Оптимизация количественных параметров переходного комплекса и состава ремонтных позиций при агрегатном методе ремонта локомотивов тема диссертации по экономике, полный текст автореферата
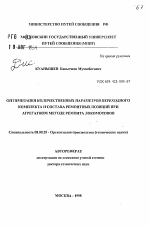
Автореферат
Ученая степень | доктор технических наук |
Автор | Куанышев, Бакытжан Муханбетович |
Место защиты | Москва |
Год | 1998 |
Шифр ВАК РФ | 08.00.28 |
Автореферат диссертации по теме "Оптимизация количественных параметров переходного комплекса и состава ремонтных позиций при агрегатном методе ремонта локомотивов"
МИНИСТЕРСТВО ПУТЕЙ СООБЩЕНИЯ РФ
Р Г 6 мф$ОВСКИИ ГОСУДАРСТВЕННЫЙ УНИВЕРСИТЕТ . л ПУТЕЙ СООБЩЕНИЯ (МНИТ)
1 8-АШЧт-Ч!-
На правах рукописи КУАНЫШЕВ Бакытжаи Муханбетовнч
УДК 629. 423. 004. 67
ОПТИМИЗАЦИЯ КОЛИЧЕСТВЕННЫХ ПАРАМЕТРОВ ПЕРЕХОДНОГО КОМПЛЕКТА II СОСТАВА РЕМОНТНЫХ ПОЗИЦИЙ ПРИ АГРЕГАТНОМ МЕТОДЕ РЕМОНТА ЛОКОМОТИВОВ
Специальность 08.00.28 - Организация производства (технические науки)
АВТОРЕФЕРАТ диссертации на соискание ученой степени доктора технических наук
МОСКВА - 1998
Работа выпонена в Московском государственном университете путей сообщения (МИИТ)
Научный консультант: доктор технических наук, профессор A.B. ГОРСКИЙ
Официальные оппоненты: доктор технических наук, профессор А.Я. Калиниченко доктор технических наук, профессор В.И. Киселев доктор технических наук, профессор Е.С. Павлович
Ведущее предприятие: Департамент локомотивного хозяйства МПС РФ
Защита состоится 18 июня 1998 г. в 14-00 часов на заседании диссертационного совета Д114. 05.11 при Московском государственном университете путей, сообщения (МИИТ) по адресу: 101475 Москва, А-55, ул. Образцова, 15, ауд._4225.
С диссертацией можно ознакомиться в библиотеке университета.
Автореферат разослан {.0^' 1998 года.
Отзыв на автореферат, заверенный печатью, просим направлять по адресу университета.
Ученый секретарь диссертационноЩ
совета д.т.н., профессор
/ A.A. ВОРОБЬЕВ
ОБЩАЯ ХАРАКТЕРИСТИКА РАБОТЫ
АКТУАЛЬНОСТЬ ПРОБЛЕМЫ. В настоящее время на техническое обслуживание и текущие ремонты оборудования локомотивов, для поддержания их работоспособности расходуются достаточно большие средства. В условиях старения локомотивного парка и отсутствии его обновления - затраты на восстановление работоспособности агрегатов будут возрастать.
Так как на процессы эксплуатации локомотивов воздействуют множество случайных факторов, кроме того, условия эксплуатации локомотивов даже в пределах одной дороги имеют существенные отличия, то наработка одноименного оборудования до отказа, реализации контролируемых параметров, характеризующие изменение технического состояния, являются случайными. Разброс ресурса оборудования локомотивов в разных условиях эксплуатации может быть настолько большим, что существенно будут отличаться не только межремонтные пробеги, но и объемы ремонтов, а следовательно, и необходимое количество для выпонения ремонтов технологических линий, станков, оборудования и запчастей.
При решении таких задач важное значение имеет информация, характеризующая техническое состояние локомотивов, содержащаяся в соответствующих учетных формах. Она позволяет организовать производственный процесс на совершенно ином качественном уровне: осуществлять непрерывное слежение за техническим состоянием локомотивов, прогнозировать изменения в будущем и в зависимости от этого производить планово-предупредительные ремонты с соответствующим технологическим обеспечением.
Поэтому для эффективной работы локомотивного хозяйства прогнозирование рациональных параметров потребности технологического оборудования и переходного комплекта агрегатов в депо дожно осуществляться на основе информационной оценки надежности оборудования в эксплуатации совместно с
задачами выбора оптимальной стратегии ремонта и установления оптимальных технических требований при агрегатном методе ремонта локомотивов.
ЦЕЛЬ РАБОТЫ заключается в выявлении, формулировании и решении проблемы оптимизации параметров технологических процессов ремонта оборудования локомотивов - числа ремонтных позиций и объема переходного комплекта с учетом множества случайных факторов, оказывающих существенное влияние на процесс в реальных условиях эксплуатации. Для этого из всего многообразия свойств агрегатов были выделены две основные компоненты: их функциональность и отношения в системе эксплуатации, технического обслуживания и ремонта локомотивов.
Достижение поставленной цели осуществляется решением следующих основных задач:
- выбор целевой функции и критерия оптимизации параметров технологического процесса ремонта оборудования локомотивов;
- построение аналитической модели определения оптимальных параметров технологического процесса восстановления работоспособности оборудования локомотивов, которая является как бы эталоном при построении статистической модели;
- разработка статистической модели и агоритма определения рационального числа ремонтных позиций и объема переходного запаса оборудования при агрегатном методе ремонта локомотивов с учетом множества факторов, имеющих место в реальных условиях эксплуатации;
- получение одинаковых результатов при расчетах на аналитической и статистической моделях при одних и тех же исходных, что является критерием их достоверности;
- реализация имитационной модели на ЭВМ и определение оптимальных параметров технологического процесса ремонта агрегатов методами математического планирования эксперимента.
В диссертации решаются конкретные задачи расчета рациональных параметров технологического процесса на основании изучения процессов изнашивания и наработок между отказами бандажей колесных пар тепловозов серии 2ТЭ10.
МЕТОДИКА ИССЛЕДОВАНИЯ. Решение поставленных задач выпонено с единых методологических позиций, основой которой является применение вероятностно-статистических методов: теории вероятностей, надежности, массового обслуживания, статистических гипотез, имитационного моделирования на ЭВМ, а также математических методов планирования эксперимента.
НАУЧНАЯ НОВИЗНА РАБОТЫ состоит в решении проблемы оптимизации параметров технологического процесса ремонта агрегатов методами имитационного моделирования, реализуемого на ЭВМ, которое с высокой степенью точности отражает реальные процессы восстановления работоспособности оборудования локомотивов с учетом фактических законов распределения наработок, продожительности простоя на ремонтных операциях, множества, поступающих на обслуживание потоков агрегатов и других факторов, имеющих место в реальных условиях эксплуатации, и позволяющего проводить имитационные эксперименты по определению рационального числа ремонтных позиций и объема переходного комплекта запасного оборудования при агрегатном методе ремонта локомотивов.
ПРАКТИЧЕСКАЯ ЦЕННОСТЬ работы заключается в создании методики оптимизации параметров технологического процесса восстановления работоспособности агрегатов с учетом реальных условий ремонтного производства и эксплуатации локомотивов с внедрением результатов работы при модернизации технологической линии ремонта колесных пар со сменой бандажей в локомотивном депо Казалинск.
АПРОБАЦИЯ И РЕАЛИЗАЦИЯ РАБОТЫ. Основные положения и результаты диссертационной работы докладывались: на Всесоюзной научно-
технической конференции (Брянск, 1991г.), на Всесоюзной научно-технической конференции Состояние и перспективы развития электровозостроения в стране (Новочеркасск, 1991г.), на 1-й и 2-й международной научно-технической конференции ((Актуальные проблемы развития железнодорожного транспорта (Москва, 1994, 1996 гг.), на 6-й международной научно-технической конференции ((Проблемы развития локомотивостроения (Москва, 1996 г.), на 7-й международной научно-технической конференции Проблемы развития рельсового транспорта (Луганск,1997 г.), на первом международном симпозиуме Энергоснабжение, качество электроэнергии, электромагнитная совместимость на железнодорожном транспорте (Москва, 1997 г.), на совместном заседании кафедр Подвижной состав и ((Безопасность жизнедеятельности Казахской академии транспорта и коммуникаций (Аматы, 1997 г.), на научно-техническом семинаре кафедры Электрическая тяга МИИТа, секция Эксплуатация, надежность и ремонт ЭПС (Москва, 1998 г.), заседаниях кафедры Электрическая тяга (1996, 1998 гг.). Практические рекомендации работы внедрены в локомотивном депо Казалинск и использованы при разработке следующих нормативных документов:
1. Указания №22Н от 29.04.96г. "Об улучшении технического состояния тепловозного парка";
2. Временных дорожных норм расхода запасных частей, материалов и ГСМ при ремонте тепловозов типа ТЭ10.
