Классификация металлорежущих станков
Вид материала | Документы |
- Ментов и других изделий, поэтому количество металлорежущих станков, их технический, 250.37kb.
- Вид работ №24. 16. «Пусконаладочные работы станков металлорежущих многоцелевых с чпу», 18.43kb.
- Рабочая учебная программа дисциплины технология конструкционных материалов птм образовательная, 142.97kb.
- I. Требования к выдаче Свидетельства о допуске к пусконаладочным работам станков металлорежущих, 211.44kb.
- Гост исо 8995-2002, 746.87kb.
- Требования к выдаче свидетельств о допуске по виду работ «Пусконаладочные работы станков, 55.97kb.
- Токарные станки. Классификация токарных станков. Характеристика токарных станков, 105.04kb.
- Допуски калибров: пробок и скоб, 51.05kb.
- Целевая программа «Развитие научного потенциала высшей школы (2006-2008 годы)» Мероприятие, 311.58kb.
- Исследование и испытание станков, 201.55kb.
- Классификация металлорежущих станков
К современным машинам и приборам предъявляются высокие требования по технико-эксплуатационным характеристикам, точности и надежности работы. Эти показатели обеспечиваются высокой точностью размеров и качеством обработанных поверхностей деталей машин и приборов. Поэтому, несмотря на большие достижения технологии производства высококачественных заготовок, роль обработки резанием и значение металлорежущих станков в машиностроении непрерывно повышаются.
Современные металлорежущие станки — это разнообразные и совершенные рабочие машины, использующие механические, электрические и гидравлические методы осуществления движений и управления рабочим циклом, решающие самые сложные технологические задачи.
Станкостроение развивается как в количественном, так и качественном отношении. Непрерывно повышаются точность, производительность, мощность, быстроходность и надежность работы станков. Улучшаются эксплуатационные характеристики, расширяются технологические возможности, совершенствуются архитектурные формы станков. Успешное развитие станкостроения обеспечивает перевооружение всех отраслей нашей промышленности высокопроизводительными и высококачественными станками, многие из которых отвечают требованиям мировых стандартов.
В основу классификации металлорежущих станков, принятой в нашей стране, положен технологический метод обработки заготовок. Классификацию по технологическому методу обработки проводят в соответствии с такими признаками, как вид режущего инструмента, характер обрабатываемых поверхностей и схема обработки. Станки делят на токарные, сверлильные, шлифовальные, полировальные и доводочные, зубообрабатывающие, фрезерные, строгальные, разрезные, протяжные, резьбообрабатывающие и т. д.
Классификация по комплексу признаков наиболее полно отражается в общегосударственной Единой системе условных обозначений станков. Она построена по десятичной системе; все металлорежущие станки разделены на десять групп, группа — на десять типов, а тип — на десять типоразмеров. В группу объединены станки по общности технологического метода обработки или близкие по назначению (например, сверлильные и расточные). Типы станков характеризуют такие признаки, как назначение, степень универсальности, число главных рабочих органов, конструктивные особенности. Внутри типа станки различают по техническим характеристикам.
В соответствии с этой классификацией каждому станку присваивают определенный шифр. Первая цифра шифра определяет группу станков, вторая тип, третья (иногда третья и четвертая) показывает условный размер станка. Буква на втором или третьем месте позволяет различать станки одного типоразмера, но с разными техническими характеристиками. Буква в конце шифра указывает на различные модификации станков одной базовой модели. Например, шифром 2Н135 обозначают вертикально-сверлильный станок (группа 2, тип 1), модернизированный (Н), с наибольшим условным диаметром сверления 35 мм (35).
Различают станки универсальные, широкого применения, специализированные и специальные. На универсальных станках выполняют самые разнообразные работы, используя заготовки многих наименований. Примерами таких станков могут быть токарно-винторезные, горизонтально-фрезерные консольные и др. Станки широкого назначения предназначены для выполнения определенных работ на заготовках многих наименований (многорезцовые, токарно-отрезные станки). Специализированные станки предназначены для обработки заготовок одного наименования, но разных размеров (например, станки для обработки коленчатых валов). Специальные станки выполняют определенный вид работ на одной определенной заготовке.
По степени автоматизации различают станки с ручным управлением, полуавтоматы, автоматы и станки с программным управлением. По числу главных рабочих органов станки делят на одношпиндельные, многошпиндельные, односуппортные, многосуппортные. При классификации по конструктивным признакам выделяются существенные конструктивные особенности (например, вертикальные и горизонтальные токарные полуавтоматы). В классификации по точности установлены пять классов станков: Н — нормальной, П — повышенной, В — высокой, А — особо высокой точности и С — особо точные станки.
