Курс лекций по дисциплине «металлорежущие станки» Москва 200 г
Вид материала | Курс лекций |
- Методические указания к лабораторной работе по курсу "Металорежущие станки" для студентов, 275.32kb.
- Гост 25379-82. Станки металлорежущие. Диаметры отверстий под инструмент с цилиндрическим, 9.14kb.
- Курсового проекта по дисциплине «металлорежущие станки» для заочного отделения, 52.19kb.
- Лекции Лабораторные, 34.8kb.
- Специалистов и магистров специальности "Металлорежущие станки и системы" со специализацией, 35.76kb.
- Курс лекций по дисциплине история экономических учений москва 2008, 5434.7kb.
- Курс лекций по дисциплине история экономики москва 2008, 991.98kb.
- Металлорежущие станки, 90.13kb.
- Текст лекций для самостоятельной работы по курсу "Теория резания". Тема, 797.43kb.
- «Технология, оборудование и автоматизация машиностроительных производств», 16.71kb.
ФЕДЕРАЛЬНОЕ АГЕНСТВО ПО ОБРАЗОВАНИЮ
Государственное образовательное учреждение высшего профессионального образования
Московский государственный индустриальный университет
(ГОУ МГИУ)
Курс лекций по дисциплине
«металлорежущие станки»
Москва 200.. г.
4. ЭЛЕКТРОФИЗИЧЕСКИЕ МЕТАЛЛООБРАБАТЫВАЮЩИЕ
СТАНКИ
Концентрированные потоки энергии различной физической природы - электронные и ионные пучки, световое (лазерное) излучение, плазменные струи и дуги, электродуговые, микродуговые и электроимпульсные воздействия - являются универсальным технологическим инструментом для обработки труднообрабатываемых деталей машиностроения.
Воздействием таких потоков можно выполнять различные технологические операции без механического силового действия инструмента на заготовку и без непосредственного контакта между инструментом и заготовкой исключительно за счет использования специфических для каждого вида подобных воздействий физических и химических явлений.
Параметры и сама возможность выполнения таких операций процесса достигается физико-химическими свойствами обрабатываемых деталей такими как: тепло- и электропроводимость; теплота и скрытое тепловое плавление и испарение; технический состав и структура обрабатываемого материала и др.
4.1. Электроэрозионная обработка
Электрическая эрозия, как явление разрушения контактов под действием электрических разрядов, известна давно.
Принцип реализации электроэрозионной обработки (ЭЭО) состоит в следующем. Если электроды (инструмент и заготовку) поместить в диэлектрик (см. рис.69), который охлаждает расплавленные частицы металла электродов, образующихся в результате электрической эрозии, и не позволяет им оседать на противоположный электрод, то, при соответствующей полярности и параметров электрического разряда, будет иметь место снятие металла с заготовки. В качестве диэлектрической среды, обеспечивающей нужную скорость такого охлаждения, обычно используют различные жидкости: керосин, масло, диэлектрическую воду и др. Иногда используют и воздушную среду.
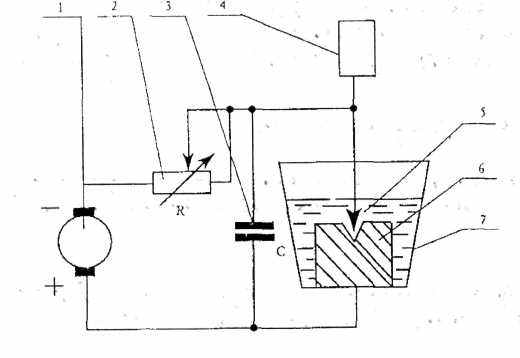
Рис. 69. Принципиальная схема электроискровой обработки
- - источник постоянного напряжения;
- - регулятор тока;
- - конденсатор;
- - механизм подачи инструмента;
- - электрод-инструмент;
- - заготовка;
- - ванна с рабочей жидкостью.
Различают электроискровой режим и электроимпульсный режим ЭЭО.
Съем металла осуществляется, главным образом, с анода за счет воздействия на него потока электронов. Поэтому в электродном режиме, а также, а электроимпульсном режиме с малой длительностью импульсов, обрабатываемая заготовка является анодом, а электрод-инструмент - катодом. Такое подключение электродов называется прямой полярностью. Воздействие потока ионов, хотя при этом режиме и незначительное, ведет к некоторому съему металла с катода. Это является вредным явлением и представляет собой износ инструмента. При малой длительности импульсов износ инструмента будет незначительным, т.е. точность обработки, обусловленная этим износом, будет более высокой, но производительность обработки будет невелика.
Увеличение длительности импульсов приводит к увеличению интенсивности воздействия в единицу времени, т.е. к росту производительности.
Основными технологическими показателями для ЭЭО, как и для традиционных технологических процессов, являются производительность, точность и качество.
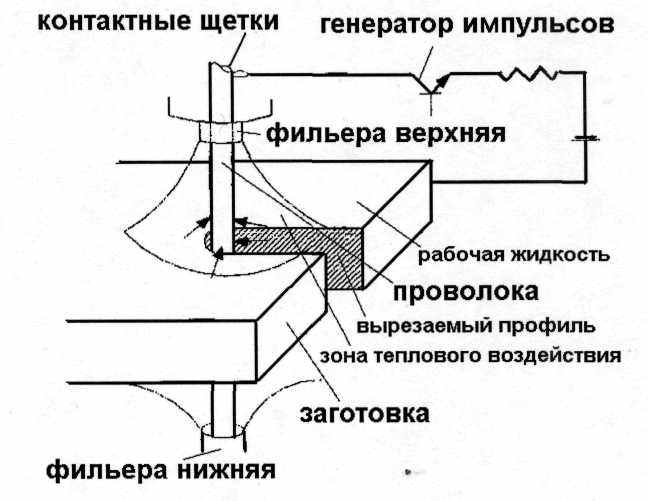
Рис. 70. Механизм электролитической вырезки профиля детали проволокой.
Сущность проволочной резки. Как уже отмечалось выше, принцип действия ЭЭСВ основан на том, что под действием импульсного электрического разряда, создаваемого между ЭИ и электродом-заготовкой, происходит направленное разрушение металла заготовки, что используется для обработки токопроводящего материала. Обработка производится в среде рабочей жидкости, в качестве которой могут быть использованы керосин и вода с антикоррозийными присадками. В качестве ЭИ используется проволока, перематывающаяся с небольшой скоростью для устранения ее износа в зоне обработки. Механизм ЭЭО с использованием ЭИ для вырезки заданного профиля детали показан на рис. 70.
Импульсный технологический ток вырабатывается специальным генератором. Для осуществления обработки детали заданного контура электрод-проволока совершает в горизонтальной плоскости взаимные продольные и поперечные перемещения, управление которыми осуществляется от устройства ЧПУ.
4.2. Электроэрозионные станки вырезные
Структура ЭЭСВ. Современные станки ЭЭСВ представляют собой сложные технологические системы, состоящие из рабочего пространства, исполнительных органов линейного и вращательного перемещения, компьютерных ЧПУ и генераторов импульсов. Примерная перечисленных сочетаний движений и управления ЭЭСП приведена на
рис. 71.