Материалы диссертации использованы в учебном пособии Система ремонта электроподвижного состава и ее оптимизация. Учебное пособие., опубликованном совместно с профессором Горским A.B. и профессором Воробьевым A.A. Результаты работы также используются в учебном процессе в двух методических руководствах к выпонению лабораторных работ.
Материалы диссертации опубликованы в 24 статьях.
ОБЪЕМ И СТРУКТУРА РАБОТЫ. Диссертация состоит из введения,
шести глав, заключения, списка литературы, включающего 223 наименования и восьми приложений. Она содержит 276 страниц машинописного текста, 28 таблиц и 108 рисунков.
СОДЕРЖАНИЕ РАБОТЫ
Во введении обоснована актуальность выбранной темы диссертации и приведена краткая аннотация работы.
В первой главе на основе анализа современного состояния вопроса сформулированы цели и задачи исследования.
Проблема совершенствования системы ремонта локомотивов, повышения надежности их оборудования, выбора рациональных параметров технологических процессов ремонта агрегатов является актуальной. Большой вклад в ее решение внесли работы Артюхова В .Я., Воробьева A.A., Горского А.В, Капранова H.H., Никифорова Б.Д., Озембловского В.Ч., Павловича Е.С., Подшивалова Н.Б., Риделя Э.Э., Стрельникова В Т., Тартаковского Э.Д., Исаева И.П., Киселева В.И., Козырева В.А., Четвергова В.А. и других ученых.
Проблеме выбора оптимальных технологических средств и запасных частей к радиоэлектронной аппаратуре, автомобилям, тракторам, самолетам, морским судам и сельскохозяйственным машинам посвящены работы С.К.Агзамова, И.Асатова, А.М.Андронова, М.Н.Бедняка, А.Ф.Вокова, Б.Геронимуса, И.В.Красонтовича, Э.Л.Лайкама, И.А.Луйка, В.М.Михлина, А.И.Нисневича, Л.Г.Осьминина, Н.Н.Савватеева, А.И.Селиванова, Х.М.Тахтамышева, А.В.Тураева, Э.О.Тятге, В.И.Черникова, А.М.Шейнина, Н.А.Шишонка и других исследователей
Проведенный анализ исследований в различных отраслях промышленности и транспорта показал их деление на две группы, которые в основном рассматриваются отдельно друг от друга:
- работы по оптимизации запаса и нормированию расхода запасных час-
тей к различному оборудованию, аппаратуре, машинам и другим транспортным средствам;
- работы, выпоненные по оптимизации выбора технологических систем (например: числа технологических линий, морских причалов, перронных стоянок самолетов, средств аэродромной механизации и т.д.).
Проведенный анализ работ по оптимизации параметров технологического оборудования и переходного запаса агрегатов показывает, что при решении задач используются либо детерминированные модели или же модели, в которых вероятностные оценки осуществляются в упрощенном варианте на основе простейших потоков.
Данная работа является дальнейшим развитием исследований по оптимизации параметров технологического процесса ремонта оборудования тягового подвижного состава. От ранее выпоненных работ отличается тем, что впервые определение рациональных параметров технологического процесса осуществляется с единых позиций выбора оптимального числа ремонтных позиций и запаса агрегатов, обеспечивающих снижение потерь от простоя локомотивов в ремонте.
Определение объемов ремонта агрегатов осуществляется на основе фактического ресурса оборудования локомотивов, определенного для конкретных условий эксплуатации.
На практике же ремонтное производство является сложнейшим механизмом на который воздействует множество факторов. Поэтому при решении оптимизированных задач, направленных на его совершенствование, необходимо разрабатывать модели, в которых учитывались все основные факторы и вероятностные характеристики с учётом реальных законов распределения и функциональных зависимостей параметров системы.
Оптимизация параметров технологического процесса осуществлена методами планирования эксперимента на имитационных моделях, реализуемых на
Во второй главе разработана математическая модель агрегатного метода ремонта оборудования локомотивов, которая представляет собой многоканальную разомкнутую систему массового обслуживания с очередью и запасом агрегатов (рис.1).
Рис. 1. Модель системы восстановления работоспособности оборудования при агрегатном методе ремонта
При рассмотрении таких систем определяют различные показатели эффективности обслуживающей системы. Необходимо, например знать, какова вероятность того, что все обслуживающие ремонтные позиции заняты. Для поной характеристики образующейся из отказавших агрегатов очереди необходимо знать закон распределения времени ожидания начала восстановления работоспособности. Во всех случаях необходимо знать вероятность того, что в системе находится к - отказавших агрегатов, как ремонтирующихся, так и ожидающих ремонта, что позволяет определить такие важные показатели, как математическое ожидание числа простаивающих ремонтных позиций - Мр, математическое ожидание числа агрегатов, простаивающих в запасе - Мз, математическое ожидание числа простаивающих агрегатов в ожидании ремонта - Ма, математическое ожидание числа простаивающих локомотивов из-за недостатка агрегатов - Мл-
Критерием эффективности такой системы при определении рационального числа ремонтных позиций и запаса агрегатов выбраны суммарные удельные затраты от простоя ремонтных позиций, от простоя агрегатов, находящихся в запасе, от простоя агрегатов в ожидании ремонта, от простоя локомотивов из-за недостатка агрегатов.
г = Мр + к,М3 ~к}Ма + кМл, (1)
где к]=Сз Ср - коэффициент относительных потерь от хранения агрегатов в запасе;
к2=Са Ср - коэффициент относительных потерь от простоя агрегатов в ожидании ремонта;
кз=Сл' Ср - коэффициент относительных потерь от простоя локомотивов из-за нехватки агрегатов;
Ср, Сз, СД, Сл - соответственно потери в от простоя ремонтной позиции, от хранения агрегатов в запасе, от простоя агрегатов в ожидании ремонта, от простоя локомотивов из-за нехватки агрегатов.
Расчеты оптимальных параметров технологического процесса осуществлены на основе теории марковских процессов. Граф-переходов системы, представленной на рис. 1 при различных соотношениях числа однотипных работающих агрегатов Ы, числа запасных агрегатов 5, числа ремонтных позиций на которых восстанавливаются агрегаты и, числа отказавших агрегатов к приведен на рис.2.
При пуассоновском потоке поступающих на ремонт агрегатов и экспоненциальном распределении продожительности восстановления были получены системы: конечно-разностных уравнений, дифференциальных уравнений Комогорова. Для установившегося режима, где
1шРк(0 = Рк (2)
система дифференциальных уравнений преобразуется в систему агебраических без правой части:
X 1-СЯХ+к(1)Л1
(к+1)цД1
1-(М+пр)А1
] Л'ДГ
прМ / (,\'+.Ч-к)Л1
Рис 2. Граф-переходов при к<п (а), при п<к<Б(б), при 5<Л<А'+5(в), при А-=Л'+5 (г)
1-пАР0+^1 = 0; к = 0
________ ___________________________________ _______ 1Ш Рк_1 - (N1 +(*) Рк+(к+1)рР к~г 0; 1_______ _______ ______________________________________ к <п
\ИХРк., - (ИХ -уш) Рк+п]иР /+=0; 1_______ ____________________ _________________ ..... ....
1 [Ш8-(к-1)]М>1.1 - [ф!+8-к)Л+п^)]Рк + п/иР -1=0; 1___________________________________________________________________ 5 < к <N-5
I АРл'^-г Р.у+5 =0; к = Г+5
Решением системы уравнений получены выражения для вероятностей:
= при к<п (4)
= при г)<к<Б (5)
р(3) = -а Р при5 <к (6)
к (И +5-к)\пк~"п\ 0
Здесь а-X/ц., где Я - интенсивность отказов, Л = 1 /То',
ц - интенсивность восстановления агрегата, /л = 1 /Те.
Здесь То - средняя наработка на отказ, Т,- среднее время восстановления агрегата.
Вероятность Ро определяется из условия Рк = 1.
