Научные основы и технологические способы обработки гетерофазных сплавов с высоким уровнем конструктивной прочности
Вид материала | Автореферат |
СодержаниеВо второй главе В третьей главе В четвертой главе |
- Рекомендовано Минобразованием России для направления подготовки диплом, 89.5kb.
- Технологические основы процесса сварки металлов и сплавов (её классификация, прогрессивные, 1329.56kb.
- Анализ тенденций развития рынка вычислительной техники в Москве и в России, 113.84kb.
- Научные основы и технологические решения получения высокопрочных алюминийсодержащих, 586.93kb.
- Ная деятельность и достаточен ли этот уровень для модернизации страны очевидны: уровень, 127.16kb.
- Вопросы вступительных экзаменов в докторантуру PhD по специальности «Материаловедение, 27.1kb.
- Физико-технологические основы новых способов термической обработки высокопрочного чугуна, 72.96kb.
- Пути и проблемы формирования здорового образа жизни, 288.04kb.
- Научные исследования и испытания авз, 66.92kb.
- Роль и функции преподавателя в подготовке нового поколения специалистов с высоким уровнем, 160.41kb.
С целью получения различного количества и типов структурных составляющих образцы нагревались до температур (g+a) области, выдерживались в течение 10 мин, охлаждались в воде, масле или на воздухе.
Термокинетические диаграммы строились микроструктурным и дилатометрическим методами. Применялся высокотемпературный микродилатометр, с помощью которого удавалось фиксировать изменение длины образца на 0,005%. На построенные термокинетические диаграммы для наглядности наносились кривые, соответствующие скорости охлаждения сердцевины образцов сечением 15х15 мм в применяемых средах: 1 – в воде, 2 – в масле, 3 – на воздухе.
Как видно на рис.1, а (кривая 1), для стали 10кп даже при закалке в воду образца сечением 15х15 мм невозможно получить чистую феррито-мартенситную структуру. При закалке в воду от 760оС из аустенита выделяется небольшое количество избыточного феррита, а оставшийся аустенит распадается на мартенсито-бейнитную смесь. Повышение температуры нагрева в МКИ до 800оС сопровождается снижением устойчивости аустенита, и после выделения избыточного феррита, переохлажденный аустенит практически полностью превращается в бейнит. Закалка в масло от всех температур двухфазной области обеспечивает образование феррито-бейнитной структуры (кривая 2 на рис.1). При охлаждении на воздухе из нижней половины межкритического интервала (кривая 3 на рис. 1,а) образуется, в основном, феррито-бейнитная структура с небольшим содержанием перлита, количество которого возрастает с повышением температуры нагрева в МКИ.
Легирование малоуглеродистой стали ~1,5% марганца способствует заметному повышению устойчивости аустенита при охлаждении из МКИ (рис. 1, б). В стали 09Г2 после закалки в воду от 760оС в сердцевине образца сечением 15х15 мм формируется феррито-мартенситная структура и отсутствует феррит превращения. Вместе с тем, при охлаждении на воздухе от любых температур МКИ перлит не образуется.
Микролегирование бором стали с 1,5% марганца в значительной мере подавляет выделение избыточного феррита и особенно перлита, понижает температуру начала мартенситного превращения и смещает область распада аустенита по II ступени в сторону меньших скоростей охлаждения (рис. 1,в). Аналогично легированная сталь с вдвое меньшим содержанием углерода (05Г2Р) после нагрева на те же температуры имеет устойчивость переохлажденного аустенита практически такую же, как у стали 10Г2Р.
![]() t,ºС ![]() 0,1 1 10 102 103 104 , с ![]() ![]() М Б Ф t,ºС ![]() П ![]() Ac3 Ac1 1 2 3 а) | ![]() 0,1 1 10 102 103 104 , с ![]() ![]() ![]() ![]() ![]() ![]() Б М Ф ![]() ![]() П ![]() ![]() ![]() ![]() Ac3 Ac1 1 2 3 б) | |
![]() 0,1 1 10 102 103 104 , с ![]() ![]() ![]() ![]() М Б Ф ![]() ![]() ![]() ![]() ![]() Ac3 Ac1 t,ºС ![]() 1 2 3 ![]() в) | ![]() 0,1 1 10 102 103 104 , с ![]() М Б Ф ![]() ![]() ![]() ![]() ![]() Ac3 Ac1 ![]() ![]() ![]() ![]() ![]() 1 2 3 г) |
Рис. 1. Термокинетические диаграммы распада аустенита в сталях 10кп (а) и 09Г2 (б), 10Г2Р (в), ТН=760оС; 05Г2С2 (г), ТН=780оС; 1 – охлаждение в воде, – в масле, 3 – на воздухе.
