Прогнозирование остаточного ресурса длительно эксплуатирующихся сварных соединений паропроводов в условиях ползучести по структурному фактору
Вид материала | Автореферат |
Классификация микроповрежденности во взаимосвязи с исчерпанием ресурса для металла ЗТВрп сварных соединений стали 12Х1МФ при пол Общие выводы. Хромченко Ф.А., Лаппа В.А., Калугин Р.Н. |
- Темы рефератов. Бактериальная коррозия. Виды бактерий, развивающихся в нефтепроводных, 6.66kb.
- Уважаемые коллеги!, 46.85kb.
- Контроль качества сварных соединений трубопроводов стальных, из полимерных материалов,, 375.15kb.
- Рекомендации по модернизации, реконструкции и замене длительно эксплуатирующихся устройств, 272.63kb.
- Особенности проведения физико-механических испытаний сварных соединений в соответствии, 41.23kb.
- «Локомотивы и локомотивное хозяйство», 231.13kb.
- Д. И. Менделеева прогнозирование свойств элементов и их соединений методические указания, 611.18kb.
- Унифицированная методика контроля основных материалов (полуфабрикатов), сварных соединений, 874.83kb.
- Вероятностное прогнозирование ресурса нефтегазового оборудования при эксплуатации, 793.67kb.
- Влияние ультразвуковой ударной обработки на механические свойства сварных соединений, 41.15kb.
Классификация микроповрежденности во взаимосвязи с исчерпанием ресурса для металла ЗТВрп сварных соединений стали 12Х1МФ при ползучести.
| Стадия | Характеристика поврежденности микроструктуры | Этап | Плотность (,п/мм2) и морфология пор | Исчерпание ресурса | Схематичное отображение микроповрежденности на примере одного зерна | ||
---|---|---|---|---|---|---|---|---|
| Iп | Поры отсутствуют, микроповрежденность не выявляется при увеличении до 1000 | | | <0,5/р | | ||
| IIп | Единичные поры (П) размером 1 – 2 мкм по границам зерен | | 100 | (0,50,6)/р | ![]() | ||
| IIIп | Единичные поры размером 2 – 3 мкм вплоть до 4 – 5 мкм по границам зерен | III.1п | 100<250 | (0,60,7)/р | ![]() | ||
| III.2п | 250<1000 | (0,70,76)/р | |||||
| III.3п | 1000 | (0,760,82)/р | |||||
| IVп | Цепочки пор и слившиеся поры, скопления пор по границам зерен; отдельные микротрещины (мТр) длиной до 5 – 15 мкм по границам зерен | IV.1п | Цепочки мелких пор размером 1 – 2 мкм | (0,820,87)/р | ![]() | ||
| IV.2п | Цепочки мелких пор размером 2 – 3 мкм, слившиеся поры и/или скопления пор, микротрещины | (0,870,92)/р | |||||
| Vп | Трещины в сочетании с цепочками пор и слившимися порами по границам зерен | V.1п | Микротрещины длиной до 500 – 1000 мкм | (0,920,95)/р | ![]() | ||
| V.2п | Макротрещины длиной 1 – 5 мм и более | (0,951)/р | |||||
Примечание: | Классификация микроповреждаемости развивающейся в металле шва (при разупрочненном шве (мш<1) и слабо разупрочненной ЗТВрп (рп<10%)), оценивается аналогично как и для металла ЗТВрп. | |
Таблица 2
Классификация микроповрежденности во взаимосвязи с исчерпанием ресурса для металла ЗТВрп сварных соединений стали 15Х1М1Ф при ползучести.
