
Ресурсосберегающая технология и технические средства уборки и приготовления органического удобрения из навоза глубокой подстилки
Автореферат докторской диссертации по техническим наукам
Страницы: | 1 | 2 | 3 | |
Рассмотрим движение воздуха по трубе, приняв за положительное направление оси Ox направление вектора скорости движения нагнетаемого воздуха. Тогда уравнение неразрывности и уравнение Эйлера для нашего случая будет иметь вид:
аа (22)
(23)
Здесь F - внешняя массовая сила, действующая на входе трубы со стороны вентилятора, нагнетающего воздух в трубу. Эта сила (H.) равна:
аа (24)
Начальными условиями системы будут v0 - начальная скорость воздуха в трубе в момент времени аt=0а в точке с координатой аx=0;а v(x) - функция скорости воздуха в трубе по координатеа x (далее v).
Давление (Па) на входе в трубу при х=0 будет:
(25)
Давление на закрытом конце трубы можно оценить из следующего соображения:
Цвоздух движется к противоположному концу трубы со скоростью, изменяющейся за счет процессов диссипации энергии, в частности, трение о стенки трубы, вязкое трение.
аа (26)
В нашем случае, силы трения будут определяться через коэффициенты скоростей напряжений и деформаций в потоке:
,аа (27)
где а - средняя скорость движения потока газа по сечению трубы.
Имеем уравнение:
(28)
У стенки трубы давление воздуха будет определяться изменением импульса объема воздуха (м3/с.), дошедшего за время (с.) до конца трубы и отразившегося от глухой стенки. Искомый объем воздуха будет равен:
(29)
За это время произойдет изменение импульса (кг*м/с), равное:
(30)
Поэтому дополнительное давление (Па.), возникшее у стенки будет:
,аа (31)
где а - скорость газа у стенки, м/с.
Следовательно, граничное условие на давление (Н/м2) у закрытого конца трубы длиной абудет:
а (32) Соответственно, плотность газа в момент отражения его от стенки будет максимальной. Затем обратная волна воздуха пойдет против внешнего потока и, дойдя до начала трубы, снимет избыточное давление в начале трубы.
Распространение воздушного потока от вентилятора происходит со скоростью звука(м/с.):
аа (33)
Предполагается, что процесс адиабатический (скорости газа малы в сравнении со скоростью звука). Имеем:
а (34)
где Цпоказатель адиабаты.
Будем решать сначала уравнение (29) в линейном приближении.
Тогда, согласно формулама (22) и (23), имеем в стационарном случае:
а
(35)
Так как
,а (36)
Приравниваем выражения
и
а (37)
перепишем систему уравненийа (35) в виде:
а (38)
Исключаем из этих уравнений , находим:
илиаа
а (39)
После интегрирования получаем:
а (40)
Из граничных условий выводим константу интегрирования (м2/с2):
а (41)
Подставляя в (41) значение , окончательно получим:
аили
аа (42)
Обозначая безразмерную переменную , получаем профиль распределения скорости вдоль трубы:
а (43)
Уравнение (43), определяющее зависимость u(x), является трансцендентным относительно скорости v(x) и может быть решено численно при различных значениях x.
Решение уравнения (43) может быть аппроксимировано уравнением с учетом граничных условий(м/с):
а (44)
Перейдем теперь к нахождению зависимости диаметров отверстий (мм) от координат x вдоль трубы.
Из условия (20) имеем:
а или
а (45)
Отсюда:
илиаа
(46)
где афункция изменения диаметров отверстий при равномерном расходе воздуха, мм;
- диаметр воздуходувной трубы, мм;
профиль скорости вдоль трубы, м/с;
количество отверстий.
Преобразовав уравнение (46), получим выражение для определения диаметров воздуховодных отверстий (мм) в любой точке воздуходувной трубы при равномерном распределении воздушного потока.
аа (47)
Распределение диаметров отверстий вдоль трубы показано на рисунке 5, рассчитанное численно по уравнению (47).
В третьей главе Ц Программа и методики экспериментальных исследований Ц приведены задачи, общая и частная методики, приборы и оборудование экспериментальных исследований, обоснование факторов, влияющих на работу технических средств. Методика экспериментальных исследований разрабатывалась в соответствии с руководящими техническими материалами, в том числе с использованием методов математического планирования многофакторных экспериментов и обработки экспериментальных данных, из анализа теоретических и экспериментальных исследований, проведенных ранее. Обработка экспериментальных исследований осуществлялась на ЭВМ с помощью пакета компьютерных программ: Matcad 2000, Statistica 6, Microsoft Exсel, и другие.
