Новые легированные кремнием износостойкие сплавы и технология их нанесения
Вид материала | Автореферат |
- Лекция чугуны, их свойства, 75.52kb.
- Рабочая программа, 831.55kb.
- "Сплавы", 35.88kb.
- Доклад по химии Тема: "Сплавы", 34.33kb.
- Рабочая программа По дисциплине «Теория и технология процессов производства, обработки, 188.96kb.
- План лекций по пропедевтике ортопедической стоматологии для студентов 2 курса стоматологического, 8.33kb.
- Аннотация рабочей программы по дисциплине «Теория и технология процессов производства,, 63.12kb.
- Контрольная работа № Студент: Специальность: Курс: Форма обучения, 198.93kb.
- Кафедра «Физическое материаловедение и технология новых материалов» (фмтм), 59.94kb.
- Свойства литейных алюминиевых сплавов и области их применения. Литейные алюминиевые, 53.7kb.
Эффект повышения жаростойкости и красностойкости при сохранении требуемого уровня технологических и служебных характеристик достигли комплексным легированием хромомолибденованадиевой стали Si(1,1-1,8%) и Al(0,1-0,25%). Характерна корреляция «критической» концентрации кремния с зависимостями «кремний-свойства» для сплава 09Х32Н9М3С2 (ОЗШ-6) и стали 17Г4С2 (ОЗН-400М), что подтверждает закономерность механизма упрочнения кремнием.
Эффект вторичного твердения при закалке с 12500С практически не выражен. Лучшие результаты 64-66НRСэ обеспечивают охлаждение в масле с 1180оС и отпуск при 5600С, при сохранении высокой красностойкости:
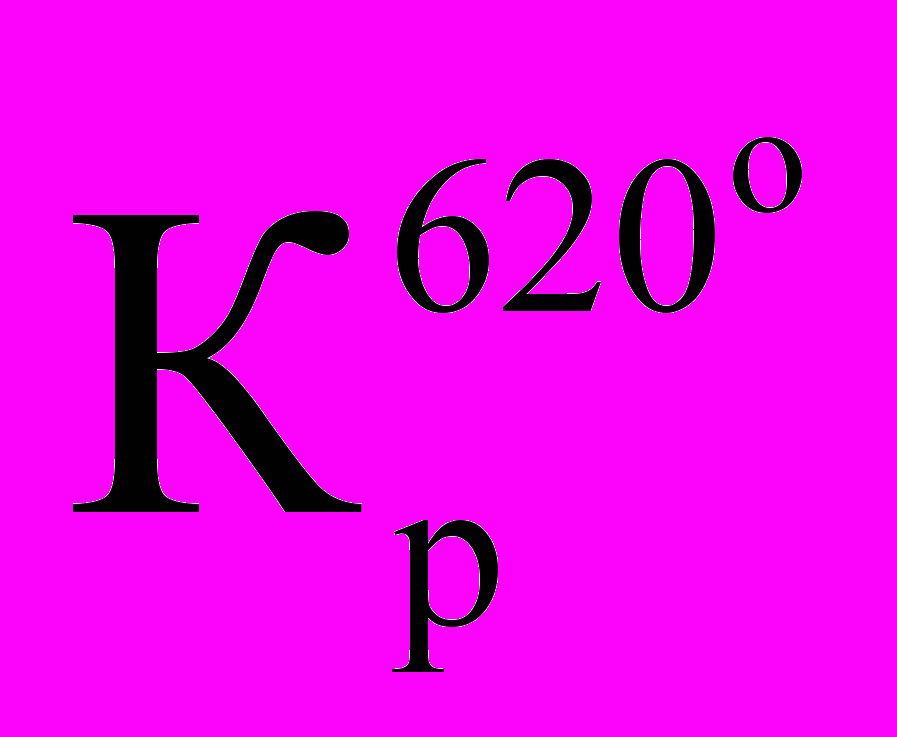
Впервые решена научно-техническая задача повышения жаростойкости, красностойкости и износостойкости молибденованадиевых быстрорежущих сталей до уровня стали Р18 за счет твердорастворного упрочнения кремнием (радиус атома 1,176Å) и молибденом (радиус атома 1,362Å) α-раствора (радиус атома 1,241Å) - увеличения барьера Пайерлса и высокой активности кремния в обеспечении жаростойкости окисной пленки при отжиге и резании.
Внедрение изготовительной наплавки многолезвийного металлорежущего инструмента электродами ОЗИ-6 на семи машиностроительных предприятиях увеличило ресурс биметаллических протяжек и фрез в 1,3-1,4 раза, по сравнению со сталями Р6М5 и 10К18В11М10Х3СФ (наплавленный металл электродов ОЗИ-5).