При известных вероятностях состояний среднее число простаивающих ремонтных позиций Мр, среднее число агрегатов, находящихся в запасе Мз, среднее число простаивающих агрегатов в ожидании ремонта Ма, среднее число простаивающих локомотивов из-за недостатка агрегатов Мл записываются в
следующем виде:
А-0 Л-0
м. = i(k- п)рр + (* - л1';Ч7 = (* - (7)
Так как в выражения вероятностей нахождения системы в каждом из рассматриваемых состояний входят значения факториалов больших чисел и показательных функций больших степеней, что при расчетах на ЭВМ приводит к перепонению разрядной сетки, поэтому были использованы экспоненциальные преобразования формулы Стерлинга и показательных функций для реализации расчетов на ЭВМ.
Задаваясь различными значениями п и рассчитаны зависимости 2(г\) и 2(5) , которые имеют ярко выраженный минимум, то есть позволяют определить рациональное число агрегатов переходного запаса и число ремонтных позиций при известном объеме ремонта. Это связано с тем, что с увеличением числа ремонтных позиций уменьшаются потери из-за простоя числа отказавших агрегатов в очереди на обслуживание, в то же время увеличиваются потери из-за простоя ремонтных позиций. Аналогично, с увеличением числа запасных агрегатов уменьшаются потери из-за простоя локомотива по причине отсутствия агрегатов для замены отказавших. С другой стороны с увеличением числа запасных агрегатов увеличиваются потерн на их хранение. Таким образом функция суммарных удельных потерь имеет минимальное значение, которому соответствует оптимальное значение числа ремонтных позиций и агрегатов переходного запаса. Результаты расчета представлены в виде графика 1 (рис.3).
Рассматриваемая модель применима в случае если:
- наработка на отказ и время восстановления имеют экспоненциальный закон распределения;
- в систему обслуживания поступает один поток отказавших агрегатов с
одним и тем же законом и параметром распределения наработки на отказ;
- процесс восстановления рассматривается как единый, который не разбивается на отдельные операции.
г=50; Л= 1 103; р. = 7 10'2.
т=нТ 5(7=2 У/Чг2
Ио=2
О 1 2 ремонтные
позиции
1-аналитический метод; 2-статистаческое моделирование на ЭВМ Рис. 3. Результаты расчетов на аналитической и статистической моделях
Эти недостатки аналитической модели не позволяют учитывать множества факторов, которые проявляются в реальных условиях ремонтного производства.
В главе 3 разработана статистическая модель марковского процесса отказов и восстановлений оборудования при агрегатном методе ремонта локомотивов. Для моделирования последовательности случайных чисел на ЭВМ использован метод их формирования с помощью рекуррентных соотношений.
На основании предложенных принципов моделирования процесса отказов, обслуживания и замены отказавших агрегатов разработан агоритм имитационного моделирования. Схема агоритма представлена на рис.4.
В блоке 1 осуществляется ввод исходных данных: периода моделирования Тм, числа работающих агрегатов Ы, числа технологических Х позиций п и числа запасных агрегатов 5, а также вида закона распределения и числовых ха-
рактеристик наработки до отказа агрегата и времени восстановления, затрат от простоя ремонтных позиций и агрегатов.
В блоке 2 задаются начальные условия, обнуляются переменные, используемые для накопления сумм. Моделирование времени безотказной работы ка-
Ввод исходных данных
Подготовка счетчиков, сукшаторов задания начальных условий
Моделирование времени безотказной
работы агрегата 7, Момент отказа /-го агрегата г, - /,-- г),
Цикл по
Момент гост)плеши агрегата га Цикл по
ремонт 1,=пип{1], 1}, {,..., 1
Выбор позиции дтя ремонта А-го агрегата г*=гят{г;, Г;, т3..... Цикл по 1<п
Моделирование времени ремонта агрегата 0
Моделирование времени безотказной работы г/к
Выбор агрегата из запаса Т, - тш{Г;, 7г, Тз.....Ы
Цикл по
Рис. 4. Блок-схема статистического моделирования
ждого из N агрегатов и моментов их отказов осуществляется в блоке 3.
Блоком 4 вычисляется момент поступления на ремонт к-то агрегата, который отказал раньше всех остальных, а в блоке 5 определяетсяу-я ремонтная позиция, освободившаяся раньше других. Моделирование продожительности восстановления отказавшего агрегата осуществляется в блоке 6. Если отказ агрегата произошел раньше времени освобождения у'-й ремонтной позиции (блок 7), то в блоке 8 вычисляется время ожидания начала восстановления к-го агрегата
Iож.к = Ъ - 4, (8)
где Т) - время освобождения у'-й ремонтной позиции; - момент отказа к-го агрегата.
В блоке 9 определяется момент времени освобождения у'-й ремонтной по-
зиции после восстановления агрегата.
В блоке 10 накапливается суммарное время простоя агрегатов в ожидании ремонта. Если же агрегат не простаивает в ожидании восстановления (условие блока 7 не выпоняется), то в блоке 11 вычисляется продожительность простоя >й ремонтной позиции в ожидании поступления на
восстановление очередного отказавшего агрегата, а в блоке 12 вычисляется момент освобождения у-й позиции после окончания восстановления к-го агрегата:
г, = П- - в, (9)
где Ь - момент отказа к-го агрегата;
О - продожительность восстановления к-го агрегата. Накопление суммарного времени простоя ремонтных позиций происходит в блоке 13.
В блоке 14 моделируется наработка до очередного отказа к-то агрегата. А в блоке 15 определяется номер агрегата с самым ранним временем постановки на хранение ТК для замены отказавшего агрегата.
Если агрегат был поставлен на хранение раньше момента отказа к-то агрегата (условие блока 16), то в блоке 17 вычисляется продожительность хранения этого агрегата:
, - Ь - 'Г, (10)
В блоке 18 определяется момент времени очередного отказа к-то агрегата, а в блоке 19 накапливается суммарное время хранения агрегатов в запасе.
Если условие блока 16 не выпоняется, то управление от него передается блоку 20, где вычисляется время задержки выдачи работоспособного агрегата в эксплуатацию
и^Ъ-Ь, (11)
которое накапливается в течение периода моделирования в блоке 21. Момент очередного отказа к-\о агрегата определяется в блоке 22.
Момент постановки отремонтированного агрегата на хранение определяется блоком 23.
Цикл моделирования повторяется до тех пор, пока момент отказа очередного агрегата будет меньше заданного периода моделирования Тм.
После завершения процесса моделирования осуществляется расчет суммарных удельных затрат на ремонт и хранение агрегатов в блоке 25.
Средние числа: агрегатов, простаивающих в ожидании ремонта, простаивающих ремонтных позиций, агрегатов, находящихся в запасе, простаивающих локомотивов, из-за нехватки агрегатов в запасе определяются по формулам:
Л'л Л, V, Л'л
где ТЛ1 - период моделирования;
Х'яч, - суммарное время простоя агрегата в ожидании ремонта.
Х'яр, - суммарное время простоя ремонтных позиций.
2'га, " суммарное время хранения агрегатов в запасе.
- суммарное время простоя локомотивов из-за нехватки агрегатов.
По минимуму целевой функции (1) определяется рациональное число ремонтных позиций и целесообразное число агрегатов в запасе.
Преимуществом разработанной статистической модели по сравнению с аналитической является то, что она позволяет реализовать процессы, происходящие в реальных условиях с наибольшей степенью достоверности, т.е. максимально приблизить моделированные процессы к аналогичным, происходящим на практике. Таким образом обеспечить адекватность модели реальным процессам, реализуемым в эксплуатации. Это, в свою очередь, позволит получать дос-
товерные результаты с использованием этой модели.
Чтобы убедиться в правильности построения разработанной статистической модели проверялась ее адекватность разработанной ранее аналитической модели.
Эта проверка выпонялась сравнением выходных параметров, полученных в результате расчета по аналитической и статистической моделям, описывающим один и тот же процесс при одних и тех же данных и допущениях
Результаты расчета показали, что при выбранных периодах моделирования полученные результаты (график 2 рис.3) отличаются незначимо, т.е. соответствующие средние значения времен: простоя ремонтных позиций, простоя агрегатов в ожидании восстановления, хранения агрегатов в запасе и простоя локомотивов из-за отсутствия агрегатов в переходном запасе и их дисперсии несущественно отличаются в различных опытах (рис.3).
Это означает, что при построении статистической модели были учтены все основные факторы, которые играют существенную роль в формировании показателей эффективности функционирования аналитической модели.
Однако, как в аналитической, так и в подобной ей статистической модели, не отражен ряд специфических моментов, характерных для реального процесса отказов и восстановления оборудования локомотивов при агрегатном методе ремонта.
