Совершенствование технологии комбинированного окомкования, загрузки, зажигания и спекания агломерационной шихты 05. 16. 02 Металлургия черных, цветных и редких металлов
Вид материала | Автореферат диссертации |
СодержаниеГлава 4. Загрузка шихты на агломерационную машину Ширина загрузочной воронки, м Глава 5. Внешний нагрев слоя спекаемой шихты Рис. 7. Зависимость давления в горне от разрежения |
- Физико-химические свойства и технологические основы получения пирротинов из пирита, 328.59kb.
- Программа вступительного испытания по направлению «Металлургия», 51.65kb.
- O Всероссийской олимпиаде по специальностям 150101 Металлургия чёрных металлов и 150102, 50.91kb.
- Московский Государственный Институт Стали и Сплавов (Технологический Университет) Кафедра, 461.38kb.
- Правительства Российской Федерации от 23 июля 2002 г. # 552 "Об утверждении Положения, 136.41kb.
- Федеральный государственный образовательный стандарт среднего профессионального образования, 904.07kb.
- Доклад об осуществлении лицензионного контроля в сфере заготовки, переработки и реализации, 129.86kb.
- Специальность «металлургия черных металлов» кафедра «металлургия» осуществляет подготовку, 63.79kb.
- Отчет по результатам исследования «Создание предприятий по заготовке, переработке, 4399.59kb.
- «производство отливок из сплавов цветных металлов», 38.25kb.
Как видно с увеличением работы уплотнения гранул окомкованной шихты удельная производительность установки линейно увеличивается. Таким образом, принципиально установлена возможность интенсификации процесса за счет увеличения уплотняющего воздействия на обрабатываемый в них поток шихты путем использования тарельчатых грануляторов (рис. 3).
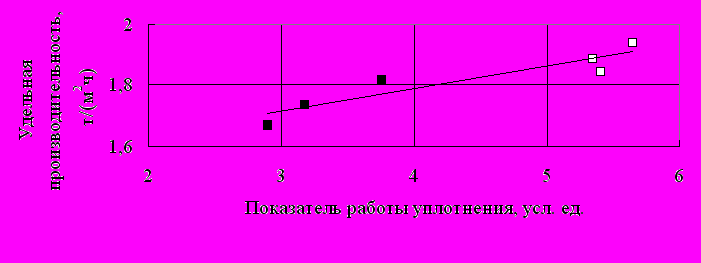
у=0,0744х+1,4908
R=0,927
Показатель работы уплотнения, усл. ед.
Рис. 3. Зависимость удельной производительности от показателя работы уплотнения гранул, полученных в различных окомкователях. ■ и □ – окомкование в лабораторных барабанном и тарельчатом грануляторах соответственно
Технико-экономические показатели работы агломашины № 4 в базовом (январь-март 2007 г) и опытном (май-октябрь 2007 г) периодах приведены в табл. 2.
Таблица 2
Технико-экономические показатели работы агломашины № 4 в базовом (январь-март 2007 г) и опытном (май-октябрь 2007 г) периодах
Период | Удел. произ-ть, т/(м2×ч) | Скор-ть А/М, м/мин | Высота слоя, мм | Разрежение, кПа | Темп-ра отход. газов, С | Прочность агломерата | Содержание –5 мм, % | |
Х+5 | Х-0,5 | |||||||
Базовый | 1,845 | 3,8 | 440 | 11,84 | 118 | 63,0÷64,6 | 7,1÷6,3 | 9,0÷7,7 |
Опытный | 1,938 | 3,6 | 461 | 11,77 | 123 | 63,8÷64,9 | 6,9÷6,3 | 8,9÷7,5 |
Глава 4. Загрузка шихты на агломерационную машину
Практика показывает, что самая тщательная подготовка шихты может оказаться неэффективной из-за неудовлетворительного формирования слоя шихты на агломашине. Для достижения высокой газопроницаемости слоя необходимо решить комплекс задач, начиная с оптимизации режима работы челнокового распределителя (ЧР) узла загрузки шихты и заканчивая конструкцией гладилки шихты.
