Производство сфероидального чугуна
Вид материала | Документы |
- Производство литейного чугуна и передельного чугуна, 96.28kb.
- Современное металлургическое производство чугуна и стали, и его продукция, 133.82kb.
- 8 Производство чугуна, 108.71kb.
- Справочник работ и профессий рабочих Выпуск 48 Разделы: "Общие профессии производств, 10592.39kb.
- Типовая форма бизнес-плана, 100.9kb.
- Особенности плазменной закалки крупногабаритных деталей из чугуна Батрак В. В., Веремейчик, 55.51kb.
- Физико-технологические основы новых способов термической обработки высокопрочного чугуна, 72.96kb.
- Металлургический комплекс. Черная металлургия. Производство чугуна и стали. Влияние, 159.02kb.
- Единый тарифно-квалификационный справочник работ и профессий рабочих выпуск, 4862.42kb.
- Справочник работ и профессий рабочих Выпуск 63 Разделы: "Общие профессии производства, 6962.99kb.
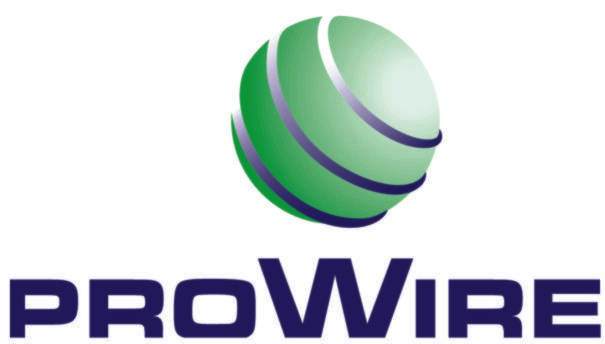
ПРОИЗВОДСТВО
СФЕРОИДАЛЬНОГО ЧУГУНА
С ИСПОЛЬЗОВАНИЕМ
ТЕХНОЛОГИИ
“ПОРОШКОВОЙ ПРОВОЛОКИ”
Представлено: PROGELTA s.r.l. ITALY написано со слов Dieter Gumbinger (ATLANTA USA)
Основные фазы при производстве сфероидального чугуна
ОПРЕДЕЛЕНИЕ ШИХТЫ

В

ЗАГРУЗКА В ПЕЧЬ





Десульфурация Десульфурация и сфероидизация
с


Цементация

Выдержка, коррекция анализов

Сфероидизация



РАЗЛИВКА
Процессы обработки с использованием магния
Используются различные типы процессов, в ходе которых применяются разнообразные виды сплавов. Однако около 90% мирового производства сфероидального чугуна использует следующие 7 процессов.
Большая часть сплавов предназначена для особых процессов, методов добавления присадок и индивидуальных требований того или иного процесса.
Каждый метод имеет свои положительные аспекты (ЗА) и отрицательные (ПРОТИВ).
- ^ OVERPOUR, SANDWICH и TUNDISH.
Система SANDWICH требует, чтобы ферросплав (обычно FeSiMg 5%) помещался в карман или выемку специального крытого ковша и имел в своем составе различные материалы для замедления реакции между ферросплавом и чугуном для обеспечения максимального эффекта полезной производительности магния.
Укрывающими материалами являются: сталь, карбид кальция или FeSi.
^ ЗА: ПРОТИВ:
- никакого ограничения по весу - дымовые газы выпускаются внутрь
помещения литейного цеха
- средняя сила реакции - обработка должна производиться рядом с печью
- смесь может иметь различную фракцию - ограниченное допустимое процентное содержание серы от базового чугуна
- повышение % Si
- Система TUNDISH COVER.
^ ЗА: ПРОТИВ:
- снижение вспышек и дымовых газов - ограничение по весу
- хорошая эффективность Mg - повышенные затраты на техобслуживание из-за шлака, образующегося внутри емкостей
- больший выбор ферросплавов - обработка должна выполняться перед печью
- грязный чугун по причине частиц шлака, плавающих в металле
- ^ FLOWTRET или SIGMAT (поток, проходящий через систему)
Специально разработанная емкость (запатентованная) устанавливается перед печью. Ферросплав добавляется в емкость и когда чугун выпускается в емкость контролируемым потоком, происходит его непосредственная обработка.
^ ЗА: ПРОТИВ:
- низкое образование дымовых газов во время - ограниченная зона обработки
обработки - требуемый сплав фракции 2-12 мм
- ограничение % допустимого базового содержания S
- грязный чугун по причине частиц шлака, плавающих в металле
- повышенное потребление ферросплавов по причине низкого % содержания S в базовом чугуне
- Процесс INMOLD
Сфероидизация и модифицирование выполняются во внутренней реакционной камере опоки.
^ ЗА: ПРОТИВ:
- отсутствие вспышек и дымовых газов - ограничение по весу
- низкое количество требуемого ферросплава - сильное ограничение базовой S (< 0,01%)
- модифицирующий эффект - фракция ферросплава 0,5 – 4 мм с содержанием более 3% фракции с размерами меньше 1 мм
- низкий выход продукции из модельной плиты из-за применения реакционной камеры
- на каждую отливку требуется выполнять контроль сфер (глобул)
- критическая скорость разливки (система подачи)
- Процесс с использованием чистого магния: КОНВЕРТЕР
^ ЗА: ПРОТИВ:
- отсутствие ограничений по % содержания - сложное оборудование для обработки базовой S и требуются повышенные затраты на
техобслуживание
- нет добавления кремния - высокая стоимость конвертера
- относительно чистый чугун - очень бурное протекание реакции
- обрабатываемый чугун очень «жесткий» и требует сильного пост-модифицирования
- Процесс ПОГРУЖЕНИЯ
Ферросплав или кусок Mg в оболочке устанавливаются во фланец и погружаются в расплавленный чугун.
