Научно-технические основы создания внешней изоляции электрооборудования высокого и сверхвысокого напряжения
Вид материала | Автореферат диссертации |
- Методика измерения сопротивления изоляции электрооборудования многофункциональным, 77.94kb.
- Удк 621. 319. 4 Закономерности старения изоляции и оценка срока службы силовых конденсаторов, 64.84kb.
- Научно-технические основы создания систем питания высоковольтных устройств пыле-, 491.12kb.
- 7. Изоляция кабельной линии и аппаратов высокого напряжения, 284.94kb.
- Рефераты публикуемых статей, 56.15kb.
- Пособие для разработки методик по электрическим измерениям и испытаниям отдельных видов, 11790.39kb.
- Перенапряжения и координация изоляции, 49.42kb.
- Р. Х. Бахтеев (зао «Казанский Рецэн»), 190.97kb.
- Технические требования к автомобилям, участвующим в рейде. Допустимые технические изменения, 64.42kb.
- Удк 620. 197. 3: 621. 311. 2 Ор3, 1584.41kb.
7. Конструирование и технологические особенности полимерных изоляторов
7.1 Трекингостойкость полимерных материалов
Полимерный опорный изолятор представляет собой сложную конструкцию, в которую входят стеклопластиковая труба или стержень с нанесенным на них покрытием для защиты от внешних воздействий и фланцы.
Стеклопластиковые стержни и трубы не могут длительно эксплуатироваться без дополнительного защитного покрытия в виде ребристой оболочки, так как под воздействием атмосферных условий в сочетании с воздействием рабочего напряжения на поверхности стеклопластикового стержня или цилиндра развивается трекинг и эрозия, что приводит к снижению их электрических характеристик и последующему выходу из строя.
На основании анализа опыта эксплуатации и результатов собственных исследований сделан вывод, что комплексу требований к полимерным изоляторам наружной установки наилучшим образом удовлетворяют защитные оболочки из кремнийорганических (силоксановых) резин. Они технологичны, позволяют получать химические соединения между оболочкой и стеклопластиковым стержнем, сохраняют эластичность в условиях холодного климата, обладают необычайно высокой устойчивостью к действию влаги, озона, солнечной радиации и действию поверхностных частичных разрядов, т.е. являются трекингостойкими. Гидрофобная поверхность кремнийорганических резин приводит к тому, что на поверхности изоляторов осаждающаяся влага собирается в капли и скатывается, не создавая сплошной плёнки увлажнения.
При наличии проводящего слоя, связанного с загрязнением и увлажнением изоляции, по поверхности покрытия протекает ток утечки.
Главным требованием к материалу защитного покрытия полимерных комбинированных изоляторов является их трекингостойкость, т.е. стойкость к образованию поверхностных проводящих дорожек за счет термического разложения материала, вызванного прохождением электрического тока или электрическими разрядами. Трекингостойкость является необходимым требованием для всех элементов изоляционных конструкций, которые находятся на открытом воздухе и подвергаются прямому воздействию атмосферных условий. Трекингостойкость является одной из важнейших физико-химических характеристик диэлектрического материала, применяемого в изоляционных конструкциях. Существуют численные значения этого показателя.
Для их определения разработан ряд методов испытаний, которые предусматривают искусственное создание условий для прохождения электрического тока по поверхности диэлектрика при определенной напряженности электрического поля.
Проведены исследования различных, как известных, так и новых материалов с использованием метода наклонной плоскости (ASTM-D2303, МЭК-587), дифференциального метода (ASTM-D2302) и капельного метода (МЭК-112). На основании результатов испытаний образцов силоксановой резины с различными наполнителями можно сделать вывод, что показатель трекингостойкости в значительной степени зависит от состава наполнителей и методик определения трекингостойкости.
Результаты испытаний образцов силоксановой резины различных марок на трекингостойкость представлены в таблице 3. Трекингостойкость оценивалась по времени образования проводящей дорожки длиной не менее 1,5 см при напряжении U=5 кВ.
В камере соленого тумана были проведены также испытания моделей полимерных изоляторов в виде стержней с различными вариантами защитных оболочек. Результаты испытаний приведены в таблице 4.
