«Чумак»
Вид материала | Сказка |
- Список використаних джерел "Чумак" выбрал новых двух, Коммерсантъ-украина, 18 марта,, 6.88kb.
- Учебная программа для высших учебных заведений по специальности 1-31 01 01 Биология, 218.03kb.
- Міністерство охорони здоров’я україни уніфікована методика з розробки клінічних настанов,, 3087.96kb.
Сказка для взрослых
о деде, бабе, производстве и MRP
(Читать только логистам!)
Александр Таранишин,
заместитель генерального директора ЗАО «Чумак»
Мы часто слышим об интегрированных информационных системах управления ресурсами предприятия класса ERP, основной частью которых является модуль MRP. Все говорят, что это хорошо. И модно. И полезно. А еще – что это дорого, и внедряется долго. Кроме того, можно внедрять-внедрять, да так и не внедрить – слишком сложно. Даже понять. Даже объяснить. Хотя объяснений много, какую книжку ни возьми – в каждой рассказывается, как правильно управлять ресурсами. Попробуем объяснить и мы. ДиЛ – журнал логистический, многие его читатели MRP пользуются. Другие решают, нужно ли это им и зачем. Надеемся, эта сказка поможет им разобраться.
Жили-были дед и баба. Жили, как и многие еще не очень старые украинские сельские пенсионеры – держали маленькое хозяйство (огород, коза, кролики и куры) и занимались частной предпринимательской деятельностью, связанной с производством напитков. Бабуля отвечала за сбыт, рекламу и финансы, а дед – за все основное, т.е. логистику и производство.
Получил дед от бабули прогноз продаж на следующий месяц: 20 литров продукта (с учетом необходимых PR-акций с участковым, семплинга перспективным потребителям и возможной убыли по причине дедушкиной жажды). Как положено, прежде, чем приступать к поставкам и производству, все тщательно спланировал:
«Сегодня, 15 сентября, в подвале есть 24 л. В этом месяце делать уже не буду (+0), может Мишка литруху вернет (+1), а продадим и выпьем где-то 15 л. Значит, на 1 октября останется литров 10. Маловато! Думаю, числа до 3–4 надо будет новую партию произвести. Решено: 4 октября! Но на 20 л, как бабуся говорит, а 30 – праздники приближаются, подзапастись необходимо. Что потребуется? Тара – бутылок и банок литров на сто наберется – не проблема. Дрова есть. А вот сиропа напитка нет. И выстаиваться он будет 6 дней. Значит, подготовить его нужно 28 сентября. Из 40 л сиропа выходит 6 л напитка. Чтобы получить 30 л, сиропа надо подготовить 200 л.
Едем дальше. Для каждых 40 л сиропа нужно 8 кг сахара и 700 г спиртовых дрожжей, остальное – вода. Т.е. для производства необходимо 40 кг сахара и 3,5 кг дрожжей. А сколько есть? Сахара – 18 кг, а дрожжей нет вовсе. Но дрожжи не проблема – они в магазине всегда есть, можно купить в день производства. Правда, продаются в пачках по 1 кг, поэтому придется брать 4 кг вместо 3,5. Ничего, не пропадут, попрошу бабульку пирожков напечь. А с сахаром сложнее – 40 кг на своем горбу не наносишься. Придется просить Мишку, он на молоковозе в райцентре каждый день бывает, и мешок с базара за бутылку привезет. В мешке, правда, не 40, а 50 кг, но и это не беда – в следующий раз использую. Единственное, что Мишку надо за два-три дня предупреждать. Значит, 25 сентября зайду и попрошу, чтобы купил. А деньги потом, дней через пять занесу – у него средства есть, в долг покупает, не отказывает».
На первый взгляд, не так-то просто разобраться, что, когда и сколько дед собрался делать и покупать. Но, в принципе, возможно, пока речь идет о десятке цифр и паре-тройке дат. А что, если продуктов на производстве не один, а двадцать, сто, пятьсот? И производиться они будут не на одном аппарате, а на двух, десяти, пятидесяти линиях и машинных центрах? И не из двух основных ингредиентов и одной тары, а из десятка, сотни или тысячи компонентов? Да еще каждый входящий материал будет иметь различные сроки поставки и размеры поставочных партий? А если стадий производства, кроме того, будет не две (6 дней для сиропа и потом один для самого напитка), а больше? Как тогда планировать производство и закупки?
