Аглюков харис исхакович управление геомеханическими процессами при разработке рудных месторождений технологией с высокоплотной закладкой
Вид материала | Автореферат диссертации |
- Единые правила безопасности при разработке рудных, нерудных и россыпных месторождений, 4828.6kb.
- Единые правила безопасности при разработке рудных, нерудных и россыпных месторождений, 2400.34kb.
- Инструкция по безопасному ведению горных работ при комбинированной (совмещенной) разработке, 247.44kb.
- Железнодорожный транспорт при открытой разработке рудных месторождений, 83.05kb.
- I. Основные положения, 2511.79kb.
- А. И. Заиченко 11 августа 1980 г. N 2196-80 методика гигиенической оценки машин и механизмов,, 289.06kb.
- Программа научно-практической конференции «Современные вызовы при разработке и обустройстве, 279.73kb.
- Программа научно-практической конференции «Современные вызовы при разработке и обустройстве, 279.73kb.
- Оптимизация параметров процесса выемки бокситов при разработке месторождений открытым, 341.33kb.
- Обоснование и разработка технологии взрывных работ, обеспечивающей устойчивость горных, 484.75kb.
ОСНОВНОЕ СОДЕРЖАНИЕ РАБОТЫ
Анализ проблемы повышения эффективности управления геомеханическим состоянием массива при отработке рудных месторождений. Изучению проблемы управления геомеханическим состоянием массива при отработке рудных месторождений с закладкой посвящены труды отечественных и зарубежных специалистов. Существенный вклад в развитие технологий отработки месторождений внесли учёные А. Г. Акимов, Д. М. Бронников, Г. Кратч, В. Кортейн, Г. И. Богданов, Н. П. Влох, Н. Ф. Замесов, М. Н. Цыгалов, Ю. В. Волков, Е. В. Бошенятов, А. Б. Макаров, В.И. Борщ-Компанеец, Ю.П. Шуплецов, А.Д. Сашурин, В. Д. Палий, Е. С. Смелянский, С. Н. Зеленцов, М. А. Кузнецов, Т. Ш. Сакаева, В. Б. Дьяковский, К. Ю. Репп, А. П. Ильюшин, Д. В. Бакиновский, а также ВНИМИ, ИПКОН, ИГД, Унипромедь, Уралгипроруда и др.
Наиболее радикальным методом комплексного повышения эффективности отработки являются технологии с твердеющей закладкой. Вместе с тем исследования учёных показывают, что при отработке мощных пологопадающих и наклонных месторождений технология с твердеющей закладкой не позволяет достаточно эффективно управлять геомеханическим состоянием массива. Потенциальная несущая способность искусственных массивов не используется в полной мере. Существуют определённые пробелы в технологии возведения искусственных массивов, снижающие качество управления геомеханическим состоянием массивов и, как следствие, эффективность отработки месторождений.
Особую актуальность приобретают исследования по повышению эффективности технологии отработки месторождений с использованием принципов логистики. Современные технологии с твердеющей закладкой традиционно ориентированы на приготовление твердеющих смесей на закладочных комплексах. При такой технологии исходные материалы «подгоняются» под требования технологии приготовления и транспортировки смеси. Так, если в качестве заполнителя предполагается использовать отвальные скальные породы, то потребуется дробление в три стадии и дальнейшее измельчение компонентов смеси по условиям транспортирования. Эти процессы достаточно энергоемки (до 25 - 30 кВт·ч/м 3 смеси) и обременительны для предприятий, а с точки зрения логики нецелесообразны - сначала измельчать в пыль, затем сцементировать, ухудшив при этом прочностные параметры. Однако такая технологическая цепочка воспринимается как аксиома – существует закладочный комплекс, трубопровод, отдалённое выработанное пространство. Вместе с тем часто предпринимаются небезуспешные попытки сокращения доли твердеющей закладки либо путем утилизации пород, получаемых в процессе горных работ под землей, либо использованием гидравлической закладки при отработке вторичных камер. В последние годы предприятия часто оставляют непогашенным выработанное пространство, особенно при выемке залежей ограниченных размеров. Подобные мероприятия позволяют в той или иной мере уменьшить долю дорогостоящей твердеющей закладки, но все же в своей основе технология предполагает эксплуатацию мощных закладочных комплексов со всеми присущими им издержками. Поэтому особую актуальность приобретают исследования, в результате использования которых эффективность разработки достигается за счет снижения затрат на погашение выработанного пространства с закладкой с одной стороны, а с другой – раскрывается в полной мере потенцальная несущая способность искусственных массивов как полноценной реакции отпора. В разработанной технологии снижение затрат на погашение выработанного пространства (по сравнению с технологиями с монолитной закладкой) достигается за счет внедрения новой технологии возведения высокоплотных искусственных массивов с принципиальным изменением содержания процессов погашения выработанного пространства с закладкой, а возникновение активной реакции отпора уплотнённого массива, вследствие механизированного динамического уплотнения с усилиями до 500 кН в условиях зажатой среды, исключает развитие концентраций напряжений в опорных зонах. Активная реакция отпора уплотнённого массива позволяет компенсировать нормальные и изгибные напряжения в породах налегающего массива.