Введение в низкоуглеродистую сталь ~1% кремния, повышающего критические точки и увеличивающего межкритический интервал температур, расширяется область выделения избыточного феррита, а области распада по перлитному и бейнитному механизму смещаются в сторону меньших скоростей охлаждения. Эти эффекты усиливаются при увеличении в стали концентрации кремния до 1,8% с одновременным легированием ~1,5% марганцем (рис. 1,г).
Параметры термокинетических диаграмм, построенных в данной работе, отражают не усредненное по объему металла состояние аустенита (его химический состав, размер зерна и т.д.), а дают спектр состояний его различных микрообъемов, «развернутый» по скоростям охлаждения (температуре и времени превращений). Так, формирование первых порций избыточного феррита или мартенсита происходит в областях аустенита наиболее бедных по содержанию углерода и других растворенных атомов, а последними будут испытывать превращение самые насыщенные примесями участки аустенита с образованием наиболее низкотемпературных продуктов распада.
Из различных параметров, описывающих превращение переохлажденного аустенита, температура начала образования мартенсита (Мн) является наиболее объективным критерием, в силу относительной точности и легкости экспериментальной и расчетной оценки, а также благодаря тому, что быстрым охлаждением «замораживается» состав аустенита. Расчет Мн для конструкционных сталей достаточно надежно проводится по уравнению А.А. Попова, которое применительно к изученным сталям имеет следующий вид:
Мн = 520 – 320(%С) – 45(%Мn) – 5(%Si) (1)
C использованием урав. (1) по химическому составу сталей (табл.1) были найдены значения Мн для образцов, испытавших полную аустенитизацию (Тн >Ас3), а также содержание углерода в аустените образцов, нагретых до определенных температур (Тн) в МКИ, которые превышали Ас1 на DТ (табл.2).
Таблица 2
Оценка содержания углерода в аустените, сформировавшемся
в МКИ, по значению Мн
Сталь | Мн, оС при Тн > Ас3 | Нагрев в МКИ | |||
Расчет по урав. (1) | Справочные данные | Тн (DТ =Тн-Ас1), оС | Мн, оС (экспер.) | % С в аустените | |
10кп | 490 | - | 760 (40) | 390 | 0,41 |
800(80) | 440 | 0,25 | |||
09Г2 | 417 | 460 | 760(40) | 315 | 0,42 |
800(80) | 380 | 0,22 | |||
10С1 | 475 | - | 800(50) | 365 | 0,46 |
860(110) | 410 | 0,32 | |||
05Г2С2 | 414 | ~ 430 | 780(20) | 285 | 0,45 |
900(140) | 370 | 0,20 | |||
970(230) | 385 | 0,15 |
Из табл. 2 видно, что первые порции аустенита, образующиеся при небольшом перегреве над Ас1 (DТ @ 40оС), сильно обогащены углеродом. Вне зависимости от содержания углерода в стали, количество углерода в аустените после такого нагрева достигает 0,41-0,46%, в результате чего устойчивость переохлажденного аустенита и Мн достигают уровня, характерного для сталей с таким общим содержанием углерода, что способствует образованию в структуре низкотемпературных продуктов распада аустенита (мартенсита, бейнита) при ускоренном охлаждении из МКИ и отсутствию перлита.
С увеличением температуры нагрева в МКИ устойчивость переохлажденного аустенита снижается, повышается Мн, что обусловлено уменьшением содержания углерода в образующемся аустените, возникновением неоднородности по химическому составу между микрообъемами образца и внутри зерен. Поэтому интенсивность действия углерода и легирующих элементов на термокинетическую диаграмму (устойчивость переохлажденного аустенита, Мн) после нагрева в различные области МКИ иная, чем в тех же сталях после полной аустенитизации (Тн>Ас3 + 30оС).
Практическая значимость данного явления состоит в том, что при совместном легировании стали Mn и Si (В) возможно снижение содержания углерода с 0,1 до 0,05% при сохранении тех же характеристик термокинетической диаграммы или при том же углероде в стали удается уменьшить скорость охлаждения изделий (увеличить их сечение).