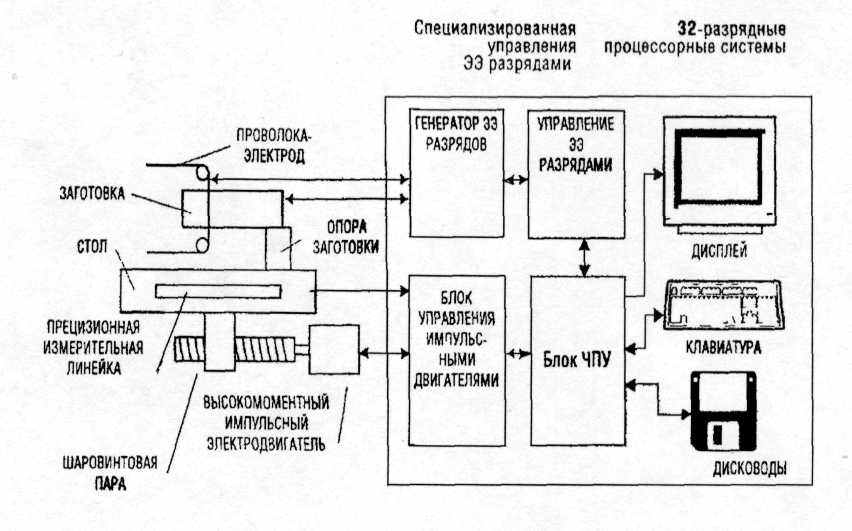
Рис. 71. Функциональная схема работы проволочного вырезного
электроэрозионного станка
Как это следует из рисунка, заготовка устанавливается на специальных опорах на верхней части стола, который, в свою очередь, имеет возможность линейно перемещаться от привода подачи. Управление перемещением стола происходит от блока компьютерного ЧПУ и далее через блок управления импульсами команда переносится на двигатели привода подачи. Питание проволоки-электрода происходит от генератора, управление которого имеет связь с системой ЧПУ.
Команда на работу станков ЭЭСВ задается от клавиатуры или дисковода ЧПУ, а весь процесс просматривается на дисплее компьютера.
Характеристики искровых разрядов в значительной степени зависят от величины искрового (межэлектродного) зазора.
Оптимальный межэлектродный зазор — это оптимальные режимы обработки, соответственно максимальная производительность.
Типовая кинематическая схема ЭЭСВ. Типовая кинематика ЭЭСВ отображает следующие формообразующие и вспомогательные движения (рис. 72):
- подъем и опускание ванны с рабочей жидкостью;
- перемещение скобы в продольном и поперечном направлении, на которой расположены механизмы натяжения проволоки;
- управление положением проволоки при обработке деталей с наклонной образующей;
- перемотка проволоки и раскладка ее на приемной катушке.
Подъем и опускание ванны осуществляется винтом 3, движение , которому передается от электродвигателя М2 через червячную пару 1,2 и ходовую гайку 4. Скорость перемещения ванны 340 мм/мин.
Перемещение скобы в продольном и поперечном направлении производится в движение шаговыми электродвигателями МЗ и М4 через редуктор. Передаточное отношение редуктора выбрано таким образом, чтобы линейное перемещение скобы на один импульс от устройства УЧПУ составлял 0,01 мм.
Ручное перемещение скобы осуществляется следующим образом:
- в продольном направлении непосредственно от ходового винта 5;
- в поперечном направлении через винтовую зубчатую передачу 7, 8.
Перемотка проволоки производится непосредственно электродвигателем Мб через ведущий ролик диаметром 15 мм. Скорость перемотки регулируется в пределах 8...20 мм/с за счет изменения частоты вращения электродвигателя. Вращение на катушку, принимающую отработанную проволоку, передается через ременную передачу. Движение проволоки в рабочей зоне происходит сверху вниз. Раскладка отработанной проволоки на приемной катушке производится за счет осевого возвратно-поступательного движения катушки, осуществляемого качающимся рычагом и торцевым кулачком. Вращение кулачку сообщается от электродвигателя через дополнительный редуктор. Шаг раскладки проволоки около 1 мм.
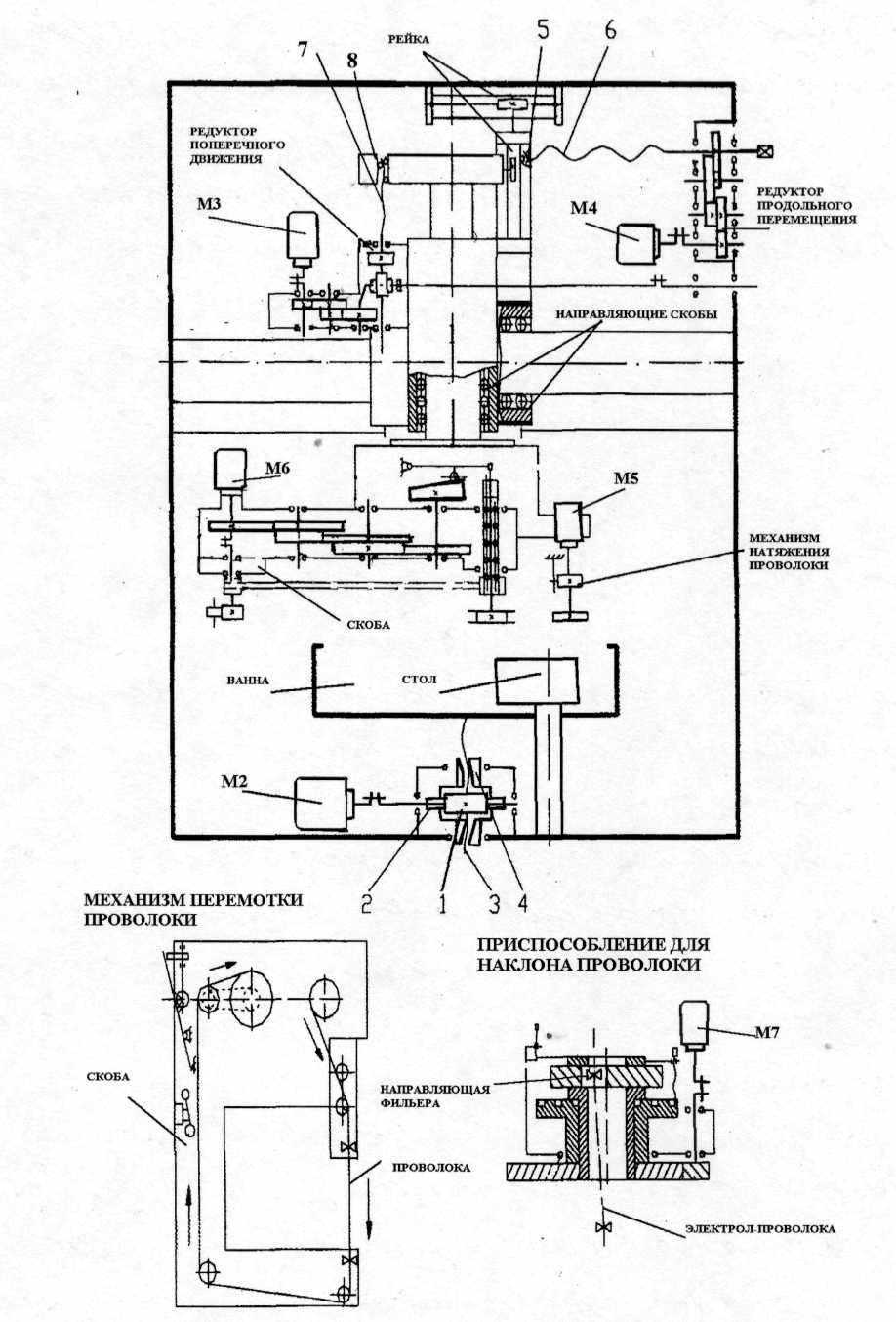
Рис. 72. Кинематическая схема ЭЭСВ.