Технология погашения выработанного пространства с уплотнённой закладкой принципиально меняет роль и место закладочных комплексов. Технология возведения искусственного массива «привязывается» к основному носителю затрат – отвальным скальным породам. В существующих технологиях, использующих отвальные скальные породы в качестве заполнителя, необходимо на дробление в три стадии с последующим измельчением в мельницах. В разработанной технологии трубопроводный транспорт закладочной смеси замещается доставкой породно-твердеющей смеси раздельно с применением комбинированного транспорта. Энергоемкие процессы среднего и мелкого дробления исключаются. Отвальная скальная порода доставляется карьерными автосамосвалами к месту перепуска в скважину на поверхности после крупного дробления до крупности –160 мм по условиям транспортирования подземным конвейером. Дроблёная порода перепускается по восстающему на гор. +350 м, далее конвейером транспортируется до закладочного восстающего. Погрузка подземных автосамосвалов производится с помощью секторного затвора. Подземная транспортировка производится 20-тонными самосвалами типа МоАЗ. Возможно применение более эффективных самосвалов германской фирмы PAUS грузоподъёмностью от15 до 25 т (модели РМКТ 8000, РМКТ 1000, РМКТ 1250). Вариант автосамосвалов с жёстко смонтированным кузовом с разгрузкой с помощью гидравлического выталкивателя позволяет уменьшить высоту выработанного пространства до 3 - 3,5 м. После отработки запасов ленты вкрест простирания залежи производится закладка выработанного пространства. Отсыпка породы в заходке производится слоями толщиной 60 - 70 см в направлении от висячего бока к лежачему в отступающем порядке. На удалении 5 - 7 м от висячего бока отсыпается первый бруствер зигзагообразной формы (2 - 3 самосвала породы) поперек ширины ленты, после чего производится первичная планировка бульдозером с созданием поперечного бруствера высотой до 1 м (с одной стороны ленты, подлежащей упрочнению). Вторая, большая, часть ленты (шириной до 6 м) планируется до проектной отметки 0,6 м от поверхности уплотненного слоя. После этого осуществляется доставка жесткой твердеющей закладки, разгрузка за породный бруствер и планировка с перемешиванием. Для ее доставки можно использовать как автосамосвал, так и миксер фирмы Atlass Copco. Жесткая твердеющая смесь доставляется самоходной техникой до забоя и выгружается за породный бруствер с левой стороны заходки. После этого породный навал надвигается бульдозером на твердеющую закладку и планируется. Уплотнение осуществляется после укладки породной и породно-твердеющей закладки по всему слою (рис.1).
