Технологические процессы и технические средства, обеспечивающие эффективную работу глубинного плунжерного насоса 05. 02. 13 Машины, агрегаты и процессы (нефтегазовая отрасль); 05. 16. 09- материаловедение (машиностроение в нефтегазовой отрасли)
Вид материала | Автореферат |
СодержаниеВо второй главе В четвертой главе В пятой главе В шестой главе В седьмой главе В восьмой главе |
- Учебно-методический комплекс дисциплины «Технологические процессы в сервисе» 2008, 1343.12kb.
- Повышение эффективности использования газового топлива в газодизельных двигателях, 298.58kb.
- Программа вступительного испытания по направлению «Металлургия», 51.65kb.
- Программа обще металлургическая практика, 101.95kb.
- Реферат по дисциплине " Технологические процессы микроэлектроники " на тему: Технологические, 1398.5kb.
- Вторая нефтегазовая конференция «экобезопасность 2011», 57.37kb.
- Третья нефтегазовая конференция «экобезопасность 2012», 209.68kb.
- Вторая нефтегазовая конференция «экобезопасность 2011», 135.77kb.
- К рабочей программе учебной дисциплины «Технологические процессы автоматизированных, 22.73kb.
- Темы рефератов по дисциплине «Материаловедение», 19.05kb.
- методы, технические средства разрушающего и неразрушающего контроля штанг при изготовлении и эксплуатации;
- методы и технические средства, снижающие величину силового воздействия на колонну штанг.
Перечисленные предложения послужили основой для проведения исследований и разработки технических решений, обеспечивших в дальнейшем эксплуатационную надежность погружного и наземного нефтепромыслового оборудования.
Так, для повышения усталостной прочности, уменьшения величины обезуглероженного слоя разработан, исследован и реализован способ изготовления насосных штанг из горячедеформированной заготовки низкотемпературной термической обработкой, преимущество которого обеспечено путем регламентирования температуры нагрева под термическую обработку штанг, а также совокупностью операций осуществления способа. Причем данная термическая обработка (отжиг 1-го рода) обеспечивает в штангах мелкозернистую однородную структуру, за счет чего на 20-30% возрастает величина предела выносливости в сравнении с пределом выносливости нормализованных штанг, что подтверждено результатами проведенных исследований.
Для восстановления насосной штанги, в случае ее разрыва в процессе эксплуатации, разработан, исследован и реализован способ химико-термического упрочнения концевых участков насосной штанги. В результате проведенных исследований достигнута возможность получить штанги насосные, концевые участки которых, а именно галтели и прилегающие к ним части тела штанги, имеют предел выносливости, превосходящей предел выносливости средней по длине части тела штанги в 1,2 раза для штанг, прошедших дополнительное упрочнение нагревом ТВЧ, и в 2,4 раза для штанг, прошедших только нормализацию в средней ее части, что позволяет увеличить межремонтный период штанги в 2,5-10 раз. Данные показатели достигнуты, благодаря присутствию в поверхностном слое концевых участков штанги благоприятных напряжений сжатия.
И, поскольку усталостное разрушение штанг будет происходить за пределами термоупрочненных концов насосной штанги, тем самым обеспечивается возможность к восстановлению разрушенной во время эксплуатации штанги, так как разрушенные по длине части штанги возможно подвергнуть механической обработке, а низкое содержание углерода в данной части штанги обеспечивает, например, свариваемость этих частей. При этом и после ремонта сохраняется достаточный для эксплуатации межремонтный период.
Для уменьшения остаточных макронапряжений и обеспечения прямолинейности тела насосной штанги разработан, исследован способ холодной правки и контроля насосных штанг продольным нагружением. Технический результат достигается за счет того, что в способе правки насосных штанг растяжением, включающем предварительное устранение местной кривизны ее тела при скорости 1,5 м/мин, упругую и пластическую деформацию штанг и контроль остаточной пластической деформации, предварительно на контрольных образцах, выполненных из бывших в эксплуатации насосных штанг, определяют зависимость величины предела выносливости от величины пластического удлинения в процессе правки продольным растяжением. Причем контроль величины остаточной пластической деформации осуществляют в соответствии с величиной требуемого пластического удлинения, определенного по наибольшему значению предела выносливости для данной штанги, и при достижении требуемого пластического удлинения насосной штанги прекращают ее нагружение и завершают процесс правки.
По результатам выполненных исследований образцов из стали 20Н2М установлена тенденция, заключающаяся в изменении величины остаточных макронапряжений от пластической деформации образца как для штанг из стали 20Н2М, так и из 15Х2НМФ. Реализация данного способа была осуществлена в НГДУ «Кунгурнефть» ПО «Пермнефть» с использованием устройства для правки насосных штанг растяжением из никелесодержащих сталей, например, 20Н2М, 15ХНМФ и технических средств для магнитоиндукционного контроля протяженных изделий. За счет использования данных технических решений была вдвое снижена обрывность штанг за период 1992-1994 гг. по фонду скважин, оборудованных штангами, бывшими в эксплуатации после холодной правки. Снижение обрывности было достигнуто за счет:
- устранения кривизны тела длинномерных штанг;
- изменения по величине и знаку остаточных макронапряжений по внешней поверхности штанг;
- перемещения остаточных макронапряжений.
Для повышения усталостной прочности длинномерных изделий, например, насосных штанг как новых, так и бывших в эксплуатации, разработан, исследован и реализован способ упрочнения изделий, включающий упругую и пластическую деформацию изделия под действием продольной растягивающей нагрузки и кручения. Причем существенным является то, что после пластической деформации длинномерного изделия продольным нагружением производят деформацию изделия кручением, при этом продольное нагружение изделия ведут со скоростью в диапазоне 0,12-12,0 мм/с до величины удлинения в 0,5-9,0 раза превышающего удлинение, соответствующее пределу пропорциональности, для новых изделий или до величины удлинения в 1,5-5,0 раза превышающего удлинение, соответствующее пределу пропорциональности для изделий, бывших в эксплуатации, после чего фиксируют величину продольного нагружающего усилия и величину пластического удлинения, и через паузу продолжительностью в пределах 0,25-60,0 с осуществляют деформацию изделия кручением со скоростью в диапазоне 0,002-1,8 об/с с одновременным контролем величины продольного нагружающего усилия, при уменьшении которого относительно зафиксированной величины в 1,25-4,0 раза заканчивают деформацию кручением и через паузу 0,25-30,0 с производят полное разгружение изделия от действия продольной растягивающей нагрузки со скоростью в пределах диапазона 0,12-14,0 мм/с и через паузу продолжительностью 0,25-30,0 с снимают полностью крутящий момент со скоростью в пределах диапазона 0,01-1,8 об/с.
Установлено, что при деформации изделия кручением с фиксированной упруго-пластической деформацией происходит уменьшение напряжений в сечении изделия, уменьшается и величина деформации продольным нагружением. В результате в приповерхностном слое изделия образуются остаточные сжимающие напряжения благоприятно влияющие на его усталостную прочность, а в центральной части изделия - остаточные растягивающие напряжения.
После снятия совместной нагрузки, ранее приложенной к штанге, в материале штанги сохраняются остаточные сжимающие напряжения, которые благоприятно влияют на усталостную прочность насосной штанги. Причем остаточные нормальные сжимающие напряжения, наведенные на поверхности тела штанги (аппроксимация Н.Н. Вассерамана), равны:
δост.п =

где: Рк - нормальное растягивающее усилие, при котором деформация штанги завершена, Н; Рпр - предельное усилие, соответствующее моменту прекращения продольной деформации (удлинения) штанги, Н; Кр - коэффициент, учитывающий неоднородность материала штанги по поперечному сечению (принимаем равным от 1 до 0,751); dус.шт – условный диаметр штанги, мм.
Установленные пределы позволяют осуществлять технологический процесс упрочнения длинномерных изделий (штанг) без их разрушения для широкого диапазона марок сталей: 40, 40Г2, 30ХМА, 20Н2М, 15Н3МА, 15Х2НМФ, 15Х2ГМФ, 14Х3ГМЮ, 38ХГМ, VМ125, N2Р, S200Н, 41МоСr11 отечественного и зарубежного производства.
Результаты усталостных испытаний насосных штанг, упрочненных по данному способу, показали, что упрочненные штанги имеют увеличенный на 15-20% предел усталости по сравнению со штангами, не прошедшими упрочнение по предлагаемому способу (испытанию подвергались насосные штанги одной марки стали, года выпуска, режима термообработки, завода-изготовителя).
При непосредственном участии автора диссертационной работы разработаны технические средства (комплекс штанговый КШ01, КШ02) компьютеризированный технологический процесс восстановления, упрочнения и установления прочностных характеристик, магнитоиндукционного контроля насосных штанг.
В настоящее время на предприятиях нефтегазодобывающего комплекса России находятся в действии 17 участков по ремонту насосных штанг, бывших в эксплуатации (общий вид участка представлен на рисунке 3), нормальной и укороченной длины отечественного и зарубежного производства, изготовленные ЗАО «ИНОКАР» (г. Пермь).
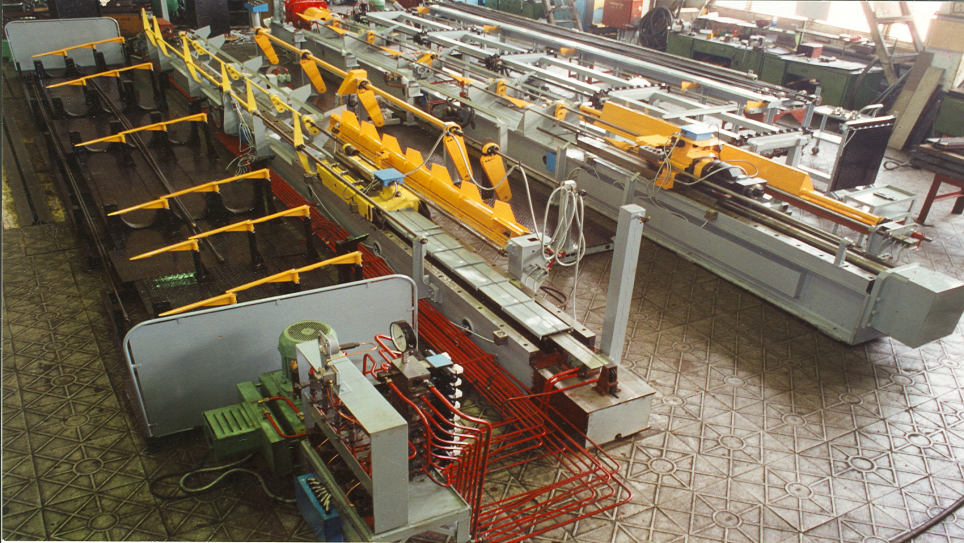
Рисунок 3 – Компьютеризированный комплекс КШ-02 (компьютеризированный стенд для восстановления, упрочнения, установления технических характеристик
насосных штанг со средствами контроля, измерения
и управления, изготовитель ЗАО «ИНОКАР»)
Реализованный технологический процесс позволяет выполнять сортировку насосных штанг по длине, условному диаметру, группам прочности, маркам стали, заводам-изготовителям и тем самым осуществлять 100%-ю паспортизацию насосных штанг; устанавливать их действительные механические характеристики с учетом группы прочности штанги и ее сорта (каждая группа прочности включает 3 сорта), тем самым обеспечивая возможность выбраковки насосных штанг до разрушения с учетом действующих нагрузок; осуществлять выбраковку насосных штанг с дефектами, нарушающими сплошность тела штанги, и со структурной неоднородностью; создавать базу данных по эксплуатационному фонду штанг, устанавливать эксплуатационные показатели штанг и тем самым оптимизировать конструкцию колонн насосных штанг, исходя из требований ее надежности и массы; обеспечивать упрочнение и повышение усталостных характеристик насосных штанг, бывших в эксплуатации; реализовывать режимы, учитывающие механические свойства материала штанг; устранять биение концевых участков насосных штанг; осуществлять режимы правки-дефектоскопии; правки-рихтовки-дефектоскопии; рихтовки-дефектоскопии и т. д.
Во второй главе представлены выполненные исследования и разработанные методы неразрушающего контроля насосных штанг для выявления дефектов, нарушающих ее сплошность и однородность структуры материала изделия.
Так, для раннего обнаружения усталостных микротрещин и видимого контроля состояния штанги на наличие микротрещин исследован магнитолюминесцентный метод неразрушающего контроля. Для подтверждения эффективности метода был выполнен комплекс работ по усталостным испытаниям штанг в коррозионной среде, приближенно моделирующей реальные условия эксплуатации.
Рассмотрены и исследованы два способа осуществления магнитолюминесцентного метода: сухой и мокрый. Сухой и мокрый способы контроля были осуществлены с применением магнитолюминесцентных сухих порошков ЛЮМАГПОР-5 (ТУ6-09-5296-86) и LY-2500 фирмы “Helling” и суспензий на их основе.
При опробовании мокрого способа исследованы три варианта суспензий: с порошком LY-2500 - два состава в разных соотношениях и с порошком ЛЮМАГПОР-5 - один состав. В процессе исследования для выявления эффективного варианта сравнивалась протяженность выявленных микротрещин и наличие фона на образцах.
Из данных способов контроля наиболее оптимальным для контроля поверхности штанги является магнитолюминесцентный контроль в приложенном поле электромагнита с использованием суспензии на основе порошка LY-2500 фирмы «Helling». Установлено, что применение порошка LY-2500 фирмы «Helling» позволяет выявлять трещины на рабочих стандартных образцах с шириной их раскрытия 1 мкм, что соответствует требованиям ГОСТ 21105-87.
