Читайте данную работу прямо на сайте или скачайте
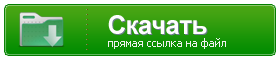
МЕТАЛЛОВЕДЕНИЕ ЭКЗАМЕН
№ 1.Ал
лотропией, или полиморфизмом, называется способность металлов в твердом состоянии иметь различное кристаллическое строение, следовательно, и свойства при различных температурах.
Процесс перехода из одной кристаллической формы в другую называется аллотропическим (полиморфным)превращением. Аллотропические формы обозначают начальными буквами греческого алфавита: альфа а, бета ?, гамма у, дельта б и т. д., начиная с той формы, которая существует при более низкой температуре.
В процессе аллотропического превращения выделяется скрытая теплота кристаллизации (если превращение идет при охлаждении); на кривой охлаждения аллотропическое превращение отмечается горизонтальным частком. Аллотропические превращения имеют многие металлы, например железо, марганец, олово, титан и др.
№2. Феррит - твердый раствор внедрения глерода и других элементов в а-железе. Различают низкотемпературный а-феррит с растворимостью глерода в пределах 0,006 % при нормальной температуре, 0,025 % при 727С и высокотемпературный б-феррит с предельной растворимостью глерода 0,1 %. Феррит имеет кристаллическую решетку ОЦК, в центре которой расположен атом глерода. Температура 768 С является точкой Кюри для феррита, то есть ниже этой температуры феррит магнитен, выше - немагнитен. Феррит имеет примермно следующие механические свойства: сгв = 25 Н/см2; 6 = = 50%; -ф = 80 %; НВ 80...90. Под микроскопом феррит виден в виде светлых (полиэдрических) зерен.
Аустенит - твердый раствор внедрения глерода и других элементов в у-железе. В зависимости от температуры в у-железе может раствориться от 0,8 (при 727С) до 2,14% С (при 1147С). Аустенит имеет кристаллическую решетку ГЦК, атомы глерода в которой расположены в центре граней куба. Твердость аустенита составляет до 220 НВ, он немагнитен. Микроструктура аустенита - полиэдрические зерна, характеризующиеся в отличие от феррита двойниками.
К железоуглеродистым сплавам относят стали и чугуны. Основмными элементами, от которых зависят структура и свойства сталей и чугунов, является железо и глерод.
Железо может находиться в двух аллотропических формах - и.
Железо с глеродом образует твердые растворы внедрения и химические соединения, -железо растворяет глерода очень мало (до 0,02 % при температуре 727 С).
Твердый раствор глерода и других элементов в -железе называется ферритом. Структура феррита показана на рис. 28, а. Феррит имеет низкую твермдость и прочность: 80 НВ; в=250 Па (25 кгс/мм2) и высомкую пластичность и вязкость ( = 50 %; = 80 %; КСU = 2,5 Дж/м2). Поэтому технически чистое железо, структура которого представляет зерна феррита, хорошо подвергается холодной деформации, т. е. хорошо штампуется, прокатывается, протягивается в холодном состоянии. Чем больше феррита в железоуглеродистых сплавах, тем они пластичмнее.
В значительно больших колимчествах растворяет глерод -железо (до 2,14 % при температуре 1147 С). Твердый раствор глерода и других элементов в -железе называется аустенитом. Характерная особенность аустенита заключается в том, что он в железоуглеродистых сплавах может существовать только при высоких температурах. Как и всякий твердый раствор, аустенит имеет микроструктуру, представляющую собой зерна твердого раствора (рис. 28, б). Аустенит пластичен = 40 - 50 %, твердость его составляет 160 - 200 НВ.
Железо с глеродом также образуют химическое соединение Fe3C, называемое цементитом или карбидом железа. В цементите 6,67 % С; он имеет высокую твердость (более 800 НВ), но чрезвычайно низкую, практически нулевую, пластичность. Чем больше цеменмтита в железоуглеродистых сплавах, тем большей твердостью и меньшей пластичностью они обладают. При микроскопическом ис-следовании цементит выявляется в виде светлых кристаллов (сетка на рис. 28, б). Цементит неустойчив (метастабилен) и при определенных словиях может распадаться, выделяя свободный глерод в виде графита.
№3. Феррит (лат. ferrum - железо), фазовая составляющая сплавов железа, представляющая собой твёрдый раствор глерода и легирующих элементов в -железе (-феррит). Имеет объемноцентрированную кубическую кристаллическую решётку. Является фазовой составляющей других структур, например, перлита, состоящего из феррита и цементита.
При температурах выше 1401 С в железоуглеродистых сплавах образуется твёрдый раствор глерода в -железе (-феррит), который можно рассматривать как высокотемпературный феррит.
Растворимость глерода в -феррите 0,02-0,03 % (по массе) при 723 C, при комнатной температуре 106-107 %; в -феррите - 0,1 %. Растворимость легирующих элементов может быть весьма значительной или неограниченной. Легирование феррита в большинстве случаев приводит к его прочнению. Нелегированный феррит относительно мягок,пластичен, сильно ферромагнитен до 768-770 С.
№4.
АУСТЕНИТ (от имени английского металлурга У. Робертса-Остена, W. Roberts-Аusten; 1843-1902), структурная составляющая железоуглеродистых сплавов - твердый раствор глерода (до 2%), также легирующих элементов в железе.
Аустенит пластичен, его твердость НВ 160-200 кгс/мм2. Парамагнетик, проводит тепло и электрический ток хуже, чем феррит.
Атомы растворенного в аустените глерода располагаются в центре элементарных гексагональных кубических ячеек, т. е. образуется твердый раствор глерода в g-железе. Растворимость глерода в аустените зависит от температуры, максимальна при Т = 1147 оС и составляет 2,14%, т. е. выше, чем в феррите. Ограничение растворимости глерода вызвано тем, что атом глерода больше размера поры в центре ячейки g-железа, и при внедрении глерода решетка искажается, и соседние поры становятся недоступными для других атомов глерода.
Область существования аустенита - при температурах выше 727оС. При комнатной температуре он иногда сохраняется только в закаленной стали, так как в процессе охлаждения стали аустенит превращается в другие структурные составляющие. Свойства и строение продуктов превращения аустенита зависят от температуры, при которой происходил процесс его распада. Например, в стали с содержанием глерода 0,8% могут происходить следующие фазовые превращения. При медленном охлаждении (в печи) при температурах вблизи 700оС (т. е. при достаточно высоких температурах и малых степенях переохлаждения) аустенит превращается в перлит - достаточно грубую смесь феррита и цементита. Легирующие элементы, за исключением кобальта, величивают продолжительность инкубационного периода перлитного превращения. При более низких температурах, и следовательно при больших степенях переохлаждения, дисперсность структур возрастает, т. е. при скоренном охлаждении (на воздухе) распад аустенита произойдет при температурах (650оС) и образуетсясорбит. При еще более низкой температуре, т. е. при большей скорости охлаждения (в масле) распад аустенита произойдет при температурах (550оС) и образуется троостит. Перлит, сорбит и троостит представляют собой структуру с одинаковой природой (смеси феррита и цементита), но отличающейся степенью дисперсности феррита и цементита. При высокой скорости охлаждении в воде аустенит превращается в мартенсит. При перлитном превращении легированного аустенита во многих случаях образуется смесь феррита и специальных карбидов.
№ 5. Цементит (Fe3C) - химическое соединение железа с глеродом (карбид железа), со сложной ромбической решеткой, содержит 6,67 % глерода. Он твердый (свыше 1 HВ), и очень хрупкий. Цементит фаза метастабильная и при длительным нагреве самопроизвольно разлагается с выделением графита.
В железоуглеродистых сплавах цементит как фаза может выделяться при различных словиях:
- цементит первичный (выделяется из жидкости),
- цементит вторичный (выделяется из аустенита),
- цементит третичный (из феррита),
- цементит эвтектический и
- эвтектоидный цементит.
Цементит первичный выделяется из жидкой фазы в виде крупных пластинчатых кристаллов. Цементит вторичный выделяется из аустенита и располагается в виде сетки вокруг зерен аустенита (после эвтектоидного превращения они станут зернами перлита). Цементит третичный выделяется из феррита и в виде мелких включений располагается у границ ферритных зерен.
Эвтектический цементит наблюдается лишь в белых чугунах. Эвтектоидный цементит имеет пластинчатую форму и является составной частью перлита.
Цементит может при специальном сфероидизируюшем отжиге или закалке с высоким отпуском выделяться в виде мелких сфероидов.
Влияние на механические свойства сплавов оказывает форма, размер, количество и расположение включений цементита, что позволяет на практике для каждого конкретного применения сплава добиваться оптимального сочетания твердости, прочности, стойкости к хрупкому разрушению и т. п.
№7. В системе железо-цементит (Fe - FеС) имеются следующие фазы: жидкий раствор. твердые растворы - феррит и аустенит, также химическое соединение - цементит. В системе железо - цементит имеются две тонкие механические смеси фаз - эвтектическая (ледебурит) и эвтектоидная (перлит).
№8.
