Повышение механических свойств рулонного проката из низколегированных трубных сталей путем управления процессами структурообразования при термомеханической обработке
Вид материала | Автореферат |
- Улучшения структуры и повышения механических свойств стальных отливок является внепечное, 179.71kb.
- Примерная программа дисциплины теория термической обработки, 165.44kb.
- Carboweld 625 Стандарты, 41.02kb.
- Бернштейновские чтения по термомеханической обработке металлических материалов, 2303.61kb.
- Повышение эффективности системы менеджмента качества применением карт бизнес-процессов, 241.65kb.
- Примерная программа дисциплины механические свойства металлов, 122.33kb.
- Влияние дополнительной термообработки на структуру и механические свойства феррито-бейнитных, 482.48kb.
- План-конспект урока по теме "Классификация и термическая обработка сталей", 100.32kb.
- Бернштейновские чтения по термомеханической обработке металлических материалов, 1294.86kb.
- Методические указания по выполнению курсовой работы, 848.06kb.
На правах рукописи
ФИЛАТОВ НИКОЛАЙ ВЛАДИМИРОВИЧ
ПОВЫШЕНИЕ МЕХАНИЧЕСКИХ СВОЙСТВ РУЛОННОГО ПРОКАТА ИЗ НИЗКОЛЕГИРОВАННЫХ ТРУБНЫХ СТАЛЕЙ ПУТЕМ УПРАВЛЕНИЯ ПРОЦЕССАМИ СТРУКТУРООБРАЗОВАНИЯ ПРИ ТЕРМОМЕХАНИЧЕСКОЙ ОБРАБОТКЕ
Специальность 05.16.01 - «Металловедение и термическая обработка металлов»
АВТОРЕФЕРАТ
диссертации на соискание ученой степени кандидата
технических наук
Москва - 2009
Работа выполнена
во ФГУП «Центральный научно-исследовательский институт
черной металлургии им. И.П. Бардина»
Научный руководитель - кандидат технических наук
НАСТИЧ Сергей Юрьевич
Официальные оппоненты:
- доктор технических наук, профессор
ОДЕССКИЙ П.Д.
- кандидат технических наук
ЛИВАНОВА О.В.
Ведущее предприятие – ОАО «Выксунский металлургический завод»
Защита состоится 23 декабря 2009г. в 15 часов на заседании диссертационного совета Д 217.035.01 при ФГУП «ЦНИИчермет им. И.П. Бардина».
Отзывы в двух экземплярах, заверенные печатью, просьба направлять по адресу: 105005, Москва, 2-я Бауманская ул., д. 9/23.
С диссертацией можно ознакомиться в технической библиотеке и на сайте ФГУП «ЦНИИчермет им. И.П. Бардина»: www.chermet@chermet.net.
Автореферат разослан 22 ноября 2009г.
Ученый секретарь диссертационного
совета Д 217.035.01,
доктор технических наук Н.М. Александрова
ОБЩАЯ ХАРАКТЕРИСТИКА РАБОТЫ
Актуальность темы. Термомеханическая прокатка является прогрессивным способом производства проката из трубных сталей, позволяющим обеспечивать повышенный комплекс прочностных свойств в сочетании с необходимым уровнем хладостойкости на сталях с экономным уровнем легирования, что обеспечивает хорошую свариваемость. В практике строительства магистральных газо- и нефтепроводов категории прочности Х65-Х80 при толщине стенки трубы до 16 мм наряду с прямошовными используются также спиральношовные трубы, отличающиеся меньшей себестоимостью в производстве в связи в использованием высокопроизводительных процессов при изготовлении рулонного проката на непрерывных широкополосных станах горячей прокатки (НШС) и при формовке труб. Использование проката с гарантией уровня прочностных свойств и характеристик при испытании падающим грузом (ИПГ) по всей длине полосы повышает конкурентоспособность таких труб благодаря отсутствию операции термической обработки.
Отечественный опыт производства рулонного проката класса прочности К56-К60 (Х70) с гарантией уровня свойств ограничен толщиной 12 мм, а спиральношовные трубы с толщиной стенки 12-16 мм из рулонного проката производят методом объемной термической обработки. ЧерМК ОАО «Северсталь» имеет высокопроизводительный НШС 2000, на котором принципиально возможно осуществление контролируемой прокатки.
Актуальность выполненной работы обусловлена ее направленностью на разработку технологии термомеханической обработки рулонного проката, позволяющей обеспечить в полосе толщиной 14-16 мм комплекс свойств, соответствующий классу прочности К60 (Х70) в сочетании с улучшенными показателями хладостойкости (в том числе при ИПГ) и свариваемости, которые необходимы для реализации проектов современных магистральных трубопроводов большого диаметра.
Целью диссертационной работы является установление влияния основных параметров технологии производства рулонного проката из микролегированных трубных сталей типа Х70 в условиях НШС на структурообразование сталей, в том числе выделение дисперсных частиц карбонитридов, при смотке и охлаждении рулонов, определение на этой базе условий достижения требуемого уровня свойств и их равномерности по длине полосы, технологической схемы производства хладостойкого проката толщиной 14-16 мм, а также опробование и освоение технологии применительно к оборудованию стана 2000 ЧерМК ОАО «Северсталь».
Для достижения поставленной цели было необходимо решить следующие задачи:
- изучить путем лабораторного эксперимента на дилатометре особенности кинетики превращения горячедеформированного аустенита сталей типа Х70 с различными добавками (Mo, Ni, Cu, Cr) и повышенным содержанием Nb (до 0,08%) и выявить условия формирования различного типа микроструктур в стали;
- исследовать влияние основного параметра охлаждения и смотки полосы – температуры смотки (Тсм), на формирование микроструктуры стали и соотношение долей структурных составляющих после контролируемой прокатки;
- выявить особенности выделения дисперсных частиц карбонитридов (Nb, V)(C, N) при различных Тсм, в том числе для разных участков рулона;
- установить зависимость характеристик микроструктуры и механических свойств рулонного проката от параметров прокатки и смотки полосы; определить возможности обеспечения высокой хладостойкости при ИПГ стали при малых значениях кратности подката с учетом особенностей оборудования НШС;
- оценить влияние композиции стали типа Х70 (0,06%C-1,5%Mn-Nb-V-(Mo; Ni; Cr+Ni; Ni+Cu)) и режима смотки на микроструктуру и тонкую структуру стали;
- используя результаты выполненных исследований разработать состав стали и технологические режимы изготовления рулонного проката толщиной 14-16 мм класса прочности К60 (Х70) с гарантией уровня механических свойств и хладостойкости при ИПГ и осуществить опробование промышленного производства на стане 2000 ЧерМК ОАО «Северсталь».
Научная новизна.