Отработка мокрого способа магнитолюминесцентного метода контроля в производственных условиях была осуществлена в период проведения усталостных испытаний фрагмента насосной штанги. После 6 081 500 циклов нагружения фрагмента штанги магнитолюминесцентным методом была выявлена трещина у основания штанги, состоящая как бы из двух трещин суммарной протяженностью 8 мм. При достижении
7 032 600 циклов нагружения протяженность трещины составила 16 мм.
Таким образом, магнитолюминесцентный метод контроля насосной штанги в приложенном поле электромагнита позволяет эффективно диагностировать поверхностные дефекты типа микро- макротрещин.
Для прогнозирования эксплуатационных возможностей насосных штанг как новых, так и бывших в эксплуатации предложен и реализован метод измерения шумов Баркгаузена, обладающий высокой чувствительностью к структурным изменениям ферромагнитного материала. Для осуществления метода были проведены исследования фрагментов насосных штанг с маркировкой 19НЗА 001 и 19Н2А 28Н1 из стали 20Н2М производства Очерского машзавода без нагрузки и при циклическом нагружении в коррозионной среде. Для установления эксплуатационных возможностей материала насосной штанги в процессе коррозионно-усталостных испытаний ее фрагмента были выполнены измерения шумов Баркгаузена при приложении к штанге продольной растягивающей нагрузки.
В процессе исследований фрагментов под нагрузкой выявлено, что уменьшение амплитуды шумов Баркгаузена связано с разрушением кристаллической решетки материала штанги, зарождением и развитием микро - и макронесплошностей с наружной поверхности фрагмента. Распределение шумов Баркгаузена вдоль фрагмента насосной штанги Очерского машзавода (маркировка 19Н2А 28Н) с магистральной трещиной, уровень шума от которой равен ~60 отн.ед., представлено на рисунке 4.
П
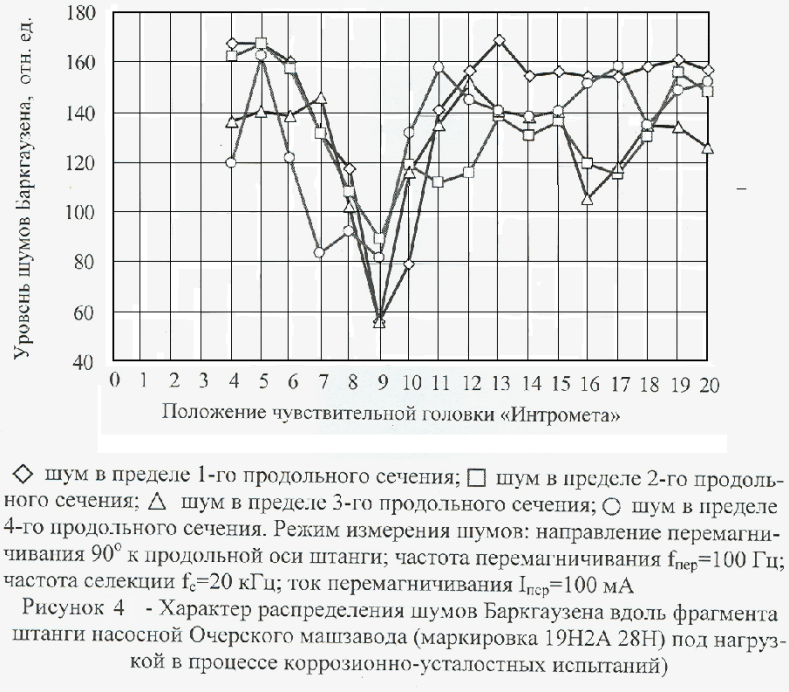
ричем процесс разрушения связей кристаллической решетки материала насосной штанги, наличие микронесплошностей и их величина в поверхностном и подповерхностном слое фрагмента были подтверждены альтернативными методами неразрушающего контроля, а именно: вихретоковым, люминесцентным, магнитолюминесцентным, магнитоиндукционным.
Таким образом, применение вихретокового, магнитолюминесцентного метода контроля позволило оперативно выявить трещины, установить характер изменения эксплуатационных характеристик изделия на примере насосной штанги, прогнозируемого методом измерения шумов Баркгаузена в процессе их ремонта.
Для автоматизированного исследования насосных штанг на длине от 6200 мм и более без очистки поверхности от органических загрязнений предложен, разработан и исследован магнитоиндукционный контроль в постоянном магнитном поле подвижной системы для выявления дефектов несплошности и неоднородности структуры материала. Наличие дефекта, типа несплошность в теле насосной штанги (например, усталостная трещина, расслоение металла и т.п.), приводит к перераспределению магнитного потока, пронизывающего ее в продольном направлении. Изменение длины силовой линии обусловлено геометрическими размерами дефекта, величиной раскрытия дефекта, площадью поперечного сечения и протяженностью дефекта.
В результате упругого и/или пластического непропорционального удлинения штанги от приложенной нагрузки, превышающей максимальное нагружение штанги в скважине, но не более предела прочности материала штанги, в теле штанги, например, бывшей в эксплуатации, при наличии дефекта несплошности происходит явное, видимое раскрытие трещины и пластическая деформация поперечного сечения штанги, наиболее пораженного дефектом несплошности, что при дефектоскопии приводит к резкому увеличению амплитуды сигнала с выхода измерительных катушек. Выделение дефектов неоднородности структуры изделия (например штанги) основано на относительном сравнении непрерывно и локально изменяющихся магнитных проводимостей участков, расположенных в зоне катушек намагничивания, так как магнитная проводимость участка зависит от объемного содержания феррита, перлита, сорбита, мартенсита в структуре изделия. При наличии дефекта типа неоднородность структуры в результате пластического непропорционального удлинения штанги в указанных пределах наблюдается образование, например, шейки, диаметр которой меньше диаметра участка штанги за пределами дефекта. Поэтому при проведении дефектоскопии происходит уменьшение магнитной проводимости в зоне дефекта, и как следствие, резкое увеличение амплитуды сигнала с выхода измерительных катушек.
Измерение магнитного поля, эквивалентного дефекту, осуществляется посредством двух обмоток измерительной системы, которые размещены коаксиально к насосной штанге, разделены между собой ферромагнитным диском и включены по дифференциальной схеме, при этом выход обмоток подключен, например, на вход быстродействующего регистратора. Измерительные обмотки перемещаются вдоль штанги одновременно с обмотками намагничивающей системы. Устройство для осуществления способа неразрушающего магнитоиндукционного контроля представлено на рисунке 5.
Таким образом, данный магнитоиндукционный способ неразрушающего контроля штанг позволяет (например, из штанг, находившихся в нефтяной скважине) выбирать штанги, пригодные для дальнейшей эксплуатации, независимо от качества подготовки их наружной поверхности.
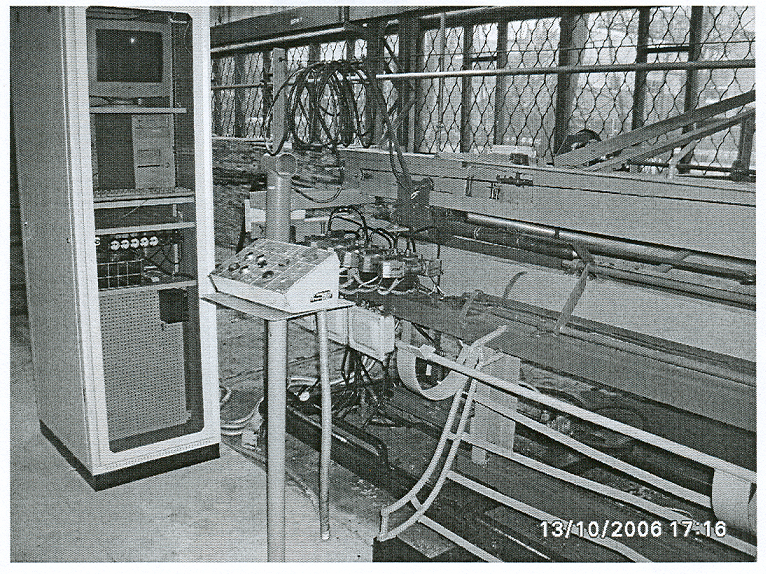
Рисунок 5 – Установка для неразрушающего контроля насосных штанг (НГДУ Кунгурнефть, объединение «Пермнефть», база производственного обслуживания)
В третьей главе рассмотрены способы и технические средства для выявления природы дефектов и установления эксплуатационных технических характеристик насосных штанг как новых, так и бывших в эксплуатации.
При современных режимах откачки жидкости из скважин, действующие номинальные напряжения в самых тяжело нагруженных штангах колонны намного меньше предела выносливости металла. Так, у выпускаемых в СССР штанг из сталей следующих марок: 40У, 36Г1, 15НМ, 15Н4М, 20ХН, 20Н2М, 20ХН2М, 30ХМ, 30ХМА, 15Н3МА, 15Х2НМФ, 15Х2ГМФ, 14Х3ГМЮ, 38ХМ, 35Г2, 40Г2, 40ХГМ, 20ХГН2М, АЦ28ХГН3ФТ предел выносливости на воздухе находится в пределе от 294 МПа до 490 МПа, а номинальные напряжения в верхнем сечении штанг в редких случаях превышают значения, находящиеся в диапазоне 117,6-166,6 МПа для некоррозионных условий ее эксплуатации по ГОСТ 13877-80. Тем не менее, при указанных напряжениях в диапазоне 117,6-166,6 МПа разрушения насосных штанг довольно часты, как установлено для условий ООО «ЛУКОЙЛ-ПЕРМЬ», вследствие следующих причин:
а) технические:
- поверхностные дефекты или дефект структуры материала штанги из-за отклонений в технологии ее изготовления, вследствие которых происходит недогрев, пережог, обезуглероженный слой, появление слоя с пониженной микротвердостью;
- недопустимые отклонения величины закалочного слоя от требуемого (конструктивного) значения, например, при упрочнении поверхности тела штанги током высокой частоты (ТВЧ), приводящие к снижению эксплуатационных характеристик штанг;
- наличие на поверхности штанг механических повреждений от ударов металлическими предметами (на дне полученных рисок создаются концентраторы напряжений, способствующие развитию трещин);
- продольный изгиб тела штанг низа колонны (при этом возможен значительный изгиб тела штанги вследствие наличия механического контакта с внутренней поверхностью НКТ);
- уменьшение сечения тела штанги вследствие ее износа в искривленных или наклонно направленных скважинах;
- пластическая деформация тела штанги при попытке извлечь заклиненный плунжер из цилиндра глубинного насоса (при этом на штанге возможно образование шейки с геометрией, характерной при разрушении тела штанги под действием статической нагрузки);
- появление перенапряжений в поверхностном слое металла из-за изгиба штанги при транспортировке или спуско-подъемных операциях;
- длительный циклический характер действия растягивающих, сжимающих усилий от статических (веса насосных штанг и жидкости), динамических (инерционных, вибрационных) нагрузок;
- коррозионная активность добываемой жидкости (откачиваемые жидкости и газы, в особенности водный раствор сероводорода).
б) организационные:
- несоответствие режимов откачки и эксплуатации глубинно-насосного оборудования (длина хода, частота двойных ходов, диаметр насоса, количество и диаметры секций насосных штанг и НКТ, центраторы и скребки и т.д.) его техническим возможностям;
- оборудование, находящееся в эксплуатации, доукомплектовано узлами и механизмами без улучшения его динамических и кинематических характеристик;
- использование оборудования не коррозионно-стойкого исполнения при наличии в откачиваемой жидкости коррозионно-активных веществ.
Практически все обрывы насосных штанг со скважин ПО «Пермнефть», как установлено, несут следы коррозионной усталости металла, под которой подразумевают разрушения, происходящие под действием постоянных растягивающих и сжимающих усилий от статических нагрузок (веса штанги) в коррозионной жидкости, инерционных сил движущихся масс жидкости и штанг, нагрузок из-за вибрации колонны штанг, несоответствия скорости движения плунжера насоса и полированного штока, наблюдается явление усталости, заключающееся в том, что в отдельных сечениях штанг с неблагоприятно расположенными зернами (анизотропность металла) возникают местные напряжения, превосходящие предел пропорциональности и даже временное сопротивление. Это приводит к образованию местных пластических деформаций, внутренних микротрещин, которые, становясь очагами концентрации напряжений, распространяются дальше, пока не наступит внезапный излом от перегрузки оставшегося сечения штанги.
Поскольку в настоящей работе использованы механические, эксплуатационные характеристики штанг, предназначенных для нефтедобычи, то, как следствие, следует испытывать фрагменты из штанг в условиях, сходных по напряженному состоянию к фактическим условиям их работы. Таким методом усталостных испытаний, создающим на поверхности фрагмента максимальные нормальные напряжения, являются испытания на консольный изгиб с вращением. Установлено, что концевой участок штанги с резьбовой частью, нагреваемый при высадке, является наиболее подверженным разрушению. Данное утверждение подтверждается результатами исследований, представленных на рисунке 6, из которого следует, что в интервале 70-90 мм от галтели до середины штанги лежит 0,744-0,574 всех обрывов, а в интервале до 70-90 мм от галтели приходится 0,256-0,426 всех обрывов.
Рисунок 6 – Распределение обрывности по длине штанги в интервале от галтели до ее середины за период 1986-1987 гг.