Следовательно, подбором композиции сталей, температуры нагрева в МКИ и скорости последующего охлаждения удается целенаправленно регулировать не только структуру и фазовый состав, но и содержание углерода и легирующих элементов в отдельных фазах, что расширяет спектр механических свойств сталей.
Во второй главе анализируются данные по микроструктуре, фазовому составу и механическим свойствам низкоуглеродистых сталей, испытавших нагрев в межкритический интервал температур.
Исследование методами оптической и электронной микроскопии группы малоуглеродистых низколегированных сталей (см. табл.1) показало, что при нагреве в межкритический интервал температур образование первых порций аустенита в образцах с исходной феррито-перлитной структурой происходит в перлитных зернах. Дальнейшее увеличение количества аустенита связано с миграцией его границ в ферритные зерна. После охлаждения низкотемпературные продукты распада аустенита (мартенсит-бейнит), окруженные выделениями нового феррита, располагаются по границам старого феррита, который не претерпел превращение при нагреве (рис. 2)
Выявление двух типов феррита: исходного, который не претерпел превращения при нагреве в МКИ, и нового, выделяющегося из аустенита при окончательном охлаждении, проводилось по специальной двухэтапной методике. Структурные характеристики (объемная доля каждой фазы, размер зерен) рассчитывались с учетом соответствующих геометрических и статистических закономерностей.
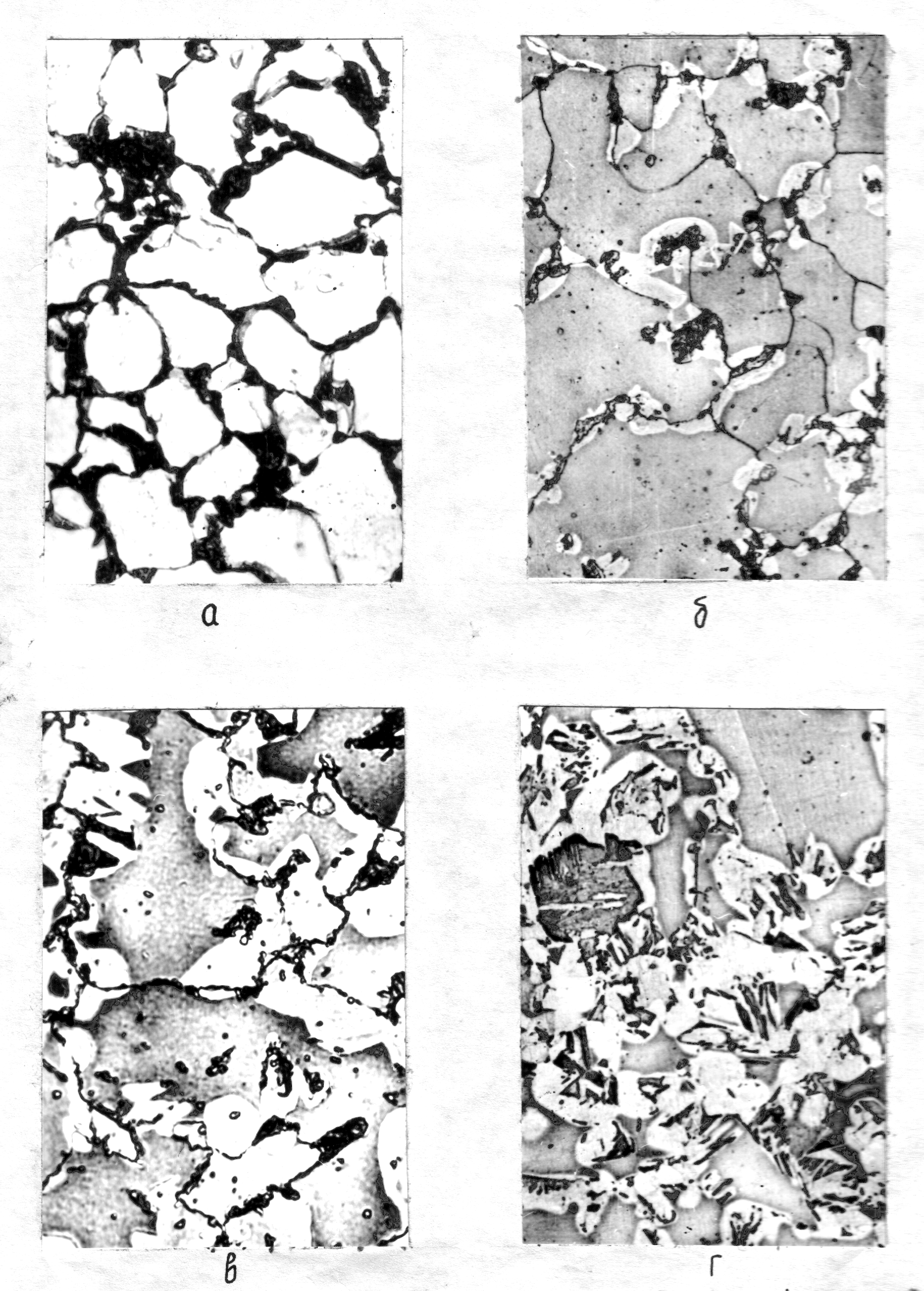
Рис. 2. Микроструктура стали 09Г2 после охлаждения в воде (а), в масле (б,в) и на воздухе (г); х 2000
При закалке образцов сечением 15х15 мм из исследованных сталей в воду или масло после нагрева на 30оС выше Ас1 образуется реечный мартенсит с «косо» расположенными мидрибом с высокой плотностью микродвойников и дислокаций, что связывается с низкой Мн из-за максимально высокой концентрацией углерода в первых порциях аустенита, сформировавшихся из перлита. Уменьшение