Ю. К. Осипов Сибирский государственный индустриальный университет
Вид материала | Документы |
- Формирование комплексного подхода к управлению аудиторским риском, 555.72kb.
- Разработка ресурсосберегающей технологии получения и использования никелевого концентрата, 307.93kb.
- «Восточно-Сибирский государственный технологический университет», 396.41kb.
- Развитие научных основ и разработка совмещенных методов обработки металлов давлением,, 606kb.
- Необходимость изучения терминологии специальности на уроках иностранного языка литовченко, 88.94kb.
- Из опыта проведения компьютерного тестирования по иностранному языку в сибгау куклина, 79.54kb.
- Томск, 11-14 октября 2006 г. Томск Сибирский государственный медицинский университет, 21461.95kb.
- «Сибирский государственный медицинский университет Федерального агентства по здравоохранению, 927.55kb.
- Министерство образования республики беларусь брестский государственный университет, 71.1kb.
- Отчет по исполнению 3 этапа Государственного контракта, 2164.3kb.
В качестве сырьевых компонентов для производства наружных стеновых блоков из пенобетона предложено применить: топкинский портландцемент марки 500 Д0; золу-унос ТЭЦ ЗСМК и пенообразователь – ПБ-2000 ( ТУ 18995.1).
Производство пенобетонных стеновых блоков организовано по резательной конвейерной технологии с тепловой обработкой в туннельных камерах в производственном здании длиной 72м и шириной 24м.
Технологический процесс состоит из следующих участков: участок приемки сырья, дозировки, подготовки и приготовления пенобетонной массы; участок формования, выдержки и разрезки массива; участок тепловой обработки, упаковки и складирования.
Технология изделий из пенобетона состоит из следующих основных технологических операций: хранения сырья; подготовки и подачи сырьевых материалов; приготовление ячеистобетонной смеси; формование массива; выдержки; распалубки; резки массива; тепловой обработки; упаковки и складирования продукции.
В состав технологической линии входит узел приемки и подготовки сырья, приготовления пенобетонной смеси и узел-оборудование формования, выдержки и разрезки массива. Этот комплект состоит из формы, перемещаемой толкателем по рельсам, постов сборки и разборки форм и резательного комплекса для разрезания массива на изделия заданных размеров. Отходы получаемые при разрезке направляются в шламбассейн для повторного использования. Для перемещения форм к камерам и на склад готовой продукции используются электропередаточные тележки. Поддоны с массивами проталкиваются через пропарочные камеры стационарными толкателями. Для механизации работ съем изделий с поддона, перенос форм и поддонов производится специальными захватами.
Цемент и зола хранятся в силосах, доставка материалов осуществляется автоцементовозами. Из силосов цемент и зола винтовыми конвейерами подаются в расходные бункера. Подготовка вяжущего и кремнеземистого компонента заключается в совместной механохимической обработки в стержневом смесителе–активаторе СК20А. Пенообразующую жидкость готовят в смесителе пенообразователя, в который подается вода и концентрат пенообразователя. Раствор в смесителе, поддерживается в автоматическом режиме и постоянно перемешивается и затем подается в работающий пенобетоносмеситель через пеногенератор. После достижения требуемого объема раствора пены в пенобетоносмесителе, производится загрузка цемента и золы. Разливка пенобетонной смеси производится посредством разливного рукава в формы под действием избыточного давления. Залитые формы выдерживаются в течение 4-5 часов в термокамере. После набора распалубочной прочности борта формы снимаются и поддон с массивом проталкивается на резательный комплекс. После резки массива остаются отходы, которые подаются в мешалку, и затем в шламбассейн, а поддон проталкивается на электропередаточную тележку, которая обеспечивает передачу поддона с массивом в одну из трех камер термообработки. Камеры закрыты с торцов подъемными дверями, что обеспечивает в них требуемый режим тепловой обработки.
После тепловой обработки изделия захватом устанавливаются на транспортный поддон, обвязываются упаковочной лентой и автопогрузчиком доставляются на склад готовой продукции. Технологическая схема приведена на рисунке 1.
Принципиальные отличия выбранной схемы производства неавтоклавного пенобетона от других технологий:
- Применена технология производства пенобетона сухой минерализации (непрерывного производства пенобетона) по баротехнологии, в которой предложен процесс перемешивания пены с цементом и золой осуществлять в герметичном бетоносмесителе, допускающим создание избыточного давления при помощи компрессора и подачи пенобетонной смеси с помощью сжатого воздуха к месту заливки массива. Основной объем пор образуется при выходе пеномассы из растворопровода, т.е. пузырьки в пеномассе не разрушаются механически, и следовательно плотность пенобетона не повышается. А также пенобетонная смесь более устойчива к расслоению и возможно применение немолотых кpемнеземистых компонентов (песков, зол электpостанций и т.д.).