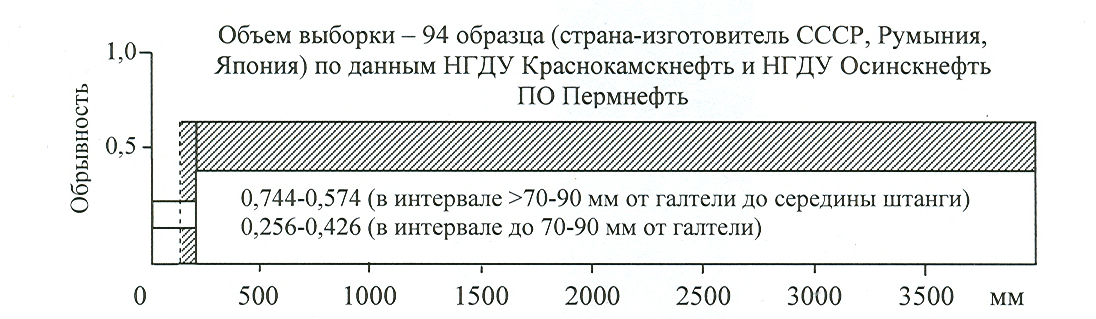
Причем, в зависимости от наличия или отсутствия дефекта процесс накопления усталостных повреждений материала штанги имеет различную длительность в диапазоне от 0,2 до 20 млн. циклов (статистика отказов 94-х штанг за период 1986-1987 гг).
Для оценки эксплуатационных возможностей насосных штанг как на воздухе, так и в коррозионной среде впервые были использованы их фрагменты со следующими конструктивными элементами (ГОСТ Р51161-2002): подэлеваторный бурт; квадратная шейка; упорный бурт; торец упорного бурта; зарезьбовая канавка; резьбовой участок.
Предложенный автором работы в соавторстве с Н.Н.Вассерманом, В.Е.Калугиным, Я.Т.Федоровичем разрушающий метод усталостных испытаний – изгиб с вращением фрагментов штанг с резьбовой частью позволил получить предел ее выносливости при симметричном цикле нагружения элементов натурных штанг с учетом влияния поверхностных и структурных дефектов, присутствующих в штанге.
Усталостные показатели на основе проведенных исследований на воздухе и в коррозионных средах (предел выносливости, предел ограниченной выносливости) и корреляция между показаниями средств неразрушающего контроля, макро- и микроструктурой материала тела штанги и сопротивлением усталости материала штанги – основа перспективного и текущего прогнозирования режимов отбора жидкости, ее физико-химических свойств, межобрывного периода работы подземного оборудования.
Для установления корреляции между показаниями средств неразрушающего магнитоиндукционного контроля и пределом выносливости были проведены усталостные испытания фрагментов насосных штанг со структурной неоднородностью на основе изгиба фрагмента в одной плоскости при консольном нагружении на воздухе с частотой 20 Гц (база испытаний 5х106 циклов) при температуре окружающей среды 20оС.
Установлено по результатам коррозионно-усталостных испытаний и по вероятностным показателям, представленным на рисунке 1, что насосные штанги, например, из стали 20Н2М, 15НЗМА, 15Х2НМФ, прошедшие входной неразрушающий и/или разрушающий контроль, сохраняют свою работоспособность более 5,5 лет.
Испытания фрагментов на усталость (разрушающий контроль) были выполнены с использованием стендов, общий вид одного из трех представлен на рисунке 7.
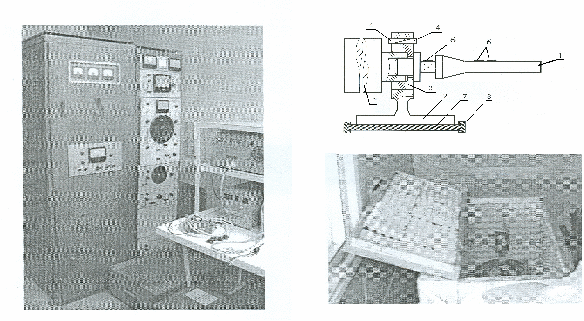
в
б
в
б
а
а – средство управления и контроля стенда; б – вибродинамическое устройство стенда с приспособлением для крепления фрагмента насосной штанги; в - приспособление для высокочастотных усталостных испытаний фрагмента насосной штанги ШН16, ШН19, ШН22, ШН25, 1 – образец штанги; 2 – рамка; 3 – оправка; 4 – клин; 5 – противовес; 6 – тензорезисторы; 7 – диафрагма вибродинамического стенда ВЭДС-200; 8 – узел крепления диафрагмы
Рисунок 7 – Стенд вибродинамический для усталостных испытаний насосных штанг
Для оценки возможности использования магнитоупругого размагничивания для неразрушающего контроля предела пропорциональности (микротекучести) конструкционных сталей были проведены исследования на стандартных образцах диаметром 10 мм, вырезанных из бывших в эксплуатации насосных штанг (стали 20Н2М, 15Х2НМФ и 15Х2ГМФ).
На рисунке 8 представлена зависимость напряженности магнитного поля рассеяния Н при растяжении на примере образца из стали 15Х2НМФ, а на рисунке 9 представлены зависимости ее логарифма от величины напряжений при растяжении. С помощью двух прямых указана точка пересечения σк. Выявлено, что при нагружении намагниченных образцов, изготовленных из различных сталей, напряженность их магнитного поля рассеяния Н (остаточная намагниченность) убывает на первых этапах быстро, а затем медленнее, а также выяснено, что зависимость логарифма напряженности поля от величины механических напряжений может быть представлена двумя пересекающимися прямыми, указывающими на существование критического напряжения (точки пересечения прямых).
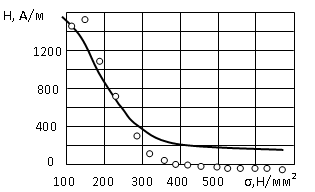
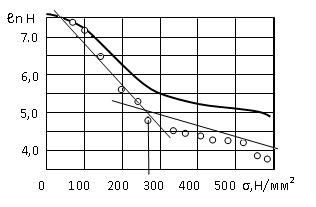
Рисунок 8 – Зависимость напряженности магнитного поля рассеяния Н образца
стали 15Х2НМФ от величины напряжений растяжения σ
Рисунок 9 – Зависимость логарифма напряженности магнитного поля рассеяния LnН образца стали 15Х2НМФ от величины напряжений растяжения σ. Прямыми показана линейная аппроксимация зависимости LnН (σ)
Механизм существования критического напряжения, выделенного двумя соприкасающимися и пересекающимися прямыми (рисунок 9) следующий: снимались кривые напряжение-деформация ΔL(σ) для того же образца, на котором снималась магнитограмма. По точке перегиба на зависимости ΔL(σ) определялась величина предела пропорциональности, обусловленного началом процесса микротекучести σмт.
Установлено, что точка перегиба σк на кривой ln H(σ) и точка предела пропорциональности σп практически совпадают у исследованных сталей (например, у образца 15Х2НМФ σп=270 МПа и σк=260 МПа соответственно). Причина совпадений заключается в том, что при достижении внешними напряжениями уровня внутренних, процесс магнитоупругого размагничивания заканчивается, так как происходит перестройка основных доменов. Далее начинается микротекучесть, и характер магнитоупругого размагничивания изменяется. Сравнение результатов определения предела выносливости разрушающим методом и неразрушающим методом путем магнитоупругого размагничивания по значению σк показало их сходимость (таблица 1).
Таблица 1 – Результаты определения предела выносливости образцов насосной штанги из стали 20Н2М различными методами
Используемый метод | σ, МПа | |
серия I нормализация | серия II закалка+отпуск | |
Усталостное разрушающее испытание на воздухе Рразр=50% | 186±29 | 284±39 |
Магнитоупругое размагничивание, неразрушающий метод | 220±20 | 268±20 300±20 |
Актуальность использования магнитоупругих явлений заключается в доступности получения информации с помощью датчиков магнитного поля, в большой структурной чувствительности метода, а также возможности контроля значения σк непосредственно на изделии путем его локального намагничивания и последующего нагружения.
Все это удовлетворяет условию минимальных материальных и временных затрат, позволяет механизировать и автоматизировать процесс контроля.
Наряду с косвенным неразрушающим методом определения предела выносливости на основе магнитоупругого размагничивания, разработан способ определения предела выносливости длинномерного изделия из стали 20Н2М при статическом его нагружении как в области упругой, так и пластической деформации. Известно, что значение тангенциальной составляющей поля Н остаточно намагниченного образца магниторазомкнутой формы близко по величине к коэрцитивной силе, поэтому по Н можно определять с помощью накладного феррозондового датчика коэрцитивную силу и исследовать связанные с ней параметры, например, упругие и пластические деформации.
Результаты изучения зависимости H от величины прикладываемой нагрузки на образцах, изготовленных из материалов в состоянии поставки, как в момент приложения, так и после ее снятия представлены на рисунке 10, из которого следует, что величина Hо в интервале напряжений от 0 МПа до 200 МПа (кривая 2) практически не меняется, т.е. после цикла "нагрузка-разгрузка-намагничивание" сталь возвращается в исходное состояние. Это означает, что статические напряжения вызывают только упругую деформацию. Однако при напряжениях =(200-250) МПа, далеких, как это видно из графика зависимости деформация-напряжение (рисунок 10, кривая 5) от предела текучести, величина Hσ начинает расти и достигает некоторого насыщения при σ=500 МПа. Полные изменения Н составляют 85% от исходного сигнала при достижении предела текучести. Измеренная после разгружения образца величина H вначале резко уменьшается с увеличением нагрузки, проходит через минимум и, достигнув максимума при =470 МПа, начинает уменьшаться (рисунок 10, кривая 3). С ростом растягивающих напряжений H убывает (рисунок 10, кривая 4), а после пластической деформации (по-видимому, за счет влияния магнитного поля) заходит в область небольших отрицательных значений.
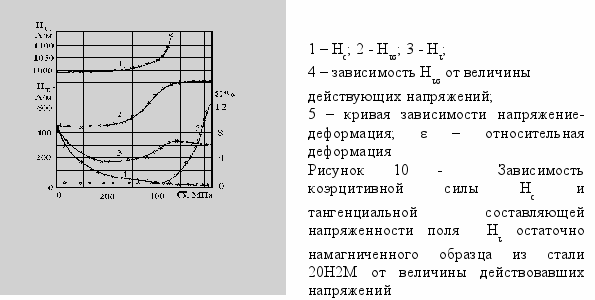
Нормальная составляющая магнитного поля рассеяния остаточного намагниченного образца так же испытывает существенные изменения, как в нагруженном состоянии, так и после разгрузки. При этом характер ее изменения качественно повторяет зависимости Н(σ). Аналогично были установлены зависимости Нτ, Нс от величины прикладываемой нагрузки на образцах, выполненных из насосных штанг, бывших в эксплуатации (сталь 20Н2М).
Благодаря выполненным исследованиям, представилось возможным оценить предел выносливости длинномерных изделий (насосных штанг), находящихся вне коррозионной среды, ускоренным магнитоупругим неразрушающим методом по изменению H, и Hс. Для достижения объективности коррозионно-усталостных испытаний фрагментов штанг исследовано влияние агрессивной среды на коррозионно-усталостную прочность штанг из стали 20Н2М в трех средах. Полученные средние значения пределов выносливости и величины средне-квадратичного отклонения представлены в таблице 2.
Таблица 2– Результаты коррозионно-усталостных испытаний фрагментов штанг в трех средах
Характеристика среды для коррозионно-усталостных испытаний фрагментов штанг | База испытания 5х106 циклов нагружения | База испытания 107 циклов нагружения | ||
σ-1,МПа | Sσ-1,МПа | σ-1,МПа | Sσ-1,МПа | |
Усть-Качкинская высокоминерализованная вода, скважина № 6 (Пермская область) | 155 | ±23,2 | 123 | ±8,14 |
Пластовая вода, скв. № 2470 Осинского месторождения (НГДУ Осинскнефть) | 175 | ±23,3 | 130 | ±1,00 |
3%-ный раствор NaCl в дистиллированной воде (Михайловский завод химреактивов) | 177 | ±8,14 | 123 | ±8,14 |
σ-1 - среднее значение предела выносливости; Sσ-1 – величина средне-квадратичного отклонения |
Сравнение результатов таблицы 2 показывает, что воздействие агрессивных сред на коррозионно-усталостную прочность штанг из стали 20Н2М, с учетом установленной погрешности, отличается незначительно. Поэтому для обеспечения воспроизводимости результатов коррозионно-усталостных испытаний фрагментов штанг, а также для сравнения с результатами других исследователей в качестве базовой агрессивной среды принят 3%-ый раствор NaCl в дистиллированной воде.
В четвертой главе рассмотрены усилия, возникающие от совокупного взаимодействия центраторов, скребков на теле штанги, соединительных муфт с добываемой жидкостью во внутренней полости НКТ. Так, в процессе добычи нефти, исходя из соотношения содержания в ней парафинов (П) к сумме содержания асфальтенов и смол (А-С), известны три типа асфальтосмолопарафинистых отложений (АСПО): асфальтеновый П/(А+С)<1; парафиновый П/(А+С)>1; смешанный П/(А+С)=1.
При наличии на внутренней поверхности насосно-компрессорных труб (НКТ) АСПО парафинового и/или смешанного типа с учетом Н2О в его составе установлено, что очистка труб достигается эффективно за счет использования центраторов, скребков, скребков-центраторов, скребков-завихрителей, установленных жестко и/или подвижно на теле насосной штанги, являющейся составной частью колонны насосных штанг. Скребки-центраторы имеют возможность вращения либо одновременного вращения и перемещения вдоль штанги. Центраторы устанавливаются жестко или с возможностью вращения.
Расчет усилий от совокупного взаимодействия центраторов и скребков, а также соединительных муфт с добываемой жидкостью во внутренней полости насосно-компрессорной трубы (НКТ) рассмотрен впервые. Как показывают расчеты, эти усилия, при отсутствии АСПО на внутренней поверхности НКТ одного порядка с усилиями от жидкостного трения с поверхностью тела штанги, а в случае наличия АСПО на внутренней поверхности НКТ, значительно превосходят их.