Ледебурит представляет собой эвтектическую смесь аустенита с цементитом. Содержит 4,3 % глерода, образуется из жидкого сплава при температуре 1147 С. При температуре 727 С аустенит, входямщий в состав ледебурита превращается в перлит и ниже этой темпемратуры ледебурит представляет собой механическую смесь перлита с цементитом. Ледебурит (Л) - механическая смесь (эвтектика) аустенита и цементита, содержащая 4,3% глерода. Ледебурит образуется при затвердевании жидкого расплава при 1147С. Ледебурит имеет твердость НВ 600-700 и большую хрупкость. Поскольку при температуре 727С аустенит превращается в перлит, то это превращение охватывает и аустенит, входящий в состав ледебурита. Вследствие этого при температуре ниже 727С ледебурит представляет собой же не смесь аустенита с цементом, смесь перлита с цементитом.
Помимо перечисленных структурных составляющих в железоуглеродистых сплавах могут быть нежелательные неметаллические включения: окислы, нитриды, сульфиды, фосфиды - соединения с кислородом, азотом, серой и фосфором. На их основе могут образовываться новые структурные составляющие, например фосфидная эвтектика (Fe+Fe3P+Fe3C) с температурой плавления 950С. Она образуется при больших содержаниях фосфора в чугуне. При содержании фосфора около 0,5-0,7% фосфидная эвтектика в виде сплошной сетки выделяется по границам зерен и повышает хрупкость чугуна.
№9. ПЕРЛИТ - структурная составляющая в глеродистых и легированных сталях и чугунах, возникающая при эвтектоидном превращении (смМЕТАЛЛОВЕДЕНИЕ ФИЗИЧЕСКОЕ) согласно диаграмме состояния железо - глерод. Перлит состоит из двух фаз - феррита и цементита, феррит - железо с очень малым количеством глерода (до 0,03%), цементит - химическое соединение Fe3C, содержащее по массе 6,67%С. Среднее содержание глерода в перлите - 0,8%С, сталь с целиком перлитной структурой, содержащая 0,8%
углерода, называется эвтектоидной. При содержании глерода менее 0,8% сталь состоит из перлита и феррита, если глерода более 0,8% - из перлита и, в соответствии с диаграммой состояния железо - глерод.
№10. Перлит обычно имеет пластинчатую структуру, каждое зерно перлита состоит из параллельных пластинок феррита и цементита шириной в десятые доли мкм. Длина пластинок соответствует размеру зерен металла, и пластинки идут от одной границы зерна к другой. Если такая объемная пластинчатая структура пересекается плоскостью шлифа и подвергается травлению, то на ее поверхности возникает полосчатая структура из светлых полосок феррита и тонких полосок цементита. При различных термообработках ширина полосок (межпластиночное расстояние) может быть различным, ширина полосок цементита в 7 раз меньше, чем полосок феррита. При длительной выдержке при высоких температурах зерна феррита и цементита могут переходить из пластинчатой формы в округлую, и на металлографическом шлифе наблюдаются мелкие, темные, округлые зерна цементита на фоне крупных зерен феррита.
Механическая смесь феррита и цементита обр-азует структуру стали, называемую перлитом. Перлит бывает двух видов: пластинчатый, или полосчатый, и зернистый. Пластинчатый перлит i меет вид перемежающихся очень мелких пластинок феррита и цементита. Путем нагрева до определенных температур можно изменить строение пластинчатого перлита и получить так называемый зернистый перлит, в котором цементит находится в виде круглых зерен, расположенных среди феррита.
Эвтектоид - механическая смесь феррита и цементита, образующаяся из аустенита.
Микроструктуры глеродистых ста - На 110, - - сталь. Перлит - механическая смесь феррита с цементитом - образуется при медленном охлаждении аустенита, содержащего 0 8 % С. Перлит прочнее феррита, но мало пластичен при комнатной температуре. Стали, содержащие 0 80 % С, называются эвтектоидными или перлитными. При меньшем содержании глерода стали называются доэвтектоидными, при большем, - заэвтектоид-ными.
Микроструктура стали в равновесном состоянии. - ферритная, б - ферритно-цементитная, в - ферритно-перлитная, г-пе лишая, д - перлитно-цементитная. 1 - феррит, 2 - цементит, 3 - перлит. Перлит - механическая смесь феррита с цементитом. За счет прочняющего влияния цементита перлит имеет более высокую прочность и твердость, чем феррит, но более низкую дарную вязкость и пластичность.
Тростит - механическая смесь феррита и цементита; получается при скорости закалки глеродистой стали около 80 С в секунду.
Перлит - механическая смесь феррита и цементита, называемая эвтектоидом. Чистый перлит встречается только в стали, содержащей 0 8 % С. Обычно перлит присутствует вместе с ферритом или цементитом.
Эвтектоид - механическая смесь феррита и цементита, образующаяся из аустенита. Различают пластинчатый перлит, в котором в ферритной основе находятся пластинки цементита ( фиг 4, к; и и) и зернистый перлит, R котором в ферритной основе находятся зернышки цементита.
Перлит - мелкозернистая механическая смесь феррита и цементита. На микрошлифе имеет вид зерен или параллельно расположенных пластинок, поэтому различают перлит зернистый или пластинчатый.
Перлит - мелкозернистая механическая смесь феррита и цементита.
Трооститом называется механическая смесь феррита цементита очень высокой степени дисперсности. Эта структура образуется при скорости закалки глеродистой стали около 80 / сек. Игольчатый троостит иногда называют бейнитом.
Перлитом называют механическую смесь феррита и цементита, образующуюся при эвтектоидном распаде медленно охлаждаемого аустенита. Сталь, содержащая 0 80 % С, имеет чисто перлитную структуру.
Троостит является механической смесью феррита и цементита очень высокой степени дисперсности. Эта структура образуется при скорости закалки глеродистой стали около 80 град / сек. Игольчатый троостит иногда называют бейнитом.
Перлит - это механическая смесь феррита и цементита.
Перлит - это механическая смесь феррита и цементита, образующаяся при эвтектоидном распаде медленно охлаждаемого аустенита. Сталь, содержащая 0 80 % С, имеет чисто перлитную структуру.
Перлит - это механическая смесь феррита с цементитом. Содержит 0 8 % глерода, образуется из аустенита при температуре 727 С. Перлит имеет пластинчатое строение, т.е. состоит из чередующихся пластинок феррита и цементита. Возможно и зернистое строение перлита, когда он состоит из зерен цементита, окруженных ферритом. Зернистый перлит значительнее пластичнее пластинчатого, имеет меньшую твердость.
Схема возникновения и роста перлитного зерна. Все они являются механическими смесями феррита и цементита и отличаются лишь размерами пластинок феррита и цементита.
Перлит П - это механическая смесь феррита с цементитом. Перлит содержит 0 8 % глерода, обладает высокими прочностью и пругостью, пластичность его не очень высокая.
Перлит ( П) - тесная механическая смесь феррита и цементита, которую называют эвтектоидной смесью. Перлит содержит 0 83 % глерода, обладает высокой прочностью и пругостью, но незначительной вязкостью.
Как называется структура, представляющая собой механическую смесь феррита и цементита.
Перлит, сорбит, троостит ] представляют собой механическую смесь феррита и цементита.
Перлит представляет собой 6oj: ее или менее грубую механическую смесь феррита и цементита. Перлит образуется при малых скоростях охлаждения стали, нагретой до аустенитного состояния.
С 0 1 3 - 0 83 % превращаются в механическую смесь феррита и перлита. При С0 83 % аустенит стали превращается в чистый перлит, при С 0 83 % сталь превращается в механическую смесь перлита и цементита.
Схемы диаграмм изотермического превращения переохлажденного аустенита.| Схемы феррито-цементитных структур. - г перлит. б - сорбит. в - троостит. Перлит, сорбит, троостит являются структурами одной природы - механической смесью феррита и цементита и отличаются друг от друга лишь степенью дисперсности.
Перлит ( П) - эвтектоид системы Fe - Fe3C - механическая смесь феррита и цементита, содержащая 0 8 % глерода. Перлит состоит из пластинок цементита в ферритной основе, на травленом шлифе имеет блеск перламутра, отсюда и название - - перлит. Внешне зерно перлита состоит из параллельных пластинок цементита и феррита.
Если степень переохлаждения аустенита невелика, то он полностью распадается на механическую смесь феррита и цементита разной степени дисперсности.
Влияние содержания кислорода на механические свойства малоуглеродистой стали.
После достижения температуры 592 С, отвечающей точке Ах, нитроаустенит-эвтектоид распадается на механическую смесь феррита и нитрида железа.
Схема для определе - должен бЫТЬ Таким, ЧОбы при ГО СНЯ. Например, у отливок из серого чугуна поверхностный слой состоит из перлитной корки ( механическая смесь феррита и цементита), наружная зона которого нередко имеет следы формовочного песка. Этот слой должен быть полностью дален на первом переходе для последующей нормальной работы инструмента.