1. Установлены закономерности изменения типа, морфологии и доли структурных составляющих в низколегированной трубной стали с добавками (Mo, Ni, Cr+Ni, Cu+Ni, Ni+Mo) при понижении температуры смотки в интервале от ≈ 600 оС до ≈ 500 оС, заключающиеся в переходе от традиционной ферритно-перлитной микроструктуры к ферритно-бейнитной микроструктуре, основными составляющими которой являются квази-полигональный феррит и игольчатый феррит, позволяющие обеспечить требуемое сочетание прочностных и вязко-пластических свойств проката.
2. Выявлено, что максимальное количество частиц Nb(C,N) размером 3-8 нм, обеспечивающих дисперсионное упрочнение проката, наблюдается для стали, микролегированной Nb+V, при Тсм ≈ 550-570 оС и для стали с добавкой только Nb при Тсм ≈ 580-610 оС.
3. Сформулировано условие равномерности механических свойств проката по длине полосы (с учетом неравномерного охлаждения рулона), состоящее в необходимости формирования для всех участков рулона: (1) мелкозернистой ферритно-бейнитной структуры и (2) выделений карбонитридных фаз размером до 10 нм без последующего огрубления частиц при охлаждении рулона; практически это реализуется путем смотки всех участков полосы при Тсм несколько ниже 580 оС.
4. Установлено влияние химического состава стали и параметров чистовой стадии контролируемой прокатки на хладостойкость рулонного проката при ИПГ, описываемое представленным параметром ΔTSv=Ткп-Ar3расч, который позволяет оценить степень сохранения проработанной структуры нерекристаллизующегося аустенита перед фазовым превращением; хладостойкость рулонного проката толщиной 14-16 мм обеспечивается при выполнении соотношения ΔTSv=Ткп-Ar3расч < 50 оС, что при ограничениях по толщине подката и температуре конца прокатки выполняется путем оптимизации химического состава стали.
Практическая ценность и реализация работы в промышленности.
1. На основании установленных закономерностей структурообразования и обеспечения свойств трубных сталей разработана промышленная технология контролируемой прокатки, ускоренного охлаждения и смотки по регламентированным режимам рулонного проката толщиной 14-16 мм для электросварных спиральношовных труб класса прочности К60(Х70), исключающая необходимость последующей термической обработки труб.
2. Разработан химический состав и научно-техническая документация на производство проката рулонных сталей класса прочности К60(Х70); разработанные марки стали и технологии с положительным результатом прошли промышленное опробование и внедрены на стане 2000 ЧерМК ОАО «Северсталь».
3. Изготовлены промышленные партии рулонного проката класса прочности К56 и К60 толщиной 14-16 мм из стали марки 05Г2НФБ и 05Г2ХНФБ для нефтепроводных спиральношовных труб 1020-1220 мм для проекта ВСТО; проката толщиной 15,9 мм класса прочности К60 (Х70) из стали марки 07Г2МНФБ для газопроводных труб 1067 мм с требованиями по свойствам при ИПГ. По разработанной технологии изготовлено и передано в ОАО «Волжский трубный завод» 620 тонн проката для изготовления спиральношовных труб.
Основные научные положения, выносимые на защиту.
1. Установленные закономерности влияния параметров ускоренного охлаждения и смотки полосы на тип и параметры микроструктуры трубных сталей и соотношение структурных составляющих.
2. Результаты исследования особенностей тонкой микроструктуры стали и кинетики выделения дисперсных частиц карбонитридов (Nb, V)(C, N) в зависимости от технологических параметров смотки полосы.
3. Установленные зависимости влияния основных параметров контролируемой прокатки и смотки полосы на структурообразование и механические свойства проката.
4. Разработанный способ обеспечения хладостойкости при ИПГ применительно к контролируемой прокатке полосы в условиях стана 2000.
5. Установленные соотношения между химическим составом стали, параметрами деформации и охлаждения полосы и рулона, обеспечивающие формирование целевой микроструктуры и комплекса свойств рулонных сталей типа Х70.
6. Разработанные режимы термомеханической прокатки с ускоренным охлаждением и смотки рулонного проката, внедренные на стане 2000 ЧерМК ОАО «Северсталь».
7. Результаты промышленного опробования и испытаний рулонного проката класса прочности К60(Х70) толщиной 14-16 мм и спиральношовных труб без термической обработки.
Апробация работы: Основные положения и результаты работы доложены и обсуждены на: VI Конгрессе прокатчиков (Липецк, 2005 г.); Международном семинаре «Современные тенденции разработки и производства сталей и труб для магистральных газо-нефтепроводов» (Москва, 2008 г.).
Публикации: По теме диссертационной работы опубликовано 9 печатных работ, в т.ч. 6 работ в журналах, входящих в список изданий, рекомендованных ВАК.
Структура и объем работы. Диссертация состоит из введения, 5 глав, общих выводов, списка литературы из 158 наименований. Работа изложена на 161 странице машинописного текста, содержит 43 рисунка и 16 таблиц.
ОСНОВНОЕ СОДЕРЖАНИЕ РАБОТЫ
Во введении раскрыта актуальность работы, обоснована цель, основные задачи, сформулированы научная новизна работы и ее практическая ценность.
В первой главе на основании опубликованных данных рассмотрены требования к современным рулонным сталям, металловедческие представления о механизмах упрочнения низкоуглеродистых микролегированных сталей и возможностях управления процессом структурообразования в рулонном прокате для улучшения комплекса его механических и технологических свойств. Показано, что важнейшим этапом формирования свойств рулонного проката являются операции ускоренного охлаждения (УО) на отводящем рольганге, смотки и охлаждения рулонов, в ходе которых происходит окончательное формирование микроструктуры стали, перед этим подвергнутой горячей пластической деформации. Отмечено отсутствие в отечественной литературе металловедческого обоснования и фактических данных о взаимосвязи технологических параметров контролируемой прокатки (КП) и смотки на процессы структурообразования, механические свойства и сопротивление разрушению рулонного проката класса прочности К60(Х70) толщиной более 12 мм. Особенности формирования спиральношовной трубы (формовка под углом и отсутствие экспандирования) вызывают повышенный уровень требований к прокату. На основании анализа обоснован выбор направления и задач исследования.
Во второй главе обосновываются и описываются выбранные материалы и методы исследования. Материалом исследования были выбраны низколегированные трубные стали с пониженным содержанием углерода (0,04-0,08)% и повышенным содержанием ниобия (0,068-0,079)% нескольких систем легирования (табл.1): 1 – сталь с добавкой ≈ 0,20% Mo без ванадия; 2 - с добавками ≈ 0,20% Ni и ванадием, 3 – с добавками ≈ 0,20%Cr+0,20%Ni и ванадием, 4 - с добавками ≈ 0,20%Ni+0,20%Cu и ванадием, 5 - с добавками ≈ 0,20%Mo+0,20%Ni и ванадием при меньшем содержании Mn.
Сталь выплавляли в 350-тонных конвертерах ЧерМК ОАО «Северсталь», подвергали внепечной обработке в ковше и разливали на установках непрерывной разливки. Слябы прокатывали на НШС 2000 горячей прокатки с ускоренным охлаждением полос в установке ламинарного типа, полосы сматывали в рулоны. Рулоны подвергали охлаждению на стендах ускоренного охлаждения.