Исследования физикоЦмеханических свойств навоза проводились на технологии группового содержание свиней в аннгараха с размерами ааметров на глубокой подстилке. (рисунок 5)
1 Цпоилка,2 - кормушка, 3Црулон сена, 4 Цглубокая подстилка, 5 - бетонированная площадка, 6 - ангар.
Рисунок 5. Технология содержания свиней на глубокой подстилке.
1
а
1
а2
а
Плотность навоза глубокой подстилки определяли следующим образом: вырезали кубики навоза глубокой подстилки (рисунок 7) на различной глубине, взвешивали на весах образцы, определяли объем образцов.
- кубик образца навоза;
- а- мерные линейки.
Рисунок 7. аОпытный образец кубика навоза глубокой подстилки.
Влияние угла заточки ножа на усилие резания навоза глубокой подстилки исследовали на разрывной машине марки ИР5047 - 50 - 03.
Для определения усилия резания на стойку 3 укладывали брикеты навоза глубокой подстилки 5, которые были заранее приготовлены, сечение брикетов было 300*300*300 мм, влажность 62% и плотность 980 кг/м3.(рисунок 8)а В процессе работы разрывной машины ИР 5047 - 50 - 03 верхняя платформа нижней скобы 1, на которой устанавливались сменные ножи 2 с разными углами заточки (рисунок 9),а и нижняя платформа верхней скобы 4, на которой устанавливалась стойка 3 с прорезью для выхода ножа из образца навоза, движутся друг относительно друга, вдоль оси стоек. Движение стоек является реверсивным. Как только нож начинает прорезать образец навоза, датчик снимает усилие, фиксируемое компьютером. Процесс резания ножом образца навоза, представлен на рисунке 10. Полученный график разбивается на три зоны.
1 - нижняя скоба с платформами; 2 - нож;3 - стойка с прорезью для выхода ножа;4 - верхняя скоба с платформами; аа5 - образец навоза глубокой подстилки.
Рисунок 8.а Рабочий узел разрывной машины ИР 5047 - 50 - 03.
Рисунок 9.а Конструкция ножей для резания навоза глубокой подстилки.
аа
Перваяа зона характеризует процесс сжатия и начало резания образца навоза. Вторая Ца процесс резания. Третья - зона снятия напряжения, нож выходит из образца навоза.
Связанная подстилка навоза требует больших усилий отрыва порций навоза погрузчиками циклического действия. При выгрузке навоза необходимо разрезать его в вертикальной и горизонтальной плоскостях. Для этого была разработана и изготовлена экспериментальная установка питателя - разрушителя навоза глубокой подстилки (рисунок 11)
1 - электродвигатель; 2 - червячный редуктор; 3 - станина; 4 - противорежущая пластина; 5 ножи; 6 - опоры; 7 - шнек.
Рисунок 11.а Экспериментальная установка питателя - разрушителя навоза глубокой подстилки.
Экспериментальная установка питателя - разрушителя состоит из станины 3, на которой установлены опоры 6, в которых крепится шнек 7; на валу шнека закреплены ножи 5, перед ножами шнека установлена противорежущая пластина 4. Вращение шнека питателя - разрушителя производится от электродвигателя 1 через червячный редуктор 2. аИсследования фракционного состава навоза глубокой подстилки проводили следующим образом. Из пласта навоза отобрали пробу 300 кг. Из 300 отобрали 30 кг затем эту смесь раскладывают тонким слоем от 0 до 50 мм, разложили на горизонтальную площадку для естественной сушки. Из этой порции отобрали частицы растительных остатков и произвели обмер. Результаты обработали и представили в виде графика рисунок 12.
Для определения длины измельченных частиц применяли классификатор измельченных грубых кормов, частицы длиной свыше 100 мм разбирались вручную. Распределенные по классам соломистые частицы взвешивали и вынчисляли их процентное содержание от общей массы пробы. Для просеивания частиц соломонавозной смеси использовали вибро-стол. На решета насыпалась проба просеивалась при частоте вибростола 30 Гц.аа
Рисунок 12. Фракционный состав навоза глубокой подстилки.
