Производственные системы «точно в срок» (jit) в этой главе
Вид материала | Документы |
- Производственное планирование в структуре логистического менеджмента промышленного, 179.15kb.
- «точно в срок», 63.96kb.
- Виды транспортных систем, 108.53kb.
- Философия микропроцессорной техники, 3706.56kb.
- 1. Понятие и характеристики всемирного хозяйства, 416.26kb.
- Клиническая справка о синдроме Ретта Тезис, 468.58kb.
- Всн 01-89 Предприятия по обслуживанию автомобилей, 605.83kb.
- Кафаров В. В., Макаров В. В. Гибкие автоматизированные производственные системы в химической, 113.42kb.
- -, 1050.84kb.
- Для заказа этой или новой работы свяжитесь, 114.85kb.
Японский подход к производительности
После Второй мировой войны руководство Японии поставило цель достичь полной занятости населения за счет индустриализации. Стратегию получения рыночного преимущества сфокусировали на определенные отрасли производства. Министерство международной торговли и промышленности Японии (MITI) при выборе приоритетных отраслей сделало ставку на конкурентоспособные отрасли2.
Для улучшения конкурентоспособности своей страны Япония начала импортировать технологии. Вместо разработки новых технологий японские промышленники покупали лицензии (чаще всего у фирм США), избегая, таким образом, больших расходов на НИОКР и связанных с ними рисков. При создании новых видов продукции они сконцентрировали усилия на организации производства для достижения высокой производительности и] уменьшения себестоимости единицы продукции. Они использовали таланты своих разработчиков больше для организации производства, а не для разработки новых изделий. Японцы также работали над улучшением качества продукции и ее надежности, пытаясь превзойти в этоМ1 своих конкурентов. Главными стали две концепции — устранение потерь и уважение к людям.
Устранение потерь и бесполезных расходов
Японцы действительно верят, что можно избежать потерь. Потери в Японии, по определению Фуджио Чо (Fujio Cho) из Toyota, представляют собой "любые расходы, кроме связанных с использованием минимального количества оборудования, материалов, комплектующих и рабочих, безусловно необходимых в производстве". Расширенное толкование JIT, предложенное Фуджио Чо, определяет семь основных типов потерь, подлежащих устранению.
- Ненужные расходы на перепроизводство.
- Потери от простоев (времени ожидания).
- Транспортные потери.
- Складские потери.
- Технологические потери.
- Потери, зависящие от длительности производственного цикла.
- Потери от дефектов продукции3.
Это определение JIT не оставляет места для излишков или страховых запасов. Не предусматриваются никакие страховые запасы; другими словами, если запасы нельзя использовать в данный момент времени — в них нет потребности. Они излишни. Скрытые материально-производственные запасы на складах, в системе транзита, на конвейерах — все это ключевые пункты уменьшения материально-производственных запасов.
Применение следующих семи элементов нацелено на исключение потерь.
- Сеть специализированных заводов.
- Групповая технология.
- Качество у истока.
- Производство "точно в срок".
- Однородная загрузка производства.
- Система управления производством "Канбан".
- Минимизация времени переналадки.
Сеть специализированных заводов. В Японии чаще предпочитают строить небольшие специализированные заводы, а не огромные вертикально интегрированные производственные конгломераты. Они считают, что большим количеством операций и многочисленной бюрократией сложнее управлять. Кроме того, это не согласуется с их стилем управления. Заводы, спроектированные с одной конкретной целью, более экономичны при строительстве и в ходе эксплуатации. Большинство японских заводов, приблизительно 60 тысяч, имеют от 30 до 1000 рабочих.
Групповая технология. Групповая технология, хотя и была предложена в США, успешнее применяется в Японии. Вместо передачи выполняемой работы с одного рабочего участка с определенной специализацией рабочих на другой специализированный участок, японцы объединили все операции, необходимые для изготовления определенной детали, и сгруппировали необходимое оборудование в одном месте. На рис. 8.2 показаны отличия между участками с различным расположением оборудования — объединенного в рабочие центры по изготовлению деталей и размещенного на специализированных участках.
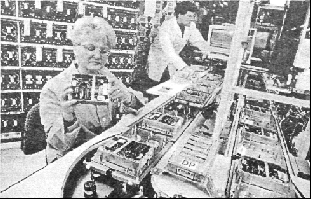
Качество у истока. Качество у истока означает контроль качества непосредственно на месте выполнения операции с самого начала процесса и предусматривает немедленную остановку процесса или конвейера при обнаружении отклонений. Заводские рабочие сами становятся контролерами, лично отвечая за качество своей продукции. Рабочие нацелены на качественное выполнение своей части работы с первой попытки, таким образом, снимается проблема качества, как например, на заводе TRW в Маршалле, штат Иллинойс, где установлены аварийные пневмодатчики. Если темп слишком высокий и у рабочего появляются проблемы с качеством или возникают вопросы, связанные с безопасностью работы, рабочий обязан нажать кнопку остановки конвейера и включить визуальный сигнал. Работающие на других участках отреагируют на тревогу и возникшую проблему. Рабочим предоставлено право самим обслуживать себя и свое рабочее место, чтобы разрешить проблему.