Таблица 1 - Химический состав опытных сталей, (% по массе)
№№ п/п | Сталь | C | Mn | S | P | Cr | Ni | Cu | V | Mo | Ti | Nb |
1 | 06Г2МБ | 0,06 | 1,60 | 0,002 | 0,009 | 0,06 | 0,06 | 0,05 | 0,004 | 0,22 | 0,019 | 0,07 |
2 | 05Г2НФБ | 0,04-0,06 | 1,61-1,62 | 0,005 | 0,007-0,010 | 0,02-0,05 | 0,19-0,21 | 0,03-0,05 | 0,053-0,055 | 0,002-0,003 | 0,012-0,018 | 0,069-0,073 |
3 | 05Г2ХНФБ | 0,06 | 1,58-1,61 | 0,003-0,006 | 0,010-0,011 | 0,18-0,21 | 0,20-0,21 | 0,02-0,05 | 0,055-0,057 | 0,002 | 0,003-0,004 | 0,069-0,074 |
4 | 07Г2НДФБ | 0,07-0,08 | 1,62-1,67 | 0,002-0,003 | 0,006-0,007 | 0,03-0,04 | 0,16-0,20 | 0,12-0,19 | 0,053-0,061 | 0,003-0,004 | 0,018-0,022 | 0,068-0,079 |
5 | 07Г2МНФБ | 0,06-0,07 | 1,47-1,50 | 0,001-0,002 | 0,006-0,008 | 0,02-0,03 | 0,21-0,22 | 0,03-0,05 | 0,046-0,047 | 0,17-0,20 | 0,013 | 0,074-0,075 |
Примечание: содержание кремния во всех плавках находилось в пределах 0,19-0,45%; алюминия – 0,04-0,06 %; азота – 0,005-0,009%.
Механические свойства проката определяли по стандартным методикам: на статическое растяжение на плоских пятикратных образцах тип II по ГОСТ 1497 и на образцах ASTM A370 с расчетной длиной 2 (50,8 мм) на машинах типа Р-50, Zwik 1200, Zwik 600; на ударную вязкость по ГОСТ 9454 на образцах типа 1 и 11 при температурах от +20 до -800С; падающим грузом (ИПГ) образцов по ГОСТ 30456-97 с определением доли вязкой составляющей в изломе в интервале температур от +20 оС до -60 оС; на твердость по Виккерсу - по ГОСТ 2999.
Кинетику полиморфного превращения при охлаждении горячедеформированного аустенита исследовали с помощью дилатометра BAHR-805, оснащенного приставкой для деформации образцов сжатием в защитной среде.
Свариваемость металла исследовали методом имитации воздействия термических циклов сварки на структуру и ударную вязкость металла околошовной зоны (ОШЗ) сварного соединения с помощью установки индукционного нагрева и высокоскоростного дилатометра ИМЕТ-ДБ.
Стойкость против водородного растрескивания (HIC) оценивали по методике стандарта NACE TM 02-84; стойкость против сероводородного растрескивания под напряжением (SSCC) – по методике стандарта NACE TM 01-77 (96).
Изучение микроструктуры проводили методами световой микроскопии, просвечивающей электронной микроскопии (ПЭМ); сканирующей электронной микроскопии (СЭМ), в том числе с использованием приставки для рентгеновского микроанализа (РМА); рентгеновской дифрактометрии (РД).
Оценку влияния параметров смотки на структурообразование, выделение частиц карбонитридов (Nb,V)(C,N) и свойства низколегированных сталей производили при помощи промышленного эксперимента на стали составов 06Г2МБ, 07Г2НДФБ с варьированием температуры смотки 500 оС, 550 оС, 600 оС после КП (рис. 1).
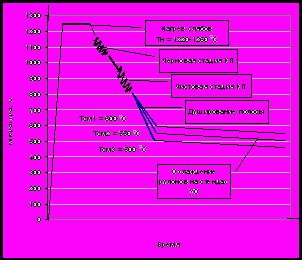
Рис. 1. Схема промышленного эксперимента для определения влияния Тсм на структурообразование и выделение частиц карбонитридов в рулонной стали Х70
В третьей главе выявлены основные технологические параметры, определяющие формирование окончательной микроструктуры рулонного проката, эффективность дисперсионного упрочнения и, как следствие, равномерность свойств по длине полосы. Главными из этих факторов являются: создание повышенной плотности мест зарождения α-фазы в нерекристаллизующемся аустените, определяемой Ткп и суммарным обжатием в чистовой группе клетей; параметры ускоренного охлаждения и смотки полосы в рулон, зависящие от температуры смотки – Тсм и распределения Тсм по длине полосы; а также условия охлаждения рулона (на спокойном воздухе или на стендах УО рулонов).
Определено, что сочетание прочности (σт ≥500 Н/мм2; σв ≥590 Н/мм2 σт/σв ≤ 0,90; δ5≥22% в продольном и поперечном направлениях), ударной вязкости (KCV-20 ≥98 Дж/см2) и хладостойкости при ИПГ (В(ИПГ-20) ≥ 90%) рулонного проката толщиной 14-16 мм, необходимые для производства спиральношовных труб хладостойкого исполнения, может обеспечиваться при переходе от стали с ферритно-перлитной микроструктурой к стали с мелкозернистой ферритно-бейнитной микроструктурой. Такая микроструктура выбрана наиболее перспективной при разработке состава стали и технологии производства рулонного проката класса прочности К60(Х70).
Методом имитации температурно-деформационных режимов контролируемой прокатки с ускоренным охлаждением (КП+УО) с использованием дилатометра BAHR-805 изучена кинетика превращения горячедеформированного аустенита в низкоуглеродистых сталях типа Х70 с добавками элементов, повышающих устойчивость аустенита при охлаждении, и содержании Nb 0,07-0,08%. Анализ термокинетических диаграмм (ТКД) позволил установить, что формирование бейнитной составляющей микроструктуры совместно с подавлением перлитного превращения в области малых скоростей охлаждения (до ≈ 5 оС/с) в стали Х70 состава 0,06%C-1,5%Mn-Nb-(V) в наибольшей степени происходит при введении в сталь 0,20%Mo, далее, по убыванию - 0,20%Cu+0,20%Ni; 0,20%Ni; 0,20%Cr+0,20%Ni (рис. 2). Таким образом, поскольку для условий охлаждения полосы толщиной 14-16 мм характерны относительно малые скорости охлаждения (W800/700 ≈ 5-10 oС/с), то необходимым условием формирования ферритно-бейнитной микроструктуры стали является введение в ее состав указанных добавок, в особенности Mo+Ni, Mo. При использовании добавок Cr+Ni, Ni+Cu возможно формирование ферритно-бейнитной микроструктуры с некоторой долей перлитной составляющей.