| Стадия | Характеристика поврежденности микроструктуры | Этап | Плотность (,п/мм2) и морфология пор | Исчерпание ресурса | Схематичное отображение микроповрежденности на примере одного зерна | ||
---|---|---|---|---|---|---|---|---|
| Iп | Поры отсутствуют, микроповрежденность не выявляется при увеличении до х1000 | | | <0,6/р | | ||
| IIп | Единичные поры (П) размером 1–2 мкм по границам зерен | | 100 | (0,60,68)/р | ![]() | ||
| IIIп | Единичные поры размером 2 – 3 мкм вплоть до 4 – 5 мкм по границам зерен | III.1п | 100<250 | (0,680,75)/р | ![]() | ||
| III.2п | 250<1000 | (0,750,8)/р | |||||
| III.3п | 1000 | (0,80,85)/р | |||||
| IVп | Цепочки пор и слившиеся поры, скопления пор по границам зерен; отдельные микротрещины (мТр) длиной до 5 – 15 мкм по границам зерен | IV.1п | Цепочки мелких пор размером 1 – 2 мкм | (0,850,89)/р | ![]() | ||
| IV.2п | Цепочки мелких пор размером 2 – 3 мкм, слившиеся поры и/или скопления пор, микротрещины | (0,890,93)/р | |||||
| Vп | Трещины в сочетании с цепочками пор и слившимися порами по границам зерен | V.1п | Микротрещины длиной до 500 – 1000 мкм | (0,930,97)/р | ![]() | ||
| V.2п | Макротрещины длиной 1 – 5 мм и более | (0,971)/р | |||||
Примечание: | Классификация микроповреждаемости развивающейся в металле шва (при разупрочненном шве (мш<1) и слабо разупрочненной ЗТВрп (рп<10%)), оценивается аналогично как и для металла ЗТВрп. | |
методика устанавливает основные требования и последовательность проведения операций при определении остаточного ресурса стыковых, тройниковых и штуцерных сварных соединений равно- и разнотолщинных трубных элементов Ду≥100 коллекторов котлов и паропроводов из теплоустойчивых хромомолибденованадиевых сталей. Методика применяется в процессе обследования сварных соединений при эксплуатационном контроле.
В методике отражены требования: к персоналу, проводящему контроль; средствам и материалам; подготовке поверхности и технике проведения контроля; порядку оформления результатов.
Для повышения достоверности оценки микроповрежденности сварного соединения рекомендовано проводить металлографический анализ с помощью реплик в 3-4 зонах обследования по периметру шва (в зависимости от типа соединения), включая каждый трубный элемент.
В методике при металлографическом анализе используются реплики, сколы (срезы) металла (микрообразцы) или проводятся исследования непосредственно по месту сварного соединения с помощью переносного микроскопа. Подробно изложена технология получения реплик различных типов (полистироловых, лаковых и ацетатных) с рекомендациями по их выбору при проведении контроля. В случае использования сколов (срезов) получают микрошлифы согласно ОСТ 34-70-690-96.
Основным участком металлографического анализа в сварном соединении является мелкозернистая разупрочненная прослойка металла зоны термического влияния ЗТВрп; дополнительными участками служат околошовная зона ЗТВоз, металл шва МШ и основной металл ОМ (при необходимости).
Металлографический анализ структуры зон сварного соединения (с реплики или микрошлифа) проводится с помощью оптического микроскопа в последовательности при увеличении 100, затем 500 и/или 800 и 1000.
При металлографическом анализе устанавливаются особенности микроповрежденности металла (размер и морфология пор ползучести; характер и плотность — количество их распределения на удельной площади, охватываемой полем окуляра микроскопа; размер и количество микротрещин; наличие макротрещин длиной 1 мм и более) и микроструктурного состояния (вид структуры, размер карбидных частиц, балл сфероидизации перлитной составляющей, балл зерна).
Результаты металлографического анализа фотографируются при увеличении структуры металла 100, затем 500 и/или 800 и 1000 для подтверждения выявленных особенностей микроповрежденности (или ее отсутствия) и микроструктуры металла зон обследования сварного соединения.
Основным показателем для оценки остаточного ресурса по металлографическому признаку служит микроповрежденность металла и вспомогательным (факультативным) — микроструктура. Развитие микроповрежденности металла оценивается по 5 стадиям, а изменение микроструктуры — по 3 стадиям.
Остаточный ресурс сварных соединений определяется в следующей последовательности: на первом этапе, по структурной шкале для сварных соединений данной марки стали с учетом выявленной стадии микроповрежденности (и дополнительно стадии микроструктуры), при этом оценивается степень исчерпания ресурса н/р, где н - длительность наработки (эксплуатации) и р - ресурс (предельный) данного соединения; на заключительном этапе расчетным путем, при этом устанавливается остаточный срок службы (остаточный ресурс о.р.) данного сварного соединения из выражения о.р.=р-н; предельный ресурс определяется из отношения н/р (табл. 1 и 2).