^ ЗА: ПРОТИВ:
- отсутствие ограничений по % содержания - ограничение по весу обрабатываемого
базовой S металла
- средняя присадка Si - добавляется стоимость станции обработки
- чистый чугун - дополнительные манипуляции с металлом и добавление стоимости фланца, используемого для погружения
- бурная реакция
- Процесс с использованием ПРОВОЛОКИ С ПОРОШКОВЫМ НАПОЛНИТЕЛЕМ
^ ЗА: ПРОТИВ:
- вес обрабатываемого металла от 150 - стоимость проволоки
до 15000 кг
- никаких ограничений по размещению - стоимость станции и трайб-аппаратов
станции обработки
- % базовой S до 0,1% - бурная реакция, если используется проволока с чистым Mg (только в особых случаях)
- низкое количество используемого ферросплава
- легкий и точный контроль подаваемой
проволоки
- жесткий контроль над конечным Mg
- чистый чугун
- отсутствие дымовых газов и вспышек в
помещении литейного цеха
- процесс может быть полностью автомати-
зирован и может включаться нажатием одной
лишь кнопки запуска
OVERPOUR и SANDWICH
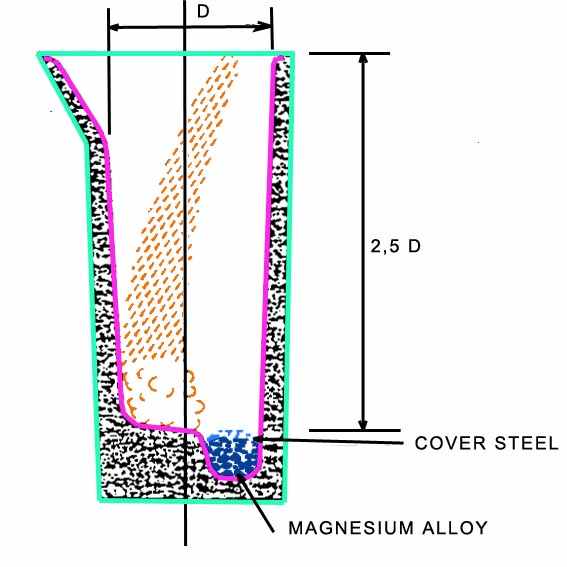
Покрывающая сталь
Сплав магния
^ TUNDISH COVER
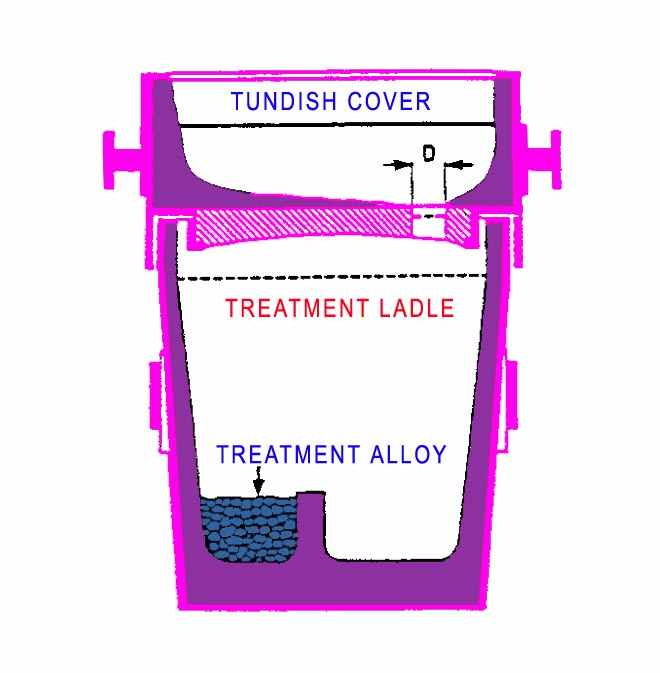
ОБРАБАТЫВАЮЩИЙ КОВШ
Сплав для обработки
КРЫШКА
FLOWTRET
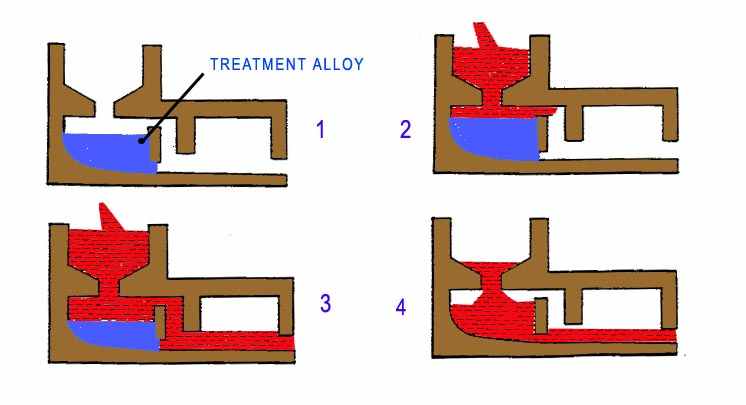
Сплав для обработки
INMOLD
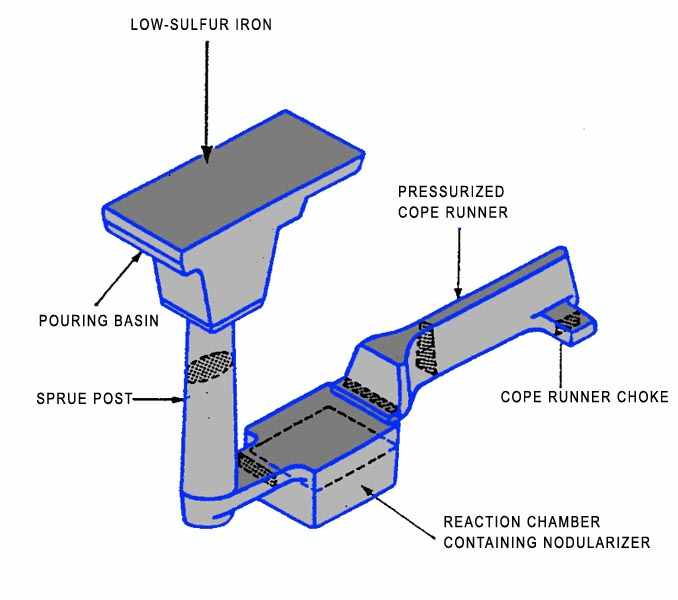
^ МАЛОСЕРНИСТЫЙ ЧУГУН
ВЕРХНЯЯ ОПОКА ЛИТНИКА ПОД ДАВЛЕНИЕМ
ШИБЕР ВЕРХНЕЙ ОПОКИ ЛИТНИКА
ЛИТНИКОВАЯ ЧАША
ВЕРТИКАЛЬНЫЙ ЛИТНИК
^ РЕАКЦИОННАЯ КАМЕРА, СОДЕРЖАЩАЯ МОДИФИКАТОР
КОНВЕРТЕР
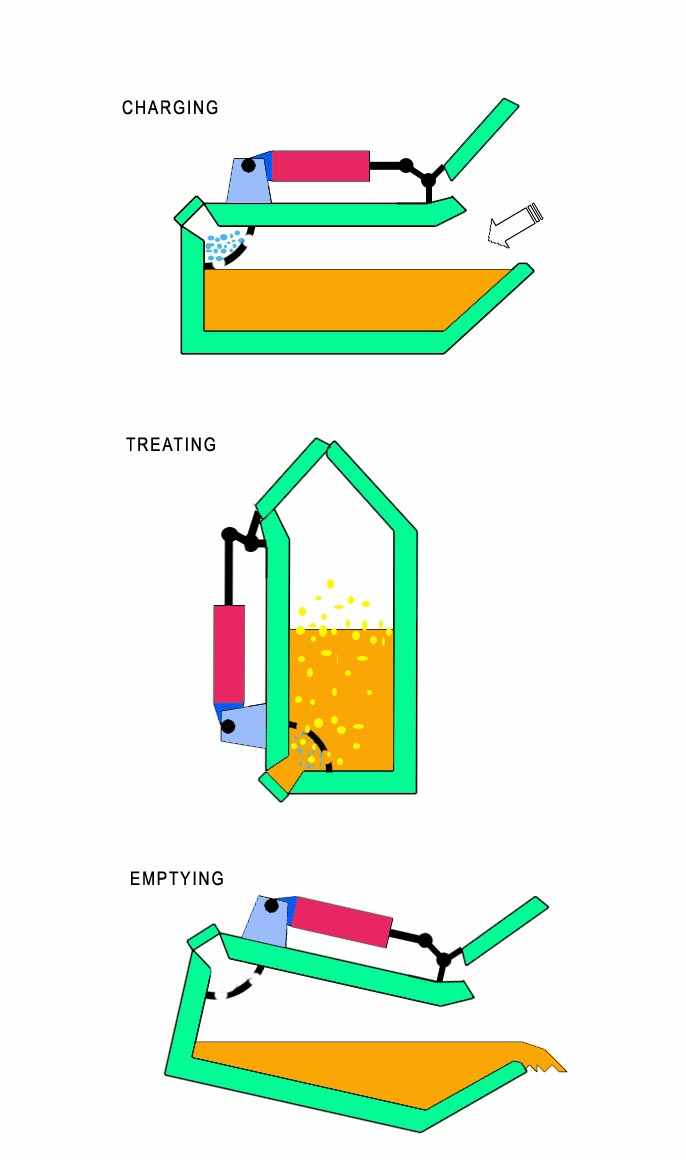
ЗАГРУЗКА
ОБРАБОТКА
ОПОРОЖНЕНИЕ
ПОГРУЖЕНИЕ
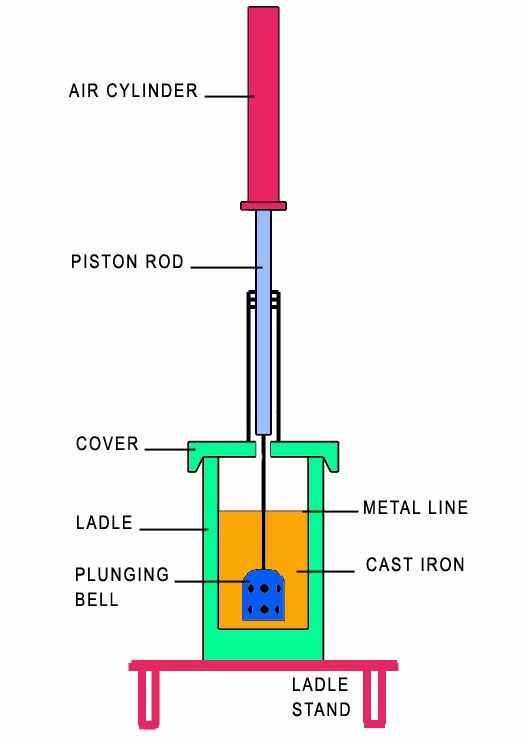
ПНЕВМОЦИЛИНДР
^ ПОРШНЕВОЙ ШТОК
КРЫШКА
КОВШ
ПОГРУЖАЕМЫЙ КОЛОКОЛ
МЕТАЛЛИЧЕСКОЕ ЗЕРКАЛО
ЧУГУН
ОПОРА КОВША
^
РАЗВИТИЕ ПОРОШКОВОЙ ПРОВОЛОКИ ДЛЯ ОБРАБОТКИ СФЕРОИДАЛЬНОГО ЧУГУНА
В 1982 году в Европе был введен новый процесс для обработки сфероидального чугуна с помощью магния.