- Обработка заготовок на станках токарной группы
Технологический метод формообразования поверхностей заготовок точением характеризуется двумя движениями: вращательным движением заготовки (скорость резания) и поступательным движением режущего инструмента — резца (движение подачи). Движение подачи осуществляется параллельно оси вращения заготовки (продольная подача), перпендикулярно к оси вращения заготовки (поперечная подача), под углом к оси вращения заготовки (наклонная подача).
Разновидности точения:
- обтачивание — обработка наружных поверхностей;
- растачивание — обработка внутренних поверхностей;
- подрезание — обработка плоских (торцовых) поверхностей;
- резка — разделение заготовки на части или отрезка готовой детали от заготовки — пруткового проката.
На вертикальных полуавтоматах, автоматах и токарно-карусельных станках заготовки имеют вертикальную ось вращения, на токарных станках других типов — горизонтальную. На токарных станках выполняют черновую, получистовую и чистовую обработку поверхностей заготовок.
Токарные резцы. По технологическому назначению различают резцы:
- Проходные - для обтачивания наружных цилиндрических и конических поверхностей;
- Подрезные - для обтачивания плоских торцовых поверхностей;
- Расточные - для растачивания сквозных и глухих отверстий;
- Отрезные - для разрезания заготовок;
- Резьбовые для нарезания наружных и внутренних резьб;
- Фасонные круглые и призматические для обтачивания фасонных поверхностей;
- Прорезные для обтачивания кольцевых канавок и др.
По характеру обработки различают резцы черновые, получистоые и чистовые. По форме рабочей части резцы делят на прямые, отогнутые, оттянутые. По направлению подачи резцы подразделяют на правые и левые. Правые работают с подачей справа налево, левые — слева направо. По способу изготовления различают резцы целые, с приваренной встык рабочей частью, с приваренной или припаянной пластинкой инструментального материала, со сменными пластинками режущего материала.
Для высокопроизводительного точения с большими подачами используют резцы с дополнительной режущей кромкой. Резец устанавливают на станке так, чтобы режущая кромка была параллельна линии центров станка.
В промышленности применяют резцы с многогранными неперетачиваемыми твердосплавными пластинками. Когда одна из режущих кромок выходит из строя вследствие затупления, открепляют механический прижим пластинки и устанавливают в рабочее положение следующую кромку.
- Обработка заготовок на токарно-винторезных станках
Токарно-винторезный станок состоит из следующих узлов. Станина с призматическими направляющими служит для монтажа узлов станка и закреплена на тумбах. В передней тумбе смонтирован электродвигатель главного привода станка, в задней тумбе — бак для смазочно-охлаждающей жидкости и насосная станция.
В передней бабке смонтированы коробка скоростей станка и шпиндель. Механизмы и передачи коробки скоростей позволяют получать разные частоты вращения шпинделя. На шпинделе закрепляют зажимные приспособления для передачи крутящего момента обрабатываемой заготовке. На лицевой стороне передней бабки установлена панель управления механизмами коробки скоростей.
Коробку подач крепят к лицевой стороне станины. В коробке смонтированы механизмы и передачи, позволяющие получать разные скорости движения суппортов. С левой торцовой стороны станины установлена коробка сменных зубчатых колес, необходимых для наладки станка на нарезание резьбы
Продольный суппорт перемещается по направляющим станины и обеспечивает продольную подачу резцу. По направляющим продольного суппорта перпендикулярно к оси вращения заготовки перемещается поперечная каретка, на которой смонтирован верхний суппорт. Поперечная каретка обеспечивает поперечную подачу резцу. Верхний поворотный суппорт можно устанавливать под любым углом к оси вращения заготовки, что необходимо при обработке конических поверхностей заготовок.
На верхнем суппорте смонтирован четырехпозиционный поворотный резцедержатель, в котором можно одновременно закреплять четыре резца. К продольному суппорту крепят фартук. В фартуке смонтированы механизмы и передачи, преобразующие вращательное движение ходового валика или ходового винта в поступательные движения суппортов. Задняя бабка установлена с правой стороны станины и перемещается по ее направляющим. В пиноли задней бабки устанавливают задний центр или инструмент для обработки отверстий (сверла, зенкеры, развертки).
Корпус задней бабки смещается относительно основания в поперечном направлении, что необходимо при обтачивании наружных конических поверхностей. Для предохранения работающего от травм, сходящей стружкой на станке устанавливают специальный защитный экран.
