Вестн. Самар. Гос. Техн. Ун-та. Сер. Технические науки. 2010. №4 (27) Машиностроение
Вид материала | Документы |
- Вестн. Самар. Гос. Техн. Ун-та. Сер. Технические науки. 2010. №7 (28) Машиностроение, 604.71kb.
- Библиографический указатель составлен на основе просмотра рж винити сер.«Физика» иСер.«Геология», 12.67kb.
- Учебное пособие по выполнению курсовой работы Сызрань 2010, 939.14kb.
- Методические указания Самара Самарский государственный технический университет 2010, 334.58kb.
- Методические рекомендации для дипломного проектирования Самара, 142.87kb.
- Список основных трудов Сафуанова Ильдара Суфияновича. Об аффинных частях алгебраических, 24.49kb.
- Александра Михайловича Ляпунова. К 150-летию со дня рождения // Вестн. С. Петерб ун-та., 105.86kb.
- Методические рекомендации по изучению дисциплины для студентов специальностей 080801, 180.47kb.
- Нефтяная и газовая промышленность Технология разработки месторождений, 445.81kb.
- Задачи дипломного проектирования 4 организация работы над дипломным проектом в период, 823.26kb.
УПРОЧНЕНИЕ КРОМОК ЛОПАТОК РАБОЧИХ КОЛЁС
ГАЗОТУРБИННЫХ ДВИГАТЕЛЕЙ
Ю.И. Кургузов1, М.Ю. Кургузов2
1 Самарский государственный технический университет
443100, Самара, ул. Молодогвардейская, 244
2 ООО «Проминвест»
443105, Самара, ул. Металлистов, 64
Рассмотрена упрочняющая обработка торцовых кромок лопаток ГТД в составе рабочего колеса на станке токарного типа дисковыми механическими щётками с секционной набивкой проволочного ворса. Обращено внимание на ударный характер процесса обработки, на формируемое качество поверхностного слоя. Установлено повышение усталостной прочности кромочных поверхностей.
Ключевые слова: рабочее колесо, торец лопатки, дисковая щётка, упрочняющая обработка, качество поверхности, усталостная прочность.
Ресурс работы газотурбинных двигателей (ГТД) в значительной степени зависит от ресурса его лопаток. Они работают в условиях, характеризующихся высокой агрессивностью рабочей среды, повышенными температурами, запылённостью среды абразивными частицами, действием сложных систем сил, попаданием в рабочую зону посторонних предметов и другими факторами. В процессе эксплуатации отмечаются обрывы уголков рабочих лопаток, являющиеся следствием развития магистральных усталостных трещин с их торцов.
В процессе изготовления к поверхностям лопаток предъявляются жёсткие требования [1, 2, 3], которые заключаются в обеспечении плавности переходов поверхностей, низкой шероховатости, отсутствии концентраторов напряжений. Механическая обработка поверхностей лопаток заканчивается упрочнением различными методами ППД. Подобранные по весу и по основному тону колебаний лопатки устанавливают в диск и обтачивают по торцам пера, придавая колесу требуемый наружный диаметр. При этом с торцов лопаток удаляется ранее упрочнённый слой и формируются острые кромки. Последующее их скругление и полирование вследствие сложности формы, ажурности, малой жёсткости детали и дискретности поверхностей производят вручную. Эти операции отличаются низкой производительностью, не гарантируют размерной и физической стабильности и не обеспечивают требуемого ресурса работы лопаток, т.к. даже заполированные кромки имеют заниженные характеристики качества поверхности и являются неблагоприятной зоной концентрации напряжений. Необходима повторная упрочняющая обработка, но уже в составе рабочего колеса.
В качестве возможных вариантов упрочнения кромок была предложена обработка вращающимися механическими щётками (ВМЩ). На начальном этапе при проектировании схемы обработки произвольно расположенные в пространстве изогнутые кромки на торцах лопаток представлялись стягивающими их хордами аb (рис. 1). Схема предусматривала, что в момент наибольшего перекрытия скруглённых по радиусу поверхностей торцов лопаток и торцов проволочек щётки её плоскость вращения ПВ должна быть перпендикулярна хорде аb.
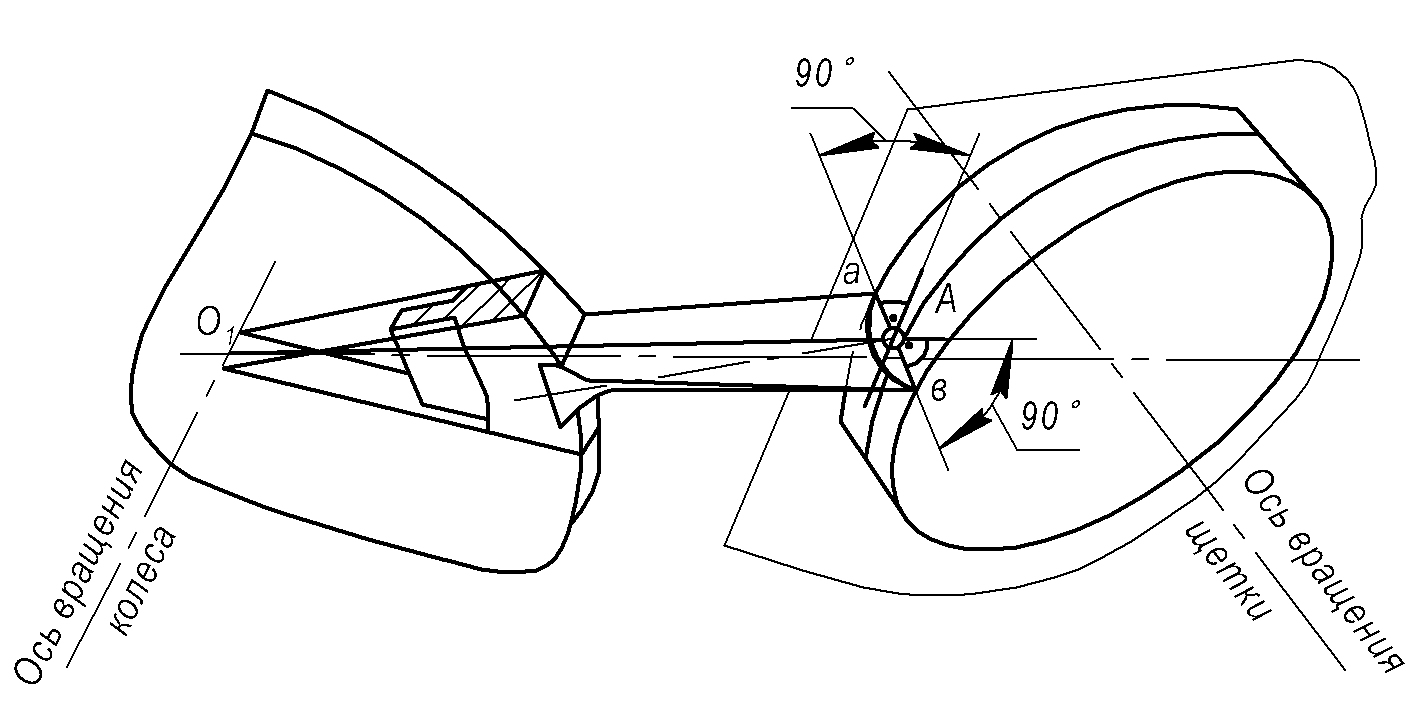
Рис. 1. Схема расположения щётки относительно торцов лопаток
Реализованная на лоботокарном станке РТ-39 полная схема обработки торцов лопаток дисковой щёткой изображена на рис. 2. Колесо с запрессованными лопатками, обвязанными резиновым жгутом для повышения их изгибной жёсткости, устанавливалось на планшайбе, выставлялось по индикатору с заданным радиальным биением и закреплялось в 4-кулачковом патроне.
