Конспект лекций по дисциплинам «Технология рэс» специальности 210201
Вид материала | Конспект |
- Методические указания к курсовой работе по дисциплинам: «Техническое обеспечение, 321.66kb.
- Рабочая программа учебной дисциплины «конструирование и технология рэс» Цикл, 170.35kb.
- Конспект лекций по курсу технология лекаственных форм и галеновых препаратов для студентов, 1506.84kb.
- Конспект лекций по теме: «Материаловедение» для специальности 120100 "Технология, 104.18kb.
- Конспект лекций по теме: «Материаловедение» для специальности 120100 "Технология, 5022.76kb.
- Конспект лекций по курсу «технология производства в отраслях городского хозяйства», 915.66kb.
- Конспект лекций для студентов всех форм обучения специальности 261201 ''Технология, 1583.67kb.
- Рабочая программа по дисциплине «Физика» для направления подготовки дипломированного, 282.66kb.
- Гражданское право. Часть первая (конспект лекций), 2930.06kb.
- Конспект лекций для студентов специальности 080504 Государственное и муниципальное, 962.37kb.
Содержание:
- Механические операции. Механическая обработка ПП. Подготовительные операции.
- Формирование токопроводящих элементов ПП. Технология металлизации. Активация поверхностей диэлектриков. Гальваническая металлизация. Формирование рисунка печатных плат. Травление меди с пробельных мест. Особенности изготовления МПП. Покрытия и маски для наружных слоев ПП. Контроль и испытания плат.
Основу модулей первого уровня РЭА составляет оригинальная деталь - коммутационная подложка, на которой устанавливаются компоненты и которая обеспечивает электрическое соединение между компонентами в соответствии с электрической схемой. В общем случае подложка представляет собой диэлектрическое основание и рисунок в виде металлических пленочных проводников, называемых печатными. Отсюда распространенное название таких плат - печатные платы (ПП). Различают следующие типы ПП: односторонние, двусторонние, многослойные и гибкие.
механические операции [3]
Механическая обработка ПП включает раскрой листового материала на полосы, получение из них заготовок, выполнение фиксирующих, технологических, переходных и монтажных отверстий, получение чистового контура ПП. Размеры заготовок определяются требованиями чертежа и наличием по всему периметру технологического поля, на котором выполняются фиксирующие отверстия для базирования деталей в процессе изготовления и тестовые элементы. При прессовании МПП на технологическом поле образуется зона некачественной пропрессовки пакета, которая удаляется при обработке контура. Ширина технологического поля не превышает 10 мм для ОПП и ДПП и 20-30 мм для МПП. Малогабаритные платы размером до 100 мм размещают на групповой заготовке площадью не менее 0,05 м2 с расстоянием 5-10 мм между ними.
Выбор метода получения заготовок определяется типом производства. В крупносерийном и массовом производстве раскрой листового материала осуществляют штамповкой на кривошипных или эксцентриковых прессах с одновременной пробивкой фиксирующих отверстий на технологическом поле. Для уменьшения вероятности образования трещин, сколов, расслоений и повышения точности обрабатываемый материал прижимают к плоскости матрицы фольгированной стороной. Вырубку в штампах производят как в холодном, так и в нагретом до 80-100 °С состоянии материала. Прогревают материал при получения сложного контура ПП и его толщине свыше 2 мм.
Заготовки ПП в единичном и мелкосерийном производстве получают разрезкой на одно- и многоножевых роликовых или гильотинных ножницах. Применяемые ножи должны быть установлены параллельно друг другу с минимальным зазором 0,01-0,03 мм по всей длине реза.
Фиксирующие отверстия диаметром 4-6 мм выполняют штамповкой или сверлением с высокой точностью (0,01-0,05 мм). Для сверления используют универсальные станки, в которых точность достигается применением кондукторов, или специальное полуавтоматическое оборудование, которое в одном цикле с обработкой пакета заготовок предусматривает пневматическую установку штифтов, фиксирующих пакет. Сверление ведут спиральными сверлами из быстрорежущей стали или твердых сплавов при скорости 30-50 м/мин и подаче 0,03-0,07 мм/об. Биение сверла при обработке не должно превышать 0,03 мм. Повышение точности сверления фиксирующих отверстий достигается их развертыванием при скорости 10-30 м/мин и ручной подаче инструмента.
Аналогичными методами выполняют и технологические отверстия, которые используют для предотвращения смещения заготовок слоев МПП в процессе прессования, но к точности их обработки не предъявляются такие жесткие требования, как к точности обработки фиксирующих отверстий, по которым идет совмещение заготовок с фотошаблонами и отдельных слоев в пакете.
Монтажные и переходные отверстия получают также штамповкой и сверлением. Пробивку отверстий на универсальных или специальных штампах применяют в тех случаях, когда отверстие в дальнейшем не подвергается металлизации и его диаметр не менее 1 мм. При пробивке отверстий в односторонних фольгированных диэлектриках применяют штампы с увеличенным зазором между пуансоном и матрицей, обеспечивающим затягивание фольги в отверстие, чем достигается его частичная металлизация. Максимальная глубина затягивания фольги в отверстия диаметром 1-1,3 мм достигается при технологическом зазоре 0,4+0,2 мм. Если плата имеет высокую плотность монтажа, большое количество отверстий и малый шаг координатной сетки, то применяют последовательную пробивку на нескольких штампах. Применение универсальных штампов, в которых необходимое количество отдельных пуансонов набирается в специальном трафарете, делает процесс штамповки экономичным в условиях мелкосерийного производства.
Металлизированные монтажные и переходные отверстия обрабатывают с высокой точностью на специализированных одно- и многошпиндельных сверлильных станках с ЧПУ. Эти станки имеют координатный стол с автоматической системой позиционирования, сверлильные шпиндели с бесступенчатым регулированием скорости и систему ЧПУ позиционного типа. В зависимости от размеров обрабатываемых плат и требуемой производительности станки можно оснастить различным числом шпиндельных головок. Каждый шпиндель имеет независимый привод скоростей, в связи с чем за одну установку и по одной общей программе могут обрабатываться отверстия разных диаметров.
Для обработки металлизированных отверстий используются специальные спиральные сверла из металлокерамических твердых сплавов. Их стойкость при обработке фольгированных стеклотекстолитов составляет 3000-7000 тыс. отверстий, при наличии лакового покрытия на ПП стойкость инструмента уменьшается в 2—3 раза. Номинальное значение диаметра сверла следует выбирать исходя из зависимости
dсв = d + 0.7(1+2),
где d - номинальный диаметр отверстия, мм; 1 - допуск на этот диаметр, мм; 2 - допустимое уменьшение диаметра обрабатываемого отверстия после охлаждения слоистых пластиков, мм.