Очевидно, в таком случае на помощь приходят не память, не интуиция и не большие запасы сырья, материалов и готовой продукции (на случай, если что-то упустишь или забудешь докупить/произвести), а четкий алгоритм расчета и компьютеры. Этот алгоритм называется MRP –Material Requirements Planning, планирование потребности в материалах, а его более продвинутая версия MRP II – Manufacturing Resource Planning, планирование ресурсов предприятия.
Компьютеризированная система MRP II предназначена для управления ресурсами производства. Она позволяет составлять планы-графики, объединяющие производство и поставки с продажами, и является инструментом совместного принятия решений представителями подразделений, отвечающих за эти три функции. Цель MRP II – подготовка основного производственного плана путем сбалансирования производственных мощностей, прогноза продаж, плана закупок и доставки материалов для обеспечения производства в экономически оптимальных партиях, необходимых для поддержки утвержденного уровня обслуживания клиентов.
Немного истории
Интересно, что у истоков этой программы стоял пусть не украинец (ведь все лучшее в мире придумали украинцы!), но славянин – американский чех Джозеф Орлицкий. Он работал в IBM и в 1961 г. успешно внедрил систему MRP в компании «Дж. Ай. Кейс», которая выпускала оборудование для сельского хозяйства. Эта программа доказала эффективность нового метода, который балансировал мощности, поставки и производство с продажами. Параллельно Оливер Вайт, Джон Харти и Джордж Плосл работали над программой, моделирующей деятельность предприятия, на «Стенли Уоркс». Они показали, насколько высокие запасы и несбалансированные производственные планы делали работу предприятия хаотичной и беспорядочной.
В 1966 г. эти талантливые люди встретились на конференции Американского общества управления производством и запасами (Americal Production and Inventory Control Society – APICS) и с тех пор начали систематизировать свой опыт, описывать использованный алгоритм и стандартизировать подходы. В 1967 г. Оливер Вайт и Джордж Плосл выдали книгу Production and Inventory Control: Principles and Techniques (Производство и управление запасами: принципы и подходы), где впервые описывается алгоритм MRP… аж на 16 страницах!
С этого момента авторы и APICS начали популяризировать MRP-подход, но все-таки больше были заняты разработкой и внедрением, чем описанием программы. Только в 1975 г. Джозеф Орлицкий выпустил более полную книгу «Material requirements planning: новый способ управления производством и запасами» (Joseph Orlicky, Material requirements planning: the new way of life in production and inventory management. McGraw-Hill, 1975. – 292 с.: ил). И тогда при поддержке APICS был объявлен «Крестовый поход за MRP», который принес позитивные результаты – управлять запасами на Западе стали лучше и экономней. Сама APICS сегодня, кстати, называется Ассоциацией операционного менеджмента и является одной из самых влиятельных организаций среди производственников и логистов (ссылка скрыта).
В Украине идея этого алгоритма известна еще с советских времен: с конца 70-х гг. Разрабатывались, так называемые, САУП (системы автоматизации и управления предприятием), где использовались многие из подходов MRP. Проблемой было лишь то, что не было установлено единого понимания этого процесса, он был расписан в десятках ГОСТов, статей и монографий. А с начала 90-х годов в страну стали заходить производители западных, а со временем и российских ERP систем со своими продуктами, появились инструкции, которые описывали логику и саму работу конкретных систем, а также их описания в интернете. Появились и украинские системы, но собственного, украинского «переосмысления» алгоритма нет. Да и нужно ли оно? Вполне можно пользоваться знаниями, которые накоплены в других странах, да перевести на украинский язык описание, сделанное специалистами APICS.
В доступной и простой форме описаны современные методы планирования производства, запасов и закупок в книгах российских авторов «Точно вовремя для России. Практика применения ERP-систем» (Питеркин С. В., Оладов Н. А., Исаев Д. В. М.: Альпина Паблишер, 2002. – 368 с.) и «Управление производством на базе стандарта MRP II» (Дмитрий Гаврилов. Санкт-Петербург: Питер-бук, 2002. – 260 с.). Дмитрия, по моему мнению, можем без преувеличения назвать гуру MRP на всем постсоветском пространстве.