Таблица 3
Результаты испытаний образцов силоксановой резины на трекингостойкость
по методике «МЭК-112»
Марка образца | Показатель трекингостойкости, час |
К-69 | 500 |
407 | 600 |
471 | 500 |
410 | 850 |
422 | 600 |
Фторопласт | 850 |
Таблица 4
Результаты испытаний моделей полимерных изоляторов на трекингостойкость
в камере соленого тумана
Образец | № образца | Еср , кВ/см | Время испытаний, час | Состояние образца |
Стержни с эпокси- фторопластовым покрытием, d = 14 мм | 1 | 0,86 | 823 | Эрозия на глубину покрытия |
Стержни с эпокси- фторопластовым покрытием, d = 14 мм | 2 | 0,75 | 1120 | Эрозия |
Стержени с кремнийоргани-ческим покрытием d=16 мм | 3 | 0,5 | 1880 | Потеря изоляцион-ных свойств |
Кремнийоргани-ческие стержни , d=20 мм | 4-8 | 0,33 | 972 | Следы эро-зии, про- дукты разло-жения не являются проводящи-ми |
На основании проведенных исследований и испытаний сделан вывод, что в качестве материала для защитной оболочки ПИ наиболее предпочтительна силоксановая резина с наполнителем аэросилом и тригидратом окиси алюминия.
По результатам испытаний образцов материалов на трекингоэрозионную стойкость в качестве материала для защитного покрытия выбрана силоксановая резина горячей вулканизации типа КТ-1410 (условное обозначение 410 в таблице 3).
7.2. Основные принципы выбора конструкции ребер изоляторов
Анализ опыта эксплуатации, опубликованных данных и результатов исследований настоящей работы показали, что наиболее оптимальным материалом для изготовления защитной оболочки полимерных изоляторов является кремнийорганическая резина горячей вулканизации.
Кремнийорганическая резина является относительно дорогим полимерным материалом. Для обеспечения ценовой конкурентоспособности полимерных изоляторов по отношению к традиционным (фарфор, стекло) в первую очередь необходимо снижать материалоемкость.
Исследования показали, что весьма эффективным путем оптимизации конструкции изолятора по материалоемкости и электрической прочности является снижения толщины ребра. При этом ребро изолятора должно удовлетворять условию непробиваемости, то есть при всех видах электрического воздействия разряд должен развиваться по поверхности ребра, не приводя к пробою его тела. Это означает, что в любом сечении профиля ребра его толщина должна быть такой, чтобы пробивное напряжение по толщине ребра Uпр было не менее наибольшего разрядного напряжения по поверхности ребра Uр . Тогда условие непробиваемости ребра может быть записано как
Uпр = Кз Uр , (15)
где Кз - коэффициент запаса, учитывающий допустимые технологические отклонения и разброс пробивных напряжений твердого диэлектрика.
Для определения зависимости толщины ребра от расстояния до его кромки были проведены исследования на макетах ребер изолятора, представляющих собой диски из силоксановой резины толщиной от 2 до 16 мм и диметром от 20 до 250 мм. Для определения пробивного напряжения и разрядных напряжений при развитии скользящего разряда вдоль поверхности макетов ребер к центру диска прижимались симметрично с обеих сторон усилием в 10-15 Н латунные электроды с радиусом закругления 1,5 мм. В результате испытаний были определены как пробивные напряжения при воздействии плавного подъема напряжения промышленной частоты и стандартных грозовых импульсов 1,2/50 мкс, так и разрядные напряжения вдоль изоляционной поверхности.
Было установлено, что значения пробивных напряжений образцов увеличиваются с ростом толщины диэлектрика нелинейно. При выборе толщины диэлектрика определяющим является напряжение положительной полярности, поскольку в этом случае пробивные напряжения оказываются ниже, чем при отрицательных воздействиях. В пределах разброса пробивных напряжений зависимость Uпр= f() аппроксимируется выражением
Uпр = А , 16
где ∆ - толщина ребра,
А – эмпирический коэффициент, равный при плавном подъеме напряжения 50 Гц и грозовых импульсах положительной полярности соответственно 32,5 и 43 кВ·мм-0,5.
С учетом разброса полученных данных, коэффициент запаса в выражении (15) может быть принят равным 1,3.
Исследования разрядных напряжений вдоль поверхности диэлектриков показали, что они зависят от вида диэлектрического материала (диэлектрической проницаемости), от толщины образца и формы воздействующего напряжения.