Натяжение проволоки осуществляется двигателем М5, работающим в заторможенном режиме. Катушка устанавливается непосредственно на вал, связанный с двигателем натяжения проволоки.
Кинематическая схема приспособления для управления наклоном проволоки обеспечивается смещением верхней направляющей для получения требуемого угла наклона проволоки, поворотом направляющей для обеспечения постоянного угла в сечении нормальном к обрабатываемому контуру. Оба движения осуществляются от одного приводного двигателя М7 через пару зубчатых колес 28, 29.
4.3. Электроэрозионные станки прошивные
Сущность ЭЭ прошивки. ЭЭСП предназначены для изготовления деталей объемной формы типа штампов, пресс-форм, матриц вырубных штампов, а также изготовления отверстий различной конфигурации в деталях основного производства, как из обычного конструкционного материала, так и -из материалов труднообрабатываемых твердых сплавов, нержавеющих сталей и тому подобное. Обработка изделий на станке выполняется профилированными формообразующими электродами из меди или графита в среде рабочей жидкости.
Кинематическая схема ЭЭСП показана на рис. 73. По компоновке станок имеет классический вариант, похожий на станки координатно-расточной группы. Станок имеет три координаты перемещения, из которых по координате Z осуществляется перемещение инструмента (вертикальное перемещение), а по координатам X, Y (крестовый стол) перемещается ванна, в которой расположена обрабатываемая деталь.
Для того, чтобы иметь представление о процессе работы ЭЭСП, рассмотрим пример обработки вставки пресс-формы показанной на рис. 74.
Деталь имеет формообразующую поверхность в виде глухой полости, описанную сложными криволинейными поверхностями. Площадь фигуры и глубина обработки небольшие, и поскольку конфигурация детали описана сложными криволинейными поверхностями, целесообразно слесарное изготовление электрода-инструмента (ЭИ).
По конструкции ЭИ представляет собой кубик из графитового материала с профилированными базовыми поверхностями, прикрепляемый винтами к стальному хвостовику с фланцем.
Размеры ЭИ уменьшены по эквидистанте относительно чертежных размеров вставки пресс-формы; для чернового электрода на 0,15 мм на сторону и для чистового электрода на 0,08 мм на сторону.
Профиль рабочей части ЭИ изготавливают с помощью трех или более шаблонов.
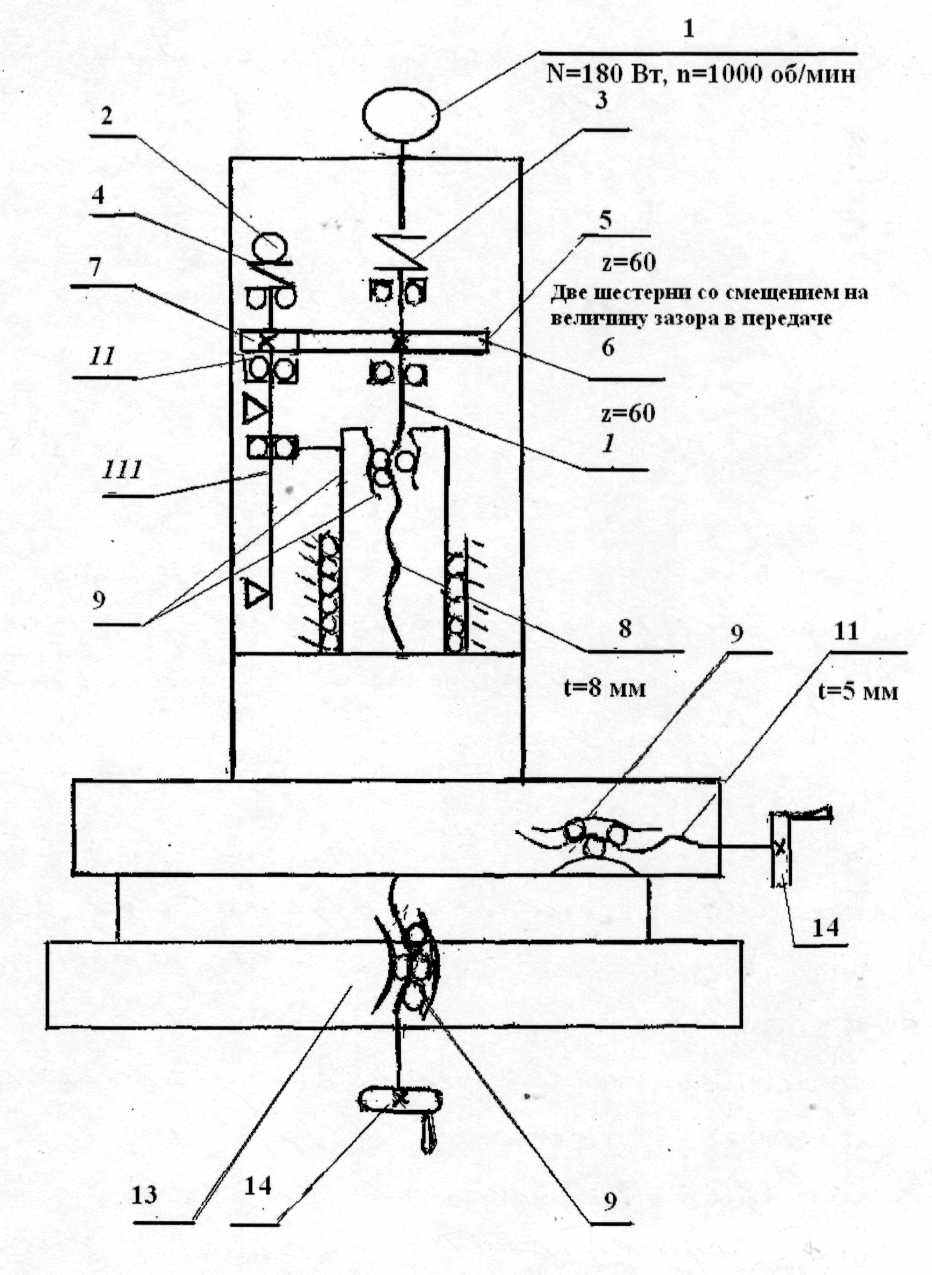
Рис. 73. Кинематическая схема ЭЭСП
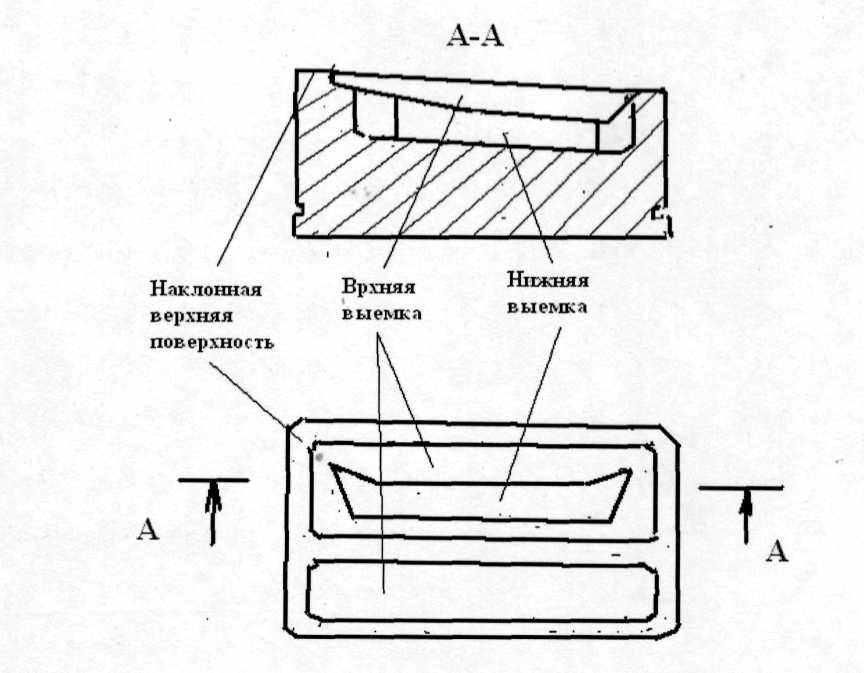
Рис. 74. Вставка пресс-формы.
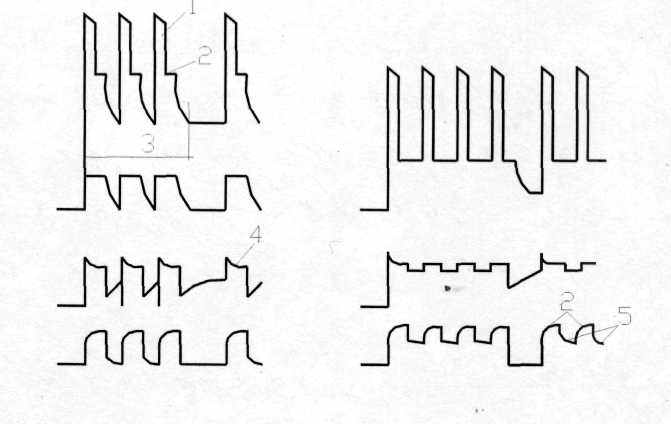
Рис. 75. Импульсы прямоугольной) и гребенчатой формы частотой в кГц:
1 - поджигающий импульс; 2 - силовой импульс; 3 - пакет импульсов; 4 - импульс напряжений на инструмент после пробоя; 5 - токовый мостик («защитные» импульсы).
Генератор импульсов. Как правило, генератор импульсов, используемый в ЭЭПС, оснащен устройством программно-адаптивного управления.