Обтачивание наружных цилиндрических поверхностей выполняют прямыми, отогнутыми или упорными проходными резцами с продольной подачей; гладкие валы, — при установке заготовки на центрах. Вначале обтачивают один конец заготовки, а затем ее поворачивают на 180° и обтачивают остальную часть.
Ступенчатые валы обтачивают по схемам деления припуска на части или деления длины заготовки на части. В первом случае обрабатывают заготовки с меньшей глубиной резания, однако общий путь резца получается большим и резко возрастает То. Во втором случае припуск с каждой ступени срезается сразу за счет обработки заготовки с большой глубиной резания. При этом То уменьшается, но требуется большая мощность привода станка,
Нежесткие валы рекомендуется обрабатывать упорными, проходными резцами, с главным углом = 90°. При обработке заготовок валов такими резцами радиальная составляющая силы резания Ру = 0, что снижает деформацию заготовок.
Подрезание торцов заготовки выполняют перед обтачиванием наружных поверхностей. Торцы подрезают подрезными резцами с поперечной подачей к центру, или от центра заготовки. При подрезании от центра к периферии поверхность торца получается менее шероховатой.
Обтачивание округлений между ступенями валов выполняют проходными резцами с закруглением между режущими кромками по соответствующему радиусу с продольной подачей или специальными резцами с поперечной подачей.
Протачивание канавок выполняют с поперечной подачей прорезными резцами, у которых длина главной режущей кромки равна ширине протачиваемой канавки. Широкие канавки протачивают теми же резцами сначала с поперечной, а затем с продольной подачей.
Сверление, зенкерование и развертывание отверстий выполняют соответствующими инструментами, закрепляемыми в пиноли задней бабки.
Растачивание внутренних цилиндрических поверхностей выполняют расточными резцами, закрепленными в резцедержателе станка, с продольной подачей. Гладкие сквозные отверстия растачивают проходными резцами; ступенчатые и глухие — упорными расточными резцами.
Отрезку обработанных деталей выполняют отрезными резцами с поперечной подачей. При отрезке детали резцом с прямой главной режущей кромкой разрушается образующаяся шейка и приходится дополнительно подрезать торец готовой детали. При отрезке детали резцом с наклонной режущей кромкой торец получается чистым.
Обтачивание наружных конических поверхностей заготовок осуществляют на токарно-винторезных станках одним из следующих способов.
1. Широкими токарными резцами. Обтачивают короткие конические поверхности с длиной образующей до 30 мм токарными проходными резцами, у которых главный угол в плане равен половине угла при вершине обтачиваемой конической поверхности. Обтачивают с поперечной или продольной подачей. Способ используют при снятии фасок с обработанных цилиндрических поверхностей.
2. Поворотом каретки верхнего суппорта. При обработке конических поверхностей каретку верхнего суппорта повертывают на угол, равный половине угла при вершине обрабатываемого конуса. Обрабатывают с ручной подачей верхнего суппорта под углом к линии центров станка (Sн). Обтачивают конические поверхности, длина образующей которых не превышает величины хода каретки верхнего суппорта. Угол конуса обтачиваемой поверхности любой.
3. Смещением корпуса задней бабки в поперечном направления. При обтачивании конических поверхностей этим способом корпус задней бабки смещают относительно ее основания в направлении, перпендикулярном к линии центров станка. Обрабатываемую заготовку устанавливают на шариковые центры. При этом ось вращения заготовки располагается под углом к линии центров станка, а образующая конической поверхности — параллельно линии центров станка. Обтачивают с продольной подачей резца длинные конические поверхности с небольшим углом конуса при вершине (2а < 8°).
4. С помощью конусной линейки. Корпус конусной линейки закрепляют на кронштейнах на станине станка. На корпусе имеется призматическая направляющая линейка, которую по шкале устанавливают под углом к линии центров станка. По направляющей перемещается ползун, связанный через рычаг с кареткой поперечного суппорта. Гайку ходового винта поперечной подачи отсоединяют от каретки суппорта. Коническую поверхность обтачивают с продольной подачей. Сложение двух движений обеспечивает перемещение резца под углом к линии центров станка. Обтачивают длинные конические поверхности с углом при вершине конуса до 30—40°.
1. Процесс сверления
Сверление — весьма распространенный способ получения в обрабатываемой заготовке сквозных или глухих отверстий, а также рассверливания уже имеющихся отверстий. Режущим инструментом при сверлении являются сверла.
Скоростью резания при сверлении называют окружную скорость точки режущей кромки, наиболее удаленной от оси сверла.