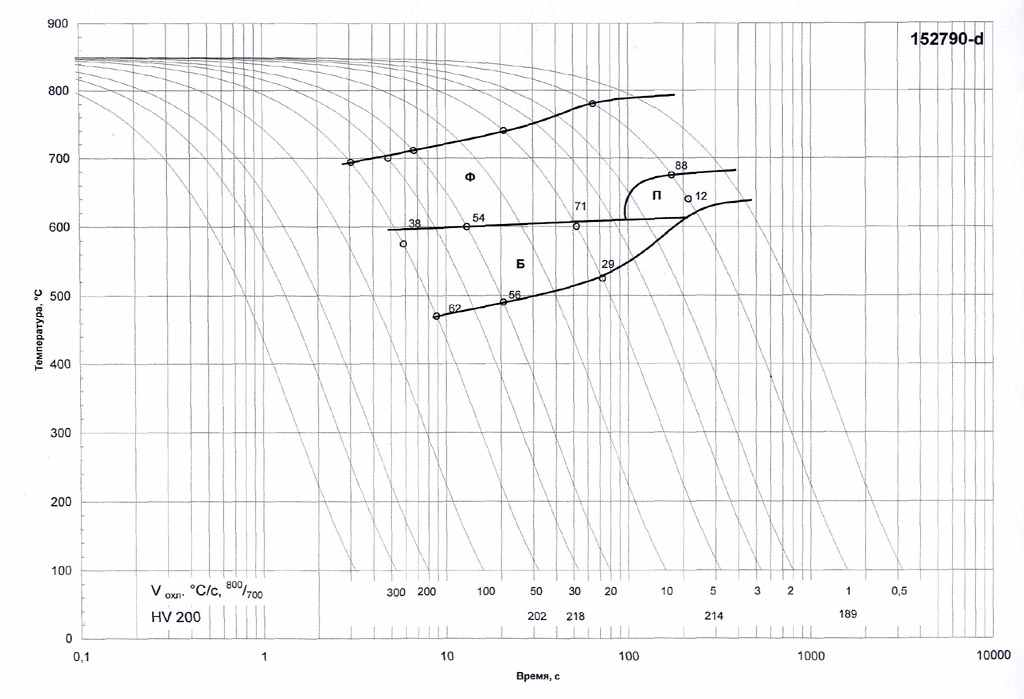
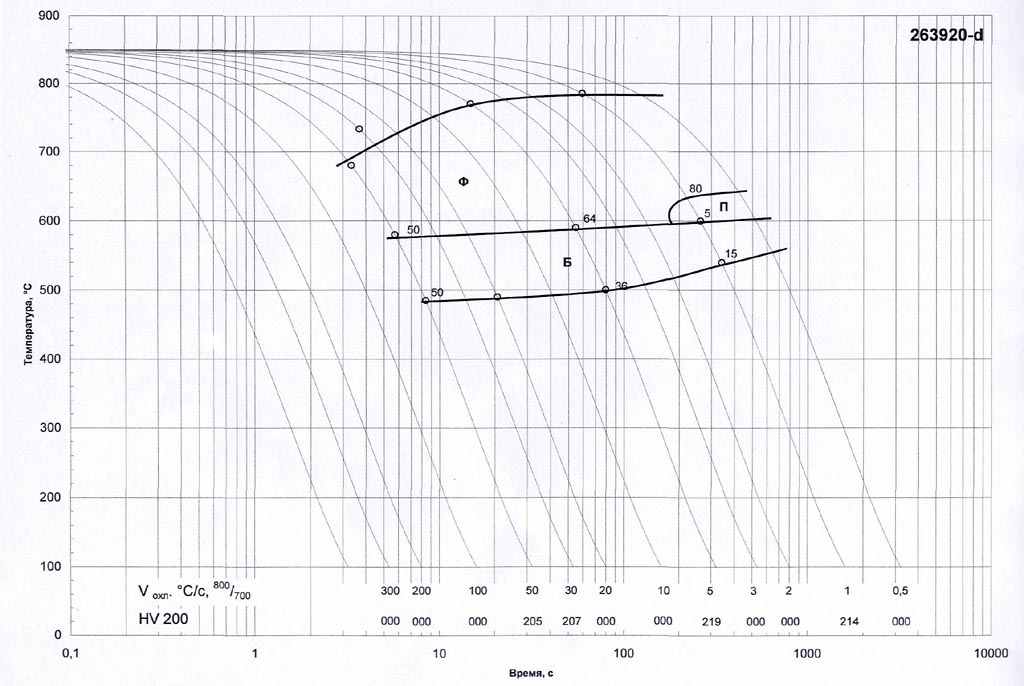
а б
Рис. 2. Термокинетические диаграммы распада горячедеформированного аустенита при непрерывном охлаждении опытных сталей типа Х70:
а - 05Г2ХНФБ; б - 07Г2НДФБ
Многообразие структур бейнитного превращения требует исследования их взаимосвязи с параметрами охлаждения и смотки, поскольку конечная микроструктура проката формируется при смотке полосы в рулон. Методом промышленного эксперимента на стане 2000 на материале сталей 07Г2НДФБ (1-й эксперимент) и 06Г2МБ (2-й эксперимент) произвели исследование влияния Тсм на тип и долю формирующихся составляющих микроструктуры, а также на выделение дисперсных частиц карбонитридов Nb и V, необходимых для дисперсионного упрочнения проката.
При проведении 1-й части эксперимента варьировали Тсм рулонов из стали 07Г2НДФБ на уровнях ≈600 оС, ≈550 оС, ≈500 оС (рис. 1) при практически фиксированных значениях остальных основных технологических параметров (Ткп=800-815 оС, Т5=1050-1085 оС, Т6=940-985 оС). Исследовали металл от 2-го наружного витка опытных рулонов. При анализе микроструктур проката (с использованием точечного метода Глаголева) выявили, что по мере понижения температуры Тсм происходит изменение типа основных микроструктурных составляющих с переходом от традиционной ферритно-перлитной микроструктуры к продуктам неполигональной морфологии (рис. 3).
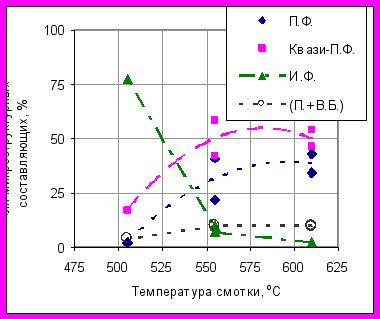
Рис. 3. Зависимость доли структурных составляющих в микроструктуре стали 07Г2НДФБ от Тсм
Доля полигонального феррита (ПФ) традиционной морфологии, максимальная при Тсм = 610 оС, при понижении Тсм уменьшается, а доля квази-полигонального феррита (Кв-ПФ, феррит с иррегулярными границами зерен и повышенной относительно ПФ плотностью дислокаций) возрастает с максимумом около Тсм = 555 оС. Ниже Тсм = 555 оС значительно увеличивается доля игольчатого феррита (ИФ). При Тсм = 505 оС ИФ становится основной структурной составляющей микроструктуры, при этом также практически полностью исчезает углеродсодержащая фаза. При Тсм = 610 оС и Тсм = 555 оС углеродсодержащая фаза представлена смесью перлита (П), вырожденного перлита (ВП, дисперсная смесь низкотемпературного перлита и феррита) и участков верхнего бейнита (ВБ).