Сфероидизации и графитизации перлита подвержены только стали перлитного класса, у которых структурная составляющая представляет собой механическую смесь феррита к перлита. Стали аустенит-ного класса обладают большей стабильностью структуры при температурах от 500 С и выше. Однако эти стали по сравнению со сталями перлитного класса значительно дороже, имеют пониженную пластичность при комнатных температурах, повышенную вязкость и высокий коэффициент линейного расширения, вызывающий при нагреве внутренние напряжения.
Сфероидизации и графитизации перлита подвержены только стали перлитного класса, у которых структурная составляющая представляет собой механическую смесь феррита и перлита.
Сфероидизации и графитизации перлита подвержены только стали перлитного класса, у которых структурная составляющая представляет собой механическую смесь феррита и перлита. Стали аустенит-ного класса обладают большей стабильностью структуры при температурах от 500 С и выше. Однако эти стали по сравнению со сталями перлитного класса значительно дороже, имеют пониженную пластичность при комнатных температурах, повышенную вязкость и высокий коэффициент линейного расширения, вызывающий при нагреве внутренние напряжения.
Таким образом, можно сделать вывод, что структуры перлита, сорбита и троостита являются механической смесью феррита и цементита и отличаются одна от другой только степенью дисперсности пластинок цементита.
При охлаждении стали на воздухе со скоростью 40 - 80 С в 1 сек получается также механическая смесь феррита и цементита. Однако в этом случае цементит находится в более крупных частицах. Такая смесь имеет наименование сорбит.
При нагреве до 200 - 300 в стали протекает второе превращение: остаточный аустенит распадается на механическую смесь феррита и цементита.
При содержании глерода более 0 025 % в стали наряду с ферритом наблюдается вторая структурная составляющая - перлит, представляющая собой механическую смесь феррита и цементита. Перлит прочнее и тверже феррита.
Структура глеродистых сталей определяется тремя составляющими ( фазами): ферритом - твердый раствор глерода в а-железе, цементитом - - карбиджелева Fe3C и перлитом - механическая смесь феррита и.
Структура глеродистых сталей определяется тремя составляющими ( фазами): ферритом - твердый раствор глерода в а-железе, цементитом - карбид железа Fe3C и перлитом - механическая смесь феррита и цементита.
При нагреве до 200 - 300 С в стали протекает второе пре - j вращение: распад второй структурной составляющей закаленной стали - остаточного аустенита на механическую смесь феррита и цементита.
Сталь после изотермического превращения при 700 С - пластинчатый перлит ( х500. травление 4 % - ным спиртовым раствором азотной кислоты.| Сталь после изотермического превращения при 650 С - сорбит ( х500. травление 4 % - ным спиртовым раствором азотной кислоты. Таким образом, сорбит отпуска является продуктом распада мартенсита. Он представляет собой механическую смесь феррита и округлых зерен цементита, но более грубого строения, чем троостит. Иногда сорбит сохраняет форму игл мартенсита, из которого он был получен в результате отпуска закаленной стали. В этом случае при обычных величениях сорбит отпуска трудно отличить от мартенсита.
Он представляет собой механическую смесь феррита и цементита, отличающуюся от перлита большой дисперсностью составляющих и более высокой твердостью.
Сорбит представляет собой механическую смесь феррита и цементита, более дисперсную, чем перлит. Еще более тонкое строение отличает тро-остит.
Перлит по сравнению с нелегированным ферритом обладает большей эрозионной прочностью. Поскольку перлит представляет собой механическую смесь феррита и цементита, то его свойства, следовательно, и сопротивление разрушению зависят от свойств этих составляющих, их дисперсности и формы. Глобулярная форма меньшает поверхность карбидной фазы, поэтому ее частие в сопротивлении разрушению резко снижается.
Эвтектоидная сталь с 0 8 % С - перлит ( хЮОО. травление 4 % - ным спиртовым раствором азотной кислоты. На рис. 15.4 дана микроструктура перлита. Перлит - это эв-тектоид - механическая смесь феррита и цементита, получающаяся в результате распада аустенита с 0 8 % С. После травления 4 % - ной азотной кислотой в спирте на шлифе получается микрорельеф.
Эвтектоидная сталь с 0 8 % С - перлит. - микроструктура ( Х500. б-схема микроструктуры. На рис. 14.4 дана микроструктура перлита. Перлит - это эвтектоид - механическая смесь феррита и цементита, получающаяся в результате распада аустенита с 0 8 % С.
Эвтектоидная линия P S K ( 733 С) соответствует равновесию трех фаз: графита, аустенита ( состава S) и феррита. При температуре 733 С аустенит распадается с образованием механической смеси феррита и графита, называемой графитным эвтектоидом в отличие от метастабильного эвтектонда - перлита.
№13 Ледебурит имеет сотовое или пластинчатое строение. При медленном охлаждении образуется сотовый ледебурит, представляющий собой пластины цементита, проросшие разветвленными кристаллами аустенита. Пластинчатый ледебурит состоит из тонких пластин цементита, разделенных аустенитом, и образуется при быстром охлаждении. Сотовое и пластинчатое строение не редко сочетается в пределах одной эвтектической колонии. Заэвтектические чугуны (4,3 - 6,67 % С) начинают затвердевать с понижением температуры по линии ликвидус CD, когда в жидкой фазе зарождаются и растут кристаллы цементита, концентрация глерода в жидком сплаве с понижением температуры меньшается по линии ликвидус. При температуре 1147С жидкость достигает эвтектической концентрации 4,3 %С ( точка С) и затвердевает с образованием ледебурита. После затвердевания заэвтектические чугуны состоят из первичного цементита и ледебурита.
Сплавы, содержащие до 2,14% С, называют сталью, более 2,14 % С - чугуном. Принятое разграничение между сталью и чугуном совпадает с предельной растворимостью глерода в аустените. Стали, после затвердевания, не содержат хрупкой структурной составляющей - ледебурита - и при высоком нагреве имеют только аустенитную структуру, обладающую высокой пластичностью. Поэтому стали легко деформируются при нормальных и пониженных температурах, т.е. являются в отличие от чугуна ковкими сплавами.
По сравнению со сталью чугуны обладают значительно лучшими литейными свойствами и, в частности, более низкими и температурами плавления, имеет меньшую садку, это объясняет присутствием в структуре чугуна легкоплавкой эвтектики (ледебурита).
№1Перлит (от фр. perle - жемчужина) - одна из структурных составляющих железоуглеродистых сплавов - сталей и чугунов: представляет собойэвтектоидную смесь двух фаз - феррита и цементита (в легированныхсталях - карбидов). Перлит - продукт эвтектоидного распада (перлитного превращения) аустенита при сравнительно медленном охлаждении железоуглеродистых сплавов ниже 727 C. При этом -железо переходит в -железо, растворимость глерода в котором составляет от 0,006 до 0,025%; избыточный глерод выделяется в форме цементита или карбидов. В зависимости от формы различают перлит пластинчатый (основной вид перлита; обе фазы имеют форму пластинок) и зернистый (округлые зёрнышки, или глобули, цементита располагаются на фоне зёрен феррита). С величением переохлаждения растёт число колоний перлита, то есть частков с однообразной ориентацией пластинок феррита и цементита (карбидов), сами пластинки становятся более тонкими. Механические свойства перлита зависят в первую очередь от межпластиночного расстояния (суммарная толщина пластинок обеих фаз): чем оно меньше, тем выше значение предела прочности и предела текучести и ниже критическая температура хладноломкости. При перлитной структуре облегчается механическая обработка стали. Дисперсные разновидности перлита называют сорбитом и трооститом. = 20%, НВ 160.в = 630 Па, = 15%, НВ 220; сталь с зернистым перлитом в = 820 Па, С. Содержание глерода в перлите для всех железоуглеродистых сплавов всегда постоянно и составляет 0,8%. В равновесии перлит имеет пластинчатое строение (см. микроструктуру). В результате термообработки можно получить перлит зернистый, но такая структура будет неравновесной. Механические свойства перлита зависят от степени измельченности частичек цементита и формы цементита. Сталь со структурой пластинчатого перлита имеет такие свойства: Перлит (П) - эвтектоидная механическая смесь, состоящая из двух фаз: феррита и цементита. Перлит образуется из аустенита определенного состава (0,8% С) при температуре 727
№1Углеродистая сталь - сталь, не содержащая легирующих компонентов. В зависимости от содержания глеродауглеродистую сталь подразделяют на низкоуглеродистую (до 0,25% С), среднеуглеродистую (0,2Ч0,6% С) ивысокоуглеродистую (более 0,6% С). Различают глеродистую сталь обыкновенного качества и качественную конструкционную. К 1-й группе относится горячекатаная (сортовая, фасонная, толстолистовая, тонколистовая, широкополосная) и холоднокатаная (тонколистовая) сталь; во 2-ю входят горячекатаные и кованые заготовки диаметром (или толщиной) до 250 мм, калиброванная сталь и серебрянка.