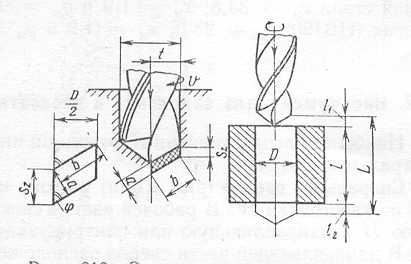
Рис. 1.1 Элементы режима резания при сверлении
Выбор скорости резания при сверлении зависит от механических свойств обрабатываемого материала и материала режущей части сверла, диаметра сверла, величины подачи, стойкости инструмента, охлаждения, глубины сверления и других факторов.. Например, при работе сверла, оснащенного пластинкой твердого сплава ВК8, скорость резания стали составляет 45 — 80, а чугуна — 50 — 95 м/мин.
2. Инструмент для сверления и обработки отверстия
Наиболее распространенный режущий инструмент при сверлении-
спиральные сверла.
Спиральное сверло (рис. 2.1а) состоит из рабочей части I, шейки III и, хвостовика IV. В рабочей части в свою очередь различают режущую II и направляющую или центрирующую части.
В направляющей части сверла расположены две канавки 1 и 6 для отвода стружки из просверливаемого отверстия, а также две ленточки 8 и 8 для обеспечения направления сверла при резании.
Режущая часть сверла имеет две главные режущие кромки 2 и 7, поперечную кромку 4 и две задние поверхности 5 и 9.
Угол при вершине сверла 2φ, образуемый режущими кромками, выбирают в зависимости от твердости и хрупкости обрабатываемого материала.
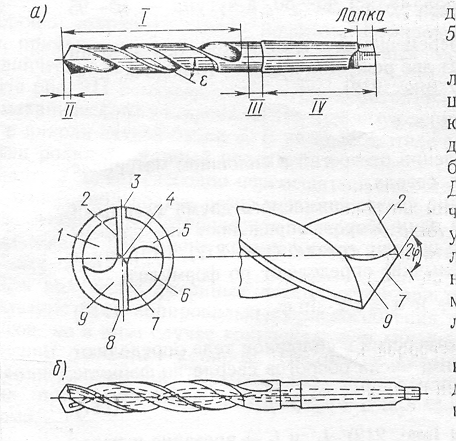
Рис. 2.1. спиральные сверла: а – обычное; б – с отверстиями для подвода охлаждающей жидкости.
Для обработки стали и чугуна средней твердости угол при вершине составляет 116 — 120º, для красной меди — 125º, для алюминия, мягкой бронзы, латуни — 130 — 140º.
Угол наклона винтовой канавки ε в зависимости от диаметра сверла принимают 18 — 30º.
Для дальнейшей обработки отверстий, полученных сверлением, литьем или штамповкой, применяют зенкерование и развертывание. Режущим инструментом при зенкеровании и развертывании служат зенкеры и развертки.
Зенкер (рис. 2.2) состоит из рабочей части I, шейки IV, конического хвостовика V и лапки VI.
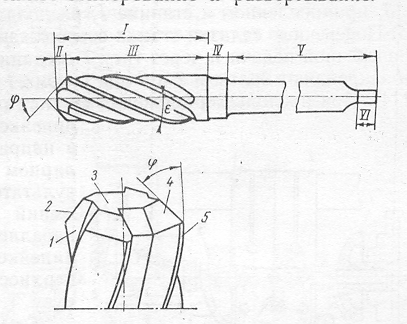
Рис. 2.2 Зенкер
В рабочей части различают режущую II (заборную) и калибрующую III (направляющую) части.
Режущая часть зенкера состоит из срезанной торцовой части— сердцевины 3 и трех или четырех режущих кромок 2. Каждая из них, как и в других инструментах, образована пересечением передней 1 и задней 4 поверхностями. Главный угол в φ выбирают в пределах 45 — 60˚.
Калибрующий участок зенкера имеет три или четыре винтовые канавки и ленточки 5. Последние являются направляющими элементами зенкера; они обеспечивают большую точность обработки, препятствуя возможному отклонению инструмента в сторону. Угол наклона винтовых канавок ε= 10 — 30˚.
По виду обрабатываемых отверстий зенкеры разделяют на цилиндрические, конические и комбинированные (многоступенчатые). Кроме цельных диаметром до 80 мм, применяют насадные зенкеры (цельные и со вставными ножами диаметром до 100 мм) и зенкеры с напаянными пластинками из твердых сплавов.
Развертка (рис. 2.3,а) имеет рабочую часть I, шейку II и хвостовик III. В рабочую часть входят направляющий конус или заборная часть IV, режущая часть V, калибрующий участок VI и обратный конус VII.