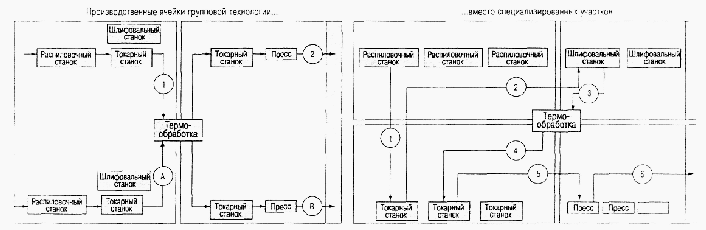
Рис. 8.2. Групповая технология по сравнению со специализацией участков
Контроль качества у истока включает также систему автономного контроля качества продукции и автоматический контроль. Японцы предпочитают контроль качества, выполняемый автоматически или с помощью роботов, так как это быстрее, легче, надежнее и высвобождает рабочих.
Система производства "точно в срок" (JIT). Система JIT предполагает производство того, что необходимо, когда необходимо и не больше того, что необходимо. Все, что больше минимально необходимого количества рассматривается как потери, так как усилия и материалы затрачены на то, что не является необходимым и не может быть использовано в данный момент. В табл. 8.1 показаны требования и допущения системы JIT.
Система JIT применима к серийному производству. Использование этой системы не всегда требует больших объемов производства и не ограничивается технологическими процессами, предназначенными для серийного выпуска продукции. Ее можно применять везде, к любой повторяющейся работе. При такой системе идеальный размер передаточной партии на каждом рабочем месте — одна единица. Рабочий выполняет свою операцию и передает ее следующему рабочему для продолжения производства. Поскольку рабочие центры могут быть территориально разбросаны, японцы минимизируют время передачи и поддерживают передаваемое количество небольшим, обычно размер партии составляет одну десятую часть дневной производственной нормы. Для поддержания заделов небольшими, а материальных запасов низкими поставщики даже отгружают потребителям комплектующие несколько раз в день. Если все ожидания в очереди сведены до нуля, капиталовложения в материальные запасы и время выполнения заказов минимальны, то фирмы могут быстрее реагировать на изменение спроса и решать проблемы качества.
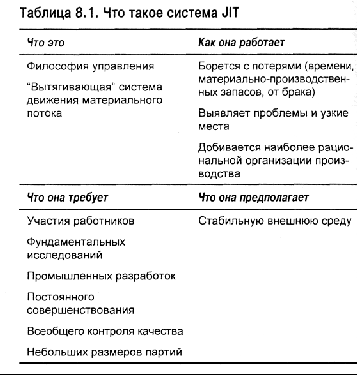
Суть этой идеи проиллюстрирована на рис. 8.3. Если вода в пруду представляет собой материальный запас, то подводные камни представляют собой проблемы, которые могут возникать в фирме.

Рис. 8.3. Проблемы, скрытые материальными запасами
Высокий уровень воды скрывает камни (проблемы). Менеджмент воспринимает это как нормальное состояние, но при спаде экономической активности уровень воды падает, обнажаются проблемы (камни). Если целенаправленно снижать уровень воды (в частности, в периоды высокой экономической активности), то можно выявить и отрегулировать проблемы, прежде, чем они приведут к еще большим проблемам. Организация производства по системе JIT выявляет проблемы, ранее спрятанные в избытках материальных запасов и штатах.
Однородная загрузка завода (производства). Цель однородной загрузки производства — сглаживание колебаний производственного потока, обычно возникающих как реакция на изменения производственного графика. Изменения, возникнув на завершающем конвейере, распространяются на всю производственную линию и цепь поставок. Единственным путем устранения таких колебаний является недопущение регулирования объемов производства. Для этого устанавливается месячный производственный план с фиксированным объемом выпускаемой продукции. (Необходимость стабильной среды для компании, работающей по системе JIT, отмечена в табл. 8.1.)
В Японии нашли, что можно решить проблему выравнивания загрузки производства ежедневным выпуском одного и того же ассортимента продукции в небольших количествах. Таким образом, в наличии всегда имеется полный ассортимент продукции для адекватного реагирования на изменения спроса. Пример Toyota показан в табл. 8.2. Месячное количество производимых автомобилей сводят к дневному (приняв, что в месяце 20 рабочих дней).
