Литье под давлением
Вид материала | Документы |
СодержаниеИспользуются следующие формующие головки Метод ИВ. Отделка и декоривование |
- Инструкция по продлению срока службы сосудов, работающих под давлением, 821kb.
- Причины нарушения герметичности емкостей с сжиженным газом введение 1 цель главы, 418.06kb.
- 7. 3 Процесс литья ж д. шпал под давлением, 79.79kb.
- Градостроительный Кодекс Российской Федерации. Статья 48 Особо опасные, технически, 25.83kb.
- Правила устройства и безопасной эксплуатации сосудов, работающих под давлением,, 2390.63kb.
- Авиационная медицина, 138.33kb.
- Учебно-тематический план литье под давлением Цель: повышения квалификации работников, 21.26kb.
- Самой развитой сферой промышленности является именно жаропрочное литье, а также другое, 369.07kb.
- Демин Андрей Константинович andrey demin@yahoo com Как дорого России обойдется дешевая, 86.06kb.
- ) и ультрафильтрация (УФ) являются сепарационными процессами, которые протекают под, 183.57kb.
ЛИТЬЕ ПОД ДАВЛЕНИЕМ
Литье под давлением - это метод пластикации и формования готовых изделий. Переработка пластических масс проводится на специальных высокопроизводительных литьевых машинах. Оформление изделия проводят в холодных формах благодаря охлаждению.
Литье под давлением - это процесс переработки гранул и порошка.
Принцип изготовления изделий методом литья под давлением показан на рис.
Композиционный полимер в виде гранул загружают через бункер (1) в нагретый цилиндр. (2) литьевой машины. Внутри цилиндра происходит пластикация пластмассовых гранул.
Пластикация происходит как в результате теплопередачи от обогреваемых стенок цилиндра (на корпусе машины находятся нагревательные элементы (3) так и выделения тепла при деформациях, которым материал подвергается в цилиндре литьевой машины. Для ускорения расплавления гранул внутри цилиндра установлена металлическая торпеда с электрообогревателем (4). С помощью плунжера (5) вязкая пластическая масса передавливается через сопло (6) в холодную форму (7), которая периодически присоединяется к соплу.
Заполнив форму, масса остывает и затвердевает, приобретая очертания формы. Готовое изделие извлекается с помощью выталкивателя.
Литьевые машины действуют в полуавтоматическом и автоматическом режимах.
Применяют одно- и многогнездовые формы. Мелкие и простые изделия изготавливают в многогнездовых формах.
Цикл изготовления изделия (даже сложного) составляет 20 -60 секунд.
Характерные особенности литьевых изделий.
1. Гладкая, зеркальная поверхность.
2. Наличие следов от литника.
Пластмасса, застывшая в впускном канале неподвижной части формы, образует литник (обычно на не лицевой стороне). После его обламывания или обрезания остается след, требующий последующей обработки (зачистки). После зачистки след литника не должен превышать 0,3 мм.
- б
ункер
- цилиндр
- нагревательные элементы
- торпеда
- плунжер (гидравлическое давление)
- сопло
- форма
- изделие
- б
ункер
- цилиндр
- нагревательные элементы
- червяк (шнек)
- сопло
- формующая головка
- фланец, на который крепится формующая головка
- изделие
ЭКСТРУЗИЯ
Экструзия - это метод формования изделий или полуфабрикатов в экструдерах.
Экструдеры - это машины, предназначенные для пластикации и выдавливания полимерного материала через головку с формующим каналом определенного сечения (профиля).
Рабочим органом экструдера является вращающийся червяк (шнек) или диск, реже поршень. Экструдеры бывают:
■ червячные;
■ дисковые;
■ поршневые (ограниченное применение).
Наиболее распространены червячные экструдеры. Это универсальные высокопроизводительные машины, в которых м.б. осуществлен непрерывный автоматизированный процесс. Червячные экструдеры бывают:
- одно-, двух-, трех-, четырехчервячные;
- одно-, двух-, многоцилиндровые (каждый червяк размещен в отдельном цилиндре);
- одно- и двухстадийные, в которых пластикация осуществляется соответственно в одну и две стадии;
- горизонтальные и вертикальные (в зависимости от расположения червяка).
