Получение структур кни с использованием методов химической обработки и сращивания кремниевых пластин
Вид материала | Документы |
- Технология прямого сращивания пластин кремния и технологические маршруты изготовления, 689.61kb.
- Технология прямого, 498.19kb.
- Технология прямого, 496.93kb.
- Рабочей программы дисциплины Структуры и алгоритмы обработки данных по направлению, 21.62kb.
- Исследован паразитный биполярный эффект в кни моп транзисторах. Создана модель взаимодействия, 28.42kb.
- Рабочая программа по дисциплине "Организация ЭВМ и систем" для специальности 230102, 93.42kb.
- Методика проектирования инструмента. Содержание рабочего чертежа на него. Формы, геометрия, 172.74kb.
- Правила обработки и анализа результатов эксперимента с использованием методов математической, 47.52kb.
- Тема 7: Организации обучения с использованием активных методов, 369.95kb.
- Программа дисциплины структуры и алгоритмы компьютерной обработки данных для специальности, 506.16kb.
Глава 5. ПОЛУЧЕНИЕ СТРУКТУР КНИ С ИСПОЛЬЗОВАНИЕМ МЕТОДОВ ХИМИЧЕСКОЙ ОБРАБОТКИ И СРАЩИВАНИЯ КРЕМНИЕВЫХ ПЛАСТИН
В данной главе приведены технологическая схема изготовления и результаты исследований параметров структур КНИ, полученных методами сращивания подложек для изготовления ИС, полупроводниковых приборов, микромеханических устройств и сенсоров специального назначения.
5.1. Влияние химической обработки на контактную разность потенциала поверхности пластин Si
В процессе обработки и послеоперационного контроля на поверхности полупроводниковой пластины адсорбируются молекулы воды в виде отдельных диполей или фрагментов, имеющих малый дипольный момент, либо образуются водородные связи. Измерением величины контактной разности потенциала (КРП) контролировалось состояние поверхности пластин кремния в процессе получения структур КНИ [2–6]. Для оценки количества воды, сорбированной поверхностью кремния в атмосферных условиях, использовался метод тепловой десорбции с использованием масс-спектрометра МХ-7302 при температурах до 900 С.
Результаты исследований показали, что снижение КРП (на 0,6 В в диапазоне температур от 100 до 900 С) после термообработки связано с удалением молекул Н2О и групп ОН, сорбированных на поверхности кремния (иными словами, с приобретением поверхностью пластины гидрофобных свойств). Наибольшее изменение КРП, имеющее место при температурах обработки 300 – 400 С, согласуется с температурным диапазоном максимальных потерь воды.
В течение нескольких часов после химической обработки подложек в атмосферных условиях значения КРП стабилизируются и далее практически не меняются. Это объясняется появлением естественного слоя оксида кремния на поверхности пластин кремния [1].
5.2. Использование процессов химической обработки для получения структур КНИ
Процесс получения структур КНИ проводился с использованием различных методов сращивания полупроводниковых пластин: непосредственного термокомпрессионного сращивания (НТКС) двух поверхностей Si пластин, сращивания с использованием расплавления стекловидного слоя [7–16]. Для подготовки поверхности Si пластин использовались различные методы химической обработки. Проводилось частичное изменение режимов обработки, в частности, снижалась температура смеси NH4OH/H2O2/H2O для уменьшения агрессивного воздействия на поверхность подложек.
Последовательная обработка подложек аэрозольно-капельным распылением растворов H2 SO4, H2O2 осуществлялась в объемном соотношении 4:1, при температуре 110 С, в течение 90 с; затем проводилась обработка в растворе смеси NH4OH/H2O2/H2O в объемном соотношении 1:2:12, при температуре 20 С, в течение 4 мин; в заключение осуществлялась отмывка в воде и сушка.
Обработка подложек погружением в раствор смеси NH4OH/H2O2/H2O осуществлялась в объемном соотношении 1:1:6,5, при температуре 20 С, в течение 10 мин, с применением звуковых волн частотой 850 кГц, мощностью 250 Вт; далее проводились отмывка в воде и сушка.
Подготовленные поверхности полупроводниковых пластин приводились в соприкосновение друг с другом в обеспыленной атмосфере. Для этого применялось устройство, позволяющее соединять Si пластины непосредственно после химической обработки (рис.4.5). Пластины, "слипшиеся" за счет возникших сил адгезии, отжигались в окислительной атмосфере.
