ТЕОРЕТИЧНОЇ БАЗИ СЕНСОРІВ ВОЛОГОСТІ……....... | 6 |
2 КОНСТРУКЦІЯ ТА ПРИНЦИП РОБОТИ СЕНСОРА ВОЛОГОСТІ НА ОСНОВІ ТРАНЗИСТОРНОЇ СТРУКТУРИ З ВІД’ЄМНИМ ОПОРОМ…………………………………………………………………... 3 ТЕХНОЛОГІЯ ВИГОТОВЛЕНЯ СЕНСОРА ВОЛОГОСТІ ТА РОЗРАХУНОК ОСНОВНИХ ПАРАМЕТРІВ………………………... 3.1 Технологічний маршрут……………………………………………. 3.2 Опис основних операцій гібридної технології ………………….. 3.3 Розрахунок розмірів плівкових елементів ………………………... | 14 19 19 22 26 |
ВИСНОВКИ…………………………………………………………….….. | 28 |
ПЕРЕЛІК ПОСИЛАНЬ…………………………………………………….. | 29 |
Додаток Д
АНОТАЦІЯ
Об’єктом дослідження є мікроелектронний частотний сенсор вологості на основі двох КМДН–транзисторів з від’ємним опором. Проведено аналіз сучасного стану існуючих сенсорів вологості та визначено, що новим актуальним напрямком в розробці мікроелектронних сенсорів вологості є створення частотних сенсорів на основі реактивних властивостей напівпровідникових структур з від’ємним опором. Розглянуто конструкцію та принцип роботи приладу, визначені основні галузі використання. Розроблено оптимальний маршрут виготовлення схеми сенсора вологості за гібридною технологією. Проведено розрахунок розмірів на платі плівкових резисторів та конденсаторів, який перевірено за допомогою математичного пакета Mathcad 2001 Professional.
Додаток Е
ВСТУП
Актуальність теми
При вимірюванні рівня відносної вологи і виконанні різних фізико-технологічних, біологічних та хімічних процесів висувають підвищені вимоги щодо характеристик сенсорів вологості, а саме: економічність, надійність, точність та чутливість до вимірювального параметра, малі габаритні розміри, маса та енергоспоживання, інформативна, конструктивна і технологічна сумісність з мікроелектронними засобами обробки інформації та можливість виготовлення за стандартною груповою інтегральною технологією. Перспективним науковим напрямком є розробка та створення первинних перетворювачів, які реалізують принцип перетворення «вологість-частота», на основі реактивних властивостей напівпровідникових структур з від’ємним опором.
Мета дослідження
Метою роботи є розробка оптимального технологічного маршруту виготовлення сенсора вологості на основі КМДН-транзисторів за гібридною технологією.
Задачі дослідження :
- проаналізувати прилади для вимірювання вологості, розглянути їх принцип дії, основні переваги та недоліки;
- роздивитись конструкцію та принцип роботи сенсора вологості на основі КМДН-транзисторів з від’ємним опором, визначити його основні галузі використання;
- розробити технологічний маршрут виготовлення сенсора вологості на основі КМДН - транзисторів за гібридною технологією;
- розрахувати розміри на платі плівкових елементів сенсора вологості.
Об’єктом дослідження є мікроелектронний частотний сенсор вологості на основі двох КМДН–транзисторів з від’ємним опором.
Структура курсової роботи
Курсова робота складається з трьох основних розділів. В першому розділі наведено аналіз теоретичної бази сенсора вологості та обумовлено актуальність розробки приладів на основі транзисторної структури з від’ємним опором. У другому розділі розглянуто конструкцію та принцип роботи сенсора вологості на основі КМДН-транзисторів, визначено його основні галузі використання. Третій розділ містить технологічний маршрут, опис основних операцій гібридної технології та розрахунок розмірів плівкових елементів схеми сенсора вологості.