Повышение температуры в зоне обработки при сверлении слоистых пластиков приводит к наволакиванию размягченной смолы на кромки контактных площадок, препятствующему последующей металлизации отверстий. Для устранения этого недостатка предлагается ряд усовершенствований: применение охлаждающих агентов, не содержащих смазок (вода, водяной туман, очищенный сжатый воздух и т. п.); двойное сверление; наложение на поверхность платы алюминиевых листов; разработка сверл с дополнительными режущими кромками, направленными в сторону, противоположную основным, и т. п. Однако все перечисленные способы оказываются малоэффективными в условиях массового производства. Предлагаемый фирмой IBM (США) процесс лазерного фрезерования хотя и устраняет наволакивание смолы на торцы контактных площадок, но не исключает ее стеклование на поверхности стенок отверстия. Наиболее эффективным средством устранения наволакивания признана последующая гидроабразивная очистка.
Чистовой контур ПП получают штамповкой, отрезкой на гильотинных ножницах или на специальных станках с прецизионными алмазными пилами, фрезерованием. Повышение производительности фрезерных работ достигается групповой обработкой пакета ПП толщиной 10-30 мм. Для исключения повреждения их поверхностей между отдельными заготовками прокладывают картон, а пакет помещают между прокладками из листового гетинакса.
В последнее время для чистовой обработки все большее распространение получают контурно-фрезерные многошпиндельные станки с ЧПУ, которые обеспечивают хорошее качество кромок ПП и точность размеров в пределах ±0,025 мм, позволяют обрабатывать внешние и внутренние контуры за одно крепление, характеризуются высокой производительностью (1500-2000 плат/ч) и надежностью. Они снабжены устройствами для автоматической смены фрез, защитными скафандрами для ограждения оператора от шума, пыли и стружки при обработке, бесступенчатым регулированием частоты вращения инструмента в диапазоне 15-60 тыс/мин.
Подготовительные операции предназначены для обеспечения качества при выполнении основных процессов формирования элементов печатного монтажа. Они включают очистку исходных материалов и монтажных отверстий от окислов, жировых пятен, смазки, пленок и других загрязнений, активирование поверхностей проводящего рисунка, специальную обработку диэлектриков, а также контроль качества подготовки. В зависимости от характера и степени загрязнений очистку (активирование) проводят механическими, химическими, электрохимическими, плазменными методами и их сочетанием.
Механическая подготовка в условиях мелкосерийного производства осуществляется вручную смесью венской извести и шлиф-порошка под струей воды. Экономически оправдано применение механизированных и автоматических конвейерных линий в условиях крупносерийного и массового производства. Инструментом на этих линиях служат абразивные круги, капроновые или нейлоновые щетки, на которые подается абразивная суспензия. В некоторых зарубежных установках для зачистки используются круги из нетканого нейлона, насыщенные мелкодисперсным порошком карборунда или алунда, которые для устранения перегрева обильно смачивают водой. Для очистки монтажных отверстий от наволакивания смолы и других загрязнений широко применяются установки гидроабразивной обработки, в которых платы со скоростью 0,2-0,4 м/мин проходят рабочую, промывную и сушильную камеры установки. В рабочей камере через инжекторные форсунки, качающиеся вокруг оси с частотой 35-100 циклов в минуту, под давлением 0,5-0,7 МПа подается пульпа, состоящая из абразивного порошка и воды. Подача воды под давлением 1-1,2 МПа обеспечивает тщательную промывку отверстий в следующей камере. Сушка заготовок осуществляется сжатым воздухом.
Химическая и электрохимическая подготовка поверхности проводится в ваннах с различными растворами при покачивании плат и последующей их промывкой, а механизированная - на автооператорных линиях модульного типа по заданной программе.
Высокое качество и производительность обеспечивает плазменная очистка ПП, которая устраняет использование токсичных кислот, щелочей и их вредное воздействие на обслуживающий персонал, материалы обработки и окружающую среду. Установки плазмохимической обработки состоят из реактора, мощного ВЧ-генератора, устройства управления и регулирования процессов, вакуумного насоса. Плазмообразующий газ, состоящий из кислорода (70%) и тетрафторметана (30%), подается в камеру со скоростью 600-900 см3/мин. Мощность ВЧ-генератора регулируется в диапазоне 0-4000 Вт, а частота составляет 13,56 МГц. На установке одновременно обрабатывается до 15 плат размером 45х60 см, каждая из которых имеет до 3000 отверстий. Длительность операции очистки пакета— 10... 16 мин.
Специальная обработка диэлектрического материала при изготовлении МПП или ПП аддитивными методами заключается в его подтравливании и придании шероховатости для увеличения прочности сцепления с металлизацией. Подтравливание диэлектрика проводится последовательной обработкой сначала в серной кислоте, а затем в плавиковой или в их смеси (5:1) при температуре 50-60°С. Серная кислота образует с эпоксидной смолой сложный, растворимый в воде, сульфированный полимер, а обнажившееся стекловолокно вступает в реакцию с плавиковой кислотой. Скорость травления составляет 40-80 мкм/мин. После обработки платы нейтрализуют в растворе щелочей и тщательно промывают.
Увеличение шероховатости диэлектрических поверхностей и клеевых композиций достигается механической (гидроабразивной) или химической обработкой.
Контроль качества подготовки металлических поверхностей заготовок ПП оценивают по полноте смачивания их водой. Состояние диэлектрических поверхностей проверяют микроскопическими исследованиями, измерением высоты микронеровностей, проведением пробной металлизации и оценкой ее прочности сцепления с основанием. Объективным показателем качества является также проверка сопротивления изоляции после пребывания в камере влажности.
К подготовительным операциям относится упаковка ПП, которая производится на автоматическом оборудовании. Заготовки со скоростью 120-240 шт./ч помещаются между слоями полиэтиленовой пленки, которая при помощи тепловой обработки заваривается с четырех сторон и образует герметичную упаковку.
формирование токопроводящих элементов печатных плат [3, 4]
Технология металлизации.
Формирование токопроводящих элементов ПП осуществляется двумя основными методами: химическим (бестоковым) и электрохимическим. Химическая металлизация используется в качестве основного слоя при изготовлении плат аддитивным методом, при этом после соответствующей активации на них осаждают химическим способом проводящий слой толщиной до 3 мкм, а затем его усиливают гальваническим способом до необходимой толщины, так как гальваническое осаждение значительно дешевле. В основном этот метод применяют для осаждения меди и никеля в межслойных переходах ПП
Процесс химической металлизации основан на окислительно-восстановительной реакции ионов металла из его соли в определенной среде, при которой необходимые для восстановления катионов металла электроны получают в результате окисления специальных веществ, называемых восстановителями.
Для создания межслойных переходов в ПП и для изготовления проводящего рисунка плат используют, как правило, восстановительную ванну для меднения в одном из растворов, приведенных в таблице.