Проведенные исследования и разработанная автором методика экспрессной оценки остаточного ресурса сварных соединений явилась основанием для создания отраслевого руководящего документа РД 153-34.1-17.467-2001 "Экспрессный метод оценки остаточного ресурса сварных соединений коллекторов котлов и паропроводов по структурному фактору", утвержденного Департаментом научно-технической политики и развития РАО "ЕЭС России" от 03.05.01 г. Документ используется при проведении эксплуатационного контроля с помощью метода МАР в соответствии с требованиями РД 10-577-03, СО 153-34.17.470-2003 и СО 153-34.17.455-2003.
Проведенное автором на отдельных отечественных ТЭС (в том числе на Костромской ГРЭС, Тверской ТЭЦ – 3, Новогорьковской ТЭЦ, Новочеркасской ГРЭС, Рязанской ГРЭС, Нижневартовской и др.) исследования с помощью разработанной методики позволили оперативно установить остаточный срок службы сварных соединений.
Проведенные исследования сварных соединений паропроводов, эксплуатирующихся в условиях ползучести позволили выявить наиболее слабые элементы и разработать рекомендации по повышению их работоспособности с целью продления сроков службы. Общий подход в решении этой задачи с рекомендациями о необходимости ремонта сварных соединений приведены в табл. 3.
По результатам металлографического анализа с реплик была установлена степень исчерпания ресурса сварных соединений после различных сроков наработки с оценкой их остаточного ресурса. Максимальная микроповреждаемость выявлена в ЗТВрп сварных соединений, что характерно для всех типов соединений. Полученные результаты обследования эксплуатирующихся сварных соединений были сопоставлены с установленной закономерностью исчерпания ресурса от микроповреждаемости по результатам испытания образцов. Отмечается хорошее совпадение данных исчерпания ресурса эксплуатирующихся сварных соединений в пределах разброса значений микроповреждаемости образцов.
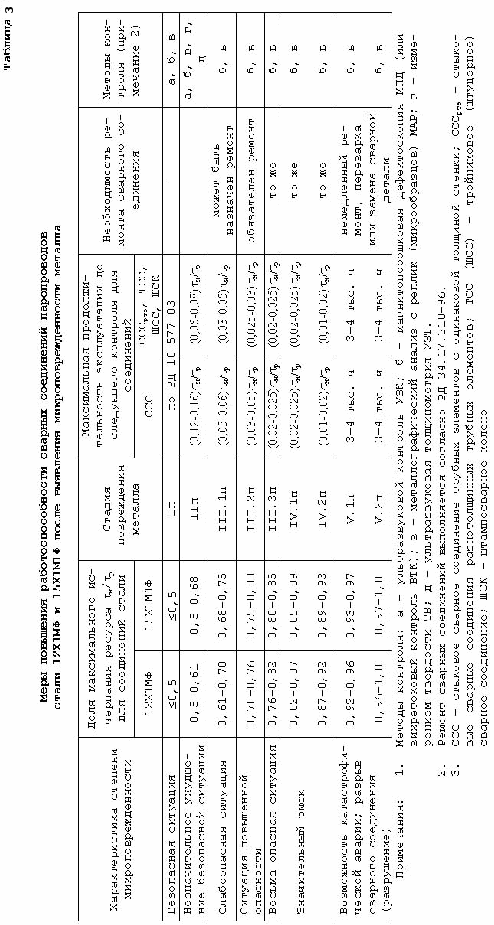
На основе методики автором был разработан комплексный подход по диагностированию и прогнозированию ресурса сварных соединений, сочетающий применение расчетных и структурных методов, дополняющих друг друга, что позволяет корректировать объемы и периодичность эксплуатационного контроля с учетом особенностей конструкционного оформления, остаточного запаса прочности и микроповрежденности сварных соединений паропроводов.
На основе комплексного подхода автором были созданы алгоритмы по определению ресурса сварных соединений и их технического состояния, уточнению регламента эксплуатационного контроля (объем и периодичность диагностических операций).
Накоплен положительный опыт успешного использования алгоритма анализа и оценки состояния сварных соединений трубопроводов в компьютерных информационно-аналитических системах на Рязанской и Костромской ГРЭС.
Общие выводы.