Алгоритм MRP (обобщенно)
Схематически алгоритм MRP изображен на Рис. 1. Его логика приблизительно такова.
1. Берем прогноз продаж на период и данные по запасам – оцениваем потребность в производстве.
2. Сравниваем потребность с нашими возможностями: оцениваем агрегировано (совокупно) мощности производства (люди, машины, остальные ресурсы) и получаем план производства основного продукта.
Это просто: планирование продаж и составление основного производственного плана. По-английски эти модули называются Demand planning, Master production planning. А вот дальше – сложнее – собственно планирование материалов, или MRP (Material Requirements Planning):
3. Берем рецептуру (технологическую карту) (Bill of materials) продукта и определяем, сколько полуфабрикатов необходимо произвести и материалов закупить, чтобы получилось запланированное количество продукции. Сравниваем с наличным запасом – разница (с учетом неснижаемого остатка!) и дает нам чистую потребность в производстве и закупках.
Причем очень важно эту потребность «разместить» во времени: если для доставки какого-то ингредиента необходимо пять дней – заказать его именно за пять дней до того момента, как он должен появиться на складе. И еще: если нужно, скажем, 8 кг, а доставить могут только 20 кг (меньше не возят или тара не позволяет), следует рассчитывать именно на приход 20 кг. Этим, собственно, и занимается модуль MRP, который является сердцем большой системы.
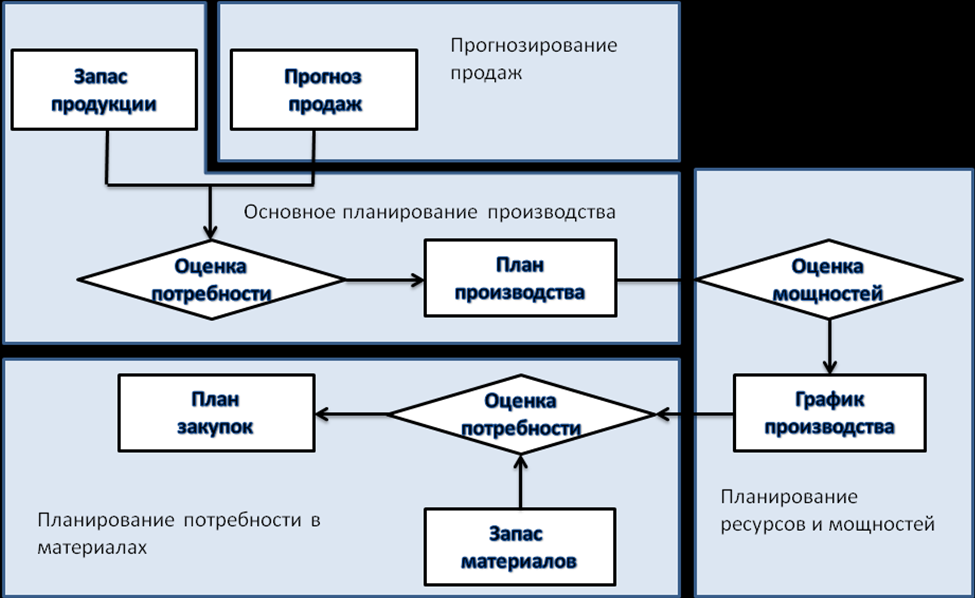
Рис. 1 Обобщенный алгоритм MRP
Кстати, наш дед этот алгоритм довольно четко и правильно прошел шаг за шагом. Правда, он пропустил пару важных моментов, которые вскоре, как мы увидим, создадут ему проблемы. А система MRP таких огрехов не допускает.
Давайте и мы вместе с дедом этот алгоритм пройдем.
Шаг за шагом
Первым пунктом у нас – самое главное – прогноз продаж.