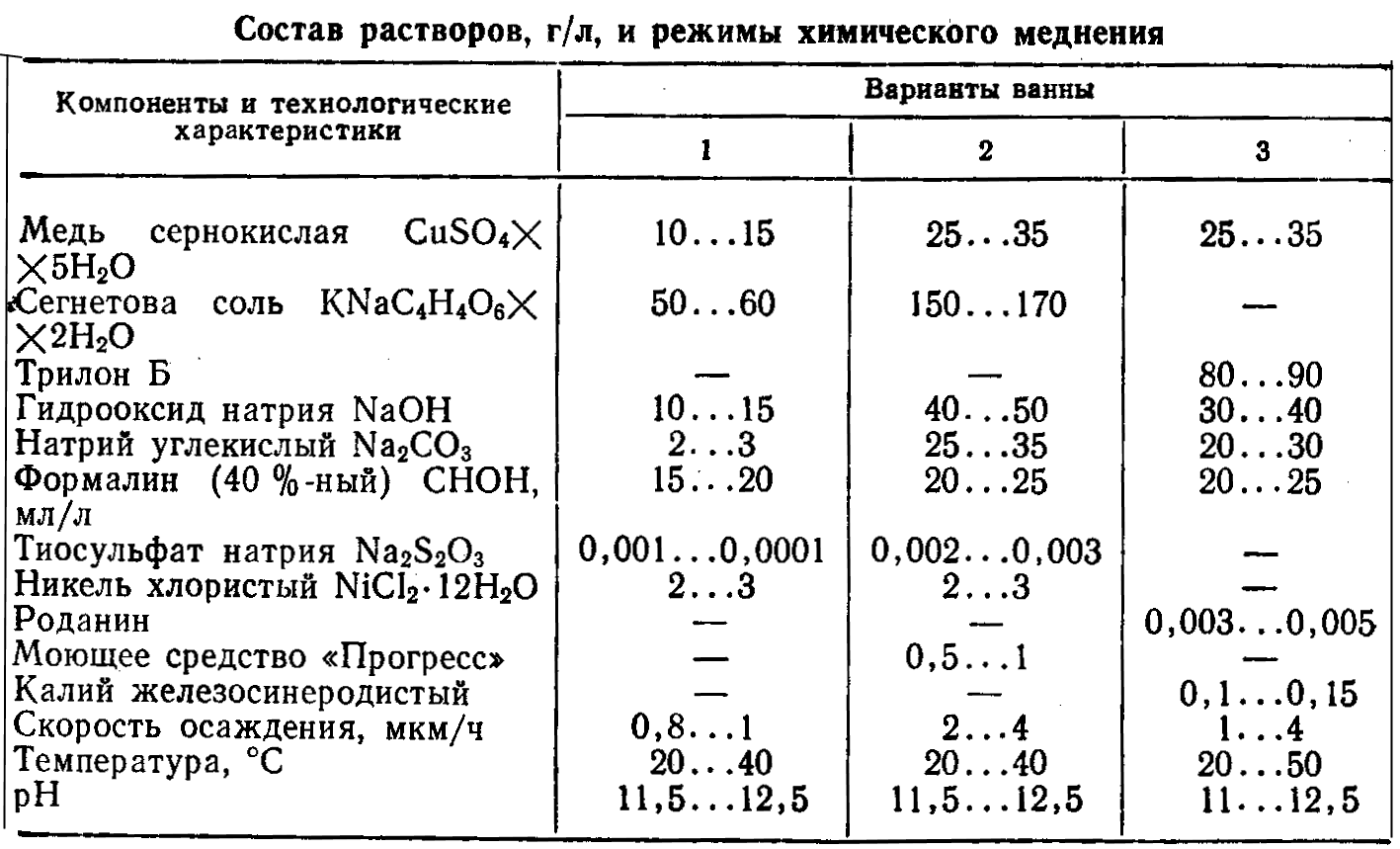
Разбавленные растворы (1) характеризуются более высокой стабильностью, чем концентрированные (2 и 3), но в них выделение меди происходит с низкой скоростью. При температуре ванны в 35-40 °С получают за 30 мин слой меди толщиной 0,5 мкм. Высокопроизводительные восстановительные ванны для меднения позволяют при температуре примерно 50 °С осадить слой в 25 мкм в течение 4 ч. Для облегчения удаления водорода, выделяющегося в процессе меднения, в растворы вводят поверхностно-активные вещества (моющее средство), а процесс ведется с плавным покачиванием плат (8-10 колеб./мин при амплитуде 50-100 мм).
В последнее время рекомендуют применять для получения металлического проводящего слоя также ванны для химического никелирования, которые являются более стабильными и простыми в управлении. В ванны добавляют стабилизаторы, способствующие тому, что реакции происходят только на нужной поверхности, а не в растворе. При температуре 52-54 °С, рН=5÷6 и соотношении площади поверхности и объема ванны 1 дм2/л за 7-10 мин образуется слой никеля толщиной в 1 мкм.
Активация поверхностей диэлектриков.
На диэлектриках реакция восстановления протекает при наличии на их поверхности каталитически активного слоя. Для придания диэлектрику способности к металлизации производят двухступенчатую операцию сенсибилизации и активирования.
Сенсибилизация — это процесс создания на поверхности диэлектрика пленки ионов двухвалентного олова, которые впоследствии обеспечат восстановление ионов активатора металлизации. ПП хорошо очищают в специальных растворах, особое внимание обращают на обезжиривание. Если печатные платы имеют отверстия особо малых диаметров, то их необходимо очищать в ультразвуковых ваннах. Затем платы опускают на 3-5 мин в солянокислый раствор дихлорида олова (SnCl2 – 5-10 г/л, HCl – 20-40 г/л). Чтобы предотвратить разрушение раствора в результате гидролиза, необходимо поддерживать высокую концентрацию кислоты. Постепенное разбавление сенсибилизирующей ванны водой, остающейся на платах после промывки, предотвращают, предварительно погружая заготовку в 10%-ную HCl. Время работы сенсибилизирующей ванны можно существенно повысить, добавляя в нее гранулы олова. После сенсибилизации платы промывают в холодной воде. При этом на их поверхности образуется нерастворимая и несмываемая гидроокись олова:
SnCl2 + 2 H2O Sn(OH)2 + 2 HCl.
Активирование заключается в том, что на поверхности, сенсибилизированной двухвалентным оловом, происходит реакция восстановления ионов каталитического металла. Обработку проводят в растворах благородных металлов, преимущественно палладия (PdCl2 – 0,5-2 г/л, НС1 – 10-20 мл/л) в течение 3-5 мин. Адсорбированные на поверхности плат ионы олова восстанавливают ионы палладия:
Sn2+ + Pd2+ Pd + Sn4+.
Атомы палладия являются высокоактивным катализатором для химической металлизации на поверхности диэлектрика. После активации необходимо хорошо промыть заготовки, чтобы не загрязнять ванны химической металлизации. Управление ванной (концентрацией реактивов, величиной рН), чистота ванны (содержание и виды примесей) и степень предварительной очистки плат определяют качество покрытия поверхности палладием, а вместе, с тем качество последующей химической металлизации.