содержания углерода в аустените при увеличении его количества и температуры образования приводит при закалке в воду к возникновению высокотемпературного мартенсита, в котором отдельные рейки с высокой плотностью дислокаций собраны в пакеты. При охлаждении из верхней области МКИ распад аустенита происходит по бейнитному механизму.
Распределение дислокаций в феррите неоднородно: вблизи границ феррит-мартенсит возникает высокая плотность дислокаций, которые образуют клубки и сложные сплетения. Повышенная плотность дислокаций на границе феррит-мартенсит связана, по всей видимости, с напряжениями, возникающими при g® a превращении. По мере удаления от межфазной границы плотность дислокаций резко падает.
В случае феррито-бейнитной структуры распределение дислокаций в феррите более однородно, чем в сталях с феррито-мартенситной структурой, хотя и здесь плотность дислокаций выше вблизи межфазной границы.
Типичные зависимости, отображающие изменение количества структурных составляющих в стали 10кп с повышением температуры нагрева в МКИ, показаны на рис. 3. В легированных сталях ход этих кривых почти аналогичный, хотя они смещены по температурным областям, и количественные соотношения иные.
Так, в сталях 09Г2 и 10Г2Р после аналогичных обработок количество аустенита qА меньше (~ 5%), чем в стали 10кп, испытавшей аналогичную обработку, при том же темпе нарастания количества аустенита с повышением температуры нагрева (рис. 4).
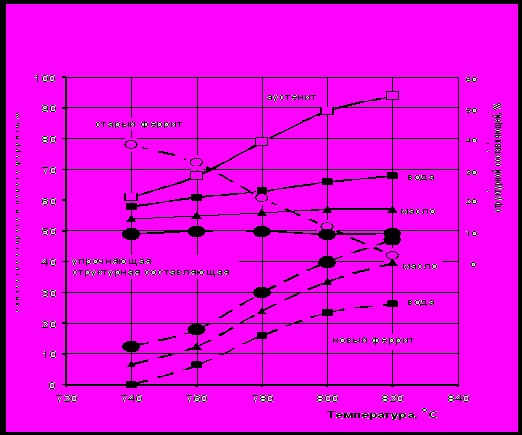


воздух
Рис. 3. Микроструктурная карта стали 10кп после охлаждения
в воде, масле и на воздухе
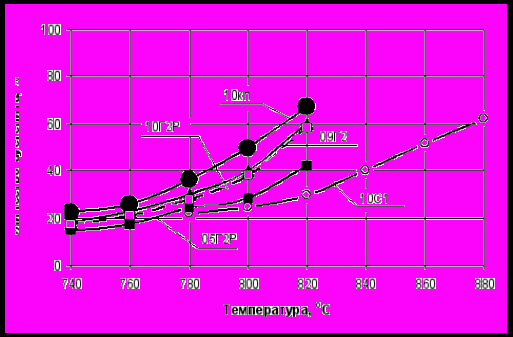
Рис. 4. Кинетика образования аустенита в исследованных сталях при нагреве в МКИ
В стали 05Г2Р эти параметры процесса аустенитизации значительно ниже, чем в стали 10Г2Р. Действие 1,2% Si сильнее, чем 1,6% Mn: процесс аустенитизации в стали 10С1 не только смещен (~60оС) в сторону более высоких температур, но и протекает замедленнее, чем в стали 09Г2.