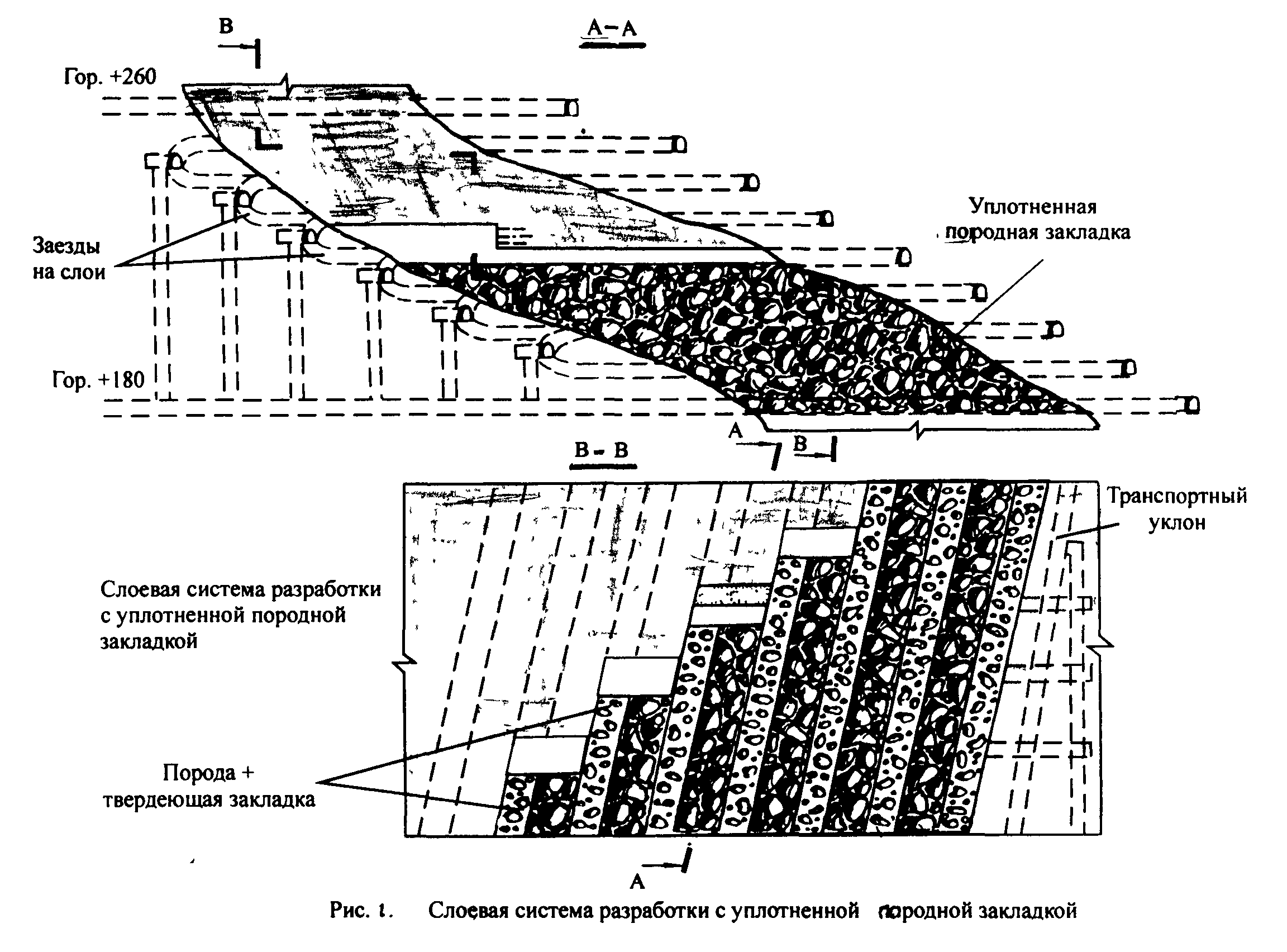
Рисунок 1- Система разработки с уплотнённой породно-твердеющей закладкой
Продолжительность отработки и закладки одной ленты протяжённостью 40 – 50 м около одной недели. Суммарное количество уплотняемых слоёв соответствует толщине отбиваемого слоя. Закладка прекращается, когда высота свободного выработанного пространства достигает 3 м. Послойное возведение искусственного массива с постоянным уплотнением незначительных по толщине слоев позволяет высококачественно уплотнять искусственный массив, а смещение участков в вертикальной плоскости, возведенных с примешиванием твердеющей смеси, создает слоеный, многократно «перевязанный» массив, обладающий повышенной устойчивостью и несущей способностью.
Применительно к Саткинскому месторождению магнезита (в начале была запроектирована камерная система разработки со сплошной твердеющей закладкой) твердеющая смесь готовилась на финском поверхностном бетонном комплексе «PARTEC». Производительность комплекса по закладке достигала 100 м3/ч. Процессы доставки руды и транспортировки породной закладки протекают последовательно во времени, что упрощает управление подземными транспортными потоками – в силу относительной равномерности интенсивности потоков (рудного и встречного породного). Послойная укладка породной и породно-твердеющей закладки с динамическим вибрационным уплотнением позволяет возводить искусственный массив в напряженном состоянии, близком к уровню давления налегающего массива. Динамическое усилие, создаваемое тяжелыми дорожными катками типа Bomag BWDM-3 (Германия), в процессе уплотнения достигает 320 и 250 кН при частоте вибрации, соответственно, 35 и 28 Гц. Масса катка 19,2 т. Катки отличаются высокой маневренностью, способны преодолевать подъем до 30º, высокопроизводительны. Часовая производительность уплотнения тяжелых скальных пород при толщине отсыпки до 0,7 м достигает 700 - 1000 м3 (степень уплотнения от 95% по Проктору). Стоимость машины 200 000 $, стоимость эксплуатации 1 машино-часа 700 рублей. Появление этих машин в отечественных дорожно-строительных компаниях подняло строительство дорог на качественно иной уровень (возможность высокопроизводительного и качественного уплотнения дорожного основания до 95 - 98 % по Проктору при низких затратах), что в принципе не было возможным при прежних технологиях. Внедрение настоящей технологии в горнодобывающей отрасли позволит отказаться от непродуктивных издержек, связанных с дроблением, измельчением и приготовлением в больших объемах твердеющих смесей.
