Ниижб госстроя СССР пособие по технологии формования железобетонных изделий (к сниП 09. 01-85)
Вид материала | Документы |
Оборудование для роликового формования |
- Ниижб госстроя СССР пособие по технологии формования железобетонных изделий (к сниП, 2149.52kb.
- Пособие по проектированию защиты от коррозии бетонных и железобетонных строительных, 2915.42kb.
- Пособие к сниП 03. 11-85 по проектированию защиты, 5625.82kb.
- Сорокина) с участием Госхимпроекта Госстроя СССР (Л. М. Волкова), ниижб госстроя СССР, 1136.27kb.
- Госстроя СССР пособие по разработке проектов организации строительства и проектов производства, 1284.3kb.
- Тальконструкция Госстроя СССР с участием вниимонтажспецстроя Минмонтажспецстроя ссср,, 3240.54kb.
- Тальконструкция Госстроя СССР с участием вниимонтажспецстроя Минмонтажспецстроя ссср,, 3818.56kb.
- Строительные нормы и правила основания зданий и сооружений сниП 02. 01-83*, 1510.56kb.
- Строительные нормы и правила государственный строительный комитет СССР, 449.82kb.
- Пособие по проектированию автоматизации и диспетчеризации систем водоснабжения (к сниП, 770.91kb.
Оборудование для роликового формования
8.25. Роликовое формование осуществляется на специальных установках (рис. 14), имеющих балку, совершающую возвратно-поступательное движение, на которой закреплены принудительно или свободно вращающиеся прессующие ролики или секторы. Бетонная смесь через течки бункера подается под ролики и при движении балки с роликами захватывается последними и вдавливается слоями в форму. По мере выдавливания из-под роликов избыточного количества бетонной смеси форма с формуемым изделием перемещается в направлении, перпендикулярном направлению возвратно-поступательного движения балки. Нижняя поверхность балки удерживает (стабилизирует) отформованную часть изделия от выдавливания из формы и одновременно заглаживает открытую поверхность изделия.
8.26. Формовочная установка в целях обеспечения качественного изготовления изделий должна иметь число двойных ходов балки с прессующими роликами в пределах от 25 до 50 в минуту.
8.27. Для повышения производительности процесса и интенсивности уплотнения рекомендуется осуществлять принудительное вращение роликов (секторов), для чего установка снабжается узлом принудительного поворота.
Следует иметь в виду, что свободное вращение прессующих элементов допускается, если их количество не более двух, или при любом их количестве, если число двойных ходов балки не превышает 30 в минуту.
8.28. Смесь под прессующие ролики следует подавать равномерно, для чего должны выполняться условия:
Вт = Ви - (2а - 1) (R + d) / a и (1)
2Rкр = 3 (R + d) + Bт, (2)
где Bт - ширина течки бункера в свету, м (для исключения зависания смеси должно выполняться условие 0,3 > Вт > 0,2); Bи - ширина изделия, м; а - количество прессующих роликов (секторов), назначаемое из условия
а ³ Ви / 2 (R + d) + (0,2 - 0,3), (3)
где R - радиус прессующего ролика (сектора), м; d - расстояние от образующей ролика до ближайшей внутренней поверхности течки бункера, м; Rкр - радиус кривошипа, м.