Анализируя работу узла загрузки, обработали данные АСУ ТП об уровне шихты в загрузочной воронке (ЗВ), частоте вращения барабанного питателя (БП) и расходу шихты по времени. Проектное распределение шихты по ширине ЗВ было нерациональным с технологической точки зрения, т.к. кривая распределения имеет выпуклую в центре ЗВ форму с понижением к краям ЗВ. Это обусловлено увеличенными размерами разгрузочного окна у краев ЗВ. Уровень шихты с левой стороны (по ходу агломашины) колебался в пределах 39-48 %, с правой — 46-54 %. Соответственно изменялся уровень сегрегации шихты по крупности и концентрации топлива — с повышением крупности и снижением концентрации топлива к краям ЗВ, что напрямую сказывалось на качестве агломерата. При этом расчетный среднеарифметический уровень шихты находится в заданных пределах: 56-65 %, т.е. эта характеристика недостаточна для управления загрузкой.
Для анализа распределения шихты в ЗВ выполнили расчеты на математической модели ОАО «УИМ», адаптированной к условиям работы АМ-4. Результаты расчетов на модели по распределению шихты в ЗВ при проектном режиме работы ЧР, т.е. при одинаковых в каждом "цикле" (последовательном проходе ЧР вперед и назад) скорости КЛ и тележки ЧР при заданном превышении уровня шихты на границах ЗВ над центром, равном 0,2 м, иллюстрируются рис. 4.
Кривая Н1 характеризует профиль слоя, который сформировался на поверхности в ЗВ в предыдущем цикле после прохода ЧР "назад" от границы О2 к границе О1 и затем опустился вниз к выпускному отверстию ЗВ. Кривая В2 характеризует профиль слоя в новом цикле после прохода ЧР вперед от границы О1 к границе О2, а Н2 – в этом же цикле при возвращении ЧР к границе О2. Расстояние между кривыми Н1 и В2 характеризует толщину поперечного слоя при движении ЧР вперед, а расстояние между В2 и Н2 – при движении ЧР назад.
![]() Н2 В2 Н1 Ширина загрузочной воронки, м | ![]() Н2 В2 Н1 Ширина загрузочной воронки, м |
а б
Рис. 4. Профиль слоя шихты в загрузочной воронке: а - при проектном режиме работы челнокового распределителя; б - при оптимальном режиме работы ЧР (Обозначения: Н – назад, В – вперед)
Оптимальным для работы ЧР является режим, в котором в дополнение к условию постоянства скорости КЛ относительно течки соблюдается условие, учитывающее накопление шихты на КЛ. В этом случае КЛ и тележка ЧР движутся "вперед" с меньшей скоростью, а назад — с большей, при этом переменна и скорость движения КЛ ЧР, а режим работы ЧР устанавливается согласно условиям:
Vлн/ Vтн = Vлв/ Vтв (8)
Vтв = Vтн (Vлн / Vтн – 1) / (Vлн / Vтн+1) (9)
Vлв = Vлн (Vлн / Vтн – 1) / (Vлн / Vтн+1) (10)
VлО1 = Vлв + Vтв (11)
VлО2 = Vлн – Vтн = VлО1 (12)
НслО1 = НслО2 и > Нсл.ц. (13)
где: Vлв и Vлн – скорость конвейерной ленты челнокового распределителя в режимах работы вперед и назад, м/мин; Vтв и Vтн – скорость тележки челнокового распределителя в режимах работы вперед и назад, м/мин; VлО1, VлО2 – скорость конвейерной ленты челнокового распределителя в режимах остановок на ближней к течке и дальней от нее границах загрузочной воронки вперед и назад, м/мин; НслО1 и НслО2 – высота слоя шихты на ближней и дальней от течки границах загрузочной воронки в момент начала движения челнокового распределителя после остановок, м; Нсл.ц – высота слоя шихты в центре загрузочной воронки в момент окончания его пересечения потоком шихты с челнокового распределителя, м.
