Обеспечение работоспособности и ресурсосбережения при восстановлении и упрочнении сложнопрофильных шлицевых деталей накаткой (на примере шлицевых деталей автотракторных карданных передач)
Вид материала | Автореферат |
- Исследование тепловых эффектов экзотермических реакций при термодиффузионном упрочнении, 113.6kb.
- Отяга модели 7А623 предназначен для обработки протягиванием разнообразных сквозных, 204.81kb.
- Моделирование и динамическая стабилизация нановыглаживания прецизионных поверхностей, 151.88kb.
- Программа вступительного экзамена в аспирантуру по специальной дисциплине 05. 02., 266.3kb.
- Механическая обработка, 11.65kb.
- 3 Допуски и посадки деталей машин и механизмов, 86.91kb.
- Особенности плазменной закалки крупногабаритных деталей из чугуна Батрак В. В., Веремейчик, 55.51kb.
- Задачи календарного планирования (теории расписаний, 162.35kb.
- Семинар на тему Оценка технологичности конструкций деталей, изготавливаемых, 461.77kb.
- Клепочное соединение, 38.71kb.
Во втором разделе «Теоретическое обоснование закономерностей формообразования при восстановлении шлицевых поверхностей накаткой» рассмотрены направления приложения сил деформирующей оснастки, линии скольжения металла при деформации и исходя из этого – конструктивная форма и размеры деформирующего и профилирующего инструмента.
Особенностью проектирования и разработки технологий восстановления сложнопрофильных поверхностей накаткой является ограниченность объема перемещаемого металла, связанная с небольшими величинами износа профиля и дефицитом металла по телу детали. Ввиду этого рассматриваются различные схемы формообразования, позволяющие оценить то или иное техническое решение с позиций наличия запасов металла, потребного для восстановления деталей; минимизации количества перемещаемого металла; направления и траектории перемещения металла; обеспечения оптимального напряженно-деформированного состояния при формообразовании восстанавливаемого профиля.
При моделировании процесса осадки шлицевой втулки установлены исходные соотношения основных технологических режимов, описывающие рациональные сочетания между степенью деформации h, температурой нагрева Т, диаметром осаживаемой поверхности D и усилием деформации Р (рисунок 2).
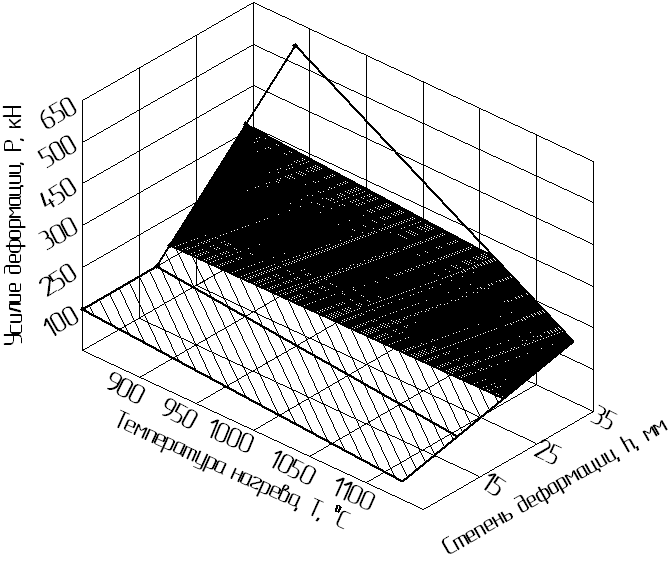
Рисунок 2 – Модель режимов осадки шлицевой втулки
Полученная математическая модель имеет вид
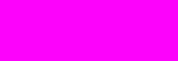
При этом экспериментально установлены: температура начала и конца пластической деформации 1150…850 о С; усилие деформации, обеспечивающее перемещение металла, 200 - 650 кН.
Исследованиями процесса деформации при принятых факторных областях: N – частота вращения детали – 200 мин-1; Δr – приращение (уменьшение) радиуса – 0,5…2,0 мм; Т – температура преддеформационного нагрева детали – 950 о С и Р – усилие накатки – 200 кН – получена эмпирическая формула без учета эффекта подстуживания детали в функции времени (рисунок 3).