Анализ зависимостей разрядных напряжений от толщины Δ и вылета а ребра модели из силоксанового эластомера показал, что они могут быть представлены в виде степенных функций для случаев:
плавного подъема напряжения промышленной частоты
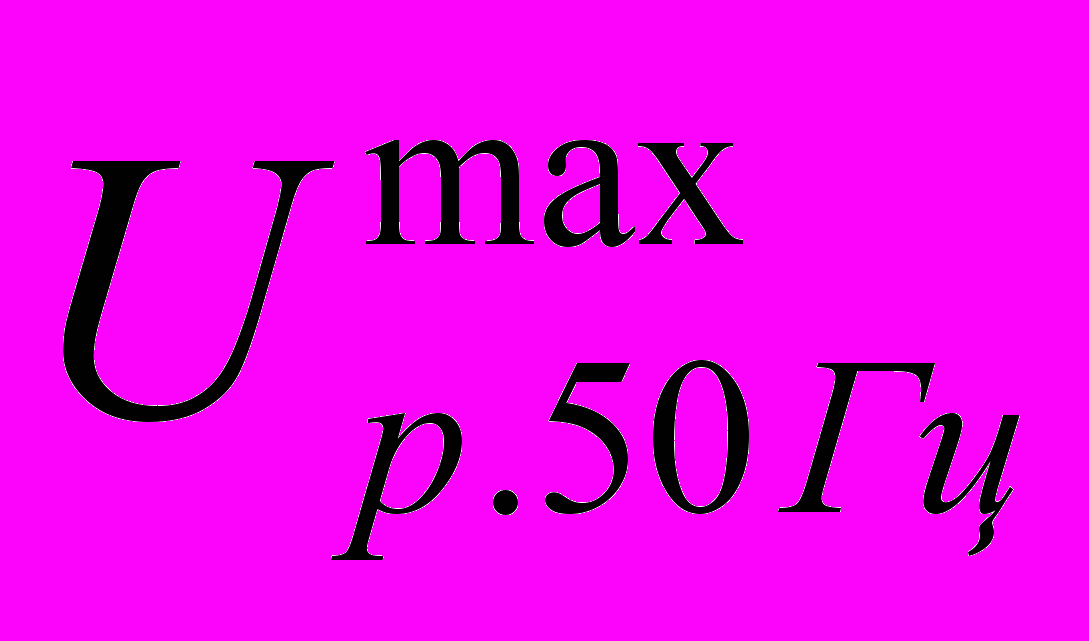
и
грозовых импульсов
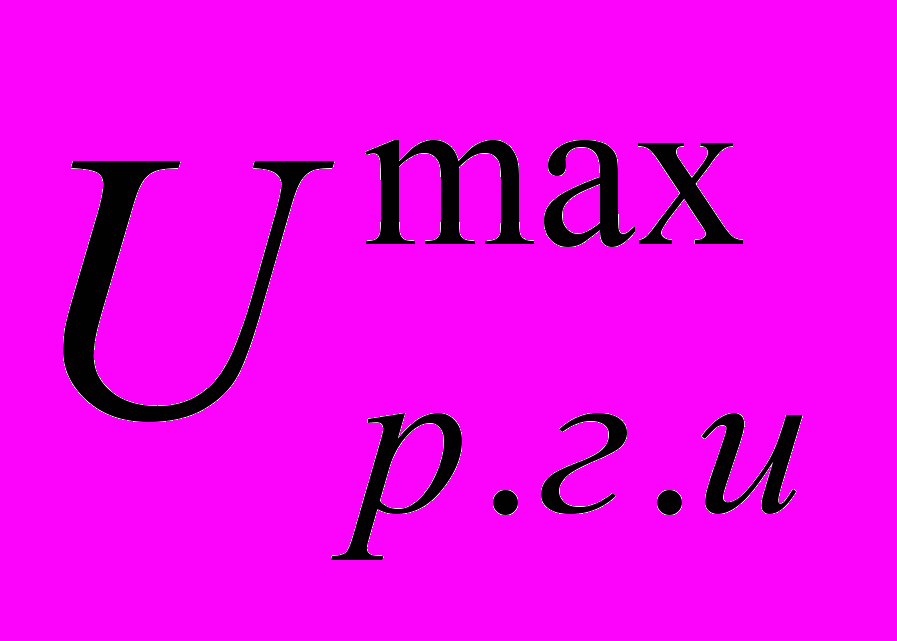
где Δ и а - в /мм/.