Основную работу выполняет режущая часть, каждый зуб которой имеет главную режущую кромку 1, переднюю 2 и заднюю 3 поверхности (рис. 2.3,б). По передней поверхности сходит срезаемая стружка. Зуб развертки имеет передний угол γ и задний α (рис. 2.3,в).
Режущая часть для обработки сквозных отверстий имеет угол, равный для ручной развертки 0,5 — 1,5˚, для машинной развертки при обработке стали 12 — 15˚ и чугуна — 3 — 5˚. Главный угол в плане φ влияет на осевое усилие: чем он больше, тем больше потребное осевое усилие.
Развертки бывают цилиндрические и конические, ручные и машинные. У машинных разверток рабочая часть значительно короче, чем у ручных. По конструктивному выполнению развертки делят на хвостовые и насадные, цельные и со вставными ножами, оснащенные пластинками из твердых сплавов.
Спиральные сверла, зенкеры и развертки при небольших скоростях обработки изготовляют из углеродистых инструментальных сталей У10А и У12А, хромистых и вольфрамовых инструментальных сталей 9ХС и B1, а при больших скоростях обработки — из быстрорежущей стали различных марок. Изготовляют также сверла, зенкеры и развертки, оснащенные пластинками из твердых сплавов марок ВК и ТК.
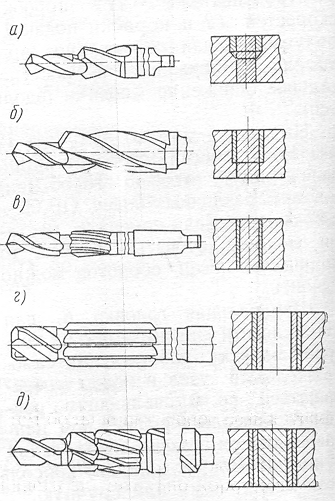
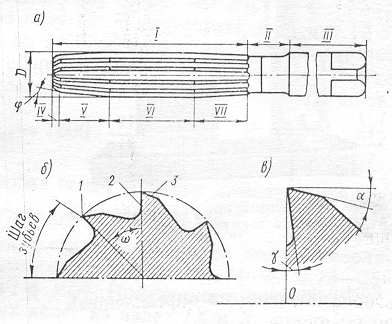
Рис. 2.3. Развертка Рис. 2.4. Комбинированные режущие
инструменты: а — сверло-сверло; б —
сверло-зенкер; в- сверло-развертка; г
зенкер-развертка; д- сверло-
зенкер-развертка.
Монолитные спиральные твердосплавные сверла (из сплавов ВК15 М, ВК10М и др.) диаметром 1,5 — 5,5 мм предназначены для сверления
труднообрабатываемых материалов. Стойкость таких сверл почти в 20 раз больше стойкости сверл из быстрорежущий стали.
Комбинированные режущие инструменты (рис. 2.4) применяют для повышения производительности при обработке отверстий в массовом производстве. Замена нескольких инструментов одним комбинированным значительно сокращает вспомогательное время (на смену инструмента), улучшает качество обработки, устраняет опасность несовпадения осей инструмента и отверстия и т. д.
3. Сверлильные станки
К сверлильным станкам относят собственно сверлильные и расточные станки.
Станки сверлильной группы разделяют на вертикально-сверлильные, радиально-сверлильные, одно- и многошпиндельные полуавтоматы, координатно-расточные, алмазно-расточные, горизонтально-сверлильные для глубокого сверления, расточные и специальные.
Указанные типы станков имеют несколько моделей. На рис. 3.1.,а показан общий вид одношпиндеольного вертикально- сверлильного станка модели 2А150. На фундаментной плите I крепится станина 9. В верхней части станины расположен электродвигатель 6 мощностью 7 кВт, который сообщает сверлу 3, укрепленному в нижней части шпинделя 4, главное (вращательное) движение. Это движение передается шпинделю через коробку скоростей, которая расположена в консольной части станка, называемой шпиндельной головкой 5. Движение подачи (поступательное вдоль оси) сверло получает от коробки подач, укрепленной в подвижном кронштейне 7.
Вертикальное перемещение шпинделя и сверла может осуществляться механически по заданному режиму от коробки подач или вручную при помощи штурвала 8. В зависимости от формы и размеров заготовки ее укрепляют на
столе 2 в машинных тисках, кондукторах или иных приспособлениях. При помощи рукоятки 10 стол можно перемещать по вертикали.