а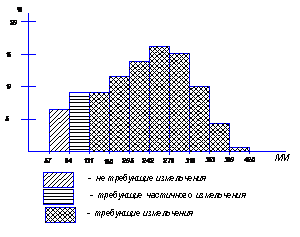
аДля проведения экспериментальных исследований по измельчению подстилочного навоза ва лаборатории кафедры МПиПСХП Мичуринского государственного аграрного университетаа была разработанаа и изготовлена экспериментальнаяа установка рисунок 13.
На данной установке исследовали производительность, степень измельчения, и удельную энергоемкостьа процесса измельчения.
1 - электродвигатель; 2 - кожух; 3 - ротор; 4 - лопатки; 5 - жолоб для подачи навоза.
Рисунока 13. Схема лабораторной установки питателя - измельчителя.
Исследования процесса распределения воздушного потока через воздуходувные отверстия проводили наа лабораторной установке (рисунок 14). Исследования проводили на стенде,а состоящем из вентилятора 1, соединенного с воздуховодными трубами 2, замеры проводили анемометром 3 и газовым счетчиком 5 СГБ G2,5 при длине воздуходувных труб 6м, диаметре воздуходувных отверстий 10мм и диаметре воздуходувных труб 100 мм.
1Цвентилятор,
2Цвоздуходувная труба,
3Цанемометр,
4Цвоздуховодное отверстие,
5 - газовый счетчик.
Рисунок 14.а Схема лабораторной установки для исследований процесса распределения воздушного потока в камере биоферментации.
Для изучения процесса биоферментации навоза глубокой подстилки в ЗАО Приволье была изготовлена экспериментальная установка, (рисунок 15) состоящая из камеры биоферментации 3, имеющей размеры 1,5*1,5*1,5, соединенной с вентиляторами 1, на которых установлены тэны 7. Измерение температурыа нагрева массы осуществлялось прибором МПРЦ51. Датчики 6 измерителя температуры помещались в компостируемый материал в 3Цх точках. Блок управления приводом вентилятора 5 осуществлял включение и выключение электродвигателя вентилятора по схеме автоматически, в зависимости от температуры в массе. Значения температуры задавалось путем программирования прибора МПРЦ51. Прибор управлял магнитным пускателем, на который запитаны вентиляторы, тэны подключены непосредственно к прибору через реле Р1 и Р2.
Схема работала следующим образом: в соответствии с заданным технологическим процессом прибор МПР51 программировался на срабатывание магнитного пускателя МП1 и реле Р1 и Р2, с помощью которых в автоматическом режиме происходит включение нагревателей и вентиляторов. Сигнала на прибор поступал с датчиков, которые располагались внутри камеры биоферментации.
В процессе работы температура в камере поддерживалась на заданном уровне системой автоматического управления (рисунок 15.а), путем включения и выключения вентиляторов и нагревателей. Температура и влажность в приборе МПРЦ51 измерялась с помощью термопреобразователей сопротивления. Использовались медные датчики ТСМ 100М (R0 = 100 Ом), интервал измерений температур Ц50 до 150 0С.
а)
аааа
аа
1Цнапорный вентилятор, 2Цвоздуходувная труба, 3Цкамера биоферментации, 4ЦМПРЦ51, 5Цблок управления, 6Цдатчики температур, 7Цтэн, 8Цизмерительный стенд,
9Цвоздуходувное отверстие.
Рисунок 15. Схема экспериментальной установки для аэрации навоза глубокой подстилки.
аКонцентрацияа кислорода в компостируемой массе определялась с помощью прибора COMBO480 на экспериментальной установке аэрации навоза глубокой подстилки (рисунок 16.б). Эксперимент проводили следующим образом: в процессе работы экспериментальной установки в компостируемую массу опускали щуп 2 на глубину 30,50,70,100 и 120 см от основания установки по схеме (рисунок 16.а) и включали прибор COMBO480.
После включения прибора активировали засасывающий насос на 20 секунд, по истечении заданного промежутка времени полученный результат записывается в журнал. Опыты проводились с 5Цти кратной повторностью. Обработка экспериментальных данных выполнялась при помощи пакета прикладных программ Matcad 2000, Statistica 6, Microsoft Exсel, Компас v9.0.