Применяется также одноступенчатая активация в коллоидном растворе, который содержит НСl, катионы Sn2+, Sn4+ и Pd в коллоидной форме (0,1 - 1 г/л). Одноступенчатую активацию проводят при комнатной температуре. Ванну не подвергают регенерации, а эксплуатируют до полной выработки, после чего составляют заново. Для покрытия 100 м2 поверхности необходимо примерно 2 г палладия. При одноступенчатой активации в ванне происходят те же процессы, что и при двухступенчатой активации. При погружении ПП в ванну зародыши палладия, как и катионы Sn2+ и Sn4+, адсорбируются одновременно. При последующей промывке ПП в результате реакции воды с ионами Sn получаются гидроксил-хлориды и четырехвалентные соединения олова, при этом продукты гидролиза удаляются, а палладий остается адсорбированным.
Основными проблемами химической металлизации являются низкая производительность, сложность процесса, использование дорогостоящих материалов. Для устранения указанных недостатков разрабатываются методы беспалладиевой металлизации, например термохимический. Процесс проводится в растворе (г/л): кальций фосфорноватисто-кислый 130-170, медь сернокислая пятиводная 200-250, гипофосфат аммония 6-10, аммиак (25%) 200-300 мл/л. После обработки платы выдерживаются в термошкафу при 100-150°С в течение 8-10 мин. В результате термического разложения комплексной соли гипофосфита меди на поверхности ПП и в монтажных отверстиях образуется электропроводящее покрытие, которое служит основой для электрохимического наращивания металла.
Конечным продуктом химической металлизации является готовая печатная плата или промежуточная заготовка, которая затем подвергается гальваническому наращиванию. В этом случае безукоризненная химическая металлизация является основой для хорошего качества гальванического покрытия. Во время гальванического процесса наращиваются не только гладкие поверхности химически осажденного слоя металла, но и все выступы, неровности и прочие дефекты. Каждая неровность, вызванная сверлением или травлением, покрывается без малейшего эффекта выравнивания. Так как гальванический слой растет преимущественно вертикально, возникают причудливые образования, которые могут затруднить установку элементов на печатные платы и пайку. Причиной появления пор при химической металлизации могут быть остатки химических растворов очистки и травления в микротрещинах диэлектрика, пористые образования на стенках отверстий. Они являются продуктами распада материала основы, образующимися при очистке и травлении, или следствием грубой механической обработки.
Гальваническая металлизация при производстве ПП применяется для усиления слоя химической меди, нанесения металлического резиста (например, олово - свинец толщиной 8-20 мкм с целью предохранения проводящего рисунка при травлении плат, защиты его от коррозии и обеспечения хорошей паяемости), создания на части проводящего рисунка (например, на концевых печатных контактах) специальных покрытий (палладий, золото, родий и т. п.) толщиной 2-5 мкм. Основой для гальванической металлизации является водный раствор солей металла, содержащий осаждаемый материал в виде положительно заряженных ионов. Необходимые для восстановления электроны поступают от внешнего источника постоянного тока. Под действием внешнего напряжения ионы металла движутся к катоду, присоединяют электроны и осаждаются на нем как нейтральные атомы. Примером может служить восстановление меди: Cu2+ + 2e- → Cu. Катодом является предмет, подлежащий покрытию, например ПП. В качестве анода преимущественно используют осаждаемый материал, реже – не растворяющийся платиновый или стальной электрод. Процессы, происходящие на аноде и катоде, имеют сложный характер. Их определяют реакции переноса, проникновения и адсорбции, которые, в свою очередь, зависят от концентрации компонентов ванны и температуры.
Заготовки плат, закрепленные на специальных подвесках - токоподводах, помещают в гальваническую ванну с электролитом. Режим электрохимической металлизации выбирают таким образом, чтобы при высокой производительности были обеспечены равномерность толщины покрытия и его адгезия.
Равномерность толщины осажденных слоев зависит от: 1) габаритных размеров металлизируемых плат (с увеличением ПП равномерность покрытий снижается, что может быть частично скомпенсировано увеличением расстояния между анодами); 2) диаметров металлизируемых отверстий (отношение диаметров к толщине платы должно быть не менее 1/3); 3) расположения плат в ванне (для улучшения равномерности платы размещают симметрично и параллельно анодам, площадь которых должна в 2-3 раза превышать площадь металлизации при расстоянии между электродами не менее 150 мм); 4) оптимальной плотности тока (при низких значениях уменьшается толщина покрытия в центре платы, при высоких происходит утолщение покрытия на углах и кромках платы); 5) наличия специальных экранов между электродами.
Адгезия гальванического покрытия зависит от качества подготовки поверхности под металлизацию, длительности перерыва между подготовкой поверхности и нанесением покрытия, от соблюдения режимов процесса.
Для меднения ПП применяют различные электролиты. Рекомендуют для предварительной металлизации борфтористоводородный электролит следующего состава (г/л): Cu(BF4)2 – 230-250, HBF4 – 5-15, Н3ВО3 – 15-40. Процесс ведут при температуре 20±5 °С, плотности тока 3-4 А/дм2 скорости осаждения 25-30 мкм/ч. Более пластичные и равномерные осадки получаются в сернокислых электролитах. Для улучшения рассеивающей способности в электролит добавляются выравнивающие добавки, а процесс ведут непрерывной подачей свежего раствора меднения непосредственно в сквозные отверстия. Сернокислый электролит имеет состав (г/л); CuS04-5 H20 – 100-200, H2S04 – 150-180, NaCl - 0,03-0,06.
Электролитический сплав олово-свинец должен иметь состав, приближающийся к эвтектическому, что обеспечит последующее оплавление при минимальной температуре и хорошую паяемость ПП. Это достигается выбором оптимального режима осаждения и строгим его поддержанием. Содержание олова в осадке возрастает при понижении плотности тока, увеличении количества вводимых добавок, снижении температуры электролита, увеличении олова в электролите и сильном его перемешивании.
Повышение объемов производства и требований к качеству ПП, усложнение аппаратуры и ее микроминиатюризация требуют развития перспективных методов электрохимической металлизации и производительного технологического оборудования. Одним из эффективных путей улучшения качества покрытий является использование нестационарных режимов электролиза. Осаждение металла в этом случае проводится под действием периодических токов - импульсного, реверсивного, произвольной формы различной частоты и скважности. Под действием реверсивного тока происходит сглаживание микрорельефа покрытия, повышается его равномерность по поверхности платы и в монтажных отверстиях. Это объясняется тем, что во время прямого импульса происходит осаждение металла, а во время обратного - преимущественное растворение выступающих участков. Одновременно снижаются внутренние напряжения в покрытиях, повышается их пластичность.
При импульсном токе измельчается структура покрытия (кристалл растет во время импульса тока и пассивируется во время паузы), уменьшается пористость, повышается электропроводность покрытия вследствие совершенства структуры и уменьшения включаемых в осадок примесей. Наибольшей эффективностью обладает оборудование, обеспечивающее программное ведение процесса. Оно позволяет на основании модели ТП автоматически изменять форму тока, его амплитуду, частоту, скважность и все временные параметры.
Формирование рисунка печатных плат.