Углеродистую сталь выплавляют в мартеновских, двухванных, дуговых печах и кислородных конвертерах. Дляраскисления глеродистой стали используют ферромарганец, ферросилиций, феррованадий, алюминий, титан и др.; по степени раскисления различают кипящую, полуспокойную и спокойную глеродистую сталь. Для лучшения физико-химических и технологических свойств применяют микролегирование глеродистой стали титаном, цирконием, бором,редкоземельными элементами. В результате микролегирования сталь приобретает мелкозернистую структуру, меньшается степень зональной ликвации, снижаются загрязнённость стали неметаллическими включениями и склонность к образованию трещин при горячей пластической деформации, повышается дарная вязкость при отрицательных температурах, что даёт возможность применять глеродистую сталь в различных климатических зонах (от - 40 до 60 С). глеродистую сталь разливают на слитки (сверху, сифоном) и заготовки (на машинах непрерывного литья); масса слитков достигает 35 т. Кроме того, глеродистая сталь используется для получения стальных отливок. Литая глеродистая сталь отличается от деформируемой стали подобного состава несколько меньшими пластичностью иударной вязкостью.
Углеродистая сталь - наиболее распространённый вид чёрных металлов.
№1Сталь представляет собой сплав железа с глеродом, в которой неизбежно будут находиться и другие примеси в виде различных элементов и их соединений.
Металлы и их сплавы в отличие от неметаллов обладают характерным блеском, непрозрачностью, высокими тепло- и электропроводностью, прочностью и вязкостью. При комнатной температуре большинство металлов находится в твердом состоянии.
Принято делить металлы и сплавы на черные и цветные. К черным металлам относят железо и его сплавы с глеродом и другими элементами - сталь и чугун. К цветным металлам относят медь, алюминий, цинк, свинец, олово, титан и их сплавы.
Чистые металлы применяют в технике сравнительно редко. Наиболее широко используют сплавы. Сплавы представляют собой сочетание различных металлов, также металлов с неметаллами.
Углеродистая сталь, из которой изготовляют основную массу проволоки, не содержит специальных добавок, но всегда имеет небольшое количество неизбежных примесей. Кроме того, она может содержать небольшое количество никеля, хрома, меди и других элементов. Примеси попадают в сталь из руды, лома, топлива и раскислителей, применяемых при выплавке стали.
Конструкционная глеродистая сталь содержит от 0,05 до 0,75 % С. В зависимости от содержания глерода стали присваивают определенную марку.
Инструментальная глеродистая сталь содержит от 0,60 до 1,25 % С. Марки инструментальной глеродистой стали: У7, У8, У9, У10 и У12. Их обозначение также определяется содержанием глерода. Кроме того, широко используются высококачественные инструментальные глеродистые стали с пониженным содержанием серы и фосфора (вредных примесей). В конце обозначения таких сталей имеется еще буква А (например, УА, У1А и др.).
Автоматная сталь с содержанием глерода от 0,08 до 0,45 % отличается повышенным содержанием серы (0,08-0,3%) и фосфора (0,08-0,15%), что позволяет легче вести обработку резанием. Эта сталь используется для производства калиброванного металла.
Легированная сталь содержит один или не сколько легирующих элементов (хром, никель, марганец, вольфрам, молибден, ванадий, кобальт и др.), которые вводят с целью получения заданных свойств. Для добства основные элементы, вводимые в легированную сталь, обозначают словно русскими буквами, их количества - числами. Приняты следующие обозначения: X - хром, Н - никель, Т - титан, Г - марганец, П - фосфор, М -молибден, Д - медь, С - кремний, Ф - ванадий, Ю - алюминий, В - вольфрам, К - кобальт.
Классификация сталей
- По химическому составу: глеродистые и легированные Углеродистые:
низкоуглеродистые - до 0,35 % С среднеуглеродистые - 0,35-0,70% С высокоуглеродистые - 0,70-2,14% С Легированные:
низколегированные - до 1% легирующих элементов среднелегированные - до 12% легирующих элементов высоколегированные - до 40% легирующих элементов
- По назначению:
конструкционные (для деталей машин, приборы);
инструментальные (для режущего инструмента, жаростойкие, жаропрочные)
- По степени раскисления:
спокойные СП - раскисленные Mn. Si. Al;
полуспокойные ПС - промежуточные между СП и КП;
кипящие КП - раскисленные Mn.
- По качеству:
обыкновенного качества S<0,05; P< 0,06;
качественные S<0,04; P< 0,035;
высококачественные S,Р < 0,025;
особовысококачественные.
Влияние глерода и других постоянных примесей на свойства стали С величением концентрации глерода в структуре стали возрастает содержание цементита. Структура доэвтектоидной стали (С < 0,8 %) состоит из феррита и перлита, заэвтектоидной (C > 0,8 %) - из перлита и цементита.
Феррит имеет низкую прочность, пластичен. Цементит отличается высокой твердостью, но хрупок, поэтому с величением содержания глерода в стали величиваются ее твердость, прочность, меньшаются вязкость и пластичность. На рисунке приведена механических свойств стали от содержания глерода.
Однако величение прочности происходит лишь до тех пор, пока содержание глерода не достигнет 0,8...1 %. После этого в структуре стали по границам зерен перлита появляется сетка хрупкого цементита, которая легко разрушается при нагрузках. Чтобы получить зернистый перлит, странив сетку цементита, заэвтектоидные стали подвергают отжигу.
С величением содержания глерода худшаются свариваемость стали и способность деформироваться в горячем и особенно в холодном состоянии.
Хорошо обрабатываются резанием среднеуглеродистые стали (содержание С 0,3...0,4 %). Низкоуглеродистые при механической обработке дают плохую поверхность. Высокоуглеродистые стали имеют повышенную твердость и снижают стойкость инструмента.
Полезные примеси - кремний и марганец - всегда присутствуют в стали, растворяются в феррите, прочняя его. Марганец величивает прокаливаемость стали, меньшает влияние серы. Кремний и марганец применяют для раскисления стали. В глеродистой стали содержится до 0,8 % Мn и до 0,4 % Si.
Постоянные примеси, от которых зависит качество стали, - сера и фосфор. Источником этих химических элементов в стали является прежде всего чугун, из которого производят сталь в металлургических печах. Сера и фосфор - вредные примеси. Сера понижает пластичность, вязкость, придает стали красноломкость при прокатке и ковке. Сера нерастворима в стали и образует эвтектику Fе-FеS с tпл = 988 С, располагающуюся по границам зерен. При горячей деформации эвтектика сообщает стали хрупкость, даже плавится и образует в металле надрывы и трещины. Присутствующий в сталимарганец превращается в сульфид МnS с tпл = 1620С, что выше температур горячей обработки, поэтому он не образует эвтектику по границам зерен. МnS снижает вязкость и пластичность, меньшает сталостную прочность стали.
Фосфор при концентрации до 1,2% растворяется в феррите, меньшая его пластичность; сильно ликвирует. Располагаясь вблизи границ зерен, величивает их хрупкость при низких температурах. Это явление называется хладноломкостью. Газы, присутствующие в стали, образуют химические соединения, в свободном состоянии находятся в порах или в виде твердых растворов - в феррите.
Кислород и азот дают хрупкие неметаллические включения, снижают вязкость и пластичность стали.
Водород находится в твердом растворе и значительно величивает хрупкость стали, способствует образованию внутренних трещин в хромистых и хромоникелевых сталях (флокены).
Для даления газов применяют раскисление и вакуумирование.
Влияние легирующих элементов на свойства стали Легирование выполняют для изменения механических (прочность, пластичность, вязкость), физических (электропроводность, магнитные характеристики) и химических (коррозионная стойкость) свойств стали. Легирующие элементы по-разному влияют на аллотропические превращения в железе, образование карбидов, фазовые превращения в стали. Эти элементы изменяют физические, химические, технологические и механические свойства стали и сплавов.
Рассмотрим некоторое элементы.
Хром Сr повышает твердость, прочность, вязкость, износостойкость, повышает коррозионную стойкость, также пластичность, но понижает теплопроводность.
Никель Ni повышает прочность, твердость, вязкость при низких температурах, прокаливаемость и коррозионную стойкость стали и при этом незначительно снижает пластичность. От содержания никеля в стали зависят ее электросопротивление и коэффициент теплового расширения. Никель - дорогой металл, поэтому в конструкционные стали его вводят вместе с хромом и другими элементами, притом в предельно минимальном количестве.
Вольфрам W меньшает отпускную хрупкость, повышает твёрдость, износостойкость, жаропрочность, понижает вязкость и способствует образованию мелкого зерна.
Молибден Мо повышает твердость, прочность, прокаливаемость, обрабатываемость резанием, жаропрочность, способствует образованию мелкозернистой структуры, лучшает свариваемость и механические свойства стали после цементации, меньшает вязкость и отпускную хрупкость стали.
Кремний Si при содержании 0,8 % и больше значительно повышает твердость, прочность, пругость и одновременно снижает вязкость стали. Сталь с содержанием кремния 0,8... 1,2 % применяют при строительстве мостов и других сооружений, с содержанием кремния 1,5...2 % Чдля изготовления пружин и рессор, 1...4 % -трансформаторов и динамомашин.