- Отходы после резки пенобетонного массива используются повторно;
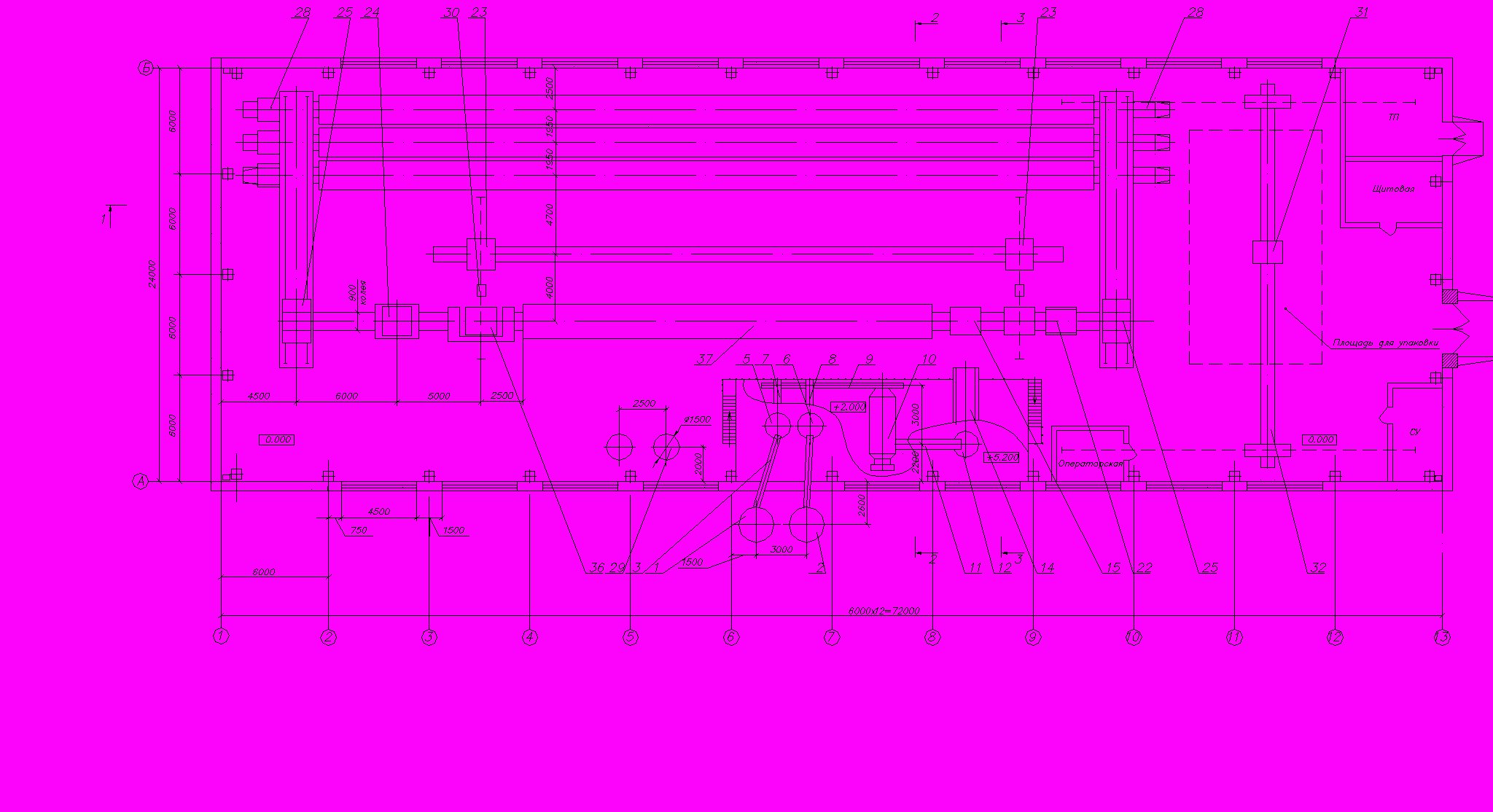
Рис. 1 Технологическая схема производства пенобетонных блоков
- После набора начальной прочности происходит резка массива: продольная и поперечная. Благодаря резке обеспечивается изготовление блоков с высокой точностью геометрических размеров, прямолинейностью граней, отличным качеством поверхностей. Это в свою очередь, позволяет выполнять кладку блоков с использованием клея, что повышает теплоэффективность наружных стен;
- При изготовлении блоков по конвейерной технологии весь производственный процесс полностью механизирован и автоматизирован;
- Применена механохимическая активация сырья.
Экономические показатели проекта: себестоимость блока составляет - 4 рубля. При производительности технологической линии 20000 м3 в год, уровень рентабельности предприятия – 30 %, срок окупаемости затрат на производство составляет 3 года.