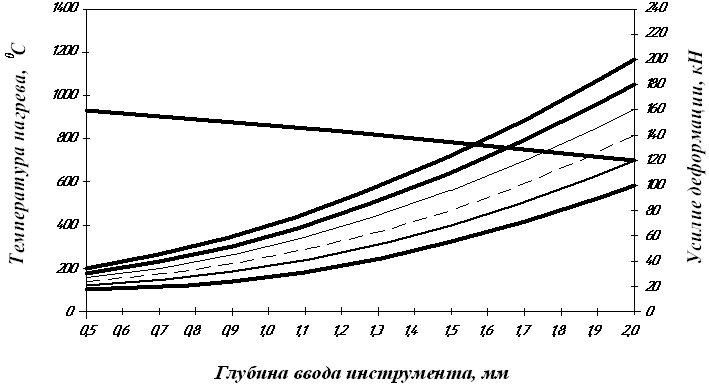
Рисунок 3 – Модель изменения усилия накатки без учета процесса подстуживания.
Для того, чтобы связать все параметры процесса деформации, принято, что показатель Z, характеризующий глубину ввода деформирующего инструмента за единицу времени, изменяется от 0 до 1. Если учесть, что скорость прохода деформирующего инструмента по обрабатываемой поверхности постоянна, то при частоте вращения детали N она будет введена в поверхность на глубину Z за время t = ZtH, следовательно, на глубине ввода инструмента в деталь Z температура ее нагрева изменяется на величину
Т = 950 - ΔТ∙t или T=950 – ΔTZtН. (13)
Тогда экспериментальный график зависимости усилия накатки Р от глубины ввода инструмента в деталь и частоты вращения патрона токарно-винторезного станка N при заданном изменении радиуса детали Δr = 1 примет несколько иной вид (рисунок 4).
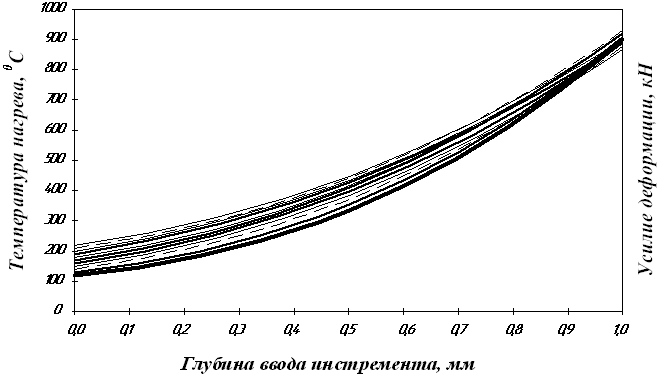
Рисунок 4 – Модель изменения усилия накатки с учетом подстуживания детали
Возрастание усилия деформации обусловливается эффектом подстуживания детали в функции времени ее накатки. Следовательно, для обеспечения постоянства процесса деформации необходимо уменьшить время прохождения детали сквозь накатное устройство. Для данного случая поверхность усилия накатки примет вид, изображенный на (рисунке 5).
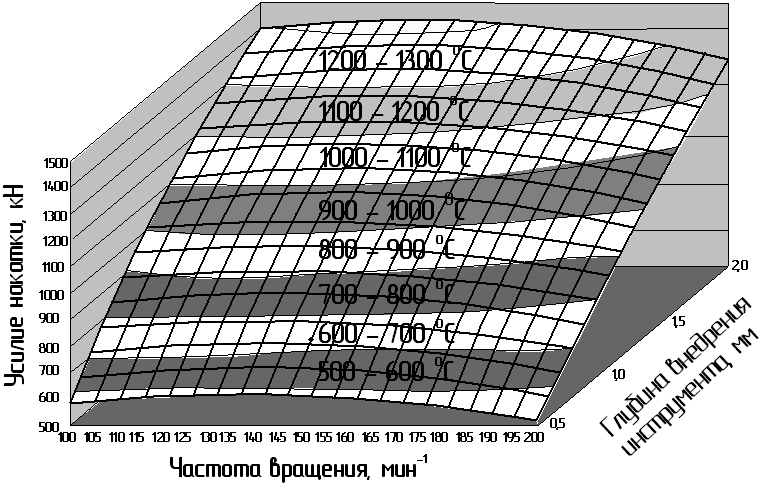
Рисунок 5 – Двухмерная номограмма поверхности усилия накатки
Максимум локальных изменений поверхности наглядно отображается на рисунке 7 в виде целевой области изменения режимных параметров, при этом качественная оценка двухмерной поверхности описывается поверхностью отклика, заключенной режимами (рисунок 6): частотой вращения 125…170 мин-1; глубиной внедрения инструмента 0,9…1,6 мм.
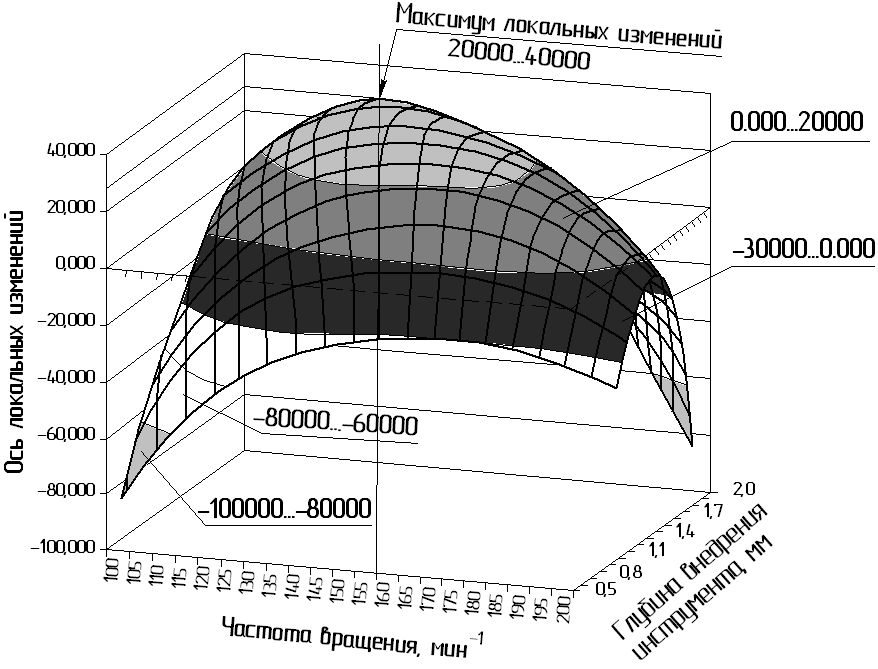
Рисунок 6 – Локальные изменения двухмерной системы режимов накатки
В общем виде функция цели, призванная обеспечить качество восстанавливаемой детали характеризуется конструктивными К, технологическими Т и экономическими факторами
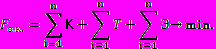
(14)
Функция цели по конструктивным факторам
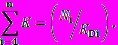
(15)
где Ni – годовой объем производства, зависит от программы восстановления Qi и конструктивной приспособленности оснастки и оборудования к высокой ритмичности производства i,