Глава VII описывает разработку самофлюсующих Fe-Cu-Si-B и Fe-Ni-Si-B-сплавов для сварки ответственных конструкций из серого и высокопрочного чугуна. Решены следующие задачи: разработаны электроды на основе медь-железо с повышенными сварочно-технологическими и служебными характеристиками; с целью экономии никеля разработаны электроды на основе никель-железо с пониженным содержанием никеля в сварном шве и лучшими сварочно-технологическими свойствами; при разработке электродов исследовано влияние кремния и бора на эффект самофлюсования, как способ решения этих задач.
Введение в состав покрытия электродов Fe-Cu по 10-12% лигатуры Fe-Cr-B и лигатуры Cu-Si обеспечивает самофлюсование металла шва и качественное повышение его литейных характеристик. Повышение прочности (до 390 Н/мм2), наряду с высокой пластичностью (δ > 28%), получили при содержании кремния в сварном шве 0,5% и бора 0,24%.
Промышленная апробация на ОАО «ЗИЛ» и «ПО КамАЗ» при ремонте дефектов литья тонкостенных конструкций показала преимущества электродов ОЗЧ-6, по сравнению с лучшими функциональными аналогами: электродами ОЗЖН-1, UТР-8 и порошковой проволокой ПАНЧ-11, - хорошая свариваемость и эксплуатационная надежность сварного соединения. Благодаря этому они 25 лет серийно выпускаются ведущими электродными заводами.
Разработку экономнолегированных Fe-Ni-электродов провели по трем направлениям: исследование и разработка электродов на сварочной проволоке Св-08 с легированием шва никелем через никелевый шлам; оценка влияния кремния и бора на самофлюсующие и служебные свойства электродов на сварочной проволоке Св-08Н50; оценка возможности снижения расхода никеля на погонный метр сварного шва путем введения в электродное покрытие лигатур Fe-Al, Fe-Cr-B и Cu-Si.
Металлографические исследования самофлюсующихся сплавов показали, что при содержании никеля в сварном шве 31,0-32,0% величина зоны отбела и значения твердости соизмеримы с таковыми при Ni ~ 50%. Уменьшение зоны отбела до 0,03-0,09 мм и Нμ до 205-230 при Si = 0,95-1,15 и В = 0,07-0.09 хорошо коррелирует с влиянием кремния на ее протяженность у Cu-Fe-сплавов и литературными данными о «критическом» содержании кремния при графитообразовании в чугуне.
Разработка и апробация принципиально новой технологии сварки труб из ВЧШГ в теплоснабжении. Основной объем теплотрасс в России проложен стальными трубами с изоляцией в бетонных лотках. Срок службы таких трубопроводов – 8-12 лет, основная причина выхода из строя – питтинговая коррозия. Последнее десятилетие применяют бесканальную прокладку предварительно изолированными трубами. Однако, опыт эксплуатации показал, что при некачественном выполнении монтажных стыков пластиковой оболочки, влага, попадающая под полиэтиленовое покрытие, вызывает коррозию труб, приводящую к авариям. Полагали, что внедрение коррозионностойких труб из ВЧШГ, выпускаемых ОАО «Липецкий металлургический завод «Свободный Сокол», повысит надежность и срок эксплуатации теплотрасс. На первом этапе сварку вели аргоном с никелевой присадкой ПАНЧ-11, подогрев до 250-3000С и отпуск при 9600С. Сварку вели встык, в два прохода. Такая технология не получила широкого распространения из-за сложности. Для перехода от аргонодуговой сварки к более привычной для монтажников сварке покрытыми электродами, нами на металлургическом заводе «Свободный Сокол» разработана конструкция и освоено производство принципиально новых, с монтажным раструбно-конусным креплением труб под сварку теплотрасс. Такая конструкция труб существенно повысила технологичность монтажа трубопровода и позволяет вести сварку углового (а не стыкового) шва электродами (а не АРДС), не опасаясь прожога стенки трубы. Подогрев под сварку и отпуск теперь не нужны, за исключением сварки при отрицательных температурах и в сложно напряженном состоянии трубопровода. Технологию аттестовали в ОАО «НПО «ЦКТИ» и получили разрешение Госгортехнадзора на сварку теплотрасс из труб ВЧШГ с применением раструбно-нахлесточного соединения. Технология апробирована при монтаже теплотрасс в ОАО «Ленэнерго», ОАО «Липецкэнерго» и ОАО «Коломенский завод», элементы технологии защищены тремя патентами.