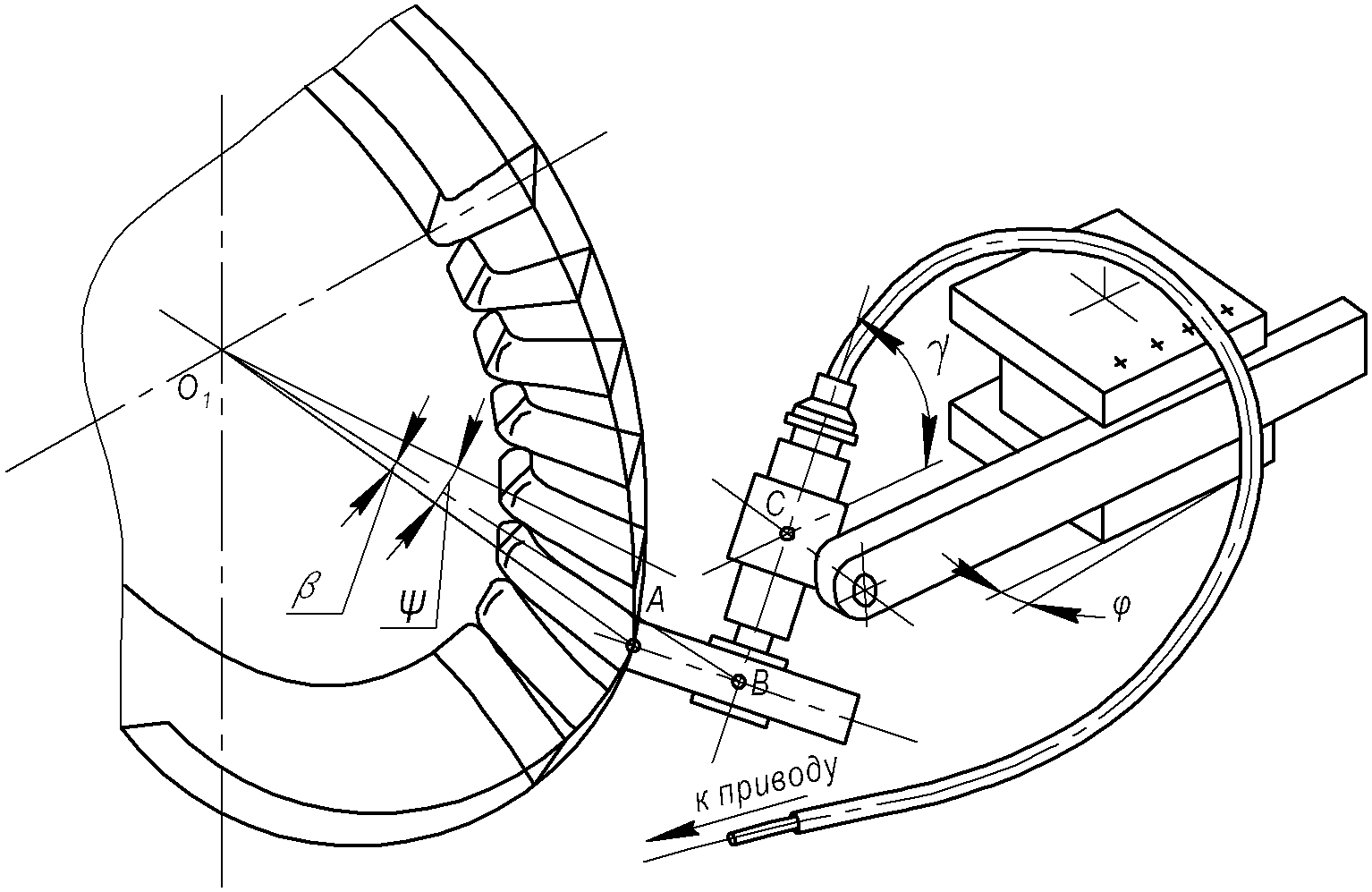
Рис. 2. Схема установки для обработки ВМЩ
Приспособление для обработки включало передвижную тележку с закреплённым на ней реверсивным электродвигателем. Вращательное движение щётке передавалось с помощью гибкого вала, который позволял щётке занимать произвольное расположение в пространстве.
При вращении рабочего колеса с установленными в нём лопатками углы, характеризующие ориентацию хорды в пространстве, изменяются, что необходимо учитывать соответственной настройкой инструмента перед обработкой. Пространственное положение хорд относительно инструмента определяется углами: γ – углом наклона хорды по отношению к горизонтальной плоскости; φ – углом между проекцией хорды на горизонтальную плоскость и прямой, параллельной оси колеса; ψ – углом между горизонтальной плоскостью и радиусом, проведённым из центра колеса к середине рассматриваемой хорды. Оси колеса и щётки должны быть скрещивающимися. При этом необходимо, чтобы ось щётки (см. рис. 1) находилась на линии О1А, проходящей через ось колеса и середину хорды (точку А).
Нетрудно представить, что для обработки лопатки, лежащей в горизонтальной плоскости колеса, повёрнутой на угол γ щёткой, последняя смещается и не может контактировать с данной лопаткой. С ней вступает в контакт другая лопатка, имеющая угол наклона хорды, отличный от того, на который инструмент был настроен. В связи со сказанным возникает достаточно сложная пространственная задача настройки технологической системы, связанной с определением требуемого положения оси щётки. При известном угле ψ ориентация щётки в пространстве достигается поворотом хомута cо щёточной головкой относительно державки вокруг оси своей цапфы, проходящей через точку С, на угол γ и разворотом резцедержателя в горизонтальной плоскости на угол φ.
Анализ взаимодействия ворса с обрабатываемой поверхностью может быть осуществлён по методике, изложенной в работе [4]. Для рассматриваемого случая схемы взаимодействия приведены на рис. 3.