В экструдерах перерабатывают главным образом термопласты. Их используют для изготовления изделий из резиновых смесей (в резиновой промышленности экструдеры называют шприц машинами).
С помощью экструдера м.б. осуществлены следующие технологические процессы:
■ гранулирование;
■ изготовление пленок;
■ производство листовых и рулонных материалов (например, ПВХ, линолеума);
■ изготовление труб, шлангов, прутков и др. профильных изделий;
■ наложение полимерной изоляции на металлические провода и кабели;
■ нанесение тонкослойных покрытий на бумагу, картон, ткани, металлическую фольгу, а также дублирование полимерных пленок;
■ получение полых штучных изделий (экструзия с раздуванием);
■ смешение полимеров с красителями, пластификаторами и др. ингредиентами.
Принцип действия экструдера сходен с литьем под давлением.
Твёрдый полимер (в виде порошка или гранул) поступает в экструдер. Через бункер (1) гранулы пластмассы попадают в цилиндр (2). Внутри цилиндра происходит пластикация пластмассовых гранул. Пластикация происходит как в результате теплопередачи от обогреваемых стенок цилиндра (корпуса), так и выделения тепла при деформациях, которым материал подвергается в экструдере. Обогрев экструдера осуществляется электронагревателями (3), находящимися на корпусе по всей длине экструдера.
Охлаждение Э., необходимое для регулирования и поддержания заданной температуры экструзии, м.б. водяным, воздушным или комбинированным.
Для автоматического контроля и регулирования температуры применяют термопары или термометры.
Вязкая масса, образовавшаяся в цилиндре, непрерывно выдавливается шнеком - червяком (4) через сопло (5) в формующую головку (6), имеющую различные профили. Привод червяка м.б. электрическим (от двигателей переменного или постоянного тока) или гидравлическим. При прохождении через сопло и выходе из формующей головки пластмасса охлаждается и затвердевает в виде профильных изделий (с сечением сопла формующей головки).
Используются следующие формующие головки:
■ плоскощелевая головка используется для получения плоских пленок и листов;
■ угловую кольцевую головку обычно применяют для получения рукавной пленки;
■ осевую кольцевую головку применяют для изготовления труб;
■ для получения профильных изделий используют специальные головки, канал которых соответствует конфигурации изделия;
■ на экструдере изготавливаю так называемые поделочные материалы;
■ при наложении полимерной изоляции на металлические провода и кабели применяют Т-образные, а также косоугольные кольцевые головки (ось первых расположена под углом 90 , вторых- 45 или 60 к оси червяка).
Экструзия с раздуванием
Экструдеры комплектуют с различными разъемными формами, позволяющими изготавливать готовые изделия (см. рис). Сначала на экструдере изготавливают полимерную трубу требуемого сечения. Затем отрезок (заготовку) трубы (или рукава) замыкается между двух частей формы. Один конец заготовки зажимается. Герметизированную т.о. заготовку раздувают сжатым воздухом (р=2-10кгс/см2 ), который подается через отверстие в формующем ниппеле. Раздувание заготовки сопровождается уменьшением толщины ее стенок и увеличением размеров сечения. Отформованное изделие охлаждают (воздухом или жидкой двуокисью углерода), после чего форму размыкают и удаляют из нее изделие, используя для этого сжатый воздух или специальные приспособления.
Продолжительность цикла составляет от нескольких секунд до десятков минут.
Характерные особенности изделий.
1. Получают полые (объемные) изделия;
2. На боковых поверхностях изделий заметны швы от мест соединения разъемной формы;
3. Сварной шов имеется только в нижней части изделия.
4. Отверстие от ниппеля;
Дефекты:
1. Облой
2. Разнотолщинность.
