Краткие данные о сварке с использованием электрической энергии
Вид материала | Документы |
- Лабораторная работа №1. Источники энергии при сварке. Лазерная сварка. Цель лабораторного, 120.5kb.
- Приказ от 17 апреля 2000 года n 32/28/28/276/75/54 Об утверждении Концепции построения, 1590.1kb.
- Постановления Правительства Российской Федерации от 31 августа 2006 г. N 529 "О совершенствовании, 20.18kb.
- Электрические цепи постоянного тока, 1039.6kb.
- О проведении закупочных процедур, 56.79kb.
- Лекция n 1, 3404.14kb.
- Лекция №1, 2690.05kb.
- Зао «радио и микроэлектроника» Счетчик электрической энергии однофазный, активный,, 170.51kb.
- Методические указания по нормированию топливно-энергетических ресурсов при производстве, 1982.9kb.
- Правительства Российской Федерации от 30 июня 2004 г. N 332 Собрание закон, 391.45kb.
Табл. 3 Выбор композиции наплавленного металла и термообработки для сварки перлитных сталей с мартенситными, ферритными и аустенитно-ферритными
Группы свариваемых сталей | Композиция наплавленного металла | Предельная температура эксплуатации, °С | Температура отпуска, °С |
I, II + VI, VIII | 09X1 М, 08ХГСМА, 08ХМ | 300 ... 350 | Подогрев, отпуск 650 ... 680 |
I, II + VII | 08Х24Н6ТАМФ | 300 | 700 ... 740 |
III, IV + VII | 0Х25Н13Г2 | 300 | 700 ... 740 |
IV + VI, VIII | 09X1 МФ, 08ХМФА | 400 ... 450 | 650 ... 700 |
При сварке деталей больших толщин целесообразно электродами типа Э-ХМ делать наплавку на кромки высоколегированной стали, а заполнение разделки осуществлять без подогрева электродами типа Э42 или Э50 в зависимости от требований прочности перлитного шва. Температуру предварительного подогрева и отпуска определяют по характеристикам более легированной, т.е. 12 %-хромистой стали, но для уменьшения размеров диффузионных прослоек применяют отпуск при минимально допустимой температуре.
При сварке перлитных сталей с более высоколегированными хромистыми сталями группы VII, содержащими 17 ... 28 % Сг, применяют электроды аустенитно-ферритного, а также аустенитного классов. Однако при этом следует учитывать вышеописанную структурную неоднородность в зоне сплавления аустенитного шва и перлитной стали. Термообработка в этом случае не требуется.
Особенности технологии сварки комбинированных конструкций из сталей разнородных сталей одного структурного класса
Сварку перлитных сталей, отличающихся лишь степенью легирования, производят электродами, применяемыми для менее легированной стали, если к швам не предъявляется требований повышенной прочности или особых свойств жаропрочности, коррозионной стойкости, характерных для более легированной. Однако технологические режимы сварки и температуру подогрева следует выбирать (рассчитывать) применительно к более легированной стали. Рекомендации по сварке различных групп перлитных сталей в пределах одного класса приведены в табл. 4
При невозможности подогрева при сварке производят наплавку кромок более легированной стали с подогревом электродами типа Э42А. Толщина наплавленного слоя должна быть достаточной, чтобы более легированная сталь не нагревалась до температур Ac1, т.е. чтобы не создавались условия для закалки.
При сварке различных сочетаний высокохромистых мартенситных (с 12 % Cr), ферритных (с 28 % Cr) и ферритно-аустенитных сталей типа Х21Н5 выбор сварочных материалов и технологий должен исключить образование холодных трещин и хрупких участков в швах. Режим подогрева назначают по наиболее закаливающейся стали, с немедленным отпуском, не допуская полного охлаждения. Для этого применяют сварочные материалы ферритно-аустенитного класса, сварку с минимальной погонной энергией, так как высокохромистые стали в 3ТВ весьма склонны к росту зерна, приводящего к охрупчиванию соединения.
Табл. 4 Выбор композиции наплавленного металла и термической обработки для сварки разнородных перлитных сталей
Группа свариваемых сталей | Композиция наплавленного металла | Предельная температура эксплуатации. °С | Термическая обработка |
I + II | Низкоуглеродистая | ±60 | Не требуется |
I + III, I +V | | | Отпуск 630 ... 650 °С |
III + III | Низколегированная | | Отпуск |
III + III | Аустенитная | ±60 | Не требуется |
I + IV | Низкоуглеродистая | До 350 | Не требуется |
I + IV | Хромомолибденованадиевая | До 450 | |
V +V | Низколегированная | 50 ... 100 | Отпуск 670 ... 700 °С Отпуск 620 °С |
V + V | Аустенитная | 50 ... 100 | Не требуется |
После окончания термообработки необходимо ускоренное охлаждение для предотвращения 475 °С-ной хрупкости. Возможна также сварка аустенитными электродами. Однако при этом термообработка не приводит к полному снятию сварочных напряжений из-за различия в коэффициентах линейного расширения шва и основного металла.