На рис.5.1, 5.2 представлены схемы пластин в зависимости от свойств поверхности, полученных в результате химической обработки пластин Si (гидрофобной после обработки в травителях оксидных слоев и гидрофильной после обработки в растворах H2SO4/H2O2, NH4OH/H2O2/H2O).
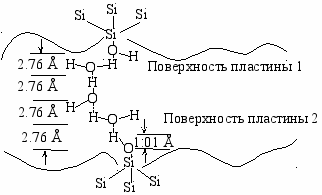
Рис. 5.1. Схема соединения гидрофильных поверхностей пластин Si
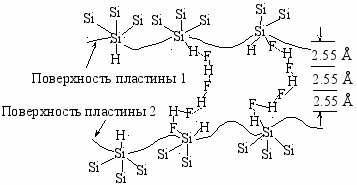
Рис. 5.2. Схема соединения гидрофобных поверхностей пластин Si
Сращивание Si пластин также проводили с использованием нанесенного на поверхность Si бариево-алюмо-силикатного стекла (BaO–Al2O3–SiO2), синтезированного в высокочастотной индукционной плазме.
Использование стекла позволило снизить требования, предъявляемые к качеству обработки и отмывки соединяемых поверхностей и дало возможность соединять различные поверхности, упрощая процесс подготовки и соединения. Однако возможная диффузия примеси в рабочий слой Si пластины при длительных термообработках при высокой температуре ограничивает применение данного метода.
На рис.5.3 представлен скол кремниевой структуры, полученной после химической обработки, имплантации ионов водорода с энергией 100 кэВ, дозой 4,5∙1016 см2 и термического отжига кремниевой пластины при T = 450 C; t = 20 мин в процессе получения структур КНИ с тонкими изолированными слоями методом газового скалывания.
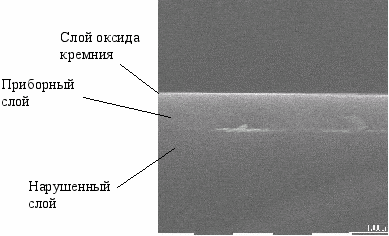
Рис. 5.3. Микрофотография скола кремниевой структуры после имплантации ионов водорода и термического отжига пластины при T = 450 C; t = 20 мин (изображение получено с использованием РЭМ)
Получение структур с толщиной рабочего слоя более 5 мкм проводили методами сращивания подложек и последующего химико-механического удаления части рабочей пластины до заданной толщины.
Рассмотренными методами были получены структуры КНИ для производства ИС с повышенной радиационной и термической устойчивостью, а также элемнты микроэлектромеханических систем специального назначения [1].
5.3. Исследование характеристик структур КНИ, полученных методами сращивания кремниевых пластин и газового скалывания
На основе анализа литературных данных и практического опыта по изготовлению структур КНИ с применением механического и плазменного утончения приборной пластины разработан технологический маршрут изготовления структур КНИ методами сращивания и газового скалывания, представленный в главе 2. Ключевой операцией этого маршрута является подготовка поверхности опорных и приборных пластин перед их стыковкой, и контроль состояния стыкуемых поверхностей. Ниже подробнее рассмотрены особенности операций маршрута.
Имплантация ионов водорода в приборную пластину сопровождается процессами, которые могут приводить к загрязнению поверхности слоя оксида и приборного слоя металлами, распыляемыми с конструкций имплантера. Для исключения загрязнения на данной технологической операции поверхность рабочей Si пластины окислялись. После имплантации перед стыковкой пластин слой SiO2 стравливали.
Стыковку пластин выполняли на воздухе и в вакууме сразу после их жидкостной химической обработки и сушки. Операцию стыковки выполняли вручную.
Отщепление части приборной пластины от сращенной структуры выполняли путем быстрого, со скоростью более 50 °С/мин, нагрева состыкованной структуры в специализированной печи СДО. Такая скорость нагрева достигалась быстрым вводом лодочки со структурами в горячую зону печи, имеющую температуру 600 С.
Процессы химической обработки и травления поверхности Si пластин применялись:
1. Перед окислением опорной и приборной пластин
- аэрозольно-капельным распылением растворов H2SO4/H2O2, NH4OH/H2O2/H2O;
- погружением в раствор NH4OH/H2O2/H2O с использованием мегазвуковой энергии;
2. При удалении слоя оксида кремния после имплантации водорода:
- травлением слоя оксида кремния в 10%-м водном растворе плавиковой кислоты;
3. При активации поверхностей приборной и опорной пластин:
- аэрозольно-капельным распылением растворов H2SO4/H2O2, NH4OH/H2O2/H2O;
- обработка в воде в течение одного часа.