Режим работы при знакопеременном движении ЧР с формированием в ЗВ поперечных слоев с одинаковой толщиной обеспечивается условием (8), а с одинаковой толщиной слоев на КЛ – условиями (9)–(12) с учетом в них условия (8). При соблюдении перечисленных условий получен оптимальный профиль шихты, показанный на рис. 4.б.
Как видно, толщина поперечных слоев в ЗВ практически одинаковая и они перемещаются сверху вниз к разгрузочному отверстию ЗВ равномерно по высоте и ширине ЗВ. При этом формируется и симметричное и одинаковое распределение шихты у краев ЗВ. Соответственно обеспечивается рациональное формирование слоя на агломерационной машине, как в объеме слоя, так и бортов паллет.
Продолжительность остановок ЧР на границах ЗВ зависит от заданного уровня превышения слоя над центром. С принятыми параметрами продолжительность остановок ЧР на границах при равномерной загрузке шихты с ближней стороны к течке составляет 0,5, с дальней – 1,7 сек, при превышении уровня у стенок на 0,1 м —1,2 и 2,2 сек, а при превышении 0,2 м — 1,9 и 3,5 сек соответственно.
Из-за накопления шихты на ленте ЧР при движении вперед и ее сокращения при обратном движении масса шихты в ЗВ соответственно снижается и возрастает. Максимальное значение объема и массы (8,2 т) устанавливается при остановках ЧР на ближней от течки границе, когда с КЛ сбрасывается в течку вся накопившаяся шихта, а минимальное значение (7,34 т) — на дальней.
Контроль и регулирование параметров разработанного режима осуществляется с помощью модернизированных приводов КР и тележки ЧР, которые оснащаются частотными преобразователями, и дистанционных датчиков уровня (в частности, радарного типа) для измерения в ЗВ на ее границах и в центре, а программа управления реализуется через контроллер. Датчик уровня установлен на раме движущейся тележки ЧР, что позволяет сканировать уровень по ширине ЗВ во времени. Совместно с алгоритмом работы загрузочного устройства, имеющего задачу стабилизировать уровень шихты в ЗВ на АМ 3 реализован алгоритм загрузки шихты на паллеты, включающий основные пункты:
- скорости агломашины и частоты вращения БП согласовываются в зависимости от скорости первой;
- уровень шихты в ЗВ стабилизируется путем изменения частоты вращения тарельчатых питателей в каждой группе шихтовых бункеров, обслуживающих окомкователи.
- при необходимости изменения скорости агломашины вначале в автоматическом режиме должен пропорционально изменяться расход шихты с помощью тарельчатых питателей шихтовых бункеров и после этого, с учетом запаздывания, — скорость агломашины.
Из известных способов борьбы с неравномерностью спекания по ширине ленты применили сочетание двух из них: уширение бортов паллет и установку плоского уширенного колосника у бортов паллет. Борта паллет были уширены на 100 мм с каждой стороны без изменения площади их колосникового поля. Благодаря этому масса загружаемой шихты возросла на 5 %, общий прирост удельной производительности в опытном периоде возрос на 4,6 %, повысилась прочность агломерата.
Глава 5. Внешний нагрев слоя спекаемой шихты
Анализ процессов, протекающих в слое под зажигательным горном.
Анализ внешнего нагрева шихты выполнен на комплексной математической модели ОАО "УИМ".
Исследования на модели провели для шихты с начальной нулевой температурой Ш0— зимние условия, 20°C — летние условия (Ш20), 40, 60 и 82 °C — подогретая шихта (Ш40, Ш60, Ш82).