Нанесение рисунка схемы на ПП необходимо для получения защитной маски требуемой конфигурации при осуществлении процессов металлизации и травления. Наиболее распространены в промышленности сеткографический (офсетной печати) и фотохимический методы.
Сеткографический метод получения рисунка ПП основан на применении специальных кислотостойких быстросохнущих красок, которые после продавливания через трафарет закрепляются на поверхности заготовки в результате испарения растворителя. Основными видами специальных трафаретных красок являются следующие: защитные щелочесмываемые; защитные гальваностойкие, смываемые органическим растворителем (хлористым метиленом). Для получения маркированных знаков используются трафаретные пентафталевые краски.
Качество наносимого защитного слоя определяется вязкостью используемых трафаретных красок. Ее оптимальная величина устанавливается исходя из температуры, номера сетки, характера изображения, наличия орошения формы и др. При оптимальном значении вязкости краска не должна самопроизвольно растекаться ни по печатной форме, ни по заготовке, должна легко и равномерно растекаться под воздействием ракеля и продавливаться сквозь отверстия печатающих элементов формы.
Ракель обычно изготавливают из листовой маслобензостойкой резины толщиной около 8 мм и высотой не менее 25 мм. Тщательно отполированная поверхность ракеля обеспечивает высокое качество.
Заготовка в станках трафаретной печати устанавливается с технологическим зазором 2-3 мм. Увеличение зазора приводит к повышению четкости рисунка, но одновременно повышается износ сетки. Постепенный отрыв сетки от заготовки в процессе нанесения рисунка уменьшает и его искажение, и износ сетки. Нанесение защитной краски через сетчатый трафарет осуществляется автоматическим оборудованием, которое включает загрузочное устройство, машину для рихтовки плат, сеткографический станок, сушильную печь, накопитель готовых изделий.
Загрузка ПП в станок происходит посредством ленточного конвейера. Подведенная заготовка фиксируется в рабочей зоне на штифтах с точностью ±25 мкм и закрепляется при помощи вакуумной системы. Краскодозирующим устройством краска подается в зону обработки, а ракель продавливает ее через ячейки трафарета. В системе управления ракелем регулируется угол наклона, скорость движения, давление и диапазон хода. Время, затрачиваемое на один цикл печатания, составляет 5-7 с. Смена трафарета и настройка станка на новый тип плат производится по контрольному шаблону. В станках для одновременного нанесения рисунка на две стороны заготовки ПП устанавливается вертикально.
Закрепление краски на заготовке осуществляется сушкой. Краски с органическими растворителями сушат в туннельных конвейерных печах горячим воздухом при температуре 150-180 °С или под действием ИК-излучения. Краски мгновенной сушки, содержащие мономерно - полимерные композиции и фотоинициатор, закрепляются под воздействием ультрафиолетовых лучей. Однако они имеют небольшой срок хранения и высокую стоимость.
Срок хранения отпечатанных плат в условиях производства составляет 3-5 суток. При больших сроках хранения становится затруднительным удаление краски. Снимают трафаретную краску 3-5%-ным раствором горячей (40-60°С) щелочи в течение 10-20 с. Аналогично промываются сетчатые трафареты после работы.
Фотографический метод предусматривает нанесение на поверхность заготовки ПП специальных светочувствительных материалов - фоторезистов, негативных или позитивных. Негативные фоторезисты образуют при воздействии света защитные маски вследствие реакции фотополимеризации, при этом облученные участки остаются на плате, а необлученные удаляются при проявлении. В позитивных фоторезистах под действием света происходит фотодеструкция органических молекул, облученные участки удаляются при проявлении. Фоторезисты могут быть жидкими и пленочными. Жидкие фоторезисты значительно дешевле пленочных, для работы с ними требуется несложное оборудование. Применение пленочных фоторезистов значительно упрощает ТП (исключаются операции сушки, дубления, ретуширования) и обеспечивает нанесение защитных слоев при наличии монтажных отверстий.
Жидкие позитивные фоторезисты на основе диазосоединений имеют повышенную разрешающую способность, химическую стойкость, в них отсутствует темновое дубление. Наносят жидкие фоторезисты окунанием, центрифугированием, накаткой валками, разбрызгиванием. При покрытии окунанием заготовки погружаются в кювету с фоторезистом и вытягиваются с постоянной скоростью (10-50 см/мин). Толщина слоя определяется вязкостью, скоростью вытягивания и колеблется от 4 до 8 мкм. Способ обеспечивает двустороннее нанесение фоторезиста. Недостатком является неравномерность нанесенного слоя. Применение центрифугирования и накатки валками приводит к повышению равномерности наносимых слоев. Валковые конвейерные установки имеют секции инфракрасной сушки резиста.
Сухие пленочные фоторезисты (СПФ) представляют собой структуру, состоящую из светочувствительного слоя, который помещается между защитной полиэтиленовой и светопроницаемой лавсановой пленками. Типичная толщина СПФ 20, 40 и 60 мкм, защитных СПФЗ 90, 110, 130 мкм. Тонкие слои СПФ применяют в качестве маски при травлении меди с пробельных мест, средние - для создания рисунка при нанесении слоя металлизации, а толстые - для защиты отверстий с металлизацией при травлении. Фоторезисты наносят на платы валковым методом при нагреве до 105-120 °С и плотно прикатывают к поверхности заготовки для удаления воздушных включений. Реализующие этот метод установки называются ламинаторами. Они снабжены терморегуляторами, тарированными устройствами прижима подающих валков, устройствами для обеспечения давления на заготовку и обрезания фоторезиста после его нанесения.
Экспонирование предназначено для инициирования фотохимических реакций в фоторезистах. Оно проводится в установках, состоящих из источников света, работающих в ультрафиолетовой области, рефлекторов и коллиматоров. Для плотного прилегания фотошаблонов к заготовкам плат используют рамы, оснащенные специальными откачными системами для создания вакуума.
Для проявления СПФ используют два вида установок: камерные для мелкосерийного производства и конвейерные для серийного производства. Камерные установки имеют насос для подачи проявителя под давлением, систему струйной промывки, змеевики охлаждения проявителя, таймеры, систему терморегулирования и устройства фильтрации проявителя. Конвейерные установки имеют зоны загрузки, первичного проявления, допроявления и промывки плат. Установки оснащены регуляторами скорости конвейера и давления жидкости, системами охлаждения и терморегулирования, основными и вспомогательными насосами фильтрации жидкости и отстойниками промывных вод.
После проявления оставшийся фоторезист должен быть твердым, блестящим, сплошным покрытием на поверхности заготовки с хорошей адгезией к ней, без проколов и других дефектов.
Травление меди с пробельных мест представляет собой сложный окислительно-восстановительный процесс удаления меди с непроводящих (пробельных) участков. Травление выполняют химическим или электрохимическим способом. Для химического процесса разработаны и используются в промышленности многочисленные составы на основе хлорного железа, персульфата аммония, хлорной меди, хромовой кислоты, и др. Выбор травильного раствора определяется типом применяемого резиста, скоростью травления, величиной бокового подтравливания, возможностью регенерации и экономичностью процесса.