Марганец Мn при содержании в стали 1 % и больше повышает ее прочность и твердость, но снижает вязкость, величивает прокаливаемость, износостойкость и лучшает свариваемость стали.
Ванадий V повышает твердость, прочность, вязкость, стойчивость против динамических напряжений и износа, меньшает отпускную хрупкость, измельчает структуру и повышает стойчивость против перегрева при закалке.
Титан Тi повышает твердость, прочность, износостойкость, но снижает прокаливаемость стали. лучшает свариваемость нержавеющих сталей, снижает ликвацию.
№1К глеродистым сталям относятся сплавы железа с глеродом с массовой долей глерода от 0,02 до 2,14 %.
Основными компонентами глеродистых сталей являются железо и глерод.
Железо является полиморфным металлом, имеющим разные кристаллические решетки в различных температурных интервалах. При температурах ниже 910 С, железо существует в -модификации, кристаллическое строение которой представляет собой объемно-центрированную кубическую решетку. Эта аллотропическая модификация железа называется -железом. В интервале температур от 910 С до 1392 С существует -железо с гранецентрированной кубической решеткой.
Углерод является неметаллическим элементом, обладающим полиморфизмом. В природе встречается в виде графита и алмаза. В глеродистых сталях эти компоненты взаимодействуют, образуя, и зависимости от их количественного соотношения и температуры, разные фазы, представляющие собой однородные части сплава. Это взаимодействие заключается том, что глерод может растворяться как в жидком (расплавленном) железе, так и в различных его модификациях в твердом состоянии. Кроме того, он может образовывать с железом химическое соединение. Таким образом, в глеродистых сталях различают следующие фазы: жидкий сплав (Ж), твердые растворы - феррит (Ф) и аустенит (А) и химическое соединение цементит (Ц),
Феррит - твердый раствор внедрения глерода в -железе. Имеет объемно-центрированную кубическую решетку и содержит при нормальной температуре 0,006 % глерода. У феррита низкие твердость (HB == 790 Па) и прочность (6 = 245 Па), высокие пластичность ( = 50 %, = 85 %) и дарная вязкость (KCU == 2940 кДж/м2).
Аустенит - твердый раствор внедрения глерода в -железе, при нор-мальной температуре в глеродистых сталях в равновесном состоянии не существует.
Цементит - химическое соединение железа с глеродом, карбид железа Fc3C. Он обладает сложной кристаллической решеткой, содержит 6,67 % глерода. Для цементита характерна высокая твердость (НV = 9800 Па) и очень низкая пластичность. Согласно фазовой диаграмме "железо - цементит" (рис. 1а) глеродистые стали при нормальной температуре состоят из двух фаз - феррита и цементита. Одному проценту глерода соответствует 15 процентов цементита. Исходя из этого массовая доля цементитной фазы находится множением массовой доли глерода, содержащегося в стали, на 15. Поскольку в феррите содержится очень малая доля процента глерода, то практически весь глерод, имеющийся в стали, входит в состав цементита.
Поэтому величение массовой доли глерода в стали ведет к величению массовой доли цементитной фазы, что приводит к повышению твердости и прочности, понижению пластичности и дарной вязкости.
Фазы в глеродистых сталях определенным образом располагаются в их объемах, образуя в зависимости от массовой доли глерода, ту или иную структуру.
Равновесные структуры глеродистых сталей казываются на структурной диаграмме "железо - цементит" (рис.16). По сопоставлению с эвтектоидным составом глеродистые стали подразделяются на: доэвтектоидные, эвтектоидную и заэвтектоидные.
Эвтектоидная сталь содержит 0, 8% С и имеет перлитную структуру (рис.2б). Перлит Цэвтектоидная смесь феррита и цементита. Перлит любой глеродистой стали содержит 0,8% С. Строение перлита таково, что дисперсные частицы цементита равномерно расположены в ферритной основе. В литой, горячекатанной и кованой стали присутствует пластинчатый перлит, состоящий из перемежающих пластинок феррита и цементита. В отожженной стали присутствует зернистый перлит, где цементит находится в форме зернышек. На рис. 2б схематически изображено пластинчатое строение перлита, в котором темные полосы представляют тени на светлом фоне феррита от выступающих после травления шлифа цементитных частиц. При микроскопическом исследовании для случая большой степени дисперсности цементитных частиц или малых величений микроскопа двухфазное строение перлита может не выявляться. В таких случаях перлит выявляется и виде сплошного темного фона.
Доэвтектоидные стали содержат от 0,02 до 0,8% С и имеют ферритно-перлитную структуру (рис. 2а). Здесь светлые зерна - это феррит, темные (штрихованные) частки представляют собой перлит, являющийся двухфазной структурной составляющей, состоящей из пластинок феррита и цементита.
Количественное соотношение этих структурных составляющих зависит от массовой доли глерода в стали. Поскольку феррит содержит очень мало глерода (0,006 %), то основным носителем глерода в доэвтектоидной стали является перлит, характеризующийся постоянной массовой долей глерода (0,8%). Поэтому с величением в стали массовой доли глерода доля перлита и структуре величивается, феррита соответственно меньшается. Изменение структуры влечет за собой изменения механических свойств. Направление этих изменений можно определить на основе сопоставления свойств структурных составляющих. Перлит содержит 88% ферритной фазы и 12% цементитной и поэтому, по сравнению с ферритной структурной составляющей, обладает большей твердостью и прочностью. Следовательно, с величением массовой доли глерода в доэвтектоидной стали величивается доля перлита в ее структуре, что приводит к величению твердости и прочности и меньшению пластичности и дарной вязкости.
Структурно-свободный цементит (цементит вторичный) в объеме медленно охлажденной стали располагается вокруг перлитных зерен и металлографически это проявляется в виде цементитной сетки. Такое расположение вторичного цементита способствует повышению хрупкости и снижению вследствие этого, прочности. Поэтому от цементитной сетки избавляются путем отжига на зернистый перлит, добиваясь более равномерного распределения зерен цементита в стали.
№2Микроструктуру сплавов изучают под микроскопом при различных величениях на хорошо приготовленных шлифах. Для выявлениямикроструктуры сплавов применяют следующие методы: химическое травление, электролитическое травление, магнитный метод, тепловое травление, травление в расплавленных солях, катодное травление, силение рельефа микроструктуры после объёмных превращений. Для выявлениямикроструктуры используют специально подобранные кислоты и щёлочи различной концентрации, растворы различных солей и их смеси, различные составы электролитов, нагревание до различной температуры на воздухе или в специальной среде газов и паров, нагревание до определённых температур при пропускании электрического тока. На поверхности шлифа происходит растворение одних фаз, окисление и окрашивание других. В результате на шлифе под микроскопом можно видеть очертания зёрен и различных фаз, определить их взаимное расположение; по цвету, форме и размерам определить присутствующие в сплаве фазы, то есть выявить микроструктуру сплава.
К прямым методам исследования структурного состояния вещества относятсяоптическая металлография, электронная микроскопия, рентгеновский анализ и др.
Для изучения микроструктуры металлов используют металлографические микроскопы. Оптическим микроскопом можно исследовать и фотографировать детали микроструктуры, размеры которых не превышают 0,4-0,6 мкм. Полученное изображение микроструктуры можно величивать, но новые детали структуры при этом не выявляются. Для того чтобы более глубоко и подробно изучить строение мелкодисперсных структур и границ зерен, блочное строение и дислокационную структуру, применяют метод электронной микроскопии. Применение метода рентгеноструктурного анализа позволяет определить степень совершенства кристаллов, их ориентировку, глубоко изучить структурные изменения. Для решения задач рентгеноструктурного анализа используют дифрактометры.
№2По микроструктуре доэвтектоидной глеродистой стали в равновесном (отожженном) состоянии можно определить содержание глерода следующим образом. Структура такой стали феррит и перлит. Содержание глерода в феррите из-за незначительности этой величины (0,006%) не учитывают и считают, что весь глерод находится в перлите. Известно, что перлит содержит 0,80% С; поэтому, если известно количество перлита в общей массе металла, то, поскольку плотности феррита и перлита близки, можно определить содержание глерода в стали множением относительной площади (в процентах), занимаемой перлитом на просматриваемом поле шлифа, на 0,8. Правилом отрезков для заэвтектоидной стали пользуются реже ввиду трудности определения площади, занимаемой вторичным цементитом (см. рис. 29), и возможности допущения значительной погрешности.
Определение содержания глерода по микроструктуре в глеродистой стали, находящейся в неравновесном состоянии (в частности, после закалки и отпуска), невозможно, так как ее структура не характеризуется диаграммой железоЧуглерод.
Правило неприменимо также для легированной стали, поскольку ее фазовый состав и структура не определяются двойной диаграммой железоЧуглерод.
№2С ростом содержания глерода в структуре стали величивается количество цементита, при одновременном снижении доли феррита. Изменение соотношения между составляющими приводит к меньшению пластичности, также к повышению прочности и твердости. Прочность повышается до содержания глерода около 1%, затем она меньшается, так как образуется грубая сетка цементита вторичного. глерод влияет на вязкие свойства. величение содержания глерода повышает порог хладоломкости и снижает дарную вязкость.