Додаток Ж
ВИСНОВКИ
1. Проведено аналіз сучасного стану існуючих сенсорів вологості, які займають домінуюче місце у вимірювальній техніці серед первинних перетворювачів різного типу, до яких на сучасному етапі розвитку науки та техніки висувають підвищені вимоги, що водночас пов’язані з автоматизацією технологічних процесів. Показано, що за останні десятиріччя спостерігається інтенсивний розвиток сенсорів вологості на основі мікроелектроніки. Новим напрямком в розробці мікроелектронних сенсорів вологості є створення частотних сенсорів на основі реактивних властивостей напівпровідникових структур з від’ємним опором.
2. Розглянуто конструкцію та принцип роботи сенсора вологості на основі транзисторної структури. Визначено, що найбільш оптимальною для виготовлення приладу є гібридна тонкоплівкова технологія.
3. Розроблено технологічний маршрут виготовлення сенсора вологості за гібридною технологією. Наведено опис основних операцій технологічного процесу, таких як електронно-променеве випаровування, літографія, монтаж навісних компонентів, термокомпресія та корпусна герметизація. Для них визначені режими, оснастка та обладнання, основні види браку та техніка безпеки.
4. Розраховано плівкові резистори та конденсатори сенсора вологості на основі транзисторної структури з від’ємним опором. Достовірність розрахунків перевірено за допомогою математичного пакета Mathcad 2001 Professional.
Додаток И
ЛІТЕРАТУРА
1. Осадчук В. С., Осадчук О. В., Крилик Л. В. Сенсори вологості. – Вінниця: УНІВЕРСУМ – Вінниця, 2003. - 210с.
2. Патент 46385 Україна, МКІ G 01 N 27/12. Вимірювач вологості / В. С. Осадчук, О. В. Осадчук, Л. В. Крилик (Україна). - №2001074689; Заявлено 05. 07. 2001. Опубл. 15. 05. 2002. Бюл. №5.
3. Осадчук В. С., Осадчук О. В., Крилик Л. В., Євсєєва М. В. Ємнісний сенсор вологості гребінцевої структури на основі полімерних матеріалів // Оптико-електронні інформаційно-енергетичні технології. – 2006. - №2(12). – С. 229-234.
4. Осадчук В. С., Осадчук О. В. Напівпровідникові перетворювачі інформації. Навчальний посібник. – Вінниця: ВНТУ, 2004. – 208 с.
5. Березин А. С., Мочалкина О. Р. Технология и конструирование интегральных микросхем: Учебное пособие для вузов. – М.: Радио и связь, 1983. – 323 с.
6. Коледов Л. А. Технология и конструкции микросхем, микропроцессоров и микросборок. - М.: Радио и связь, 1989. - 399 с.
7. Степаненко И. П. Основы микроэлектроники. – М.: Лаборатория базовых знаний, 2003. – 488с.
8. Малишева И. А. Технология производства интегральных микросхем. – М.: Радио и связь, 1991. – 344с.
9. Готра З. Ю. Технология микроэлектронных устройств: Справочник. – М.: Радио и связь, 1991. – 528с.
10. Маслов А. А. Технология и конструкции полупроводниковых приборов. – М.: Энергия, 1970. – 296с.
Додаток К
ПРИКЛАД ТЕХНОЛОГІЇ ВИГОТОВЛЕННЯ
ТОВСТОПЛІВКОВИХ ЕЛЕМЕНТІВ
Типовий технологічний процес виготовлення товстоплівкових структур наведено на рис. К.1. Коротко розглянемо його основні етапи.
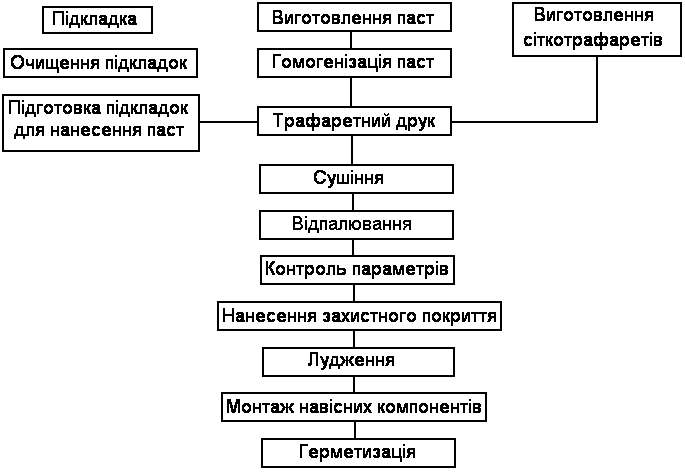
Рисунок К.1 – Типовий технологічний процес виготовлення
товстоплівкових структур
Виготовлення сіткотрафаретів. При створенні конфігурації елементів у товстоплівковій технології використовують сітчасті та металеві (фольгові) трафарети.