В четвертой главе изложены результаты статистического моделирования с учетом реального характера процесса отказов и восстановления оборудования при агрегатном методе ремонта локомотивов.
Построенная статистическая модель процесса отказов и восстановления оборудования агрегатным методом основана на тех же допущениях, что и аналитическая модель: о пуассоновском распределешга потока агрегатов, поступающих на восстановление; об экспоненциальном распределении времени восстановления агрегатов; о моделировании процесса восстановления без разделе-
ния на отдельные технологические операции.
Однако положенные в основу модели допущения далеко не в поной мере отражают некоторые существенные особенности процесса восстановления агрегатов локомотивов, поэтому сама модель нуждается в определенной доработке с целью учета этих особенностей.
В частности доработанная статистическая модель дожна воспроизводить процессы восстановления агрегатов с учетом фактических законов распределения наработок, продожительности простоя на ремонтных операциях, множества, поступающих на обслуживание потоков агрегатов и других факторов, имеющих место в реальных условиях эксплуатации.
Использование такой статистической модели позволит максимально приблизить имитационный эксперимент к условиям реальной эксплуатации локомотивов и их оборудования и получить достоверные и практически значимые результаты.
Чтобы в процессе доработки не нарушить структуру агоритма моделирования и логические связи, достаточно отработанные в уже построенной модели (рис.4), целесообразно использовать так называемый модульный принцип построения агоритма. Для этого он разбивается на отдельные блоки, так называемые модули, каждый из которых выпоняет впоне определенные функции, при этом логические взаимосвязи между всеми модулями остаются теми же, что и в исходной модели.
При доработке агоритма, изменения вносятся только в в отдельный модуль, представляющий собой некоторую подпрограмму, которая отрабатывается изолированно от остальных модулей до тех пор, пока ее выходные параметры не будут удовлетворять поставленным требованиям. Затем таким же образом последовательно вносятся изменения в остальные модули, а при необходимости разрабатывается новые модули, которые встраиваются в уже отработанный агоритм, не меняя ранее задействованных логических связей.
Такая процедура позволяет постепенно шаг за шагом приближать разработанную модель к реальным условиям функционирования моделируемой системы. При этом на каждом шаге осуществляется контроль выходных параметров как корректируемого модуля, так и всей модели, что исключает возможность внесения ошибок.
В эксплуатации возникает два потока поступающих на ремонт агрегатов: на плановые ремонты в результате естественного износа агрегатов в процессе эксплу атации и потока неплановых - в результате отказов агрегатов. Кроме того каждый из рассматриваемых потоков в свою очередь складывается из нескольких потоков агрегатов, поступающих на восстановление из различных локомотивных депо дороги. Поэтому каждый из этих потоков имеет свои статистические характеристики.
Для каждого агрегата моделируются, исходя из вида закона распределения наработки до планового ремонта и её числовых характеристик, сроки постановки на плановый ремонт.
Исходя из экспоненциального закона распределения наработки на отказ определяется вероятность постановки этого агрегата на неплановый ремонт в рассматриваемом межремонтном периоде в интервале наработок до планового ремонта. В случае отказа агрегата определяется наработка до этого отказа. Поэтому статистическая модель дожна содержать модуль, генерирующий два потока агрегатов, поступающих на плановые и неплановые ремонты, при этом дожна учитываться неординарность первого потока.
Схема агоритма моделирования наработки агрегата до планового и непланового ремонтов показана на рис.5. Блоком 1 из основной программы передаются переменные: номер агрегата /, вид закона распределения и числовые характеристики законов распределения. Наработка агрегата до планового ремонта Г/7, генерируется в блоке 2.
В блоке 3 вычисляется вероятность выпонения непланового ремонта в
периоде /д до планового ремонта. В блоке 4 моделируется равномерно распределенная величина у! - критическое значение вероятности. Если вероятность отказа больше критического значения у! (условие блока 5), то агрегату будет произведен очередной неплановый ремонт. Наработка до непланового ремонта вычисляется в блоке 7. Для этого в блоке 6 вычисляется равномерно распределенная случайная величина у2. Затем управление передается на выход в основную программу.
Если условие блока 5 не выпоняется, то в блоке 8 наработке (щ присваивается значение периода моделирования Тм. После чего управление передается на выход из подпрограммы в основную программу (блок 9).
Моделирование ^[0,1]
'я,= т. I
Малелирование у
Наработка до ногвноиж) ремонта 'я. = - Г*п,
Рис.5. Схема агоритма моделирования потока плановых и неплановых ремонтов
В практике работы железных дорог очень часто ремонт одноименного оборудования локомотивов, приписанных к разным депо, сосредоточен в одном ремонтном пункте. Поскольку условия эксплуатации локомотивов на разных участках обслуживания весьма существенно отличается друг от друга, то, по крайней мере, числовые характеристики распределений межремонтных наработок агрегатов, поступающих из разных депо, также являются различными. Следовательно доработанный вариант модели дожен содержать модуль, генерирующий потоки агрегатов из различных локомотивных депо, и формирующий из этих потоков один - поступающий в пункт, где осуществляется восстановление агрегатов. Агоритм моделирования потока поступления агрегатов из различных локомотивных депо на плановые и неплановые ремонты представлен на рис.6.
Блоком 1 в подпрограмму вводятся параметры из основной программы.
Блоки 2, 13 и 14 организуют цикл вычислений по числу локомотивных депо N. В свою очередь блоками 3, 11 и 12 организуется цикл по числу локомотивов л,(/)у-го локомотивного депо.
Кроме того в блоке 3 наименьшим значениям времени поступления на плановые и неплановые ремонты присваиваются моменты поступлений на плановые ремонты агрегатов первого локомотива и на неплановый ремонт его первого агрегата. Блоками 4 и 5 осуществляется выбор локомотива и запоминание раннего времени постановки на плановый ремонт.
Цикл определения агрегата с наиболее ранним временем постановки 1-го локомотивау-го локомотивного депо на неплановый ремонт осуществляется блоками 6-10.
После выбора локомотива, раньше других поступивших на плановый ремонт (/птт) и агрегата, раньше других поступившего на неплановый ремонт (///ДДД) осуществляется выход из подпрограммы в основную программу блоком 15.
Рис.6. Схема агоритма моделирования потока агрегатов, поступающих на ремонт из различных депо
Поскольку в исходной статистической модели (рис.4) на восстановление поступает ординарный поток агрегатов, то и.замена их работоспособными агрегатами из переходного комплекта осуществляется поштучно. В доработанном
варианте модели дожна быть предусмотрена возможность одновременного изъятия из переходного комплекта нескольких агрегатов для замены всех однотипных агрегатов локомотива, поступившего на плановый ремонт. При этом дожна быть учтена возможность возникновения ситуации, когда число содержащихся в запасе агрегатов недостаточно для замены поного комплекта агрегатов одного локомотива. В этом случае локомотив простаивает в ожидании окончания восстановления недостающих для поного комплекта агрегатов. В соответствии с этим разработан агоритм процесса замены отказавшего оборудования работоспособными агрегатами из переходного запаса.
Блок-схема представлена на рис7.
Блоком 1 в подпрограмму передаются все значения переменных, необходимых для моделирования процесса. Если локомотив поступает на плановый ремонт, то в блоке 2 счетчик числа комплектов агрегатов, поступивших на плановый ремонт увеличивается на единицу и фиксируется момент 1(Пр) поступления этого комплекта агрегатов (локомотива) на ремонт.
Если в переходном запасе недостаточно агрегатов 5, для замены поступившего на ремонт комплекта (условие блока 3), то управление передается на выход из этой подпрограммы (блок 14) в раздел программы, где осуществляется продожение моделирования технологического процесса восстановления агрегатов. При накоплении в запасе щ числа агрегатов, необходимых для замены поступивших на ремонт, блоками 4-8 осуществляется изъятие из переходного запаса п0 агрегатов. Для этого в блоке 4 определяются п0 агрегатов находящихся в запасе, которые раньше других поступили на хранение Тт,Д. Если локомотив простаивал в ожидании накопления агрегатов в переходном запасе (условие блока 5), то в блоке 6 накапливается сумма времени простоя локомотива. В блоке 7 счетчик числа локомотивов, простаивающих в ожидании переходных комплектов агрегатов, уменьшается на единицу, а число агрегатов в запасе, соответственно, уменьшается на число однотипных агрегатов на локомотиве.