Рекомендации по выбору композиций наплавленного металла и термообработки при сварке высокохромистых сталей приведены в табл. 5
При выборе материалов для сварки аустенитных сталей различного легирования главное требование - исключить образование горячих трещин кристаллизационного и подсолидусного типа, а также локальных разрушений и снижение коррозионной стойкости. Сварку сталей с малым запасом аустенитности производят электродами (табл. 6), обеспечивающими в шве 4 ... 6 % ферритной фазы. Однако при сварке различных стабильно - аустенитных коррозионно-стойких сталей, как правило, не допускается в швах наличия ферритной фазы. Необходимо применять сварочные материалы, обеспечивающие швы с однородной аустенитной структурой без горячих трещин, что достигается легированием их молибденом, марганцем и азотом, например Св-04Х15Н25М6Г2АФ. Для сварки аустенитных сталей, обладающих особо высокой жаропрочностью (до 1000 °С), применяют электроды, дающие наплавленный металл с аустенитно-боридной или аустенитно-карбидной структурой, образуемой за счет высокого содержания в шве углерода, ниобия и титана или бора.
Табл. 5 Выбор композиции наплавленного металла и термообработки для сварки высокохромистых сталей
Группы свариваемых сталей | Композиция наплавленного металла | Предельная температура эксплуатации, °С | Термическая обработка |
VI + VIII | Мартенситно-ферритная на базе 12 % хрома . | До 500 | Отпуск |
VI + VIII | Аустенитно-ферритная | До 400 | Не требуется |
VI + VII | Мартенситно-ферритная на базе 12 % хрома | В коррозионных средах | Отпуск |
VI + VII | Ферритно-аустенитная | До 350 | Не требуется |
VI + IX | Ферритно-аустенитная | До 350 | Не требуется |
Табл. 6 Выбор композиции наплавленного металла и термообработки для сварки аустенитных сталей и сплавов на никелевой основе
Группы свариваемых сталей | Композиция наплавленного металла | Предельная температура эксплуатации, ºС | Термическая обработка |
Х + Х | Аустенитно-ферритная | <500 | Не требуется |
Х + Х | Аустенитно-ферритная | >500 | Аустенизация |
X + XI | Аустенитная | >500 | Аустенизация + стабилизация |
X + XII | Аустенитная | < 500 в коррозионных средах | Не требуется |
X(ХI) + XIII | На никелевой основе | <650 | Аустенизация + стабилизация |
Термообработка сварных соединений указанного типа производится только по необходимости снятия остаточных сварочных напряжений. Этого достигают стабилизацией при 800 ... 850 °С. Если конструкция предназначена для работы при высоких температурах, предпочтительна аустенизация при температуре 1100 ... 1150°С.
Сварка двухслойных (плакированных) сталей
Двухслойные стали позволяют резко уменьшить потребление дефицитных высоколегированных сталей без снижения работоспособности конструкций. Эти стали обычно используют для изготовления аппаратуры, работающей в коррозионной среде. Для облицовочного коррозионно-стойкого слоя, находящегося в контакте с агрессивной средой, толщина которого может достигать 12 мм, применяют высоколегированные хромоникелевые аустенитные (12Х18Н10Т, 08Х18Н10Т, 12Х18Н12Т, 08Х18Н12Б и др.) и хромистые ферритные и мартенситно-ферритные (08X13, 12X13 и др.) стали. Основной слой толщиной до 150 мм и более воспринимает силовые нагрузки и изготовляется из углеродистых низколегированных сталей (Ст3, 20К, 15ХМ и др.). Сварные соединения из этих сталей должны отвечать следующим требованиям:
- Облицовочный слой должен быть однородным, при этом его коррозионная стойкость в месте сварки не должна быть пониженной;
- В сварном шве между облицовочным и основным слоями не должны образовываться комплексные сплавы с пониженными механическими свойствами. Достигается это выбором способа сварки и его режима, соответствующих сварочных материалов, разделки кромок и последовательности выполнения сварки.
Основные типы и конструктивные элементы формы подготовки кромок в зависимости от способа сварки регламентированы ГОСТ 16098-80. Слои сваривают раздельно, используя различные сварочные материалы. В последнюю очередь обычно сваривают облицовочный слой для предупреждения его повторного нагрева. Сварка основного слоя обычно не представляет трудностей и выполняется в первую очередь с использованием соответствующих сварочных проволок, флюсов, электродов и т.д. (см. гл. 6).