Для трафаретного друку під час створення товстоплівкових шарів використовують різні типи трафаретів. Трафарет забезпечує створення заданої конфігурації рисунка і дозування пасти, яка надходить на підкладку за допомогою продавлювання пасти через отвори в сітці трафарету або відкриті області в металевій фользі.
Сітку або фольгу в натягнутому стані розміщують у рамці з алюмінію або сталі і закріплюють механічно або приклеюють. Рамка обробляється так, щоб обидві поверхні були плоскими і паралельними. Якість рамок трафарету дуже важлива для досягнення рівномірного натягнення сітки. Робоча площа трафарету розміщується на відстані не менше за 25 мм від краю рамки.
При нанесенні паст застосовують сітчасті і фольгові трафарети. Фольговий трафарет являє собою металеву фольгу з одного або двох металів товщиною, яка дорівнює заданій товщині шару пасти і закріпленої на жорсткій рамці. Сітчастий трафарет складається зі стальної (шовкової, капронової, нейлонової тощо) сітки, рівномірно натягнутої на рамі.
Для металевих фольгових шаблонів застосовують твердокатані нікелеві або мідні сплави завтовшки 20…50 мкм. Фольгу прикріплюють до рамки клеєм, точковим зварюванням, паянням або гальванічним методом як до, так і після витравлення рисунка шаблона.
Металеві комбіновані трафарети-маски для нанесення лудильних паст виготовляють з листової фольги з нержавіючої сталі, нікелевих або мідних сплавів товщиною 25…200 мкм з використанням металевої сітки, яку виготовляють методом фотолітографії.
Трафаретний друк. Технологія трафаретного друку застосовується для нанесення паст не тільки на керамічні, але й на інші типи підкладок (полімерні, стальні емальовані, скляні) з використанням металевих, полімерно-металевих та інших сіток. Основними характеристиками, які повинні ретельно контролюватись під час отримання товстих плівок, є: матеріал, чистота поверхні, паралельність і товщина підкладки; розміри комірок, товщина і натяг сітки; тиск, швидкість руху і кут нахилу ракеля; зазор між трафаретом і підкладкою.
Трафаретний друк полягає у дозуванні пасти на підкладку продавлюванням її через трафарет за допомогою спеціального ракеля. Ракель, що рухається по трафарету, просуває перед собою пасту, яка під тиском ракеля заповнює отвори трафарету. Тиск ракеля залежить від швидкості його руху, кута зустрічі з поверхнею, від щільності прилягання ракеля до трафарету і зазору між трафаретом і підкладкою. Існує неконтактний і контактний метод нанесення пасти через сіткотрафарет (рис. К.2). При неконтактному методі сіткотрафарет розташований на деякій відстані від підкладки. Після відведення ракеля сітка внаслідок свого натягу віддаляється від підкладки, залишаючи на ній рисунок. При контактному методі сітка і підкладка притиснуті одна до одної і розділяються механічно після закінчення руху ракеля (тобто нанесення пасти).
Подавання пасти відбувається при прямому і зворотному русі ракеля. Кут нахилу леза ракеля впливає на тиск ракеля і, отже, на товщину плівки. Чим менший кут нахилу, тим більший тиск. Залежно від в’язкості використаної пасти і загальної площі комірок сітки в трафареті кут вибирається 45…60°. Для нанесення паст в основному застосовують сітчасті та біметалеві фольгові трафарети.