Лопатки поступают на обработку с полированными по радиусу r кромками. Начальное касание кромок лопаток с торцами проволочек (см. рис. 3, а) происходит ниже вершины кромки при углах θ н и λ н, которые определяются по формулам:
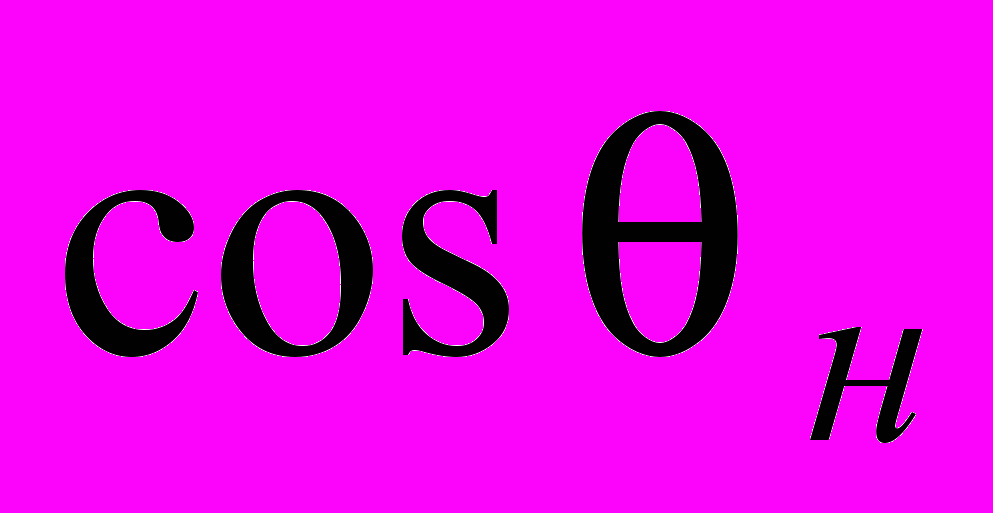

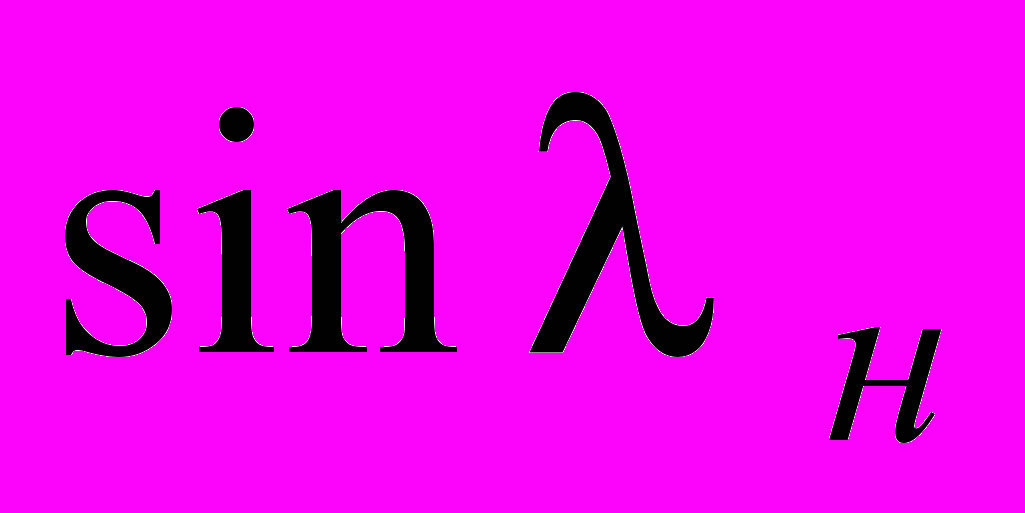
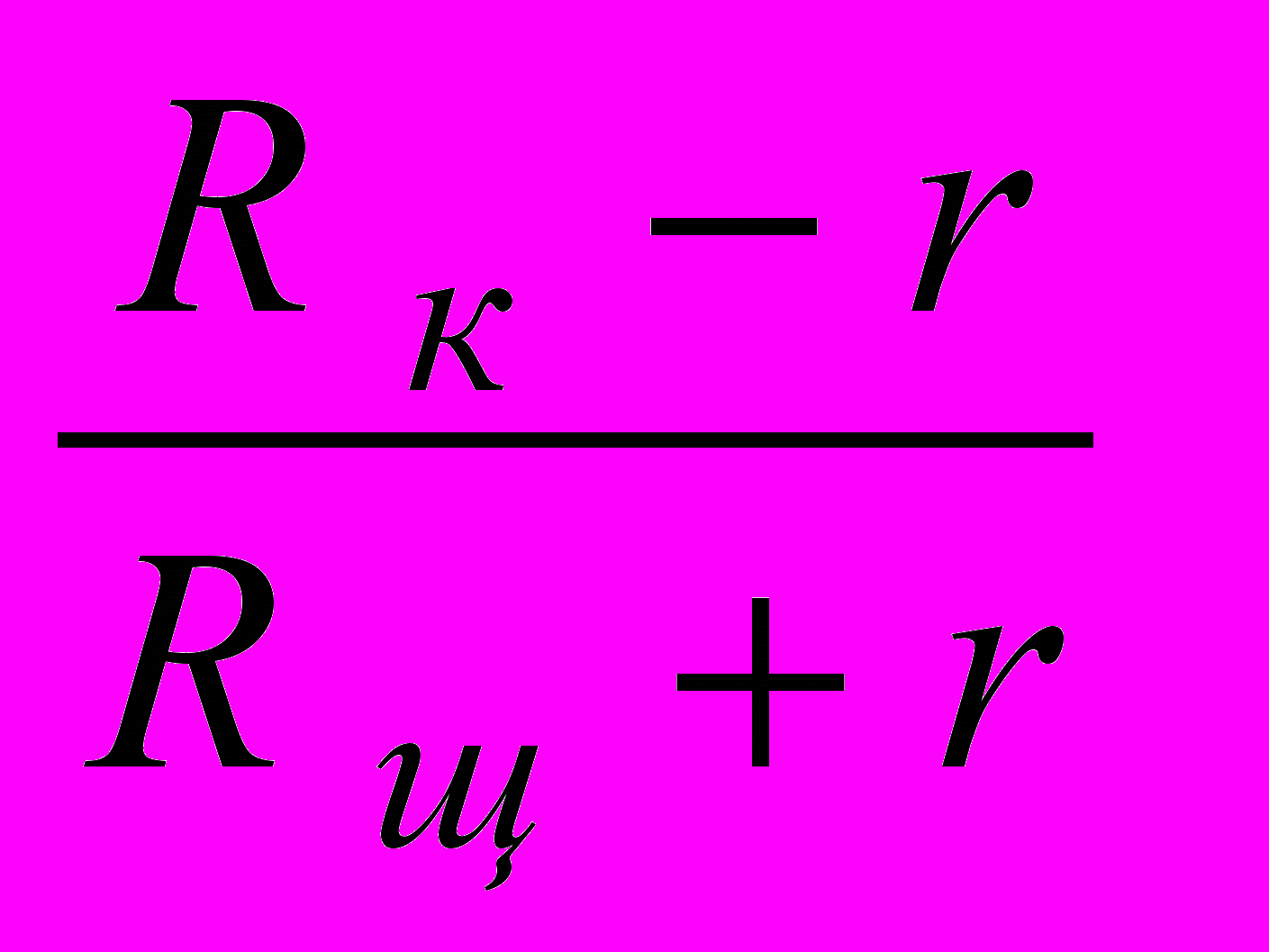
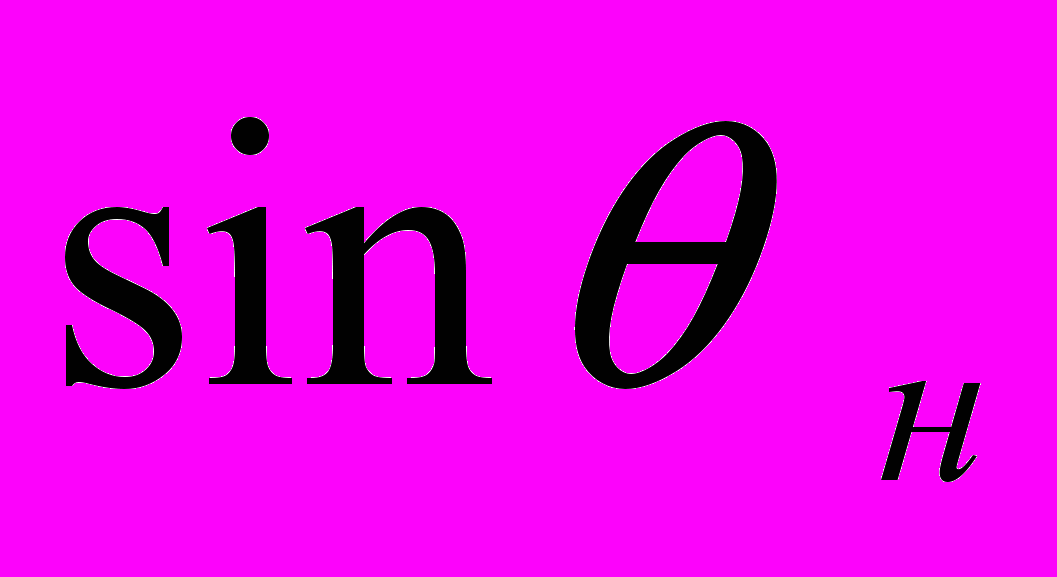
Так, при R к = 452,45 мм, R щ = 125 мм, r = 1 мм и натяге i = 1 мм θ н = 1˚ 47΄, λ н = 6˚ 26΄. Для кромки с радиусом r = 0,5 мм при прочих равных исходных параметрах θ н = 1˚ 15΄, λ н = 4˚31΄.
Можно отметить случай (рис. 3, в), при котором проволочки перестают контактировать своими торцами с радиусной кромкой. Натяг, соответствующий этому случаю, будет наибольшим. Он вычисляется по формуле:

После подстановки в формулу значений, приведённых выше, получим при r = 1 мм натяг i max = 0,996 мм. При i > i max проволочки контактируют с кромкой боковой (цилиндрической) поверхностью. Угол атаки (δ + λ) становится равным 90°. В области перехода кромки в перо лопатки образуются, как будет показано ниже, более глубокие следы, интенсивно упрочняется поверхностный слой и, наряду с этим, ухудшается его шероховатость.