Определение моментов времени поступления на хранение оставшихся агрегатов осуществляется в блоке 8. Блоками 9-13 осуществляется цикл вычисле-
Рис.7. Агоритм процесса замены отказавшего оборудования работоспособными агрегатами из переходного запаса
ния и накопления суммарного времени нахождения агрегатов на хранении. Выход из подпрограммы в основную программу осуществляется в блоке 14.
В исходном варианте моделирование восстановления работоспособности агрегатов осуществляется как бы на единой технологической линии без учета деления ее на отдельные операции. Для того чтобы реализовать пооперационный технологический процесс с целью выбора оптимальной численности технологического оборудования на каждой операции и переходного запаса агрегатов модель требует некоторого совершенствования, позволяющего моделировать последовательность восстановления агрегатов на отдельных операциях и учитывать множество потоков поступления агрегатов, каждый из которых имеет свои параметры.
Любой технологический процесс может быть представлен в виде сетевого графика. Предположим, что некоторая работа кг опирается на работы гк, ]к, 1к, то есть она не может начаться раньше, чем закончится самая продожительная из тех работ, на которые она опирается.
Технологические линии в общем случае могут содержать несколько паралельных позиций для выпонения каждой работы, например >Ьк для выпонения работы к, п1к для выпонения работы ]к и т.д. Продожительность каждой работы является случайной величиной, поностью характеризуемой функцией ее распределения. При известном виде функции распределения для моделирования продожительности работы достаточно задать ее числовые характеристики, например т и а при нормальном законе распределения.
Для моделирования технологического процесса на ЭВМ наиболее удобна матричная форма представления сетевого графика, его временных параметров и численности ремонтных позиций на каждой отдельной операции (работы).
Например, при нормальном законе распределения продожительности работ для ввода в ЭВМ сетевого графика, необходимо и достаточно ввести в запоминающее устройство три матрицы:
средних значений продожительности технологических операций
(работ);
- дисперсий продожительности работ;
- численности паралельных позиций для выпонения каждой технологической операции.
Для того чтобы смоделировать технологический процесс восстановления работоспособности агрегата, необходимо определить моменты начала и окончания каждой технологической операции, учитывая, что каждая из них выпоняется на нескольких ремонтных позициях.
Агрегат готов к переходу по технологической цепочке для выпонения следующей ремонтной операции, как только закончится выпонение предыдущей операции на любой из ремонтных позиций, т.е.
где т1к - момент окончания технологической операции к на одной из ремонтных позиций.
Агрегаты у которых технологические операции к, к, 1к заканчиваются раньше момента ^простаивают в ожидании этого момента
где <Ркг- момент готовности агрегата к выпонению работы кг.
Работа кг может начаться в момент щг только в том случае, если к этому моменту освободится хотя бы одна из ремонтных позиций, выпоняющих операцию кг.
Момент освобождения одной из ремонтных позиций, выпоняющих операцию кг, определяется из соотношения
'вас* - Фкг Ч
Здесь с - номер той ремонтной позиции, которая освобождается раньше других.
то в ожидании поступления агрегата простаивает ремонтная позиция, освободившаяся раньше других, т.е. с номером с.
В процессе моделирования накапливаются суммы Вож и ЯДр - времени межоперационного ожидания агрегатов и времени простоя ремонтных позиций, необходимые для расчета числовых характеристик распределений числа агрегатов, ожидающих ремонта, и числа простаивающих ремонтных позиций с целью оптимизации объема переходного комплекта агрегатов и необходимого числа ремонтных позиций для выпонения каждой ремонтной операции.
На основании изложенных принципов построен агоритм пооперационного моделирования технологического процесса ремонта колесных пар со сменой бандажей (рис.8).
В блоке 1 из модуля, формирующего поток агрегатов, поступающих на ремонт из различных локомотивных депо, задается момент поступления очередной партии агрегатов ь и ее объем п. Если агрегат поступает на неплановый ремонт, то п = 1; если на плановый - п - п о - числу одноименных агрегатов, установленных на одном локомотиве. При моделировании технологического процесса ремонта колесных пар тепловоза 2ТЭ10Л,В,М значения п0 = 12. Блоком 2 задается начальное значение счетчика числа агрегатов, поступающих на технологическую линию, номер первой операции которой задается блоком 3. (/= 1).
В блоке 4 фиксируется (р, - момент готовности агрегата к выпонению первой ремонтной операции и блоке 5 определяется номер /-ой ремонтной позиции (1-27 п/), которая раньше других освобождается при выпонении /-ой ремонтной операции, а также момент ее освобождения ту .
/Ввод данных из основной / программы - 1ь п /
1 Т1} = Ш1П^Г,ьГ,г,. Г,. ' Цша
1<У < п,
д. - г
<Р.= Цикл 1<у < я,
Х5 1
/ = т, щ ~<рщ
5 - 5 * 1; Ш = я
I г-Л/ |
Рис. 8. Агоритм пооперационного моделирования технологического процесса ремонта колесных пар
Блоком 6 передается управление к модулю, в котором генерируется реализация случайной величины 0, - продожительности /-ой ремонтной операции в соответствии с ее законом распределения и числовыми характеристиками, заданными векторами ТП и а.
Блоком 7 задается номер следующей технологической операции.
Если агрегат готов к выпонению /-ой ремонтной операции раньше, чем освободится одна из ремонтных позиций, которая эту операцию выпоняет (соблюдается условие блока 8), то управление передается к блоку 9, в котором вычисляется время ожидания агрегатом начала /-ой ремонтной операции - ^ и накапливается суммарное время ожидания Вож.
Момент начала /-ой ремонтной операции на у-ой ремонтной позиции Ду задается блоком 11.
В случае невыпонения условия блока 8, когда у-ая ремонтная позиция освобождается раньше, чем агрегат окажется готовым к началу /-ой технологической операции, управление передается к блоку 10, в котором вычисляется время простояу-ой ремонтной позиции <р, - и накапливается суммарное время
простоя Л Др. Далее блоком 12 задается Д, - момент начала г-ой ремонтной операции на у'-ой ремонтной позиции, а момент окончания этой операции определяется в блоке 13.
В блоке 14 определяется момент готовности агрегата к выпонению следующей ремонтной операции.
В блоке 15 фиксируется номер г следующей ремонтной операции и момент <р, - готовности агрегата к ее выпонению.
Если выпонены не все ремонтные операции (выпоняется условие блока 16), то управление передается к блоку 5 для определения номера ремонтной позиции, которая раньше других освободится для выпонения очередной ремонтной операции.
После окончания цикла, задаваемого блоком 16, т.е. после окончания технологического процесса ремонта агрегата, управление передается к блоку 17, в котором счетчик числа агрегатов, находящихся в переходном комплекте, 5 увеличивается на единицу и фиксируется момент поступления агрегата в переходной комплект 71(5).
В блоке 18 счетчик г числа агрегатов, поступающих на ремонт, увеличивается на единицу и, если не все поступившие агрегаты отремонтированы, то блоком 19 организуется цикл для моделирования технологического процесса ремонта следующего агрегата.
После восстановления всех п агрегатов, поступивших на ремонт в данной партии, управление передается в основную программу для выпонения очередного модуля.
Разработка и апробация модели осуществлялась на примере ремонта колесных пар тепловозов серии 2ТЭ10 двенадцати локомотивных депо Западной железной дороги (бывшей Западно-Казахстанской). Ремонт колесных пар со сменой бандажей по дороге осуществляется, в локомотивном депо Казалинск, специализирующемся на этом виде ремонта.
Средние значения времени ремонта колесной пары, затрачиваемого на каждой из операций технологического процесса, и его среднеквадратические отклонения, использованные при пооперационном моделировании, представлены в таблице 1.
Таблица. 1.
Числовые характеристики распределения продожительности _выпонения операций _
опера- Краткое содержание Числовые характе-
ции операции ристики, мин
х. т(1) ЫО
1 Осмотр колесной пары 30 2.7
2 Очистка и мойка. Проверка наличия клейм и знаков 42 3.696
3 Дефектоскопия оси и зубчатого колеса 28 2.716
4 Подготовка к снятию бандажей 32 2.94
5 Снятие бандажей 135 14 85
6 Обработка колесных центров 270 25.92
7 Проверка колесных центров 28 2.548
8 Ремонт колесных центров 28 2.632
9 Подборка бандажей 28 2.576
10 Насадка бандажей на колесные центры 210 23 94
И Контроль размеров и нанесение контрольных отметок на бандажи и колесные центры 12 1.056
12 Обточка бандажей 123 11.808
13 Контроль размеров и окраска 12 1.092
Моделирование процесса ремонта колесных пар осуществляется с определенным набором числа ремонтных позиций и объема переходного комплекта запасных агрегатов. Цикл моделирования процесса осуществляется блоками в пределах заданного периода моделирования Тм, после окончания которого осуществляется вычисление параметров модели и суммарных удельных затрат при заданных исходных данных.