В станке предусмотрена возможность сверления отверстий на заданную глубину с автоматическим отключением подачи. На этом станке можно сверлить отверстия диаметром до 50 мм и глубиной до 300 мм. Станки имеют широкий диапазон чисел оборотов, шпинделя и подач; поэтому их применяют не только для сверления, но также для зенкерования и нарезания внутренней резьбы.
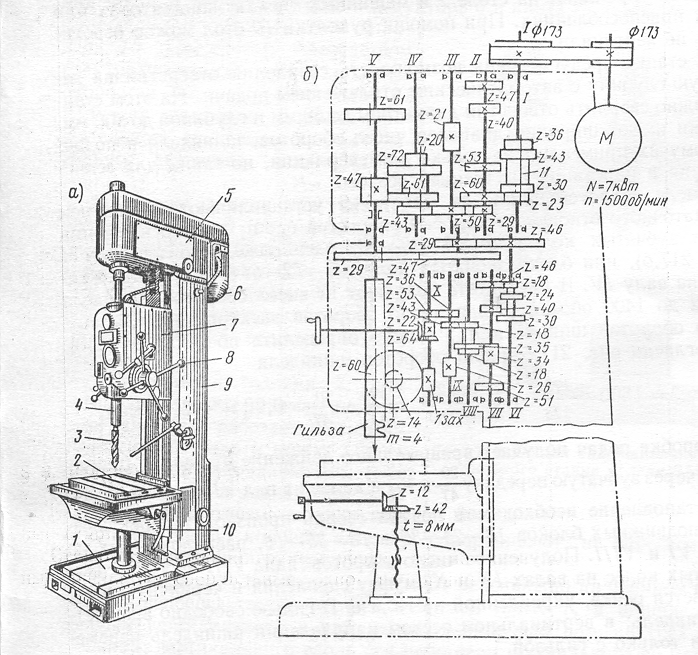
Рис. 3.1. Одношпиндельный вертикально – сверлильный станок модели 2А150 а – общий вид; б – кинематическая схема
На рис. 3.2 показан общий вид радиально-сверлильного станка, модели 2А53. Эти станки используют для сверления, рассверливания, зенкерования и развертывания отверстий, отдаленных от краев заготовки, а также для получения и обработки отверстий в крупных заготовках, установка которых на столе вертикально –сверлильного станка невозможна или неудобна.
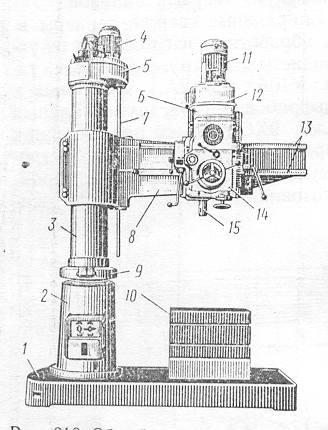
Рис. 3.2 Общий вид радиально – сверлильного станка модели 2А53.
На фундаментальной плите I крепится неподвижная колонна 2 с поворотной гильзой 3. Разрезной хомут 9, скрепляющий гильзу с колонной, стягивается специальным устройством. На гильзе закреплена консоль или рукав 8, перемещающийся по ней вверх или вниз при помощи двигателя 4, двухступенчатого редуктора 5 и винта 7. Консоль имеет шпиндельную головку 6 и шпиндель 15. Последний посредством электродвигателя 11, коробки скоростей 12 и коробки передач 14 получает заданное главное (вращательное) движение и поступательное движение подачи (вдоль оси)
На станке можно пол учить 12 различных чисел оборотов шпинделя в минуту (от 55 до 2240 об/мин) и восемь различных подач. Если поменять местами сменные зубчатые колеса, то количество чисел оборотов можно удвоить.
Шпиндельная головка 6 устойчивости фиксируемая на консоли зажимом, работает как самостоятельный узел и может перемещаться по направляющим рейкам 13 консоли в радиальном направлении при помощи специальной рукоятки. Вокруг колонны консоль поворачивают на определенный угол механически или вручную.
При сверлении заготовку укрепляют неподвижно на съемном столе 10 или непосредственно на фундаментной плите 1, а шпиндель со сверлом устанавливают в рабочее положение при помощи трех перемещений: вертикального вдоль оси шпинделя; радиального по направляющим консоли и вокруг колонны (на определенный угол).