Равновесная температура испарения Трвн, и, соответственно, «точка росы» падает по мере удаления от поверхности слоя в результате снижения температуры газа на входе в зону сушки. Затем происходит её дополнительное снижение вследствие перехода слоя из первой секции горна с высокими значениями температуры (1290 оС) и содержания водяных паров в газе (11,6%) во вторую, с более низкими значениями (984 оС и 8,1% соответственно). И, наконец, следующее небольшое, но непрерывное снижение температуры tр обусловлено переходом слоя за пределы горна, где в него поступает атмосферный воздух.
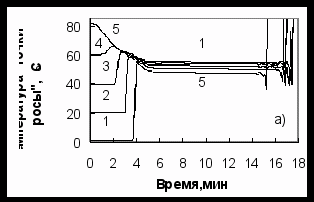
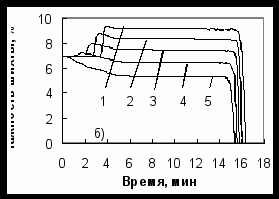
а б
Рис. 5. Распределение температуры "точки росы" (а) и влажности (б) шихты с разной начальной температурой на нижней границе слоя (1-Ш0, 2 – Ш20, 3- Ш40, 4 – Ш60, 5-Ш82).
Для шихт с начальной температурой 0, 20 и 60оС (далее Ш0, Ш20 и Ш60) конденсация влаги завершается за 3,76, 3,15 и 1,45 мин соответственно (рис. 5). При температуре tшо=82оС (Ш82) и базовой влажности шихты конденсация влаги практически отсутствует и сразу начинается подсушка шихты (рис. 5б).
Изменение исходной влажности на (Wшо) на максимальное значения температуры tр и влажность шихты по высоте слоя (Wшм,), а также максимальную влажность шихты на нижней границе слоя (W'шм ) после завершения конденсации, % (шихта Ш20) приведена в табл. 3.
Таблица 3
Влияние исходной влажности на (Wшо) на некоторые параметры спекаемой шихты в начальный момент агломерации (шихта Ш20)
Наименование параметра | Исходная влажность | ||
6,5 % | 6,9 % | 7,45% | |
Максимальное значения температуры tр макс | 75,0 | 75,4 | 75,8 |
Максимальная влажность шихты по высоте слоя Wшм, % | 8,80 | 9,40 | 9,85 |
Максимальная влажность шихты на нижней границе слоя W'шм после завершения конденсации, % | 7,78 | 8,46 | 8,87 |
Таблица 4
Температура и влажность переувлажненной шихты на нижней границе слоя
Шихта | Скорость фронта сушки U, % (отн.) | Температура переувлажненной шихты, оС | Влажность шихты, % | Количество испарившейся при подсушке влаги, % | ||
max | в конце сушки | max | в конце сушки | |||
Ш0 | 100 | 56,7 | 54,9 | 9,28 | 9,05 | 0,23 |
Ш20 | 101,4 | 60,5 | 53,4 | 8,60 | 8,27 | 0,41 |
Ш40 | - | 62,6 | 51,8 | 7,94 | 7,37 | 0,57 |
Ш60 | 105,1 | 65,6 | 49,9 | 7,17 | 6,39 | 0,78 |
Ш82 | 114,3 | 81,8 | 47,3 | 7,07 | 5,20 | 1,87 |
Повышение степени переувлажнения шихты с ростом ее начальной влажности являются основными причинами несовпадения оптимальной влажности шихты, оцениваемой по ее начальной газопроницаемости и по скорости процесса спекания (первая всегда выше).
Из данных рис. 5 и табл. 4 видно, что чем выше температура tшо, тем больше влаги удаляется при ее подсушке.
Благодаря подсушке шихты скорость перемещения фронта сушки шихты (Uc), предшествующая скорости перемещения фронта горения топлива, растет с увеличением температуры tшо (табл. 4).
Для уточнения влияния влажности горновых газов исследовали на модели "агломерацию" сухой шихты Ш20. Максимальное значение температуры tр составило 52оС, а максимальная влажность переувлажненной шихты – 1,0 %.