1ЦCOMBO480, 2Цщуп,
3Цсоединительный шланг,
4Цнавоз глубокой подстилки,
5 - камера аэратора.
Рисунок 16. Схема замеров содержания кислорода в компостируемой массе (а)а и экспериментальная установка аэрации навоза глубокой подстилки (б).
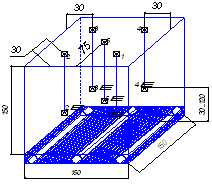
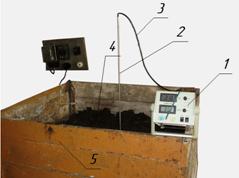
В четвертой главе - Результаты экспериментальныха исследований технического средства для измельчения,а разрушения соломонавозной смеси и распределения воздушного потока в воздуховодных трубах аэратора представлены результаты исследований производительностиа рабочих органов питателя - разрушителя от частоты вращения и поступательной скорости, результаты исследования распределения размеров и однородности частиц измельченной соломонавозной смеси в зависимости от частоты вращения барабана питателя - измельчителя, результаты исследования процессаа распределения воздушного потока в воздуховодных трубах аэратора.Результаты аэкспериментальных исследований, плотности навоза глубокой подстилки от времени содержания животных, влажности и высоты пласта представлены на рисунках 17,18.
Из графика (рисунок 17) видно, что плотность навоза глубокой подстилки с истечением времени увеличивается с 330кг/м3 до 980 кг/м3. Влажность навоза уменьшается по высоте слоя от 60% до 20% (рисунок 18). Следовательно, гравитационная влага навоза концентрируется в нижних слоях.
а
Рисунок 17.а Зависимость плотности навоза глубокой подстилки от времени содержания свиней.
аРисунок 18. Зависимость влажности навоза глубокой подстилки от высоты пласта.
ааНа рисунке 19,20 приведены результаты экспериментальных исследований зависимости коэффициентов трения покоя навоза по поверхностям, материал которых используется в машинах и оборудовании для подготовки органических удобрения при влажности 62%.
1 - деревянная, 2- хлопчатобумажная,
3- стальная.
Рисунок 19. аЗависимости
коэффициентов трения покоя
навоза
по поверхностям от
толщины слоя (W=62%).
а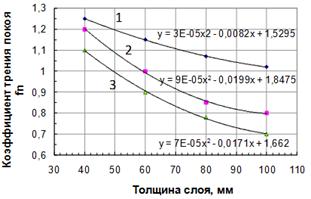
1 - резиновая, 2- прорезиненная,
3- бетонная
Рисунок 20.а Зависимости коэффициентов трения покоя навоза по поверхностям от толщины слоя (W=62%).
а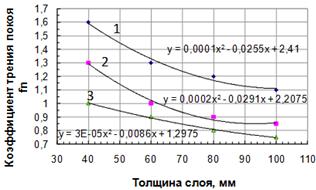
Графики показывают гиперболический характер изменения коэффициента трения навоза по поверхностям. аПри толщине слоя а80, 100 мм коэффициент трения покоя находится в пределах 0,8..1,2.Результаты экспериментальных исследованийаа по определению коэффициента внутреннего тренияа от удельного давления по поверхностям представлены на рисунке 21.
Из графика (рисунок 21) видно, что с увеличением давления коэффициенты внутреннего трения изменяются по гиперболическому закону. Для навоза глубокой подстилки коэффициент внутреннего трения уменьшается аот 0,75а до 0,29. Интенсивное снижение объясняется тем, что при повышении давления выделяется больше влаги, которая является смазкой.
Рисунок 21. Зависимость изменения коэффициентов внутреннего трения (fв) от удельного давления (Р, кПа).
а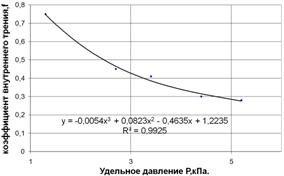
Результаты экспериментальных исследованийа по обоснованию параметров ножа при резании навоза глубокой подстилки представлены на рисунке 22.
Как видно из графика (рисунок 22) с увеличением угла заточки ножа сила резания уменьшается, достигает минимума при угле заточки а=450, затем начинает увеличиваться. Наиболее интенсивное увеличение силы резания происходит в интервале значений угла
а=60 - 900 . Это изменение объясняется образованием уплотненного ядра перед кромкой ножа, которое перемещается вместе с ним, увеличивая при этом рост ширины зоны влияния ножей на массу материала.