Поэтому для формирования определенного количества аустенита стали 10кп, 09Г2, 10Г2Р должны нагреваться практически на одну температуру, тогда как стали 05Г2Р и 10С1 выше на 30-40 и 60оС, соответственно. В то же время, доминирующее влияние на количество упрочняющей структурной составляющей (мартенсита+бейнита) имеет устойчивость переохлажденного аустенита.
Количественные соотношения между структурными составляющими играют определяющую роль в формирующемся комплексе механических свойств ДФМС. Найдено, что при постоянной объемной доле мартенсита изменение свойств стали определяется не только количеством нового феррита, но и морфологией его образования. Зарождение и рост нового феррита по границам старых ферритных зерен приводит к наиболее заметному снижению предела текучести и повышению общего и равномерного удлинения.
Обобщение экспериментальных данных значительного круга малоуглеродистых низколегированных сталей показывает, что оптимальный комплекс свойств после ускоренного охлаждения из МКИ достигается при наличии 15-25% мартенсита, 20-30% эпитаксиального феррита и, соответственно, 45-65% исходного феррита.
В стали 10кп количество упрочняющей структурной составляющей при охлаждении в масле и на воздухе практически не зависит от температуры нагрева в двухфазную область (см. рис.3). В результате имеет место и стабильность свойств после нагрева до температур 740-800оС. Наилучший комплекс свойств (σв=510-530 МПа; σ0,2 /σв=0,52-0,56; δр-16-17%) обеспечивается после закалки в масле.
Легирование малоуглеродистой стали бором и марганцем приводит к существенной зависимости механических свойств от температуры нагрева. Так, после закалки в воде упрочняющей структурной составляющей в сталях 05Г2Р и 10Г2Р является мартенсит, количество которого монотонно возрастает с увеличением температуры нагрева. Соответственно, и прочностные характеристики обеих сталей возрастают с темпом упрочнения 7-8 МПа на один процент мартенсита. Значения общего и равномерного удлинения находятся на сравнительно невысоком уровне и монотонно снижаются с повышением температуры нагрева в двухфазную область.
Охлаждение в масле и на воздухе приводит к некоторому снижению темпа упрочнения, что связано с увеличением доли бейнита в упрочняющей структурной составляющей и появлением нового эпитаксиального феррита.
Установлены следующие режимы термической обработки, обеспечивающие оптимальный комплекс свойств. Для стали 05Г2Р – это нагрев в межкритический интервал до температур 740-780оС с охлаждением на воздухе (sв = 550-600 МПа; s0,2 =300-320 МПа; d = 31-33%; dр =15,5-17,5%; Т50 = 10-15оС; KCVmax = 2,2-2,4 МДж/м2). Близкий уровень механических свойств (sв = 570-610 МПа; s0,2 =320-350 МПа; d = 28-29%; dр =15-17%; Т50 = 15-25оС; KCVmax = 1,7-1,9 МДж/м2) формируется после нагрева до температур 740-780оС с охлаждением в масле .
У стали 10Г2Р нагрев в межкритический интервал до температур 780-820оС с последующим охлаждением на воздухе приводит к следующему комплексу механических характеристик: sв = 625-650 МПа; s0,2 =310-320 МПа; d = 28-31%; dр =14-15%; Т50 = 25-30оС; KCVmax = 1,8-1,9 МДж/м2.
В стали 05Г2С2 оптимальный комплекс свойств обеспечивается при наличие в структуре 15-25% мартенсита и 20-30% нового феррита: s0,2 = 380-400 МПа; sв = 720-750 МПа; dр =15-16%; Т50 = 40-45оС; KCVmax=2,4-2,6 МДж/м2.
Таким образом, изученные в работе стали имеют непосредственно после формирования двухфазной структуры высокую пластичность, оцениваемую по δ ≈30 %, и, главное равномерное удлинение δР ≈ 15 %, что особенно важно для изделий, получаемых холодной деформацией. Однако уровень ударной вязкости (KCV≈2,0 МДж/м2) и температура вязко-хрупкого перехода (Т50 ≈ 20оС) весьма низок, что указывает на необходимость проведения отпуска готовых изделий для их улучшения.