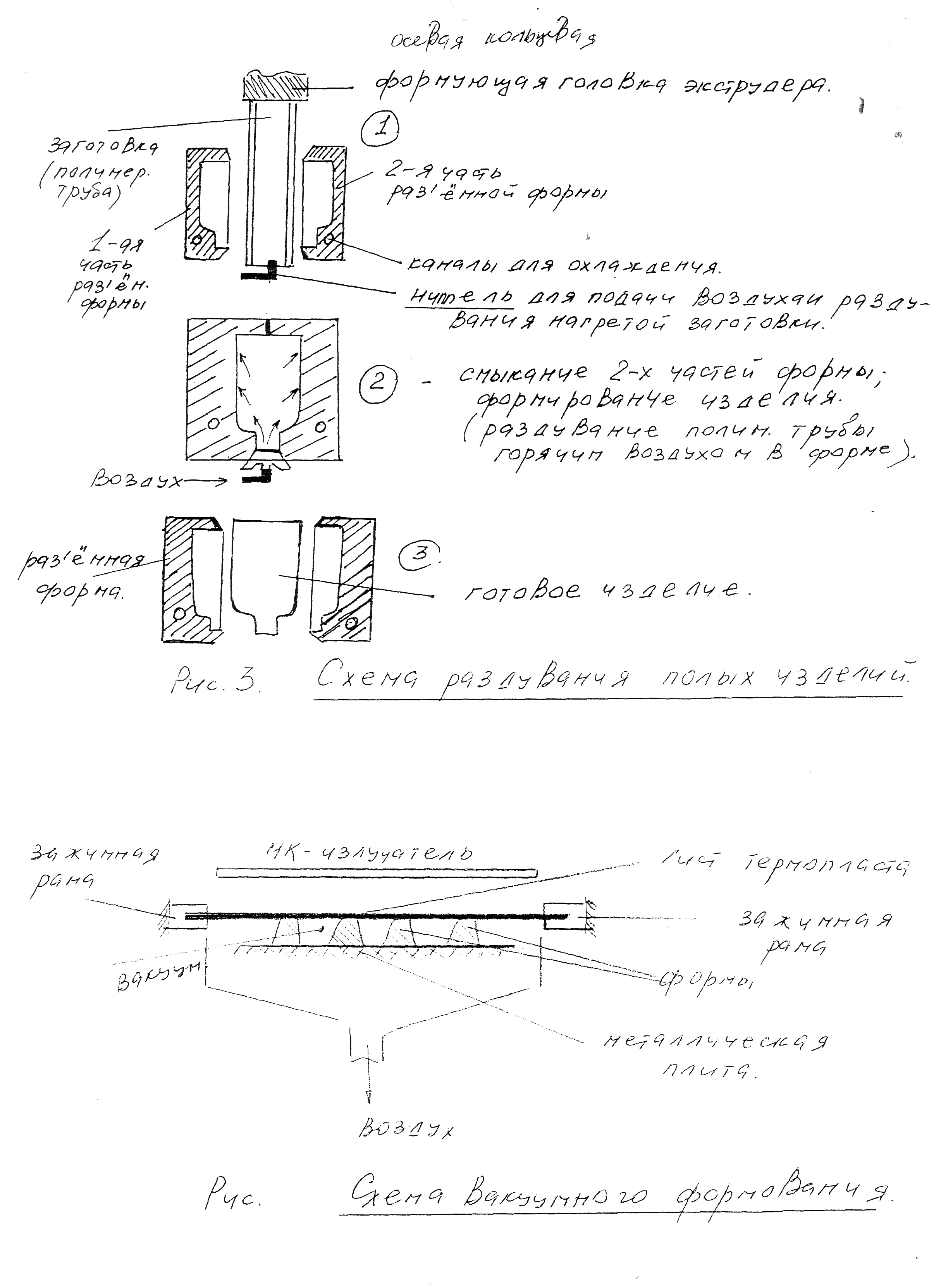
Пневматическое формование.
Пневматическое формование и его разновидности (вакуумное формование, выдувание) основаны на действии атмосферного или избыточного давления (1.5-5 атм.) воздуха или иного газа на разогретые заготовке (листы) термопластов.
Старейший из этих метод- выдувание. Раньше он применялся для изготовления полых игрушек из листового целлюлойда.
На сегодня широкое распространение получил метод вакуумного формования из листовых термопластов.
Сущность метода состоит в том, что:
■ лист термопласта прижимается к форме зажимной рамой;
■ лист прогревается инфракрасным излучателем до размягчения;
■ между формой и размягченным листом создается разряжение (вакуум);
■ заготовка (лист) равномерно обжимает форму;
■ формирование изделия при охлаждении (см. рис.).