Глава VIII. Специальные стали для изготовления металлоформ центробежного литья труб из ВЧШГ (17Х2НМФЮ) и литых корпусов задвижек для нефтепровода «ВСТО» (10ГНМЛ). Опыт изучения зависимостей «химический состав-структура-свойства» применили при создании специальных сталей.
Разработанная сталь 17Х2НМФЮ имеет повышенную жаропрочность и жаростойкость, по сравнению с функциональным аналогом сталью 20ХМ:
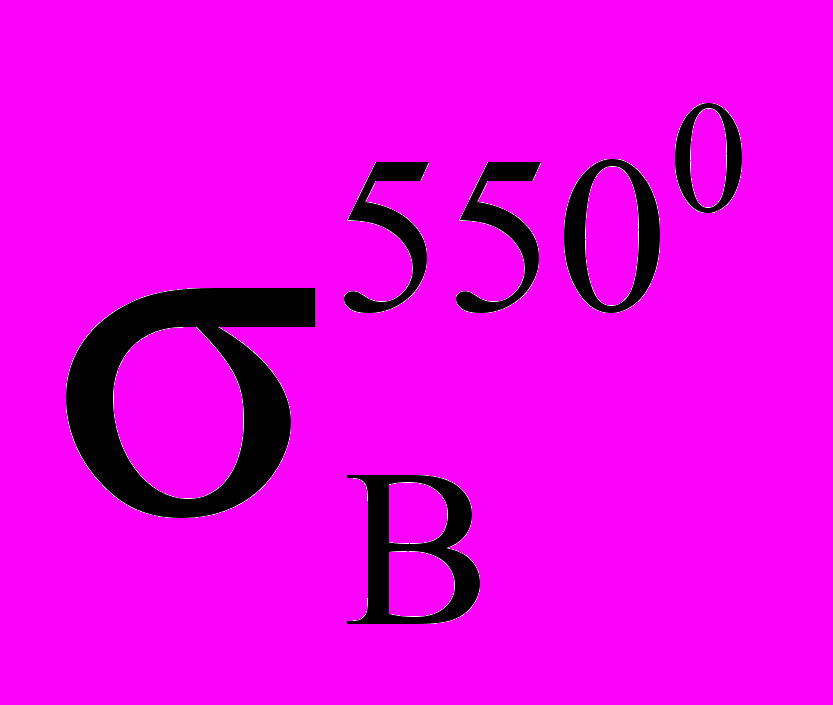
Разработанная, совместно с ОАО «Волжский трубный завод» и ОАО «ЧТПЗ», технология изготовления трубных заготовок металлоформ из стали 17Х2НМФЮ, спроектированная установка и технология автоматической аргонодуговой ремонтной наплавки металлоформ проволокой Св-07Х25Н13 обеспечили экономический эффект свыше 30,0 млн. руб. в год (в ценах 2004 года) и позволили отказаться от дорогих и менее стойких кованых заготовок металлоформ из стали 20ХМ. Новизна стали подтверждена патентом.
Сталь 10ГНМЛ. Основные требования к стали для трубопроводной арматуры, эксплуатируемой в условиях климатического холода: повышенная прочность (σВ > 480 МПа и σ0,2 > 300 МПа) при КСV
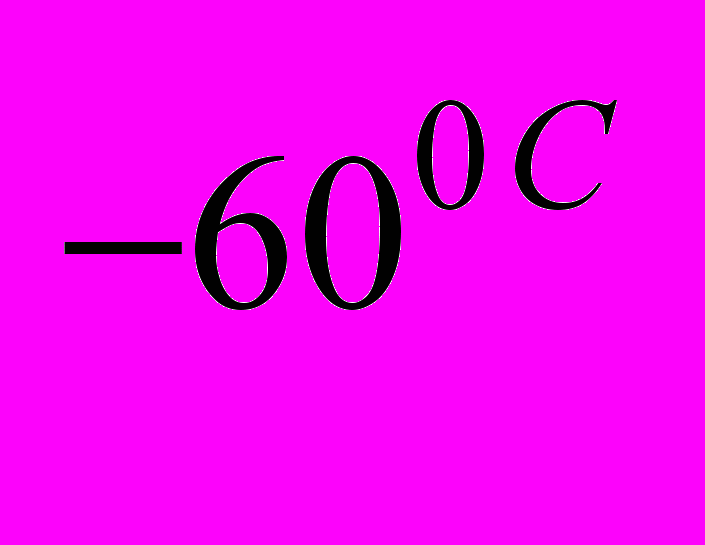
На сталь 10ГНМЛ разработаны ТУ 0870-001-05785572-2007, получен патент 2340698, она успешно выплавляется на ОАО «Тяжпромарматура» с 2007 года и ее качество подтверждено безаварийной эксплуатацией задвижек на нефтепроводе «ВСТО». Разработана технология автоматической сварки корпусных деталей и приварки катушек. Результаты испытаний образцов, вырезанных из корпуса задвижки: предел текучести 334-394 МПа, временное сопротивление 514-530 МПа, относительное удлинение 28-31%, сужение 63-69%. Температура хрупко-вязкого перехода ТКО = -400С. Параметр мастер-кривой Т0 = -1230С (температура, соответствующая вязкости разрушения 100МПа·м0,5 для вероятности 50%).