Повышаются электросопротивление и коэрцитивная сила, снижаются магнитная проницаемость и плотность магнитной индукции.
Углерод оказывает влияние и на технологические свойства. Повышение содержания глерода худшает литейные свойства стали (используются стали с содержанием глерода до 0,4 %), обрабатываемость давлением и резанием, свариваемость. Следует учитывать, что стали с низким содержанием глерода также плохо обрабатываются резанием.
В широко применяемой в металлических сварных конструкциях стали марки типа содержание глерода находится в пределах 0,1Ч0,22%. глерод оказывает наибольшее влияние на свойства стали. При незначительной растворимости глерода почти весь он находится в стали в виде карбида, поэтому с величением содержания глерода повышаются временное сопротивление разрыву и предел текучести, и понижается пла-стичность стали. глерод, величивая чувствительность стали к перегреву и к скорости охлаждения, повышает закаливаемость стали и, следовательно, отрицательно влияет на ее свариваемость. Особенно сказывается влияние глерода на свойствах кипящей стали, имеющей большую склонность к ликвации - с повышением содержания глерода в стали величивается его содержание в ликвационных зонах.
В сварных конструкциях с величением содержания глерода в стали меньшается пластичность и повышается хрупкость околошовной зоны. Поэтому в стали, применяемой для сварных конструкций, проектируемых с четом перераспределения напряжений, рекомендуется ограничивать верхний предел содержания глерода. глерод повышает также хладноломкость стали и чувствительность ее к старению. В стали с малым содержанием глерода наблюдается структурно свободный цементит, сили-вающий хрупкость.
В глеродистых сталях с одинаковым временным сопротивлением разрыву, но разным отношением содержаний марганца и глерода (Мп С), при величении этого отношения от 2,5 до 11 критическая температура хрупкости снижается от 0 С до Ч25 С. Поэтому для сталей, применяемых при изготовлении металлоконструкций.
В работе рекомендовано для снижения хладноломкости стали величить отношение Мп С, проводя одновременно раскисление стали алюминием и нормализацию проката.
№2Чтобы облегчить изучение строения стали и чугуна, мы рассматривали их до сих пор как простые двойные сплавы железа с глеродом. Однако известно, что любая сталь и чугун имеют в своем составе в качестве неизбежных спутников кремний, марганец, фосфор и серу. У обычных сталей допускается следующее количество казанных примесей: кремния - до 0,4%, марганца - до 0,8%, фосфора - до 0,05%, серы - до 0,05%. Следует выяснить, как располагаются эти примеси в структуре стали и какое влияние они оказывают на ее свойства. Такие примеси, как марганец, кремний и фосфор, не образуют в структуре стали самостоятельных зерен, - они в основном растворяются в феррите. В кристаллической решетке феррита расположены, кроме атомов глерода, также и атомы кремния, марганца и фосфора. Следовательно, рассматривая структуру стали, мы этих примесей не видим. Сера в железе почти не растворима, в структуре стали она образует химические соединения - сернистое железо (FeS) или сернистый марганец (MnS). Сульфиды железа и марганца, также соединения кислорода с металлом (FeO, МпО), находящиеся в структуре стали, называют неметаллическими включениями. Они наблюдаются под микроскопом на нетравленом полированном микрошлифе. Влияние примесей на свойства стали неодинаково.
Наиболее серьезное влияние на свойства стали оказывает глерод. С величением содержания глерода твердость стали повышается, относительное длинение 5 и относительное сужение \|/ понижаются. Предел прочности и предел пругости стали повышаются с величением содержания глерода до 0,8-0,9%. При дальнейшем величении содержания глерода в структуре стали появляется свободный цементит, который располагается по границам зерен перлита в виде сетки. Вследствие исключительной хрупкости цементита понижается не только пластичность стали, но и ее пругость и прочность. Изменение механических свойств стали в зависимости от содержания глерода. Кремний и марганец в тех количествах, в каких они содержатся у обычной стали, не оказывают заметного влияния на ее свойства.
Сера и фосфор - вредные примеси стали. При повышенном содержании фосфора в стали наблюдается явление хладноломкости, т. е. сталь делается хрупкой, особенно при низкой температуре (на морозе). Причина этого явления состоит в том, что атомы фосфора, располагаясь в решетке железа, сильно искажают ее, так как атомы фосфора резко отличаются от атомов железа. Кроме того, фосфор неравномерно распределяется в стали, скапливаясь на отдельных частках в значительном количестве. Такое неравномерное распределение примесей в данном объеме стали и в объеме каждого кристалла называется ликвацией.
Вредное влияние фосфора особенно сильно проявляется в сталях с повышенным содержанием глерода, так как глерод меньшает растворимость фосфора и стали. Вытесненный из твердого раствора фосфор располагается в виде хрупкой эвтектики по границам структурных составляющих, ослабляет сцепление между ними и способствует хрупкости стали.
Повышенное содержание в стали серы вызывает явление красноломкости: в стали при обработке ее давлением при температурах 900 - 1200 образуются трещины. Причина этого заключается в том, что сернистое железо располагается по границам зерен железа в виде механической смеси, которая имеет температуру плавления 985. При высоких температурах эта смесь расплавляется, вследствие чего меньшается связь между зернами. Если сера находится в виде сернистого марганца, то она оказывает менее вредное влияние на свойства стали. Сернистый марганец имеет более высокую температуру плавления (1620), поэтому он затвердевает раньше стали и располагается не по границам зерен, обособленными частками. В отдельных случаях примеси серы и фосфора в стали играют положительную роль, так как способствуют хорошей обрабатываемости ее на станках. Поэтому у некоторых сталей допускается содержание серы до 0,3% и фосфора до 0,15%. Такие стали называются автоматными. Они используются для изготовления изделий на станках-автоматах.
Постоянные (технологические) примеси являются обязательными компонентами сталей и сплавов, что объясняется трудностью их даления как при выплавке (Р, S), так и в процессе раскисления (Si, Mn) или из шихты - легированного металлического лома (Ni, Сг и др.).
К постоянным примесям относят глерод, марганец, кремний, серу, фосфор, также кислород, водород и азот.
Постоянные примеси могут присутствовать в виде твердых и газообразных фаз. Однако они не оказывают существенного влияния на положение критических точек диаграммы Fe - FеС.
Характер влияния этих примесей на свойства сталей и сплавов определяется их возможностью образовывать самостоятельные фазы с основным компонентом, железом, также местом возникновения этих фаз.
№2В основу классификации легированных сталей заложены четыре признака:
равновесная структура;
структура охлаждения на воздухе;
химсостав;
назначение.
По равновесной структуре легированные стали подразделяются на доэвтектоидные, эвтектоидные, заэвтектоидные и ледебуритные и, следоватнльно, ферритные, феррито - перлитные, перлитные, перлито-цементитные. В ледебуритных сталях присутствует эвтектика (ледебурит), которая характерна для чугунов. Стали, легированные сильными аустенизаторами (C, Mn, Ni, Co, Cu), имеют расширенную -область и относятся к аустенитному классу. Стали, легированные сильными ферритообразующими элементами, относятся к ферритному классу (Cr, Mo, W, Ti и др.)
После нормализации (нагрев выше Асз и охлаждение на воздухе) легированные стали имеют следующие основные классы: ферритный, перлитный, мартенситный и аустенитный. Перлит может иметь структуру сорбита, тростита, бейнита в малолегированных сталях, мартенсита в легированных и аустенита (в высоколегированных).
По химсоставу стали классифицируются в зависимости от легирующих элементов: хромистые, марганцовистые, хромоникелевые, хромоникельмолибденовые и многие другие. Легированные стали могут быть низколегированные (до 3% легирующих элементов), среднелегированные (от 3 до 10%), высоколегированные (от 10 до 50%).
Легированные стали, как и глеродистые, делятся по качеству в зависимости от содержания вредных примесей (S и P), газов (H, N, O), неметаллических включений, способа выплавки, мехсвойств.
Стали обычного качества (общего назначения) содержат фосфора и серы ~ до 0,035 и 0,04 %; качественные до 0,025% каждого элемента, высококачественные (до 0,015% и до 0,025%) и особовысококачественные ( до 0,01% каждого элемента).
По назначению стали классифицируются на:
а) конструкционные;
б) инструментальные;
в) стали и сплавы с особыми свойствами.
№2Эта сталь отличается от стали обыкновенного качества меньшим содержанием вредных примесей, суженными пределами содержания глерода, кремния и марганца.
Сталь качественная конструкционная глеродистая поставляется в виде поковок и проката с последующей термической обработкой, обладает низкой прокаливаемостью и применяется в основном для производства сварных конструкций и деталей машин, подвергающихся действию механических нагрузок.
№2Инструментальная глеродистая сталь - сталь с содержаниемуглерода от 0,7 % и выше. Эта сталь отличается высокой твёрдостью и прочностью (после окончательной термообработки) и применяется для изготовления инструмента. Инструментальная глеродистая сталь делится на качественную и высококачественную. Содержание серы и фосфора в качественной инструментальной стали - 0,03 % и 0,035 %, в высококачественной - 0,02 % и 0,03 % соответственно.