8.29. Величина зазора между нижней кромкой точек бункера и верхней плоскостью формы (см. рис. 15) находится по формуле
D = 0,02R. (4)
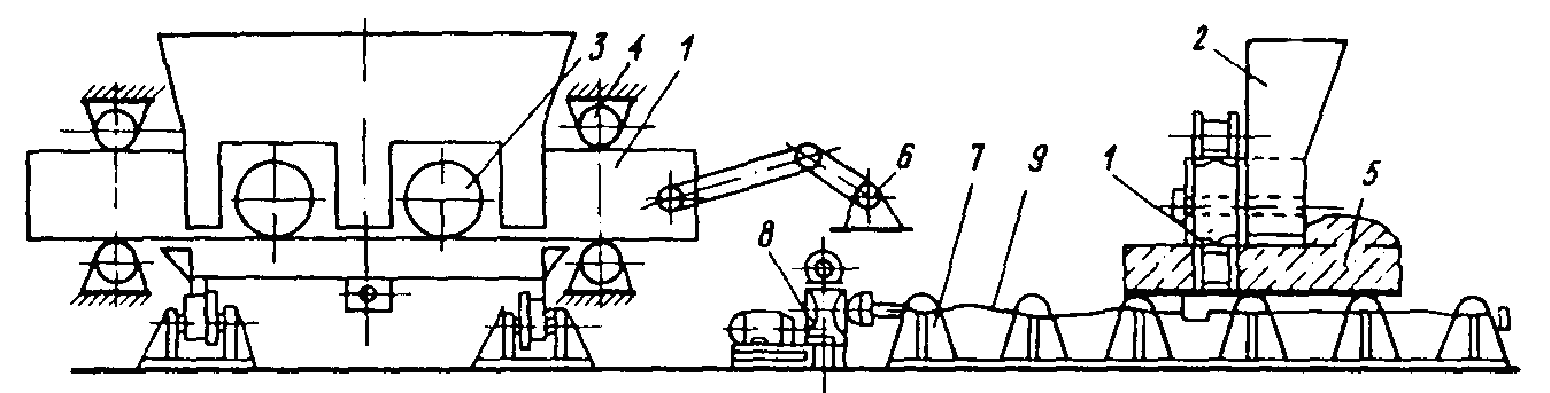
Рис. 14. Конструктивная схема устройств роликового формования
1 - балка; 2 - расходный бункер; 3 - формующие ролики; 4 - направляющие; 5 - форма; 6 - кривошипно-шатунный механизм; 7 - рольганг; 8 - привод перемещения формы; 9 - ходовой винт
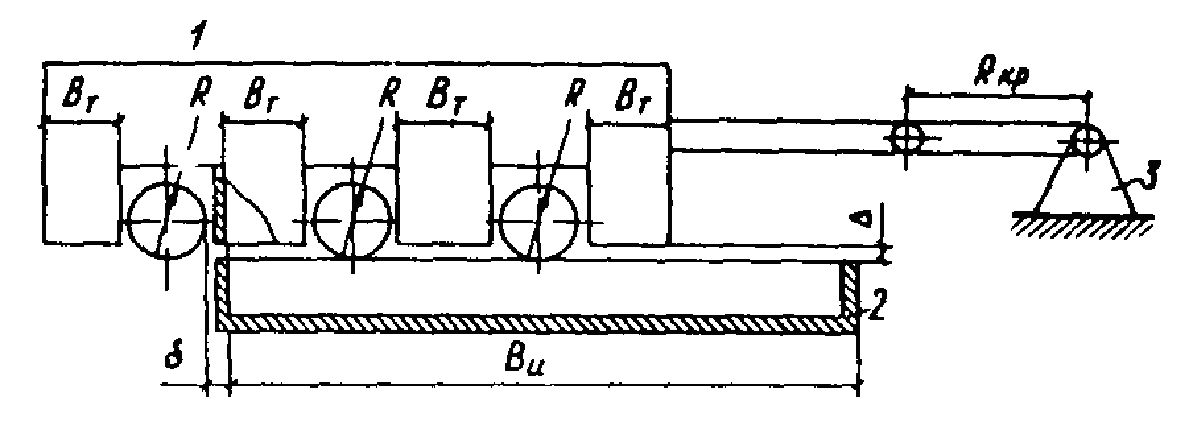
Рис. 15. Схема к расчету по формулам (6) и (7)
1 - бункер; 2 - форма с изделием; 3 - привод
8.30. Подачу смеси в течки бункера, во избежание ее зависания, рекомендуется осуществлять непрерывно, обеспечивая минимальную высоту столба, т.е. в количестве, соответствующем расходу смеси при формовании. Линейные размеры выходной течки в свету должны быть не менее 0,2´0,25 м. Вибровозбудители на вибробункере допускаются, так как они способствуют уплотнению смеси в течках бункера и препятствуют свободному истечению смеси. Допускается применение механических ворошителей.