Demand forecast (прогнозирование продаж) – это первый модуль системы, в который заносятся прогнозные продажи и реальные заказы клиентов. В зависимости от мощности и настроек системы, она является либо простой базой данных будущих продаж, или же сама, на основе истории продаж и определенных алгоритмов, предлагает прогноз, который потом подтверждается плановиком. Дедушка в нашем примере «прикинул» будущее потребление и определил его на уровне 30 бутылок
За этим следует, естественно, оценка существующих запасов и составление плана производства. Эти действия и осуществляются в следующем модуле –
Master Production planning (основное планирование производства). Он «переводит» план (прогноз) продаж и реальные заказы клиентов в общую потребность в производстве конечной продукции, принимая во внимание остатки на складах. В нашем случае запас на складе (тьфу ты, в погребе!) – 24 л. Запланированное производство – 0, приход – 1 бутылка (от Мишки), прогнозированное потребление – 12 л, остаток на начало периода – 10 л. При этом запасе дедушка считает необходимым начать новое производство. Если бы это был завод, то цех розлива получил бы следующий производственный заказ:
- Дата поступления напитка на склад (в погреб) – 4 октября
- Количество – 30 л
После этого нужно оценить, какие ресурсы необходимы для производства этого количества продукта. Это делается в модуле Resource planning (планирование ресурсов). Но сначала рассмотрим еще один важный подмодуль программы, о котором мы уже упоминали, –
Bill of materials (список рецептур, техкарт производства, описание продуктов), содержащий основные данные о продуктах, которые производятся. Он помогает определить, сколько и чего входит в производство. Без этих данных, понятно, планировать дальше нечего. В файле описываются сами продукты и необходимые для них материалы. Например, минимальная партия производства или поставки, срок производства и поставки (по-английски – lead time). Production routes (маршруты производства) описывают последовательность действий по производству каждого вида продукта, а также время прохождения каждого этапа. У деда все довольно просто: сначала кастрюли для закваски сиропа, а потом сам аппарат для производства напитка.
Все это – ресурсы, которыми оперирует следующий модуль MRP –
Resource planning (планирование ресурсов). Именно он определяет агрегированную потребность в материальных ресурсах для производства определенного планом количества продукции. В нашем случае необходимые материалы: дрова, бутылки в объеме 30 л с пробками и сироп в объеме 200 л. В свою очередь, производство сиропа занимает 6 дней, и чтобы он был готов 4 октября, начинать нужно 28 сентября. Значит, участок подготовки сиропа получил бы следующее производственное задание:
- Дата поступления сиропа в цех розлива – 4 октября
- Количество – 200 л
- Дата подготовки сиропа – 28 сентября.
Для производства оговоренного количества сиропа необходимо 40 кг сахара и 17,5 кг дрожжей, доставленных в день производства (28.09). Из-за различных сроков поставки необходимо выставить заказы на закупку несколько раньше. Поэтому, заказ на закупку должен выглядеть приблизительно, как в Табл. 1. Причем, обратите внимание, необходимо учитывать минимальную партию заказа, а также кратность заказа согласованному объему. В данном случае, повторяюсь, при необходимых 40 кг дед заказывает 50 кг сахара (кратно целому мешку, который готов привезти поставщик Мишка), и вместо 3,5 кг дрожжей – 4 кг, поскольку в продаже есть только пачки по 1 кг.
Табл. 1 Заказ на закупку материалов для производства
Материал | Дата поставки | Время поставки | Дата заказа | Размер заказа |
Сахар | 28.09 | 3 дня | 25.09 | 50 кг |
Дрожжи | 28.09 | 1 день | 27.09 | 4 кг |
Кстати, среди всего многообразия программ различных разработчиков некоторые считают только потребность в промышленных ресурсах, другие, как и в этом примере, рассчитывают также, чего, сколько и когда нужно закупить.
Цена ошибочки
А вот теперь мы подходим к моменту, который дед в своих расчетах упустил. Он посчитал, что все 30 л продукта выгонит 4 октября. Хорошо бы! Да только в его распоряжении всего один аппарат, который может произвести 6 л напитка за 8 ч. Да и сам дедушка это время выдерживает с трудом: необходимость постоянно тестировать качество производства приводит к преждевременной утомляемости. Поэтому, чтобы произвести весь объем, потребуется не один, а пять дней. Дальше все зависит от плановых сроков. Если к 4 октября нужно иметь все 30 л, то начинать надо 30 сентября. Но возможно, 4.10 достаточно выдать первую партию – тогда все производство будет закончено 9.10.