Моделирование потоков агрегатов, поступающих на плановые и неплановые ремонты, осуществляется на основе анализа процесса изнашивания и наработок между отказами бандажей колесных пар тепловозов, эксплуатирующихся на Западной железной дороге.
Поэтому в главе 5 для рассматриваемых локомотивных депо по информации об изменении контролируемых параметров и наработках на отказ определены зависимости средних значений и дисперсии тощины бандажей колесных пар тепловозов, рассчитаны функции распределения ресурса и соответствующие функции плотности.
Решением уравнения Вольтерра рассчитаны зависимости параметра потока отказов от наработки, обусловленных изнашиванием бандажей, входящие в целевую функцию для расчета оптимальных пробегов до смены бандажей колесных пар:
где К - отношение затрат на плановые и неплановые ремонты;
Ь - межремонтный период; и'(I)- функция параметра потока отказов и по функции суммарных удельных затрат на плановые и неплановые ремонты определены оптимальные сроки ремонта колесных пар со сменой бандажей.
Объем ремонта колесных пар, обусловленный ослаблением и проворотом бандажей на колесном центре определен по информации о наработках между отказами по которым рассчитывались усеченные эмпирические функции распределения для каждого локомотивного депо
где п,1(Ь,) - число восстановлений < -го экземпляра рассматриваемого оборудования, предшествующего наработке Ь ; 1=1,2,. .., N(1);
-общее число восстановлений 1 -го экземпляра оборудования в течение периода
Анализ и проверка соответствия эмпирических функций распределения различным теоретическим законам осуществлялась по критерию Комогорова-
л Гл'(') "1
Смирнова. В результате чего установлено, что наработка бандажей колесных пар до ослабления и проворота хорошо описывается экспоненциальным законом распределения.
Смена бандажей колесных пар тепловозов 2ТЭ10 может быть осуществлена в результате их естественного износа (параметрическая надежность) или же вследствие ослабления их посадки на колесном центре (непараметрическая надежность).
Таким образом имеются два потока колесных пар, поступающих на ремонтные позиции, где осуществляется их ремонт. Один поток, обусловленный естественным износом бандажей, имеет параметры, представленные в таблице 2. Другой поток обусловлен внезапными ослаблениями посадки бандажей. Интенсивность этих потоков для различных депо приведена в крайне правом стобце табл.2.
Таблица 2
Характеристики потоков колесных пар, поступающих на ремонт
Параметры распределения Интенсивность ослабле-
NuNs Депо оптимального пробега, тыс.км ния бандажей колесных
п/п m(t) oft) пар X 1/106 км
1 Кзыл-Орда 427 28 5 0.178
2 Казалинск 366 24.4 0.213
3 Саксаульская 263 175 0.241
4 Чекар 126 84 0 776
5 Эмба 182 12 13 0.304
6 Кандагач 313 20,87 0.128
7 Актюбинск 342 22.8 0 107
8 Уральск 280 18 67 0.184
9 Шубар-Кудук 274 18 27 0.337
10 Манат 318 212 0.418
11 Мангышлак 204 136 0.497
12 Атырау 407 27.13 0 238
Полученные в главе 5 результаты были взяты в качестве исходных для расчета по разработанной имитационной модели параметров технологического процесса ремонта колесных пар в депо Казалинск, который осуществлен в главе 6.
Для сокращения объема вычислений при поиске оптимального числа ремонтных позиций по восстановлению оборудования и объема переходного запаса агрегатов целесообразно использовать математические методы планирования эксперимента.
Поиск оптимального решения осуществляся градиентным методом скорейшего спуска, который реализован в виде многошагового процесса постановки последовательной серии опытов, причем условия проведения каждой последующей серии определяются после математической обработки результатов предыдущей серии опытов. Так последовательно, шаг за шагом, достигается область оптимума.
На основании анализа технологического процесса ремонта колесных пар тепловозов со сменой бандажей установлено, что математическая модель исследуемого процесса восстановления колесных пар включает в себя 14 управляемых факторов: 13 из них соответствует числу ремонтных позиций на соответствующих операциях, а 14-й фактор - числу агрегатов переходного комплекта.
Математическая модель процесса ремонта колесных пар, т.е. зависимость параметра оптимизации - суммарных удельных потерь от управляемых факторов, принята линейной функцией.
Адекватность линейной модели обеспечивается выбором уровней варьирования управляемых факторов. Неоднократное проведение эксперимента показало, что модель получается адекватной, а коэффициенты 6,- значимыми, если в качестве основного уровня числа ремонтных позиций взять число равное 2, а интервал варьирования факторов равный 1. Таким образом, верхний уровень числа ремонтных позиций равен 3, а нижний -1. Исходя из аналогичных рассуждений выбраны уровни переходного запаса агрегатов: основной - 14 колесных пар, нижний -12 колесных пар, верхний -16 колесных пар.
Ввиду того, что полный факторный эксперимент обладает большой избы-
точностью опытов был проведен дробный факторный эксперимент с 16 опытами.
При построении дробной реплики для сокращения числа опытов при введении в планирование нового фактора нужно поместить этот фактор в вектор-стобец матрицы планирования, принадлежащий взаимодействию, которым можно пренебречь. Тогда значение нового фактора в условиях опытов определяется знаками этого стобца.
При построении матрицы планирования выбраны следующие генерирующие соотношения: Х} = Х/Х}; Хб = X/ X/, Х7 = X; X/, Хц = Х2Х3\ Хд = Х2Х/, Х/о = ХзX/, Хц = XI Х2 Хз\ Хц = X] Х3Х4, Хц = Х2Х3 Х4, Х]4 = Х]Х2 X; Х4.
Матрица планирования эксперимента представлена в таблице 3.
Таблица 3
Матрица планирования эксперимента_
№№ опытов Технологические параметры
XI Хз X! Хб Х7 Хв Хц х ю Хц Хц Х14
1 - - - - + + + + + + - - - +
2 - - + + + - + - - - + + -
3 - - + - + - + - + - + + + -
4 - - + + + - - - - + + - - +
5 - + - - + + - - + - + -
6 - + + - + - - + - + + - +
7 - + + - - + + - - - + - +
8 - + + + - - - + + + - - + -
9 + + + + + + - -
10 + - + - - + + - - -ь - + +
11 + - + - - + - - + - - - + +
12 + - + + - + + - + - + - -
13 + + + - - - + - + + +
14 + + - + + - + - +
15 + + + + + - + - - + - - -
16 + + + + + + + + + + + + + +
Здесь знак (+) соответствует верхнему, а (-) - нижнему уровню варьирования факторов.
Каждая горизонтальная строка матрицы планирования - это условия проведения опытов. Одновременное изменение всех факторов вносит в условия
опытов большое разнообразие.
Такое многообразие наборов числа ремонтных позиций и переходного запаса агрегатов дает возможность провести имитационные эксперименты и определить их оптимальное количество для требуемых объемов ремонта локомотивов.
Чтобы убедится в однородности результатов имитационного моделирования было проведено по пять повторных расчетов в каждом опыте.
Однородность результатов эксперимента, адекватность модели и значимость коэффициентов уравнения регрессии проверялись методами теории статистических гипотез.
Результаты расчетов в первой серии опытов показали, что линейная модель является адекватной, и уравнение регрессии имеет следующий вид:
2= 80.297 +3.86x1 - 0.604*, - 2.69*, + 0.981*, +0.25*5 - 26.32** - 4.71*7 -1.005*5+ 0.0383*9 - З.ЗЗх,о+ 2.996хи - 1,42*;; + 3.424*,5 + 0.718*н
Установлено, что коэффициенты, соответствующие 2, 3, 4, 5, 7, 8, 12 и 14 операциям оказались незначимыми. Незначимость коэффициентов показывает, что выбранные нами нулевые уровни близки к оптимальным значениям, для тех же параметров, у которых коэффициенты значимы, необходимо продожить вариации переменных с целью поиска их оптимальных величин.