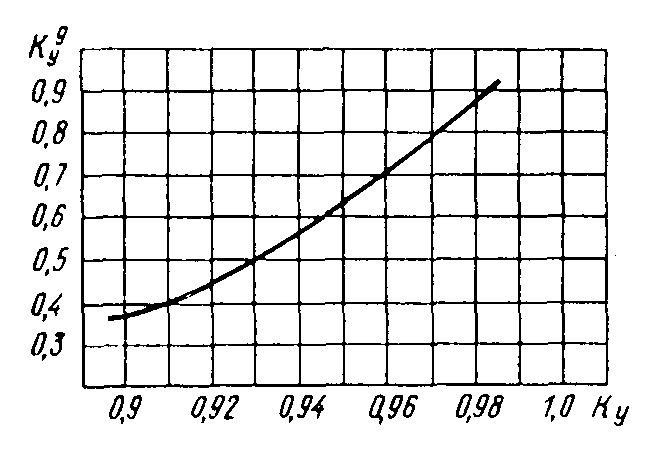
Рис. 16. Номограмма для определения Ку9 в интервале значений Ку 1…9
8.31. Скорость перемещения формы при роликовом формовании Vф ориентировочно (проектный расчет) может быть найдена по формуле
Vф = 2 · 10-2 R lр n (1 - cosa) / Ky9 hи, (5)
где lp - длина подпитываемой части прессующего ролика, м; п - число двойных ходов рабочего органа в минуту; hи - толщина формуемого изделия, м; a - угол захвата прессующего ролика, рад
a = (0,19 + 0,057 Ц/В) (0,75 + 4,65 · 10-3n); (6)
Ку - коэффициент уплотнения свежеотформованной бетонной смеси.
8.32. Номограмма для определения Ку в интервале значений К = 1,0…0,9 приведена на рис. 16.
8.33. Коэффициент уплотнения Ку = 0,96…1 может быть достигнут только при соблюдении условия
R = (0,9…1) hи. (7)
Условие (7) полностью справедливо для изделий высотой до 0,15 м. В случае формования изделий большей высоты Ку нижней части изделия будет на 15…20 % ниже, чем верхней.
По конструктивным соображениям должно соблюдаться условие
0,07 < R < 0,2. (8)
8.34. Для исключения возможности выпирания свежеотформованной бетонной смеси из-под стабилизирующей балки должно соблюдаться условие
Bd ³ 2hи, (9)
где Bd - ширина стабилизирующей балки, м.
8.35. Прессующие ролики можно устанавливать консольно или на двух опорах. Для повышения надежности их работы второй вариант предпочтительней.
Длина роликов назначается при консольном креплении
lр = 0,2…0,3 м; (10)
при креплении роликов на двух опорах
lр ³ 2,5D, (11)
где D - диаметр ролика, м.
8.36. Верхняя плоскость бортов формы должна иметь минимально возможный зазор с нижней образующей прессующих роликов (в пределах допусков на формы); непараллельность осей роликов верхней плоскости бортов формы не должна превышать 1 мм.
8.37. При повышенных требованиях к соблюдению проектной толщины изделия рекомендуется применять плавающую стабилизирующую балку, т.е. осуществлять ее поджатие к верхней поверхности бортов формы, например, с помощью пневмоцилиндров.
8.38. Зазоры между задним торцом прессующих роликов и передней кромкой стабилизирующей балки не должны превышать 4 мм, а нижняя образующая прессующих роликов должна находиться на уровне стабилизирующей плоскости балки.
8.39. Смесь, снятую стабилизирующей балкой во время калибровки, подают непосредственно в следующую форму. Накопление отходов бетона для последующего их использования не допускается.
8.40. Методика определения нагрузок, действующих на форму и на установку в процессе роликового формования, приведена в прил. 13.