Результаты подтверждены данными исследования с применением СЭМ и ПЭМ (рис. 4). Наличия остаточного аустенита и М/А фазы в стали в исследованном диапазоне Тсм=500оС - 600оС не выявлено.
![]() а П.Ф. И.Ф. П | ![]() б | ![]() в И.Ф. Б |
Рис. 4. Тонкая микроструктура (ПЭМ) стали 07Г2НДФБ при Тсм: а - 600˚С (Ф-П); б - 550˚С (ИФ, ПФ, П); в - 500˚С (ИФ, ВБ) |
Известно, что для эффективного использования микролегирования Nb и V для дисперсионного упрочнения проката, в соответствии с моделью Орована дополненной Эшби и Гладманом, необходимо создать условия для формирования карбонитридов этих элементов размером менее 10 нм. Особенности кинетики выделения и роста частиц (Nb,V)(C,N) в зависимости от температуры смотки с уровнями изменения Тсм ≈600 оС, ≈550 оС, ≈500 оС исследовали на материале стали 07Г2НДФБ (см рис. 1).
С целью изучения особенностей выделения частиц Nb(C,N) и NbC в зависимости от температуры смотки и для различных участков рулона при замедленном охлаждении рулонов выполнили 2-й промышленный эксперимент на стали 06Г2МБ (с 0,22% Mo и 0,07% Nb, но без добавок V). Опытный рулон был произведен с понижением величин Ткп и Тсм от «головного» участка полосы (внутренних витков) к «хвостовому» участку полосы (наружные витки рулона): Ткп от 840-860 оС до 820-840 оС и Тсм от 625-645 оС до 570-580 оС, соответственно.
Методом ПЭМ в стали выявлены частицы двух типоразмеров: размером 0,1-0,5 мкм (100-500 нм) и до ≈ 0,05 мкм ≈ 50 нм, а так же частицы нано-метрических размеров – от 3-4 до 20 нм.
Частицы размером 0,1-0,5 мкм (100-500 нм) выявлены при всех значениях Тсм в стали 07Г2НДФБ, они имеют округлую или слабо ограненную форму, распределены равномерно по всем структурным составляющим, а частицы размером (≈ 0,05 мкм ≈ 50 нм) преимущественно в крупнозернистом феррите, что позволяет сделать вывод об их зарождении в аустените, вероятно, при подстуживании подката перед началом чистовой стадии КП. Выделение частиц перед чистовой стадией обеспечивало, наряду с Nb, находящимся в твердом растворе, торможение рекристаллизации аустенита при повышенных температурах, характерных для прокатки на НШС.
Выявлено, что максимальное количество дисперсных частиц карбонитридов Nb и V, обеспечивающих дисперсионное упрочнение, формируются при Тсм ≈ 550-570 оС для сталей с добавками Nb+V (07Г2НДФБ) и при Тсм ≈ 580-610 оС для стали с добавкой только Nb (06Г2МБ). Карбонитриды состава (Nb,V)(C,N), Nb(C,N) и NbC имеют размер ~3-4 нм и расположены в местах с большой плотностью дислокаций в виде цепочек; по границам зерен выделяются более крупные частицы карбонитридов размером ~6-8 нм (рис. 5).
![]() | ![]() |
а | б |
Рис. 5. Дисперсные выделения карбонитридов (Nb,V)(C,N). ПЭМ (темнопольные изображения в рефлексе карбонитридов): а – Тсм=600˚С, б – Тсм=550˚С |
По данным РД, параметр ГЦК решётки частиц размером до ~ 20 нм в стали 07Г2НДФБ соответствует примерно равному содержанию V и Nb. Повышение Тсм приводит к огрублению частиц до 20 нм, обусловленному достаточно высокой диффузионной подвижностью атомов при 600˚С, что уменьшает эффект дисперсионного упрочнения. Снижение Тсм до ≈ 500 оС, приводит к отсутствию выявляемых частиц из-за торможения диффузионных процессов (порог обнаружения составлял 1 нм). При низких значениях Тсм (≈ 500 оС) прочностные свойства проката реализуются в основном за счет формирования продуктов игольчатой морфологии (ИФ). В стали, содержащей только ниобий (06Г2МБ), объёмная доля нано-размерных частиц типа NbC увеличивается с повышением температуры смотки с 570 до 625 оС.
Выявлены условия образования выделений цементита на границах ферритных зерен, ухудшающих хладостойкость проката: при Тсм выше 600-620 оС частицы цементита образуют протяженные прослойки, а при Тсм ≈ 550 оС и ниже они имеют дисперсный и прерывистый характер, что способствует обеспечению хладостойкости.
Таким образом, обеспечение высокого и равномерного по длине полосы уровня свойств рулонного проката может быть достигнуто на основе сбалансированного влияния для всех участков полосы процессов формирования структурных составляющих ферритно-бейнитной микроструктуры стали и выделения частиц (Nb,V)(C,N) размером 3-8 нм без их последующего огрубления в рулоне после смотки. Осуществление смотки стали с Nb+V в интервале 550 оС <Тсм<570-600 оС и последующее ускоренное охлаждение рулонов обеспечивают формирование микроструктуры, состоящей из смеси квази-полигонального феррита (основная часть), полигонального и игольчатого феррита, и при этом также происходит образование частиц (Nb,V)(C,N) размером 3-8 нм, эффективных для дисперсионного упрочнения.
В четвертой главе изложены установленные в ходе промышленных экспериментов с использованием стали типа Х70 взаимосвязи между параметрами деформации и последующей смотки в условиях прокатки на стане 2000 и, с другой стороны, механическими свойствами низколегированных сталей.
На материале рулонного проката толщиной 14-16 мм опытных партий из стали 05Г2ХНФБ и 07Г2НДФБ выполнен анализ влияния Ткп (при изменении Тсм в диапазоне 540-555 оС) и Тсм (при Ткп в пределах 790-820 оС), показавший, что комплекс свойств рулонного проката класса прочности К60(Х70) для наружных витков рулона может быть обеспечен для диапазона значений Ткп=790-820 оС, а Тсм=560-540 оС для стали 05Г2ХНФБ (рис. 6) и Тсм=500-600 оС для стали 07Г2НДФБ (рис. 7) благодаря совместному влиянию различных механизмов упрочнения стали. Снижение Ткп в нижней части γ-области обеспечивает повышение прочностных свойств полосы благодаря улучшении проработки структуры нерекристаллизующегося аустенита перед γ→α превращением и формированию мелкого зерна феррита. Понижение Тсм ниже 600 оС (при Ткп = 790-820 оС) также приводит к повышению прочностных свойств рулонного проката, что объясняется увеличением доли продуктов неполигональной морфологии в структуре стали. Наибольший эффект дисперсионного упрочнения полосы выделениями частиц (Nb,V)(C,N) наблюдается при Тсм немного ниже 580 оС, что, однако, может вызывать уменьшение ударной вязкости проката (рис. 7 б).