Анализ уравнения регрессии (23) показал, что для уменьшения параметра оптимизации необходимо уменьшить значения тех факторов, которые входят в уравнение регрессии с плюсовым значением коэффициентов Ь1. Такими факторами являются */, Хц , Хц. Но поскольку в предыдущих опытах значения этих факторов были равны 2, то остается единственно возможный вариант - приравнять эти факторы 1, т.е. оптимальное значение числа ремонтных позиций принять равным 1 и на этом прекратить их варьирование.
Остаются для варьирования факторы х6, х;0|причем в сторону их увеличения, а это свидетельствует о том, что при выпонении технологических операций по обработке колесных центров (х6) и насадке бандажей на колесные центры (дгю) недостаточно ремонтных позиций.
Для нахождения оптимальных значений параметров хб, х10 необходимо построение второй серии опытов. Поэтому изменяем уровни варьирования факторов Хб, хю : в качестве основного уровня числа ремонтных позиций принимаем число равное 3, а интервал варьирования факторов примем равным 1: нижний уровень - х.=2, верхний - дг+=4. Матрица планирования второй серии эксперимента представлена в таблице 4.
Таблица 4 Матрица планирования эксперимента _ (вторая серия)_
№№ Технологические параметры
опытов хл Хю
Анализ результатов эксперимента второй серии опытов показал значимость коэффициента, соответствующего 6-й ремонтной операции и незначимость коэффициента, соответствующего 10-й операции.
Это свидетельствует о том, что нулевой уровень факторов для 10-й операции близок к оптимальному значению, равному 3 ремонтным позициям.
Для нахождения оптимального значения по единственному фактору 6-й операции уже нет необходимости проводить планирование эксперимента. Достаточно будет, изменяя пошагово значения фактора и проведя имитационный эксперимент определить значения параметра оптимизации. В результате эксперимента оптимальное значение фактора 6 операции получено равным 4.
В области оптимума целевая функция является достаточно гладкой, поэтому небольшие вариации управляемого фактора могут не вызвать существен-
ного изменения функций. Особенно это характерно для 14 фактора - числа агрегатов в переходном комплекте. Для того чтобы убедиться в том, что найденные по первой серии опытов число агрегатов переходного комплекта действительно оптимально были проведены имитационные эксперименты с пошаговым изменением числа переходного запаса агрегатов при постоянных значениях числа ремонтных позиций. Их результаты расчета показали, что оптимальное число переходного запаса колесных пар для выпонения требуемых объемов ремонта действительно равно 14 .
Оптимальное число ремонтных позиций процесса ремонта колесных пар со сменой бандажей в локомотивном депо Казалинск (рис.9) для большинства технологических операций равно 2, по одной позиции требуется для операций осмотра колесной пары перед ремонтом, проверки размеров и нанесения контрольных отметок на бандажи и колесные центры, окраски
Ремонтные позиции
I II III IV V VI VII VIII IX X XI XII XIII
3ti* кокмыхпар
Рис.9. Оптимальная технологическая линия по ремонту колесных пар со сменой бандажей (депо Казалинск)
колесной пары. Для насадки бандажей на колесные центры необходимо 3, а для обработки колесных центров - 4 ремонтные позиции. Объем переходного комплекта насчитывает 14 колесных пар.
ЗАКЛЮЧЕНИЕ
1. Аначиз исследований в области выбора оптимальных технологических средств и запасных частей к подвижному составу, радиоэлектронной аппаратуре, автомобилям, тракторам, самолетам, морским судам и сельскохозяйственным машинам показал, что при решении задач используются либо детерминированные модели или же модели, в которых вероятностные оценки осуществляются в упрощенном варианте на основе простейших потоков, без учета разного характера наработок и времени восстановления агрегатов на плановых и неплановых ремонтах. Необходим системный подход, позволяющий учитывать функциональные свойства агрегатов и их отношения с учетом реальных законов распределения наработок агрегатов до плановых и неплановых ремонтов, времени восстановления, а гак же особенностей условий эксплуатации оборудования локомотивов в различных регионах.
2. Системный подход реализован в виде разработанной имитационной модели технологических процессов с высокой степенью точности, отражающей реальные процессы восстановления работоспособности оборудования локомотивов, с учетом фактических законов распределения наработок, продожительности простоя на ремонтных операциях, множества, поступающих на обслуживание потоков агрегатов и другие факторов, имеющих место в реальных условиях эксплуатации, которая позволяет проводить имитационные эксперименты по определению рационального числа ремонтных позиций и объема переходного комплекта запасного оборудования при агрегатном методе ремонта локомотивов.
3. Практическая апробация разработанных методов осуществлена на основании изучения изнашивания и наработок между отказами бандажей колесных пар тепловозов серии 2ТЭ10Л,В,М локомотивных депо Кзыл-Орда, Каза-линск, Саксаульская, Чекар, Эмба, Кандагач, Актюбинск, Уральск, Шубар-
Кудук, Манат, Мангышлак, Атырау Западно-Казахстанской (ныне Западной) железной дороги. Объемы первичной информации составили: от 96 до 216 значений по замерам тощины бандажей и 42 - 126 значений по отказам колесных пар, что позволяет получить достоверные статистические выводы.
4. Годовая программа ремонта колесных пар в депо Казалинск, где сосредоточен ремонт колесных пар всех локомотивных депо Западной дороги, определена исходя из условий реализаций в каждом депо оптимальных пробегов до ремонта колесных пар со сменой бандажей, которые рассчитаны по критерию минимума затрат на проведение плановых и неплановых ремонтов и составляют для тепловозов 2ТЭ10Л,В,М в локомотивных депо: Кзыл-Орда - 427 тыс.км, Казалинск - 366 тыс. км, Саксаульская - 263 тыс. км, Чекар - 126 тыс. км, Эмба -182 тыс. км, Кандагач - 313 тыс км, Актюбинск - 342 тыс. км, Уральск - 280 тыс. км, Шубар-Кудук - 274 тыс.км, Макат - 318 тыс. км, Мангышлак - 204 тыс. км, Атырау - 407 тыс. км. Наработка на отказ, обусловленных ослаблением бандажей на колесном центре, для рассматриваемых депо составляет 1.289 - 9.346 мн. км.
5. В качестве целевой функции (параметра оптимизации) выбраны суммарные удельные потери от простоя ремонтных позиций, от простоя агрегатов, находящихся в запасе, от простоя агрегатов в ожидании ремонта, от простоя локомотивов из-за отсутствия агрегатов в переходном комплекте.
6. Разработанная аналитическая модель процесса восстановления работоспособности оборудования локомотивов агрегатным методом учитывает случайные вариации моментов поступления агрегатов на ремонт, времени их восстановления и позволяет рассчитать оптимальное число ремонтных позиций и объем переходного запаса агрегатов, чтобы обеспечить выпонение требуемой программы ремонта с наименьшими затратами.
7. На основе теории вероятностей, теории надежности, теории массового обслуживания разработана и реализована на ЭВМ статистическая модель вое-
становления работоспособности агрегатов. Использованный при разработке ее агоритма и программы модульный принцип дает возможность не меняя структуры и логики агоритма, производить расчеты при любых распределениях временных параметров потока, поступающих на восстановление агрегатов и времени их обслуживания, учитывать случайный характер распределений наработок до плановых и неплановых ремонтов, неординарность потока агрегатов, поступающих на плановые ремонты, многоканальность поступления агрегатов из различных пунктов их эксплуатации.
8. Практическое совпадение выходных параметров статистической модели, рассчитанных в предположении, что процесс восстановления работоспособности агрегатов является марковским, с аналогичными характеристиками аналитической модели, построенной при тех же допущениях, свидетельствует о том, что в статистической модели достаточно поно отражены существенные стороны исследуемого процесса.
9. Предложенные принципы статистического моделирования процесса восстановления агрегатов в виде последовательности технологических операций, заданной сетевым графиком, создают основу для проведения имитационных экспериментов по оптимизации числа ремонтных позиций для выпонения каждой отдельной технологической операции.
10. Рациональная организация имитационных экспериментов на разработанной статистической модели при поиске оптимальных параметров технологического процесса ремонта колесных пар в депо Казалинск осуществлялась методом математического планирования эксперимента.
И. полный факторный эксперимент обладает большой избыточностью опытов, поэтому был осуществлен дробный эксперимент, число опытов в котором равно 16, что дает возможность производить по заранее составленному плану вариации 14 управляемых факторов: дг;-дг^ - число ремонтных позиций для выпонения отдельных технологических операций при ремонте колесных
пар; Хц - объем переходного комплекта колесных пар.