Для шихт Ш0, Ш20, Ш60 и Ш82 максимальное значение содержания водяного пара под горном по отношению к сухому газу составляет в слое 56, 62, 82 и 118 % (об.) соответственно, а на нижней границе слоя – 22, 27, 37 и 108 %. Для шихт Ш0 и Ш20 начальные значения скорости фильтрации газа на входе в слой wвх (рис. 6) и на выходе из него wвых очень высокие, при этом скорость wвх больше wвых. Обе пограничные скорости быстро падают в результате общего роста объема газов за счет испарении влаги и увеличения средней температуры газа. Температура газового потока в слое к концу горна достигает 200–250оС.
Разрежение в вакуум-камере определяется условиями работы газоотводящего тракта и остается постоянным, а рост сопротивления слоя проявляется через падение скорости фильтрации газа.
Характер изменения кривых скорости фильтрации газа во времени стабилен, что важно для управления газодинамическим режимом зажигания при входных возмущениях. При спекании холодной шихты (Ш0), а также при зажигании перегретой шихты (Ш82) нестабильность газодинамического режима резко возрастает.
Таким образом, для начального периода характерно наличие трех видов скорости фильтрации: на входе и выходе из слоя, и средней по слою.
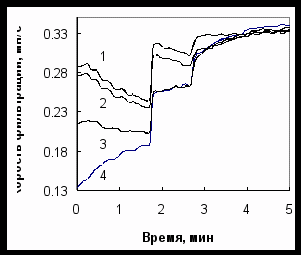
Время, мин.
Рис. 6. Распределение скорости фильтрации газа на входе в слой у шихт с разной начальной температурой и одинаковом прикрытии дроссельных заслонок первых двух вакуум-камер (1- Wвх0; 2- Wвх20; 3- Wвх60; 4- Wвх82)
Последняя, наряду с коэффициентом сопротивления слоя и температурой газового потока, определяет его сопротивление, первая – реальное количество горновых газов, которое может пропустить через себя слой, а средняя влияет на степень прикрытия дроссельной заслонки вакуум-камер. Расчетные параметры газа в слое и в сборном коллекторе в начальном периоде агломерации без дросселирования вакуум камер приведены в табл. 5, а с ним – в табл. 6.
Таблица 5
Параметры газа в слое и газоотводящем тракте в начальном периоде агломерации в базовом режиме КНШ без дросселирования первых вакуум-камер
Наименование | Температура шихты, оС | |||||||
0 | 20 | 60 | 82 | |||||
№ вакуум-камеры | 1-2 | 3 | 1-2 | 3 | 1-2 | 3 | 1-2 | 3 |
Скорость фильтрации, мн/с: на входе в слой средняя в слое на выходе из слоя | 0,399 0,393 0,368 | 0,334 0,409 0,327 | 0,388 0,416 0,365 | 0,333 0,406 0,401 | 0,332 0,405 0,402 | 0,321 0,389 0,403 | 0,297 0,389 0,429 | 0,316 0,374 0,391 |
Разрежение в коллекторе, кПа | 11,74 | 11,60 | 11,31 | 11,13 | ||||
Температура газа в коллекторе, оС | 106 | 117 | 124 | 129 |
Без дросселирования и при одинаковом прикрытии заслонок в/к с ростом начальной температуры шихты увеличивается температура уходящих газов и падает разрежение в коллекторе и в первых вакуум-камерах. Отсюда следует, что чем ниже начальная температура шихты, тем меньше должно быть разрежение в первых вакуум-камерах, т.е. тем сильнее их нужно дросселировать.
Практика показывает, что начальная температура шихты 60оС в принципе достаточна с точки зрения ограничения конденсации влаги. Однако, просос атмосферного воздуха с температурой 20оС через слой шихты Ш60 перед горном приводит к падению температуры материала в верхних элементах слоя до 6оС с подсушкой шихты до влажности 4,3 %. При перемещении слоя под горн влажность переувлажненной шихты достигает 7,3 %, т.е. в слое конденсируется до 3% влаги по сравнению с 0,8% при температуре шихты 60оС.