Технология с вибрационным механизированным уплотнением предполагает сплошную отработку запасов рудных тел. Выемка ведется в восходящем порядке лентами шириной 8-10 м (см. рис. 1). Для повышения устойчивости подработанной рудной консоли-потолочины предполагается придание наклона забою в пределах 10-15° от вертикали (в направлении искусственного массива), что создаёт дополнительную усиленную боковую плоскость опоры рудной консоли. «Забивка» породно-твердеющей смеси расклинивает боковую плоскость рудной консоли (потолочины соседней заходки) и компенсирует растягивающие напряжения в ней. Боковое давление, создаваемое уплотнённой породно-твердеющей закладкой, повышает устойчивость обнажений в заходке, особенно в местах тектонических нарушений массива.
Уплотнённая закладка. Эффект динамического воздействия на породную насыпку при уплотнении проявляется прежде всего за счет активного заполнения пустот более мелкими фракциями, смятия и уплотнения наиболее слабых частиц. В силу воздействия усилий не только в вертикальной, но и горизонтальной плоскости интенсивность заполнения существующих пустот заметно возрастает. В последующем происходит взаимодействие более прочных частей породной насыпки, интенсивно сопровождающееся процессами среза, смятия и сжатия. Высокие динамические нагрузки способствуют образованию достаточно высоких локальных напряжений, приводящих к разрушению с последующим уплотнением. Процесс уплотнения массива, включающего крупные фракции, можно условно разделить на три части (рис.2).
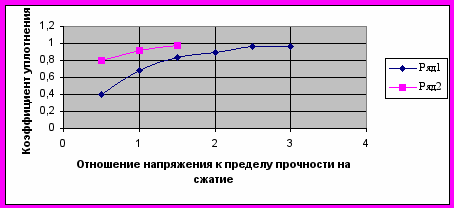
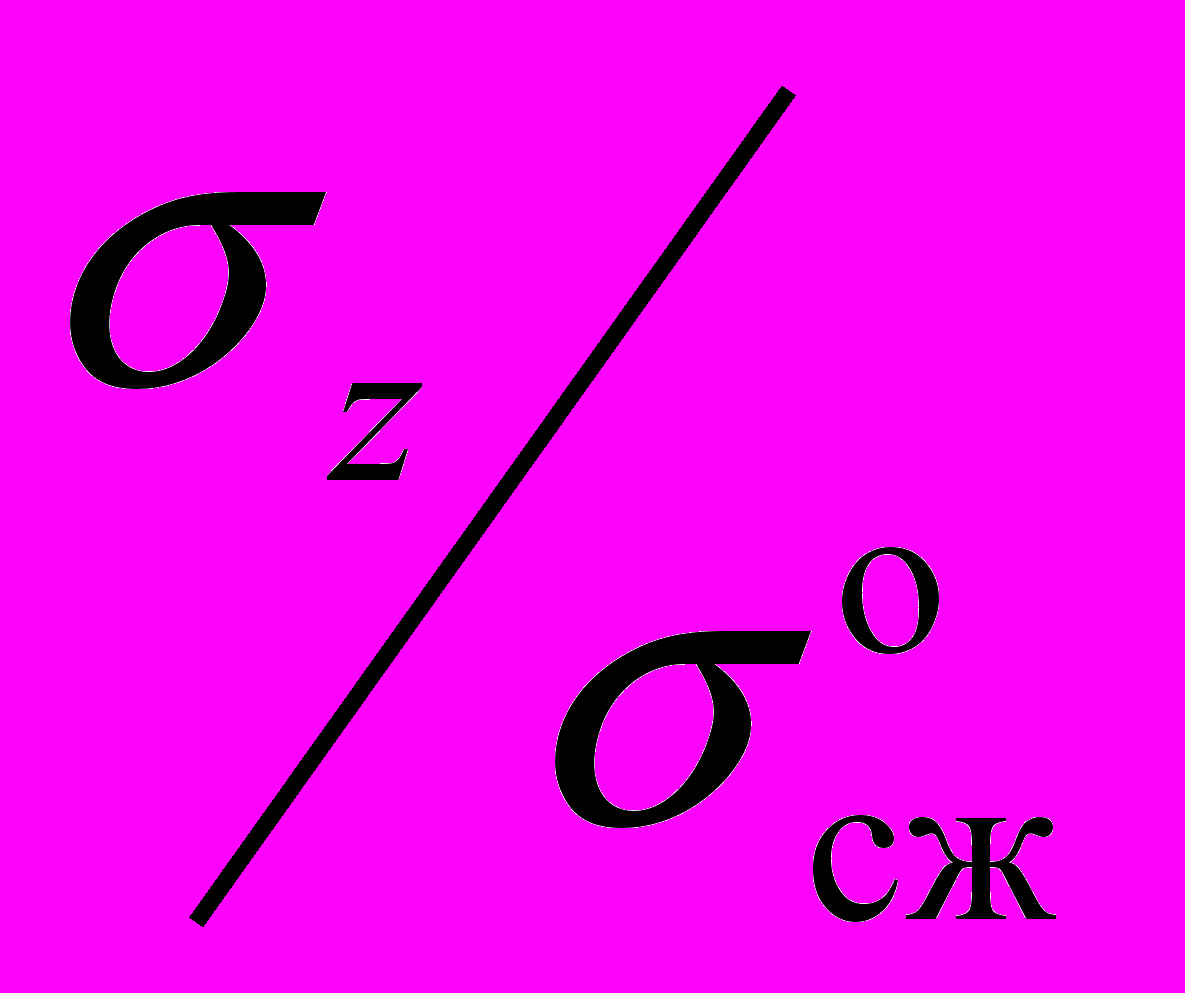
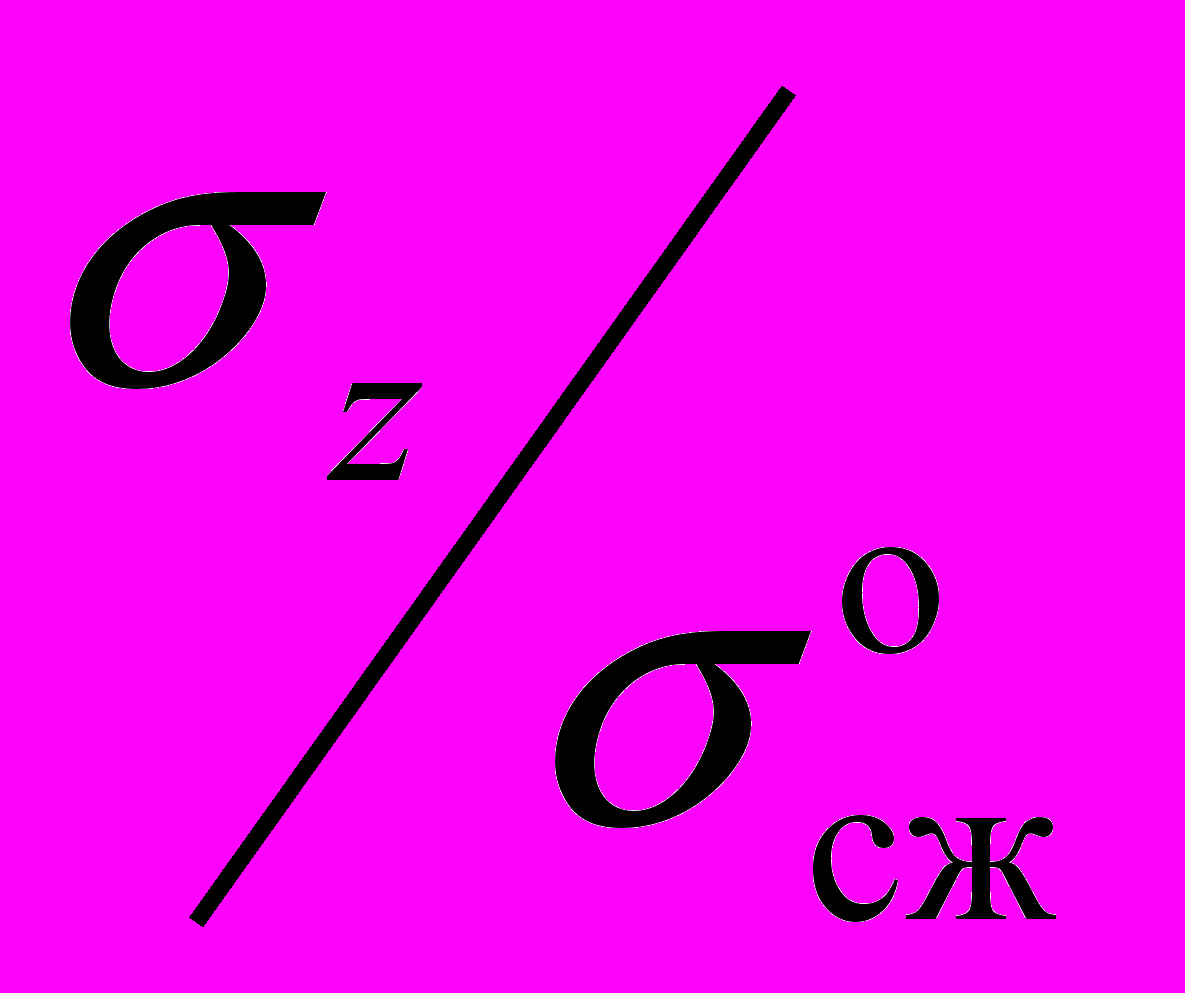
На первой, начальной, происходит перемещение крупных фракций под давлением и «выборка» пустот; на второй начинается взаимодействие между собой крупных фракций с процессом их разрушения, дальнейшего уплотнения и роста местных точек концентрации напряжений. На третьей происходит процесс переуплотнения с разрушением крупных фракций в условиях, близких к объемному сжатию, при наличии некоторой податливости сыпучего массива в плоскости приложения сжимающих сил. Первая стадия уплотнения (при статическом нагружении) протекает при нагрузках, не приводящих к возникновению разрушающих напряжений; вторая - при разрушающих напряжениях и превышающих его на 15 - 50% и третья – при напряжениях, превышающих предел прочности в два-три раза. По достижении предела упругости появляется первая макроскопическая плоскость