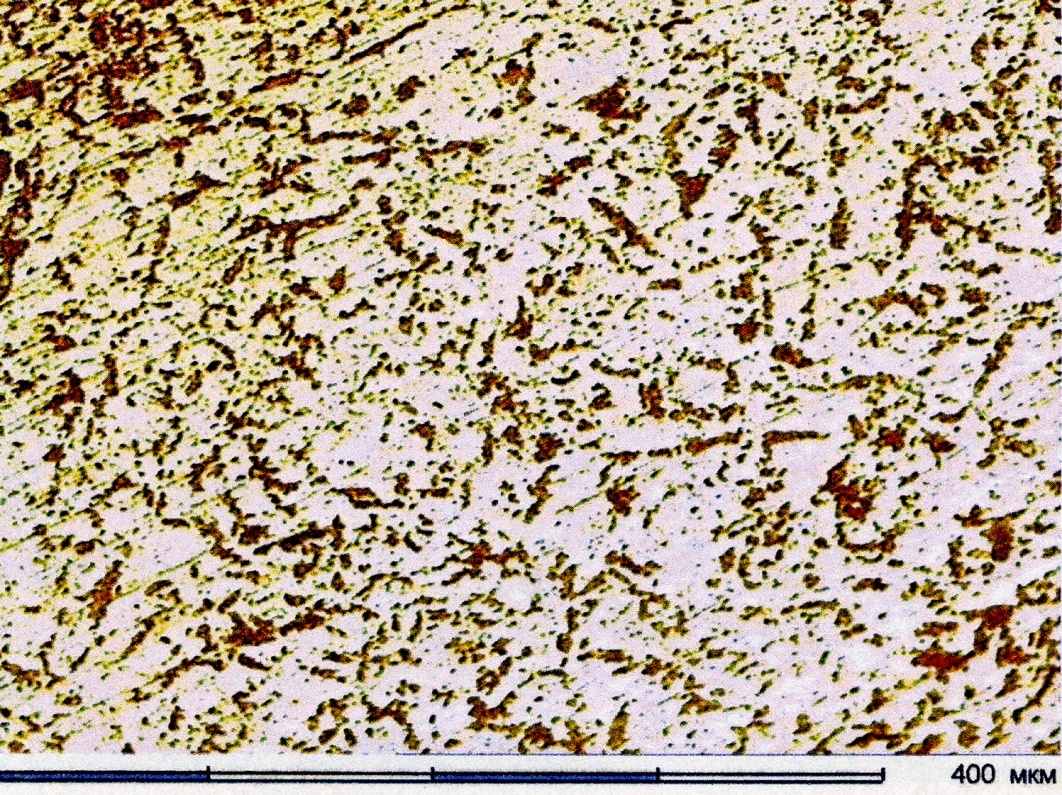
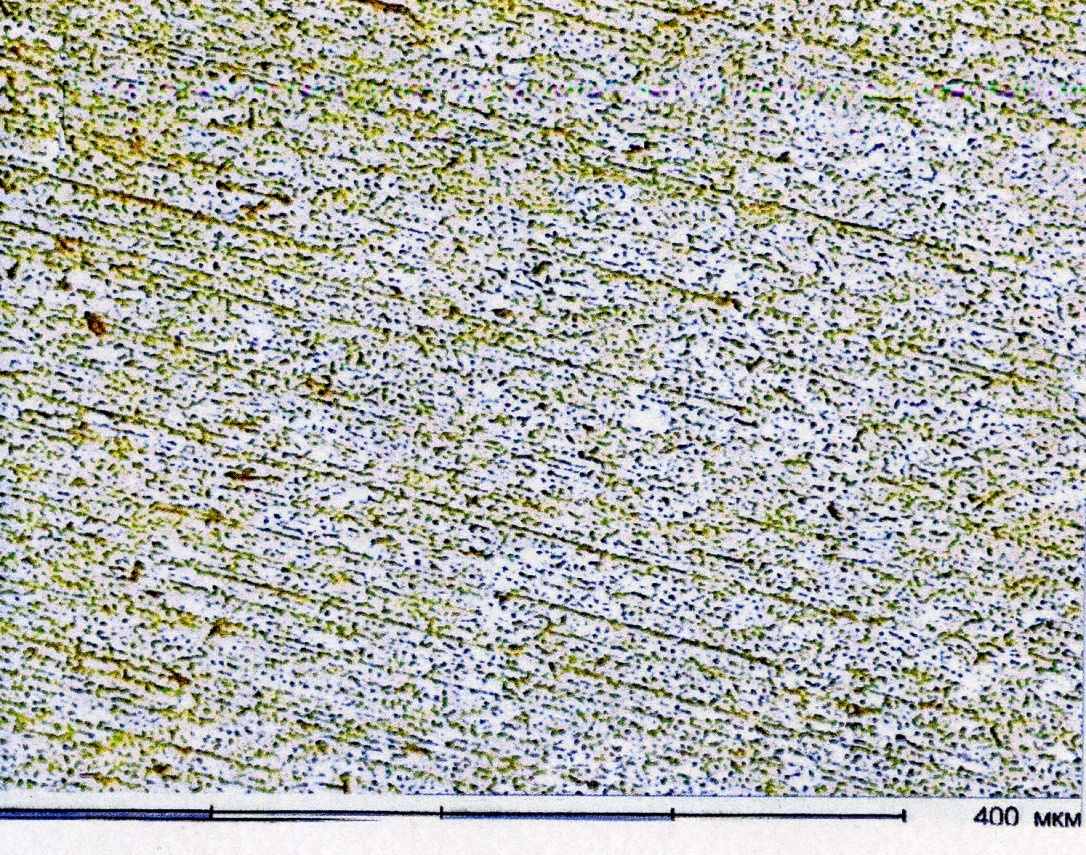
а б
Рисунок 7. Микроструктура стали 20ГМЛ (а) и стали 10ГНМЛ (б), ×300
ОБЩИЕ ВЫВОДЫ И РЕЗУЛЬТАТЫ РАБОТЫ
1 На основе изучения влияния кремния на механизм упрочнения и изнашивания, созданы методика разработки и гамма унифицированных легированных кремнием сталей и сплавов для изготовительной наплавки тяжелонагруженных элементов пар трения в металлургии, машиностроении, энергетике, нефтяной, газовой и горнодобывающей промышленности.
На основе изучения структурных и фазовых превращений в наплавленном соединении, разработана технология изготовительной наплавки новых сталей и сплавов, обеспечивающая высокую эксплуатационную надежность биметаллических деталей и узлов.
2 Предложена физическая модель изнашивания легированных кремнием сталей при высокотемпературном трении металл по металлу, согласно которой износостойкость обеспечивает взаимодействие трех факторов: жаростойкой, с высокой регенерирующей способностью кремнийсодержащей пленки вторичных структур, жаропрочного подповерхностного слоя поверхности трения и механизма его упрочнения диффундирующими атомами молибдена, для которых SiO2 – барьер для диффузии.