Данный процесс использует порошковую проволоку с металлическими наполнителями для обработки расплавленного чугуна.
В течение первых лет проволока с наполнителем имела диаметр 5 и 9 мм и была заполнена порошковым магнием и небольшим количеством редкоземельных элементов. Одной из первых отливок, произведенных с помощью этого нового процесса, стали выпускные коллекторы из сфероидального и вермикулярного чугуна.
С 1984 года стало очевидным, что проволока, заполненная чистым магниевым порошком, имела различные недостатки, которые наблюдаются и сегодня и выражаются в быстром затухании обрабатываемого чугуна и необходимости в сильном пост-модифицировании, поскольку реакция при использовании проволоки протекает очень бурно и требует специально разработанного оборудования, а также проволоку с диаметром максимум 9 мм для обеспечения безопасности.
Для улучшения ситуации были произведены особые, более дорогие, сплавы, которые при их смешивании со стандартными чистыми сплавами, используются в качестве материалов для заполнения проволоки с диаметром до 13 мм. С недавнего времени начала развиваться более точная технология.
В настоящее время предлагаются различные комбинации сложных ферросплавов с узким диапазоном применяемых элементов, разрабатываемых для каждого отдельного применения, с учетом специфических требований литейных производств, в ходе которого в чугун добавляются необходимые элементы для изготовления отливок с требуемыми характеристиками.
^
ЧТО ТАКОЕ ПРОВОЛОКА С ПОРОШКОВЫМ НАПОЛНИТЕЛЕМ
Проволока с порошковым наполнителем – это «трубка» обычно с диаметром 9 или 13 мм, в которой находятся смеси присадок, необходимых для особых технологических процессов.
Данные смеси могут быть в виде порошка или гранул с внешней оболочкой, выполненной из стальной полосы, свернутой в форму трубки.
^ СТАЛЬНАЯ ОБОЛОЧКА
ПОРШКОВАЯ СМЕСЬ
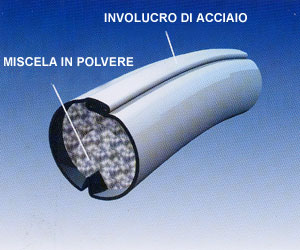
Такая трубка сворачивается в бобины.
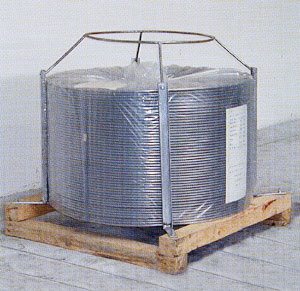
^
ТЕХНИЧЕСКИЕ ПРЕИМУЩЕСТВА ИСПОЛЬЗОВАНИЯ ПРОВОЛОКИ С ПОРОШКОВЫМ НАПОЛНИТЕЛЕМ
Ниже приводится список технических преимуществ, которые достигаются путем сфероидизации чугуна, с применением метода “Cored wire”
- Обрабатываемый вес металла от 300 до 30.000 кг.
- Нет ограничений по установке станции обработки: она может быть установлена как можно ближе к разливочной линии для минимизации рассеивания Mg.
- Обрабатываемый чугун может иметь базовую серу выше 0,09%: в этом случае можно спокойно обрабатывать как расплавленный чугун в вагранковой печи, так и первый чугун, произведенный после кампании серого чугуна.
- Точный и легкий способ контроля количества добавляемой проволоки.
- Точный контроль конечного Mg.
- Отсутствие дымовых газов и вспышек внутри литейного цеха.
- Процесс может быть полностью автоматизирован. Операции с металлом не могут быть подвержены ошибкам или невнимательности со стороны человека.
- Низкое количество добавляемого сплава, что приводит к уменьшению образования шлака, более низкой потери температуры и меньшему количеству добавляемого Si по сравнению с традиционными методами обработки.
- Сфероидизирующая и модифицирующая обработка может быть сделана в том же ковше, но за отдельные операции.
- Высокая химическая активность, например, по сравнению с методом INMOLD, гарантирует «чистый чугун», поскольку очень быстро на поверхность выводятся все дроссы и шлаки, которые впоследствии могут быть легко удалены. Помимо этого, бурность реакции способствует однородности графитизации.
^ КАКИЕ ЛИТЕЙНЫЕ ПРОИЗВОДСТВА ИМЕЮТ ПРЕИМУЩЕСТВА ОТ ПРИМЕНЕНИЯ ТЕХНОЛОГИИ ПРОВОЛОКИ С ПОРОШКОВЫМ НАПОЛНИТЕЛЕМ?