Скорость травления меди зависит от состава травителя, условий его доставки в зону обработки, температуры раствора и количества меди, перешедшей в раствор. Скорость травления оказывает существенное влияние на качество формируемых элементов ПП. При малых скоростях время пребывания платы в травителе увеличивается, что приводит к ухудшению диэлектрических свойств оснований и увеличению бокового подтравливания. Величина бокового подтравливания оценивается фактором травления K=S/a, который представляет собой отношение толщины фольги S к величине изменения ширины печатного проводника а. Уменьшают фактор травления введением в используемые растворы специальных добавок: ионы металлов с более низким потенциалом, чем у меди (Ag, Hg, Pt, Pd, Au).
Технологический процесс травления состоит из операций предварительной очистки меди, повышающей равномерность ее удаления, непосредственно удаления меди с пробельных участков платы, очистки поверхности диэлектрика, осветления при необходимости поверхности металлорезиста и сушки.
Наибольшее распространение в технологии производства ПП получили травильные растворы на основе хлорного железа. Они отличаются высокой и равномерной скоростью травления, малой величиной бокового подтравливания, высокой четкостью получаемых контуров, экономичностью. Скорость процесса в свежеприготовленном растворе составляет 40 мкм/мин, но по мере накопления в нем ионов меди постепенно снижается и при 100 г/л составляет 5-6 мкм/мин. Повышение температуры и рН травителя относительно оптимальных значений приводит к образованию смеси фильтрующейся меди и оксида железа, который адсорбируется поверхностью диэлектрика, с трудом удаляется при промывке и ухудшает изоляционные свойства подложки.
Травитель не пригоден для получения плат, покрытых металлорезистами на основе олова. В этом случае рекомендуется применять раствор персульфата аммония. Он дешевле хлорного железа, быстро приготавливается на рабочем месте, прозрачен и невязок, не образует шлама при травлении, легко поддается регенерации. Реакция сопровождается выделением тепла, что вызывает необходимость стабилизации температурного режима. Травление приводит к большому боковому подтравливанию медных проводников, сопровождается зубчатостью краев из-за различия скоростей химических реакций по зернам металла, а раствор склонен к саморазложению.
Стабильными параметрами травления характеризуются растворы на основе хлорной меди. Разработанные кислые и щелочные составы несколько уступают по скорости растворам хлорного железа, но намного их дешевле. В них не образуется шлам, ПП легко отмываются по после обработки, а боковое подтравливание не превышает 3-6 мкм. Отсутствие в растворе посторонних катионов позволяет проводить полную регенерацию в непрерывном замкнутом цикле. Повышение производительности процесса достигается использованием раствора на основе двух окислителей - хлорной меди и хлорного железа.
Травление меди в растворе перекиси водорода проводится в кислый среде с добавлением серной или соляной кислоты. Используемые травители совместимы практически со всеми типами резистов. Получаемая H2S04 является химически чистым веществом, легко извлекается и используется для технических целей. При накоплении 60-80 кг/м2 меди раствор истощается и скорость травления снижается. Полезную емкость по меди до 130 кг/м2 имеют соляно-кислые растворы. В них травящей способностью обладают не только исходные компоненты, но и продукты реакции. Процесс травления сопровождается поддержанием состава ванны и разложением перекиси водорода.
Химическое удаление меди проводится погружением ПП в травитель, наплескиванием раствора на их поверхность или разбрызгиванием через форсунки. Давление раствора в форсунках колеблется в пределах 0,1-0,5 МПа, а струя подается перпендикулярно поверхности платы или при небольшом отклонении от перпендикуляра. Постоянное обновление окислителя в зоне обработки и удаление продуктов реакции обеспечивают высокую производительность струйному травлению, а траектория струи - незначительное боковое подтравливание. Производительное технологическое оборудование компонуется по модульному принципу и содержит модули травления, регенерации, промывки, осветления и сушки, которые объединяются транспортной системой и системой трубопроводов. Автоматические модульные линии конвейерного типа оснащаются устройствами для контроля кислотности раствора, его температуры и давления в форсунках.
Электрохимическое травление ПП основано на анодном растворении меди с последующим восстановлением ионов стравленного металла на катоде. Такой процесс по сравнению с химическим травлением обладает рядом преимуществ: упрощением состава электролита, методики его приготовления, регенерации и очистки сточных вод, высокой и стабильной скоростью травления в течение длительного периода времени, экономичностью, легкостью управления и автоматизацией всех стадий.
Широкое применение электрохимического травления сдерживается неравномерностью удаления металла по плоскости платы, что приводит к образованию невытравленных островков. Полностью реализовать преимущества электрохимического метода позволяют подвижные носители заряда, которые представляют собой частицы графита в суспензированном электролите. Эти частицы принимают заряд с анода и переносят его на поверхность меди, переводя последнюю в ионную форму. Использование электрохимического травления сводит к минимуму боковое подтравливание токопроводящих дорожек и обеспечивает разрешающую способность, равную 70-100 мкм, но стоимость технологического оборудования превышает стоимость машин для химического травления.
После удаления меди с пробельных участков ПП промывают холодной проточной водой. Если на поверхности металлических резистов (особенно Sn-Pb) в результате химического взаимодействия с травителем образуются нерастворимые соединения, вызывающие потемнение и ухудшение их паяемости, то их осветляют при температуре 18-25 °С в течение 3-5 мин. Растворы осветления готовят на основе кислот и тиомочевины, например (г/л): соляная кислота – 50-60, тиомочевина – 90-100, этиловый спирт – 5-6, моющее средство или поверхностно-активное вещество – 1-10.
Особенности изготовления МПП.
Для изготовления МПП разработано много вариантов конструктивно-технологического исполнения, номенклатура их постоянно обновляется и совершенствуется. Практический опыт изготовления МПП показывает, что наиболее технологичным является вариант МПП с металлизацией сквозных отверстий. Он позволяет получать до 20 слоев МПП, характеризуется высокой плотностью, хорошим качеством межслойных соединений, относительной простотой и экономичностью. При этом методе используются: для наружных слоев односторонний фольгированный диэлектрик, для внутренних одно- или двусторонний фольгированный диэлектрик, а в качестве межслойной изоляции стеклоткань. Из этих материалов изготавливают заготовки, в которых пробивают базовые отверстия для совмещения слоев и производят очистку поверхностей. На заготовках внутренних слоев рисунок получают с двух сторон негативным фотохимическим методом, выполняя при необходимости контактные переходы химико-гальванической металлизацией. Рисунок наружных слоев получают комбинированным позитивным фотохимическим методом. Изготовленные слои совмещают друг с другом по базовым отверстиям, прокладывая между ними межслойную изоляцию, и спрессовывают в монолитную структуру.
Внутренние слои МПП, выполненные на тонком одностороннем фольгированном диэлектрике, после стравливания медного покрытия склонны к линейной деформации. Поэтому базовые отверстия на технологическом поле заготовок пробивают после операции травления меди, ориентируясь на специальные реперные знаки.
