Закономерности превращения
Вид материала | Закон |
- Лекция 1 Углеводы, липиды, минеральные вещества, 68.17kb.
- Вопросы для вступительных экзаменов для магистров по программе «Агропочвоведение, 65.13kb.
- Методика обучения иностранным языкам как педагогическая наука, 306.62kb.
- Норбеков Мирзакарим Санакулович Рыжий ослик или Превращения: книга, 1568.06kb.
- Научные основы процесса пиролиза углеводородов термодинамика пиролиза углеводородов, 238.08kb.
- Задачи на исследование изучить понятие экосистемы и исследовать их законы и закономерности, 22.52kb.
- Анализ ликвидности баланса, 30.22kb.
- 5. Работа и энергия Тема Работа и энергия, 159.82kb.
- 2,4-диарилбицикло 1]нон-2-ен-9-оны: синтез, строение и некоторые химические превращения, 300.55kb.
- Учебно-методический комплекс Учебник «Биология. Общие закономерности»,С. Г. Мамонтов,, 68kb.
^ 6. Основное оборудование для термической обработки.
Нагрев стали для термической обработки производится в термических печах. Различают термические печи электрические, работающие на газообразном и жидком топливе.
Электрические печи обеспечивают температуру 1350оС , они позволяют очень точно регулировать температуру.
^ По способу передачи тепла деталям, подвергающимся термообработке, печи подразделяются на камерные, муфельные, шахтные и печи-ванны.
В камерных печах детали загружаются в камеру, сюда же поступают и горячие газы.
В муфельных печах изделия загружаются в муфель (камеру), который нагревается снаружи.
В шахтных печах рабочее пространство (шахта) вытянуто в вертикальном направлении, изделия загружаются сверху.
В электрических печах-ваннах рабочее пространство представляет собой тигель, муфель, ванну с расплавленными солями или маслом, куда погружаются изделия. Они обеспечивают более равномерный и быстрый нагрев, детали в них меньше окисляются.
^ По назначению различают печи для отжига, нормализации, закалки, отпуска, цементации и т. п. . Каждая из этих печей имеет свои конструктивные особенности, определяемые характером вида обработки.
При термической обработке температуры измеряются термометрами, термоэлектрическими (состоящими из термопары и гальванометра) и оптическими пирометрами (состоящего из аккумулятора, лампочки, реостата, зрительной трубы).
^ Когда нет приборов, температуру можно определить приближенно по цветам побежалости – появляющейся оксидной плёнке на светлой поверхности металла при нагревании в пределах температур от 220-3300С и цветам каления – цветам свечения, которые приобретает раскалённый металл при 530- 13000С.
Цвета побежалости и
цвета каления и
соответствующие им температуры.
Таблица 3
^ Цвета побежалости | температура | Цвета каления | температура |
Светло-жёлтый | 220 | Начало свечения | 530-580 |
жёлтый | 230 | Тёмно-красный | 580-660 |
коричневый | 255 | Тёмно-вишнёвый | 660-720 |
Коричнево-красный | 265 | Светло-вишнёвый | 780-830 |
Фиолетовый | 285 | Светло-красный | 900-1050 |
Тёмно-синий | 295-310 | Светло-жёлтый | 1150-1250 |
серый | 330 | Белый | 1250 и выше |
Термическая обработка легированных сталей.
Легированные стали подвергаются тем же видам термической обработки, что и углеродистые, но процессы термообработки легированных сталей имеют свои особенности.
Легирующие элементы (особенно вольфрам) понижают теплопроводность стали, поэтому нагрев легированных сталей нужно вести медленно, иначе могут появиться трещины.
Легирующие элементы изменяют также температуры, при которых происходят превращения в сталях. Хром, ванадий, вольфрам, молибден, титан, медь повышают критические точки Ас3 и Ас1. Значит, при отжиге , нормализации, закалке сталей, содержащих эти элементы, нагрев должен вестись до более высоких температур, чем для углеродистых сталей. Марганец, никель, наоборот, понижают критические точки. Соответственно, стали, легированные этими элементами, нагревают до более низких температур.
Все легирующие элементы (особенно те, которые образуют карбиды: хром, ванадий, молибден, титан, вольфрам) препятствуют росту зерна аустенита. Располагаясь по границам зёрен, карбиды затрудняют рост зерна. Поэтому все легированные стали можно нагревать до более высоких температур, не опасаясь перегрева стали, что способствует более полному растворению карбидов в аустените.