- Те литейные производства, которые находятся в постоянном поиске улучшений собственного производства сфероидального чугуна.
- Те литейные производства, которые имеют проблемы с рассеиванием и температурой по причине большой продолжительности по времени манипуляций, производимых с обработанным чугуном.
- Все литейные производства любого размера, имеющие проблемы с дымовыми газами.
- Литейные производства, которые производят серый и сфероидальный чугун из одного и того же базового чугуна (высокое содержание S), и те, которые плавят чугун с помощью вагранковых печей, поскольку у них есть возможность выполнять десульфурацию и сфероидизацию в течение одной-единственной простой операции.
- Литейные производства, которые стремятся удалить шлак от карбида кальция, остающегося от процесса десульфурации.
- Литейные производства, у которых имеется высокий показатель конечного Si, а, следовательно, проблемы с собственными перерабатываемыми материалами.
- Литейные производства, которые производят сфероидальный чугун, количество которого постоянно варьируется.
- Литейные производства, которые хотели бы производить вермикулярный чугун.
- Литейные производства, которые желали бы иметь полностью автоматизированный, подконтрольный и оптимизированный процесс добавления ферросплавов с документированием всех параметров технологического процесса.
^ СТАНЦИЯ ОБРАБОТКИ С ИСПОЛЬЗОВАНИЕМ ПРОВОЛОКИ С ПОРОШКОВЫМ НАПОЛНИТЕЛЕМ “CORED WIRE”
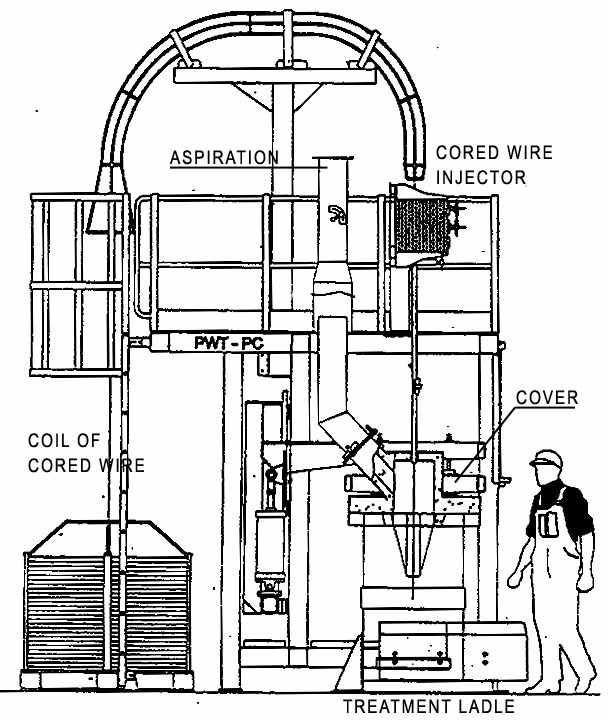
АСПИРАЦИЯ
ТРАЙБ-АППАРАТ ПОДАЧИ ПРОВОЛОКИ
КРЫШКА
БОБИНА С ПОРОШКОВОЙ ПРОВОЛОКОЙ
КОВШ ДЛЯ ОБРАБОТКИ МЕТАЛЛА
^
ЧИСТЫЙ ЧУГУН
ОБЩИЕ СВЕДЕНИЯ
При производстве сфероидального чугуна было доказано, что именно при добавлении сплавов с содержанием Mg и модификаторов после выпуска чугуна из печи, образуется до 95% примесей в отливках. Таким образом, очень важно, в особенности у отливок малой толщины, производить обработку с использованием наиболее эффективных сплавов Mg с наиболее эффективными модификаторами и с наиболее низким количеством присадок.
^
ОБРАБОТКА с использованием Mg
Используется такой метод обработки, при котором производится «очищающий эффект» чугуна за счет высокого содержания Mg в ферросплаве. Бурное образование испарений из-за высокого содержания Mg удалит примеси, которые в ином случае остались бы на долгое время плавать в чугуне. Это одна из причин, по которой происходит в литейном производстве быстрое развитие технологии обработки металлов с использованием проволоки с порошковым наполнителем.
Наиболее подходящие виды проволоки с порошковым наполнителем содержат 25-40% Mg вместе с Ca. Помимо этого также и редкоземельные материалы дозируются определенным образом для каждого отдельного технологического процесса.
Во многих случаях рекомендуется добавление в чугун химических продуктов, которые увеличивают текучесть чугуна (например, PROFLUX), которые облегчают перемещение к поверхности зеркала металла различных примесей, которые после этого могут быть легко удалены во время выполнения операций по шлакоудалению. Кроме того, характеристики заполнения форм будут улучшены, а работа фильтров (если он есть) будет облегчена за счет высокой текучести чугуна.
^ B. МОДИФИЦИРОВАНИЕ
Основным правилом в данном случае является то, что чем меньше количество добавляемого модификатора, тем чище будет чугун.
Степень окисленности модификатора в тот момент, когда данный модификатор добавляется в металл, имеет огромное значение.
Самым «чистым решением» будет являться метод производства проволоки с добавлением в нее модификатора в качестве наполнителя.
Модифицирующая проволока в особенности эффективна, когда используется печь/ковш разливки в качестве пост-модифицирования в емкости для разливки, куда подается проволока в чугун и эффект модифицирования используется на 100%. Данный факт предоставляет контролируемый и эффективный способ модифицирования с небольшим количеством добавления ферросплава. Этот метод может быть автоматизирован без малейших трудностей.