По мере вращения рабочего колеса углы атаки ворса щётки с кромкой лопатки изменяются и вместе с ними меняются контактные условия взаимодействия. Вычисление углов атаки связано с определением текущих значений углов θ и λ, а также угла δ. Линия τ – τ – касательная к окружности радиуса R щ в точке М (см. рис. 3, в).
С математической точки зрения касание проволочек щётки с радиусной кромкой торца лопатки можно рассматривать как касание окружностей радиусов R щ и r. При вращении радиусной кромки вокруг центра О 1 эти окружности пересекаются в точках М и М ′ (рис. 3, в). При попутной обработке точкой встречи вращающегося ворса с кромкой является точка М с текущими координатами x и y. Решая совместно систему двух уравнений, выражающих окружности с радиусами R щ и r, и вводя обозначения

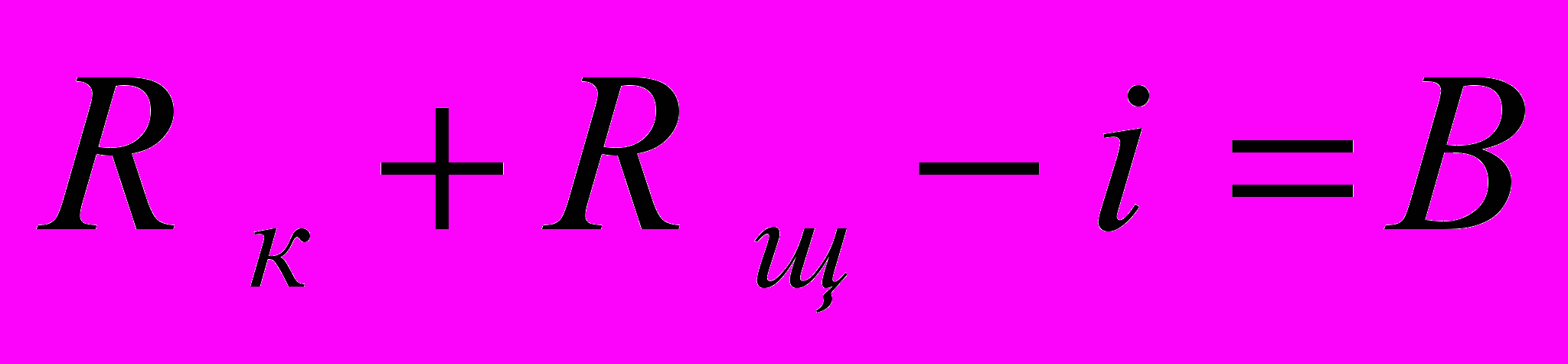
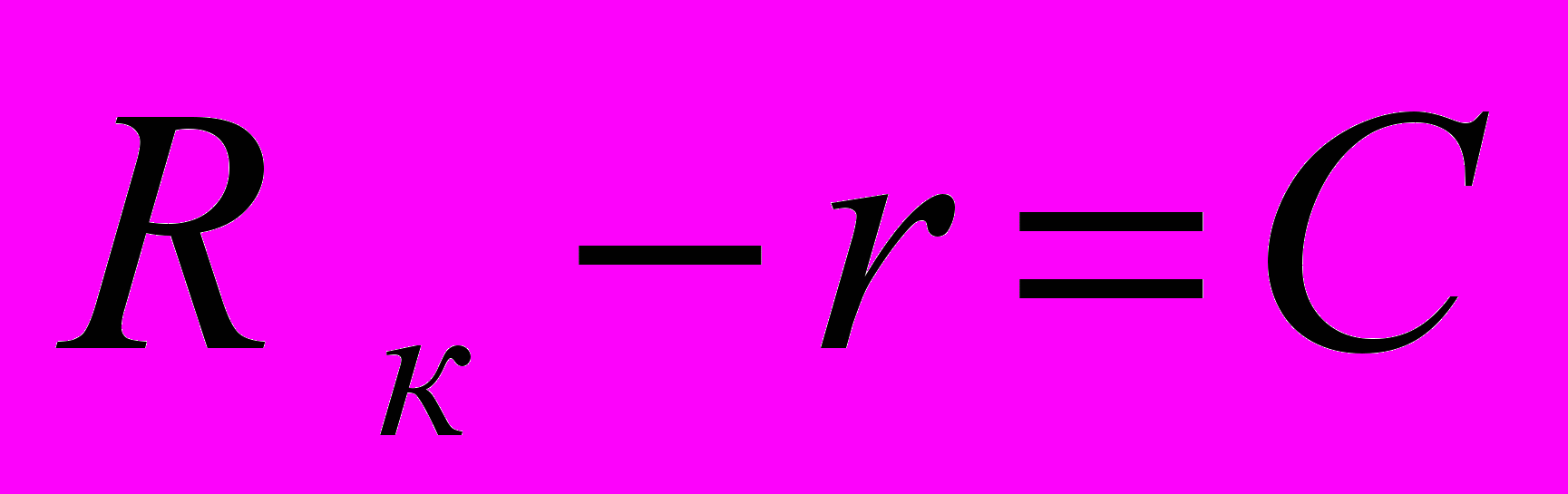
получим для одной из координат квадратное уравнение типа
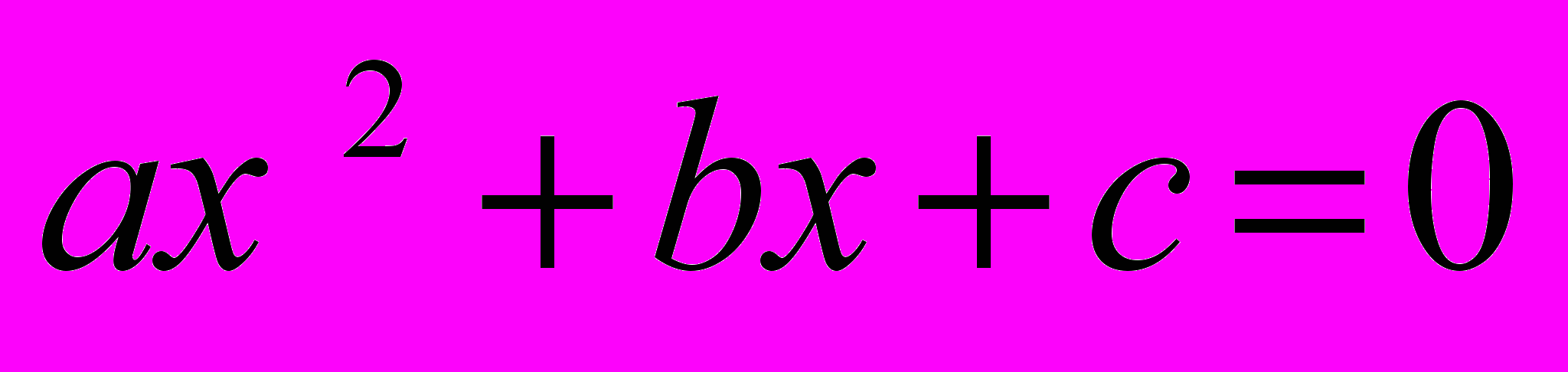
где


Придавая углу θ фиксированные значения, можно получить соответственные ему координаты x и y. Угол δ находится из равенства