На основе разработанных процессов химической очистки были получены образцы по технологии сращивания и последующего утончения (аналог BESOI) и технологии сращивания и газового скалывания (аналог smart-cut). Качественную оценку степени совершенства кристаллической структуры изолированных кремниевых слоев структур КНИ осуществляли на основе анализа кривых качания. Полуширина дифракционных пиков кривых качания от поверхности приборного слоя полученных структур КНИ составила 20 – 25", что близко к аналогичным параметрам исходных кремниевых пластин. Данный результат свидетельствует о низкой дефектности кремниевых слоев структур КНИ и отсутствии в них значительных напряжений. Исследования сколов и шлифов полученных структур на оптическом, растровом электронном, атомно-силовом микроскопах, а также неразрушающий контроль многослойных структур методом ИК-фотометрии показали, что в области спая структур отсутствуют как макро-, так и микродефекты – несоединившиеся участки, полости, поры.
По технологии сращивания подложек и газового скалывания были изготовлены опытные образцы структур КНИ, предназначенные для производства радиационно-стойких ИС со следующими характеристиками:
- диаметр структур, мм……………………….………100, 150;
- удельное сопротивление, Ом∙см ………………………….20;
- толщина изолированного слоя Si, мкм…………..0,5, 0,8, 37;
- тип используемого диэлектрического слоя.…………….SiO2;
SiO2/Si3N4/SiO2 + многокомпонентное стекло (BaO/Al2O3–SiO2);
- толщина изолирующего слоя диэлектрика, мкм…1,2; 4 – 10;
- тип опорной подложки………..КЭФ-4,5 (100), КДБ-12 (100),
КДБ-10 (111), стекло ЛК 105;
- толщина структуры, мкм……………………...460-525, 2000.
На границе газового скалывания наблюдаются неровности поверхности приборного и рабочего слоев структуры КНИ, вызванные разрывом пор, образующих нарушенный слой (рис. 5.4). Эти неровности удаляются последующей суперфинишной химико-механической полировкой.
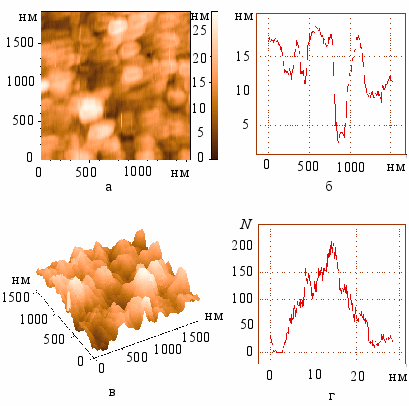
Рис. 5.4. Поверхность приборного слоя структуры КНИ, полученной газовым скалыванием: а – внешний вид поверхности образца сверху; б – профиль шероховатости поверхности; в – внешний вид поверхности в изометрии; г – распределение неровностей поверхности по размерам
5.4. Результаты разработки процесса формирования островковых структур КНИ
На основе процессов сращивания кремниевых пластин через слои многокомпонентного стекла и удаления части рабочей пластины кремния была разработана технологическая схема изготовления островковых структур КНИ.
1. Подготовка опорных пластин:
1.1. Контроль геометрических, кристаллографических параметров пластин, механической и химической чистоты их рабочей поверхности.
1.2. Обработка аэрозольно-капельным распылением растворов H2SO4/H2O2, NH4OH/H2O2/H2O либо погружением в раствор NH4OH/H2O2/H2O с использованием мегазвуковой энергии.
1.3. Окисление во влажном кислороде или парах воды для получения слоя двуокиси кремния толщиной 1,80,1 мкм.
1.4. Контроль параметров пластин после окисления:
- толщины слоя SiO2;
- электрофизических параметров слоя SiO2 (напряжения пробоя, наличия подвижного заряда, плотности зарядовых состояний на границе с кремнием);
- шероховатости окисленной поверхности;
- пористости.
2. Подготовка приборных пластин.
2.1. Контроль геометрических, кристаллографических параметров пластин, механической и химической чистоты их рабочей поверхности.