^ ПРОИЗВОДСТВО СФЕРОИДАЛЬНОГО ЧУГУНА С ИСПОЛЬЗОВАНИЕМ ПРОВОЛОКИ С ПОРОШКОВЫМ НАПОЛНИТЕЛЕМ
Количество добавляемого Mg
Не весь добавляемый Mg идет на формирование сфероидального графита даже тогда, когда он добавляется соответствующим правильным образом.
Определенная часть Mg теряется при десульфурации для снижения содержания S. Если чугун содержит сфероидальный графит, а содержание S выше 0,01%, то изделие, возможно, содержит сульфат магния Mg. Это тот случай, когда базовый чугун содержит повышенный процент S. Десульфурация с Mg происходит при формировании сульфата магния (MgS).
Оставшаяся часть добавляемого Mg теряется по причине его сильного раскисляющего свойства. Другая часть Mg вступает в реакцию с кислородом, присутствующим в форме и формирует оксиды.
Однако же, большая часть потерянного Mg, обусловлена «сгоранием» Mg. Mg вступает в реакцию с кислородом в атмосфере и формирует дымовые газы, содержащие оксид Mg. Количество Mg, потерянного таким образом, достаточно большое по сравнению с остальными вышеперечисленными ситуациями.
Как уже известно, остаточного Mg должно быть достаточно, и обычно его количество составляет 0,035-0,040%, поскольку графит сфероидизирован. Быстрое охлаждение позволяет осуществлять формирование полностью сфероидального графита с относительно низким процентным содержанием магния Mg. Данный факт встречается при производстве труб с использованием непрерывного цикла производства. Низкая скорость охлаждения, например, у толстостенных изделий требует более высокого содержания остаточного Mg для обеспечения полностью сфероидальной формы графита. Рекомендуемый диапазон значений остаточного Mg:
Остаточный магний: 0,035 – 0,055 %
Иными словами, количество добавляемого Mg должно быть достаточно большим, чтобы предоставить необходимое его количество для десульфурации, раскисления чугуна, выгорания и для гарантии обеспечения достаточного его остатка. В общих чертах все выше сказанное можно выразить, сказав, что при добавлении порошковой проволоки для обработки чугуна с использованием Mg зависит от следующих факторов:
- количество базового металла, подвергающегося обработке;
- % S, содержащейся в базовом чугуне;
- % O, содержащегося в базовом чугуне;
- температура обработки;
- скорость подачи проволоки и типы ферросплавов, содержащихся в проволоке;
- конфигурация ковша (высота до зеркала металла);
- толщина и условия охлаждения отливок.
Состав базового чугуна
Чугун для плавки для производства отливок из сфероидального чугуна должен быть как можно более свободным от элементов приводимых ниже.
Максимально возможное рекомендуемое содержание элементов в обрабатываемом с помощью Mg чугуне:
Pb 0,002 %
Sb 0,002 %
Bi 0,002 %
B 0,001 %
As 0,02 %
Ti 0,04 %
V 0,04 %
Se 0,02 %
Помимо этого, такие элементы как Cu и Sn могут иметь отрицательный эффект на форму сфер (глобул), в особенности в присутствии элементов из вышеприведенного списка. Рекомендуется удерживать содержание данных элементов ниже следующих ниже граничных значений:
Cu 1,0 % макс.
Sn 0,08 % макс.
Mn, Cu, Sn и Ni выступают в роли стабилизирующих элементов перлита. Для сфероидального ферритного чугуна их содержание должно быть ограничено и определено в зависимости от толщины отливок.
Сr – это элемент, который мощным элементом, образующим карбиды. В случае если карбиды являются нежелательными образованиями в сфероидальном чугуне, то содержание Cr должно быть как можно более низким, но в любом случае не должно превышать 0,05%.
S - По причине присутствия особых соединений сплавов в порошковой проволоке базовый чугун с высоким содержанием S (выше 0,09%) также может быть десульфурирован и обработан в течение одной лишь операции. Данная операция представляет собой экономически выгодное решение, а также говорит о чистоте с экологической точки зрения, поскольку дымовые газы могут быть легко удалены и соответствующим образом переработаны.
P – хотя и не имеет прямого влияния на формирование сфероидального графита, однако обладает отрицательным воздействием, так как наличие фосфидов приводит к ухудшению механических характеристик материала (охрупчивание). Для получения максимальной пластичности и ударопрочности, содержание данного элемента должно быть ограничено следующим образом:
P макс. 0,05 % для ферритного чугуна
P макс. 0,03 % для перлитного чугуна
Расчет количества порошковой проволоки, добавляемой для производства сфероидального чугуна
Требуемое количество проволоки для каждого отдельного применения может быть рассчитано с использованием следующей формулы:
Метры проволоки = кг чугуна x 0,76 x S (%) + Mg требуемый (%) x 1000
Mg эффект. (%) x Mg проволоки (г/м)
- Пример расчета:
Тип проволоки: XXX Кол-во чугуна: 1000 кг
S в базовом чугуне: 0,015 % S конечная: 0,010 %
S (S базовая – S конечн.): 0,005 % Mg требуемый: 0,045 %
Желаемая эффект-ть Mg: 40 % Mg в проволоке: 60 г/м
Метры проволоки = 1000 x 0,76 x (0,015 – 0,010) + 0,045 x 1000 = 20,3 метра
40 x 60
20,3 метра x 360 г/м = 7,3 кг проволоки на тонну обработанного чугуна
= 0,73 % добавляемой проволоки
Расчет эффективности магния
Эффективность Mg на обработку с использованием порошковой проволоки должна рассчитываться по нижеприводимой формуле, а все значения должны основываться на результатах анализов, полученных на литейном производстве в данный конкретный момент.