Метод вакуумного формования широко используется для изготовления упаковочных средств и для изготовления одноразовой посуды.
При непосредственном пневматическом формовании используют избыточное давление (до 5 атм.) и получают крупногабаритные с четким рисунком (по сравнению с вакуумным формованием) изделия.
Форма для пневматического формования состоит из матрицы и камеры для газа, давящего на предварительно разогретый лист термопласта. После разъема формы производят обрезку краев (полей) отходы при этом составляют 15-20% массы листовой заготовки. Этим методом изготавливают крупные изделия и детали:
-фотокюветы;
-ванны;
-раковины;
-корпуса ящиков;
-чемоданы;
-обшивку стенок и дверей холодильников и др.
Для изготовления этих изделий широко используют винипласт, ударопрочный полистирол, сополимеры полистирола.
Характерные признаки:
1. простая форма
2. гладкие (отсутствуют стыковые швы)
3. хрупкие
Горячее прессование
Изготавливают изделия из фенопластов, аминопластов. Исходное сырьё – порошок, таблетки. Формование проводят ф форме, состоящей из 2-х частей (неподвижной матрицы, подвижной – пресс).
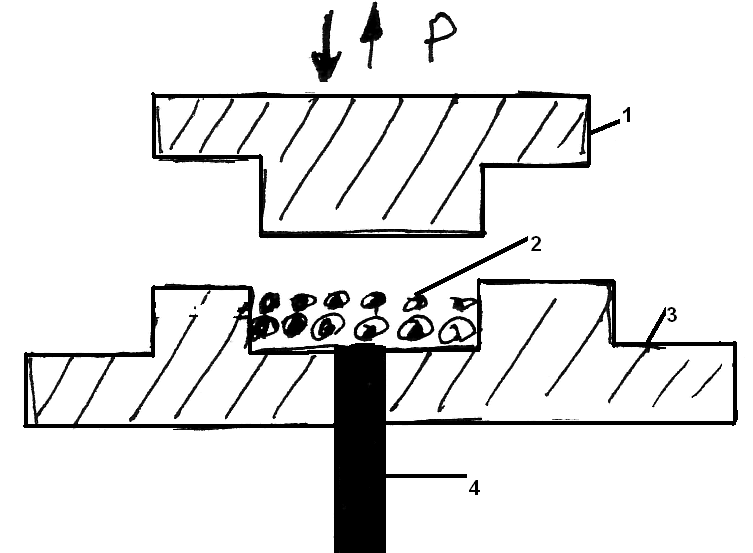
1. пресс
2. пресс-порошок
3. матрица
4. выталкиватель
1. Загрузка порошка в подогретую металлическую форму (Т=160-1800С)
2. Замыкание пресс-формы (рис.2.)
3. Формование под давлением (150-350 кгс/см2); Т=1800С; с выдержкой при высокой температуре.
Размягчённый пресс-порошок под давлением заполняет пресс-форму.
Форма остаётся замкнутой до полного отверждения изделия.
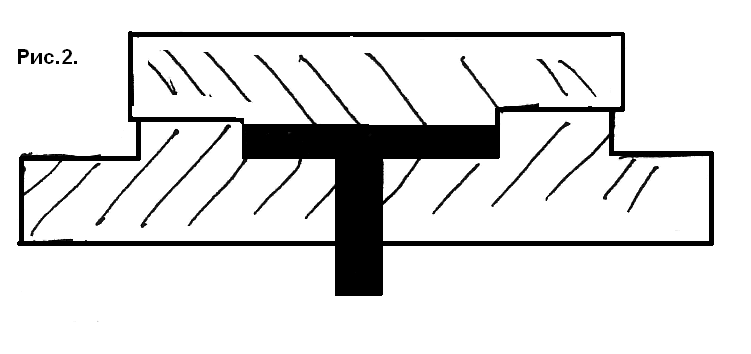
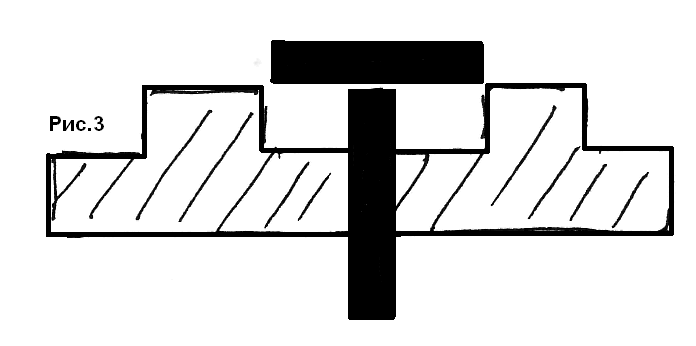
4. Извлечение изделия с помощью выталкивателя.