Разрядные напряжения при отрицательной полярности грозового импульса оказываются примерно на 10% выше, чем при положительной, поэтому выражение (18) относится к отрицательной полярности импульсного напряжения.
С учетом выражений (15) - (18) при Кз = 1,3 определяем минимальную толщину ребра (в мм):
при воздействии напряжения 50 Гц
пр.50Гц = 0,007 a 1,73 (19)
и
при воздействии грозового импульса
пр.г.и = 0,03 a 1,17 (20)
При выборе толщины ребра берется большее из значений, найденных по формулам (19) и (20). Это позволяет построить оптимальный профиль ребра. В общем случае оптимальное ребро имеет достаточно сложный геометрический профиль. Однако расчеты показывают, что применение ребер с таким профилем не дает заметного снижения материалоемкости, поэтому с учетом технологичности целесообразно применять клиновидные ребра.
Для клиновидного профиля толщина ребра у основания может быть выражена через вылет a и угол α между верхней и нижней поверхностями ребра:
Δ = a tg α
Для реальных вылетов ребер (свыше 20 мм), как показывают расчеты, определяющим является напряжение промышленной частоты (19). Подставляя значение Δ в формулу (19), получим
tgα = 0,007 a0,73. (21)
Полученная формула позволяет определить профиль ребра из силоксановой резины с минимальной материалоемкостью и обеспечением условия непробиваемости при выбранном вылете ребра. Так для вылета ребра a = 0,55 мм tgα = 0,13, толщина ребра у основания составляет 7,2 мм. Такой профиль ребра удовлетворяет и условиям механической прочности.
Таким образом, в результате исследований установлено, что наиболее оптимальным при разработке конструкции опорных полимерных изоляторов является клиновидный профиль ребра при соответствующей оптимальной толщине у основания и оптимальном межреберном расстоянии.
7.3 «Монолитность» полимерных изоляторов
В общем случае полимерный изолятор является монолитной конструкцией. Даже небольшое расслоение материалов не допустимо, т.к. приводит к значительному снижению длительной электрической прочности.
Для сохранения прочности связи между цилиндром и оболочкой, а, следовательно, для выполнения условия «монолитности» изолятора, необходимо, чтобы адгезионная прочность на сдвиг и отрыв была бы выше, чем суммарные механические напряжения от всех видов воздействий.
В общем случае условие «монолитности» имеет вид:
экспл. адг.; cдв. адг
Получены расчетные формулы для определения напряжений сдвига и отрыва на границе раздела. Учтены также напряжения, возникающие при воздействии технологических факторов (от натяга оболочки и усадки промежуточного слоя при отверждении).
Исследования показали что необходимыми технологическими факторами, обеспечивающими высокие значения cдв, являются применение специальных подслоев либо клеев и механическая обработка поверхности цилиндра. Все рассмотренные технологии обеспечивают достаточный запас адгезионной прочности, как в исходном состоянии, так и после воздействия циклических изгибающих нагрузок и увлажнения. Наилучшие результаты дает технология «напрессовки», которая имеет адгезионную прочность на сдвиг в 4-6 раз большую для исходного состояния изделия и в 4-5 раз большую после воздействия изгибающих нагрузок. Образцы, изготовленные по этим технологиям, подвергались также испытанию на электрическую прочность.
Исследования показали, что изгибающие нагрузки не приводят к изменению электрической прочности Eпр. бездефектных образцов. При наличии дефектов на границе раздела воздействие циклических изгибающих нагрузок способствует увеличению размеров дефектов, что сопровождается снижением Eпр. образцов.
Соблюдение условия «монолитности» изолятора обеспечивает также неизменность его электрической прочности вдоль границы раздела.
Специфической особенностью полимерного изолятора является его работа в ряде конструкций под давлением газа во внутренней полости цилиндра, поэтому недостаточная герметичность цилиндра может привести к отслоению оболочки. В этом случае условием «монолитности» является стандартность режима переноса газа через двухслойную стенку. Давление Р2 , возникающее на границе раздела в этом случае может быть скомпенсировано давлением Р1 , обусловленным радиальным растяжением внешней оболочки под воздействием внутреннего давления Р в цилиндре. Для того чтобы выполнялось это условие, коэффициент газопроницаемости цилиндра не должен превышать:

где D1 , D2 - коэффициенты газопроницаемости цилиндра и оболочки;
d1 , d2 - внутренние диаметры цилиндра и оболочки,
Е1 , Е2 – модули упругости цилиндра и оболочки,
- коэффициент Пуассона,
1, 1 – толщины слоев цилиндра и оболочки,
Кр - коэффициент, учитывающий релаксационные процессы в эластомере.