Рациональным легированием марганцем, бором, кремнием (даже при снижении до ≈ 0,05 % углерода) удается повысить на 30-40 % прочностные свойства фактически без ухудшения вязко – пластических характеристик.
В третьей главе рассматриваются строение и механические свойства сталей 20 и 09Г2С промышленной выплавки с феррито-мартенситной структурой, полученной ступенчатой закалкой.
Разработан новый способ создания ДФМС – ступенчатая закалка, включающая нагрев на температуру вблизи Ас3 для формирования неоднородного по содержанию углерода аустенита из исходной феррито-перлитной смеси, переохлаждение под Аr1 с оптимальной выдержкой, в течение которой происходит выделение необходимой порции избыточного феррита и обогащение углеродом нерастворившегося аустенита, трансформирующегося, при закалке в воду, в мартенсит и бейнит.
Светооптические исследования показали, что микроструктура обеих сталей после ступенчатой закалки по оптимальному режиму (Та = 860оС; Тп = 680оС с выдержкой 20 мин для стали 20 и 5 мин для стали 09Г2С) состоит из зерен избыточного феррита размером 20-50 мкм, находящихся в контакте между собой, и разомкнутых округлых “зёрен” размером 10-30 мкм, внутри которых сформировались игольчатые кристаллы мартенсита и бейнита. Площадь “зёрен” упрочняющей фазы составляла 40-45 %.
Металлографические исследования на тонких фольгах стали 20 позволили конкретизировать эти заключения. В зернах избыточного феррита с плавно изогнутыми границами имеется повышенная плотность однородно распределённых дислокаций, несколько большая. Вблизи игольчатых кристаллов α-фазы.
Обнаруживается мартенсит двух морфологических типов. Кристаллы мартенсита первого типа содержат столь высокую плотность дислокаций (~1·10″ см-2), что отдельные дислокации не разрушаются. Они имеют форму реек толщиной ~ 1 мкм, иногда собраны в пакеты. Такой тип мартенсита характерен для среднеуглеродистых сталей.
Широкие пластины мартенсита с пачками параллельных микродвойников толщиной ~ 100 Å, характерны для высокоуглеродистого мартенсита.
Рейки α-фазы с выделениями цементита в виде одинаково ориентированных частиц цементита интерпретированы как нижний бейнит. Ширина таких реек с несколько изогнутыми границами достигает ~ 3 мкм.
Итак, данные электронной микроскопии показывают, что в низкоуглеродистой стали после ступенчатой закалки наряду с ферритом присутствует спектр сдвиговых продуктов превращения, формирующихся поочерёдно по мере понижения температуры во всё более богатых по углероду областях аустенита.
Особенности такой гетерофазной структуры показали и результаты рентгеноструктурного анализа, проведенного с использованием дифрактометра Bruker D8 Advance.
Для дифрактограммы образца стали 20 после ступенчатой закалки (Та = 860оС + Тп = 680оС + охлаждение в воде) характерно:
- отсутствие физического уширения линии 222 (следовательно, отсутствие в металле микроискажений или точнее, их глубокая компенсационная релаксация);
- линия 110 состоит из острого высокого максимума, имеющего значительное размытие в сторону меньших углов Вульфа-Брегга, что связывается с формированием мартенсита различной тетрагональности.
Основываясь на данных электронной микроскопии, это можно интерпретировать следующим образом. Отражение 110 является наложением линий 110 феррита и мартенсита, а размытие интерференционного максимума в сторону меньших углов Вульфа-Брегга связано с отражением от плоскостей (101) и (011) тетрагонального мартенсита, имеющего широкий диапазон отношений периодов с/а. Площадь линий 101м – 011м мартенсита составляет ~ 25 % площади линии 110, хотя на дифрактограммах мартенсита интегральная интенсивность линий 101м + 011м больше интегральной интенсивности линии 011м. Ясно, что это связано с относительно небольшим количеством тетрагонального мартенсита в исследованном образце.
Расчет периодов а по линии 110 и с по минимальному и максимальному углу Вульфа-Брегга линии 101м– 011м дал следующие значения: а = 2,868 Å, с = 2,918 – 3,003 Å, с/а = 1,02-1,05.