Ножи с ассиметричной заточкой имеют несколько меньшую силу резания по сравнению с симметричной заточкой, в среднем на 22% для ножей толщиной 4мм и на 7% для ножей толщиной в 8мм. С увеличением угла азаточкиаот 150 до 900 сила резания изменяется для ножей толщиной 4мм от 1020(Н) до 1350(Н) при симметричной заточке и от 750(Н) до 780(Н) при асимметричной. Минимальная сила резания навоза глубокой подстилки при угле заточки
=450, где сила резания Ррез анавоза, соответственно, равна 720(Н) с симметричной заточкой и 520(Н) с ассиметричной заточкой. Анализ полученных результатов экспериментальных исследований показал, что для резания навоза глубокой подстилки целесообразно применять ножи с асимметричной заточкойа и углом заточкиа 45
1 - b=4мм, 2 - b=8мм
Рисунок 22. Зависимость усилия резания навоза глубокой подстилки от угла заточки ножа (а) с симметричной и (б) асимметричной заточкой.
а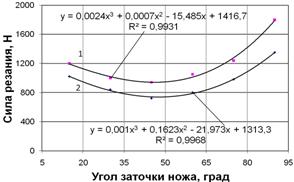
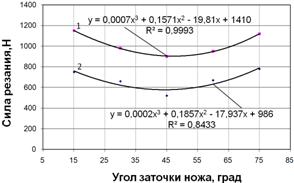
Результаты экспериментальных исследований производительностиа рабочих органов питателя разрушителя от частоты вращения и поступательной скоростиа шнека представлены на рисунках 23,24.
Рисунок 23.а Зависимость производительности от оборотов
питателя-разрушителя.
а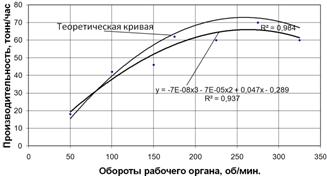
Рисунок 24.а Зависимость производительности от поступательной скорости.
а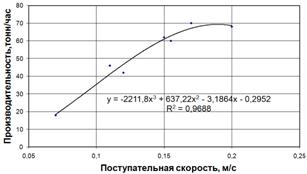
На графике (рисунок 22) видно, что производительность повышается с увеличением оборотов, достигая экстремума 250 об/мин. Затем наблюдается спад. Это уменьшение связано с тем, чтоа шнек при увеличении оборотов (300 об/мин) не успевает наполняться, следовательно, производительность снижается. Оптимальное число оборотов рабочего органа питателя - разрушителя находится в интервале от 150 об/мин до 250 об/мин. При этих значениях производительность составляет 52 - 68 тон в час. Из графика (рисунок 23) видно, что рост производительности наблюдается до значения скорости в 0,195 м/с, затем происходит ее снижение. Это падение можно объяснить тем, что рабочий орган получает большую подачу массы навоза, которую может переместить.
Оптимальную поступательную скорость шнека принимаем в интервале от 0,14 до 0,195 м/сек. При этих значениях скорости производительность достигает значение от 52 до 68 тонн в час.
Для получения математической зависимости влияния выбранных факторов (таблица 1) на процесс резания был реализован некомнпозиционный план второго порядка Бокса - Бенкина в виде полинома второй степени.
Таблица 1 - Факторы, принятые для исследований
Факторы и их обозначения |
Уровни варьирования |
Интервал варьирования |
||
нижний ( - 1) |
базовый (0) |
верхний (+1) |
||
Х1 - влажность, %. |
40 |
50 |
60 |
10 |
Х2а - плотность, кг/м3. |
700 |
850 |
1000 |
150 |
Х3а Ца обороты, об/мин. |
150 |
200 |
250 |
50 |
аВ результате обработки опытных данных получено уравнение.
Y=9,718 - 0,1729x1+0,004x12 - 0,0308x2+0,0001x22+0,0544x3+0.0002x32 - 0.0004x1x2+0.0008x1x3Ц0.0002x2x3а а аа(48)
Таблица 2 Ца Оптимальные значения факторов
Кодовое обозначение |
Наименование факторов |
Оптимальные значения |
X1 |
Влажность, % |
44,016 |
X2 |
Плотность, кг/м3 |
936 |
X3 |
Обороты, об./мин. |
206.031 |
а При подстановке в уравнение (48) найденных оптимальных факторов (таблица 2) определили функцию выхода Ца производительность питателя разрушителя, которая составила 65т/ч. Это говорит о том, что центр поверхности фигуры находится в области априорно выбранного центра эксперимента.