Получаемые при работе с генератором результаты обработки деталей зависят от параметров электрического режима (полярности электрода-инструмента и обрабатываемой детали, установленных характеристиками импульсов разрядов) и способа управления процессами.
Генератор позволяет производить обработку при прямой и обратной полярности электродов. При прямой полярности деталь подключается к положительному полюсу генератора, а ЭИ к отрицательному, при обратной полярности - наоборот.
К числу характеристик импульсов, устанавливаемых органами управления, относятся форма импульсов (прямоугольная и гребенчатая), частота и скважность силовых импульсов, количество импульсов, длительность паузы между пакетами, средний рабочий ток, среднее напряжение на эрозионный промежуток. Форма импульсов показана на рис. 75.
При обработке импульсами прямоугольной формы производительность процесса выше, чем при обработке импульсом гребенчатой формы. Однако износ инструмента в первом случае значительно больше.
Форму импульсов выбирают с учетом требований к процессу в зависимости от обрабатываемого материала и размеров обрабатываемой поверхности.
Электроды - инструменты. ЭИ состоят из рабочей части, поверхность которой участвует в формообразовании, и вспомогательных элементов, базовые поверхности которых служат для его установки и выверки. Формообразования осуществляется по методу копирования.
Рабочая часть ЭИ представляет собой негативную копию обрабатываемой поверхности с размерами, уменьшенными на величину межэлектродного зазора и припуска на последующую обработку и скорректированные в случае орбитального движения ЭИ на величину его амплитуды.
При проектировании технологического процесса, исходя из серийности, материала, формы, размеров и качества поверхности обрабатываемой детали, руководствуются рекомендациями завода -производителя станков, или по результатам тестовых испытаний подбирают параметры электрического режима с учетом материала ЭИ и метода его изготовления.
4.4. Разновидности обработки конструкционных материалов
электрофизическими методами.
Электроннолучевая обработка. При взаимодействии ускоренных электронов с твердым телом происходит множество процессов, в результате которых наблюдается эмиссия атомных частиц, а свойства самого твердого тела могут существенно изменяться. Многие из этих процессов используются на практике в электровакуумных приборах разнообразного типа и назначения. Другая обширная область применения электронных потоков - это использование их в качестве универсального технологического инструмента, позволяющего не только изменять заданным образом свойства обрабатываемых материалов, но и весьма тонко контролировать эти изменения. Схема подобной технологической установки приведена на рис. 76.
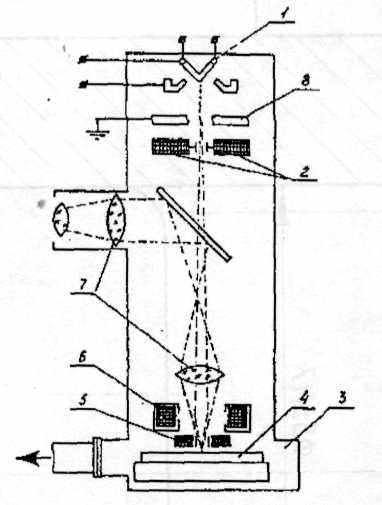
Рис. 76. Схема установки для электроннолучевой обработки.
1 - катод; 2 - система центрирования; 3 - вакуумная камера; 4 - заготовка; 5 – линза для фокусировки; 6 - магнитная линза; 7 - оптическая система для наблюдения; 8 - анод.