Такие расчеты в системе производит модуль
Сapacity planning (оценка мощностей), который осуществляет проверку возможности исполнения производственной программы, исходя из наличных мощностей. Нашего дедушку он заставит пересмотреть многое в своих первоначальных планах. В том числе все, что касается производства сиропа. Ведь он должен быть израсходован именно на шестой день выстаивания (плюс-минус день). Если пустить его в производство на пару суток позже или раньше, невозможно добиться тех качественных параметров, которыми так славен дедов продукт в селе и его окрестностях. Значит, и заказ на производство сиропа должен быть смещен с 28 сентября в соответствии с новым графиком розлива.
Представим, что дед решил все требуемые 30 л напитка поставить к 4 октября. Тогда он должен начать производство 30 сентября и ежедневно изготавливать по 6 л. Чтобы продукт получился качественный, сироп следует также готовить в течение пяти дней.
Поскольку для производства 6 л напитка необходимо 40 л сиропа, получается следующий график его приготовления: 24.09 – 40 л; 25.09 – еще 40 л; 26.09 – еще 40 л; 27.09 – еще 40 л; 28.09 – еще 40 л. Т.е. всего надо заквасить 200 л в пяти 40-литровых кастрюлях.
Но вот незадача: у нашего деда кастрюли под закваску не по 40, а по 50 л каждая. И их не 5, а 4! 200 л сделать можно, но немного в другом порядке:
- 24 сентября – заквасить 50 л; 30 сентября – 40 л будет использовано, а 10 л перейдут на 1 октября;
- 25 сентября – заквасить еще 50 л; 1 октября из них будет использовано 30 л (+10 л из первой кастрюли), а 20 л перейдут в производство 2 октября;
- 26 сентября – заквасить еще 50 л; 2 октября из них будет использовано 20 л (+20 л из кастрюли № 2), а 30 л останутся на 3 октября;
- 27 сентября – заквасить еще 50 л; 3 октября будет использовано 10 л (+30 л из кастрюли № 3), а 40 л уйдут в производство 4-го октября.
Непростая задачка! Причем не все MRP-системы решают ее в полном объеме. Некоторые из них имеют мощные модули оптимизации производственных планов, а другие просто выдают предупреждения (флаги/flags) о том, что наблюдается превышение производственных мощностей по данному продукту, линии или другому ресурсу. В нашем случае действует простая система, которая просто предупреждает, что есть узкие места, т.е. недостаток мощностей: производительность дедушки на аппарате (человеческие ресурсы) и емкость кастрюль (ограничения оборудования). А мы уж самостоятельно, путем проб и ошибок создаем такой план, который система воспримет без вывешивания флагов.
Скажете, такой подход примитивен? Тем не менее, даже самая простая система MRP с примитивным модулем CRP (Capacity Requirement Planning/агрегированной оценки мощностей) поможет плановику не допустить дефицита мощностей или их недогруза.
Окончательный план-график
Но теперь у деда появилась новая задача: нужно рассчитать поставки сахара и дрожжей в соответствии с новым графиком подготовки сиропа так, чтобы не покупать слишком рано и не прервать процесс производства дефицитом. В системе MRP это делает модуль
Materials requirements planning (планирование потребности в материалах). Он создает детализированный план производства и закупок на базе информации, которая рассчитана или получена другими модулями. Это сердце программы, которое и дает название всему пакету.
Необходимо отметить, что все модули системы работают взаимосвязано. Любое изменение, скажем, в основном производственном плане (конечного продукта) потянет за собой оценку мощностей в соответствующем модуле и выльется в изменение графиках производства компонентов. Поэтому очень тяжело провести четкую линию, где заканчивается один модуль и начинается другой. В нашем примере расчет производства сиропа описан в предыдущем параграфе, а на самом деле он производится в модуле планирования потребности в материалах, который выдает результаты двух типов:
- производственные задания/заказы (work orders) – на производство комплектующих, субкомпонентов, полуфабрикатов;
- закупочные задания/заказы – на закупку материалов, сырья, комплектующих и полуфабрикатов, которые предприятие не производит.
Дедушке, как мы помним, для производства необходимо 40 кг сахара и 3,5 кг дрожжей. Поставка может быть осуществлена кратно 50 кг сахара и 1 кг дрожжей. Какие проблемы? – Поставляем все это количество к 24 сентября, и не ломаем голову!