Таблица 6
Параметры газа в слое и газоотводящем тракте в начальном периоде агломерации при дросселировании первых двух в/к в режиме зажигания шихты
№ в/к | Разрежение в вакуум-камере, кПа. | Средняя темпера- тура газа в слое, оС | Доля пара, % (об.) к сухому газу | Скорость фильтрации, мн/с | ||||||
на входе в слой | средняя по слою | |||||||||
Ш20 | Ш60 | Ш20 | Ш60 | Ш20 | Ш60 | Ш20 | Ш60 | Ш20 | Ш60 | |
1 | 3,49 | 4,94 | 65 | 99 | 8,4 | 31,2 | 0,226 | 0,222 | 0,223 | 0,265 |
2 | 4,54 | 5,80 | 108 | 135 | 13,2 | 29,3 | 0,233 | 0,230 | 0,252 | 0,284 |
Исследование зажигания шихты. Двухсекционный зажигательный горн АМ-3 со сводовым размещением 16-и горелок имеет в просвете длину 7890, ширину – 4360 мм. Горн отапливается смесью природного (12 %) и доменного (88 %) газов. Расход газа изменяется в зависимости от состава шихты и скорости ленты от 8200 до 9500 м3/ч, расход воздуха практически постоянный, так как он ограничен производительностью дутьевого вентилятора, равной ~ 22000 м3/ч. Управление тепловым режимом горна осуществляется по температуре поверхности слоя над вакуум-камерами 1 и 2 и сразу за горном по центру слоя и на его периферии.
![]() Рис. 7. Зависимость давления в горне от разрежения: а - в вакуум-камере 1; б – в вакуум-камере №2. ![]() | ![]() |
В соответствии с технологическими требованиями к осваиваемой в настоящее время АСУ ТП агломашины АМ 3 в патрубках первых двух вакуум-камер установили дроссельные устройства с исполнительными механизмами, а также уплотнение между этими вакуум-камерами.
В ходе исследований оценили уровень снижения расхода газа за счет дросселирования вакуум-камер и при условии сохранения температуры поверхности слоя. Cвязь между разрежением в вакуум-камерах и в горне (рис. 7а, 7б) не является достаточно тесной. Это обусловлено тем, горн разуплотнен относительно бортов паллет и слоя, а также недостаточным уровнем дросселирования первых вакуум-камер для установления атмосферного давления в горне.
Вместе с тем, достоверность связи разрежения в горне и температуры поверхности слоя (рис. 8а и 8б) является высокой: при снижении разрежения в горне с 0,9 до 0,5 мм вод. ст. температура поверхности слоя возросла на 90 и 120оС соответственно в первой и второй секциях горна. Это можно объяснить только снижением количества подсосов воздуха в горн.
![]() Рис. 8. Зависимость температуры поверхности слоя в вакуум-камере 1 от разрежения в горне: а – в первой вакуум-камере; б – во второй вакуум-камере | ![]() ![]() |
Как следствие подсосов воздуха в горн температура поверхности, измеряемая сразу за торцевой стенкой горна пирометрическими датчиками, составляет в центре, слева и справа слоя по ходу ленты 664, 624 и 621оС. Указанная неравномерность является одной из причин и неравномерного подхода зоны горения к колосникам: отклонение температуры уходящих газов, измеряемой термопарами, установленными непосредственно под колосниковой решеткой, на периферии слоя от центра составляет от 14оС (справа) до 45 оС (слева).
При закрытом дросселе в/к 1 разрежение в ней составило 7,4 кПа, после открытия – 8,50 кПа (при разрежении в коллекторе 12,0кПа). Для сохранения температуры поверхности расход газа был увеличен с 9200 до 9480 м3/ч.