а
Рисунок 25.а Зависимости производительности питателя - разрушителя от влажности, плотности навоза аи оборотов шнека.
Производительность измельчающего аппарата зависита от угла установки противорежущей пластины, количества лопаток, установленных на измельчающем аппарате, и скорости вращения лопастного метателя.
1) W=58%; z=2; ?=17;
2)W=58%; z=6; ?=17.
Рисунок 26. Зависимость производительности измельчителя
навоза аот числа оборотов крылача.
Из графиков (рисунок 26) авидно, что пропускная способность меняется в зависимости от количества установленных лопаток. С аувеличением числа лопаток с 2 до шести производительность возрастает 0,227до 0,338 т/ч, соответственно. При увеличении числа оборотов крылача также происходит увеличение пропускной способности измельчителя. При двух лопатках и угле установки ?=170 производительность возрастает от 0,109 до 0,227 т/ч. Приа шести лопатках и угле установке противорежущей пластины ?=170а производительность возрастает с 0,196 до 0,338 т/ч.
Из графиков (рисунок 27) видно, что производительность измельчителя сильно изменяется в зависимости от угла установки противорежущей пластины. Это связано с тем, что противорежущая пластина перекрывает зону подачи навоза.а
1) W=47%; z=2; ?=1050;
2) W=47%; z=2; ?=170;
Рисунок 27. Зависимость производительности аизмельчителя навоза
от оборотов крылача.
1) W=76%; z=2; ?=1050;
2) W=76%; z=4; ?=1050;
3) W=76%; z=6; ?=1050.
Рисунока 28. Зависимость потребляемой мощности от оборотова крылача.
Из графикаа видно, что потребляемая мощность зависит от угла установки противорежущей пластины (рисунок 28). При уменьшении угла установки противорежущей пластины происходит увеличение потребляемой мощности. т.к в процессе измельчения нет резания, а происходит трепание соломонавозной смеси. а
На рисунке 29,30 представлены результаты экспериментальных исследований по определению расхода воздуха по длине трубы с одинаковыми диаметрами отверстий. Эксперименты проводили при длине воздуходувной трубы 6м, диаметре воздуходувной трубы 100 мм и диаметре воздуходувных отверстий 10мм.
Рисунок 29. аЗависимости расхода воздуха по длине аэрационной трубы при установке одной трубы (а)а и при установке трех труб (б).
а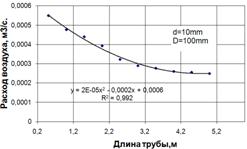
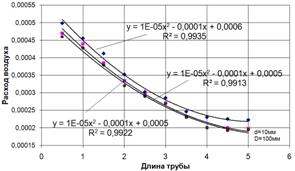
Анализ графической зависимости, представленной на рисунке 29.а, показывает, что при увеличении расстояния от вентилятора расход воздуха из воздуходувных отверстийа снижаетсяа с 0,00052 до 0,00024 м3/с на 52%, аа при установке трех воздуховодных труб (рисунок 29.б) происходит потеря расхода воздуха по отношению к центральной трубе с 0,0004998 до 0,00023605 м3/саа иа боковым трубам са 0,0004457 до 0,0001598 м3/с в начале и в конце соответственно.
Следовательно, асредние потери напора между центральной и боковыми воздуходувными трубами составляют 10%.
Рисунок 30. Зависимости расхода воздуха по длине аэрационной трубы от производительности вентилятора (а) и от диаметра воздуховодной трубы (б).
а1 - W=0,7м3/с.;
2 - W=1,1м3/с;
3- W=0,5 м3/с.
а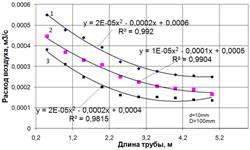
1 - d=80мм;
2 - d= 60мм;
3 - d = 40мм.
а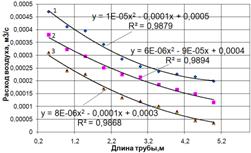
Страницы: | 1 | 2 | 3 | |