Помимо рассмотренных конструкций, распространение получили центраторы и скребки со специальными прорезями в их теле. В этом случае при расчете учитывается площадь, создаваемая прорезью, что в конечном итоге, обеспечивает снижение давления перед скребком ∆Рс или перед центратором ∆Рц . Установлено, что наибольшее усилие возникает от поршневого эффекта при наличии центраторов и пакетов из скребков как при отсутствии АСПО, так и при наличии АСПО на внутренней поверхности НКТ. Таким образом, следует, что усилия от поршневого эффекта весьма значительны и их следует учитывать при расчете колонны штанг на прочность.
Для повышения эффективности очистки рабочих поверхностей внутрискважинного оборудования от АСПО при глубиннонасосной эксплуатации скважины актуально использование штанговращателей и/или амортизаторов, а также в особых случаях представляется необходимым применение центраторов и/или скребков с подогревом.
В пятой главе приводятся доказательства, что использование химического метода как наиболее распространенного из технических средств (дозаторов, транспортных систем, контейнеров) для исключения осложнений от АСПО на ряде месторождений ООО «ЛУКОЙЛ-ПЕРМЬ» недостаточно эффективно вследствие высокой стоимости химреагентов, технических средств, а также ввиду чрезмерных затрат, связанных с поиском высокоэффективных ингибиторов (твердых, жидких) конкретно для каждой скважины. В связи с этим, из известных физических методов (волновых, магнитных и т.д.), наиболее перспективной по эксплуатационной надежности является магнитная обработка добываемых жидкостей (нефтей) скважин Туркинского, Горновского, Константиновского месторождений ООО «ЛУКОЙЛ-ПЕРМЬ» с использованием технических средств, обеспечивающих многомерное магнитное поле с напряженностью в рабочем канале от 1 кЭ и более.
Д
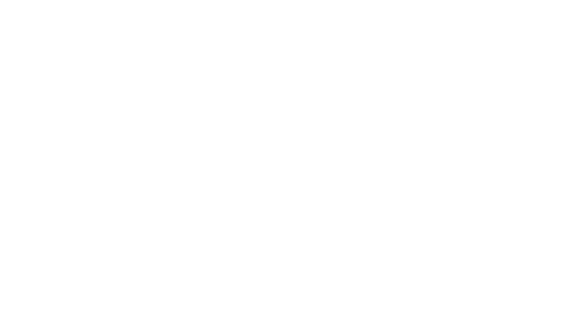
Установлено, что эффективность обработки нефтей Горновского и Туркинского месторождений постоянным магнитным полем при напряженности 15,5 кЭ в рабочем канале устройства приближается к 40%. Магнитная «память» нефтей после такой эффективной обработки превышает 3 ч.
Выявлено влияние скорости течения нефти, с которой она проходит через магнитный аппарат, на эффективность ее обработки. Наиболее эффективная обработка нефти осуществляется при скорости от 0,1 до 1,0 м/с. Причем эффективность магнитной обработки нефти также зависит от напряженности магнитного поля в рабочем канале устройства, кратности его конструктивных особенностей. Длительные наблюдения за состоянием нефти после магнитной обработки показали существенные изменения (до 30%) относительного содержания фазы углеводородов, непосредственно контактирующих с сольватной оболочкой.
Таким образом, по результатам исследований установлено, что нефти месторождений ООО «ЛУКОЙЛ-ПЕРМЬ» восприимчивы к магнитному воздействию постоянным полем, а также установлены критерии для разработки технических средств для эффективной магнитной обработки жидкости (нефти) для исключения осложнений по причине АСПО:
- высокая напряженность постоянного магнитного поля в рабочем канале устройства, то есть более 10 кЭ;
- многократная магнитная обработка жидкостей (нефтей) в неоднородном магнитном поле с высокой напряженностью в рабочем канале устройства;
- скорость потока намагничиваемой жидкости в диапазоне от 0,1 м/с до 1,0 м/с;
- обеспечение магнитной памяти после намагничивания жидкости;
- изменяемое соотношение между продольной и поперечной составляющей напряженности магнитного поля.
В шестой главе установлено, что одной из причин образования АСПО, гидратов и высоковязких эмульсий является путевое охлаждение добываемой жидкости (нефти). В настоящее время, благодаря наличию новых материалов и проектных решений, технически осуществима тепловая обработка добываемой жидкости по стволу нефтяных скважины с использованием протяженных распределенных источников тепловой энергии.
Восприимчивость нефтей на примере Москудьинского, Гожанского, Степановского месторождений Пермского края к тепловому воздействию подтверждена результатами многолетних исследований, в процессе которых установлено следующее:
1) нелинейное изменение вязкости нефти с изменением температуры среды, связанное с ее химическим составом, структурой отдельных компонентов;
2) понижение температуры застывания нефти после термообработки;
3) разные значения температуры насыщения нефти парафином.
В результате проведенных исследований для месторождений Пермского края подтвердилось, что температура насыщения нефти парафином соответствует такой температуре, при которой из нефтяных фракций выделяется растворенная вода, парафины, бензол, видимые невооруженным глазом.
Выявлено, что естественными физико-химическими параметрами, определяющими эффективность путевой тепловой обработки добываемой жидкости (нефти) являются:
- вязкость добываемой жидкости;
- содержание смол, парафинов, асфальто-смолистых веществ, Н2О;
- температура застывания добываемой жидкости (нефти);
- температура насыщения нефти парафином;
- реологические свойства добываемой жидкости (нефти).
Причем во всех тех случаях, когда традиционные методы предотвращения осложнений при добыче нефти по причине АСПО по экономическим и техническим показателям малоэффективны, то в данной ситуации перспективным является путевой прогрев жидкости нефтяных скважин с использованием внутрискважинных нагревателей.
Рассмотрены технические решения (многовариантные протяженные внутрискважинные и сосредоточенные источники тепловой энергии по исполнению и размещению), которые предназначены для внутрискважинной тепловой обработки жидкости в следующих режимах:
а) путевой нагрев жидкости в пластовых условиях до температуры пласта;
б) путевой нагрев жидкости под давлением до температуры плавления парафина (парафинистая нефть);
в) путевой нагрев жидкости под давлением до температуры плавления асфальтенов (асфальтеносодержащая нефть);
г) путевой нагрев жидкости до температуры, превышающей температуру насыщения нефти парафином;
д) путевой нагрев жидкости до температуры, свыше которой происходит незначительное снижение ее вязкости;
е) путевой нагрев среды выше температуры гидратообразования с учетом давления по стволу скважины.
ж) путевой нагрев жидкости до температуры, при которой меняются ее реологические свойства.
Выбор конструкции, геометрические размеры протяженных и/или сосредоточенных нагревателей, режимы их эксплуатации определены с использованием математической модели, устанавливающей характер распределения температуры жидкости, движущейся по стволу скважины с учетом ее физико-химических свойств и теплофизических свойств горных пород, тампонирующих материалов, жидких сред вне ствола (крепления) скважины.
В основу математической модели, устанавливающей характер распределения температуры жидкости, движущейся по стволу скважины, положено уравнение теплового баланса, в соответствии с которым тепловой поток в окружающую среду на рассматриваемом участке скважины (тепловые потери) равен изменению внутренней энергии жидкости на этом участке за единицу времени. При определении тепловых потерь по стволу скважины учитывается теплопроводность каждого слоя в плоскости поперечного сечения многослойной оболочки. При построении математической модели использован метод конечных разностей, включая зависимости теплофизических свойств сред (вязкости, плотности, теплоемкости) от температуры.
Результаты теоретических и лабораторных исследований подкреплены результатами промышленного использования протяженных распределенных нагревателей. Пример тепловой обработки добываемой жидкости с использованием внутрискважинного нагревателя представлен на рисунке 11.
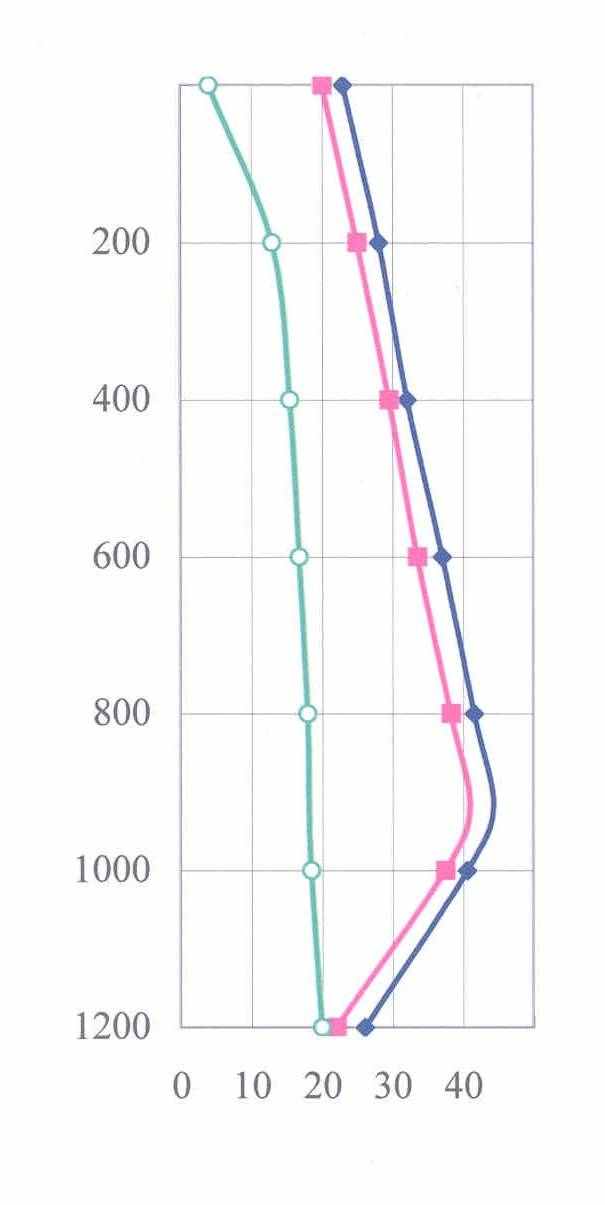
Lтек,м



3


~380 В
1
2


4
5
1 – станок-качалка УСШН
2 – насосно-компрессорные трубы (НКТ)
3 – станция управления источником
тепловой энергии
4 – низкотемпературный участок внутри-скважинного нагревателя
5 – место соединения участков внутри-скважинного нагревателя
6 – высокотемпературный участок внутри-скважинного нагревателя
7 – концевая заделка внутрискважинного нагревателя
6
6


7

t,оС

- геотерма породы; - расчетная температура жидкости во внутренней полости НКТ;
- фактическая температура жидкости во внутренней полости НКТ
Рисунок 11 - Общий вид размещения внутрискважинного нагревателя и распределение температуры по стволу скважины № 52 Андреевского месторождений, эксплуатируемой механизированным способом (УСШН), НКТ 2,5" без теплоизоляции с протяженным источником тепла
ловой энергии



При проведении промысловых исследований на скважине № 2210 Павловского месторождения установлено, что за счет тепловой обработки добываемой жидкости нефтяной скважины снизилась величина максимальной нагрузки на полированный шток с 46305 Н (данные на 18.05.2005) до 40445 Н (данные на 30.01.2007), при ходе его вверх с одной стороны, а также увеличилась нагрузка на полированный шток с 16268 Н (данные на 15.02.2002) до 20335 Н при ходе его вниз с другой стороны.
До внедрения путевого прогрева добываемой жидкости обычно выполняли пять промывок горячей нефтью и три промывки горячей водой в течение года для обеспечения работы скважины без осложнений.
Таким образом, по результатам промышленного использования технических средств для тепловой обработки жидкости нефтяных скважин достигнута возможность исключить с минимальными затратами осложнения при ее добыче без техногенной нагрузки на окружающую среду.
В седьмой главе приводится обоснование разработки конструкции погружного привода глубинного насоса. Самым распространенным из механизированных способов добычи нефти из наклонно-направленных скважин является штанговый глубиннонасосный.
Несмотря на значительный прогресс в совершенствовании СШНУ они в недостаточной мере отвечают современным требованиям эксплуатации наклонно-направленных скважин.
Основные недостатки СШНУ обусловлены преобразующими и, прежде всего, передающими звеньями (станком-качалкой и колонной штанг):
- деформация колонны насосных штанг при ходе вниз и вверх и потеря длины хода плунжера насоса;
- коррозионно-усталостное разрушение насосных штанг, особенно в наклонно-направленных скважинах;
- механическое истирание рабочей поверхности штанг и НКТ;
- ограниченные регулировочные свойства СШНУ.
Указанные недостатки приводят к снижению эффективности эксплуатации нефтяных скважин в осложненных условиях с помощью СШНУ.
Техническая целесообразность глубинных плунжерных насосов для данных условий, необходимость их эффективного использования обусловили востребованность разработки, проведения исследований погружного ЛАД плунжерного насоса.
Решающим аргументом в относительно применения ЛАД в качестве привода глубинного плунжерного насоса, являются требования по управляемости, возможность получить строго дозированный отбор жидкости, , удобство транспортировки и эксплуатации независимо от почвенно-климатических условий.
Электроплунжерный погружной агрегат (ЭППА) по данной разработке включает: линейный асинхронный двигатель (ЛАД), плунжерные насосы, силовой кабель, станцию управления. Исключение промежуточных звеньев привода (штанговой колонны, станка-качалки), приближение двигателя к насосу обеспечило данному оборудованию ряд существенных преимуществ в сравнении с глубиннонасосным оборудованием.