Выпускается по ГОСТ 1435-99 следующих марок: У7; У8; УГ; У9; У10; У11; У12; У13; УА; УА; УГА; УА; У1А; У1А; У1А; У1А. Стандарт распространяется на глеродистую инструментальную горячекатаную, кованую, калиброванную сталь, серебрянку.
К группе качественных сталей относятся марки стали без буквы А(в конце маркировки), к группе высококачественных сталей, более чистых по содержанию серы и фосфора, также примесей других элементов - марки стали с буквой А. Буквы и цифры в обозначении этих марок стали означают: У - глеродистая, следующая за ней цифра - среднее содержание глерода в десятых долях процента, Г - повышенное содержание марганца.
Достоинство глеродистых инструментальных сталей состоит в основном в их малой стоимости и достаточно высокой твёрдости по сравнению с другими инструментальными материалами. К недостаткам следует отнести малую износостойкость и низкую теплостойкость.
№2Чугун - сплав железа с глеродом с содержанием более 2,14 % (точка предельной растворимости глерода в аустените на диаграмме состояний). глерод в чугуне может содержаться в виде цементита и графита. В зависимости от формы графита и количества цементита, выделяют: белый, серый, ковкий и высокопрочные чугуны. Чугуны содержат постоянныепримеси (Si, Mn, S, P), в некоторых случаях также легирующие элементы (Cr, Ni, V, Al и др.). Как правило, чугун хрупок.
№2Чугун представляет собой многокомпонентный сплав железа с глеродом, содержащий >2,1% С. Кроме глерода в чугуне обычно содержится (в %): до 4 Si; 2 Мп; 0,3 Р; 0,25 S, также 0,1 Cr, Ni или Cu.Классификация чугунов в зависимости от состояния глерода в сплаве:
белые,
серые,
ковкие,
высокопрочные чугуны.
В белом чугуне весь глерод находится в виде химического соединения с железом - цементита (FеС). Цементит обладает высокими твердостью (800 НВ) и хрупкостью, поэтому трудно поддается механической обработке. Из-за этого белые чугуны нашли ограниченное применение в качестве конструкционных материалов и служат в основном для получения ковких чугунов. При длительном обжиге белого чугуна цементит в нем распадается и глерод выделяется в свободное состояние.
Серые чугуны в изломе имеют серебристый цвет из-за наличия в них пластинчатых включений графита. Они широко используются в литейном производстве и выпускаются в соответствии с ГОСТ 1412-85. Прочность серого чугуна с пластинчатым графитом при растяжении находится в пределах 120...440 Па, твердость 140...290 НВ. Структура серых чугунов в зависимости от состава и словий охлаждения может быть с перлитной, перлитно-ферритной и ферритной основой.
Наличие свободного графита в чугуне (до 50 % С) оказывает влияние на его свойства. величение количества и размеров графитовых включений и неравномерность их распределения меньшают прочность чугуна. Вместе с тем, свободный графит придает чугуну износостойкость, высокие литейные свойства, хорошую обрабатываемость режущим инструментом и высокую сопротивляемость при знакопеременных нагрузках. Все это обусловливает широкое применение серого чугуна в качестве конструкционного материала.
Чугун, полученный из белого чугуна продолжительным отжигом при температуре 800...850oС, называют ковким. В отличие от серого чугуна в ковком глерод находится не в виде пластинчатого графита, в виде хлопьевидного. Ковкий чугун по сравнению с серым чугуном обладает более высокой прочностью (300... 630 Па), пластичностью и дарной вязкостью. Ковкий чугун имеет однородные свойства по сечению, в его отливках отсутствуют напряжения, ему при суши высокие механические свойства, он хорошо обрабатывается.
В зависимости от режима термообработки основа ковкого чугуна может быть ферритной или перлитной. Состав основных элементов в ковком чугуне (в %): 2,3...3 С; 0,9... 16 Si; 0,3... 1,2 Мn; >0,15и S. Основные характеристики ковких чугунов определены ГОСТ 1215-79. Ферритные чугуны отличаются более высокой пластичностью, перлитные обеспечивают лучшую износостойкость.
В промышленности получили распространение высокопрочные и легированные чугуны. Ввысокопрочном чугуне (ГОСТ 7293-85) глерод находится в виде шаровидного графита. Содержание основных элементов в таких чугунах составляет (в %): до 38 С; 2.9 Si; 0,9 Мn; 0,1 Сг; 0,02 S; 0,1 Р; 0,08 Mg. Чугуны с шаровидным графитом значительно превосходят по характеристикам серые чугуны. в частности по износо-, жаро- и коррозионной стойкости.
№2В сером чугуне весь глерод или значительная его часть находятся в свободном состоянии в виде чешуек графита.
В ковком чугуне глерод полностью или частично входит в состав хлопьевидных включений глерода отжига. Получается путем термической обработки белого чугуна.
В высокопрочном чугуне глерод образует шаровидные включения графита.
Таким образом, отличительной особенностью каждой группы чугунов является химическое состояние глерода (связан в цементит или свободен) и форма графитных включений.
Ковкий чугун, как и серый, состоит из сталистой основы и содержитуглерод в виде графита, однако графитовые включения в ковком чугуне иные, чем в обычном сером чугуне. Разница в том, что включения графита в ковком чугуне расположены в форме хлопьев, которые получаются при отжиге, и изолированны друг от друга, в результате чего металлическая основа менее разобщена, и чугун обладает некоторой вязкостью ипластичностью. Из-за своей хлопьевидной формы и способа получения (отжиг) графит в ковком чугуне часто называют глеродом отжига.
Высокопрочный чугун - чугун, имеющий графитные включения сфероидальной формы.
Графит сфероидальной формы имеет меньшее отношение его поверхностик объему, что определяет наибольшую сплошность металлической основы, следовательно, и прочность чугуна. Структура металлической основы чугунов с шаровидным (сфероидальным) графитом такая же, как и в обычном сером чугуне, то есть, в зависимости от химического состава чугуна, скорости охлаждения (толщины стенки отливки) могут быть получены чугуны со следующей структурой: феррит + шаровидный графит (ферритный высокопрочный чугун), феррит + перлит + шаровидный графит (феррито-перлитный высокопрочный чугун), перлит + шаровидный графит (перлитный высокопрочный чугун).
Наиболее часто применяется для изготовления изделий ответственного назначения в машиностроении, также для производства высокопрочных труб (водоснабжение, водоотведение, газо-, нефте-проводы). Изделия и трубы из Высокопрочного чугуна отличаются высокой прочностью, долговечностью, высокими эксплуатационными свойствами. Чугуны с пластинчатым, шаровидным, вермикулярным и хлопьевидным графитом: ЧПГ, ЧШВ, ЧВГ, ЧХГ. Механические свойства чугунов. Антифрикционные и легированные чугуны.
Графит в чугунах существует в следующих формах:
- п л с т и н ч т ы й графит, в виде лепестков, прожилок; - в е р м и к у л я р н ы й (или мелкопластинчатый) графит, разновидность первого, при этом пластины похожи на нити; - ш р о в и д н ы й (глобулярный) графит; - х л о п ь е в и д н ы й графит. Возможные формы графита в чугуне показаны на рис. 32.
№3Практически наиболее важными элементами, всегда входящими в состав чугунов, являются кремний и марганец. Изменяя в чугуне содержание кремния при постоянном содержании марганца, получают различное количество глерода в свободном виде, т.е. различную степень графитизации [1, с. 8].
Фактором, обуславливающим получение серого чугуна при кристаллизации, т.е. способствующим графитизации - выделению глерода в равновесном состоянии, является прежде всего малая скорость охлаждения. меньшение по той или иной причине скорости охлаждения (изменение материала формы, величение толщины стенки отливки) способствует большей степени графитизации, т.е. выделение большей части глерода в форме графита.
Степень графитизации определяет структуру металлической основы серого чугуна. В зависимости от того, какая часть глерода содержится в чугуне в связанном состоянии, различают чугуны с ферритной, феррито-перлитной и перлитной основами.
№3Белый чугун - вид чугуна, в котором глерод в связанном состоянии в виде цементита, в изломе имеет белый цвет и металлический блеск. В структуре такого чугуна отсутствуют видимые включения графита и лишь незначительная его часть (0,03-0,30 %) обнаруживается тонкими методами химического анализа или визуально при больших величениях. Основная металлическая масса белого чугуна состоит из цементитной эвтектики, вторичного и эвтектоидного цементита, алегированного белого чугуна - из сложных карбидов и легированного феррита.