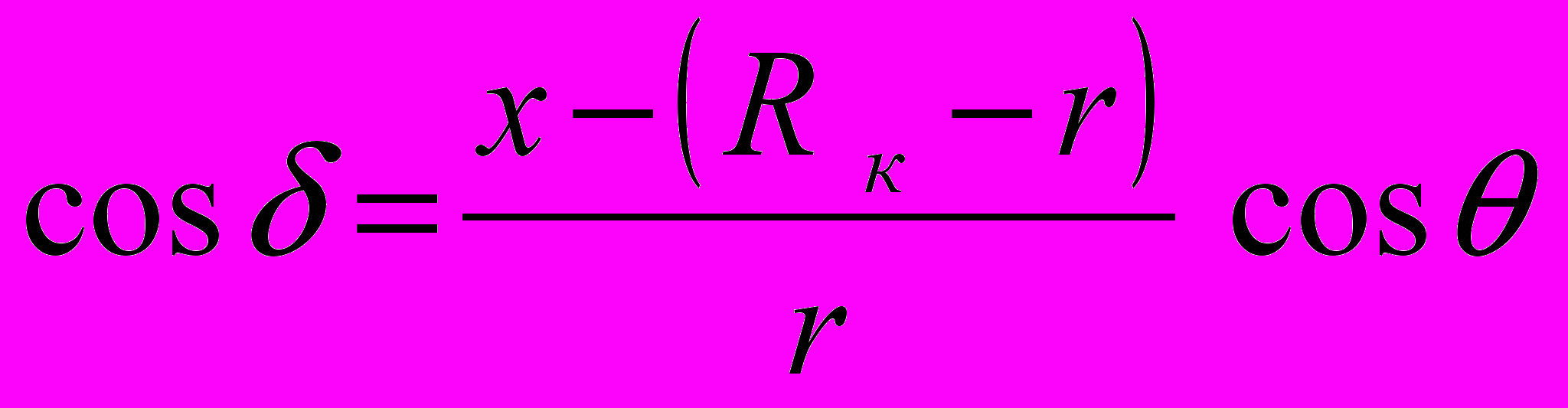
а угол λ – из формулы sin λ = y / R щ.
Контакт проволочки с кромкой продолжается и в зоне отрицательных значений углов θ. В общем виде угол атаки равен δ ± λ, где знак «+» – при y > 0, знак «-» – при y < 0.
Для упрочняющей обработки применяли секционную дисковую щётку с набивкой ворса из холоднотянутой, нагартованной, высоколегированной и жаростойкой проволоки по ГОСТ 18143-72 (химический состав по ГОСТ 5632-72). Распределение ворса по секциям обеспечивалось сепараторными гнёздами, предусмотренными в конструкции щётки. Ранее проведенные исследования [4] дали возможность определить параметры инструмента: наружный диаметр щетки D щ = 250 мм, вылет ворса l = 75 мм, диаметр проволочек d = 0,2 …0,25 мм, количество проволочных пучков по окружности N = 10. Количество проволочек в пучке 550…650 штук. Коэффициент плотности набивки ворса, определяемый отношением суммарной площади торцовых сечений проволочек к боковой площади цилиндра, образованного наружным диаметром щетки, k п = 0,16…0,18. При ширине лопатки l = 42 мм ширина рабочей части щетки составила 48 мм.