Эта модель легла в основу разработки дисперсионноупрочняемой стали 09Х32Н9М3С2 (ОЗШ-6), теплостойкость (10800С), жаропрочность (
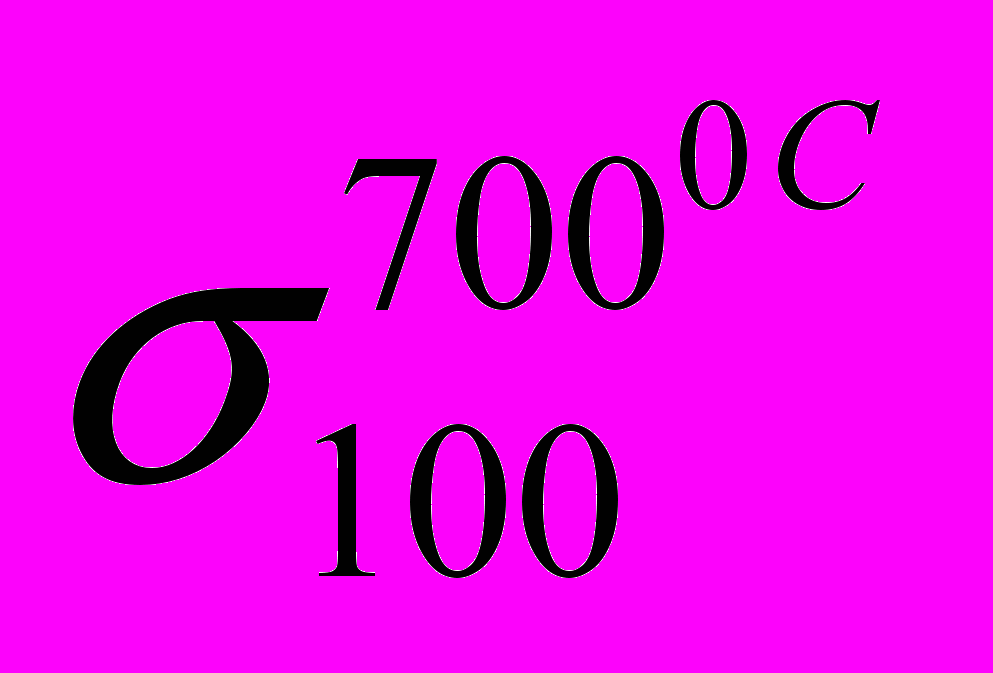
Характерная особенность изнашивания стали ОЗШ-6 - отсутствие микросхватывания поверхностей трения, подтверждающая влияние кремния на обе его составляющие: молекулярную и механическую.
3 На основе изучения влияния уровня легирования Fe-Cr-Ni-Si-Mo-сталей на кинетику σ-упрочнения, разработан способ повышения сопротивляемости образованию трещин при многослойной наплавке сплава ОЗШ-6 путем уменьшения температурно-временного интервала дисперсионного упрочнения и изменения морфологии σ-фазы высокотемпературными карбидами ванадия; и, наряду с легированием 0,1-0,3% алюминия, измельчающим структуру стали, реализован при создании стали 09Х32Н10М3С1ФЮ (ОЗШ-8).
Экспериментально установлена возможность упрочнения наплавленной оснастки автоматических ковочных комплексов непосредственно в контакте с первыми штампуемыми деталями, что впервые в мировой практике сокращает технологию с семи до двух операций: наплавка (без подогрева и отпуска) и механическая обработка (без отжига).
4 На основе исследования фрактограмм поверхности трения: микротрещины и наплывы, свидетельствующие о многократном передеформировании, - определили усталостный характер изнашивания в газоабразивном потоке сталей типа 09Х30Н10С2М1. С учетом этого, экспериментально установили содержание кремния (~1,7% при резком скачке износостойкости) и режим старения (5800С, 4ч), фиксирующие процесс σ-старения на стадии предвыделения, когда параметры решетки второй фазы и аустенита когерентны и релаксационная способность сплава еще велика.
Для стали 09Х30Н10С2М1 характерно редкое качество – высокая износостойкость как при α = 15, так и 900, что можно объяснить двумя факторами: упрочнением поверхностного слоя диффундирующими к поверхности раздела «металл-окисная пленка» атомами кремния и, как следствие, замедлению образования и слияния микропустот, и уменьшением кремнием количества мартенсита деформации (при α = 900 увеличение кремния от 0,20 до 3,79% уменьшает количество мартенсита от 32 до 14%) и, как результат, повышением релаксационной способности при изнашивании.
Плотность дислокаций, за счет интенсификации сигма- и мартенситного упрочнений, растет до 1010-1011 см-2. Исчерпание возможностей скольжения дислокаций из-за высокой дисперсности σ-фазы приводит к фрагментации тонкой структуры и двойникованию, эти процессы релаксируют напряжения трения и повышают износостойкость сплава.
5 Установлено, что при содержании Si ~ 1,1% в сталях типа 15Г3С1 и 17Г4С2 мартенситное упрочнение переходит в твердорастворное и зернограничное. Это позволило решить научно-техническую задачу обеспечения стабильности свойств наплавленного металла электродов средней твердости (250-400НВ): разработанные электроды ОЗН-300М и ОЗН-400М отличает повышенная стабильность служебных характеристик наплавленного металла, практически не зависящая от погонной энергии наплавки и скорости охлаждения детали.
Зависимость «кремний-размер блоков- микродеформации» носит бимодальный характер: наименьшие блоки и микродеформации кристаллической решетки при Si = 0,94 и 3,84%, - что хорошо коррелирует с повышением износостойкости в этих точках и подтверждает принятую концепцию усталостного характера изнашивания и переход к прогнозируемому твердорастворному упрочнению.