Процесс прессования является одной из важнейших операций изготовления МПП. Монолитность структуры и точность ее элементов обеспечиваются качеством прокладочной стеклоткани, тщательностью подготовки слоев, совершенством технологической оснастки и строгим поддержанием режимов прессования.
Прокладочная стеклоткань, которая поступает на сборку пакетов МПП, должна содержать 45-52% термореактивной эпоксидной смолы с отвердителем, находящейся в состоянии неполной полимеризации. Процентное содержание смолы, растворителя и летучей фракции проверяется при использовании новой партии и через каждые 5 дней применения. При поступлении нового материала проводятся опытные запрессовки на технологических платах и контроль их качества при термических испытаниях (нагрев до 120 °С и выдержка в течение 1 ч, термоудар при температуре 260 °С в течение 10 с).
Прессование МПП проводят в специальной пресс-форме с плоско-параллельными плитами, обеспечивающей точное совмещение и фиксацию слоев с помощью направляющих штырей по углам и через каждые 100-150 мм по периметру плиты. Температурный режим прессования платы предусматривает нагрев пакета до температуры 150-180 °С, удаление летучих компонентов смолы по мере расплавления и смачивания слоев пакета, полимеризацию и затвердевание смолы, охлаждение пакета до 30-40 °С. При нагреве пакета для обеспечения теплопередачи необходимо предварительное его сжатие и плотное прилегание пресс-формы к плитам пресса. Для этого устанавливают первоначальное давление (100-300 кПа), которое препятствует удалению летучих компонентов смолы из прокладочной стеклоткани. Высокое давление прессования должно быть создано до начала затвердевания смолы в момент желатинизации, когда смола перестает течь и вязкость ее нарастает. Приложение высокого давления (1-4 МПа) до момента желатинизации приводит к выдавливанию большого количества жидкой смолы и ухудшению сцепления слоев. Приложение давления после момента желатинизации, перешедшей в твердое состояние, приводит к растрескиванию и образованию пустот, ухудшающих связь между слоями. Для объективного контроля момента желатинизации измеряют объемное сопротивление изоляции склеивающих прокладок. Под воздействием температуры по мере разжижения связывающего вещества объемное сопротивление падает, достигая минимального значения в момент начала желатинизации, а затем по мере отверждения связывающего вещества увеличивается. Регистрация объемного сопротивления проводится датчиком, который изготавливается на технологических полях заготовок из фольги методом травления. При сборке пакета МПП слои располагают таким образом, чтобы электроды были обращены друг к другу, а между ними помещалась склеивающая прокладка.
Для прессования МПП применяют гидравлические прессы, оборудованные системами нагрева и охлаждения плит и устройствами для регулирования технологических режимов. Прессы обеспечивают плоскостность и параллельность плит в пределах 0,1 мм, точность поддержания температуры на их плоскости ±3 °С, давления ±3°/о. Для повышения производительности прессования промышленностью выпускаются автоматические линии. Процессы изготовления МПП подробно рассмотрены в специальной литературе.
Покрытия и маски для наружных слоев ПП выполняются для защиты медных печатные проводников от окисления, для формирования паяльных масок, для создания износоустойчивых соединителей непосредственного контактирования.
Защитное покрытие печатных проводников серебром в настоящее время не применяется. У серебра обнаружено неприятной свойство: в условиях повышенной влажности под действием электрического поля происходит рост кристаллов-дендритов по поверхности и в глубину изоляционного основания печатной платы, что приводит к уменьшению электрической прочности изоляции.
Введение в конструкцию ПП паяльной маски является необходимым условием, т.к. обычная стеклоэпоксидная основа печатных плат не обладает достаточной теплостойкостью при температурах пайки (220-240 оС), и без паяльной маски за время, необходимое для проведения пайки, может происходить поверхностная деструкция материала диэлектрика. По методу формирования рисунка паяльные маски делятся на два типа:
- Паяльные маски, рисунок которых формируется методом трафаретной печати. Как правило, это составы на эпоксидной основе, отверждаемые термически или ультрафиолетовым (УФ) излучением. При относительной дешевизне их недостатком является низкая разрешающая способность и необходимость использования сеткографического трафарета.
- Паяльные маски, рисунок которых формируется фотолитографическим методом (фоторезистивные маски). Способ позволяет формировать маски любой сложности и в последнее время получил наибольшее распространение. Для этих целей применяются сухие и жидкие фоторезистивные материалы. Размеры окон в маске на платах 3-го и более высоких классов точности должны превышать размеры контактных площадок на величину от 0,05 до 0,1 мм.
Припой на контактные площадки наносится либо электроосаждением (с последующим оплавлением для снятия пористости осажденного металла) либо непосредственно окунанием платы, защищенной маской, в расплавленный припой. Применяются и другие варианты покрытий, обеспечивающие хорошую паяемость:
- а) Иммерсионная или химическая металлизация золотом, серебром, палладием. Применяется в ПП для аппаратуры ответственного назначения. Иммерсионный слой металла имеет способность самоограничения при росте и обычно очень тонкий (0,05-0,2 мкм).
- б) Органические покрытия, связанные с обработкой меди (составы на основе бензимидазола или имидазола).
Если на плате имеются контакты электрического соединителя непосредственного контактирования, на эти контакты должно наноситься покрытие, дающее стабильное низкое переходное сопротивление и обладающее высокой износоустойчивостью. В таких случаях применяется многослойное покрытие, в верхнем слое которого наносится золото или палладий. Толщина слоя от 0,5 до 2 мкм. Для подслоя золота обычно используют никель, что предохраняет медь от миграции через пористый золотой слой на поверхность.
Контроль и испытания плат.
Технологический процесс изготовления плат, особенно многослойных, состоит из большого числа операций, при выполнении которых возникают неучтенные возмущения, приводящие к отклонениям выходных параметров от номинальных. Контроль и испытание ПП предназначены для определения качества изготовленных изделий, под которым понимают степень их соответствия требованиям чертежа, технических условий и стандартов. На повышение качества влияют: 1) входной контроль исходных материалов; 2) соблюдение режимов и последовательности операций процесса производства; 3) использование автоматизированного технологического оборудования со средствами активного контроля; 4) организация пооперационного и выходного контроля; 5) проведение испытаний.
Входному контролю подвергается каждая партия поступающего на производство диэлектрика, фоторезиста, трафаретной печатной краски. Особое внимание уделяется технологическим свойствам материалов. Проверяются и постоянно корректируются электрофизические и химические параметры используемых технологических сред на операциях травления, металлизации.
Операционный контроль качества проводится после наиболее ответственных технологических операций. Число контрольных точек определяется совершенством и стабильностью процесса. Тщательно проверяется качество фотошаблонов и сетчатых трафаретов, монтажных отверстий, межслойных соединений. На этих операциях стремятся использовать автоматизированное технологическое оборудование с системами управления и контроля.