1. Установлены критерии и параметры оценки структурной и механической неоднородности, которые отражают микроструктурные изменения в металле зон сварных соединений паропроводов из теплоустойчивых хромомолибденованадиевых сталей (12Х1МФ, 15Х1М1Ф) в процессе длительной эксплуатации (до 300-350 тыс. ч.) при ползучести. Микроструктурные изменения в металле зон сварных соединений оцениваются по критериям: размер карбидных частиц, морфология выделения карбидной фазы (карбидные цепочки, прослойки из слипшихся карбидов), размер зерна микроструктуры. Микроповрежденность оценивается по плотности и морфологии пор ползучести от единичных пор до цепочек и слившихся пор ползучести вплоть до микро- и макротрещин по границам зерен. Механическая неоднородность характеризуется степенью разупрочнения в разупрочненной прослойке зоны термического влияния и металле шва (рп, мш).
2. Разработана методика исследования кинетики изменений микроструктуры и микроповреждаемости металла для условий термодеформационного старения образцов сварных соединений в условиях ползучести. Обоснованы форма и размеры образцов для испытаний на термодеформационное старение с периодической регистрацией структурного состояния металла зон сварного соединения с помощью реплик и микрошлифов. Определён способ металлографического анализа зон сварного соединения путём предварительного сканирования при увеличении 100 (для выявления мелкозернистых зон) и последующего исследования особенностей микроструктуры при увеличении от 500 до (800-1000).
3. Установлена взаимосвязь изменения микроструктуры металла зон сварного соединения (металла шва и ЗТВрп) с исчерпанием их ресурса для условий ползучести (/р). Деградация микроструктуры классифицирована на три стадии. Начальный период (0,30,35)/р характеризуется относительной стабильностью структурного исходного состояния; второй период (0,60,65)/р – дополнительным выделением феррито-карбидной структуры, распадом упрочняющих составляющих микроструктуры (бейнита, перлита, сорбита), коагуляцией карбидных частиц, сфероидизацией структуры; заключительный период (0,60,65)/р характеризуется мелкозернистой структурой (8-10 баллов) в виде феррито-карбидной смеси.
4. Установлена закономерность развития микроповреждаемости металла зон во взаимосвязи с исчерпанием ресурса сварных соединений в условиях ползучести (/р). Процесс развития микроповреждаемости классифицирован на пять стадий. Начальный период (0,50,6)/р характеризуется отсутствием (не выявляются при увеличении до 1000) пор ползучести размером до 1 мкм; второй период (0,50,7)/р - появлением единичных пор размером 1-2 мкм плотностью 100 пор/мм2; третий период (0,60,85)/р - увеличением размера пор до размера 2-3 мкм и их плотности до 250<1000 пор/мм2 и более; четвёртый период (0,70,9)/р - появлением цепочек пор (и/или слившихся пор) и микротрещин длиной до 5-15 мкм по границам зёрен; пятый период (0,91)/р - развитием микро- и макротрещин.
5. Разработаны структурные шкалы для оценки остаточного ресурса сварных соединений по критериям микроповрежденности и структурных изменений металла. Единственным и основным критерием при оценке остаточного ресурса служит фактическое состояние металла ЗТВрп, которое выявляется при диагностировании методом металлографического анализа с помощью реплик; поврежденность этой зоны свидетельствует об остаточном ресурсе сварного соединения.
6. Выявлено, что микроструктурные изменения и накопление микроповрежденности в разупрочненной прослойке ЗТВрп при ползучести протекают более интенсивно по сравнению с металлом шва и основным металлом. Однако, сильное влияние на место развития микроповреждаемости оказывает степень неоднородности свойств металла зон сварных соединений. При разупрочненном шве (мш<1) и слабо разупрочненной ЗТВрп (рп<10%) микроповрежденность преимущественно развивается в металле шва. На разупрочнение металла шва 09Х1МФ влияет его микроструктурное состояние (содержание избыточного феррита в виде оторочек). Показана необходимость ограничения максимальной ширины ферритных оторочек Lф45 мкм по условию необходимого упрочнения металла швов (мш>1).
7. Разработана методика металлографического анализа с помощью реплик (и/или срезов микрообразцов металла) для оценки остаточного ресурса реальных сварных соединений в рамках неразрушающего контроля паропроводов, эксплуатирующихся в условиях ползучести. Определены зоны обследования сварных соединений сталей 12Х1МФ и 15Х1М1Ф. Основным структурным фактором для оценки ресурса сварных соединений принята микроповрежденность металла зон и вспомогательным фактором — изменение их микроструктуры при ползучести.