Исключение составляют стали, легированные марганцем. Марганец не препятствует росту зерна аустенита. Поэтому марганцовистые стали следует нагревать до температур, возможно более близких к критической точке Ас3.
Так как легированные стали имеют меньшую теплопроводность, то для полного прогрева детали и более полного растворения карбидов в аустените нужна более продолжительная выдержка при достигнутой температуре, чем для углеродистых сталей.
Все легирующие элементы, кроме кобальта, уменьшают критическую скорость закалки, следовательно, легированные стали при закалке можно охлаждать с меньшей скоростью. Обычно в большинстве легированных сталях мартенсит получается при закалке в масле, а в некоторых высоколегированных сталях даже на воздухе.
Прокаливаемость у легированных сталей более высокая, чем у углеродистых. Стали с высоким содержанием легирующих элементов закаливаются на большую глубину даже при больших сечениях изделий.
- Контрольные вопросы.
- Сталь подвергалась закалке и последующему отпуску. Из каких основных превращений складывается этот технологический процесс? (см. пункты 2, 3, 4).
- Какие мероприятия обеспечивают получение мелкого зерна аустенита при нагреве стали?
- Какие соединения называют карбидами? Какие легирующие компоненты образуют карбиды? Как влияют на рост зерна карбиды?
- Укажите особенности термической обработки марганцовистой стали.
- В чём проявляется перегрев и пережог стали? Какой из этих дефектов можно исправить и как это сделать?
- Как предупредить появление окалины и обезуглероживание поверхности при нагреве? Как создать защитную атмосферу в печи?
- Какие структуры стали являются неустойчивыми и какие превращения они претерпевают при повторном нагревании?
- Какие дефекты устраняются при отпуске стали?
- Что называется критической скоростью закалки? Как она изменяется в зависимости от содержания углерода в стали?
- Перечислите виды термообработки. Что такое термическая обработка детали (изделия)?
- **Как определить температуру стали. Нагретой до температуры ниже критической точки Ас1?
- **Как определить температуру стали, нагретой до температуры выше критической точки Ас3?
- Чем можно объяснить целесообразность неполной закалки заэвтектоидных сталей?
- Задание.
- 1.Составьте таблицу «Брак при термической обработке» по схеме:
-
-
Вид брака
Причины появления брака
Способы предупреждения брака
Методы устранения брака
1.
2.
3.
4.
5.
6.
7.
2. Стальной лист после холодной вытяжки и рекристаллизационного отжига получил крупнозернистое строение. Как можно исправить этот дефект?
А) подвергнуть листы полному отжигу
Б) …нормализации.
- Лекция 10
-
Химико-термическая обработка стали: цементация, азотирование, нитроцементация и диффузионная металлизация.
- Химико-термическая обработка стали
- Назначение и технология видов химико-термической обработки: цементации, азотирования нитроцементации и диффузионной металлизации
- Цементация
- Цементация в твердом карбюризаторе.
- Газовая цементация.
- Структура цементованного слоя
- Термическая обработка после цементации
- Азотирование
- Цианирование и нитроцементация
- Диффузионная металлизация
^ 1. Химико-термическая обработка стали
Химико-термическая обработка (ХТО) – процесс изменения химического состава, микроструктуры и свойств поверхностного слоя детали.
Изменение химического состава поверхностных слоев достигается в результате их взаимодействия с окружающей средой (твердой, жидкой, газообразной, плазменной), в которой осуществляется нагрев.
В результате изменения химического состава поверхностного слоя изменяются его фазовый состав и микроструктура,
Основными параметрами химико-термической обработки являются температура нагрева и продолжительность выдержки.
В основе любой разновидности химико-термической обработки лежат процессы диссоциации, адсорбции, диффузии.
Диссоциация – получение насыщающего элемента в активированном атомарном состоянии в результате химических реакций, а также испарения.
Например,

Адсорбция – захват поверхностью детали атомов насыщающего элемента.
Адсорбция – всегда экзотермический процесс, приводящий к уменьшению свободной энергии.
Диффузия – перемещение адсорбированных атомов вглубь изделия.