Допустимые коэффициенты газопроницаемости цилиндров для различных типов изоляторов в зависимости от конструкционных размеров и газопроницаемости оболочки с учетом D2 = f(t) и релаксационных процессов в эластомере составляют (25)10-10 cм2 / с атм. Эти данные были использованы при разработке методики испытаний цилиндров на герметичность, что позволяет производить их контроль еще перед сборкой изолятора.
7.4 Электрическая прочность вдоль границы раздела полимерных изоляторов
Граница раздела полимерных изоляторов является наиболее ответственным местом и требует особого внимания при конструировании полимерных изоляторов.
Было исследовано влияние влагопроницаемости оболочки полимерного изолятора на электрическую прочность границы раздела между стеклопластиковым цилиндром и оболочкой из силоксанового эластомера. На основании уравнения диффузии Фика получена зависимость, описывающая величину парциального давления паров влаги в воздушном включении, находящемся на границе раздела двух материалов, которая связывает парциальное давление в атмосфере с учетом его суточных и сезонных изменений температуры окружающей среды и время, а также толщину оболочки и размер дефекта g с влагосодержанием в воздушных включениях. Учтено также изменение коэффициента влагопроницаемости оболочки от температуры окружающей среды, поскольку изделие работает в условиях наружной установки.
Расчеты проведены для различных дефектов g=(0,10,5) см при значениях толщины оболочки (0,41,0) см, характерных для реальных конструкций, с учетом ежедневных суточных колебаний температуры и влажности, изменяющихся в течение года, для различных климатических районов.
При коэффициенте влагопроницаемости
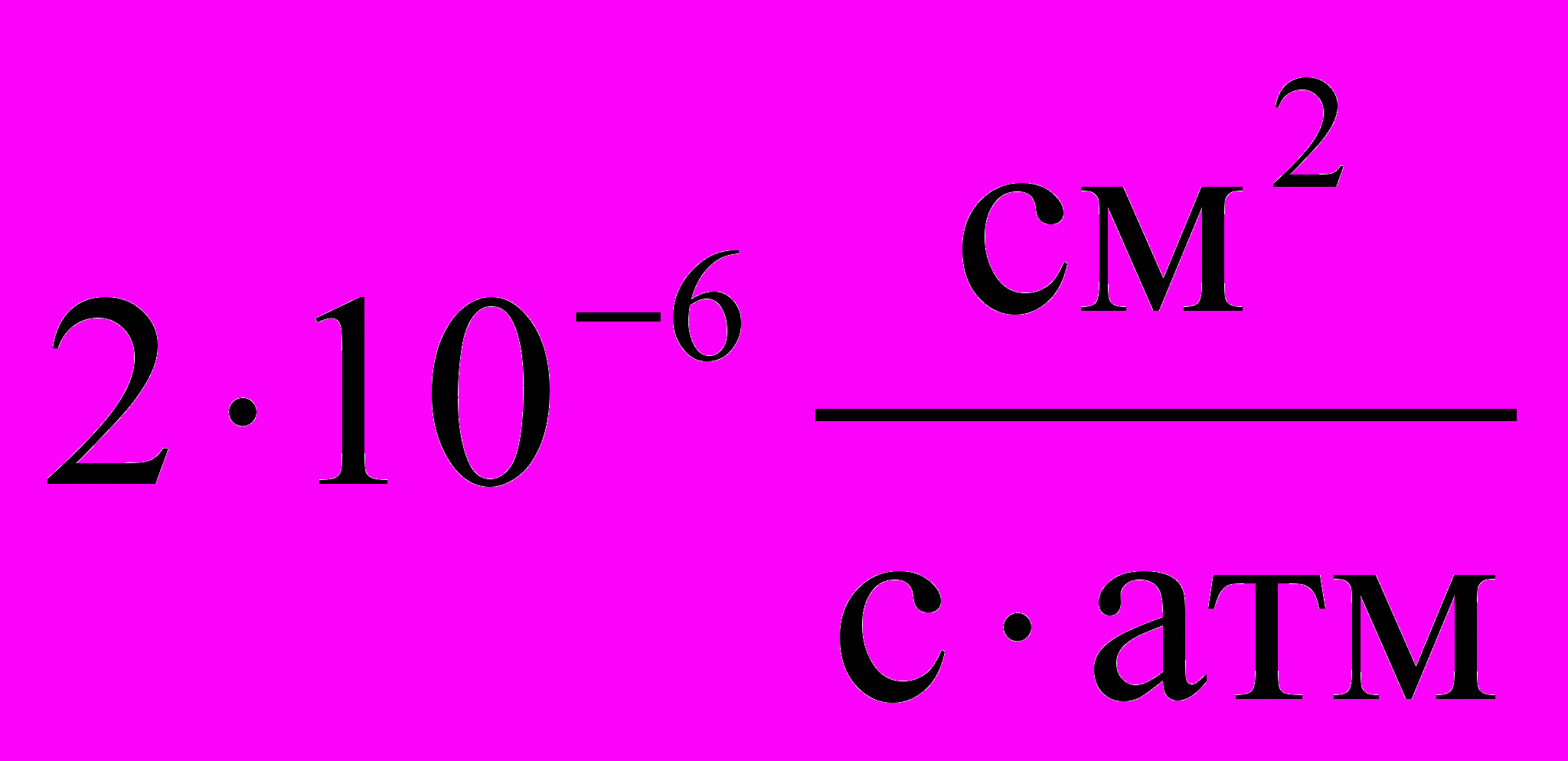
Электрическая прочность границы раздела образцов, изготовленных по различным технологиям, после испытаний кипячением по методике МЭК снижалась как при наличии дефектов, так и без них. Образцы с дефектами имели более низкие значения Uпр. Наибольшие значения Uпр наблюдались для образцов, изготовленных по технологии «напрессовки». Для исследований причин, вызвавших резкое снижение электрической прочности при испытании кипячением, были проведены эксперименты с разделением влияния влажности и температуры. Испытывалиcь две группы