Указания по применению природных каменных материалов при строительстве дорожных искусственных сооружений
Вид материала | Документы |
- Правила безопасности при строительстве подземных сооружений пб 03-428-02, 4281.3kb.
- Правила безопасности при строительстве подземных сооружений пб 03-428-02, 4437.54kb.
- Руководство по применению микротоннелепроходческих комплексов и технологий микротоннелирования, 820.39kb.
- Требования к выдаче свидетельств о допуске по виду работ «Возведение сооружений в морских, 49.23kb.
- Документ содержит указания по конструированию и расчету нежестких дорожных одежд автомобильных, 3047.06kb.
- Методика и техника для контроля прочности бетонов и других искусственных каменных материалов, 164.95kb.
- Пособие по проектированию каменных и армокаменных конструкций (к #M12291 9056429СНип, 13145.52kb.
- Приказ от 8 июня 1999 г. N 410 о совершенствовании нормативно-правового регулирования, 666.38kb.
- Приказ от 8 июня 1999 г. N 410 о совершенствовании нормативно-правового регулирования, 937.49kb.
- Геосинтетические и геопластиковые материалы в дорожном строительстве, 1315.78kb.
При помощи клиньев и взрывным способом монолиты разделывают путем предварительного бурения ряда небольших шпуров глубиной 8-10 см или большей глубины (для крупных монолитов) на расстоянии 20-25 см один от другого в зависимости от колкости породы. В подготовленные шпуры вставляют две щечки, а между ними клинья, которые последовательно забивают молотком.
Для развалки монолита взрывным способом (слабыми взрывами) шпуры делают глубже (до 50 см), но в меньшем количестве, а для сравнительно небольших монолитов может быть только один шпур, который бурят перфораторами. Разметка монолитов для высверливания шпуров - важный процесс при их разделке, так как от нее зависит правильность кусков и количество отходов.
Раскалывание крупных монолитов (более 5 м



Для дальнейшей разделки и обработки полученный каменный материал транспортируют на специально предназначенные для этой цели площадки или к месту погрузки. Транспортирование осуществляется при помощи лотков, бремсбергов, канатных дорог, автомобилей и т.д.
Из скальных пород изготовляют щебень, бутовый камень, шашку для мощения, шашку пакеляжную, бортовой камень, брусчатку, блоки, каменную муку.
Щебень представляет собой смесь угловатых обломков размером 5-70 мм, полученных в результате дробления скальных горных пород, и применяется для получения щебеночных конструктивных слоев, асфальто-, пласт- и цементобетонов.
Природный щебень образуется в результате физико-механического выветривания скальных горных пород и отложений на месте своего образования, состоит из обломков горных пород в той или иной стадии выветривания и содержит разное количество землистых примесей.
Технология переработки горной массы на щебень и погрузочно-разгрузочные работы могут быть полностью механизированы, а отдельные операции автоматизированы. Щебень изготавливают дроблением горных пород в камнедробилках. Ведущим показателем дробления является показатель степени измельчения

где Д- максимальный размер куска породы до дробления, мм; d- максимальный размер зерен породы после дробления, мм.
Процесс дробления для получения щебня необходимых размеров обычно осуществляют в несколько стадий. В этом случае общую степень измельчения определяют как произведение степеней измельчения. Различают: крупное дробление - куски породы более 250, среднее - 250-40 и мелкое - меньше 40 мм.
В зависимости от признаков и свойств породы применяют щековые, конусные, молотковые (ударного действия) и другие дробилки. Процесс дробления осуществляют в две, три, а иногда и четыре стадии. Щековые дробилки используют преимущественно’ для крупного и среднего дробления при степени измельчения 5-6. Конусные дробилки пригоды для крупного, среднего и мелкого дробления горных пород разной прочности. Степень измельчения на них 3-5. Дробить вязкие, мокрые и глинистые породы на этих дробилках не следует. Производительность конусных дробилок значительно больше щековых.