Характеристики изделия:
1. изделия простой формы;
2. след от выталкивателя;
3. верхний больше нижнего
4. формование несколько минут (из расчёта от 20 сек. до 1 мин, на 1мм толщины изделия).
Этим методом из листового винипласта, ударопрочного полистирола и сополимеров стирола получают:
-фотокюветы;
-ванны;
-раковины;
-корпуса ящиков;
-чемоданы;
-обшивку стенок и дверей холодильников и др.
- упаковку для пищевых продуктов (стаканчики, баночки и т.д., разовую посуду).
Горячее штампование
Изготавливают изделия несложной формы из листов термопластов.
Из целлулоида получают галантерейные изделия: мыльницы, футляры для очков и зубных щёток. Исп. ПММА. Заготовка (лист) прогревается на плитах, прижимается к матрице и формуется пуансоном.
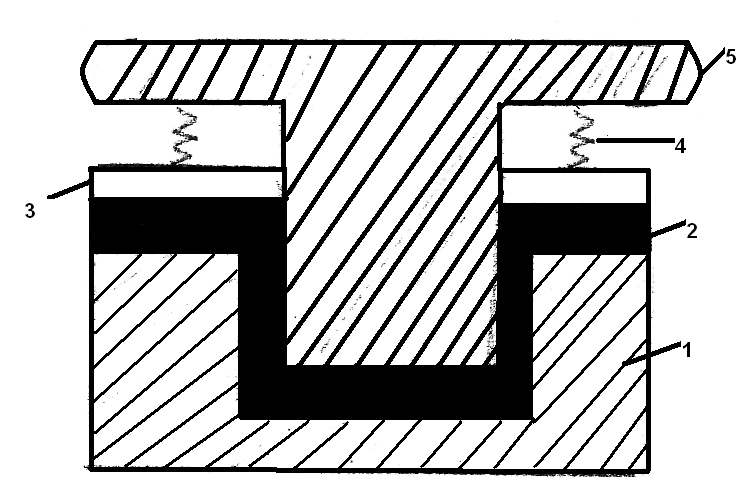
1. матрица
2. заготовка
3. пружинная плита
4. пружина
5. пуансон
изделия в штампах охлаждаются сжатым воздухом. Недостаток – форма изделий – простая; - износ штампов.
Изготовление пластмассовых бутылок и флаконов
На сегодня существует два способа изготовления бутылок и флаконов:
-экструзия с раздуванием (ЭР);
-выдувание из преформы (инжекционно - выдувное формование - ИВ).
Метод ИВ.
Преформа - это заготовка в виде пробирки. Ее изготавливают методом литья под давлением (на дне преформы присутствует литник). Разработаны специальные высокопроизводительные агрегаты по производству преформ, способные производить до 40 тыс. преформ в час.
По конфигурации преформы делятся на три группы:
■ универсальные (массово распространены);
■ толстостенные;
■ укороченные.
Преформы изготавливают цветные и бесцветные, прозрачные и непрозрачные.
Преформы помещаются в специальные автоматы или полуавтоматы по выдуву бутылок. В пресс-формах их нагревают до состояния эластичной резины и раздувают сжатым воздухом. Готовые бутылки остывают на холодных стенках пресс-формы.
Автомат по выдуву бутылок может выдувать до 24 тыс. штук.
Полуавтомат - 600 бутылок в час. Полуавтомат обслуживается одним оператором. В полуавтомате легко меняются пресс-формы (за 15-20 мин.). На одном полуавтомате можно изготавливать целый спектр бутылок: 0,33; 0,5; 1; 1,5; 2,.....5 литров.