2.2. Обработка кремниевых пластин аэрозольно-капельным распылением растворов H2SO4/H2O2, NH4OH/H2O2/H2O .
2.3. Диффузия сурьмы.
2.4. Удаление стекла травлением в 10%-ном водном растворе плавиковой кислоты и очистка поверхности аэрозольно-капельным распылением растворов H2SO4/H2O2, NH4OH/H2O2/H2O.
2.5. Контроль типа проводимости и уровня легирования приборного слоя.
3. Нанесение стекловидного материала на поверхность полупроводниковых пластин.
4. Очистка, активация, взаимная ориентация и стыковка опорной и приборной пластин. Обработка пластин кремния аэрозольно-капельным распылением растворов H2SO4/H2O2, NH4OH/H2O2/H2O либо погружением в раствор NH4OH/H2O2/H2O с использованием мегазвуковой энергии.
5. Контроль качества предварительного соединения:
- наличия полостей;
- взаимной ориентации.
6. Термообработка стыкованных пластин. Термическое сращивание заготовок структур КНИ.
7. Контроль качества сращивания.
8. Шлифовка приборной пластины и травление в растворе КОН.
9. Контроль параметров структуры после шлифовки и травления в растворе КОН:
- толщины остаточного слоя;
- морфологии поверхности остаточного слоя;
- внешнего вида.
10. Полировка приборной пластины.
11. Контроль параметров КНИ структуры после полировки приборной пластины:
- толщины остаточного слоя;
- морфологии поверхности остаточного слоя;
- внешнего вида.
12. Окончательный контроль структуры:
- внешнего вида, морфологии поверхности и кромки приборного слоя;
- толщины приборного слоя;
- толщины диэлектрического изолирующего слоя;
- типа проводимости приборного слоя;
- уровня легирования приборного слоя;
- плотности кристаллографических дефектов в приборном слое;
- плотности дефектов в изолирующем диэлектрическом слое;
- плотности заряда в изолирующем диэлектрическом слое;
- плотности зарядовых состояний на границе между приборным и диэлектрическим слоями;
- кристаллографической ориентации приборного слоя по отношению к опорной пластине;
- подвижности носителей заряда в приборном слое.
Определены параметры изготовленных экспериментальных образцов структур. Ниже приведены типовые характеристики экспериментальных образцов структур КНИ, являющихся основой для биполярной технологии:
Диаметр структур, мм……………………………..100, 150;
Ширина краевой зоны, на которой
приборный слой отсутствует, мм…………….…..…….3-4;
Общая толщина структуры, мкм…………….……480-720;
Параметры приборного слоя:
- толщина, мкм………………….….…….…8, 12, 18, 36;
- тип проводимости………………..…………..……n, p;
- концентрация носителей заряда, см-3………..…1015;
- плотность распределения дефектов,
выявляемых травлением, см-2………………….…....10;
- неоднородность толщины, %…………………...….10;
- шероховатость внешней поверхности, нм……….…3.
На рис. 5.5 представлено изображение островковой структуры КНИ, полученной на основе разработанной технологической схемы.
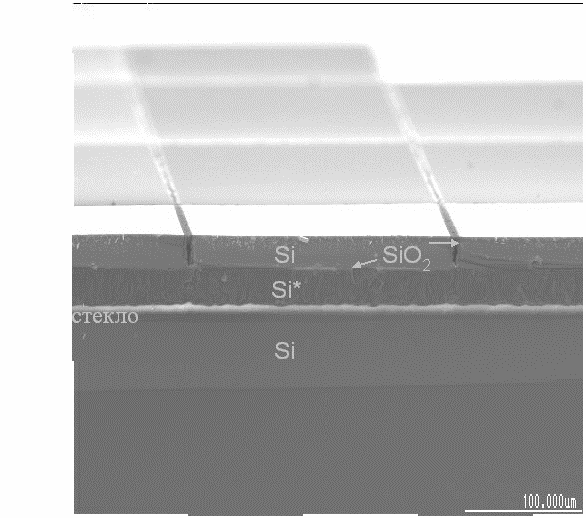
Рис. 5.5. Изображение островковой структуры КНИ
Параметры полученных образцов подтверждают перспективность выбранных технологических маршрутов получения структур КНИ. На островковых структурах КНИ были изготовлены работоспособные микросхемы. Полученные результаты подтверждают целесообразность подобного производства на предприятиях микроэлектроники для ИС с повышенной радиационной и термической устойчивостью, а также датчиков и элементов микроэлектромеханических систем специального назначения.