Молотковые камнедробилки выпускают ударного действия (молотки-била подвешены шарнирно) и роторные, в которых била закреплены жестко. Эти камнедробилки пригодны для дробления неабразивных пород прочностью до 120-150 МПа (например, известняков), для крупного, среднего и мелкого измельчения. Значительное увеличение скорости вращения повышает образование каменной мелочи.
В необходимых случаях щебень для приготовления бетонов подвергают мойке. Промывка не только увеличивает производительность грохота, но и значительно улучшает качество щебня.
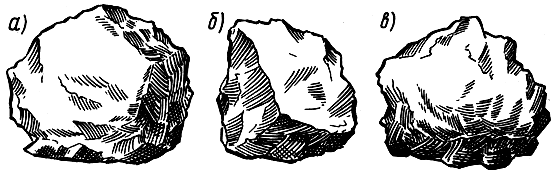
Рис.10 Форма зерен щебня
а- кубиковидная;
б- клиновидная;
в- угловатая.
В процессе дробления получаются зерна щебня разной геометрической формы (рис.10, 11), с микротрещиноватостью (при дроблении прочных, крупных пород) или со смятой поверхностью (раздробленные зерна), а также некоторое количество смятой мелочи - отходов. Содержание зерен по крупности и смятой мелочи зависит не только от свойств исходной горной породы, но и от принятой технологии дробления. Для получения щебня повышенного качества, однородного по прочности и улучшенной формы, применяют обогащение - избирательное дробление, обогащение по прочности, по форме зерен и др.

Рис.11. Форма зерен щебня
а- плитовидная;
б- лещадная;
е- пальцеобразная.
При избирательном дроблении в дробилках-грануляторах улучшение формы зерен происходит вследствие разрушения слабых зёрен и примесей, что дает возможность удалить их при последующем грохочении.
При наличии равнопрочного щебня в необходимых случаях прибегают к разделению по прочности предварительно отгрохоченного щебня в классификаторах.
Значительно улучшить качество щебня можно путем повышения активности поверхности зерен.
Обработка зерен поверхностно-активными веществами повышает сцепление их с вяжущими веществами или придает зернам щебня водоотталкивающие свойства.
Щебень по крупности зерен для дорожного строительства делят на сорта (щебень размером 70-150 мм называют гигантским):
Крупный……………… 70-40 мм;
Средний……………… 40-20/25 мм;
Мелкий……………….. 20/15-10/15 мм;
Клинец………………... 10/15-5 мм;
Высевки (или искусственный дробленый песок)….. <5 мм.
Качество щебня, т. е. степень соответствия показателей его признаков и свойств проектируемому назначению, определяют в карьере (на месте его производства) и на месте его потребления (на строительном объекте) путем изучения внешних признаков и испытания отобранных проб. При этом определяют петрографические признаки и однородность горной породы, из которой получен щебень:
- крупность, зерновой состав, форму зерен (количество лещадных и игольчатых зерен);
- шероховатость поверхности; количество и качество примесей (глинистых, органических и др.);
- количество смятых (раздробленных) зерен;
- физические свойства (плотность и объемную массу, пустотность, влажность, водопоглощение, морозостойкость);
- механические свойства (прочность при расколе, растяжении, ударе, раздавливании в цилиндре, износ в барабане).
По прочности при износе (истираемости) в полочном барабане щебень подразделяют на четыре марки (табл. 6).
Таблица 6
| | |
| Износ (потеря массы при испытании), % | |
Марка щебня | Известняки, доломиты | Изверженные, метаморфические и другие осадочные породы |
И-1 | <30 | <25 |
И-II | 31-40 | 26-35 |
И-III | 41-50 | 36-45 |
И-IV | 51-60 | 46-55 |
Определение качества щебня по прочности при сжатии исходной горной породы является весьма приближенным, так как показатель прочности зависит не только от качества исходной горной породы, но и от размеров, формы и других признаков щебня. Поэтому в последнее время прочность щебня определяют косвенно по показателю дробимости.