Для получения отверстий сверлением, зенкерованием, расточкой или развертыванием в крупных литых корпусах применяют расточные станки, которые бывают горизонтально- и вертикально-расточные. На рис. 3.2 показан общий вид горизонтально-расточного станка модели 262Г. На жесткой литой станине 1 укреплена передняя стойка 2, по направляющим которой может вертикально перемещаться шпиндельная бабка 3 с горизонтально расположенным шпинделем 4. Шпиндель получает главное (вращательное) движение и осевую подачу, параллельную плоскости стола. На шпинделе закреплена борштанга с расточным резцом, второй конец которой поддерживается специальным люнетом 6 задней стойки 7. Обрабатываемая деталь (литые крупные корпуса редукторов, станины, массивные блоки двигателей и т. д.) укреплена на столе 5, имущем продольную и поперечную подачи. Движения подач на станке осуществляются вручную и механически.
Во время расточки отверстий вершина резца описывает круговую " траекторию и вместе со шпинделем получает продольную подачу. Иногда продольную подачу сообщают обрабатываемой заготовке вместе со столом; в этом случае шпиндель и резец получают только вращательное движение.
Растачивание отверстий может производиться резцами, устанавливаемыми в борштанге, и сверлами, зенкерами и развертками, закрепляемыми в шпинделе станка. Основным размером, характеризующим горизонтально-расточные станки, является диаметр шпинделя.
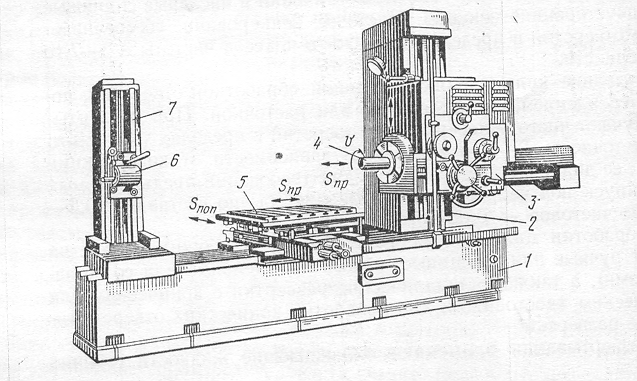
Рис. 3.3. Общий вид горизонтально- расточного станка модели 262Г
4. Основные виды сверлильных работ
Сверление. Различают обычное и глубокое сверление. При обычном сверлении и для получения сквозных или глухих отверстий применяют спиральные сверла с коническими или цилиндрическими хвостовиками. Первые закрепляют в шпинделе станка непосредственно или при помощи переходных конусных втулок (рис. 4.1,а), вторые — при помощи двух- и трехкулачковых патронов (рис. 4.1,6).
В зависимости от величины партии обрабатываемых деталей сверление производят по разметке или в кондукторах.
Сверление по разметке применяют при небольших партиях обрабатываемых деталей и при выполнении ремонтных работ, когда затраты на изготовление кондуктора не окупаются. В этом случае точность обработки получается меньшей (не выше 5-го класса). При сверлении по разметке в зависимости от формы и размеров деталей их устанавливают и зажимают либо непосредственно на столе станка, либо в приспособлениях. Чаще всего применяют машинные тиски (рис. 4.1, в), призмы (рис. 4.1,г) и угольники (рис. 4.1, д, е), укрепляемые на столе станка.
При обработке больших партий деталей производит сверление и кондукторах — специальных приспособлениях, изготовляемых по форме обрабатываемой детали. Кондукторы позволяют вести сверление без предварительной разметки детали и получать более высокую точность обработки (до 4-ro класса).
При пользовании накладным кондуктором (рис. 220,ж) обрабатываемую деталь 1 закрепляют в машинных тисках или непосредственно на столе станка; кондуктор 3 накладывают и укрепляют боковыми винтами 2 на той части поверхности детали, где нужно просверлить отверстие.
Перед сверлением производится наладка станка (установка и проверка инструмента, укрепление обрабатываемых деталей и т. д.) и его настройка (выбор числа оборотов шпинделя и подачи).