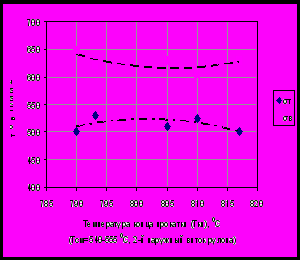
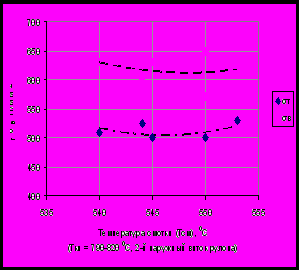
Рис. 6. Зависимости прочностных характеристик рулонного проката толщиной 16 мм из стали 05Г2ХНФБ от значений Ткп и Тсм (отбор проб от середины 2-го витка рулона)
![]() а | ![]() |
Рис. 7. Зависимость уровня механических свойств проката из стали 07Г2НДФБ от параметров смотки: а – прочностные характеристики; б - ударная вязкость |
Для обеспечения равномерности свойств по длине полосы, исходя из вероятных процессов огрубления выделений Nb и V в серединных участках рулона, предложено после прокатки по контролируемым режимам осуществлять смотку полосы при Тсм несколько ниже 580 оС для всех участков по длине полосы, а затем осуществлять ускоренное охлаждение рулонов. Такая технология позволяет обеспечивать условия охлаждения, при которых формируется дисперсная ферритно-бейнитная микроструктура и не происходит существенного огрубления частиц карбонитридов для всех участков рулона, что обеспечивает выгодное сочетание прочностных и вязко-пластических свойств.
С целью определения влияния параметров состава стали и технологии деформирования аустенита на хладостойкость проката при ИПГ произведено обобщение данных промышленных экспериментов по прокатке полосы толщиной 16 мм из сталей 05Г2НФБ, 05Г2ХНФБ и 07Г2НДФБ на стане 2000. Показано, что количество вязкой составляющей в изломе образца ИПГ не менее 90 % (B(ИПГ)-20 ≥ 90 %) при температуре испытания -20 оС достигается при отношении толщины подката к конечной толщине полосы (кратность подката) не менее 3,1-3,2 (рис. 8).
Свойства металла при ИПГ являются в значительной мере структурно-чувствительной характеристикой, и их обеспечение основывается на положении о необходимости сохранения проработанной структуры аустенита, характеризующейся величиной удельной эффективной поверхности (Svэфф) аустенита перед превращением. Для оценки степени сохранения проработанности структуры нерекристаллизующегося аустенита перед превращением представлен параметр ΔTSv=Ткп-Ar3расч, связывающий фактическое значение Ткп и расчетное значение Ar3расч.. Значение Ar3расч определяли по известной формуле (C. Ouchi, 1982) для стали контролируемой прокатки с Nb и накопленной деформацией более 30% при температуре ниже 900 оС: Ar3(оС)=910-310C-80Mn-20Cu-15Cr-55Ni-80Mo+0,35(t-8), где C, Mn, Cu, Cr, Ni, Mo – массовые доли элементов, %; t – толщина листа, мм.
Исследовали возможность повышения свойств рулонного проката толщиной 14-16 мм при ИПГ путем оптимизации взаимного расположения расчетной критической точки (Ar3расч) и фактически реализуемых значений Ткп. Хладостойкость при ИПГ оценивали по порогу хладноломкости при ИПГ (Т90 В.С. ИПГ), определяемому в ходе сериальных испытаний проката в интервале температур от +20 оС до -60 оС. На рис. 9 показана зависимость пороговой температуры, при которой обеспечивается 90% вязкой составляющей в изломе образца ИПГ при температуре -20 оС (В(ИПГ-20)) (Т90 В.С.ИПГ) от параметра ΔTSv=Ткп-Ar3расч. Для ранее опробованных вариантов стали Х70 (05Г2ХНФБ, 07Г2НДФБ) величина ΔTSv имела достаточно большое значение: ≈50-70 оС. Температура Т90 В.С.ИПГ была около -20…-30 оС, что не в полностью обеспечивало запас по свойствам ИПГ при изготовлении спиральношовных труб в случае испытаний при температуре -20 оС.
![]() | ![]() |
Рис. 8. Зависимость количества вязкой составляющей в изломе образцов (B(ИПГ-20)) от отношения подката к конечной толщине полосы | Рис. 9. Зависимость пороговой температуры при которой обеспечивается 90% В(ИПГ) от величины ΔTSv =Ткп-Ar3расч |
Для обеспечения свойств при ИПГ для рулонного проката толщиной 14-16 мм произвели оптимизацию состава рулонной стали типа Х70, предназначенной для производства проката толщиной 14-16 мм в соответствии с фактическим условиям завершения деформации в группе чистовых клетей. Разработанный состав стали марки 06Г1МНДФБ характеризуется минимизированным значением параметра ΔTSv для условий завершения прокатки на стане 2000. В ходе реализации новой концепции рулонной стали для проката толщиной 14-16 мм была обеспечена температура Т90 В.С.ИПГ около -40оС (рис. 9), причем для всех участков по длине полосы. Показано, что в условиях стана 2000, когда увеличение кратности подката и существенное снижение Ткп не представляются возможными, свойства рулонного проката толщиной 14-16 мм при ИПГ (В(ИПГ-20)≥90%) обеспечиваются при выполнении соотношения ΔTSv=Ткп-Ar3расч < 50 оС, которое достигается выбором оптимального состава стали.
Разработаны рекомендации по составу стали и технологии производства рулонного проката с гарантией уровня механических свойств и хладостойкостью при ИПГ, основывающиеся на использовании стали Х70 с пониженным содержанием углерода (0,05-0,07%), экономными добавками Cr, Ni, Cu, Mo и оптимизацией состава по параметру ΔTSv; применении контролируемой прокатки полосы с окончанием в нижней части γ-области; смотке полосы при температуре ниже 580 оС и ускоренном охлаждении рулонов.
Пятая глава посвящена представлению результатов промышленного опробования в ЧерМК ОАО «Северсталь» производства рулонного проката с применением разработанных технологических решений.
На основе предложенных выше рекомендаций разработана технология производства рулонного проката класса прочности К60(Х70) толщиной 14-16 мм с гарантией уровня механических свойств, в том числе хладостойкости при ИПГ, применительно к условиям стана 2000 ЧерМК ОАО «Северсталь». Состав стали и технология производства на стане 2000 оптимизированы в соответствии с требованиями к хладостойкости проката. Стали отличались пониженным содержанием углерода (0,04-0,07%) и комплексным микролегированием Nb+Ti+V с повышенным содержанием Nb. Все стали имели мелкозернистую ферритно-бейнитную микроструктуру с размером элемента ферритной матрицы, соответствующим 11-13 номеру по ГОСТ 5639.