Несмотря на значительные успехи, достигнутые в развитии теории линейных асинхронных двигателей, в настоящее время существуют нерешенные задачи, имеющие большое значение для создания совершенных ЛАД плунжерного насоса и системы автоматического управления ими.
Условия работы погружного оборудования для добычи нефти предъявляют к конструкции ЛАД следующие требования: герметизация статора от внешней среды (подвижный вторичный элемент находится непосредственно в добываемой жидкости) либо герметизация электродвигателя в целом от окружающей среды с помощью устройства гидрозащиты (вторичный элемент двигателя помещен в специальную жидкость).
В таких конструкциях между вторичным элементом и статором погружного ЛАД располагаются слои с различными электрическими и магнитными свойствами.
Из практики проектирования ЛАД для нефтедобычи вытекает, что погружной двигатель должен удовлетворять следующим геометрическим соотношениям:
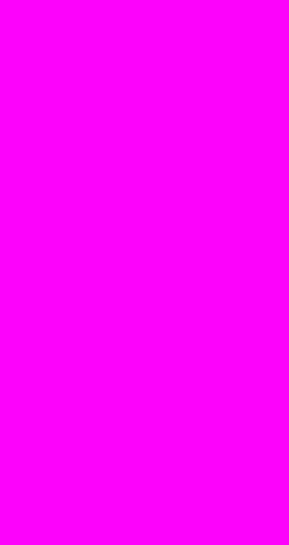
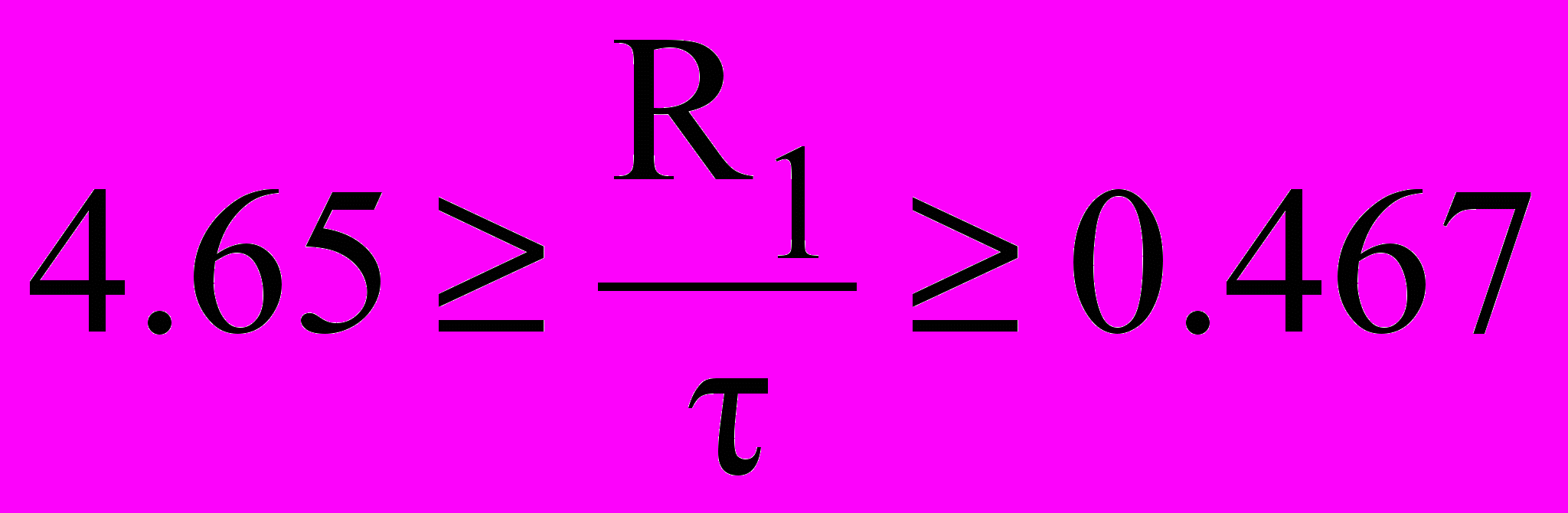
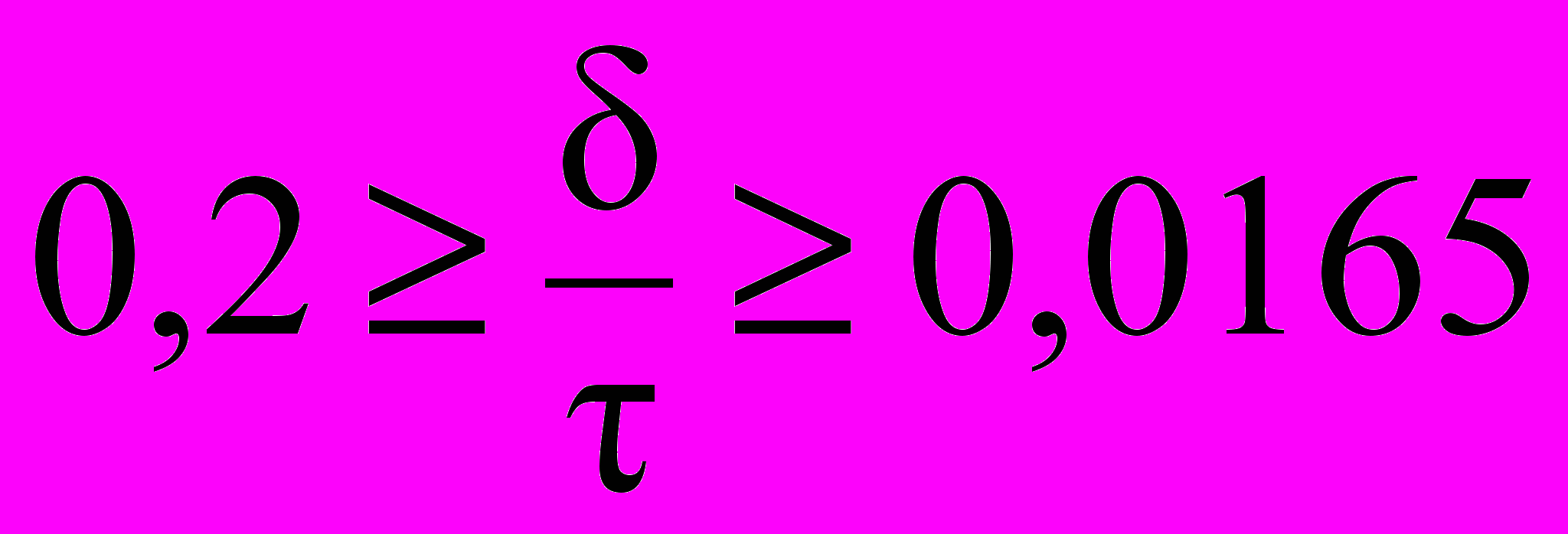
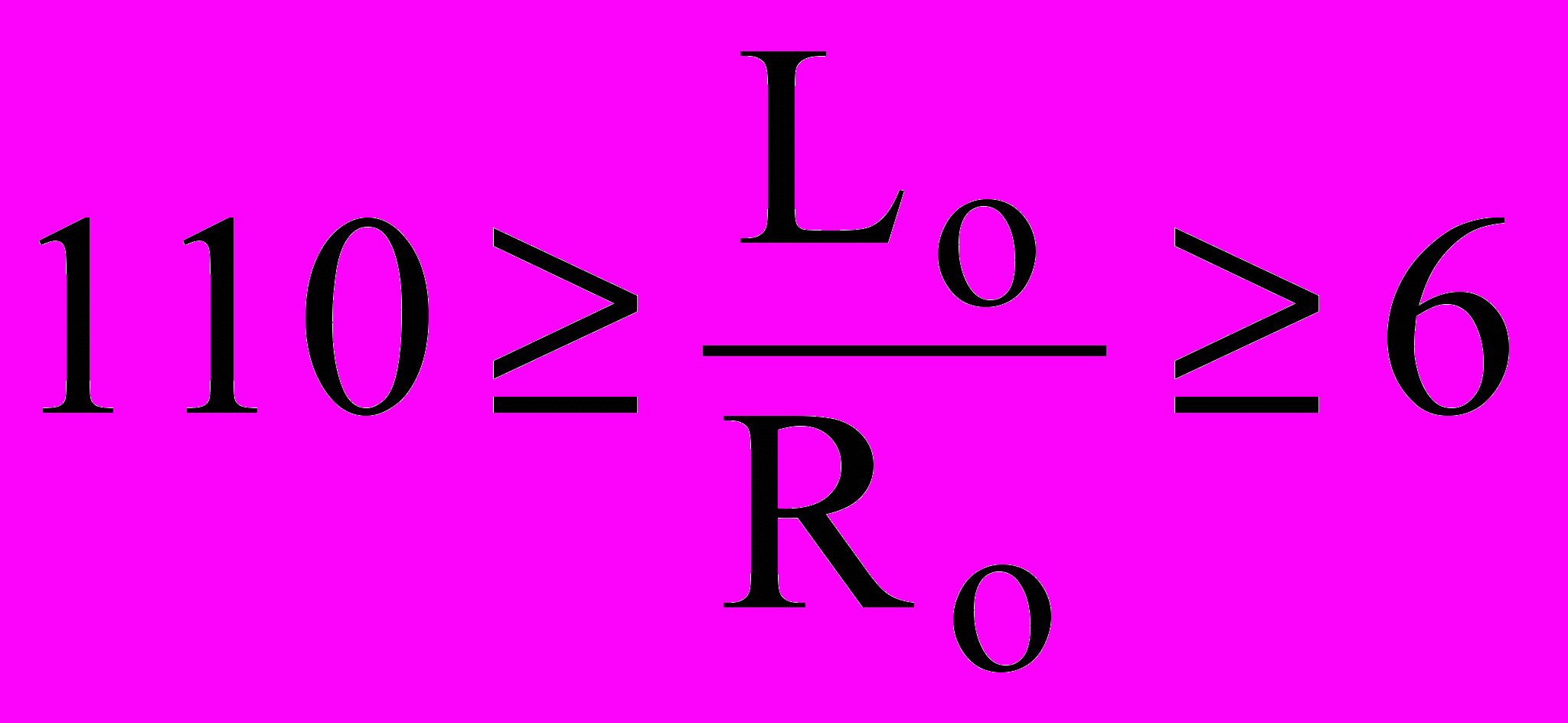
где R1 - внутренний радиус цилиндрического статора; - полюсное деления ЛАД; - немагнитный зазор между статором и подвижным вторичным элементом; L
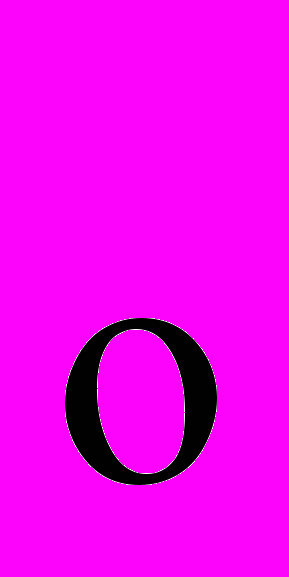
Скорость движения вторичного элемента V выбрана в диапазоне от 1 до 2 м/с.
Критерием для выбора активной длины статора и параметров вторичного элемента погружного ЛАД является комплекс факторов, из которых наиболее важные: внешний диаметр статора ограничен внутренним диаметром обсадной колонны скважины; внутренняя полость ЛАД заполнена жидкостью; наружная поверхность корпуса электродвигателя смывается жидкостью.
Первый фактор ведет к тому, что прирост мощности электродвигателя для данного диаметра обсадной колонны зависит от его длины, второй и третий факторы интенсивно воздействуют на охлаждение погружного ЛАД. Согласно выполненным исследованиям, предпочтение отдано зубцово-пазовой структуре статора и вторичного элемента ЛАД.
В восьмой главе установлено, что известные расчеты асинхронных вращающихся и линейных асинхронных двигателей на основе метода удельных магнитных проводимостей работы А.И.Вольдека, О.Н.Веселовского не позволяют получить реальную картину поля в зазоре между зубцово-пазовой структурой статора и вторичного элемента ЛАД.
В связи с этим приобретает особое значение метод численного анализа взаимного расположения зубцово-пазовой структуры статора и вторичного элемента. Необходимость данных исследований вызвана тем, что рекомендуемые Постниковым И.М. и другими авторами числа зубцов статора и ротора асинхронных вращающихся двигателей оказались неприемлемыми (данные эксперимента) для погружных ЛАД.
Для анализа расположения обеих зубцово-пазовых структур рассмотрено уравнение:
τ1 + N1tz1 + γ1 = τ2 + N2tz2 + γ2 , (7)
где τ1, τ2, γ1, γ2 –расстояние между точками отсчета и близлежащими продольными осями зубцов статора и вторичного элемента ЛАД; N1, N2 – целое число зубцовых делений.
Из уравнения (7) методом численного анализа входящих в него величин найдены условия совпадения пары продольных осей и из наличия одного совпадения получено условие существования бесконечного количества совпадений пар осей через равные периоды при неограниченной длине ЛАД.
Из этого следует, что применительно к ЛАД предпочтительнее выбрать значения tz1 и tz2, имеющие единственный делитель – единицу.