Марки щебня из осадочных, пород по дробимости при сжатии (раздавливании) в цилиндре даны в табл. 7, а из магматических и метаморфических пород в табл. 8.
Таблица 7
| | |
Марка щебня | Дробимость щебня (потеря массы при испытании), % | |
| сухого | водонасыщенного |
1200 | ![]() | ![]() |
1000 | 7-8 | 10-11 |
800 | 9-10 | 12-14 |
600 | 11-14 | 15-18 |
400 | 15-24 | 19-28 |
300 | 25-28 | 29-38 |
200 | 29-35 | 39-54 |
Прочность щебня можно также определить испытанием на раскол на гидравлическом прессе между двумя взаимно направленными рифлями или конусами.
Таблица 8
| | |
| Дробимость щебня (потеря массы при испытании), % | |
Марка щебня | из изверженных интрузивных и метаморфических пород | из изверженных эффузивных горных пород |
1200 | ![]() | ![]() |
1000 | 17-20 | 10-11 |
800 | 21-25 | 12-14 |
600 | 26-34 | |
Бутовый камень(бут) получают при разработке карьеров посредством отделения кусков породы взрывом или применения ударных инструментов (перфораторы, кирки, ломы и др.). При разработке песчаников, известняков и других пород пластового залегания, а также трещиноватых, крупные отдельности отделяют экскаваторами с последующей развалкой кусков до требуемых размеров камнекольными инструментами.
Бутовый камень (рис.12) имеет неправильную форму и различные размеры, но не более 50 см по наибольшему измерению.
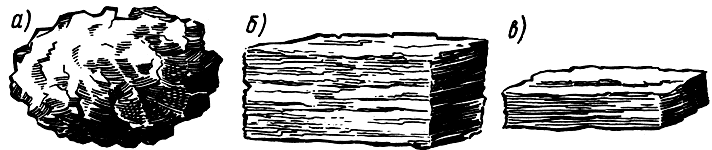
Рис.12. Бутовый камень
а- рваный;
б- поостелистый;
в- лешадочный.
По форме бывает бут постелистый, плитняковый и пиленый (1-й сорт), рваный (2-й сорт).
Наиболее удобны для выработки бутового камня плитовидные и слоистые породы. Бутовый камень употребляют для кладки фундаментов, мостовых устоев, укрепления откосов насыпей и берегов рек, кладки подпорных стен. Кроме того, бут может идти для дальнейшего раскола на шашку и дробления на щебень. Породу для получения бутового камня выбирают с учетом его назначения. Так, для кладки лучше брать поостелистый или плитняковый бут, который получают из слоистых пород. Свойства породы по прочности при сжатии, влагоемкости и погодоустойчивости должны соответствовать конструкции элементов сооружения. Например, для бутобетона должен быть рваный бут из однородных без трещин морозостойких пород прочностью не ниже 35 МПа.
Объемная масса бутового камня, сложенного в штабеля, в среднем равна 1400, поостелистого - 1700 кг/м

Таблица 9
| | | |
Размеры шашки | Высокая | Средняя | Низкая |
Высота, см: | | | |
средняя | 18 | 16 | 14 |
предельная | 16 и 20 | 14 и 18 | 12 и 16 |
Размеры по лицу, см | 10 и 20 | 10 и 18 | 10 и 15 |
Площадь лица, см ![]() | 100 | 100 | 100 |
Площадь постели, см ![]() | 60 | 50 | 50 |
Шашка каменная для мощения(рис.13) - грубоколотые камни неправильной формы, приближающейся к призме или усеченной пирамиде. Лицевая поверхность (верхняя сторона) должна быть полигонального очертания, например четырехугольник или многоугольник, постель (нижняя сторона) - тупой, приближаться к параллели с лицом и вписываться в очертания лицевой стороны. Боковые грани не должны иметь резких выступов. Такого вида шашку применяют для обыкновенного мощения. Если шашка правильной формы имеет плоское лицо с параллельными длинными сторонами, она допускается для рядового мощения. По размерам шашка должна удовлетворять требованиям, приведенным в табл. 9.