Рассмотрим, какие из физических явлений, сопровождающих электронную бомбардировку, могут быть использованы для этих целей.
Закономерности протекания процессов при такой бомбардировке определяются параметрами электронного луча: энергией электронов, направлением их движения и интенсивностью потока.
Тип системы, диапазон ускоряющих напряжений, допустимый разброс по энергии и углам вылета электродов, минимальный поперечный размер пучка и плотность электронного тока в каждом случае определяется конкретно.
Особенностью электроннолучевого нагрева является то, что можно достигнуть очень высокой концентрации тепловой энергии при сравнительно малой общей мощности пучка.
Все основные операции электроннолучевой обработки можно разбить натри группы:
- плавление (операции локального переплава, плавка в вакууме);
- испарение (испарение в вакууме, размерная электроннолучевая обработка);
- термообработка без изменения агрегатного состояния вещества.
Локальный переплав обрабатываемых поверхностей с помощью электронного луча дает возможность получать чрезвычайно высокие скорости кристаллизации металла в зоне плавления. Образуемая при этом структура обрабатываемой детали значительно отличается от структур, получаемых в обычных условиях. Расширяются границы растворимости для твердых растворов, измельчается микроструктура, значительно повышается пластичность и твердость. Быстрое остывание расплавленного металла приводит к последующей дополнительной закалке с мелкозернистой структурой с высокой твердостью.
Электроннолучевая плавка, или лучом в вакууме, применяется тогда, когда необходимо выплавить особо чистые металлы, в том числе, химически активные. Переплавляемый материал может быть использован в любом виде (шихта, пруток, лом, спеченные кубики и т.п.). Особую роль при этом играет вакуум как защитная среда, что объясняется следующим:
- в вакууме происходит интенсивное удаление растворенных в металле газов, что значительно улучшает их механические свойства;
- некоторые из примесей (нитриды, карбиды, оксиды) при нагревании в вакууме разлагаются, что приводит к рафинированию (очищению) переплавляемого металла;
- при плавке металла в вакууме все время происходит удаление газообразных продуктов из зоны реакции.
Электроннолучевая сварка. Эта операция является одним из самых распространенных технологических применений электронного луча. Поскольку при сварке происходит локальное плавление с последующей кристаллизацией, величина зоны расплавленного металла имеет важное значение. Кристаллизация металла в сварочной ванне в значительной мере определяет свойства металла шва, и изменение ширины зоны проплавления при сварке оказывает существенное влияние на свойства сварного соединения. Кроме того, от объема расплавленного при сварке металла зависит деформация и напряжения, возникающие в конструкциях после сварки.
Электроннолучевое испарение металлов. Испарение в вакууме материалов при нагреве их электронным лучом используют для получения тонких пленок. В отличие от других способов испарения, здесь осуществляется прямой нагрев поверхности испаряемого металла.
Электроннолучевое испарение применяют в микроэлектронике при нанесении различных покрытий на стальную ленту. Характерным примером электроннолучевого напыления является изготовление листового теплоотражающего стекла, когда на стеклянную заготовку напыляют тонкий слой хрома, меди, а затем боросиликатного стекла.
Размерная обработка электронным пучком. В результате такого рода обработки в заготовке получают глухие или сквозные отверстия заданных размеров и заданный контур с определенными допусками. Размерная обработка основана на том, что при достаточно большой поверхностной удельной мощности скорость испарения и давления пара возрастает настолько, что весь жидкий металл с потоком пара выбрасывается из зоны обработки.
Параметры электроннолучевой размерной обработки связаны с энергетическими характеристиками материала (температура плавления, упругость пара) и не зависят от его механических свойств (прочность, твердость, пластичность). Поэтому электронный луч нашел применение в первую очередь при обработке твердых материалов - алмазов, кварца, керамики, кристаллов кремния и германия.
Особой разновидностью размерной обработки является перфорация, т.е. получение мелких сквозных отверстий, заданных формы и размеров в необходимом количестве на единицу площади. Так изготовление металлических и керамических элементов фильтров, пористый материал для камер сгорания ракетных двигателей и для лопаток турбин. Другим примером являются фильеры до 30...50 мм, которые при толщине перфорируемой пластины 1 ..3 мм могут содержать до 500 отверстий.
Электроннолучевая термообработка. Этот процесс позволяет осуществлять локальный нагрев обрабатываемых участков поверхности с целью структурных превращений (в основном, закалки) или для отжига в вакууме с целью увеличения пластичности и очистки поверхностей от адсорбированных газов.
Например, упрочнение лезвия режущего инструмента из быстрорежущей стали, производится этим методом, в результате чего рабочий ресурс инструмента повышается в два раза по сравнением с традиционным методом упрочнения.
Термообработка листового материала или фольги производится сканированием луча на обезжиренную, очищенную и предварительно нагретой до 200...400°С поверхности.
Лазерная технология. Лазерное излучение представляет собой наиболее концентрированный источник энергии, превосходящий в этом плане возможности электроннолучевой обработки. Однако при одинаковой мощности излучения лазерная обработка обеспечивает меньшую глубину плавления, чем электроннолучевая, что является определенным недостатком.