Функция цели по технологическим факторам обусловливается совершенством
принимаемых технологических решений, в той или иной мере обеспечивающих качество восстановления:
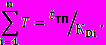
(16)
где tтп - технически обоснованная и наиболее приемлемая технология восстановления.
Функция цели по ресурсосберегающим факторам характеризуется экономией ресурсных составляющих на восстановление детали по принятой Тпр и сравниваемой Тср технологии.
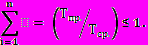
(17)
Для решения задачи определения деформируемых поверхностей и величины перемещаемого объема металла при формировании восстанавливаемого профиля шлицев проведены износные микрометражные исследования. Установлено, что величина максимального износа шлицев ступицы составляет 1,2 мм, а шлицевой втулки 1,6 мм. Это и является основным условием величины приращения профиля шлицев и требует исследования процессов формообразования, связанного с определением мест расположения перемещаемых объемов металла, а также с усилием деформации, обеспечивающим формирование восстанавливаемых поверхностей (рисунки 8, 9).
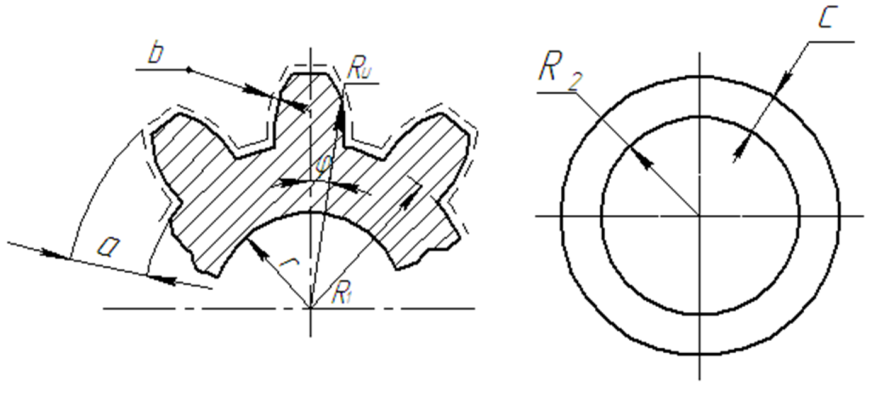
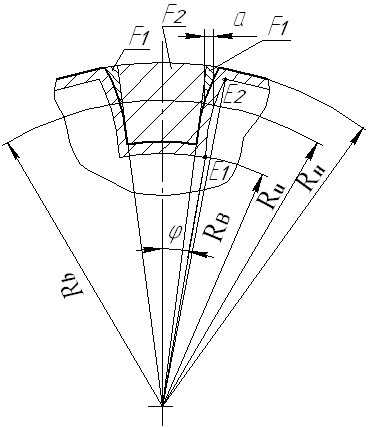
Рисунок 7 – Расчетная схема площади поперечного сечения шлица | Рисунок 8 – Расчетная схема необходимого объема металла для восстановления шлицевой ступицы |
Площадь шлица описывается равенством
(18)
Площадь F1 обусловливается размерами высоты перемещенного радиуса Rи и радиуса дна впадины Rв в изношенном состоянии с угловыми координатами Е1 и Е2.
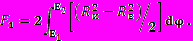
(19)
где φ – переменный угол.