8. Эффективность использования разработанного метода оценки остаточного ресурса сварных соединений подтверждена положительным промышленным опытом на отечественных ТЭС.
9. Методика оформлена и введена в действие в виде отраслевого руководящего документа РД 153-34.1-17.467-2001 "Экспрессный метод для оценки остаточного ресурса сварных соединений коллекторов котлов и паропроводов по структурному фактору". Применение методики металлографического анализа с помощью реплик для оценки ресурса сварных соединений регламентировано в отраслевых инструкциях СО 153-34.17.470-2003, СО 153-34.17.455-2003 и РД 10-577-03.
Перечень работ по теме диссертации.
1. Хромченко Ф.А., Лаппа В.А., Федина И.В, Калугин Р.Н. Влияние технологической и металлургической наследственности на повреждение зон сварных соединений стали 15Х1М1Ф в условиях ползучести//Сварочное производство.- 1998.- №4.- С.14-16.
2. Структурный метод оценки остаточного ресурса сварных соединений паропроводов ТЭС/Калугин Р.Н., Хромченко Ф.А., Лаппа В.А.//Повышение надежности паропроводов и арматуры ТЭС. Научно-практический семинар: Сб. докладов.- Москва: ВВЦ, 1998.
3. Зависимости структурных изменений и микроповрежденности металла при ползучести от исчерпания ресурса сварных соединений стали 15Х1М1Ф/Калугин Р.Н., Хромченко Ф.А., Лаппа В.А., Федина И.В.//Современная сварочно-термическая технология восстановления работоспособности элементов энергетического оборудования ТЭС. Сварочные материалы. Всероссийский научно-практический семинар: Сб. докладов.- Санкт-Петербург: ВТИ-АО «Электродный завод», 1998.
4. Оценка остаточного ресурса сварных соединений по микроповрежденности металла в условиях ползучести/ Хромченко Ф.А., Лаппа В.А., Калугин Р.Н.//Диагностика оборудования с использованием магнитной памяти металла. Международная научно-техническая конференция: Сб. докладов.- Москва: РНТСО, РОНКТД, ИПК Госслужбы, фирма «Энергодиагостика», 1999.
5. Хромченко Ф.А., Калугин Р.Н., Лаппа В.А., Федина И.В. Особенности структурных изменений в сварных соединениях стали 15Х1М1Ф при ползучести//Сварочное производство.- 1999.- №10.- С.10-12.
6. Ресурс и диагностика сварных соединений паропроводов/Хромченко Ф.А., Лаппа В.А., Калугин Р.Н.//Сварные конструкции. Международная конференция: Сб. докладов.- Киев: ИУПК, 2000.
7. Хромченко Ф.А., Лаппа В.А., Калугин Р.Н. Диагностика и ресурс сварных соединений паропроводов ТЭС. Ч. 1. Анализ эксплуатационных повреждений сварных соединений и задачи технического диагностирования//Сварочное производство.- 2001.- №7.- С. 8-9.
8. Хромченко Ф.А., Лаппа В.А., Калугин Р.Н. Диагностика и ресурс сварных соединений паропроводов ТЭС. Ч. 2. Расчетная оценкаресурса сварных соединений//Сварочное производство.- 2001.- №8.-С.14-16.
9. Хромченко Ф.А., Лаппа В.А., Калугин Р.Н. Диагностика и ресурс сварных соединений паропроводов ТЭС. Ч. 3. Оценка сварных соединений по структурному фактору//Сварочное производство.- 2001.- №9.- С.18-21.
10. Перевезенцева Т.В., Злепко В.Ф., Калугин Р.Н. Структурные особенности и жаропрочность металла центробежнолитых труб из стали 15Х1М1Ф//Электрические станции.- 2002.- №6.- С.5-7.
11. Хромченко Ф.А., Калугин Р.Н. Регламент эксплуатационного контроля сварных соединений паропроводов//Технология машиностроения.- 2004.- №5.-С.3-7.
12. Компьютерная информационная система по анализу технических характеристик, условий эксплуатации и результатов регламентного контроля с оценкой состояния трубопроводов электростанций/ Калугин Р.Н.//Металл оборудования ТЭС. Проблемы и перспективы. Научно-техническая конференция: Сб. докладов.- Москва: ОАО «ВТИ», 2006.