Дрожжей у нас нет в наличии (остаток 0 кг), и поставить их можно все сразу в день начала производства или по 1 кг каждый день. Скажете, зачем мучиться? В данном случае, может, и нет смысла. А представьте, что стоимость этих дрожжей не 5 грн. за 1 кг, а 400–500 грн., и покупать их надо не 1 кг в день, а, скажем, 700–800 т. Тогда, может, и стоит подвозить каждый день, а не создавать ненужный (пусть даже 2–3-дневный) запас. Это, кстати, немалые деньги – всего один день сокращения запасов позволяет компаниям экономить тысячи и даже миллионы долларов! Но как же сэкономить этот день?
Рассмотрим на примере сахара. Его у деда есть 18 кг в запасе. На 40 л сиропа нужно 8 кг. Поскольку мы уже определились, что будем делать по 50 л сиропа, то и сахара туда пойдет больше. Рассчитываем по пропорции: в 40 л – 8 кг, значит, на каждые 5 л – 1 кг. У нас кастрюля вмещает 50 л сиропа, поэтому класть в нее надо 10 кг сахара. Итого, расходовать его будем в таком порядке: 24.09 – 10 кг, 25.09 – 10 кг, 26.09 – 10 кг, 27.09 – 10 кг.
Допустим, наш дед – человек предусмотрительный и очень рачительный. Он не хочет покупать весь сахар сразу. А поскольку вынужден это сделать (меньше 50 кг Мишка не привезет), то он, как и плановик запасов любой толковой компании, захочет максимально отложить процесс закупки, чтобы не терять деньги на преждевременно закупленном запасе. Имея остаток 18 кг, он рассчитывает приблизительно так: «Могу попросить Мишку привезти мешок сахара за день до начала закваски, но смысла нет – мужик он надежный, точный, как часы. Так что скажу, чтобы доставил 25 сентября. После закваски 24-го останется 8 кг (10 кг уйдет в сироп), 2 кг будет не хватать, вот он как раз и подвезет. Но сказать ему надо за три дня, т.е. надо зайти к нему 22-го».
Вот теперь процесс планирования завершен. Его результаты – во второй части Табл. 2. Можно сравнить ее с первой частью и понять, насколько план-график изменился по сравнению с первоначальным.
Табл.2 Первоначальный и окончательный план-график закупок и производства
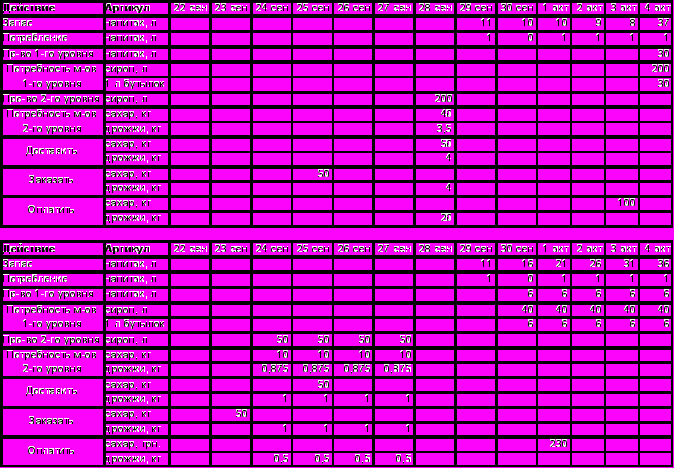
Ко второму варианту претензий нет – он выполним, не допускает дефицита как готовой продукции, так и материалов. Производственные мощности загружены полностью по своей полной производительности:
- дедушка – людские ресурсы;
- аппарат – линия производства конечного продукта;
- кастрюли – линия производства полуфабриката.
А вот к первоначальному плану, который дедушка составил пусть по правильному алгоритму, но в уме, без бумаги и карандаша, вопросов много. Во-первых, он нереалистичен: произвести 30 л напитка за один день (4 октября) невозможно. Если заквасить 200 л сиропа в один день и вовремя не использовать, большая его часть будет потеряна – перестояв два дня, сироп теряет свои свойства, и его необходимо сливать либо продавать на розлив, как менее прибыльный продукт. К тому же, заказав сахар 25 октября, дед рискует привезти его слишком поздно.
Альтернативы
Да, обновленный план более сложен в составлении. Но какая разумная альтернатива более точному графику производства? – То дефицит, то излишки, а то и списание!