Для осуществления процессов адсорбции и диффузии необходимо, чтобы насыщающий элемент взаимодействовал с основным металлом, образуя твердые растворы или химические соединения.
Химико-термическая обработка является основным способом поверхностного упрочнения деталей.
Основными разновидностями химико-термической обработки являются:
- цементация (насыщение поверхностного слоя углеродом);
- азотирование (насыщение поверхностного слоя азотом);
- нитроцементация или цианирование (насыщение поверхностного слоя одновременно углеродом и азотом);
- диффузионная металлизация (насыщение поверхностного слоя различными металлами).
^ 2. Назначение и технология видов химико-термической обработки: цементации, азотирования нитроцементации и диффузионной металлизации
Цементация
Цементация – химико-термическая обработка, заключающаяся в диффузионном насыщении поверхностного слоя атомами углерода при нагреве до температуры 900…950 oС.
Цементации подвергают стали с низким содержанием углерода (до 0,25 %).
Нагрев изделий осуществляют в среде, легко отдающей углерод. Подобрав режимы обработки, поверхностный слой насыщают углеродом до требуемой глубины.
^ Глубина цементации (h) – расстояние от поверхности изделия до середины зоны, где в структуре имеются одинаковые объемы феррита и перлита ( h. = 1…2 мм).
Степень цементации – среднее содержание углерода в поверхностном слое (обычно, не более 1,2 %).
Более высокое содержание углерода приводит к образованию значительных количеств цементита вторичного, сообщающего слою повышенную хрупкость.
На практике применяют цементацию в твердом и газовом карбюризаторе (науглероживающей среде).
Участки деталей, которые не подвергаются цементации, предварительно покрываются медью (электролитическим способом) или глиняной смесью.
^ Цементация в твердом карбюризаторе.
Почти готовые изделия, с припуском под шлифование, укладывают в металлические ящики и пересыпают твердым карбюризатором. Используется древесный уголь с добавками углекислых солей ВаСО3, Na2CO3 в количестве 10…40 %. Закрытые ящики укладывают в печь и выдерживают при температуре 930…950 oС.
За счет кислорода воздуха происходит неполное сгорание угля с образованием окиси углерода (СО), которая разлагается с образованием атомарного углерода по реакции:

Образующиеся атомы углерода адсорбируются поверхностью изделий и диффундируют вглубь металла.
Недостатками данного способа являются:
- значительные затраты времени (для цементации на глубину 0,1 мм затрачивается 1 час);
- низкая производительность процесса;
- громоздкое оборудование;
- сложность автоматизации процесса.
Способ применяется в мелкосерийном производстве.
Газовая цементация.
Процесс осуществляется в печах с герметической камерой, наполненной газовым карбюризатором.
Атмосфера углеродосодержащих газов включает азот, водород, водяные пары, которые образуют газ-носитель, а также окись углерода, метан и другие углеводороды, которые являются активными газами.
Глубина цементации определяется температурой нагрева и временем выдержки.
Преимущества способа:
- возможность получения заданной концентрации углерода в слое (можно регулировать содержание углерода, изменяя соотношение составляющих атмосферу газов);
- сокращение длительности процесса за счет упрощения последующей термической обработки;
- возможность полной механизации и автоматизации процесса.
Способ применяется в серийном и массовом производстве.
Структура цементованного слоя
Структура цементованного слоя представлена на рис. 15.1.
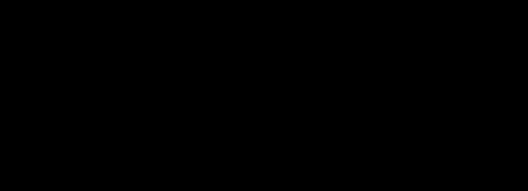
Рис. 15.1. Структура цементованного слоя
На поверхности изделия образуется слой заэвтектоидной стали, состоящий из перлита и цементита. По мере удаления от поверхности, содержание углерода снижается и следующая зона состоит только из перлита. Затем появляются зерна феррита, их количество, по мере удаления от поверхности увеличивается. И, наконец, структура становится отвечающей исходному составу.
Термическая обработка после цементации
В результате цементации достигается только выгодное распределение углерода по сечению. Окончательно формирует свойства цементованной детали последующая термообработка. Все изделия подвергают закалке с низким отпуском. После закалки цементованное изделие приобретает высокую твердость и износостойкость, повышается предел контактной выносливости и предел выносливости при изгибе, при сохранении вязкой сердцевины.