Согласно найденным значениям с/а и уравнению с/а = 1 + 0,0467р, содержание углерода в мартенсите (соответственно, в аустените, из которого он сформировался) составляет р = 0,5-1,2 мас. %. Это показывает, насколько глубоко происходит обогащение микрообъемов аустенита по углероду и разброс по его содержанию в процессе ступенчатой закалки.
Таким образом, теоретически обосновано и экспериментально подтверждено, что уникальный комплекс механических свойств стали 20 (σВ = 669 МПа, σ0,2 = 400 МПа, δобщ = 22 %, δР = 14 %) и стали 09Г2С (σВ = 760 МПа, σ0,2 = 460 МПа, δобщ = 21%, δР = 12 %) после ступенчатой закалки связан с формированием особого структурного состояния.
Определённое количество упрочняющей фазы (мартенсит + бейнит) с заданной твердостью (плотностью дислокаций, содержанием углерода) обуславливает повышенный уровень прочностных характеристик. Эти продукты сдвиговых превращений образуются порционно по мере снижения температуры из неоднородного по углероду аустенита в окружении ранее сформировавшегося феррита. Мягкая “оболочка” феррита компенсирует генерированием напряжений противоположного знака ансамблем образующихся в нем дислокаций напряжения, порождаемые при возникновении бейнита и мартенсита. Сталь с уравновешенными внутренними напряжениями (их суммарная величина близка к нулю) обладает удовлетворительной пластичностью, несмотря на высокую плотность дефектов кристаллического строения.
Благодаря применению ступенчатой закалки (формированию феррито-мартенситной структуры) удается поднять прочностные свойства низкоуглеродистых сталей в ~ 1,5 раза по сравнению с нормализованным состоянием, сохранив характеристики пластичности на уровне, удовлетворяющем требованиям ГОСТа на горячедеформируемую продукцию. Это позволяет рекомендовать ступенчатую закалку как окончательную термообработку при производстве листа, профилей, труб и других изделий, получаемых горячей прокаткой.
В четвертой главе описываются эксперименты по закалочному и деформационному старению гетерофазных сталей и их трактовка.
Низкотемпературный отпуск, применяемый непосредственно после закалки из МКИ, используется для улучшения комплекса механических свойств ДФМС. Для всех исследованных сталей характерна экстремальная зависимость условного предела текучести σ0,2 и общего удлинения δ от температуры отпуска. Значение временного сопротивления σВ слабо изменяется при температурах более низких, чем температура, соответствующая максимальному значению σ0,2, но затем заметно снижается.
Анализ микроструктурных особенностей отпущенных ДФМС наряду с данными амплитудной и температурной зависимостей внутреннего трения позволяют считать, что экстремальное изменение предела текучести с повышением температуры старения обусловлено протеканием ряда конкурирующих процессов: образованием сегрегаций атомов углерода на дислокациях в феррите, сопровождающимся возвратом площадки текучести; распадом упрочняющей фазы; релаксацией остаточных напряжений, возникающих из-за несоответствия объемов аустенита и мартенсита; образованием карбидных частиц на дислокациях в феррите и их укрупнением при повышенных температурах отпуска (“перестаривание” феррита). Первый и третий из указанных процессов преобладают при низких температурах отпуска, а второй и четвертый - при повышенных. Это и предопределяет экстремальную зависимость предела текучести от температуры отпуска.
Применение ДФМС в различных отраслях промышленности предъявляет повышенные требования к сопротивлению этих сталей хрупкому и вязкому разрушению в готовой конструкции. Изучение влияния деформационного старения на характеристики разрушения ДФМС проводилось на примере сталей 05Г2Р и 05Г2С2.
Установлено, что с повышением степени холодной деформации происходит закономерное возрастание температуры вязко-хрупкого перехода Т50 и снижение максимальной ударной вязкости при полностью вязком изломе (например, деформация растяжением на 10% приводит к возрастанию Т50 на 35-40оС и почти двукратному снижению KCVmax). Такое возрастание Т50 связано, по всей видимости, с упрочнением феррита, в котором локализуется практически вся деформация.