Далее для оценки закономерности расхождения между близлежащими продольными осями зубцов ЛАД на N-ом зубцовом делении статора, исследуем отношение
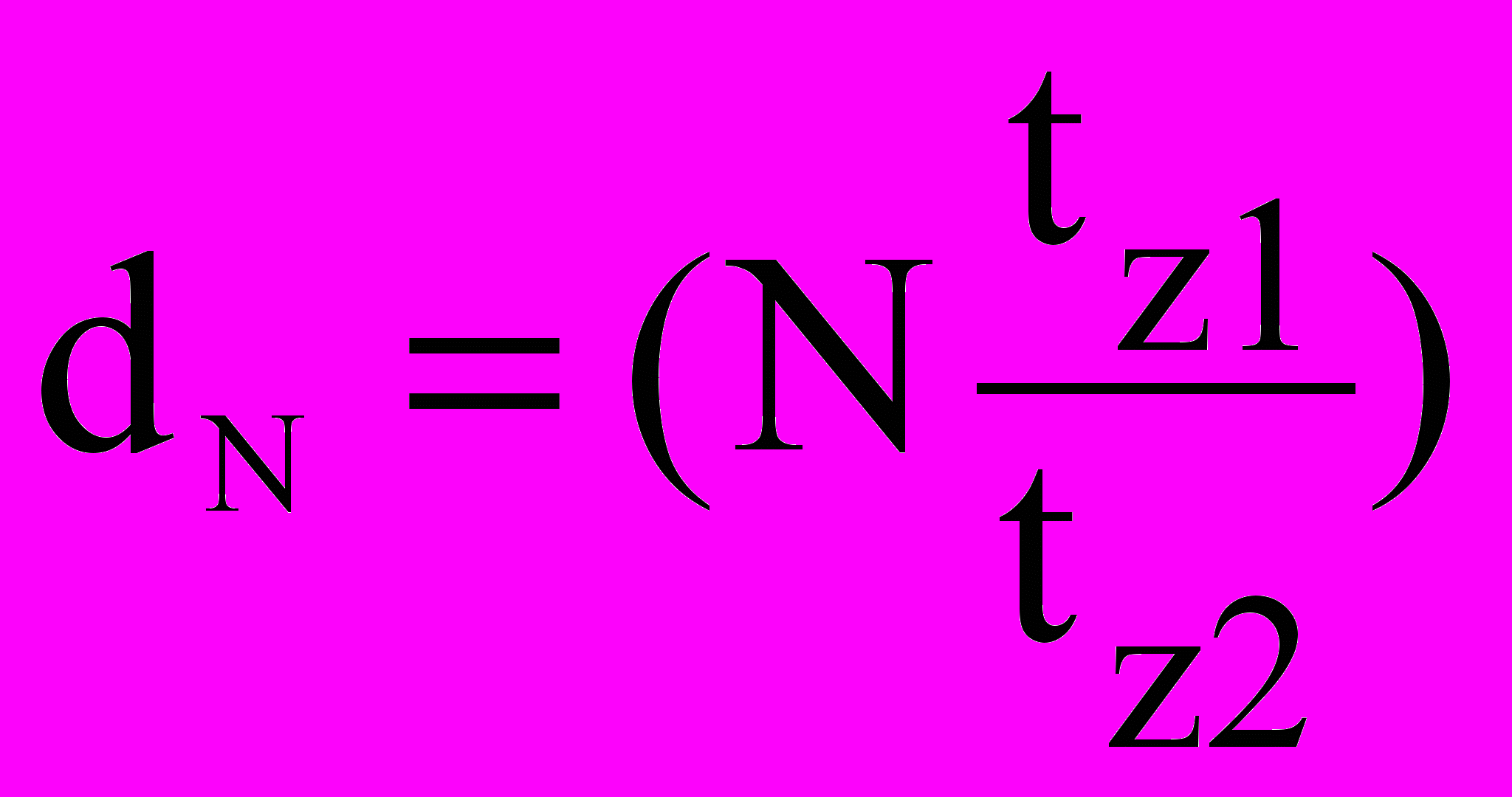
tz1 –величина зубцового деления статора ЛАД;
tz2 –величина зубцового деления вторичного элемента ЛАД;
где
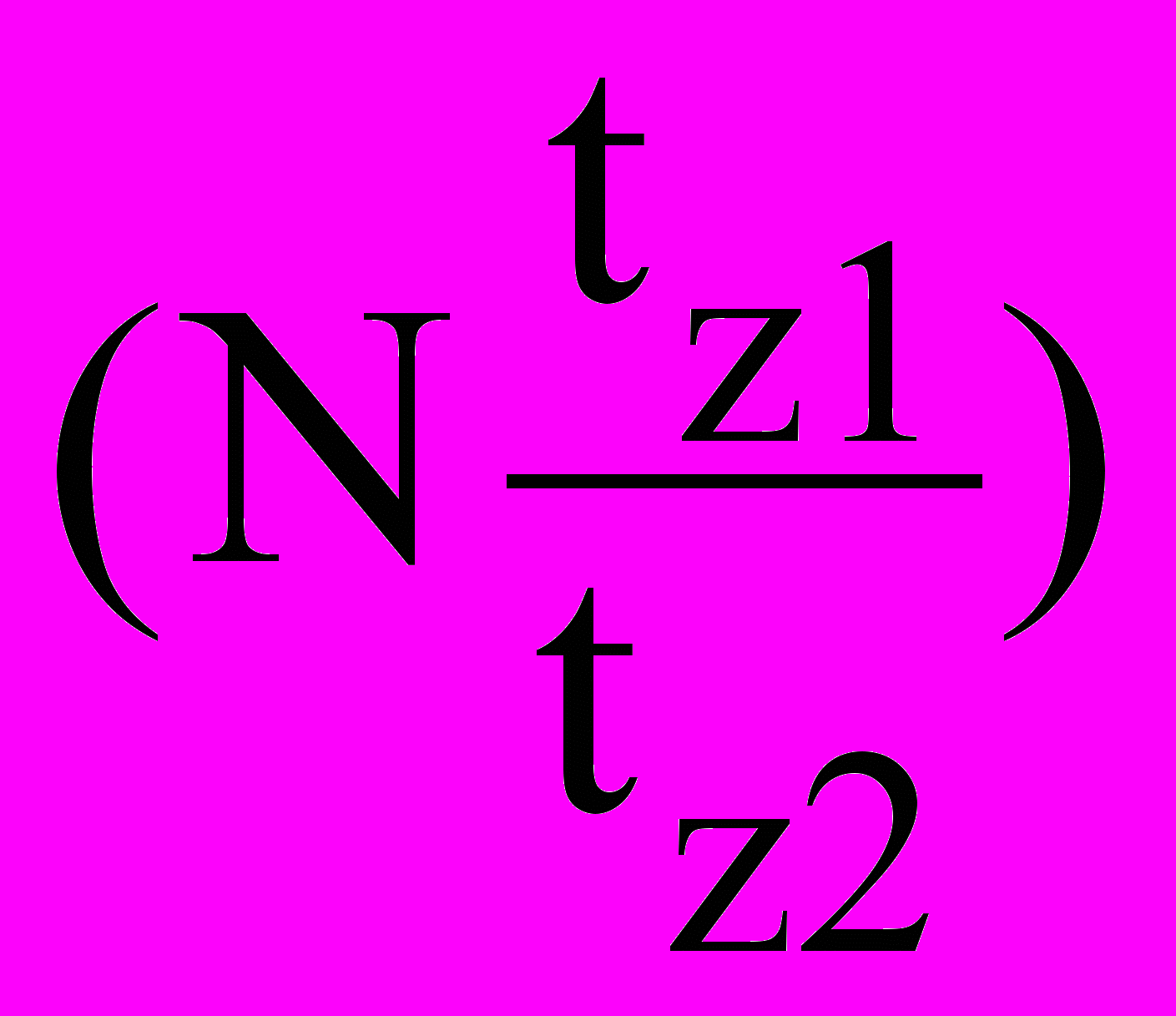
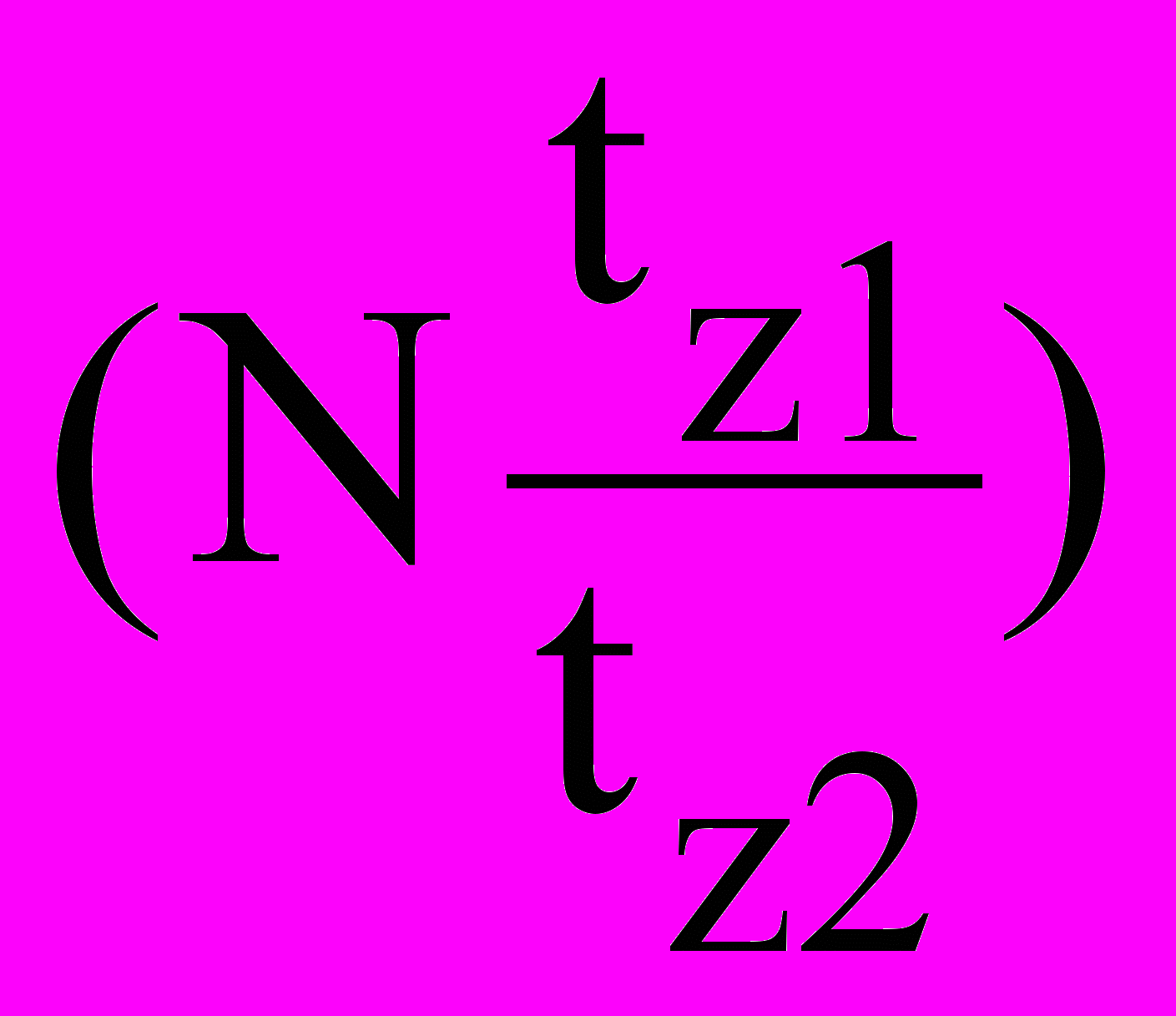
Согласно (8) найдены свойства отношения dN: если период существует, то величина расхождения внутри периода не может принимать одно и то же значение более одного раза при изменении N от 0 до n2-1. В данном случае величина dN принимает все значения вида
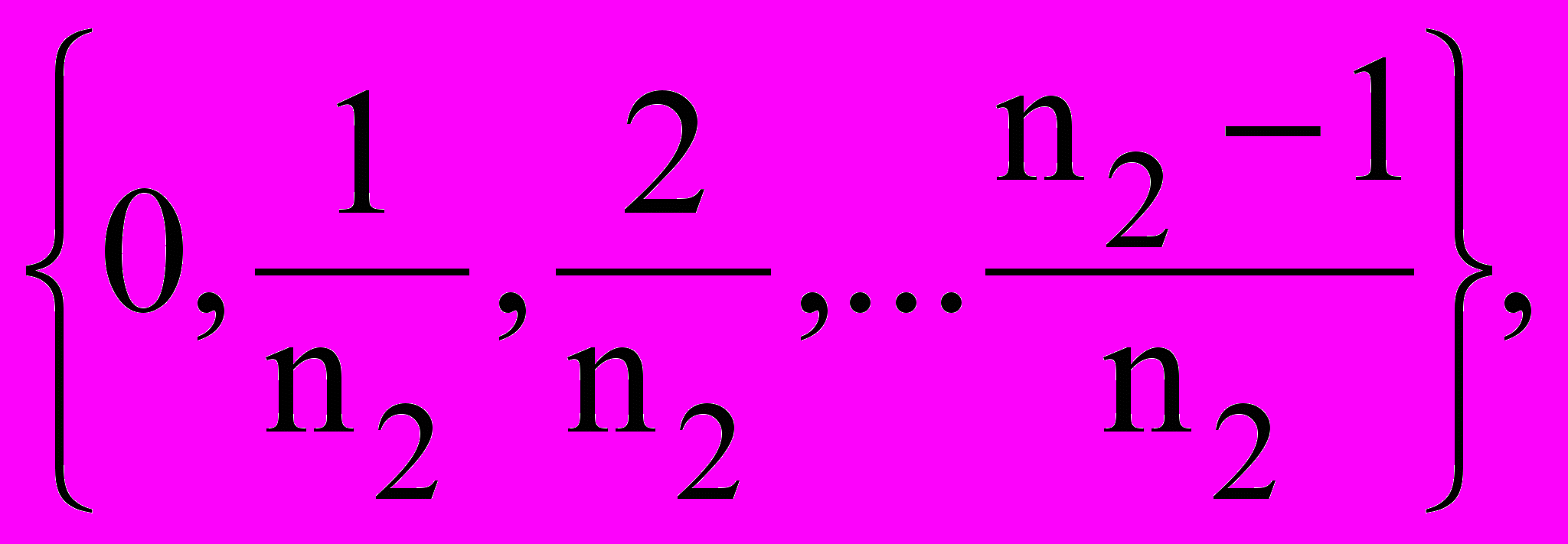
где n2 – целое число зубцовых делений статора, входящих в период.