6 На примере стали 80Х6Г6С3РАФ (ОЗН-7) показана эффективность комплексного упрочнения кремнием (твердорастворного) и карбидного. Изучено влияние структурного и фазового состава на механизмы упрочнения и изнашивания легированных кремнием сталей. Аустенитная структура стабильна при изнашивании (вплоть до энергии удара 2,5×105 Дж/м2), напряжения решетки минимальны (Емакс = 0,01-0,03×10-2), а их рост в процессе изнашивания (до 0,63×
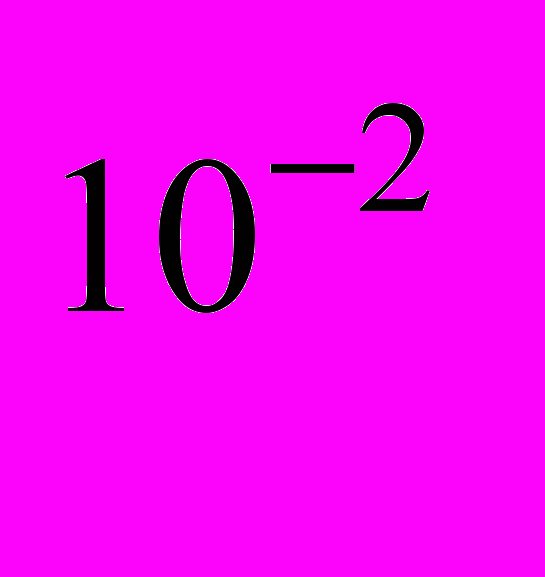
При метастабильности аустенита, γ→α - превращение активно уже при небольшой энергии удара, сталь 80Х6Г6Р1АФ исчерпывает запас внутренней энергии и истирается.
Эти результаты коррелируют с характером зависимости «кремний-размер блоков-величина микродеформаций-износостойкость» для Fe-C-Mn-Si-сплавов типа 15Г3С1 и 17Г4С2 и подтверждают общность процессов твердорастворного и зернограничного упрочнений кремнием для сплавов разного структурного и фазового состава.
7 Решена научно-техническая задача повышения жаростойкости, красностойкости и износостойкости при резании металла низколегированных вольфрамом молибденванадиевых сталей до уровня стали Р18. Этот эффект наиболее ярко выражен при ~ 1,1% кремния и объясняется термической стабильностью твердорастворного упрочнения и высокой активностью ионов кремния в формировании жаростойкой окисной пленки при отжиге и резании. На основе стали 110Х5М8Ф2В2С2Ю (ОЗИ-6) разработана технология изготовительной наплавки многолезвийного инструмента автоматических линий, ресурс которого в 1,4-2,5 раза превышает сталь Р18.
8 Установлено, что легирование кремнием (0,5-0,8%) и бором (0.2-0,5%) уменьшает протяженность зоны отбела при сварке разработанными железомедными (ОЗЧ-6) и железоникелевыми электродами (ОЗЧ-7) за счет достижения самофлюсующих свойств сплавов.
Более того, достигнутое свойство самофлюсования позволяет существенно уменьшить содержание никеля от 50-55% (принятый уровень) до 31-32% без снижения уровня служебных характеристик сварного соединения, что наряду с разработанной технологией легирования никелем через шлам, существенно повышает технико-экономические показатели разработанных электродов ОЗЧ-7.
9 На основе принципиально новых конструкции соединения (раструбно-конусного) труб, технологии монтажа и сварочной проволоки впервые в мировой практике разработана и аттестована технология сварки электродами теплотрасс из труб ВЧШГ. Элементы технологии защищены тремя патентами, а теплотрассы проложены в С.-Петербурге, Липецке, Коломне, Ростове и успешно эксплуатируются в течение 5-7 лет.
10 Опыт изучения зависимостей «химический состав-структура-свойства» применили при разработке специальных сталей:
- впервые разработаны сталь (17ХН2МФЮ) и технология производства (на ОАО «ВТЗ» и «ЧТПЗ») трубных заготовок металлоформ для центробежного литья труб из ВЧШГ, повышающие ресурс кокилей до 2,5-крат, по сравнению с обычно применяемыми в мировой практике коваными заготовками из стали 20ХМ;
- по заданию ОАО «Транснефть» для проекта «нефтепровод Восточная Сибирь – Тихий океан» разработаны хладостойкая повышенной прочности свариваемая сталь для литых корпусов задвижек DN150-1200 мм, РN 8,0- 12,5 МПа, отвечающая требованиям «API Standard 600», технология автоматической приварки днищ и катушек. Высокие значения прочностных свойств и свариваемости достигли, в основном, существенным измельчением зерна, по сравнению со сталью 20ГМЛ, что отвечает современным тенденциям в разработке конструкционных сталей.