Проведение последеформационного отпуска заметно снижает температуру вязко-хрупкого перехода и значительно повышает величину KCVmax . В частности, сталь 05Г2Р после деформации растяжением на 10% и отпуска 200оС, 1 ч имеет практически такую же величину Т50, как и в исходном состоянии после охлаждения в масле от 760оС. Наблюдающееся повышение KCVmax и Т50 обусловлены влиянием двух противоположно действующих процессов: разупрочнения мартенсита при отпуске и снижения пересыщения твердого раствора феррита за счет образования сегрегаций примесных атомов на дислокациях в результате протекания деформационного старения. Превалирующее влияние первого фактора объясняет, по-видимому, экспериментально наблюдаемое повышение сопротивления хрупкому и вязкому разрушению при отпуске предварительно деформированной ДФМС.
Проведенные микрофрактографические исследование ударных образцов, разрушенных при различных температурах, подтверждают сделанные выше выводы
Низкотемпературный отпуск сталей с гетерофазной структурой позволяет повысить значение предела текучести на 100-140 МПа, при этом значение отношения σ0,2/σВ, равное 0,50-0,55 в исходном состоянии, повышается до величины 0,65-0,75. Температура вязко-хрупкого перехода Т50 снижается на 40-50оС, ударная вязкость KCVmax возрастает по сравнению с исходным состоянием на 20-25%. Такое изменение свойств делает возможным применение ДФМС в качестве конструкционных материалов непосредственно после отпуска.
Процесс деформационного старения ДФМС обычно совмещается с технологическими операциями нанесения или сушки антикоррозионных лакокрасочных покрытий. Установлено, что пластическая деформация растяжением оказывает немонотонное влияние на склонность этих сталей к старению. Наиболее благоприятные условия для старения возникают после деформации 4-6%, вероятно благодаря более коротким путем диффузии для атомов внедрения при повышении плотности дислокаций равномерно по всему объему ферритного зерна. Образование ячеистой дислокационной структуры, при увеличение степени деформации до 10%, приводит к замедлению процесса старения.
На примере стали 05Г2С2 с использованием ядерной гамма-резонансной спектроскопии и удельного электросопротивления показано, что во время деформационного старения при температурах сушки антикоррозионных лакокрасочных покрытий происходит локальное перераспределение атомов легирующих элементов замещения. После закалки из межкритического интервала температур наблюдается ближний порядок типа ближнего упорядочения в расположение атомов легирующих элементов замещения. Пластическая деформация понижает степень ближнего порядка, а последующее старение вновь его восстанавливает.
С учетом установленных закономерностей деформационного старения ДФМС построены диаграммы зависимости упрочнения исследованных сталей от степени предварительной деформации. Диаграммы позволяют оценить прочность готовых изделий из сталей этого типа после низкотемпературного отпуска, соответствующего нанесению и сушке антикоррозионных лакокрасочных покрытий. Диаграммы свидетельствуют, что в готовых конструкциях ДФМС имеет очень высокий комплекс прочностных и пластических характеристик, не достигаемый на сталях того же состава с феррито-перлитной структурой. Так, предел текучести в стали 10кп с феррито-перлитной структурой может достигать 550-590 МПа при сохранении общего удлинения на уровне 24-20%. В гетерофазном состоянии у стали 05Г2Р при величине общего удлинения δ =20% предел текучести находится на уровне 650 МПа, а у стали 05Г2С2 достигается значение σ0,2 = 780 МПа при той же величине общего удлинения.
Применение ДФМС требует обеспечения надежности в процессе эксплуатации изготовленных из них деталей и конструкций. Многие типы разрушений при эксплуатации образуются в результате усталостного нагружения. В связи с этим, научный и практический интерес представляют данные по влиянию скорости охлаждения из межкритического интервала температур и последующего деформационного старения на сопротивление ДФМС усталостному разрушению.
Усталостное испытание проводили по схеме чистого изгиба при кручении на машине типа УВМ согласно ГОСТ 25.502.79.
Установлено, что стали с феррито-мартенситной (бейнитной) структурой обладает более высокими значениями предела выносливости, чем стали с феррито- перлитной структурой одного и того же химического состава. Это подтверждено результатами микрофрактографического исследования усталостных образцов, разрушенных при различных амплитудах цикла. В то же время относительное повышение предела выносливости существенно ниже, чем статических характеристик прочности. Деформационное старение, сочетающееся с некоторыми технологическими операциями, не изменяет значение предела выносливости в случае феррито-перлитной структуры и очень незначительно (2-3 %) увеличивает эту характеристику в ДФМС, что связывается с циклическим разупрочнением предварительно деформированных и состаренных образцов.