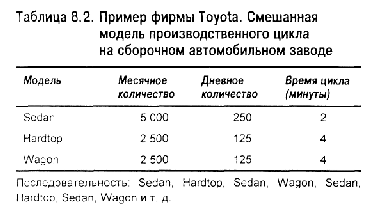
Исходя из полной загрузки сборочного конвейера определяют такт (время между сборкой на конвейере двух идентичных изделий) в минутах. Продолжительность такта используют для регулирования ресурсов, необходимых для выпуска установленного количества продукции. Производительность оборудования или сборочной линии не имеет значения. Важно производить именно то количество продукции, которое необходимо каждый день. Система JIT обязывает производить по графику, с минимальными издержками и с наилучшим качеством. (Более подробное обсуждение смешанной модели сборки приведено в главе 10).
Система управления производством "Канбан". Для регулирования JIT-потоков в системе "Канбан" используют сигнальные устройства. "Канбан" в переводе с японского означает "знак" или "карточка с инструкцией". В безбумажной системе контроля вместо карточек можно использовать контейнеры. Карточки или контейнеры составляют суть "вытягивающей" системы "канбан". Разрешение производить или поставлять дополнительные комплектующие исходит из последующих операций. Карточка является разрешением на получение или производство следующей партии комплектующих. На рис. 8.4 показана сборочная линия конвейера, который питается комплектующими из центра механической обработки.
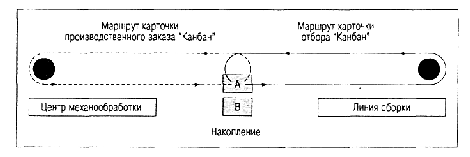
Рис. 8.4. Маршрут движения двух карточек «Канбан»
Центр механообработки производит две комплектующие детали — А и В. Эти две детали хранятся в контейнерах, расположенных на границе сборочного конвейера и центра механообработки. Каждый контейнер, расположенный у сборочной линии, имеет карточку отбора "канбан", а каждый контейнер у центра металлообработки имеет карточку производственного заказа "канбан". Эту систему часто называют двухкарточной системой "канбан".
Когда сборочная линия принимает первое комплектующее изделие А из контейнера, рабочий снимает карточку отбора с контейнера и передает ее на место складирования в центре механообработки. В центре механообработки рабочий находит в контейнере изделия А карточку производственного заказа "канбан" и заменяет ее карточкой отбора "канбан". Размещение этой карточки на контейнере разрешает движение контейнера к сборочной линии. Освободившаяся карточка производственного заказа "канбан", прикрепленная на стеллаже рабочим центра механообработки, разрешает производство следующей партии деталей. Карточка на стеллаже становится официальным документом для центра механообработки. Способом передачи информации о необходимости производства комплектующих изделий являются не только карточки. Используют и другие сигнальные методы, показанные на рис. 8.5.
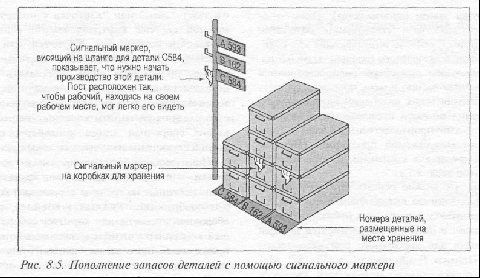
Рис. 8.5. Пополнение запасов деталей с помощью сигнального маркера
Ниже приведены некоторые другие возможные способы.
Контейнерная система. Иногда сам контейнер можно использовать в качестве сигнального устройства. В этом случае появление пустого контейнера на производственном участке визуально сигнализирует о необходимости его заполнения. Количество материальных запасов регулируется простым добавлением или удалением контейнеров.
П
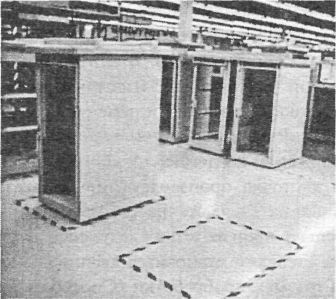
Окрашенные шары для гольфа. На заводе двигателей в Кавасаки при уменьшении количества деталей, используемых на вспомогательной сборке, до предельного уровня рабочий-сборщик сбрасывает окрашенный шар для гольфа по трубопроводу в обрабатывающий центр. Это служит сообщением оператору, какую деталь делать следующую. На основе этого подхода разработано много вариантов.
Систему контроля на основе "вытягивающего канбана" можно использовать не только в пределах одного производства, но и между различными производственными подразделениями (например, "вытягивание" двигателей или трансмиссии при сборке автомобилей), а также между производителями и внешними поставщиками.
Определение необходимого количества карточек "канбан". Применение системы "канбан" требует определения необходимого количества карточек "канбан" (или контейнеров). В случае двухкарточной системы определяют количество карточек отбора и карточек производственного заказа. Сколько карточек "канбан" - столько контейнеров с изделиями, циркулирующими между участками снабжения и потребления. Емкость каждого контейнера определяет минимальный размер производственного задела (запаса). Поэтому число контейнеров однозначно отражает объем материальных запасов, находящихся в производстве.