Для проката для нефтепроводных труб Ø1020-1220х14-16 мм класса прочности К60 (без требований при ИПГ) выбрана композиция стали 05Г2НФБ и 05Г2ХНФБ без добавок молибдена, для класса прочности К56 и К60 (14 мм) – с добавкой Ni, а для класса прочности К60 толщиной 16 мм – с добавкой Cr+Ni. Сталь имела невысокий уровень легирования: Сэ≈0,36-0,37% для 05Г2НФБ и Сэ≈ до 0,40% для 05Г2ХНФБ. Прокатка на стане произведена с малой толщиной подката, что позволило не перегружать клети чистовой группы. Сталь для газопроводных спиральношовных труб с толщиной стенки 15,9 мм и требованиями при ИПГ (07Г2МНФБ) содержит добавку Mo+Ni, и имеет относительно более высокий уровень легирования (Сэ≈0,39-0,42%). Технология прокатка полос из стали 07Г2МНФБ предусматривает оптимизацию толщины (кратности) подката для обеспечения свойств при ИПГ.
В результате опытно-промышленного опробования производства разработанных сталей подтверждено, что применение разработанной технологии КП+УО, отличающейся контролем за формированием ферритно-бейнитной микроструктуры и мелко-дисперсных выделений (Nb,V)(C,N) при смотке и охлаждении рулонов, в условиях стана 2000 ЧерМК ОАО «Северсталь» позволяет получить в прокате из стали Х70 (07Г2МНФБ) высокий комплекс механических свойств: σт ≥ 535 Н/мм2, σв ≥ 640 Н/мм2, δ5 ≥ 23% (на продольных и поперечных образцах), KCV-20 ≥ 160 Дж/см2, В(ИПГ-20)=90-100%, в сочетании с обеспечением равномерности уровня прочностных свойств в пределах 7 % для поперечных образцов. Результаты подтверждены Актом промышленного опробования, выданным ЧерМК ОАО “Северсталь”.
Для производства листового проката, получаемого порезкой рулонного и для производства спиральношовных труб с хладостойкостью при ИПГ до -40 оС, разработан состав и внедрена технология производства стали 06Г1МНДФБ (Сэ≈0,36-0,37%) с оптимизированным содержанием основных легирующих элементов, обеспечивающим значение ΔTSv=Ткп-Ar3расч.<50 оС (табл. 2). Впервые в отечественной практике опробована порезка рулонного проката толщиной 14, 15,9 и 16 мм на листы мерных длин, в ходе чего подтверждена равномерность уровня механических свойств, в том числе при ИПГ, по длине полосы.
Таблица 2 - Механические свойства проката из стали 06Г1МНДФБ
Толщина проката, мм | Направление отбора образцов | σт, Н/мм2 | σв, Н/мм2 | σт/σв | δ5, % | KСV-20, Дж/см2 | KСU-60, Дж/см2 | В(ИПГ-20), % |
Требования спецификации | 480-580 | 590-690 | ≤ 0,9 | ≥22 | ≥69 | ≥78 | ≥70 (лист); ≥90 (рулон); | |
14 | Поперек | 490-575 530 | 595-675 635 | 0,82-0,86 0,84 | 24-26 25 | 277-390 330 | 248-330 290 | 100 |
16 | Поперек | 490-555 520 | 590-650 620 | 0,84-0,86 0,85 | 24-26 25 | 261-318 300 | 224,6-297 263 | 90-98 93 |
14,4 | Под углом 45º | 490-560 525 | 590-625 610 | 0,84-0,88 0,86 | 25-27 26 | 278-349 311 | - | 88-100 94 |
Примечание: в числителе – разброс свойств, в знаменателе – среднее значение параметра
Методом имитации воздействия сварочного цикла на структуру и свойства металла околошовной зоны (ОШЗ) показано, что стали 05Г2ХНФБ и 06Г1МНДФБ характеризуется отсутствием склонности к образованию холодных трещин в металле ОШЗ и удовлетворительной ударной вязкостью металла ОШЗ (KCV-40≥50 Дж/см2) в условиях дуговой сварки под флюсом, ручной дуговой сварки и сварки в среде защитных газов труб с толщиной стенки 14-16 мм.
С использованием представленных технологических решений разработан состав и технология производства стали марки 07ГФБ для газонефтепроводных труб класса прочности К55-К56, получаемых сваркой ТВЧ, и используемых вместо бесшовных труб. Формирование в прокате толщиной 8-10 мм равновесной мелкозернистой феррито-перлитной микроструктуры с пониженным уровнем сегрегации обеспечивает требуемое сочетание прочности, хладостойкости и сероводородостойкости труб.
Общие Выводы
1. Исследовано влияние химического состава стали и основных параметров технологии производства рулонного проката толщиной 14-16 мм из микролегированных трубных сталей на процессы фазовых превращений, тип формирующейся микроструктуры, доли структурных составляющих и выделение дисперсных частиц карбонитридов в стали после ускоренного охлаждения полосы и ее смотки в рулон; разработано металловедческое обоснование обеспечения равномерности уровня механических свойств по длине полосы и хладостойкости проката при ИПГ; созданы технологические схемы производства хладостойкого проката; в условиях стана 2000 ЧерМК ОАО «Северсталь» осуществлено опробование и изготовлены промышленные партии рулонного проката для ОАО «Волжский трубный завод».
2. Определено в ходе исследования опытных сталей, что введение в сталь типа Х70 с пониженным содержанием углерода добавок ≈0,20% Mo, ≈(0,20-0,40)%(Ni+Cu; Ni; Ni+Cr) обеспечивает формирование ферритно-бейнитной микроструктуры стали при скорости охлаждения не менее 2-5 оС/с, что соответствует условиям ускоренного охлаждения полосы толщиной 14-16 мм.
3. Установлено определяющее воздействие температуры смотки полосы в рулон (Тсм) на параметры микроструктуры стали с добавками Ni+Cu, Mo, которое состоит в последовательной замене продуктов диффузионного превращения (полигональный феррит и перлит) продуктами промежуточного (бейнитного) превращения (квази-полигональный феррит, игольчатый феррит, верхний бейнит), а также уменьшении полосчатости микроструктуры и доли углеродсодержащей фазы при понижении Тсм от ≈ 600 оС до ≈ 500 оС.
4. Определены значения температуры смотки, при которых наблюдаются выделения карбонитридов (Nb,V)(C,N) размером 3-8 нм, эффективные для дисперсионного упрочнения проката: Тсм ≈ 550-570 оС для сталей с добавками Nb+V и Тсм ≈ 580-610 оС для сталей с добавками только Nb, при этом повышение Тсм приводит к огрублению частиц до ≈ 20 нм; а снижение Тсм до ≈ 500 оС – к отсутствию выявляемых частиц размером от 1 нм.