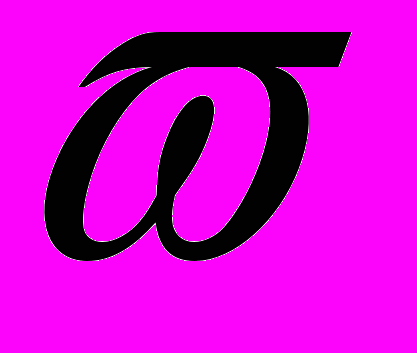
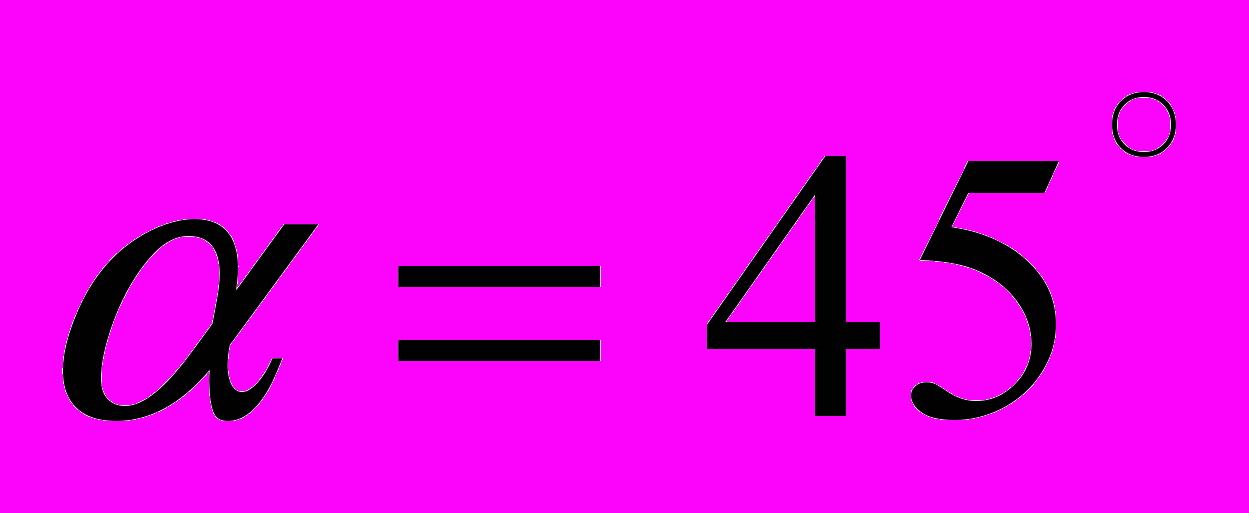
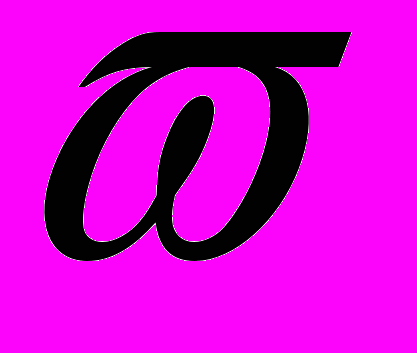
Участок диаграммы от предела упругости до предела прочности характеризуется однородностью деформации по всему объему образца. На пределе прочности однородность деформации прекращается. Процесс локализуется на наиболее слабых плоскостях сдвига, остальные плоскости из процесса исключаются. На оставшихся в работе плоскостях начинают уменьшаться площади сдвига. Это приводит к уменьшению сечения образца и, следовательно, к снижению общего усилия, необходимого для продолжения деформации. Однако по мере роста бокового давления в условиях объемного сжатия интенсивность роста деформаций резко падает (конец II стадии), начинается процесс переуплотнения материала при более высоких напряжениях. В условиях высокого бокового давления (более 10 - 15 МПа) сдвиговые процессы прекращаются и начинается сжатие с разрушением пород на контактах и заполнением оставшихся микропустот.