Чтобы облегчить себе жизнь, можно:
- прибрести и установить систему класса MRP;
- попробовать написать простую программу, выполняющую функции MRP, самостоятельно, пока новая большая система закупается, настраивается и запускается в действие. В зависимости от потребностей и размеров бизнеса, это может занять от нескольких месяцев до нескольких лет.
Лучше, конечно, иметь полномасштабную систему. Но на первых порах, когда нет никакой, и планировать приходится либо на колене, либо используя систему точки перезаказа (когда пополнение запасов материалов, полуфабрикатов, комплектующих происходит после того, как запас на складе (складах) упал до определенного уровня, без учета будущего потребления), можно обойтись и «полумерами». К тому же, прописав весь алгоритм самостоятельно, сотрудники компании лучше поймут логику процесса и смогут точнее определить требования к новой, более мощной системе.
Тем более, что рынок предлагает широкий выбор систем, далеко не одинаковых по функционалу и возможностям. Ведь со времен появления алгоритма MRP прогресс не стоял на месте.
История развития: от MRP до ERP II
В частности, первые программы MRP не могли планировать платежи. Они осуществляли только расчет производственного плана и выдавали два вида заданий: на производство (work orders) и на закупку материалов и комплектующих (purchase orders). Причем не могли учитывать ограничения производства и поставок. В этом и была слабость систем MRP первого поколения.
Но со временем алгоритм совершенствовался и превратился в MRP II – систему планирования ресурсов производства, в которой есть модуль оценки мощностей (capacity requirements planning). Кроме того, появилась обратная связь (closed loop systems): если план невозможно было выполнить из-за отсутствия материалов или мощностей, график производства и закупок пересчитывался до тех пор, пока все конфликты не устранялись. Появились также модули, которые позволяли не только планировать, но и управлять закупками и производством.
Причем, все действия происходят в режиме реального времени, и система может пересчитывать планы в соответствии с поступившими заказами чуть ли не каждый час. Хотя из-за огромного объема данных полный пересчет запускается обычно раз в день, как правило, ночью.
Сегодня MRP II можно использовать не только для краткосрочного (оперативного), но и как часть стратегического планирования: модули планирования продаж и операций (sales and operations planning) и агрегированная оценка мощностей (Rough-cut capacity planning) позволяют осуществлять планирование на долгосрочную перспективу без лишней детализации.
Следующий уровень – системы класса ERP (Enterprise Resours Planning/Планирование ресурсов предприятия), позволяющие планировать ресурсы не только производства, но и всего предприятия. В них есть все: работа бухгалтерии, финансового отдела, отделов продаж, маркетинга, персонала, вся система закупок и логистики (собственно перемещения продукции и материалов между производствами и складами, в т.ч. удаленными).
Впрочем, это тоже не вершина пирамиды – сейчас на базе все того же старого доброго модуля расчета потребности в материалах MRP появились системы класса ERP II. Хотя их разработчики зачастую свои продукты ERP не считают – называют их системами синхронизированного планирования ресурсов (Customer Synchronized Resource Planning), совместного планирования и сотрудничества (Collaborative planning and replanishment system) и т.д. и т.п. Но суть от этого не меняется. Среди дополнительных возможностей таких систем – связь между различными предприятиями и возможность «общения» систем ERP разных предприятий, обмена данными в режиме реального времени, совместного планирования с целью оптимизации общей цепи поставок. Причем, одна компания и ее информационная система являются частью многих цепей поставок, с которыми они сотрудничают. Круто!
Дедушка компьютеризовался!
Впрочем, героям нашей сказки, как и подавляющему большинству малых и средних предприятий, все эти чудеса цивилизации не по плечу. Да и не по карману. Так что же – по-прежнему гадать на кофейной гуще или решать бесконечные примеры в столбик в блокнотике?
Не обязательно! Ведь наш дедушка живет в довольно продвинутом селе, у него есть компьютер и интернет. Конечно, написать программу MRP ему не по силам. Зато у деда есть внук, который работает логистом на большой фирме, занимается планированием и дружит с головой. Он и разработал для любимого деда маленькую программу в Excel, которая позволит ему планировать его производство. Плод его трудов можно найти на сайте ссылка скрыта
Подробное описание этой программы с инструкцией по использованию – в следующем номере