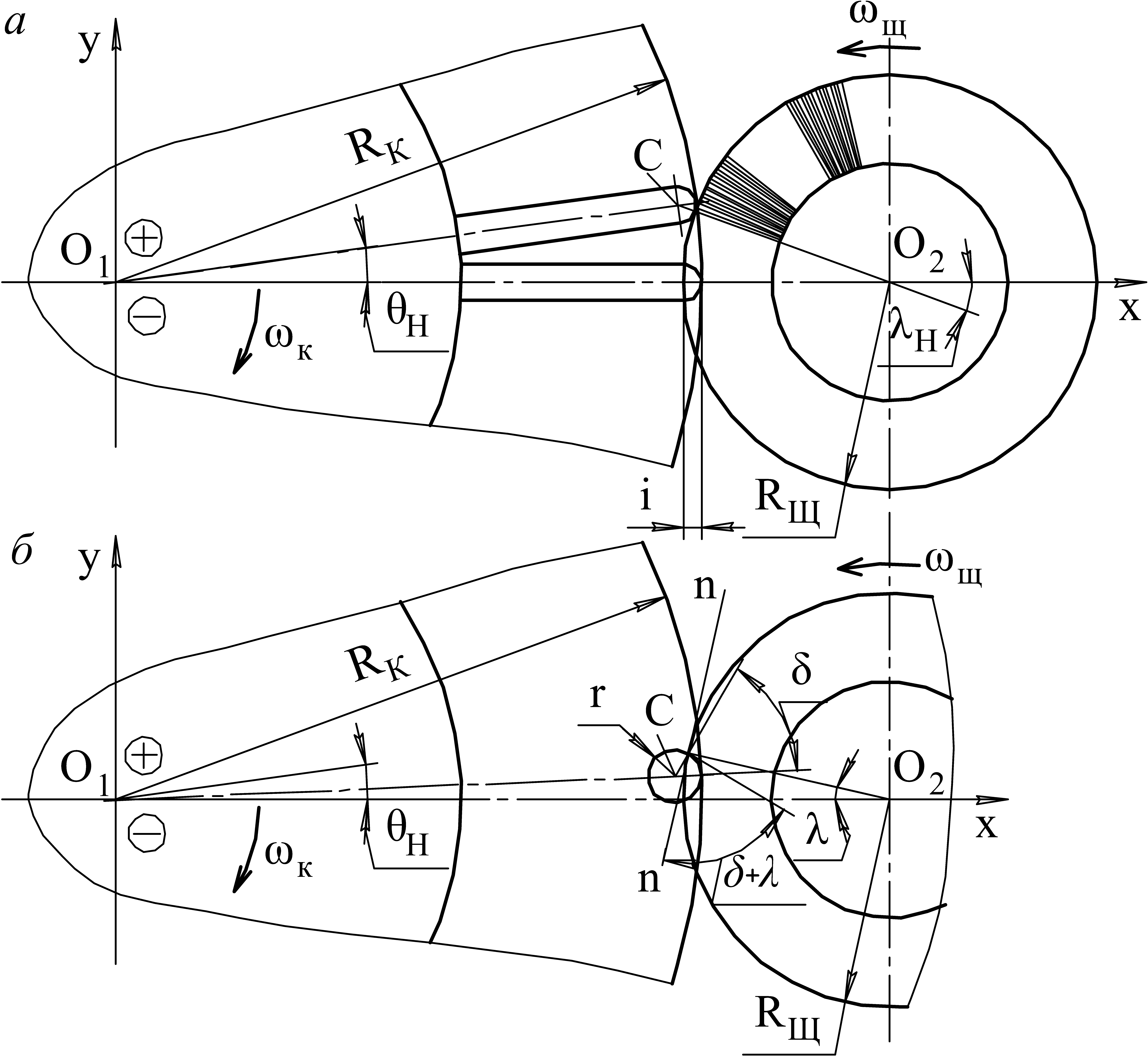
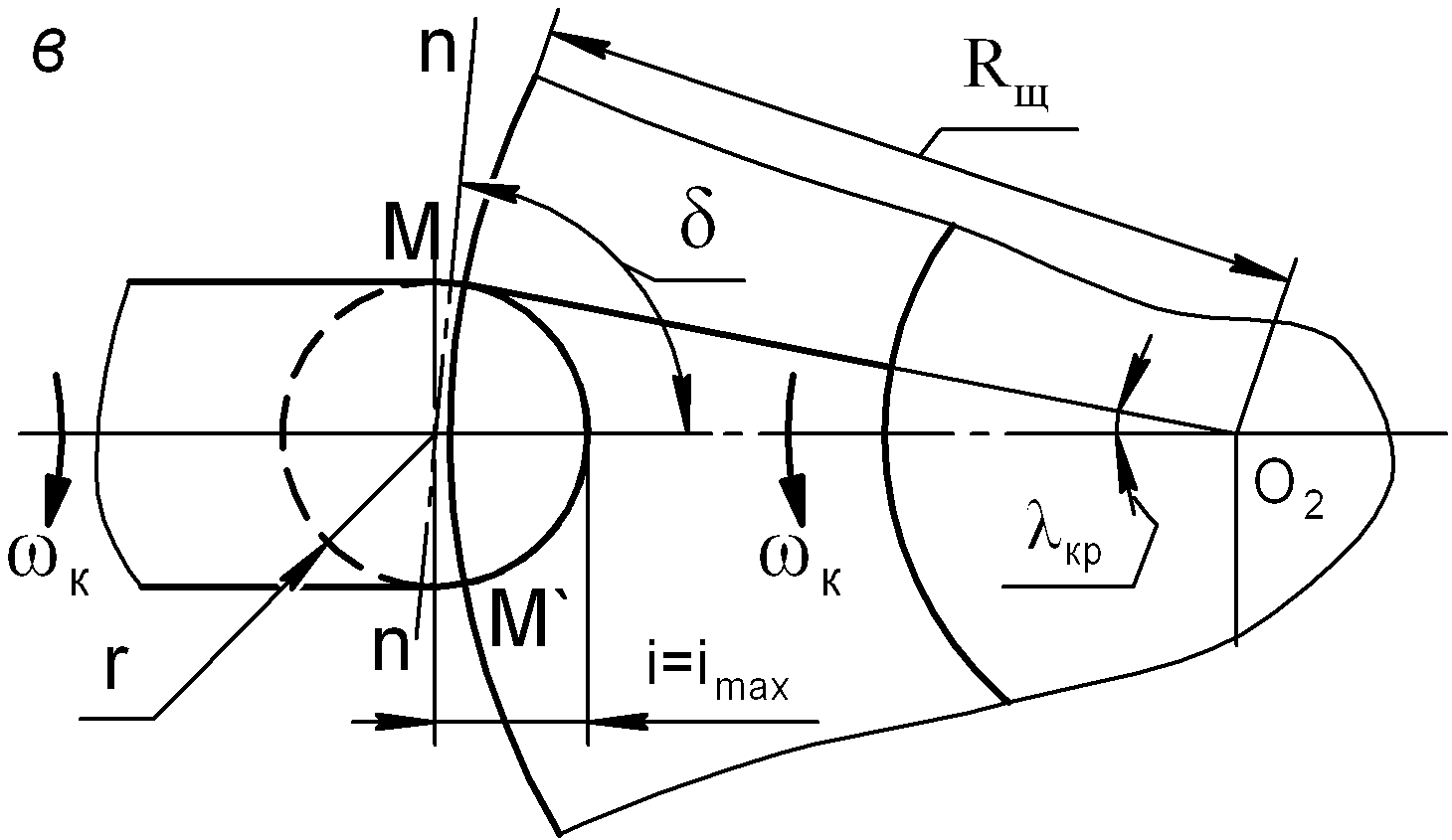
Рис. 3. Схема контактного взаимодействия проволочки с кромкой при расчёте начальных (а), текущих (б) геометрических параметров и при максимальном натяге (в)
Cила, действующая на конце проволочки, в момент удара направлена перпендикулярно к её оси и определяется по формуле [4]

где k – коэффициент повышения жёсткости проволочек при действии на них центробежной силы инерции; ω щ – угловая скорость вращения щётки; l и – длина изгибающейся части проволочек (l и = 0,8 l); m – масса проволочки; Е – модуль упругости материала проволочки; J – момент инерции её поперечного сечения.