Анализируя деформации гидрозакладочного массива, твердеющей закладки, можно отметить, что связь между пустотностью и напряжением, практически прямо пропорциональна при напряжениях ниже предела прочности на одноосное сжатие. В дальнейшем эта связь носит экспоненциальный характер и интенсивность снижения деформаций заметно падает по мере роста напряжений, в такой же степени изменяется пустотность материала. Уплотнение менее крепких пород происходит, соответственно, при более низких напряжениях. Высокоплотные тонкозернистые шихтованные материалы обладают низкой пустотностью и низкими деформациями, соизмеримыми с твердеющими смесями.

Динамическое механизированное уплотнение дорожными катками. Проведенные сравнительные испытания по уплотнению щебенистых грунтов гладковальцовым и кулачковым виброкатками (рис. 3) показывают, что наибольший эффект при уплотнении скальных пород достигается при использовании виброкатков ABG-100. При уплотнении шихтованного скального материала динамическое уплотнение эффективнее статического более чем на 150 - 200% при напряжениях, достигающих 60 - 70% от предела прочности материала на одноосное сжатие. Вибрационные катки создают давление до 5 - 7 МПа, что ниже предела прочности доломита на одноосное сжатие. Но данный уровень напряжений достаточен для интенсивного разрушения по контактам крупных частиц доломита. Динамическое воздействие нагрузок способствует более эффективному заполнению пустого пространства между обломочными фракциями без расходования излишней энергии на разрушение материала в процессе его уплотнения.
Исследование уплотнения крупнообломочных скальных пород было осуществлено с помощью радиоизотопного влаго-плотномера «Troxler-3440». При статическом воздействии уплотняющих нагрузок для достижения равного эффекта по уплотнению скального материала необходимы напряжения превышающие предел прочности на одноосное сжатие в два - три раза. Динамическое механизированное уплотнение породной и породно-твердеющей отсыпки производится тяжелыми (20т) дорожными катками типа Bomag BWDM-3 (Германия). Сравнительные испытания по уплотнению щебенистых грунтов вибрационными катками (см.рис. 3) показывают, что наибольший эффект при уплотнении скальных пород достигается за 4 - 6 проходов катка, за 8 – 10 проходов катка плотность укладки достигает 0,97 - 0,98 по Проктору.
Усилие вибрации, создаваемое катком, составляет 304,8 и 243 кН при частоте вибрации 35 и 29 Гц, соответственно. При статическом уплотнении для достижения равного эффекта по уплотнению необходимы напряжения, многократно превышающие предел прочности на сжатие (два - три раза). Анализируя динамическое вибрационное уплотнение и деформационные характеристики породной и породно-твердеющей закладки, можно отметить, что по степени уплотнения массива динамическое вибрационное уплотнение не уступает технологии с твердеющей закладкой. Имеет существенное качественное преимущество – он не даёт усадки и деформаций при давлениях до 5-7 МПа.
Уравнение равновесия сил в системе: бандаж катка - закладка имеет вид
FB = Fstat + Fz - ma,
где FB – сила реакции отпора уплотненного массива; Fstat – статическая нагрузка; Fz – центробежная сила; m - масса бандажа; a - ускорение.
Смещение бандажа Х = А∙sinωt, ускорение a = -Aω2 sinωt,
где А - амплитуда; ω - угловая скорость.
ma = - m Aω2 sinωt, при частоте колебаний 29 и 35 Гц , амплитуда – 1,8/0,9 и 1,84/0,82 мм, центробежная сила 320 и 250 кН, масса катка 18016 кг (BOMAG BW 217D-2).
Пустотность крупнообломочного материала зависит от степени заполнения пустот мелкой фракцией. При этом пустотность однородной крупнообломочной фракции может достигать 40 - 45%. Под действием давления на первоначальном этапе начинается процесс уплотнения и перемещения более тонких фракций в свободное пространство. Дальнейшее нагружение приводит к контактному взаимодействию крупнообломочных фракций между собой. При механизированном динамическом уплотнении крупнообломочных фракций, включающих не менее 30% мелкой фракции, степень уплотнения выше, чем у твердеющей закладки.