Основными видами выходного контроля ПП являются: 1) контроль внешнего вида; 2) инструментальный контроль геометрических параметров и оценка точности выполнения отдельных элементов, совмещения слоев; 3) проверка металлизации отверстий и их устойчивости к токовой нагрузке; 4) определение целостности токопроводящих цепей и сопротивления изоляции.
Рассмотрим характерные дефекты, имеющие место при изготовлении ПП.
Расслоение многослойной структуры возникает при использовании склеивающих прокладок с просроченным сроком годности или низким содержанием смолы, при некачественной подготовке слоев перед прессованием, при нарушении режимов прессования или механической обработки контура.
Теми же причинами вызывается отслоение элементов печатного монтажа. Вероятность его увеличивается при применения узких и длинных печатных проводников, занижения размеров контактных площадок по отношению к размерам просверленных отверстий. Дефект может устраняться подклеиванием.
Выход отверстий за пределы контактных площадок наблюдается из-за недостаточной точности оборудования и технологической оснастки, смещения слоев при прессовании, деформации диэлектрических оснований и неправильного базирования ПП при выполнении отверстий. Дефект практически не устраняется.
Вздутие происходит, если между слоями остались воздух или влага или при прессовании полное давление прикладывается раньше начала желатинизации клея. Дефект не устраняется.
Коробление плат вызывается несбалансированностью конструкции ПП, неоднородностью склеивающего материала, снятием заготовок с пресса до полного охлаждения плит. Уменьшить коробление можно терморихтовкой.
Короткие замыкания между элементами печатного монтажа могут быть вызваны некачественным травлением, смещением слоев при прессовании, малыми расстояниями между элементами печатного монтажа, попаданием посторонних металлических включений между слоями МПП при сборке.
Разрыв токопроводящих цепей обусловливается подтравливанием печатных проводников, наличием глубоких царапин на поверхности исходного материала, возникновением внутренних напряжений при прессовании, некачественной подготовкой поверхности отверстий перед металлизацией.
Геометрические характеристики ПП - толщина, диаметр отверстий, расстояние между их центрами, величина коробления, габаритные размеры и смещение отверстий относительно центра контролируются с помощью инструментов для измерения линейных размеров. Погрешности формы элементов рисунка ПП определяются визуально при (10, 20)-кратном стереоскопическом увеличении.
Проверку металлизации монтажных отверстий проводят разрушающим или неразрушающим методом. При разрушающем методе изготавливают микрошлиф и по нему определяют толщину слоя, равномерность распределения металлизации, структуру покрытия, его пористость, наличие трещин, качество срастания с элементами печатного монтажа. Экспрессную проверку качества металлизации проводят по калибровочным графикам измерением омического сопротивления контактного перехода при подаче тока 1 А. Границей качественного и некачественного соединений является значение 500 мкОм, которое уточняется для каждого монтажного перехода.
Проверка устойчивости соединений к токовым нагрузкам осуществляется на основе многочасовой работы металлизированных отверстий под током 1-3 А. Ослабленные соединения выгорают или в них увеличивается температура, изменение которой эффективно и с высокой точностью контролируется тепловизионными системами.
Целостность токопроводящих цепей и сопротивление изоляции между проводниками проверяются электрическим методом на автоматических тестерах с числовым программным управлением. Печатная плата при помощи контактного устройства соединяется на входе через коммутатор с блоком опроса, а на выходе - с измерительным устройством. Контактное устройство представляет собой матрицу из иглообразных подпружиненных контактов, расположенных в узлах координатной сетки. На каждую проверяемую цепь подается сигнал 5-12 В, результат измерения сравнивается с эталонным, и на основании этого сравнения определяется годность цепи. Снабжение блока опроса высоковольтным источником (150-1500 В) позволяет контролировать электрическую прочность изоляции.
Испытания ПП и МПП позволяют в условиях климатических и электрических воздействий оценить их соответствие техническим требованиям, предъявляемым к аппаратуре, и установить скрытые дефекты. Они разделяются на приемосдаточные, периодические и типовые.
Приемосдаточные испытания проводятся партиями не более 1000-1200 шт., изготовленными по одной конструкторской и технологической документации, и включают: 1) стопроцентный контроль габаритных и установочных размеров, внешнего вида диэлектрического основания и проводящего рисунка на соответствие конструкторской документации, величины изгиба и скручивания, правильности монтажных соединений на отсутствие обрывов и коротких замыканий; 2) выборочную проверку (3% от партии, но не менее 3 шт.) сопротивления изоляции в нормальных климатических условиях при ручном контроле и стопроцентную проверку при автоматизированном; 3) выборочный контроль (1-2 платы от ежедневной выработки) толщины металлизации в отверстиях; 4) выборочную проверку (3% от партии, но не менее 3 шт.) паяемости контактных площадок и металлизированных отверстий, а также их устойчивости к перепайкам.
Периодические испытания ПП и МПП проводятся с целью подтверждения их эксплуатационных характеристик, правильности выполнения ТП и соответствия конструкторской документации не реже одного раза в шесть месяцев. Для контроля случайным образом выбираются платы, прошедшие приемосдаточные испытания в количестве 5 плат при опытном и мелкосерийном производстве и 10 плат при серийном производстве. В объем испытаний входят: 1) многократные изгибы ГПП и ГПК (ГПП должны выдерживать 5-кратный цикл изгибов радиусом 10±0,5 мм, а ГПК 150-кратный цикл изгибов радиусом 3±'0,5 мм на 90° в обе стороны от исходного положения); 2) перепайка (5-10) отверстий и (5-10) контактных площадок, проверка паяемости (1-2 платы); 3) проверка омического сопротивления металлизированных отверстий (3 шт.) и их устойчивости к кратковременной токовой перегрузке; 4) проверка в нормальных климатических условиях целостности электрических цепей и сопротивления изоляции (но не менее чем на 5 парах проводников, в том числе цепей питания); 5) контроль внешнего вида, целостности соединений и сопротивления изоляции после воздействия климатических факторов, устанавливаемых в зависимости от группы жесткости испытаний по соответствующему стандарту.
Типовые испытания проводятся для определения эффективности внесенных изменений в конструкцию и технологию ПП. Программа испытаний составляется предприятием, изготавливающим ПП, и согласовывается с разработчиком.
Литература
- Ивченко В.Г. Конструирование и технология ЭВМ. Конспект лекций. - /Таганрог: ТГРУ, Кафедра конструирования электронных средств. – 2001. - ссылка скрыта
- Конструкторско-технологическое проектирование электронной аппаратуры: Учебник для вузов. – М.: Изд. МГТУ им. Н.Э. Баумана, 2002. – 528 с. URL: ссылка скрыта
- Технология приборостроения: Учебник / Под общей редакцией проф. И.П.Бушминского. – М.: МГТУ им. Н.Э.Баумана. URL: ссылка скрыта
- Тупик В.А. Технология и организация производства радиоэлектронной аппаратуры. – СПб: Издательство: СПбГЭТУ "ЛЭТИ" – 2004. URL: ссылка скрыта