Характер ударного деформирования поверхности радиусной кромки лопатки определяется не только силой Р, но и физико-механическими свойствами соударяющихся тел, размерами и формой внедряемого конца проволочки. Для нахождения глубины остаточного отпечатка при ударе проволочкой можно воспользоваться эмпирической зависимостью [5]
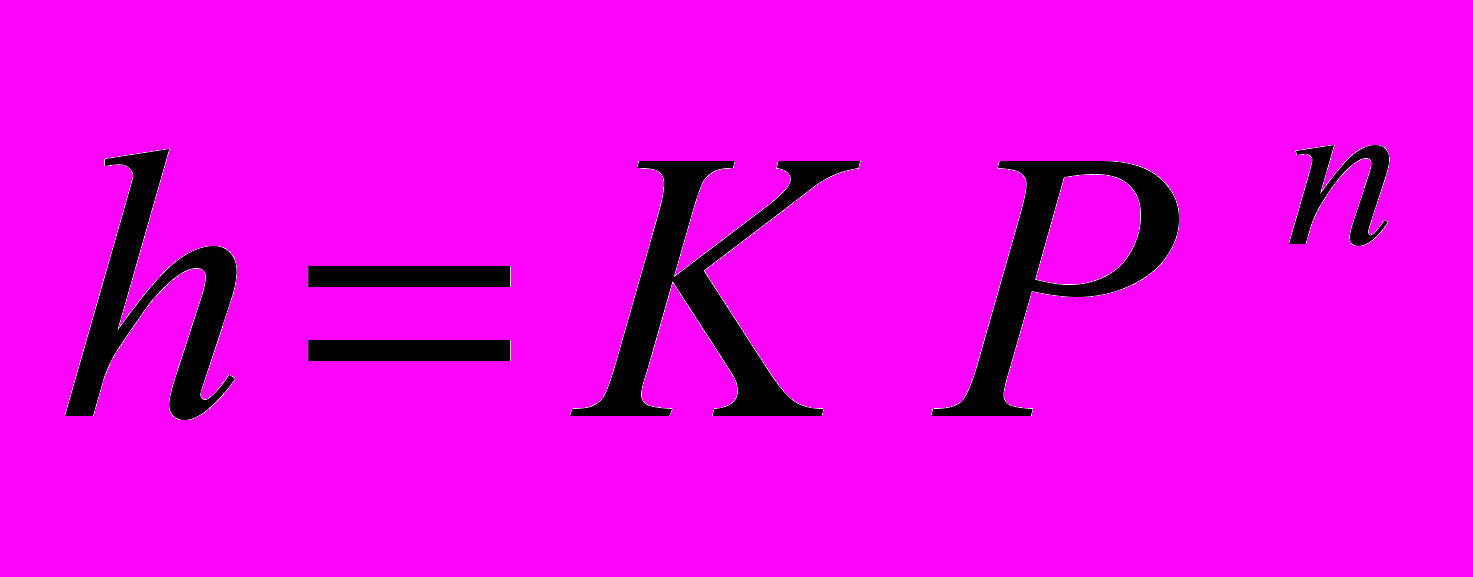
где K и n – соответственно коэффициенты, зависящие от свойств материалов и формы ударного элемента.
Экспериментальными исследованиями установлено, что при обработке титановых сплавов K = 3,067 · 10 – 5 м / Н n, n = 0,67.
При косом ударе максимальная глубина отпечатка h max (рис. 4) определялась проецированием последнего равенства на нормаль к обрабатываемой поверхности:

В
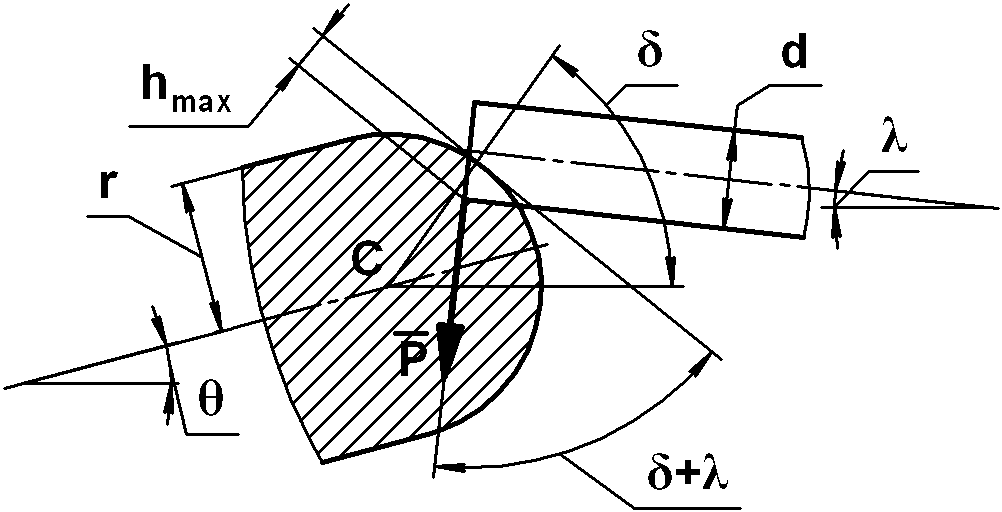
И
Рис. 4. Схема к расчёту деформации при ударе
з таблицы видно, что с возрастанием угла атаки глубина отпечатка сначала резко увеличивается (в районе вершины радиусной кромки), а затем в месте перехода кромки в поверхность пера лопатки стабилизируется, достигая наибольших значений. При этом сглаживающая обработка, приводящая к снижению шероховатости обработанной поверхности, возможна при условии h max ≤ R max. Обработке щётками предшествует операция полирования кромок, которая обеспечивает R max = 6,4…8 мкм. Близкая к этим значениям глубина h max имеет место при вращении щётки с угловой скоростью ω щ = 152 с –1 (v щ = 19 м/с). К допустимому для рассматриваемого случая сглаживанию приводит также обработка со скоростью v щ = 16 м/с. Использование этих скоростей считалось наиболее целесообразным.
Исследование шероховатости и микротвёрдости поверхности обработанных участков проводилось на натурных образцах. Образцы подразделялись на исходные (с неупрочнёнными кромками) и опытные. Исходные образцы представляли собой часть, отрезанную от пера лопатки на электроэрозионном станке 4Г721М. Сами лопатки затем запрессовывали в гнёзда диска и обрабатывали щёткой на различных режимах. После обработки их выпрессовывали из диска и вырезали ещё один опытный образец с упрочнённой кромкой. Таким образом, появлялась возможность сравнивать показатели качества поверхности опытных и исходных образцов, принадлежащих одной лопатке.