В результате исследований разработан маршрут изготовления и получены образцы структур КНИ различными методами с использованием технологических операций сращивания через слои SiO2, многокомпонентного стекла, а также газового скалывания и различных способов утончения. Исследованы поверхности пластин кремния и приборного слоя структур КНИ, полученных с использованием указанных методов. Результаты исследований параметров полученных образцов позволяют говорить о перспективности выбранных технологических процессов получения структур КНИ.
В ходе изучения работоспособности полученных ИС на основе изготовленных образцов сделан вывод о том, что технология получения структур КНИ методами сращивания кремниевых пластин и газового скалывания, а также утончения (в том числе и технология получения островковых структур КНИ), несомненно, найдёт широкое применение в разработке и производстве оптоэлектронных, силовых, трехмерных, микроэлектромеха-нических, квантовых и вакуумно-микроэлектронных ИС, радиационно- и термостойких ИС, различного рода датчиков.
СПИСОК ЛИТЕРАТУРЫ К ГЛАВЕ 5
1. Тимошенков С.П., Прокопьев Е.П., Калугин В.В., Дьячков С.А. Очистка и активация поверхности в методе прямого соединения пластин кремния с использованием химической сборки поверхности методом молекулярного наслаивания // Оборонный комплекс – научно-техническому развитию России. № 3. 2000. С. 75 85.
2. Жарких Ю.С. и др. Контроль результатов химических обработок кремния безконтактными методами // Микроэлектро-ника. 1980. № 1. C. 82 – 85.
3. Мажулин А.В. Исследование возможности производственного контроля качества отмывки поверхности кремния методом Кельвина // Электронная техника. Сер. Материалы ЭТ. 1981. Вып.1. С. 30, 31.
4. Белановский А.С. Абсорбция и адсорбция на поверхности полупроводников // Обзоры по ЭТ. Сер. Микроэлектроника. 1969. Вып. 58(127). С. 201.
5. Абессонова Л.Н. Влияние толщины окисла на характеристики структуры Si–SiO2 // Тезисы докладов конференции. Сер. 3. Микроэлектроника. 1989. Вып. 1. С. 17.
6. Александров Е.В Дигностика и контроль физико–химического состояния поверхности кремниевых пластин методом контактной разности потенциалов // Тезисы доклада конференции. Сер. 3. Микроэлектроника. 1989. Вып. 1.
7. Furuhawa. M. Silicon-to-Silicon direct bonding method // J.Appl.Phys. 1986. V. 60. № 8. P. 2987 – 2989.
8. Masaru S. Технология прямого соединения кремниевых пластин и ее применение // J. Inst. Electron. аnd Соmmun. Еng. Jар. 1987. V. 70. № 6. P. 593 – 595.
9. Lestic A., Muller R. S. Low-temperature silicon-silicon bonding with oxides. FIELD // Acts polytechn. seand. Elec. End. Sr. 1988. № 63.P. 151 – 153.
10. Kanda Y., Matsuda K., Murayama C., Sugaya J. The mechanism of field-assisted silicon-glass bonding // Sensors and Actuators. 1990. V. A21–A23. P. 939.
11. Jeung Sang Go, Young-Ho Cho. Experimental evaluation of anodic bonding process based on the Taguchi analysis of interfacial fracture toughness // Sensors and Actuators. 1999. Vol. 73.P. 52-57.
12. Carison D.E. Ion depletion of glasses at a blocking anode: I. Theory and experimental results for alkali silicate glass // J. Am. Ceram. Soc. 1974. V. 57. P. 291.
13. Anthony T. R. Anodic bonding of imperfect surfaces // J. Appl. Phys. 1983. V. 54. № 5. P. 2419 – 2428.
14. Дьячков С.А., Калугин В.В. Анодное соединение элементов микроэлектромеханических приборов // Тезисы докладов Всероссийской межвузовской научно-технической конференции "Микроэлектроника и информатика – 99". Москва. 1999. C. 62.
15. Tong Q.-Y., Goesele U. Semiconductor Wafer Bonding: Science, Technology // Wiley. New York. 1988.
16. Попов В.П. Создание КНИ-структур для ультрабольших интегральных схем // Известия вузов. Электроника. 1998. № 5. C. 22 – 29.