Поперечное сечение шлицевой впадины



(21)
Переменный радиус Rи изношенного шлица

Переменный радиус Rв восстанавливаемого шлица

Нужное приращение площади поперечного сечения шлица

Исходя из полученного, объем металла, необходимый для формообразования шлица по длине l, равен

С целью создания универсальных технологий восстановления шлицевых деталей различных типоразмеров исследованию напряженно–деформированного состояния подвергались шесть схем формообразования.
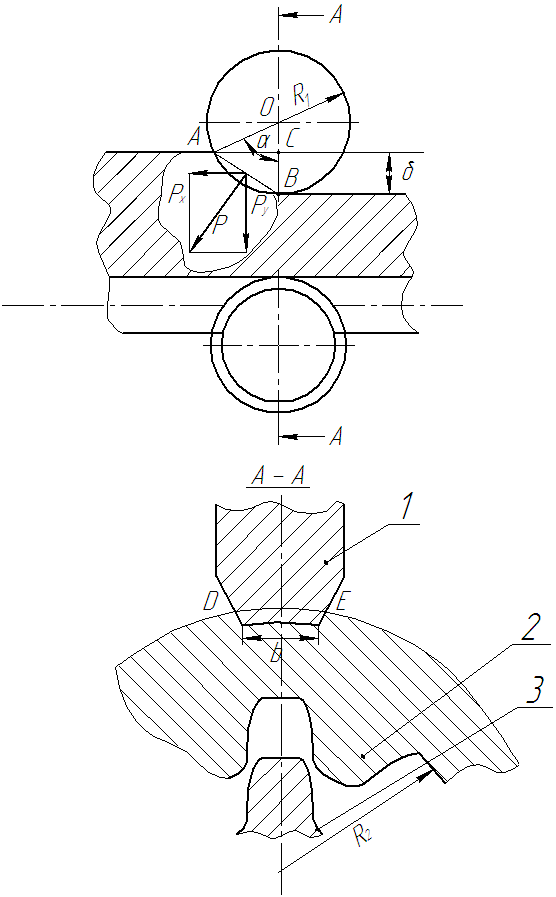
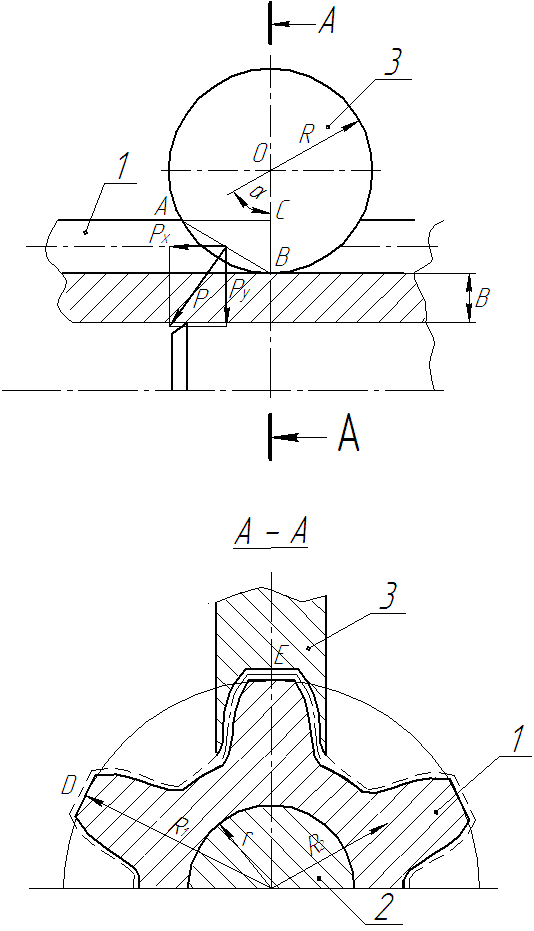
Рисунок 9 – Схема формообразования при продольной накатке и профилировании шлица 2 роликом 3 | Рисунок 10 – Схема формообразования раздачей полости пуансоном 2 и профилированием шлица 1 роликом 3 |
Усилие, необходимое для пластической деформации втулки по рассматриваемой схеме формообразования (рисунок 9), имеет вид