11 Экспериментально установлены концентрации кремния, обеспечивающие высокую износостойкость сталей и сплавов для основных видов изнашивания. Близкие значения «критического» содержания кремния для сплавов различных структурных классов и видов изнашивания указывают на универсальность свойств исследованных твердорастворного и зернограничного упрочнений и их ведущую роль в обеспечении износостойкости.
Научную и практическую значимость разработанных в диссертационной работе износостойких сплавов и системы их унификации подтверждают 30-летний опыт серийного изготовления (ведущими электродными заводами) и применения в различных отраслях техники семнадцати созданных сплавов (электродов) для изготовительной наплавки тяжелонагруженных пар трения основных видов изнашивания: трение металл по металлу при высоких температурах и удельных давлениях, абразивный и газоабразивный износ различной интенсивности, коррозионно-механический износ, импульсно-ударное нагружение.
Разработанная технология изготовительной наплавки новых сплавов обеспечивает высокую эксплуатационную надежность биметаллических деталей и узлов. Апробирована технология нанесения новых сплавов методами пайки, индукционной наплавки и прокатки.
СПИСОК ОСНОВНЫХ ПУБЛИКАЦИЙ ПО ТЕМЕ ДИССЕРТАЦИИ
1. Лужанский И.Б., Медриш И.Н. Плазменная наплавка стеллита на уплотнительные поверхности энергетической арматуры. //Сварочное производство, 1971, 10.
2. Лужанский И.Б., Рунов А.Е., Гельман А.С. Плазменная наплавка с токоведущей проволочной присадкой уплотнительных поверхностей энергетической арматуры. // Сб. научных докладов Всесоюзного технического совещания: Прогрессивные методы сварки и наплавки в черной металлургии и машиностроении. Жданов, 1972.
3. Лужанский И.Б., Рунов А.Е. Материалы для наплавки уплотнительных поверхностей энергетической арматуры. Материалы научной конференции: Износостойкая наплавка в энергомашиностроении, Киев, ИЭС, 1972.
4. Лужанский И.Б., Рунов А.Е., Гельман А.С. Новые сплавы системы Fe-Cr-Ni-Si-Mo для наплавки уплотнительных поверхностей энергетической арматуры. // НИИНФОРМТЯЖМАШ, 14-73-8, с. 12-15.
5. Лужанский И.Б. Исследование и разработка технологии автоматической плазменной наплавки с токоведущей проволочной присадкой уплотнительных поверхностей энергетической арматуры. // Труды ЦНИИТМАШ, 1974, 120.
6. Камакин Н.И., Лужанский И.Б. Выбор сварочных материалов и способа механизированной наплавки никелевых сплавов на углеродистую сталь. //Сварочное производство, 1974, 2.
7. Ким Э., Шенк Р.И., Могильнер М.Н., Ермоленко Е.В., Лужанский И.Б., Рунов А.Е., Яровинский Х.Л. Коррозионная стойкость наплавленных уплотнительных поверхностей арматуры. // Сварочное производство, 1974, 4, с. 38-40.
8. Лужанский И.Б. Плазменная наплавка уплотнительных поверхностей энергетической арматуры. // Энергомашиностроение, 1979, 7, с. 28-31.
9. Лужанский И.Б., Яровинский Х.Л. Исследование и разработка экономнолегированных электродов для наплавки режущего инструмента. // Материалы научной конференции: Применение пайки, сварки и склеивания при изготовлении режущего инструмента. М., 1981, с. 123-125.
10. Лужанский И.Б., Яровинский Х.Л. Новые эффективные наплавочные электроды МОСЗ. //Материалы научно-практической конференции: Повышение качества и эффективности сварочного производства. М., МДНТП, 1982.
11. Лужанский И.Б. Разработка наплавочных сплавов для различных условий износа на основе их легирования кремнием. // Материалы научно-практической конференции: Повышение качества и эффективности сварочного производства на предприятиях г.Москвы. М., МДНТП, 1984.
12. Лужанский И.Б. Исследование свойств металла, наплавленного электродами ОЗИ-6. // Материалы научного семинара: Новые процессы наплавки, Киев, ИЭС, 1984, с. 58-63.
13. Лужанский И.Б. Прогрессивные способы наплавки. М, Машиностроение, 1984, 55 с.