Существование набора данного вида вытекает из зубчатой структуры статора и вторичного элемента. Внутри абсолютного периода максимум расхождения определяется выражением
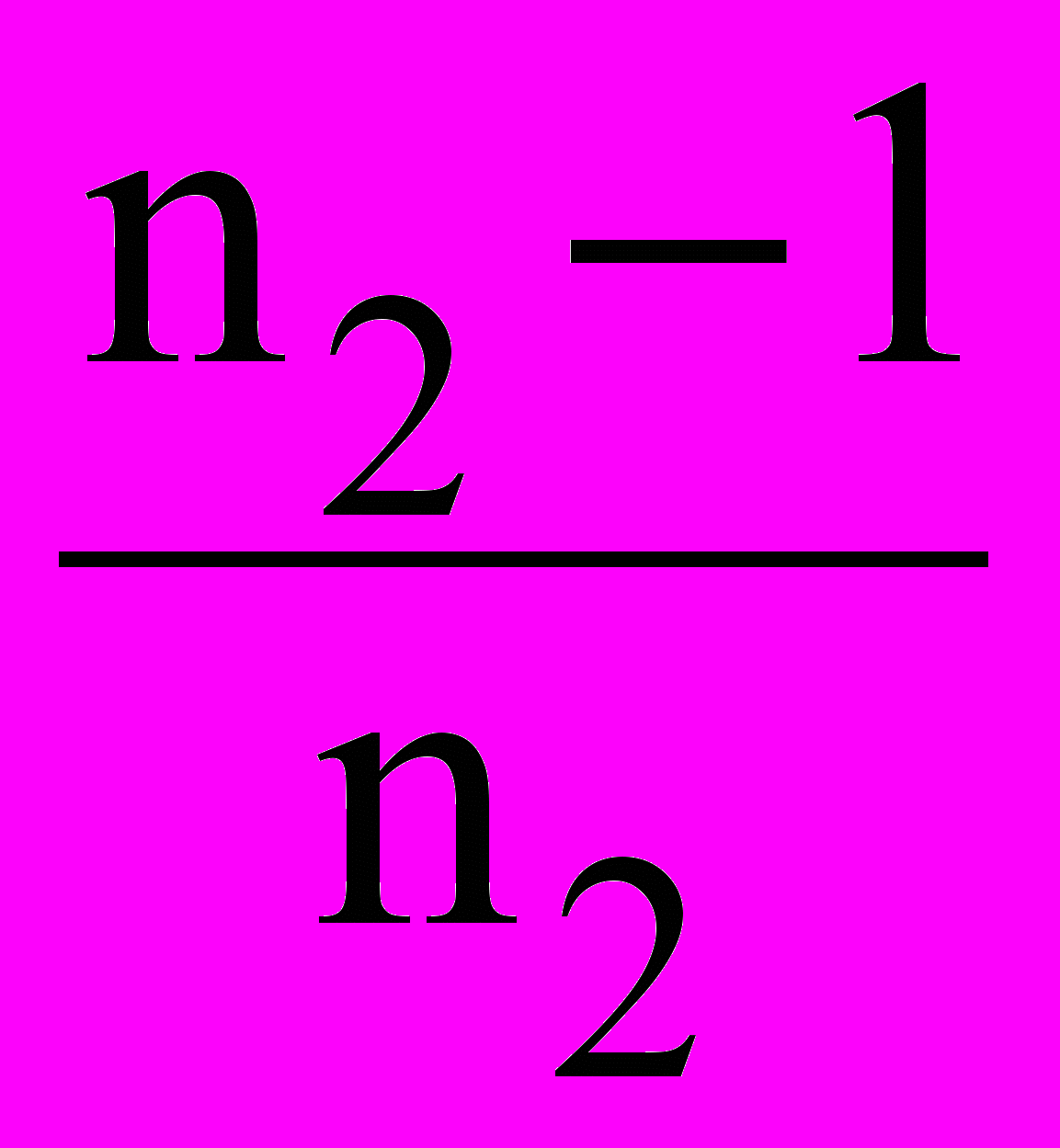
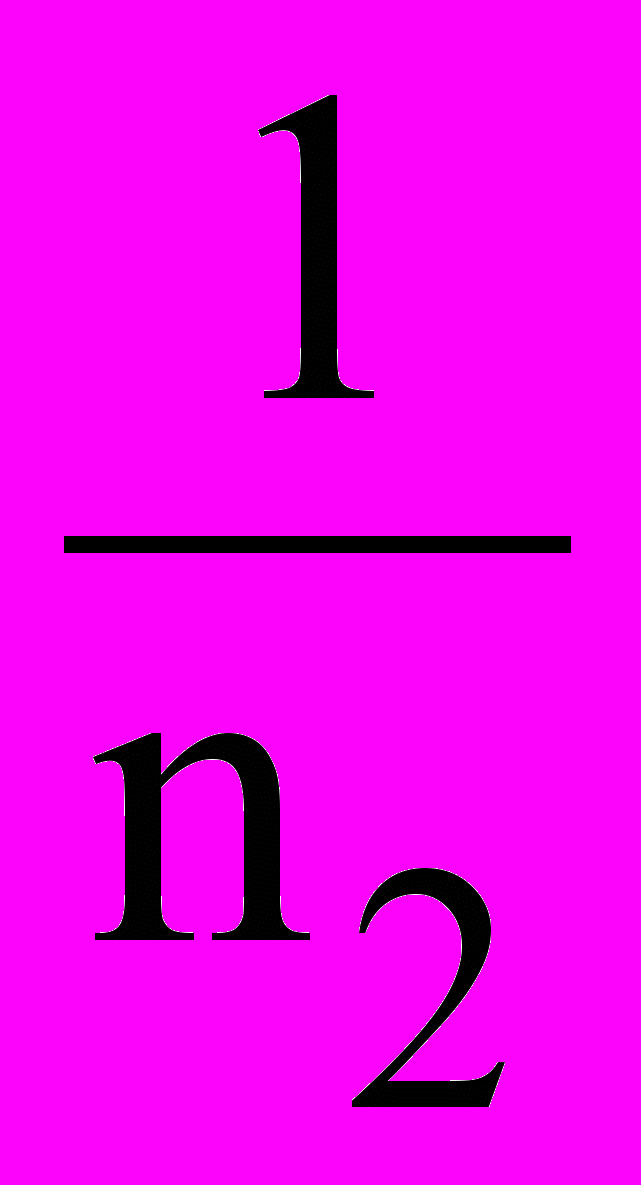
Картина распределения магнитных силовых линий в воздушном зазоре ЛАД весьма сложна и зависит от положения каждого элемента (зубец, паз) по длине ЛАД. Найдены линейные и угловые функции через координаты элементов зубцово-пазовой структуры ЛАД в прямоугольной системе координат. Причем взаимное расположение элементов зубцово-пазовой структуры статора и вторичного тела ЛАД характеризуется величиной перекрытия проекции элементов bz1,z1, bz2,z2 данных структур на координатную ось ОХ. При этом возможны следующие по виду элементарные перекрытия:
- часть зубца статора располагается напротив зубца вторичного элемента;
- часть паза статора располагается напротив зубца вторичного элемента;
- часть паза статора располагается напротив паза вторичного элемента;
- часть зубца статора располагается напротив паза вторичного элемента.
Из условия существования ненулевого перекрытия можно оценить количество элементарных перекрытий между элементом i, принадлежащим зубцово-пазовой структуре статора и элементом j, принадлежащим зубцово-пазовой структуре вторичного элемента, при изменении j от jmin до jmax, при которых
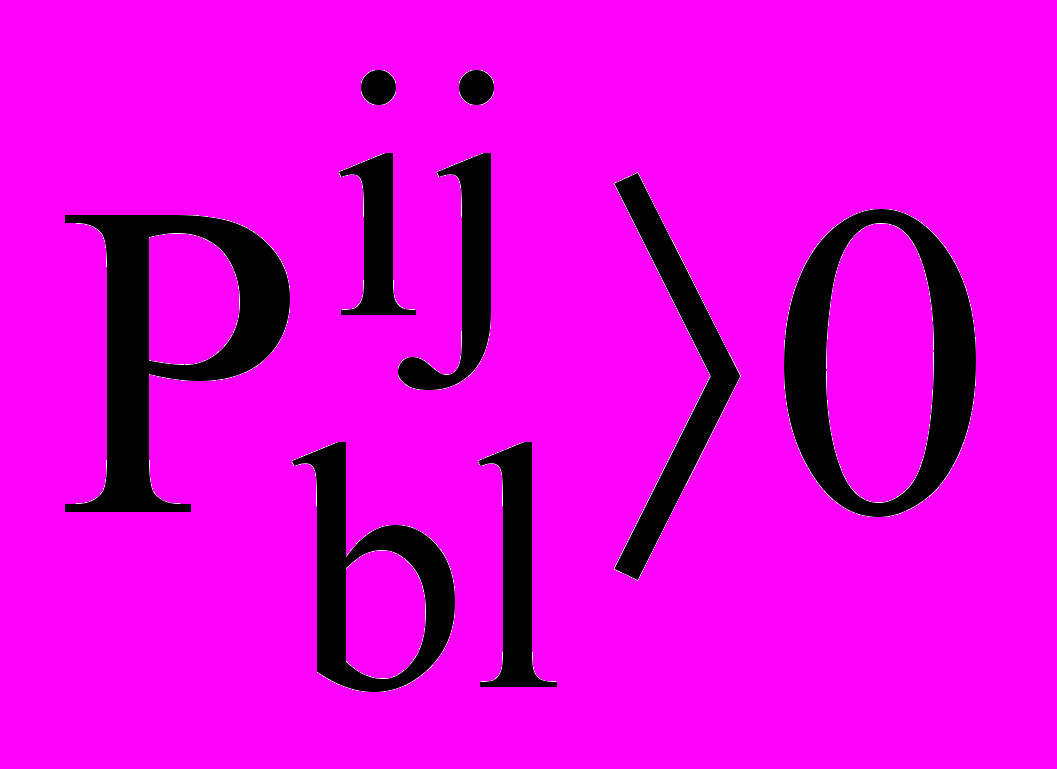
Из данных рассуждений следует, что возможен случай, когда проекция элемента зубцово-пазовой структуры статора намного превышает проекцию элемента зубцово-пазовой структуры вторичного элемента на ту же ось. Функцию перекрытия для данной структуры ЛАД зададим, введя понятие «обобщенное перекрытие».