образцов: первая – термоударами от 20 до 100ОС, время и очередность приложения которых соответствовали графику испытаний кипячением, вторая – перепадами относительной влажности от 100 до 60% при температуре 20ОС. Испытания показали, что снижение Uпр происходит не под влиянием термоударов, а вследствие увлажнения при больших значениях давления насыщенного пара.
Значительное снижение электрической прочности после кипячения как дефектных, так и бездефектных образцов, ставит вопрос об изучении влияния этого процесса на характеристики конструкционных материалов изолятора. С этой целью были подвергнуты кипячению плоский стеклопластик марки СТЭФ, используемый для изготовления двух- и трехслойных образцов, образцы, вырезанные из стекло и лавсанопластиковых цилиндров, а также образцы используемых эластомеров. Было получено, что снижение Uпр эластомеров практически не происходит. После 18 часов кипячения Uпр лавсанопластика снижается на 35%; плоского стеклопластика СТЭФ – на 75%; образцов, вырезанных из стеклопластиковых труб – на 50%. Эксперименты показали, что снижение электрической прочности границы раздела – результат увлажнения поверхностного слоя стеклопластика. Когда поверхность стеклопластика защищена оболочкой, что имеет место в изоляторах, уменьшение электрической прочности образцов наблюдается в значительно меньшей степени. При этом средняя пробивная напряженность образцов составила: для стеклопластиковых цилиндров, защищенных эластомером – 1,76 кВ/мм, для лавсанопластиковых – 1,92 кВ/мм. Эти величины определены без учета процессов эвакуации влаги с границей раздела. Было установлено, что спустя 30 суток после кипячения бездефектных образцов и образцов с дефектами размерами до 0,5см, полностью восстанавливаются свойства границы раздела.
Расчетные значения напряженностей Е (кВ/мм) для изоляторов типа ИПВО-110, ИПВО-220, а также для покрышек трансформаторов тока 500 кВ не превышают 0,5 кВ/мм
Результаты исследований на стекло- и лавсанопластиковых цилиндрах типов ТСПО и ЦЛЭВ, используемых для изготовления аппаратных полимерных изоляторов, показали, что после 6000 часов старения при Еср. = 0,5 кВ/мм снижение электрической прочности образцов не происходит, интенсивность ЧР в них не увеличивается (q 1· 10-12 пКл).