Mg эффективн. (%) = 0,76 x S (%) + Mg треб. (%) x 100
Mg добавл. (%)
Содержание S до и после обработки, остаточный Mg, количество добавленного Mg в г/м и длина проволоки, используемой для обработки, является известными данными.
На эффективность Mg влияют следующие факторы:
- S, содержащаяся в базовом чугуне;
- Количество чугуна;
- Отношение между высотой и диаметром ковша;
- Температура обработки;
- Скорость подачи проволоки;
- Содержание Mg в проволоке;
- % конечного требуемого Mg.
Другими факторами, которые влияют на эффективность Mg, являются: содержание Ca и РЗМ (редкоземельные материалы), а также содержание кислорода в чугуне. Эти последние факторы не входят в расчетную формулу, однако в любом случае должны приниматься во внимание.
4 постулата, которые в их комбинации являются основополагающими для ТЕХНОЛОГИИ использования ПОРОШКОВОЙ ПРОВОЛОКИ для ПРОИЗВОДСТВА СФЕРОИДАЛЬНОГО ЧУГУНА
- Инжениринг, оборудование и автоматизированный контроль.
Станция подачи проволоки включает в себя:
- От одного до нескольких трайб-аппаратов, из которых каждая машина имеет следующие характеристики:
- скорость подачи проволоки регулируется от 5 до 60 метров в минуту;
- трехфазный двигаетль переменного токана 4KW-460V, 60
- 4 ролика (2 ведущих и 2 ведомых);
- прижимные ролики с предварительно натянутой пружиной и пневматической системой;
- счетчик импульсов на ведомых роликах;
- смотровая дверца с автоматическим выключателем безопасности.
- Платформа взвешивания (Дополнительная опция)
- Панель управления в комплекте с ПЛК (программируемый логический контроллер), частотный преобразователь для регулировки скорости и вспомогательные цепи питания. При необходимости устанавливается разъем для предачи данных, касающихся веса, и для подключения внешних сигналов. Есть возможность соединения со спектромером, выполняющим анализы структуры. Все оборудование соответствует спецификациям СЕЕ.
- Операторский пульт управления для вывода на экран параметров и их программирования:
- скорость подачи проволоки;
- параметр расчета длины подаваемой проволоки;
- общая длина проволоки в бобине;
- обратный ход проволоки после обработки;
- реле времени для прочистки направляющих труб подачи проволоки;
- реле времени для открытия и закрытия крышки ковша.
- вес расплавленного чугуна в ковше (в случае если данная информация не поступает автоматически);
- % содержания серы в базовом чугуне (в случае если данная информация не поступает автоматически);
- температура чугуна подлежащего обработки.
Цикл обработки контролируется автоматически и имеет следующие фазы:
- Тележка с заполненным ковшом устанавливается внутри станции обработки;
- Закрытие дверцы стании обработки;
- Крышка опускается на ковш;
- Происходит обработка с одновременным участием нескольких трайб-аппаратов;
- Происходит возврат проволоки для освобождения ковша;
- Поднятие крышки;
- Открытие дверцы станции обработки;
- Тележка с ковшом выводится за пределы станции обработки;
- Автоматическая очистка направляющих труб подачи проволоки с помощью сжатого воздуха.
Ковш с обработанным чугуном, из которого был уже удален весь шлак, может быть перемещен на линию разливки.
В поставку оборудования обычно включается: чертежи установки станции обработки и всего электрооборудования, списки монтажных узлов и деталей, а также инструкция по эксплуатации и техническому обслуживанию.
- Выбор и формула порошкового наполнителя проволоки для получения наилучших результатов металлургического процесса.
- Основные моменты.
Каждая проволока должна поставляться с учетом того, что должен быть получен максимально эффективный результат, на основании всех рабочих условий, на каждом отдельно взятом литейном производстве.
Содержание серы в базовом чугуне – это наиболее важный фактор для определения типа проволоки, поскольку мы должны привести его к тому значению, которое позволило бы нам получить эффект сфероидизации.
Тем не менее, нам необходимо также принимать во внимание типы производимых отливок (толщина стенок), все производимые манипуляции с обработанным чугуном на литейном производстве, а также специфику отливок (перлитная или ферритная структура).
- Диаметр проволоки.
Основываясь на производстве проволоки и на ее применении в литейном производстве, наиболее подходящим внешним диаметром является диаметр 13 мм с небольшими отличиями по размеру. Толщина используемой стальной полосы составляет 0,35-0,40 мм.
Проволока на 9 мм может использоваться только для обработки небольшого количества чугуна или иметь в своем составе исключительно чистый магний и использоваться в особых случаях.
c) Сравнение цен с конкурирующими производителями проволоки.
Очень важно не останавливаться только лишь на простой цене за килограмм проволоки, поскольку эффективность обработки, выраженная в килограммах проволоки на каждую тонну обработанного чугуна может значительно отличаться у разных производителей. Для правильной оценки необходимо сравнить всю стоимость затрат на обработку одной тонны чугуна.
- Разработка и производство ковша для обработки.
Наиболее подходящий ковш имеет соотношение между внутренней высотой и внутренним диаметром, равное 2:1, а при обработке большого количества чугуна данное отоншение имеет гораздо меньшее значение.