На рис. 77 показана схема процесса лазерной обработки заготовки с учетом баланса энергетических затрат, выраженных следующими уравнениями:

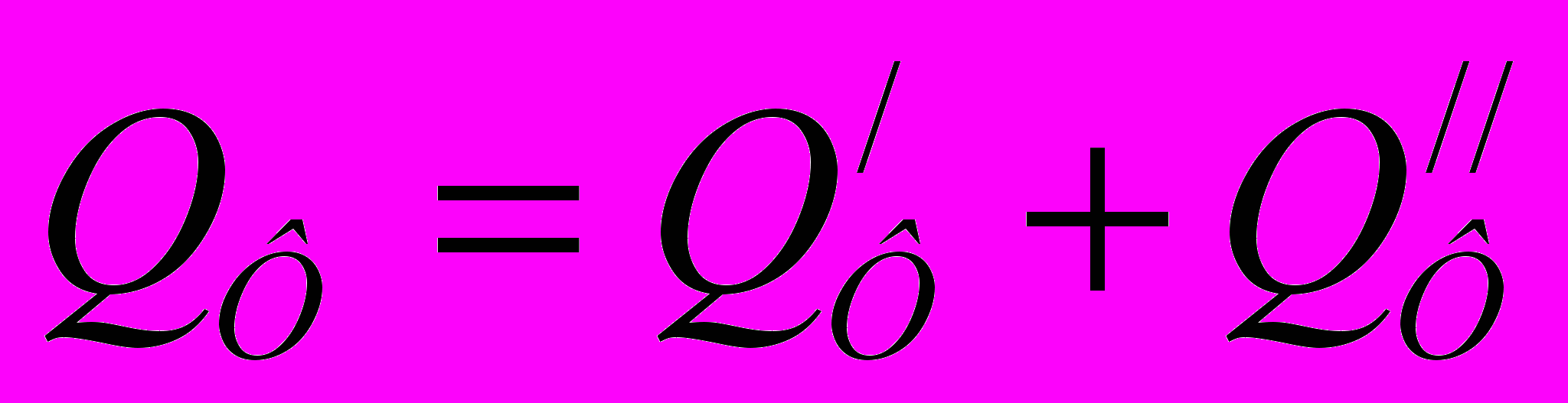

здесь:
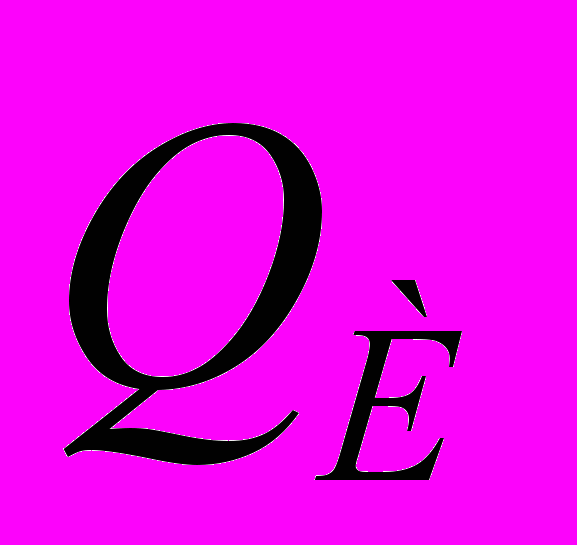
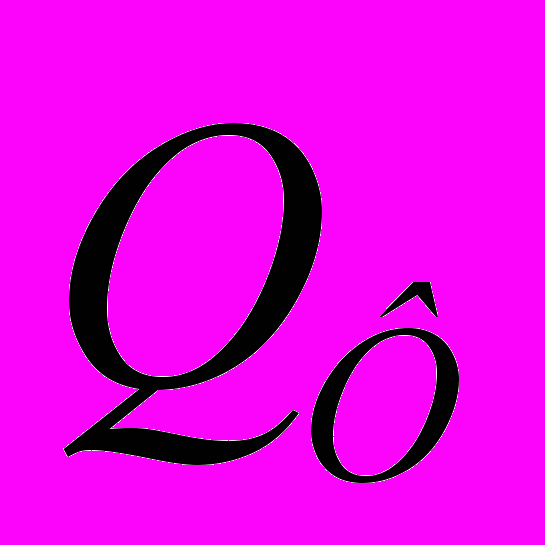
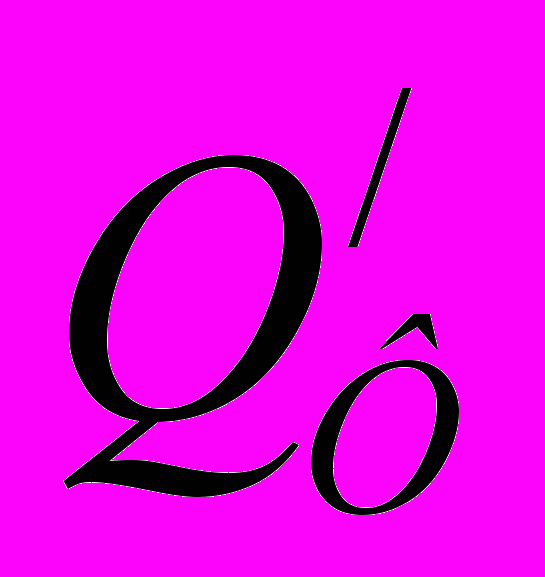
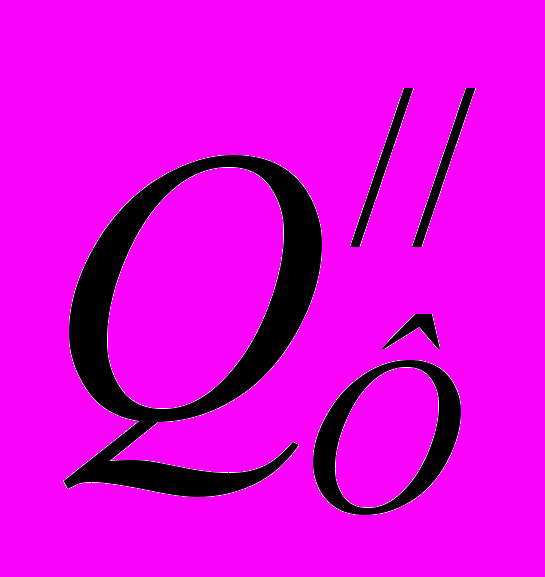
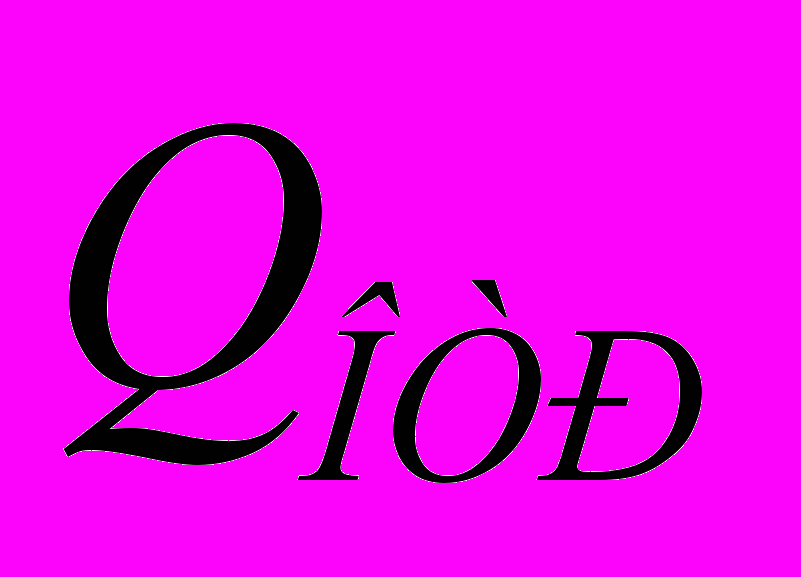
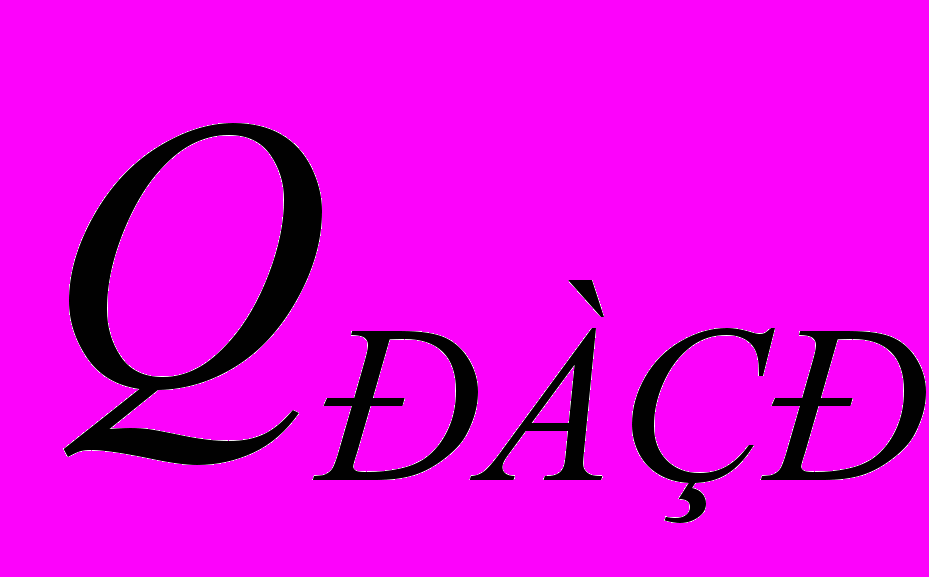
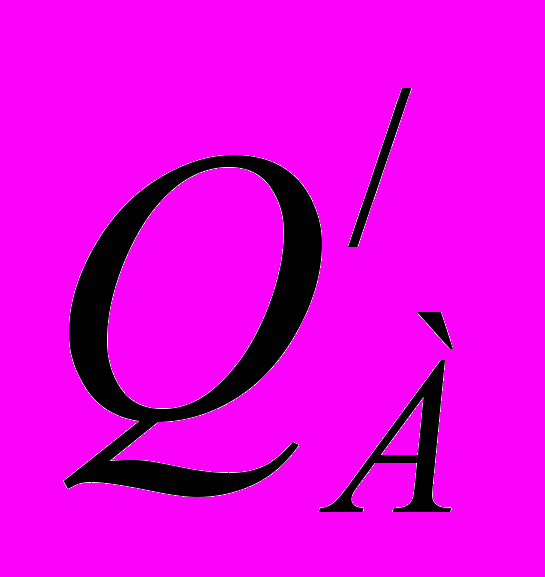
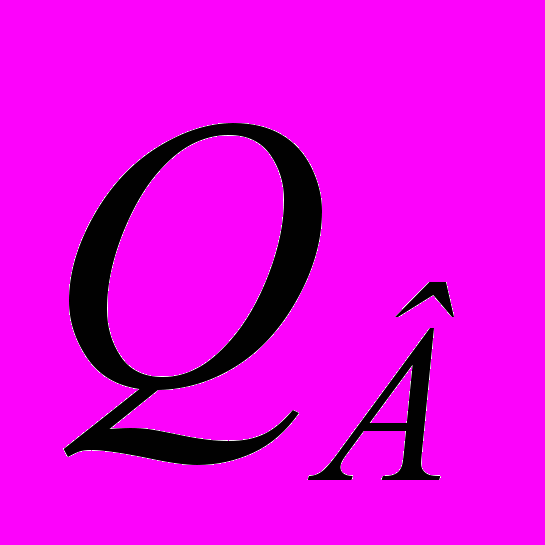

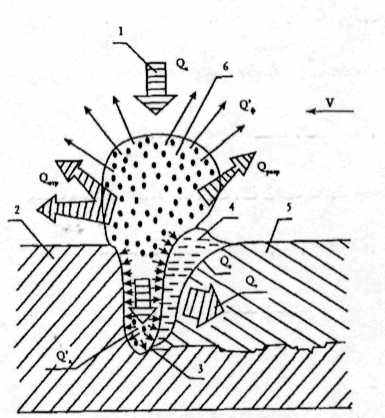
Рис. 77. Схема энергетических затрат в установившимся режиме проплав.анин
металла сфокусированным лазерным излучением:
1 -сфокусированный луч лазера; 2 - основной металл; 3 - кратер (парогазовая область); 4 - жидкий металл; 5 - переплавленный металл (сварной шов); 6 - плазменный факел.
Эффективность передачи лазерного излучения обрабатываемому материалу определяется значением эффективного коэффициента поглощения, который фактически характеризует эффективный КПД лазерной обработки. Приближенно значение этого коэффициента может быть получено из вышеприведенной системы уравнений:

Рассмотрим типовые операции лазерной технологии.
Нагрев. Поверхностная термообработка проводится для отдельных зон поверхности с последующим их охлаждением в любых средах (вода, воздух, эмульсия и т.п.). Это позволяет избирательно термически упрочнять поверхность изделия из склонных к закалке материалов (чугун, сталь и т.д.). Нагрев лазером для закалки выгодно использовать для таких деталей как шейки валов и осей, гильзы, вкладышей, зубьев шестерен и т.д. По сравнению с закалкой ТВЧ, здесь не требуется изготавливать для каждой детали свой индуктор, получаются более узкие зоны закалки, производительность возрастает на 70...90%.
Плавление и локальный переплав. Нагрев, расплав и быстрое охлаждение позволяет получать структуры, которые иначе получить нельзя. Быстрое охлаждение для массивных деталей достигается тепловым отводом в материал.