5. Показана возможность достижения комплекса свойств рулонного проката класса прочности К60 (Х70) для наружных витков рулонов из разработанной стали марки 07Г2НДФБ при Ткп=790-820 оС и в широком диапазоне значений Тсм от ≈500 до ≈600 оС благодаря совместному влиянию различных механизмов упрочнения стали; однако для получения равномерности уровня свойств по длине полосы рациональным является режим смотки при Тсм для всех участков полосы несколько ниже 580 оС, позволяющий обеспечить, как формирование постоянного фазового состава стали, так и выделение частиц карбонитридной фазы размером 3-8 нм без их последующего огрубления, а также предотвратить образование протяженных выделений цементита по границам зерен феррита.
6. Установлена и входе промышленного опробования на разработанной стали 06Г1МНДФБ подтверждена возможность обеспечения хладостойкости при ИПГ для рулонного проката толщиной 14-16 мм в случае ограничений по толщине подката для группы чистовых клетей и температуре окончания прокатки в случае выполнения соотношения ΔTSv=Ткп-Ar3расч < 50 оС, что достигается путем оптимизации химического состава стали; при этом представленный параметр ΔTSv=Ткп-Ar3расч характеризует степень сохранения проработанной структуры аустенита после чистовой стадии контролируемой прокатки до начала фазового превращения.
7. Разработана технология производства хладостойкого рулонного проката класса прочности К60(Х70) толщиной 14-16 мм на стане 2000, предусматривающая:
- выбор состава стали с пониженным содержанием углерода (0,05-0,07)%, комплексными микролегированием (Nb+V+Ti) и экономными добавками элементов, способствующих формированию ферритно-бейнитной микроструктуры (Mo, Ni, Cu, Cr); оптимизацию состава стали по соотношению ΔTSv=Ткп-Ar3расч < 50 оС;
- применение технологии контролируемой прокатки с оптимизированной в соответствии с требованиями к хладостойкости толщиной подката для чистовых клетей, завершением прокатки в нижней части аустенитной области и ускоренным охлаждением со скоростью от 5 оС/с для формирования дисперсной ферритно-бейнитной микроструктуры;
- смотку полосы при Тсм < 580 оС и последующее ускоренное охлаждение рулонов для обеспечения условий для выделения частиц карбонитридов Nb и V и предупреждения существенного роста частиц и образования прослоек цементита на границах зерен.
8. Произведено промышленное опробование разработанной технологии в условиях стана 2000 ЧерМК ОАО «Северсталь», в ходе которого разработаны низколегированные стали и технология производства рулонного проката, предназначенного для изготовления спиральношовных труб без термической обработки: сталь марок 05Г2НФБ и 05Г2ХНФБ - для нефтепроводных труб Ø1020-1220х14-16 мм класса прочности К60; стали марок 07Г2МНФБ и 06Г1МНДФБ - для газопроводных труб категории прочности Х70 с гарантией свойств при ИПГ. Применение разработанной технологии позволило получить в прокате высокий комплекс механических свойств (сталь марки 07Г2МНФБ): σт ≥ 535 Н/мм2, σв ≥ 640 Н/мм2, δ5 ≥ 23% (в поперечном и продольном направлениях), KCV-20 ≥ 160 Дж/см2, В(ИПГ-20)=90-100% в сочетании с равномерностью уровня прочностных свойств по длине полосы в пределах 7 % и хорошей свариваемостью. Впервые в отечественной практике опробовано производство рулонного проката с поставкой в листах толщиной 14-16 мм. Результаты подтверждены Актом промышленного опробования, выданным ЧерМК ОАО “Северсталь”.
Основное содержание работы изложено в следующих публикациях:
1. Филатов Н.В., Настич С.Ю., Голованов А.В., Торопов С.С., Попов Е.С., Соя С.В. Обеспечение равномерности свойств и хладостойкости при ИПГ в рулонном и листовом прокате из стали Х70 со стана 2000 // Металлург. 2009. № 8. С. 57-61.
2. Настич С.Ю., Филатов Н.В., Немтинов А.А., Попов Е.С., Голованов А.В. Формирование гарантированного комплекса свойств рулонного проката категории прочности Х70 // Металлург. 2008. № 7. С. 46-51.
3. Настич С.Ю., Филатов Н.В., Морозов Ю.Д., И.В. Лясоцкий, Е.В. Шульга. Структурообразование и выделение наноразмерных частиц в стали Х70 при смотке и охлаждении рулонов // Сталь. 2009. № 9. С. 82-87.
4. Эфрон Л.И., Настич С.Ю., Столяров В.И., Лубе И.И., Голованов А.В., Филатов Н.В. Рулонная сталь контролируемой прокатки для труб класса прочности К60 // Сталь. 2006. № 7. С. 75-78.
5. Голованов А.В., Зикеев В.Н., Харчевников В.П., Филатов Н.В., Краснов А.В. Разработка состава стали и технологических параметров производства хладостойкого и сероводородостойкого проката для нефтегазопроводных труб // Сталь. 2005. №9. С. 70-71.
6. Голованов А.В., Филатов Н.В., Эфрон Л.И., Настич С.Ю., Лубе И.И. Опытно-промышленное производство на стане 2000 ОАО «Северсталь» рулонного проката класса прочности К60 для хладостойких спиральношовных труб большого диаметра // Труды VI Конгресса прокатчиков (том 1) (Липецк, 18-21 октября 2005 г.)/ Москва. 2005. МОО «Объединение прокатчиков», Корпорация производителей черных металлов. С. 44-48.
7
. Зикеев В.Н., Харчевников В.П., Филатов Н.В., Анучин К.В. Новые конструкционные стали для свариваемых ТВЧ газонефтепроводных, обсадных и насосно-компрессорных труб повышенной прочности, хладостойкости и сопротивления сероводородному растрескиванию // Проблемы черной металлургии и материаловедения. 2008. № 3. С. 12- 17.
8. Зикеев В.Н., Харчевников В.П., Филатов Н.В., Анучин К.В. Разработка и опробование конструкционных сталей повышенной хладостойкости и сопротивления сероводородному растрескиванию для электросварных (ТВЧ) труб нефтяного сортамента // Металлург. 2008. №9. С. 35-39.
9. Луценко А.Н., Немтинов А.А., Филатов Н.В., Настич С.Ю., Морозов Ю.Д. Рулонный прокат категории прочности Х70 производства ЧерМК ОАО «Северсталь» // Международный семинар «Современные тенденции разработки и производства сталей и труб для магистральных газо-нефтепроводов» (г. Москва, 12-13 февраля 2008 г., ФГУП «ЦНИИчермет им. И.П. Бардина») / Сб. докладов. – М.: Металлургиздат, 2009. – 102 с. Илл. С. 30-33.
50>