Комплекс термической обработки зависит от материала и назначения изделия.
Графики различных комплексов термической обработки представлены на рис. 15.2.
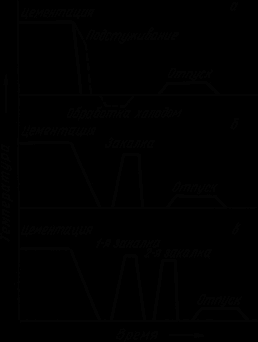
Рис. 15.2. Режимы термической обработки цементованных изделий
Если сталь наследственно мелкозернистая или изделия неответственного назначения, то проводят однократную закалку с температуры 820…850oС (рис. 15.2 б). При этом обеспечивается получение высокоуглеродистого мартенсита в цементованном слое, а также частичная перекристаллизация и измельчение зерна сердцевины.
При газовой цементации изделия по окончании процесса подстуживают до этих температур, а затем проводят закалку (не требуется повторный нагрев под закалку) (рис. 15.2 а).
Для удовлетворения особо высоких требований, предъявляемых к механическим свойствам цементованных деталей, применяют двойную закалку (рис. 15.2 в).
Первая закалка (или нормализация) проводится с температуры 880…900oС для исправления структуры сердцевины.
Вторая закалка проводится с температуры 760…780oС для получения мелкоигольчатого мартенсита в поверхностном слое.
Завершающей операцией термической обработки всегда является низкий отпуск, проводимый при температуре 150…180oС. В результате отпуска в поверхностном слое получают структуру мартенсита отпуска, частично снимаются напряжения.
Цементации подвергают зубчатые колеса, поршневые кольца, червяки, оси, ролики.
Азотирование
Азотирование – химико-термическая обработка, при которой поверхностные слои насыщаются азотом.
Впервые азотирование осуществил Чижевский И.П., промышленное применение – в двадцатые годы.
При азотировании увеличиваются не только твердость и износостойкость, но также повышается коррозионная стойкость.
При азотировании изделия загружают в герметичные печи, куда поступает аммиак NH3 c определенной скоростью. При нагреве аммиак диссоциирует по реакции: 2NH3>2N+3H2. Атомарный азот поглощается поверхностью и диффундирует вглубь изделия.
Фазы, получающиеся в азотированном слое углеродистых сталей, не обеспечивают высокой твердость, и образующийся слой хрупкий.
Для азотирования используют стали, содержащие алюминий, молибден, хром, титан. Нитриды этих элементов дисперсны и обладают высокой твердостью и термической устойчивостью.
Типовые азотируемые стали: 38ХМЮА, 35ХМЮА, 30ХТ2Н3Ю.
Глубина и поверхностная твердость азотированного слоя зависят от ряда факторов, из которых основные: температура азотирования, продолжительность азотирования и состав азотируемой стали.
В зависимости от условий работы деталей различают азотирование:
- для повышения поверхностной твердости и износостойкости;
- для улучшения коррозионной стойкости (антикоррозионное азотирование).
В первом случае процесс проводят при температуре 500…560oС в течение 24…90 часов, так как скорость азотирования составляет 0,01 мм/ч. Содержание азота в поверхностном слое составляет 10…12 %, толщина слоя (h) – 0,3…0,6 мм. На поверхности получают твердость около 1000 HV. Охлаждение проводят вместе с печью в потоке аммиака.
^ Значительное сокращение времени азотирования достигается при ионном азотировании, когда между катодом (деталью) и анодом (контейнерной установкой) возбуждается тлеющий разряд. Происходит ионизация азотосодержащего газа, и ионы бомбардируя поверхность катода, нагревают его до температуры насыщения. Катодное распыление осуществляется в течение 5…60 мин при напряжении 1100…1400 В и давлении 0,1…0,2 мм рт. ст., рабочее напряжение 400…1100 В, продолжительность процесса до 24 часов.
Антикоррозионное азотирование: в жидких средах состава 40% КСNO + 60% NaCN (тенифер-процесс) при температуре 500…560oС 0,5…2 часа, при этом повышаются усталостная прочность и коррозионная стойкость. Недостатком является этого способа высокая токсичность и стоимость цианистых солей.