Для изделий из чугуна и высокоуглеродистой стали целесообразен не сплошной поверхностный переплав, а создание зоны проплавления в виде отдельных сеток, линий, спиралей и т.д. В этом случае удается сочетать прочность и пластичность основного металла с повышенной температурой и износостойкостью переплавленных зон. Причем вкрапление этих зон в основной материал увеличивает их прочность и снижает склонность к трещинообразованию. Это находит применение при изготовлении направляющих и других опор трения.
Лазерная сварка, как процесс, связанный с локальным плавлением, конкурирует как с традиционными процессами, так и с электроннолучевой сваркой. Наиболее часто лазерная сварка применяется для малогабаритных деталей и конструкций из тонколистовых материалов. Применяются точечная сварка и шовная сварка герметичным швом. Сравнительно небольшой разогрев позволяет осуществлять герметизацию корпусов, заполненных веществами, разогревать которые недопустимо. Например, так герметизируются корпуса малогабаритных щелочных аккумуляторов, заполненных электролитом.
В автомобилестроении лазером сваривают детали кузова, шестерни коробки передач и карданного вала.
Сварка неметаллических деталей (стекла, керамика и др.) осуществляется за счет хорошего поглощения ими с большой длиной волны (λ= 10,6 мкм у лазера на СО2). По такой технологии изготавливаются корпуса термометров, где капилляр вваривается в оболочку и осуществляется заварка донышка. Подобным образом производится сварка пальчиковых ламп.
Резка и размерная обработка металлов основаны на использовании локального расплавления металла и его последующего удаления под действием силы тяжести, конвективного потока или газовой струи. Пары перегретого материала могут удаляться из зоны реза за счет собственной упругости и дополнительно струей инертного газа.
Эффективность резки может быть значительно повышена за счет введения в зону активного газа, например, кислорода. Реакция с ним увеличивает выделение энергии в месте взаимодействия материалов. Такой процесс называется газолазерной резкой.
Прошивка отверстий. Параметры и режимы, используемые при прошивке отверстий из различных материалов, сведены в табл. 12.
-
Материал
Толщина, мм
Диаметр отверстий, мм
Время импульса, мс
Энергия импульса, Дж
Входн.