где
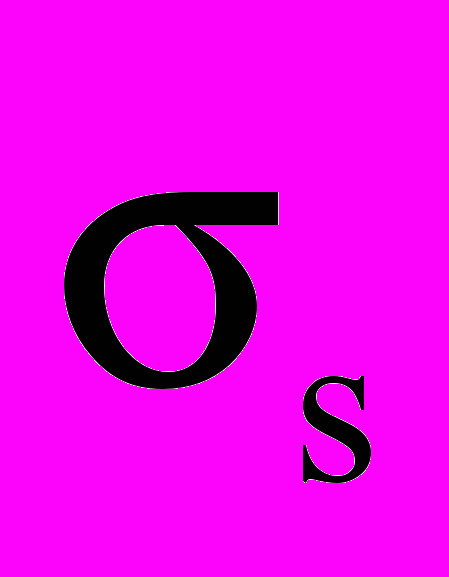
Усилие деформации по схеме на рисунке 10:
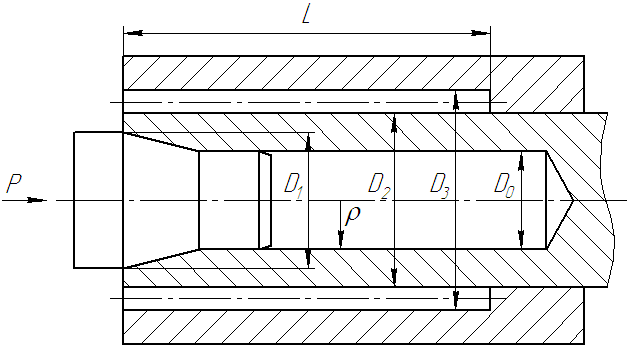

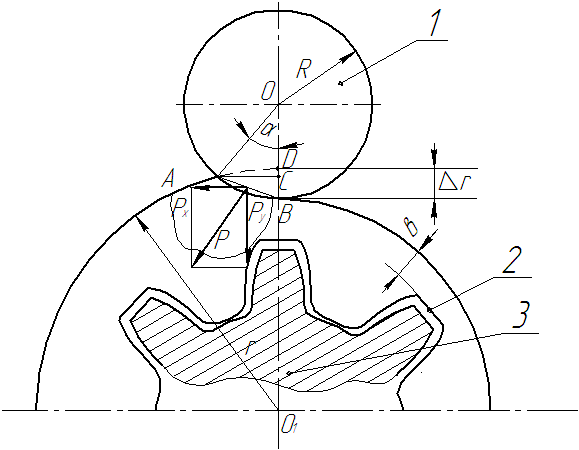
Рисунок 11 – Схема раздачи отверстия ступицы пуансоном в разъемном штампе | Рисунок 12 – Схема формообразования при поперечной накатке внешней поверхности деформирующим роликом 1 и профилировании внутреннего шлица 2 калибрующим пуансоном 3 |