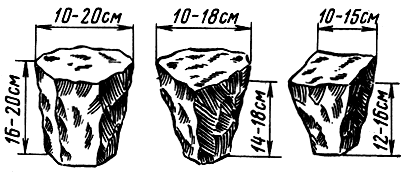
Рис.13. Шашка для мощения
Брусчатка- колотые и тесаные бруски камня, приближающиеся по форме к параллелепипеду, имеющие по лицу фигуру прямоугольника (рис.14). Верхняя и нижняя плоскости (лицо и постель) брусчатки должны быть параллельны, боковые грани суживаться книзу так, чтобы размер скола у подошвы низкой брусчатки был с каждой стороны не более 5 мм, а у средней и высокой - не более 10 мм. По размерам брусчатку делят на три сорта.
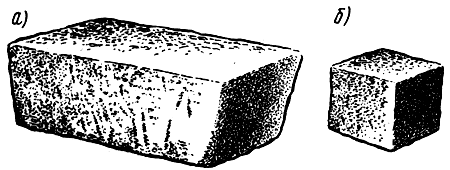
Рис.14. Брусчатка и шашка для мозаиковой мостовой
а- брусчатка;
б- шашка.
Облицовочные плиты,а также блоки изготовляют из однородных, прочных, погодоустойчивых горных пород, обладающих хорошей обрабатываемостью, а в необходимых случаях хорошей полируемостью и рисунком. Процесс изготовления имеет следующие операции: развалку монолита, грубую околку, получистую и чистую теску.
Развалку монолитов производят клиньями или распиловкой. Отколотые от монолитов болванки требуемых размеров подвергают грубой теске при помощи долот различной формы с наконечниками из нехрупкой стали. Для тески углов пользуются широким долотом - скарпелью, неровности обивают остроконечным долотом, которое называется спицей. Иногда для грубой тески употребляют тесовки массой 2-4 кг. Полугрубую теску производят теми же инструментами, что и грубую, но, кроме того, применяют молоток крупного номера с зубчатой насадкой (бучарда). Для чистой тески лицевых поверхностей бордюрных и облицовочных плит используют бучарду со средней и мелкой насечкой.
Для механической тески применяют механические молотки, которые в зависимости от назначения производят разное количество ударов в минуту (1600-3800) и имеют разные рабочие части (долота). Кроме молотков, применяют пневматические спицы и бучарды.
Бортовые камни- параллелепипедальные бруски длиной в среднем 75 см в поперечном сечении с наклонной или вертикальной лицевой гранью. Бортовые камни могут быть прямые и лекальные; верхняя их часть, выступающая над покрытием, обтесана чисто, а нижняя - грубо. По размерам бортовые камни бывают: низкие - 30 и высокие- 40 см с шириной поверху 10, 15 и 25 см (рис.15). Бортовые камни применяют для устройства дорожных одежд в городских условиях. Они служат для отделения проезжей части дороги от тротуара, обочин и др.
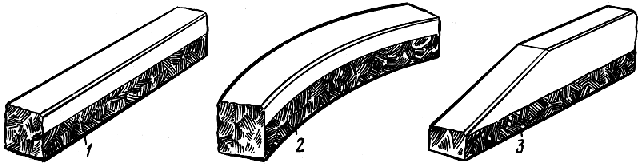
Рис.15. Бортовой камень
1- прямой;
2- лекальный;
3- для съездов.
Камни для облицовкимогут быть плитообразные (толщиной 15-25 см) и утолщенные с пирамидальной хвостовой частью (толщина не менее 30 см). Камни ледорезныедолжны иметь точечную или бороздчатую фактуру. Форму и размеры устанавливают по требованиям проекта ледореза.