Основным отечественным производителем такого оборудования является фирма «Продвижение».
Сравнительная характеристика методов ЭР и ИВ.
1. Метод ИВ более производительный, чем ЭР.
2. Методом ИВ получают более прочные бутылки (для газированных и слабо газированных напитков).
3. Метод ЭР предлагает более широкие возможности:
■ четкая проработка мелких деталей (бордюры, логотип, ребра и т.п.);
■ простое регулирование толщины бутылки (перемещение дорна относительно мундштука). Например, методом ЭР можно изготовить бутылку в виде гитары (широкую снизу и узкую вверху), используя специальный программный привод для перемещения дорна;
■ можно производить бутылки и флаконы с ручками (используя ИВ: необходимо сделать бутылку, отдельно ручку методом ЭР, а затем вставить ее в бутылку и соединить с ней. При этом значительно увеличиваются расходы).
Т.о., эти методы дополняют друг друга. Бутылки и флаконы используются для:
■ для газированной и негазированной воды, пива;
■ растительного масла, кетчупа, горчицы;
■ автомобильной косметики;
■ горюче-смазочных жидкостей;
■ шампуней, гелей, жидкого мыла и др. косметических средств;
■ средств бытовой химии;
■ лаков, красок и др.
ОТДЕЛКА И ДЕКОРИВОВАНИЕ
Обычно изделия из пластмасс после формования не требуют специальной отделки.
Лишь механически обработанные поверхности после зачистки облоя и литников тщательно полируют (до блеска).
Для некоторых изделий применяют двухцветное литье.
Для улучшения качества готовых изделий применяют декоративную отделку. В зависимости от типа материала и условий его эксплуатации проводят различные отделочные операции:
■ гравирование;
■ горячее тиснение;
■ раскрашивание (печать, деколь);
■ металлизацию.
Эти декоративные эффекты и другие получают непосредственно при формовании изделия или после его окончания.
Тиснение.
Тиснение - это нанесение на гладкую поверхность изделия рельефного рисунка. На многие пластмассовые изделия рельефный рисунок наносится непосредственно при формовании. Тиснение пленочных материалов проводят на валковом оборудовании, пропуская их между гладкими прижимным валом и металлическим валом с рельефной поверхностью. Перед тиснением полимерная пленка разогревается до вязкотекучего состояния, что позволяет наносить рисунок без больших усилий. Рисунок на полимерной пленке закрепляется путем последующего охлаждения. Тиснение может различаться глубиной и характером рисунка. Рельефное декорирование готовых изделий проводится непосредственно в рельефных формах (литьё, экструзия).
Деколь
Печатный рисунок можно наносить с помощью переводных изображений. Изображение предварительно наносится на специальную подложку, с которой оно затем переводится на поверхность изделия. Такую подложку с нанесенными на ней в виде тонкой пленки переводным изображением называют деколем.
Различают три основных способа нанесения деколя:
- мокрый, когда необходимо предварительное смачивание деколя для набухания клеевого слоя изображения и сквозного промокания подложки; после этого деколь слегка прижимают к поверхности изделия - рисунок переходит на поверхность изделия, а чистая подложка отделяется от переводного изображения;
- сухой, не требующий предварительного смачивания деколя, когда перевод изображения осуществляется после снятия защитной пленки с лицевой поверхности деколя; при этом способов легкое отделение переводного изображения от подложки и переход его на декорируемую поверхность возможны благодаря малой адгезии между подложкой и переводным изображением;
- термический, сопровождаемый повышением температуры; при этом способе переводное изображение впитывается поверхностным слоем полимерного изделия, чем объясняется повышенная стойкость изображения истиранию и механическим повреждениям.
Аппликация
Аппликация - способ художественного декорирования поверхности полимерных изделии с помощью накладных элементов из разноцветных материалов.
Аппликация бывает:
- накладной;
- заформованной.
Если элементы аппликации закрепляют на поверхности готового изделия приклеиванием или сваркой, то такая аппликация называется накладной. Способ, при котором элементы художественного декорирования закладывают в форму и закрепляют на изделии в процессе его формования, называют заформованной аппликацией.