Выходн.
Нержавеющая сталь
0,9
0,5
0,25
2,35
5,9
Никелевая сталь
1,78
0,3
0,22
0,8
16,0
Вольфрам
0,5
0,2
0,15
2,0
3,3
Молибден
0,5
0,25
0,2
2,0
3,3
Тантал
1,6
0,3
0,1
2,42
8,0
Медь
0,8
0,2
0,2
2,25
4,9
Магний
1,5
0,4
0,3
2,0
3,3
Получение отверстий с помощью лазера применяется для изготовления фильер, подшипников из кристаллических материалов для измерительных приборов, микротрафаретов для пленочных схем, форсунок и др. Используются заготовки из керамики, металла, феррита, рубина. Осуществляется как предварительная, так и финишная операция при изготовлении часовых камней. В последнем случае по сравнению с механической обработкой производительность оказывается в 100... 1000 раз выше.
Лазерная резка неметаллических материалов. Этот вид обработки позволяет резать материалы любой твердости, при этом обеспечиваются высокая точность и качество реза (малая ширина реза и параллельность кромок), малая зона нагрева, большая производительность, вдзможность точного, автоматизированного управления.
Таким способом обрабатываются: металлокерамика, стеклоуглерод, композитные материалы на основе нитей бора и углерода, стеклоткань (со значительным улучшением условий труда по сравнению с механической резкой).
Большое преимущество дает лазерная резка в деревообрабатывающей промышленности. Например, при раскрое фанеры отсутствуют опилки, достигается малая ширина реза, чистая поверхность кромок, высокая точность при очень сложных формах раскроя. Отмечается резкое повышение производительности бумагорезательного производства при переходе на лазерный раскрой бумаги и картона.
Лазерная маркировка. При воздействии лазерного излучения на металлы и неметаллы за короткий промежуток времени происходит нагрев поверхности до высокой температуры, при которой происходит плавление и испарение материала. Это приводит к появлению определенного следа или метки. Перемещая изделие относительно лазерного луча с определенной скоростью (см. рис. 78), можно получить на поверхности изображение в виде букв, линий, символов, знаков, цифр или рисунков.
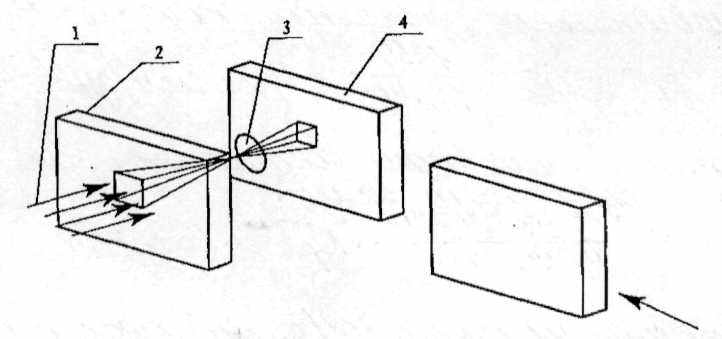
Рис. 78. Схема маркировки лазерным лучом.
1 - лазерное излучение; 2 - маска с изображением;3 - фокусирующая линза; 4 - маркируемое изделие.
Лазерное легирование металлическими компонентами осуществляется путем подачи присадочного порошка в зону обработки (рис. 79).
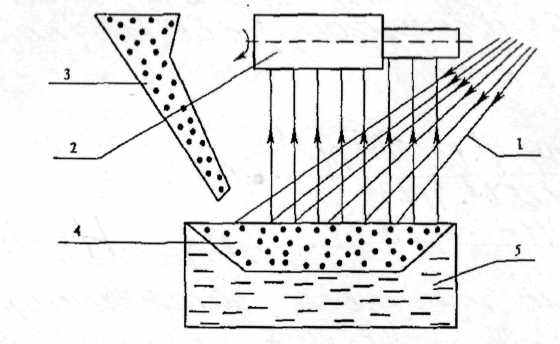
Рис. 79. Схема лазерного напыления металла.
Испаряемый порошок 4 подается из бункера 3 и охлаждаемый тигель 5, где под действием лазерного излучения 1 испаряется и оседает на обрабатываемой детали 2. Этот процесс ведут с использованием непрерывного излучения. В результате в. зоне обработки образуются пересыщенные твердые растворы, что приводит к повышению микротвердости.
Плазменная технология. В основе плазменной технологии лежит электрический дуговой разряд, в дуговом промежутке которого при высокой температуре образуются ионы и электроны. Эти заряженные частицы обеспечивают прохождение электрического тока через газ и придают ему ряд ценных с практической точки зрения свойств. Среда, в которой находится значительная часть молекул или атомов, называется плазмой.
Плазма находит технологическое применение, прежде всего в процессах, которые требуют высокотемпературного концентрированного нагрева значительных зон заготовки. В промышленности широко используются плазменная резка металлов, плазменные наплавка, сварка, напыление тугоплавких металлов, оксидов, карбидов и нитридов, а также комбинированное воздействие, называемое плазменно-механической обработкой.
Сущность плазменно-механического метода обработки состоит в том, что при обработке резанием высокопрочных материалов и сплавов перед резцом устанавливается плазмотрон, нагревающий узкую зону обрабатываемого материала. Так как при нагреве прочность обрабатываемого материала снижается, а пластичность увеличивается, можно без ущерба для качества поверхности увеличить подачу и глубину резания. Плазменно-механическая обработка применяется при изготовлении деталей из жаропрочных сталей и сплавов на базе вольфрама, молибдена и других материалов, в которых при механической обработке при обычной температуре в поверхностных слоях образуются микротрещины.
Плазменная технология нашла применение и при покрытиях материалов. Одной из разновидностей процесса плазменного напыления является ионная технология плазменного нанесения покрытий с помощью плазменных ускорителей. Схема такого процесса изображена на рис. 80.
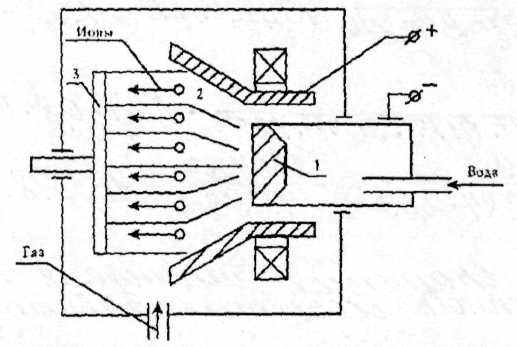
Рис. 80. Схема ионного нанесения покрытий с помощью плазменного ускорителя.
В соответствии с этой схемой материал покрытия получается путем испарения, в вакууме охлаждаемого водой, катода 1. Затем его ионизируют в электрическом разряде и превращают в плазму 2, которая с помощью электромагнитного поля ускоряется и фокусируется по направлению к обрабатываемой поверхности 3. Значительная энергия, которую можно сообщить ионам в плазме, позволяет внедрять их в обрабатываемые поверхности и получать прочные поверхностные покрытия.