Существуют два важных фактора в отношении ковша, которые должны приниматься во внимание при обработке с использованием проволоки.
- Высота уровня чугуна в ковше.
Скорость подачи проволоки должна быть соответствующим образом соотнесена с высотой уровня чугуна. При слишком низкой высоте уровня чугуна обработка с использованием проволоки имеет меньшую эффективность и является несущественной при высоте уровня металла в ковше меньше 200 мм.
В идеале проволока должна высвобождать ферросплав на дне ковша.
Если скорость подачи проволоки является слишком низкой, то ферросплав вступает в реакцию рядом с поверхностью чугуна и происходит сгорание впустую большого количества магния в емкости, в которой находится чугун (раекция происходит слишком быстро).
Когда скорость подачи проволоки является слишком высокой, то появляются те же проблемы. Проволока опускается вниз и когда достигает дна, поскольку она еще не расплавилась, поднимается наверх, вызывая те же проблемы, что были описаны выше (реакция наступает слишком поздно).
В обоих случаях = низкая эффективность магния
Правило из практики применения:
Низкая высота уровня зеркала чугуна = низкая скорость подачи проволоки
Высокая высота уровня зеркала чугуна = высокая скорость подачи проволоки
^ Важное замечание:
Проволока всегда должна подаваться вертикально в емкость, содержащую чугун. В том случае, если подается только одна проволока, то она должна подаваться строго в центр ковша. В том случае, если подаются параллельно две проволоки, то идеальным расстоянием между ними должно быть расстояние от проволоки до стенок ковша.
- Свободное пространство (расстояние между поверхностью чугуна и верхней плоскостью ковша).
Минимальное свободное пространство должно составлять 400 мм.
Чем больше свободное пространство, тем меньше будет нагрузка, которую испытывает крышка ковша, что приводит, в свою очередь, к снижению затарт на техническое обслуживание.
Во время обработки происходит «кипение» чугуна внутри ковша – это является положительной характерной чертой процесса с использованием проволоки, поскольку блягодаря этому производится чистый чугун. В то же самое время мы хотим удержать как можно дальше от крышки пузыри, производимые продуктами реакции.
Благодаря давлению, создаваемому данными завихрениями и из-за высокого модержания Mg в проволоке мы получаем в итоге «очищающий эффект» чугуна, поскольку все примеси, такие как дроссы и шлаки очень быстро выталкиваются к поверхности зеркала чугуна, производя тем самым чистый чугун.
- Разработка и монтаж клети с проволокой под размер и на основании операций, производимых с ней, а также на основании размещения оборудования в литейном цеху.
Разработка и монтаж клети с проволокой под размер и на основании операций, производимых с ней, на литейном производстве выполняется для гарантии равномерной подачи проволоки в трайб-аппараты.
Виды клетей, в которых может находится проволока:
- Eye to the sky = раскручивание бобины вверх;
- Eye to the side = боковое раскручивание бобины.
Разработка клети очень важна для избежания опадания последних слоев проволоки во время раскручивания бобины.
Помимо этого, также важна прочность клети для избежания смещения бобины при транспортировке.
Тип клети “Eye to the side” с боковым раскручиванием бобины
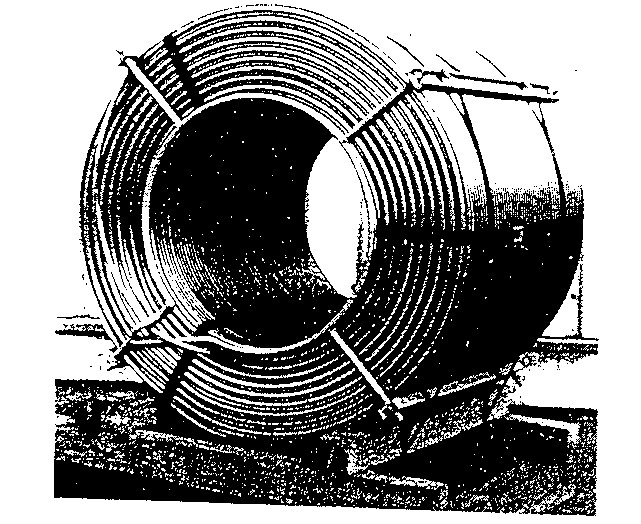
Тип клети “Eye to the sky” с раскручиванием бобины вверх
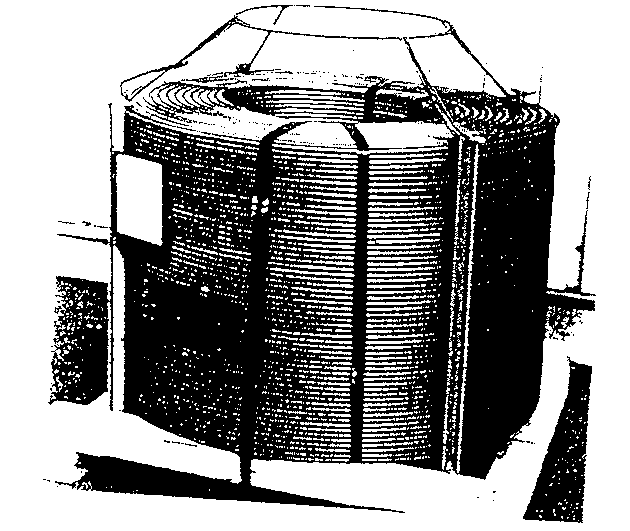