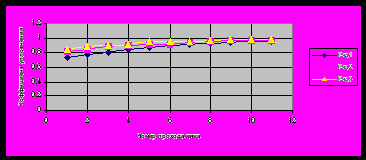
Рисунок 3 – Изменение коэффициента уплотнения скальных грунтов в зависимости от количества проходов катка ABG-100 (гладковальцовый вибрационный каток)
Ряд 1 – грунт щебенистый, крупнообломочный с 20% мелкозема;
ряды 2 и 3 - грунт щебенистый, крупнообломочный с 30% мелкозема
С целью создания монолитных искусственных массивов с устойчивостью вертикальных обнажений не менее 10 м были исследованы технологии совместной укладки породной засыпки и низкомарочного состава бетона (М-100), близкого по прочностным свойствам жесткой твердеющей закладке. Соотношение скальной породной засыпки и бетонной смеси 4 : 1. Перемешивание смеси при укладке осуществлялось бульдозером. Были проведены также исследования уплотнения породных массивов сцементированных глинопесчаной смесью в количестве до 30%. Степень уплотнения породно-твердеющей закладки достаточно высока и достигает 0,98 по Проктору, т.е. близка плотности естественного нетронутого массива (рис. 4). Данные массивы отличались как высокой плотностью, так и высокой прочностью массива, достигающей 7 МПа. Результаты промышленных исследований производительности уплотнения тяжелых скальных пород при строительстве дорог, представлены в табл.1.
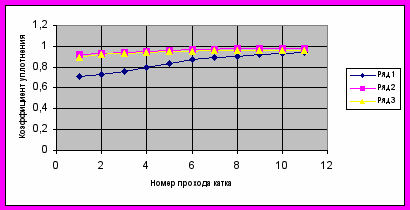
Рисунок 4 – Изменение коэффициента уплотнения скальных грунтов (ряд 1) и массивов, перемешанных с твердеющей смесью (ряд 2) и глинопесчаными составами (ряд 3), в зависимости от количества проходов гладковальцового катка ABG-100.
Ряд 1 – дробленый доломит фракции 0 - 200 мм с включением мелкой фракции (0 - 6 мм) в количестве 10%; ряд 2 – дробленый доломит фракции 0 - 200 мм с твердеющей смесью до 20%; ряд 3 – дробленый доломит фракции 0 - 200 мм с включением глинопесчаной смеси до 30 %
Следует отметить что, несмотря на примерно равную пустотность твердеющей закладки и уплотнённой (от 2 до 5 %), это качественно разная пустотность. Природа остаточной пустотности уплотнённой закладки обусловлена процессами уплотнения и переуплотнения в результате воздействия значительных динамических нагрузок в условиях объёмного сжатия. Структура уплотнённого массива сродни предварительно напряжённой сотовой конструкции. Твердеющая закладка, напротив, представляет собой разгруженную конструкцию, и деформации её при напряжениях, соизмеримых с давлением налегающей толщи пород на глубине 300 – 400 м, составляют не менее 3%.
Высокий уровень прочностных свойств массива и низкие деформации свидетельствуют о высоких качественных характеристиках процесса механизированного динамического уплотнения. С экономической точки зрения эффективность также бесспорна – цена эксплуатации 1 машино-часа, по данным ЗАО «Южуралавтобан», около 500 руб., то есть менее 1руб/м3 на планировку и уплотнение. Себестоимость доставки в выработанное пространство и планировки породной закладки на шахте «Магнезитовая» около 70 руб/м3. Что же касается капиталовложений, здесь также выигрышная ситуация по сравнению с традиционной технологией с твердеющей закладкой. Стоимость катка ABG-100 в пределах 200 тысяч долларов США, закладочного комплекса производительностью до 500 тыс. м3 в год около 10 млн. долларов (данные института «Уралгипроруда»).
Таблица 1- Производительность уплотнения скальных пород, м3/ч
Количество проходов | Скорость, км/ч | Толщина уплотнённого слоя, см | Уплот- нённая пло- щадь, м2/ч | ||||||||||
20 | 30 | 40 | 50 | 60 | 70 | 80 | 90 | 100 | 110 | 120 | |||
2 | 1 4 5 | 475 430 825 | 727 990 1218 | 990 1320 1650 | 1238 1650 2063 | | | | | | | | 2455 3300 4125 |
4 | 1 4 5 | 248 330 413 | 371 495 619 | 485 650 815 | 619 825 1052 | 743 980 1218 | 867 1075 1394 | 990 1320 1650 | 1114 1485 1837 | | | | 1236 1550 2022 |
6 | 1 4 5 | 165 220 275 | 247 330 412 | 330 440 540 | 413 550 688 | 495 660 825 | 578 770 963 | 660 880 1080 | 743 990 1238 | 825 1100 1353 | 908 1210 1513 | | 825 1100 1323 |
8 | 1 4 5 | 124 145 201 | 186 227 104 | 247 320 412 | 109 402 516 | 371 485 609 | 433 578 722 | 495 660 825 | 553 743 928 | 619 825 1021 | 681 908 1034 | 743 990 1171 | 610 805 1011 |