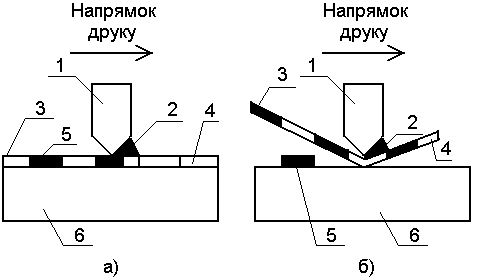
Рисунок К.2 – Схема контактного (а) та неконтактного (б) трафаретного друку: 1 – ракель; 2 – паста; 3 - сіткотрафарет; 4 – вільні місця в сіткотрафареті; 5 –паста, нанесена на підкладку; 6 – підкладка
На відтворюваність розмірів елементів конфігурації під час друку впливають: тип трафарету; швидкість руху; матеріал, форма, тиск, кут нахилу ракеля; натяг трафарету; товщина емульсійного шару; величина зазору трафарет - підкладка; в’язкість пасти.
В’язкість пасти повинна бути такою, щоб забезпечити правильний рисунок і щоб окремі нанесені точки сполучались разом і утворювали рисунок, що відповідає трафарету, через декілька секунд після закінчення друку схеми, лінії повинні бути щільні, безперервні, а шари пасти однорідні за товщиною. Якщо паста довго залишається на трафареті, вона поступово висихає внаслідок випаровування розчинників, і закриває отвори сітки, тому в товстій плівці утворюються пори. У зв’язку з цим кількість пасти, що наноситься на трафарет, повинна бути мінімальною, а свіжі порції її необхідно додавати через певні інтервали часу.
Методами трафаретного друку за товстоплівковою технологією можна отримувати провідні лінії і проміжки між ними 50…150 мкм з використанням металевих фольгових трафаретів. Для отримання складних рисунків і ширини ліній, які перевищують межі звичайного трафаретного друку, використовують метод формування рисунка за допомогою фотолітографії з подальшим спіканням. Підкладки покривають тонким шаром органічної фоточутливої смоли, яка потім зазнає впливу ультрафіолетового випромінювання через позитивний фотошаблон.
Спікання паст. Під час термообробки (сушіння і відпалювання паст на підкладці), швидкість термохімічних реакцій залежить від багатьох факторів, особливо від концентрації і фізичної форми реагуючих матеріалів, температури, часу і довкілля (інертного, окислювального).
Після нанесення пасти на підкладку необхідно з метою вирівнювання слідів сітки виділити деякий час (5…20 хв) на її осадження. Отримані відбитки сушать за температури до 437 К за допомогою радіаційного інфрачервоного нагрівання в камерах або конвеєрних печах. Висушування призначене для видалення легких органічних розчинників і утворення досить міцного шару, зчепленого з підкладкою. Особливий інтерес становить інфрачервоне сушіння. Довжина хвилі інфрачервоного випромінювача повинна бути більшою за 3 мкм, тоді випромінювання проникає в плівку і рівномірно висушує її.
При поверхневому нагріванні на поверхні плівки утворюється твердий шар, який перешкоджає випаровуванню летких органічних складових, що може привести до здування плівки і утворення раковин після відпалювання. При рівномірному проведенні сушіння плівка виявляється досить пористою, що поліпшує випаровування органічних складових і не приводить до її руйнування. Після сушіння шарів можна наносити інші пасти і проводити термообробку.
Наступним процесом є спікання плівок за температури до 1373 К у спеціальних конвеєрних печах протягом 20…60 хв. За температур 673….773 К усувається органічна складова зв’язки, що залишилася, спікаються металеві частинки скла, утворюючи механічно міцне зчеплення з шорсткуватим нижнім шаром металу, що спікся, і розплавлюється скляна фаза в підкладці. Утворюється цілісний зв’язок між металом і підкладкою.
Додаток Л
ПРИКЛАД ТЕХНОЛОГІЧНИХ МАРШРУТІВ
ВИГОТВЛЕННЯ МДН - ТРАНЗИСТОРІВ
Найбільше розповсюдження отримали такі маршрути виробництва: технологія МДН-ІМС на p-канальних транзисторах з алюмінієвими та кремнієвими затворами, технологія МДН-ІМС на n-канальних транзисторах із кремнієвими затворами.
На рис. Л.1 наведено послідовність технологічних операцій при виробництві p-канальних МДН-ІМС із алюмінієвими затворами, на рис. Л.2 – n-канальні МДН-ІМС із кремнієвими затворами.