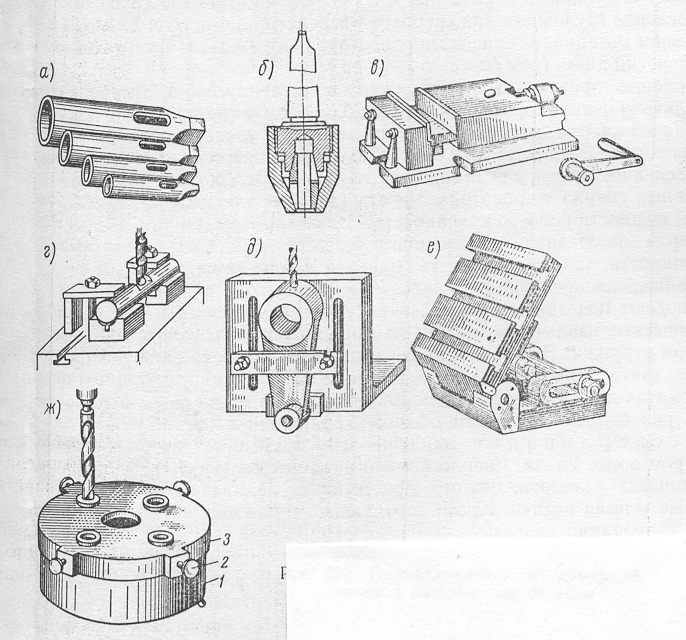
Рис. 4.1. Принадлежности и приспособления к сверлильным станкам
При сверлении пользуются механической и реже ручной подачей сверла. При подходе сверла к выходу из сквозного отверстия во избежание его поломки механическую подачу выключают и досверливание производят при ручной замедленной подаче.
На многих станках имеются устройства, для автоматического выключения подачи при достижении сверлом заданной глубины. Этими устройствами пользуются также при сверлении глухих отверстий на определенную глубину; часто при сверлении глухих отверстий применяют упорные приспособления или упорную втулку, закрепляемую на сверле.
При глубоком сверлении, когда длина отверстия превышает его диаметр в пять раз и более, обычно применяют специальные сверла (ружейные для сверления отверстий диаметром до 25 мм в сплошном материале, пушечные одностороннего резания для сверления отверстий диаметром более 25 мм и др.).
Сверление производят на горизонтально-сверлильных (глубоко- сверлильных) станках с вращением обрабатываемой детали и продольной подачей сверла, что уменьшает вероятность увода последнего от оси отверстия. Деталь закрепляют в кулачках патрона и в люнете.
В последнее время для сверления глубоких отверстий применяют спиральные сверла с прокатанными отверстиями для подвода охлаждающей жидкости непосредственно к режущим кромкам (см. рис. 2.1,б). Эти сверла, по сравнению со сверлами без отверстий, имеют повышенную стойкость, так как жидкость, попадая в зону резания, обеспечивает охлаждение режущих кромок. Кроме того, охлаждающую жидкость подают под давлением, облегчая удаление стружки и устраняя периодическое извлечение сверла из обрабатываемого отверстия для удаления стружки. Это увеличивает производительность станка. Применение таких сверл особенно эффективно при обработке отверстий на автоматах и автоматических линиях. Стойкость таких сверл в три- девять раз больше стойкости обычных спиральных сверл.
Рассверливание. Эту обработку применяют для отверстий диаметром более 25 мм. Сверла больших диаметров имеют перемычки значительных размеров, поэтому при их применении необходимы увеличенные усилия подачи. Кроме того, такие сверла часто отклоняются от оси сверления.
Сначала в заготовке просверливают отверстие меньшего диаметра (0,3 — 0,6 диаметра требуемого отверстия), затем его рассверливают сверлом заданного диаметра. Рассверливание уменьшает усилие подачи и увод сверла, поэтому процесс ведут при подаче в 1,5 — 2 раза больше, чем при сверлении одним сверлом.
Важным видом сверлильных работ является сверление отверстий под резьбу. Эти отверстия сверлятся спиральным сверлом в сплошной заготовке или рассверливают в отливках и поковках.
Зенкерование и развертывание. Отверстия, полученные в заготовках сверлением, литьем или штамповкой, с целью получения большей точности размеров и чистоты поверхности подвергают зенкерованию и развертыванию.
Зенкероваиие применяют для окончательной обработки отверстий или для предварительной обработки под развертывание. Припуск под зенкерование зависит от диаметра отверстия, составляя от 0,6 — 1,0 мм для диаметров 10 — 18 мм и до 3 — 5 мм для диаметров 50 — 80 мм. При зенкеровании под развертку диаметр зенкера должен быть меньше окончательного размера отверстия на величину припуска, снимаемого разверткой.
Для зенкерования обычно применяют зенкеры с коническим хвостовиком, насадные цельные зенкеры и зенкеры со вставными ножами из твердых сплавов.
Для обработки центровых отверстий и торцовых поверхностей применяют соответственно центровочные зенковки
Развертывание является окончательной обработкой отверстий, полученных сверлением, зенкерованием или расточкой
Для обработки цилиндрических, сквозных и глухих отверстий применяют ручные или машинные развертки (цельные или со вставными ножами), а также цилиндрические развертки с коническим или цилиндрическим хвостовиком; для обработки конических отверстий— конические развертки.
При развертывании применяют охлаждающие жидкости (обычно эмульсии).