Н


Рис. 5 Подготовка кромок (а) и последовательность (б - в) наложения слоев (1 - 3) при сварке двухслойных сталей: I - углеродистая; II - коррозионностойкая
Табл. 7 Материалы для выполнения разделительного 1 и плакирующего 3 слоев шва при сварке под флюсом двухслойных сталей (см. рис. 5, в)
Марка стали (коррозионностойкий слой) | Марка сварочной проволоки | Марка флюса | Назначение слоя |
08Х18Н10Т | Св-07Х25Н12Г2Т Св-08Х25Н13БТЮ Св-06Х25Н12ТЮ | Ан-26, Ан-45 | Разделительный и плакирующий |
12Х18Н10Т 12Х18Н9Т | Св-06Х19Н9Т Св-07Х19Н10Б Св-05Х20Н9ФБС | АН-26, АН-45 | Плакирующий |
10Х17Н13М2Т | Св-07Х25Н12Г2Т Св-08Х25Н13БТЮ Св-06ХН12ТЮ | Разделительный | |
10Х17Н13МЗТ | Св-ОХ30Н40М6ТБ Св-06Х20Н11МЗТЮ Св-08Х19Н10МЗБ | АН-45 АН-26 | Разделительный и плакирующий |
АН-18 | Плакирующий | ||
06ХН28МДТ | СВ-06Х20Н11МЗТБ | АН-45 АН-18 | Разделительный |
СВ-01Х23Н28МЗДЗТ | АН-18 | Плакирующий | |
08X13,12X13 | СВ-10Х16Н25АМ6 | АН-45, АН-18 | Разделительный и плакирующий |
Табл. 8 Марка и тип покрытых электродов для сварки высоколегированного слоя двухслойного металла
Марка электрода | Тип электрода по ГОСТ 10052-78 | Наплавленный металл | Марка (тип), высоколегированного слоя и характеристика металла шва | |
Тип | Структура | |||
ЗИО-7 | Э10Х25Н13Г2Б | 08Х24Н13Б | Аустенитно-ферритная; до 2,5 % α-фазы | (18-10), когда к металлу шва предъявляются требования по стойкости к МКК |
СЛ-25 | Э10Х25Н13Г2 | 09X25HI2T 09Х25Н12ТЮ | Аустенитно-ферритная; до 4 ... 5% α-фазы | 12Х18Н10Т,08Х13, когда к металлу шва не предъявляются требования по стойкости к МКК. Сварка неаустенитных сталей с аустенитной 12Х18Н10Т, а также хромистой 18X13 |
ЗИО-8 | Э10Х25Н13Г2 | 07Х24Н12 | То же, 2,5 ... 5 % α-фазы | (18-10), когда к металлу шва не предъявляются требования по стойкости к МКК. Сварка ненагруженных конструкций из стали 08X13 без последующей термической обработки, а также сварка сталей 12Х18Н10Т с низкоуглеродистыми не аустенитными сталями |
ЦЛ-9 | Э10Х25Н13Г2Б | 12X21НИБ | То же, более 2,5 % α-фазы | 12Х18Н10Т, 08X13 и им подобные, работающие в агрессивных средах, когда к металлу шва предъявляются требования по стойкости к МКК. Используются для сварки 15Х25Т и ей подобных |
Табл. 9 Режим сварки сдвоенной проволокой корозионностойкого слоя (толщиной 3 ... 5 мм) двухслойного металла
Диаметр одной проволоки, мм | Расстояние между электродными проволоками, мм | Вылет электрода, мм | Сварочный ток, А | Напряжение дуги, В | Скорость подачи электрода, 1х10-3 м/с |
3 | 12 ... 13 | 35 ... 38 | 450 ... 600 | 38 ... 40 | 20 ... 25 |
4 | 14 ... 15 | 40 ... 45 | 480 ... 600 | 38 ... 40 | 10 ... 16 |
При соединении двухслойных сталей толщиной 16 ... 36 мм без подварки переходного слоя для сварки облицовочного слоя из сталей ОХ18Н10Т и 12Х18Н10Т рекомендуется использовать порошковую ленту ПЛ-АНВ-54, а облицовочного слоя из сталей 10Х17Н13М2Т, 07Х17Н13МЗМ и 08Х17Н15МЗТ - порошковую ленту ПЛ-АНВ-69. Сварку ведут на постоянном токе обратной полярности с применением флюса АН-18 или АН-26.
При односторонней ручной сварке с заполнением разделки со сто¬роны основного низкоуглеродистого слоя (слой 1 рис. 6, а) и при сварке с заполнением со стороны облицовочного коррозионно-стойкого слоя (слои 3, 4, рис. 6, б) используют электроды типа Э-ПХ15Н25М6АГ2.


Рис. 6 Последовательность (1 - 4) наложения отдельных слоев
при односторонней сварке двухслойных сталей:
а - начало сварки со стороны углеродистого слоя;
б - то же, со стороны облицовочного коррозионно-стойкого слоя
Некоторые образцы соврменного сварочного оборудования.
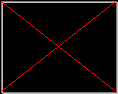