Ч

исло контейнеров рассчитывается исходя из времени выполнения заказа. Время выполнения заказа — это функция от продолжительности процесса изготовления всего количества комплектующих, возможного времени ожидания в течение производственного процесса и времени, необходимого для транспортирования материалов к потребителю. Достаточным является количество карточек, необходимых для покрытия ожидаемого спроса в течение времени выполнения заказа, плюс некоторое дополнительное резервное количество. Количество карточек определяют по формуле:
где
DL — ожидаемый спрос в период выполнения заказа;
k — количество карточек "канбан";
D — среднее количество деталей, потребляемых последующим участком в единицу времени;
L — время выполнения заказа (выраженное в соответствующих единицах);
S — страховой запас, выраженный в процентах относительно спроса за период выполнения заказа (как показано в главе 15, его можно определить по уровню обслуживания и дисперсии);
С — емкость контейнера.
Следует отметить, что система "канбан" не приводит к нулевым материальным запасам, она скорее контролирует количество материалов, которое должно находиться в производственном процессе в данный момент времени, — по числу контейнеров для каждой детали. Систему "канбан" легко перестроить, приспособив ее к текущей потребности, так как карточки можно легко добавить или изъять из системы. Если рабочие обнаружат, что некуда складывать изготовленные детали, можно поставить дополнительный контейнер, сопровождаемый карточкой "канбан". Если же обнаружено, что контейнеры с деталями накапливаются, наборы карточек легко изъять, уменьшив, таким образом, объем материальных запасов.
Пример 8.1. Определение количества карточек "канбан"
Компания An/in Automotiv, занимающаяся сборкой глушителей для Большой Тройки, была вынуждена использовать систему "канбан" для "протаскивания" комплектующих через все свои производственные участки. Arvin спроектировала каждый участок для изготовления конкретного семейства глушителей. Изготовление глушителя включает резку и сгибание отрезков трубы, которые затем приваривают к глушителю и каталитическому конвертеру (каталитическому дожигателю выхлопных газов). Глушитель и каталитический конвертер "вытягиваются" из участка в соответствии с текущим спросом. В свою очередь каталитические конвертеры изготавливаются на отдельном специализированном участке.
Каталитические конвертеры изготавливают партиями по 10 штук и перемещают на специальных ручных тележках к производственным участкам. Участок для каталитического конвертера спроектирован таким образом, что различные виды каталитических конвертеров можно изготавливать фактически без потерь на переналадку. Участок может отреагировать на заказ партии каталитических конвертеров приблизительно за четыре часа. Поскольку участок каталитического конвертера находится непосредственно возле участка сборки глушителя, время транспортирования ничтожно. Производственный участок сборки глушителя позволяет выполнять приблизительно восемь сборок за час. Каждая сборка использует одинаковый каталитический конвертер. Из-за некоторой нестабильности процесса руководство решило иметь резервный запас, эквивалентный 10% от необходимого количества материальных запасов.
Сколько карточек "канбан" необходимо для управления запасами каталитических конвертеров?
Решение
В этом случае время пополнения запаса конвертеров (L) равно четырем часам. Спрос (D) составляет восемь каталитических конвертеров в час. Резервный запас (S) равен 10% от ожидаемого спроса и емкость контейнера (С) составляет 10 единиц. Таким образом получаем:

В этом случае необходимо четыре карточки "канбан" и в системе будет четыре контейнера для конвертеров. Во всех случаях при вычислении k необходимо округлять полученную цифру в большую сторону, так как для работы всегда необходимо иметь полный контейнер комплектующих изделий.
Минимизация времени переналадки. Если небольшие размеры задела становятся нормой, то переналадка оборудования также должна выполняться быстро, чтобы на сборочной линии можно поочередно выпускать разные модели. Здесь уместно вспомнить широко известный пример конца 70-х годов, когда бригада прессовщиков фирмы Toyota, производящая капоты и крылья для автомобилей, проводила переналадку 800-тонного пресса за 10 минут, в то время как такую же операцию рабочие в США выполняли в среднем за 6 часов, а немецкие рабочие — за 4 часа. Сейчас такая скорость стала обычной для большинства автомобильных заводов в США. На заводе John Deere в 1985 году время переналадки штамповочного пресса уменьшено с одного часа до одной минуты. Для сокращения времени из процесса переналадки выделяют работы, выполняемые во время остановки оборудования, и те, которые можно провести при работающем оборудовании. С той же целью используют времясберегающие устройства, например, дублирующие держатели инструментов. Благодаря этому японская бригада наладчиков обычно не занимается переналадкой в выходные дни.