Обобщенное перекрытие отличается от элементарного перекрытия условием:
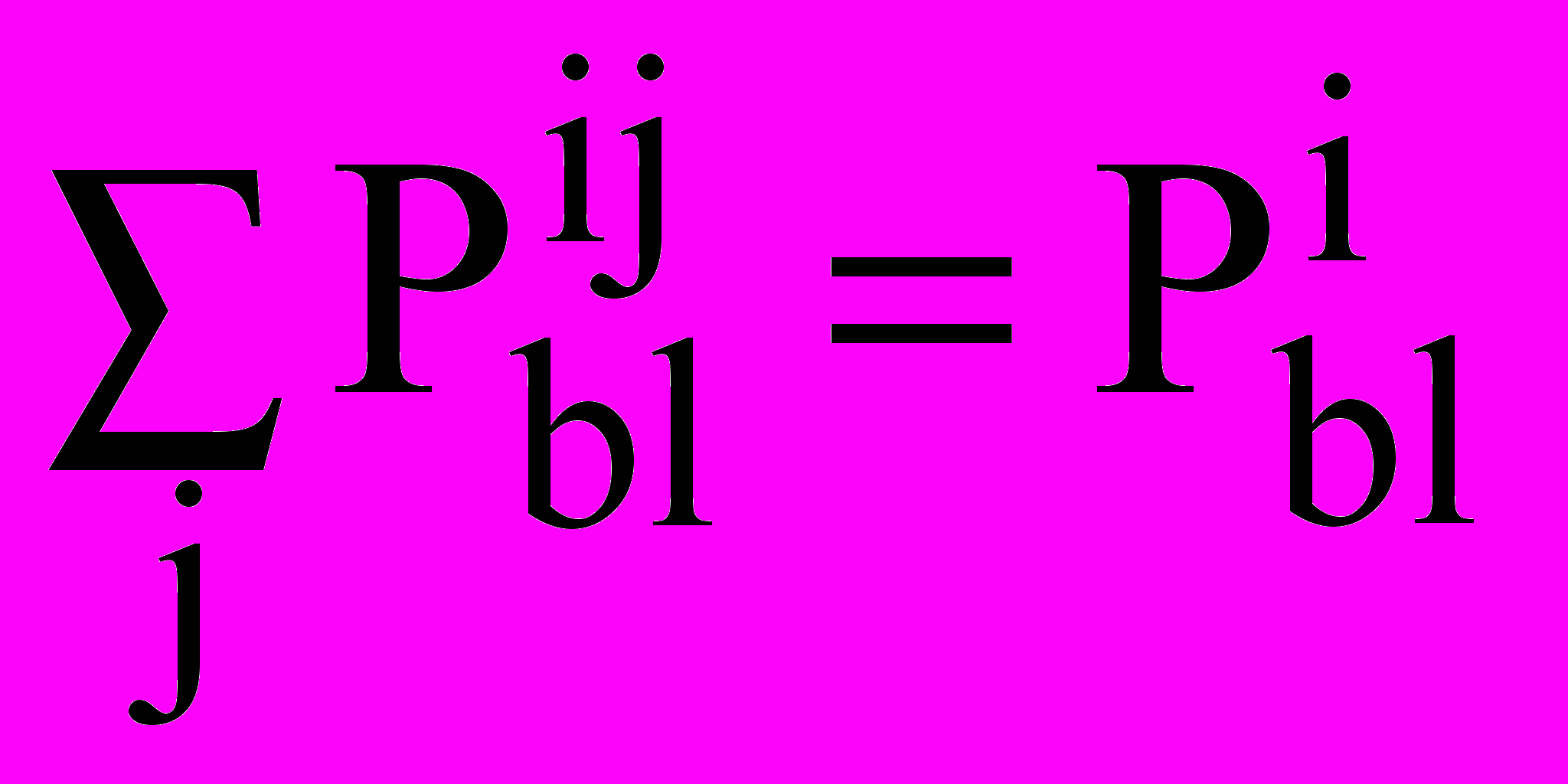
Как следствие изложенного, обобщенное перекрытие для произвольного положения зубцов, пазов статора и вторичного элемента имеет вид:

где
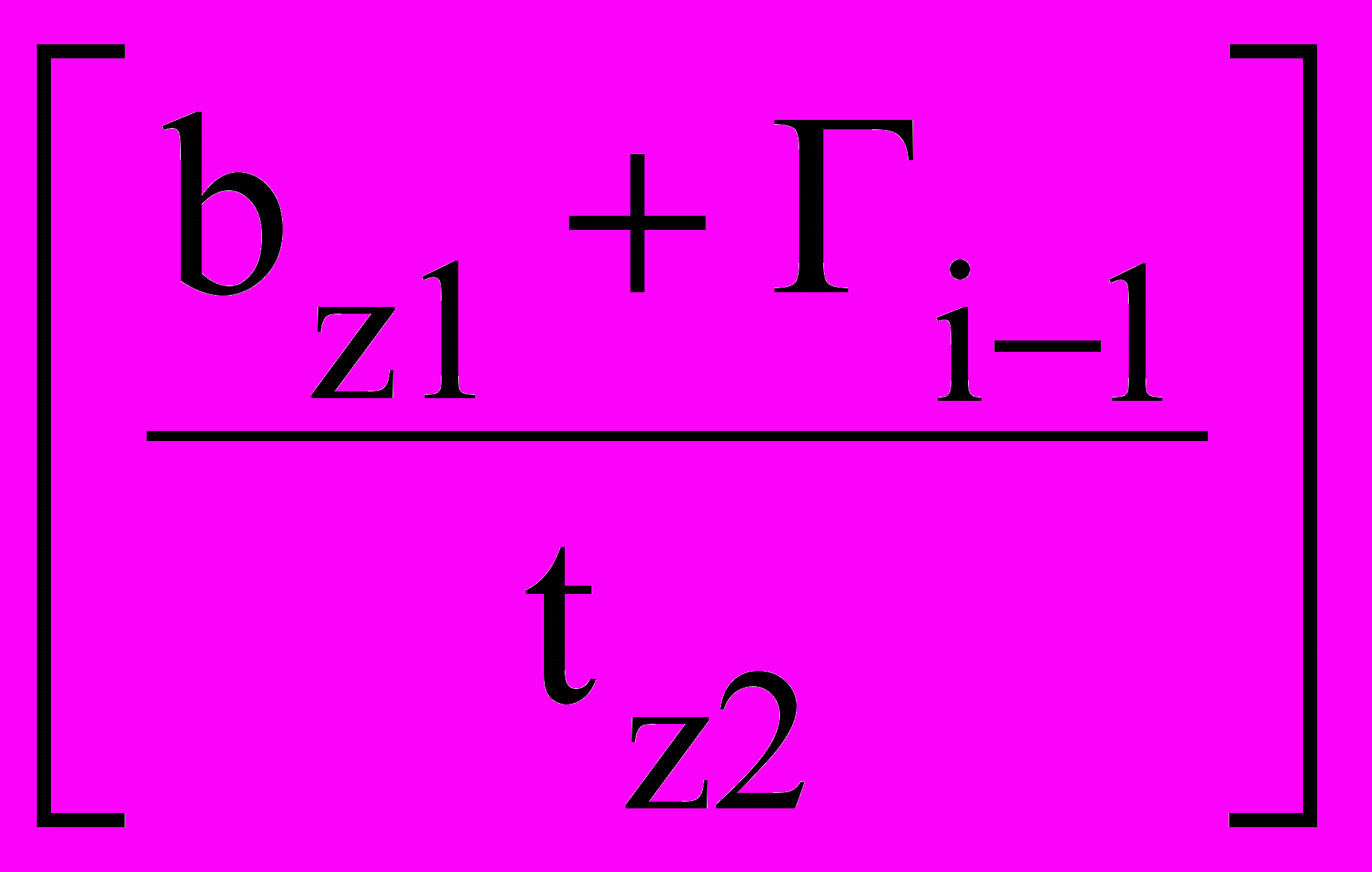
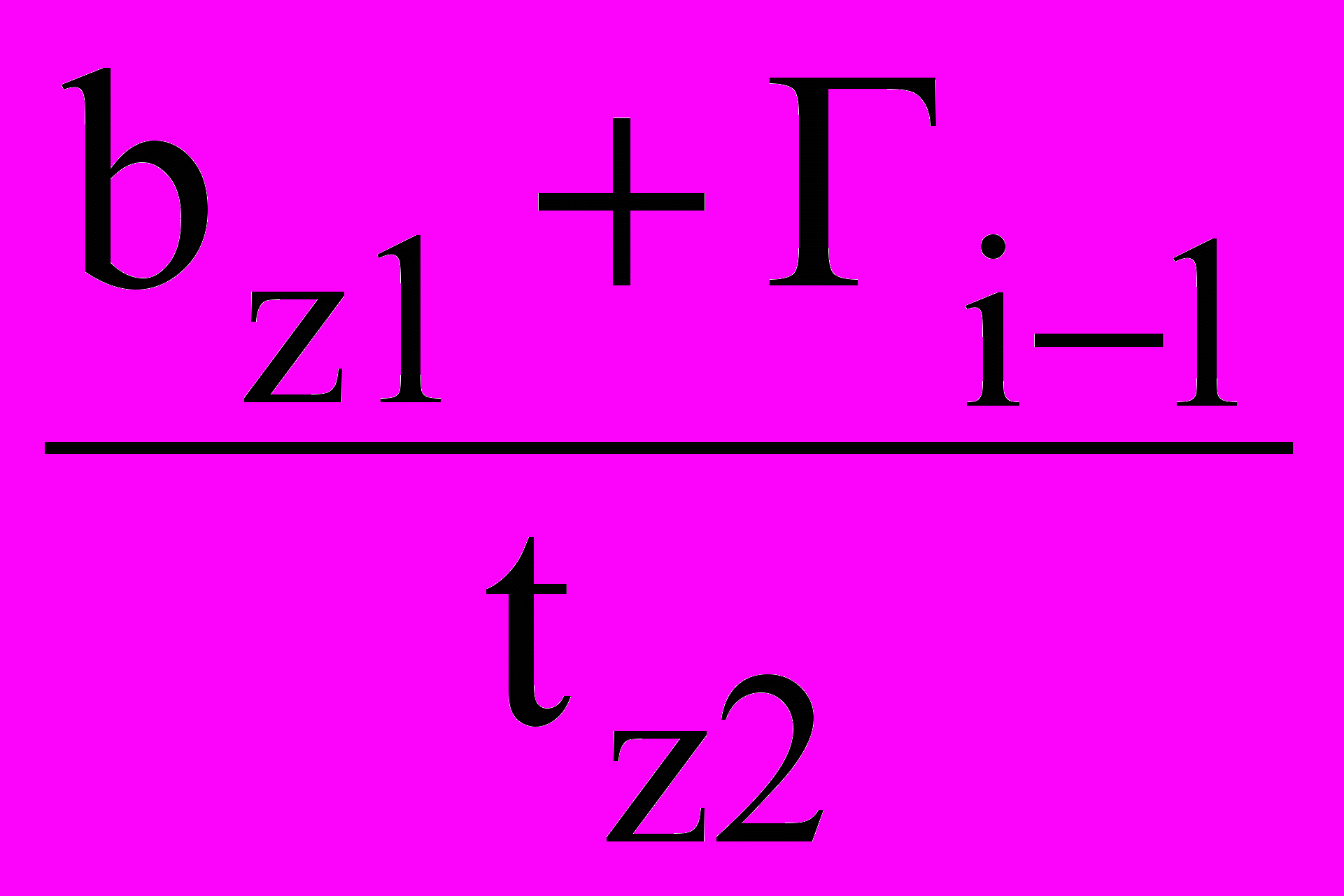
Элементарные обобщенные перекрытия позволили при помощи зависимости коэффициента проводимости λzn от величины перекрытия
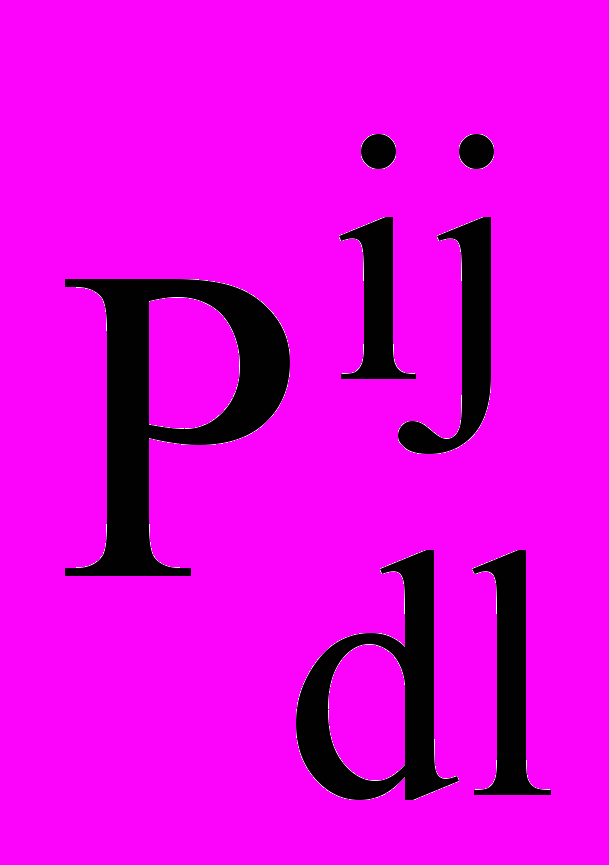
Предложена система линейных уравнений первой степени согласно магнитной схеме замещения, для которой число уравнений совпадает с числом неизвестных, записанная на основе закона полного тока для средней магнитной линии.
Совместное решение уравнений вида
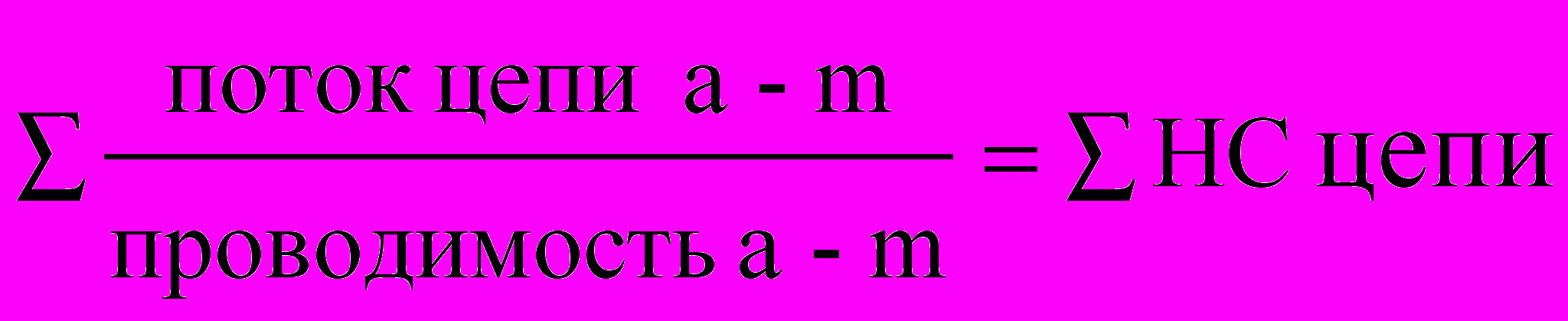
методом Гаусса дает частичные потоки ai-mi.
Значение частичных потоков позволяет определить токи в пазах вторичного элемента от Iz1 до Izi. Значение токов Izi зависит от выбора момента времени и от параметров зубцово-пазовой структуры вторичного элемента. Так, для каждой комбинации числа пазов статора и вторичного элемента имеются два предельных положения:
- положение, когда под серединой зубца статора находится середина зубца вторичного элемента ЛАД;
- положение, когда под серединой зубца статора находится середина паза вторичного элемента ЛАД.
Различие между этими предельными положениями определяет величину полезного усилия, действующего на зубец ЛАД в отдельности.
Взаиморасположение зубцово-пазовых структур ЛАД определяет также и силу магнитного притяжения. Для уменьшения влияния сил магнитного притяжения зубцовые деления вторичного элемента и зубцовое деление статора подобраны так, что их величины представляют между собой взаимно простые числа и отношение величины зубцового деления вторичного элемента к величине зубцового деления статора находится в пределах 0,1-0,2. Правомерность выдвинутых положений подкрепляется данными экспериментальных исследований в лабораторных и промысловых условиях.