12. Математическая модель исследуемого процесса ремонта колесных пар, т.е. зависимость параметра оптимизации от управляемых факторов, принята в виде линейной функции . Проверка методами теории статистических гипотез, подтвердила адекватность этой модели.
13. Поиск оптимального решения осуществляся градиентным методом скорейшего спуска, который реализован в виде многошагового процесса постановки последовательной серии опытов, причем условия проведения каждой последующей серии определяются после математической обработки результатов предыдущей серии опытов.
14. Оптимальная численность ремонтных позиций для выпонения отдельных технологических операций и объем переходного комплекта колесных пар были определены за три шага по градиенту целевой функции.
15. Оптимальное число ремонтных позиций процесса ремонта колесных пар со сменой бандажей в локомотивном депо Казалинск для большинства технологических операций равно двум, по одной позиции требуется для операций осмотра колесной пары перед ремонтом, проверки размеров и нанесения контрольных отметок на бандажи и колесные центры, окраски колесной пары. Для насадки бандажей на колесные центры необходимо три, а для обработки колесных центров - четыре ремонтные позиции. Объем переходного комплекта насчитывает 14 колесных пар.
16. Разработанные математические модели и агоритмы оптимизации числа ремонтных позиций и объема переходного комплекта запасных агрегатов, реализованные на примере агрегатного метода ремонта колесных пар, могут быть применены для оптимизации параметров технологического процесса ремонта любого оборудования тягового подвижного состава.
Основные положения диссертации опубликованы в следующих работах.
1. Горский A.B., Воробьев A.A., Куанышев Б.М. Оценка эффективности повышения ресурса изнашиваемого оборудования электровозов технологическими методами // Тез. докл. Всесоюз. науч.-техн. конф. -Брянск. -1991. -2 с.
2. Горский A.B., Воробьев A.A., Куанышев Б.М. Выбор критерия оптимальности межремонтных пробегов для оборудования локомотивов //Вопросы совершенствования системы ремонта ЭПС при применении средств технической диагностики: Сб. науч. тр./ ВНИИЖТ. -М.: Транспорт, 1991. -С. 15-20.
3. Алькиязов P.A., Куанышев Б.М. Анализ использования ресурса оборудования ЭПС и выбор элементов, лимитирующих межремонтные пробеги // Состояние и перспективы развития электровозостроения в стране: Тез. докл. Всесоюз. науч.-техн. конф. -Новочеркасск, 1991. -С. 142-143.
4. Горский A.B., Воробьев A.A., Куанышев Б.М. Система ремонта электроподвижного состава и ее оптимизация. Учебное пособие. -М.: МИИТ, 1993. -118с.
5. Горский A.B., Воробьев A.A., Козырев В.А., Куанышев Б.М. Влияние системы ремонта локомотивов на обслуживание поездов//Железнодорожный транспорт, 1994. -№11. -С. 51-53.
6. Альниязов P.A., Куанышев Б.М. Влияние возраста электровоза на использование ресурса его оборудования // Актуальные проблемы развития железнодорожного транспорта: Тез. докл. I междунар. конф. в г. Москве 18-21 апреля 1994 г. / МИИТ. -МД 1994. -С. 60.
7. Куанышев Б.М., Чернова Е.П. Определение рационального запаса агре-гатов//Акгуальные проблемы развития железнодорожного транспорта: Тез. докл. II междунар. конф. в г. Москве 26-28 сентября 1996 г./МИИТ. -М., 1996. -С. 95.
8. Куанышев Б.М. Определение переходного запаса агрегатов и рационального числа ремонтных позиций //Проблемы развития локомотивостроения: Тез. докл. VI междунар. конф. в г. Москве 28-31 октября 1996 г. / МИИТ. -М.,
1996. -С. 76.
9. Горский A.B., Воробьев A.A., Куанышев Б.М. Сравнительный анализ использования ресурса бандажей колесных пар электровозов в разных условиях эксплуатации //Ж.-д. трансп. Сер. Локомотивы и локомотивное хозяйство. Ремонт локомотивов. ОИ/ ЦНИИТЭИ МПС.-1997. -Вып. 2. -44 с.
10. Куанышев Б.М. Оценка эффективности лазерного упрочнения бандажей колесных пар электропоездов //Энергоснабжение, качество электроэнергии, электромагнитная совместимость на железнодорожном транспорте: Сб. тр. /МИИТ-РАПС. -М, 1997. -83-84 с.
11. Куанышев Б.М. Аналитическая модель процесса восстановления оборудования при агрегатном методе ремонта локомотивов //Проблемы развития рельсового транспорта: Тез. докл. VII междунар. конф. Крым, Ливадия, 29 сен-тября-4 октября 1997 г. / ВУГУ. -Луганск, 1997. -83-84 с.
12. Горский A.B., Воробьев A.A., Куанышев Б.М. Анализ непараметрической надежности локомотивов: Тез. докл. VII междунар. конф. Крым, Ливадия, 29 сентября-4 октября 1997 г. / ВУГУ. -Луганск, 1997. -24-25 с.
13. Куанышев Б.М. Тепловоздары жОндеудш тшмд! мерзшдерш аныктау //Болат жол. -1997. -№31. -С. 3.
14. Куанышев Б.М. Определение оптимальных сроков ремонта тепловозов //Болат жол. -1997. -№31. -С. 4.
15. Куанышев Б.М. Определение оптимальных сроков ремонта тепловозов с учетом фактического состояния //TeMip жол. -1997. -№3. -С. 12.
16. Горский A.B., Воробьев A.A., Куанышев Б.М. Определение эффективности лазерной закаки бандажей колесных пар //Ж.-д. трансп. Сер. Локомотивы и локомотивное хозяйство. Ремонт локомотивов. ОИ/ ЦНИИТЭИ МПС.-1997. -Вып. 4. -С.16-33.
17. Куанышев Б.М. Моделирование технологического процесса восстановления работоспособности агрегатов локомотивов /МИИТ. -М., 1998. -12 с.
-Деп. в ЦНИИТЭИ МПС, №6145-ж.-д.-98.
18. Куанышев Б.М. Определение оптимальных параметров технологического процесса ремонта оборудования локомотивов методами планирования эксперимента /МИИТ. -МД 1998. -21 с. -Деп. в ЦНИИТЭИ МПС, №6147-ж.-д,-98.
19. Куанышев Б.М. Математическая модель индивидуального метода ремонта оборудования локомотивов /МИИТ. -М., 1998. -9 с. -Деп. в ЦНИИТЭИ МПС, №6146-ж.-д.-98.
20. Куанышев Б.М.Статистическая модель агрегатного метода ремонта локомотивов //Вестник МИИТа. -Вып.2. -1998. -с. 12.
21. Куанышев Б.М. Оценка эффективности повышения ресурса оборудования локомотивов// Сб. науч. тр./ МИИТ. -1998. -Вып.893: Научное решение актуальных задач транспорта. -С. 11.
22.Горский A.B., Воробьев A.A., Куанышев Б.М. Имитационная модель расчета параметров технологического процесса ремонта оборудования локомотивов //Актуальные проблемы и перспективы развития железнодорожного транспорта: Тез. докл. III межвуз. научно-методич. конф. /РГОТУПС. -М., 1998. -Ч.1.-С.67.
23. Куанышев Б.М. Расчет параметров технологического процесса ремонта оборудования локомотивов методами планирования эксперимента //Актуальные проблемы и перспективы развития железнодорожного транспорта: Тез. докл. III межвуз. научно-\<^^С??"конф"7Т^^;УПС. -М., 1998. -4.2. -С. 9.
24. Куанышев Б.М. Ремонт локомотивов с учетом реального состояния //Локомотив. -1998. -№2. -С. 34-35.
КУАНЫШЕВ Бакытжан Муханбетович
ОПТИМИЗАЦИЯ КОЛИЧЕСТВЕННЫХ ПАРАМЕТРОВ ПЕРЕХОДНОГО КОМПЛЕКТА И СОСТАВА РЕМОНТНЫХ ПОЗИЦИЙ ПРИ АГРЕГАТНОМ МЕТОДЕ РЕМОНТА ЛОКОМОТИВОВ
Специальность08.00.28-^н^шациящ^Кзодства (техническиенауки)
Подписано к печати 05". Формат 60x84/16 /492*
Объем 30 п.л. Заказ 246, Тираж 100.
Типография МИИТа Москва, А-55, ул. Образцова, 15