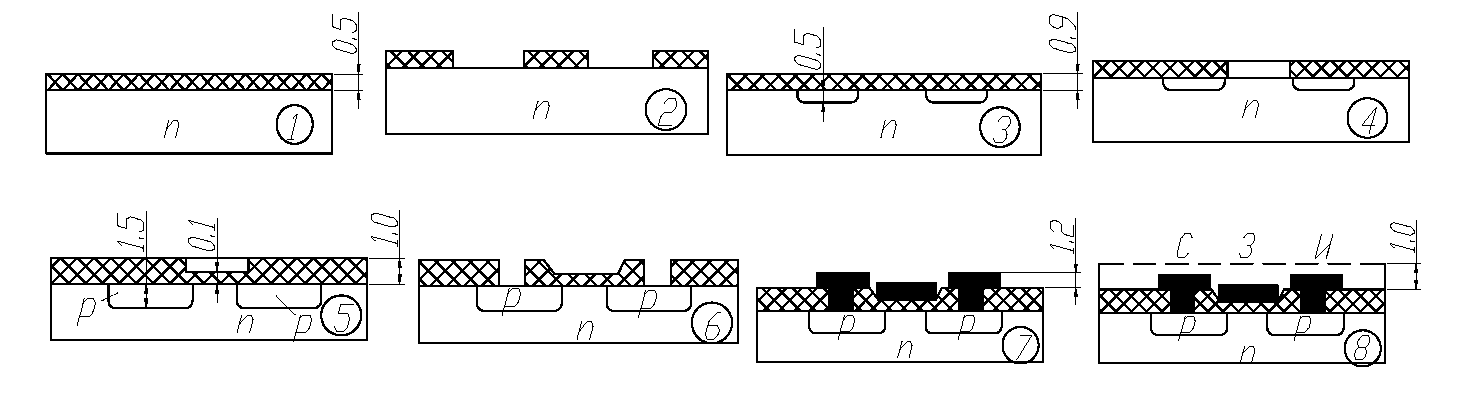
Рисунок Л.1 – Послідовність технологічних операцій при виробництві р-канальных МДН-ІМС із алюмінієвими затворами: 1 – окислення кремнієвої пластини n-типу; 2 – фотолітографія для розкриття вікон під області стоків, витоків і дифузійних шин; 3 – локальне заганяння домішки р-типу в поверхневу область майбутніх стоків і витоків методом іонного легування та друге окислення з одночасним розгоном домішки; 4 – фотолітографія для видалення окису з підзатворних областей; 5 – формування підзатворного діелектрика окисленням у сухому кисні і додатковому розгоні домішки в областях стоків і витоків; 6 – фотолітографія для розкриття вікон під контакти до областей стоку, витоку та дифузійних шин; 7 – нанесення плівки алюмінію й фотолітографія для створення рисунку розведення провідників; 8 – нанесення захисного шару, із наступним фотолітографічним розкриттям вікон над контактними площадками й областями скрайбування.