В качестве элементов аппликации используют разноцветные набивные ткани, бумагу с красочным рисунком или текстом, а также декорируемые изделия.
Печать
Печать - это нанесение печатного рисунка на поверхность материала. Различают одноцветную и многоцветную печать. Печать наносят различными способами. Для декорирования полимерных материалов и изделий из них широко используются три основных способа печати:
■ высокая;
■ офсетная;
■ глубокая.
Способ высокой (типографской) печати основывается на использовании жестких металлических форм, в которых печатающие элементы выступают над пробельными. Способ обеспечивает чистый и четкий оттиск и хорошую передачу красок.
При офсетном (плоском) способе печати пробельные и печатные элементы практически находятся в одной плоскости. Принцип офсетной печати основан на смачивании печатной формы увлажняющим раствором и накатывании жирной краски, которая при этом избирательно задерживается на несмачиваемых (печатных) элементах. С печатной формы красочный оттиск переходит на резиновый (офсетный) вал, а с него на запечатываемый материал.
Способ глубокой печати заключается в применении формного цилиндра, печатающими элементами которого являются ячейки, углубленные на поверхности формы, а пробельными - промежутки между ними. Ячейки, образуемые обычно фотохимическим травлением, имеют различную глубину, соответствующую свето- и цветоплотности воспроизводимого рисунка. Печатный вал, вращаясь в окрасочной ванне, постоянно покрывается краской, которая тут же счищается с его поверхности специальным скребком-ракелем. Способ глубокой печати является наиболее распространенным при декорировании поверхностей изделий. Схематически основные способы печати на поверхности полимерного материала при непрерывном способе производства представлены на рис.
Нанесение печатного рисунка осуществляется на печатно-отделочных агрегатах. При многоцветной печати число печатных узлов может доходить до восьми.
К
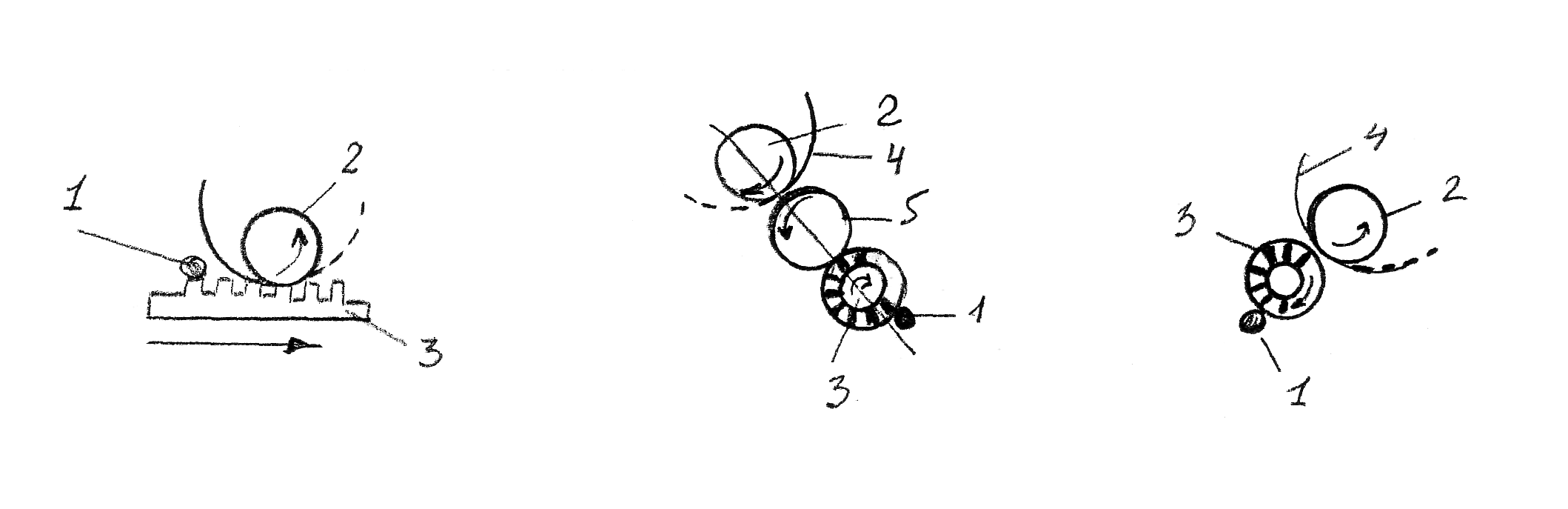
1. краситель
2. печатный вал
3. печатная форма
4. печатная основа
5. резиновый вал
Классификация бытовых пластмассовых изделий.