Плиты парапетные и карнизныедля мостов и набережных изготовляют следующих размеров: парапетные - длиной 100-200, шириной не менее 90 и толщиной 20-30 см; карнизные - длиной 100-200, шириной не менее 50 и толщиной 20-30 см.
Плиты тротуарныеизготовляют из слоистых и сланцеватых горных пород. Они должны иметь форму прямоугольной или квадратной плиты размером от 20 до 80 см с относительно ровной поверхностью лица и постели, толщиной не менее 4-5 и не более 12-15 см.
Блоки и плитыдля кладки цоколей и сводов, для облицовки набережных, мостовых устоев и быков подвергают тщательной обработке обычно с лицевой стороны. В блоках различают переднюю сторону - лицо, нижнюю и верхнюю поверхности - постели, боковые поверхности - заусенные плоскости или заусенки, заднюю поверхность (если она не отесана) - хвост.
Характер обработки лицевой поверхности носит название фактуры, которая может быть абразивной и ударной, Различают следующие абразивные фактуры:
- пиленую - гладкую с тонкими штрихами;
- шлифованную - тонкошероховатую, шероховатую;
- лощеную - гладкую с бархатистым блеском, зеркальную - гладкую с зеркальным блеском. Ударные фактуры бывают:
- скала - со сколом камня, образующим бугры и гребни без следов инструмента;
- бугристая - с равномерным чередованием бугров и впадин со следами инструмента;
- рифленая - с непрерывными параллельными бороздками;
- бороздчатая - с параллельными прерывистыми буграми;
- точечная - грубо-шероховатая.
Для нанесения рисунков и надписей на полированную лицевую поверхность укрепляют металлический шаблон с вырезанным рисунком или надписью, при этом незащищенные шаблоном места вырабатывают струей кварцевого песка с помощью пескоструйного аппарата. Чтобы облицовочные плиты и блоки имели ровную и полированную поверхность, их подвергают шлифовке и полировке при помощи шлифовальных станков. Шлифовка камня производится чугунным бруском или диском с подсыпкой стального или корундового порошка.
Абразивы или материалы, служащие для резки, шлифовки и полировки, могут быть природные и искусственные. Природные абразивы - кварц, корунд, наждак, алмаз, искусственные - карборунд, алунд, стальмасса. Кварц применяют в виде чистого кварцевого песка крупностью до 1 мм. Корунд - минерал, состоящий в основном из кристаллической окиси алюминия. Наждак содержит 20-50% зерен корунда в тесной связи с магнетитом. Карборунд - сплав углерода и кремния при 1900-2200 °С, состоит из карбида кремния, по твердости несколько выше корунда. Алунд (искусственный корунд) по составу аналогичен корунду и получается электроплавкой, поэтому иногда носит название электрокорунда. Стальмассу получают из каленой углеродистой стали и чугуна с последующим дроблением их на станках.
Для ускорения шлифовки применяют шлифовальные круги и бруски. Обычно работы по шлифовке и полировке состоят из ряда последовательных операций: обдира (грубая шлифовка), шлифовки, лощения (тонкая шлифовка), мастичения и полировки.
Обдир ведут мокрым способом при помощи тонкого слоя шлама и отходов стальмассы. В процессе грубой шлифовки поверхность камня смазывают свежей стальмассой или ее отходами, шлифуют зерновым абразивом (корундом или карборундом) с периодическим увлажнением. Окончательная обработка ведется пемзой или карборундовым кругом (бруском). Тонкую шлифовку производят тонким зерновым абразивом. После лощения перед полировкой поверхность камня мастичат путем закрытия мелких дефектов шеллачной мастикой горячим способом. Полировка достигается путем накатки тщательно промытой поверхности полирующими порошками при помощи войлочных полировальных дисков. В качестве полирующих порошков применяют окись олова, окись железа, свинцовые опилки, азотистокислое олово и др.
30>5>