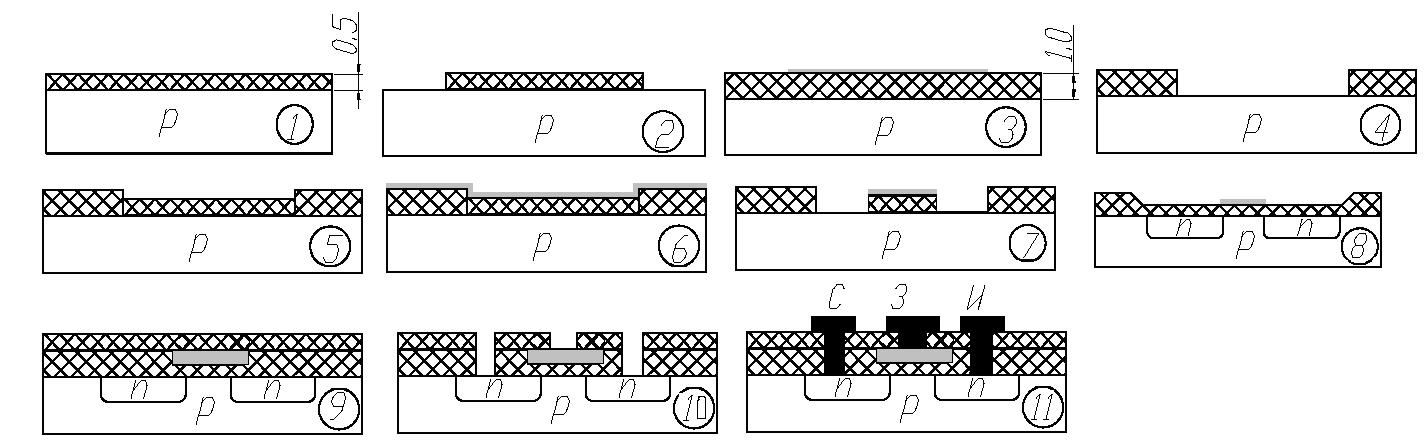
Рисунок Л.2 – Послідовність технологічних операцій при виробництві n-канальних МДН-ІМС із кремнієвими затворами: 1 – окислення кремнієвої пластини р-типу; 2 – фотолітографія для розкриття вікон під дифузію домішки р-типу й формування областей розміщення n-канальних транзисторів; 3 – іонне впровадження бора в розкриті області, окислення й одночасний розгін бора; 4 – фотолітографія для розкриття вікон під області n-канальних транзисторів, дифузійних шин і запобіжних кілець; 5 – формування підзатворного окису кремнію; 6 – нанесення плівки полікристалічного кремнію й фотолітографія по полікристалічному кремнію для формування кремнієвих затворів і шин; 7 – фотолітографія для розкриття вікон під легування областей стоків, витоків р-канальних транзисторів, р-шин і р-запобіжних кілець і проведення заганяння бора іонним легуванням, потім фотолітографія для розкриття вікон під легування областей стоків, витоків n-канальних транзисторів, n-шин і n-запобіжних кілець і проведення заганяння фосфору іонним легуванням; 8 – окислення й одночасний розгін домішок в іонно-легованих шарах; 9 – нанесення фосфоросилікатного скла (міжшарова ізоляція); 10 – розкриття вікон під контакти методом фотолітографії; 11 – напилювання алюмінію й фотолітографія для формування металевих провідних доріжок, перемичок на затвори й контактних площадок.
Додаток М
ПРИКЛАД СХЕМИ ТЕХНОЛОГІЧНОГО ПРОЦЕСУ
ВИГОТВЛЕННЯ ДИФУЗІЙНО-ПЛАНАРНОЇ СТРУКТУРИ НАПІВПРОВІДНИКОВИХ МІКРОСХЕМ
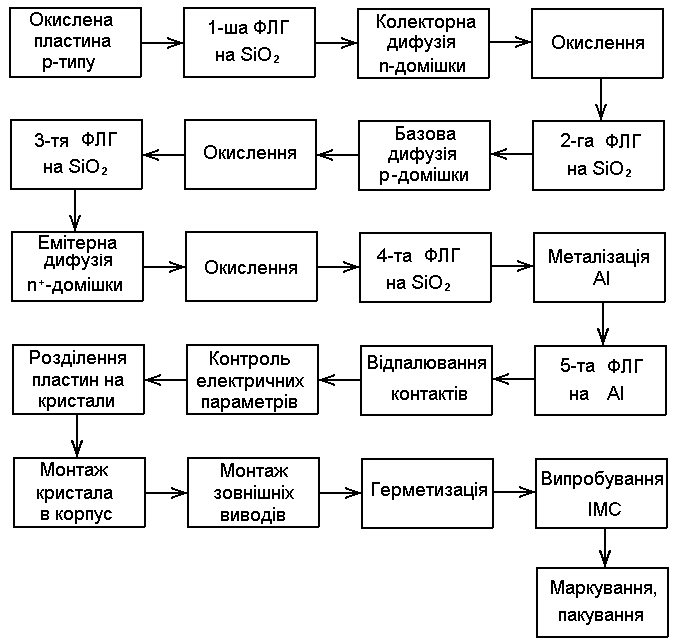