Согласно ОКП пластмассовые бытовые изделия относятся к классу 22, подклассу 9, группе 3 (Изделия культурно-бытового назначения и хозяйственного обихода из пластмасс - 2293001.
2293ЗД- изделия хозяйственного обихода из пластмасс.
229311-из ПЭ.
229312- из ПГТ
229313- из ПВХ.
229314- из ПС;
229318 - из прочих реактопластов.
И т.д.
На практике (в торговле, в учебном процессе) используют классификации бытовых изделий по назначению. Бытовые пластмасс
■ хозяйственные товары;
■ галантерейные товары;
■ культурно-бытовые товары.
Хозяйственные товары делятся на 4 группы:
■ изделия посудохозяйственного обихода (сухарницы, хлебницы, солонки, миски, кувшины и др.);
■ изделия для ванной комнаты и туалета (корзины для белья, вешалки для полотенец, емкости для стиральных порошков и др.);
■ изделия для сада-огорода (лейки, плодосъемники, ящики для инструментов, насадки для шлангов и др.);
■ изделия мебельные и для интерьера жилых помещений (кашпо, горшки для цветов, табуреты, карнизы, полки и др.).
Посудохозяйственные изделия делятся: я изделия, контактирующие с пищей:
- для сыпучих продуктов;
- для холодных продуктов;
- для горячих продуктов;
■ изделия, не контактирующие с пищей (губки, подставки, щетки, контейнеры для мусора и др.).
По комплектности пластмассовые изделия делятся на штучные и комплектные (наборы и гарнитуры).
По конструкции: простые и сложные, сборные.
По форме посудохозяйственные изделия могут быть круглые, овальные, прямоугольные, цилиндрические, конические.
Конструкция и форма определяют фасон изделия.
По размерам: различаются по емкости, по диаметру по длине, ширине, высоте.
По отделке: с отделкой и без отделки.
Галантерейные товары подразделяются:
■ туалетные принадлежности;
■ гребенн
■ фурнитура одежная;
■ украшения;
■ декоративные изделия;
■ предметы для рукоделия;
■ сумки, кошельки.
Культурно-бытовые товары делятся на:
■ игры;
■ настольные украшения;
■ игрушки:
■ канцелярские товары:
■ фототовары.
Согласно ГОСТ 5G962-96 «Посуда и изделия хозяйственного назначения из пластмасс. Общие технические условия.». Бытовые пластмассовые изделия делятся:
■ посуда (тарелки, миски, стаканы, блюда, хлебницы, солонки, соусницы, масленки и др.);
■ столовые приборы (ложки, вилки, ножи, соломка для коктейля, щипцы для льда, лопатка для торта т т.п.);
■ предметы сервировки стола (скатерти, салфетки, подставки под горячую посуду, подносы, салфетницы, ведерко для льда и др.);
■ кухонные принадлежности (дуршлаг, скалка, воронка, сито, ручной миксер, высечки для печенья и т.д.);
■ емкости и вспомогательные изделия для хранения и переноски продуктов (канистра, фляга, бидон, бутыль, ведро, банка, контейнер, судок и др.);
■ изделия санитарно-гигиенического назначения (рукомойник, таз, ведро для мусора, корзина для бумаг и т.д.);
■ изделия детского ассортимента (ванночка, мяч, бутылочка для детского питания);
■ предметы интерьера (полка, шкафчик, табурет, ваза, кашпо, рама для зеркала, стул и т.д.);
■ галантерейные изделия (сумка из полимерной пленки, бижутерия, пепельница, мундштук и т.п.);
■ приспособления для развешивания белья, одежды и т.п. (вешалка, крючок, прищепки, сушилка для белья и др.).