Шероховатость обработанной поверхности кромки определяли как путём сравнения с эталоном на микроскопе МБС-2, так и измерением на профилометре реплик-слепков, отображающих микронеровности на ацетилацетатной (ацетонорастворимой) кинофотоплёнке. Для реализации этого метода измерения были разработаны специальные устройства размягчения плёнки, подготовки и крепления реплик.
Контактная сила и глубина отпечатка при ударе
Угол θ, град | Скорость щётки v щ , м/с | Угловая скорость ω щ , с-1 | Коэффициент k | Контактная сила Р, Н | Угол атаки (δ + λ), град | Глубина отпечатка h max· 10-6, м |
1,77 1,25 0,75 0,25 0 | 16 | 128 | 1,06 | 0,086 | 12,8 38,8 55,4 75,5 90 | 1,3 3,7 4,9 5,7 5,9 |
1,77 1,25 0,75 0,25 0 | 19 | 152 | 1,08 | 0,106 | 12,8 38,8 55,4 75,5 90 | 1,5 4,3 5,6 6,6 6,8 |
Обработка со всеми указанными режимами приводит к улучшению поперечной шероховатости кромок (с исходной шероховатостью Ra = 2,5 мкм). Уменьшение высоты микронеровностей происходит заметнее на участках кромки, прилежащих к поверхностям спинки и корыта пера, и в меньшей степени – на среднем участке радиусной кромки. Риски на кромках с исходной шероховатостью R a = 2,5 мкм полностью не выводятся, но сглаживаются вершины микронеровностей. Наилучший результат по шероховатости получен при скорости v щ = 19 м/с.
Микротвёрдость поверхности оценивали на приборе ПМТ-3. Образцы устанавливали в металлическое кольцо и фиксировали в требуемом положении заливкой сплавом Вуда. Отмечается относительное повышение микротвёрдости поверхностного слоя на 17…22%, причём большие значения прироста микротвёрдости соответствуют обработке с большими скоростями. Толщина упрочнённого слоя составляет 20…25 мкм. В вершине кромки и в местах сопряжения с телом лопатки толщина слоя отличается на 2,2…2,5 мкм. Для исследования остаточных напряжений по методу Н.Н. Давиденкова применялись образцы – прямые цилиндрические стержни диаметром, равным двойному радиусу кромки, с шероховатостью Ra = 2,5 мкм и длиной, равной ширине лопатки. Обработка образцов ВМЩ производилась в специально спроектированном приспособлении, запрессованном в паз диска колеса и представляющем собой имитатор лопатки компрессора. По мере удаления обработанных поверхностных слоёв непрерывно фиксировался изгиб образцов.
Остаточные напряжения рассчитывались по формуле, полученной для случая, когда толщина а стравливаемого слоя мала в сравнении с толщиной Н образца
(Н/ а = 2 / 0,1 = 20 > 15):
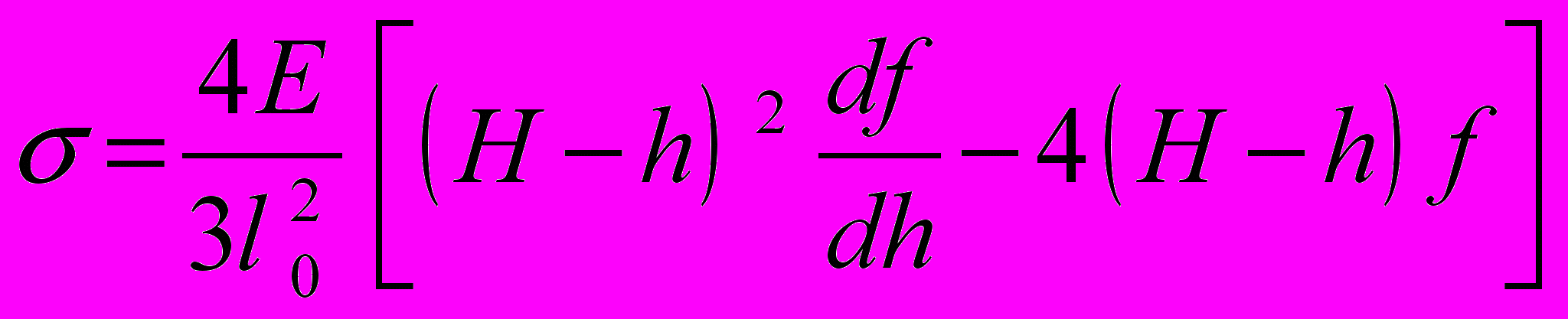
где Е – модуль упругости материала образца; l0 – длина исследуемой поверхности (длина травящегося участка); h – толщина удалённого на данный момент слоя; f – прогиб образца, образовавшийся при стравливании слоя h.
В круглом стержне – образце получена типичная картина распределения остаточных напряжений по толщине упрочнённого слоя. Так, обработка кромки щёткой со скоростью vщ = 19 м/с обеспечивает формирование в поверхностном слое толщиной 23…25 мкм сжимающих остаточных напряжений величиной 54…56 МПа.
Проведены усталостные испытания лопаток на специальном вибростенде воздушного возбуждения по сложной пластиночной форме колебаний (71 гармоника). Частота возбуждения колебаний лопаток f = 6600 Гц, база испытаний N = 2 · 107 циклов. Предел выносливости лопаток, упрочнённых при скоростях 16 и 19 м/с, вырос приблизительно на 18% по сравнению с прочностью неупрочнённых лопаток. Длительные испытания упрочнённых лопаток в составе изделия засвидетельствовали отсутствие трещин на их торцовой поверхности.
БИБЛИОГРАФИЧЕСКИЙ СПИСОК
- Сулима А.М. и др. Основы технологии производства газотурбинных двигателей: Учеб. – М.: Машиностроение, 1996. – 479 с. – ISBN – 5-217-02800-9.
- Александров В.Г. и др. Авиационный технический справочник (эксплуатация, обслуживание, ремонт и надёжность) – М.: Транспорт, 1975. – 432 с.
- Дёмин Ф.И. и др. Технология изготовления основных деталей газотурбинных двигателей. – М.: Машиностроение, 2002. – 328 с. – ISBN – 5-217-03119-0.
- Кургузов Ю.И., Папшев Д.Д. Технологическое обеспечение качества поверхности при упрочнении механическими щётками // Вестник машиностроения. – 1986. – №4. – С. 54-58.
- Батуев Г.С. и др. Инженерные методы исследования ударных процессов. – М.: Машиностроение, 1977. – 240 с.
Статья поступила в редакцию 19 октября 2009 г.
UDC 55.21.21
HARDENING OF BLADES’ EDGES OF THE DRIVING WHEEL
GAS-TURBINE ENGINES
J.I.Kurguzov1, M.J.Kurguzov2
1 Samara State Technical University
244, Molodogvardeyskaya st., Samara, 443100
2 «Prominvest» Сo, Ltd
64, Metallistov st., Samara, 443105
The method of choosing the geometrical parameters of adjustment of a disk brush with a section arrangement of pile for processing of blades’ edges of compressor disk, and also a method of choosing the regimes of processing, providing required quality of a surface and increasing the fatigue durability are described in the article.
Key words: the driving wheel, shovel end face, the disk brush, strengthening processing, quality of the surface, fatigue durability.
УДК 681.5