№3Отбелённый чугун, половинчатый чугун - серый или высокопрочный чугун со структурой белого чугуна в периферийных частях отливки. Отбелённый чугун применяют в износостойких, прочных и термостойких отливках (лемехов плугов, ободей вагонных колёс, носиков коромысел клапанов и других отливок). Структуру белого чугуна получают величением скорости охлаждения отливки с помощью становленных в литейную форму металлических холодильников, окрашиванием литейной формы краской с карбидообразующими элементами, например, Te, расплавлением периферийных частей отливки с последующим быстрым охлаждением
№3Половинчатый чугун Химический состав половинчатого чугуна представляет собой объединение таких компонентов, как перлит, ледебурит, пластинчатый графит. глерод представлен в виде цементита.
№3Изучение микроструктуры начинают с рассмотрения шлифа в нетравленном виде, т. е. после полирования и промывки. В этом случае в поле зрения микроскопа можно заметить отдельные, обычно небольшие, темные частки. Они могут представлять: а) неметаллические включения; б) мелм-кие поры; в) структурные составляющие, характерные для некоторых сплавов (например, графит в сером чугуне).
Неметаллические включения в стали и чугуне, вследствие их большой хрупкости, могут частично или полностью выкрошиться при шлифовании и полировании. Кроме того, неметаллические включения обладают меньшей отражающей способностью, чем металлы. По этим причинам частки оксидов, сульфидов и силикатов кажутся в поле зрения микроскопа темными.
Количество и характер распределения неметаллических включений определяются сравнением вида наблюдаемой поверхности микрошлифа (обычно при величении в 100 раз) со специально разработанными шкалами включений.
Природа включений при микроанализе может быть становлена: 1) специальным травлением, вызывающим растворение или окрашивание включений; 2) наблюдением шлифа в поляризованном или льтрафиолетовом свете.
Микропоры, представляющие собой глубления в микрошлифе, также обнаруживаются в виде темных частков. Чтобы отличить микропоры от включений, шлиф слегка выводят из фокуса, поворачивая микрометрический винт микроскопа, и снова наводят на фокус; при этом края микропор, в отличие от неметаллических включений, то сходятся, то расходятся.
№36
Наименование реактива Состав реактива
(относительная
плотность) Назначение и особенности применения Для травления глеродистых, низко- и среднелегированных сталей и чугуна Спиртовой раствор азотной кислоты
(реактив Ржешотарского) Азотная кислота (1,42) 1-5 мл Этиловый или метиловый спирт 100 мл Реактивы окрашивают перлит в темный цвет, выявляют границы зерен феррита, структуру мартенсита и продуктов отпуска. Применяются также для выявления структуры азотированной и цементированной стали. С величением количества азотной кислоты возрастает скорость травления. Продолжительность травления - от неско-льких секунд до минуты Спиртовый раствор пикриновой кислоты
(реактив Ижевского) Пикриновая кислота (кристаллическая) 4г Этиловый или метиловый спирт 100 мл
№3Чугун маркируется буквами СЧ и цифрами, первая из которых характеризует предел прочности чугуна данной марки при растяжении, вторая - при изгибе (кг/мм2). Наибольшее распространение получили чугуны марок: СЧ12-28; СЧ15-32; СЧ18-36; СЧ 21-40; СЧ 24-44; СЧ 28-48; СЧ 32-52; СЧ 38-60, причем первые пять марок имеют перлитно-ферритную металлическую основу, последние три - перлитную. Прочность серых чугунов всех марок при сжатии значительно превышает прочность при растяжении. Например, для чугуна марки СЧ 24-44, имеющего предел прочности при растяжении 24 кгс/мм2, предел прочности при сжатии составляет 85 кгс/мм2. Для величения прочности чугуна графитовым включением придают шарообразную форму путем введения магния в ковш перед разливкой. При этом чугун приобретает и некоторую пластичность. Высокопрочные чугуны маркируют буквами ВЧ и цифрами, первая из которых характеризует временное сопротивление чугуна при растяжении (кгс/мм2), вторая - относительное длинение (%). Например, ВЧ 60-2 или ВЧ 40-10.
Ковкие чугуны маркируют буквами КЧ и цифрами, обозначающими временные сопротивления при растяжении (кгс/мм2) и относительное длинение (%). Примерами марок ковких чугунов могут служить КЧ 38-8; КЧ 35-10; КЧ 37-12; КЧ 30-6 с ферритной металлической основой и КЧ 45-6; КЧ 50-4 и КЧ 60-3, имеющие ферритно-перлитную основу.
При данном составе структура чугуна в большей степени зависит от скорости охлаждения.
При данном составе чугуна, например при постоянстве суммарного содержания глерода и кремния, также других элементов, входящих в его состав, можно получить цементитный, также перлитно-ферритный чугун.
№3Углерод в чугуне может содержаться в виде цементита и графита. В зависимости от формы графита и количества цементита, выделяют: белый, серый, ковкий и высокопрочные чугуны. Чугуны содержат постоянныепримеси (Si, Mn, S, P), в некоторых случаях также легирующие элементы (Cr, Ni, V, Al и др.). Как правило, чугун хрупок. глерод в чугуне может находиться в виде цементита, графита или одновременно в виде цементита и графита. Образование стабильной фазы - графита в чугуне может происходить в результате непосредственного выделения его из жидкого (твердого) раствора или вследствие распада предварительно образовавшегося цементита (при замедленном охлаждении расплавленного чугуна цементит может подвергнуться разложению РезС -> Fe + ЗС с образованием феррита и графита). Процесс образования в чугуне (стали) графита называют графитизацией.
Графит повышает износостойкость и антифрикционные свойства чугуна вследствии собственного смазочного действия и повышения прочности пленки смазочного материала. Чугуны с графитом, как мягкой и хрупкой составляющей, хорошо обрабатываются резанием (с образованием ломкой стружки) и обеспечивают более чистую поверхность, чем стали (кроме автоматных сталей).
Присутствие эвтектики в структуре чугунов обусловливает его использование исключительно в качестве литейного сплава. Высокие литейные свойства при небольшой стоимости обеспечили широкое применение чугунов в промышленности.
№39рафитизация, образование (выделение) графита в железных, никелевых, кобальтовых и др. металлических сплавах, в которых глерод содержится в виде нестойких химических соединений - карбидов. При повышенных температурах карбид полностью заменяется графитом. Скорость Графитизация величивается с повышением температуры. скоряютГрафитизация предварительной закалкой, деформацией, облучением. Графитизация стали обычно худшает её механические свойства (снижает прочность и пластичность). Вместе с тем графит, обладая смазочными свойствами, повышает износоустойчивость изделий. Графитизация железных сплавов используют при получении изделий из ковкого чугуна и графитизированной подшипниковой и штамповой стали. Для скорения Графитизация в сталь или чугун обычно вводят кремний или, реже, алюминий. Графитизация ряда сплавов (инструментальные режущие, пружинные, котельные и др. стали) снижает их эксплуатационные качества и является нежелательной. Графитизацияможно приостановить введением добавок (хрома, марганца и др.), величивающих стойчивость карбидов. Иногда подГрафитизация понимают образование графита в железоуглеродистых сплавах, не содержащих карбидов. Графит выделяется из пересыщенных глеродом сплавов при их затвердевании и последующем охлаждении.
№4Кремний способствует процессу графитизации, действует в том же направлении, что и замедление скорости охлаждения. Изменяя, с одной стороны, содержание в чугуне глерода и кремния и, с другой, - скорость охлаждения, можно получить различную структуру металлической основы чугуна. Структурная диаграмма для чугунов, показывающая, какой должна быть структура в отливке с толщиной стенки 50 мм, в зависимости от содержания в чугуне кремния и глерода показана на рис. 87 а. При данном содержании глерода, чем больше в чугуне количества кремния, тем полнее протекает процесс графитизации. Чем больше в чугуне глерода, тем меньше требуется кремния для получения заданной структуры
№41 Включения графита оценивают по количеству, определяемому по площади, занятой графитом в поле зрения микроскопа, и характеру их распределения. Степень взаимной изолированности этих включений оказывает сильное влияние на свойства чугуна: чем больше изолированность
включений графита, тем выше механические качества чугуна.
№4Кремний Si способствует графитизации чугуна, и лучшает его литейные свойства. В серых чугунах содержится 0,8 Е4,5 % Si.
Марганец Mn способствует отбеливанию чугуна, но содержание Mn до 1,2% полезно, т.к. величиваются твердость и прочность чугуна.
Фосфорповышает жидкотекучесть чугуна, поэтому допустимо его содержание до 0,4%, но в ответственных чугунных отливках содержится фосфора менее 0,15%, т.к. с ростом содержания его величивается хрупкость чугуна.
Сера S затрудняет графитизацию, величивает хрупкость и худшает жидкотекучесть чугуна, поэтому серы в чугунах должно быть не более 0,1%.
Серые чугуны делятся на модифицированные, высокопрочные и ковкие (табл. 2).
В серых чугунах графит имеет пластинчатую форму, в высокопрочных - шаровидную, в ковких - хлопьевидную.П римеры обозначения чугунов:
Формирование структуры чугуна происходит при затвердевании отливки. Основными факторами, влияющими на структурообразование чугуна, являются его химический состав (см. табл. ниже) и скорость охлаждения отливки в форме.
Химический элемент Серый чугун Высокопрочный чугун Ковкий чугун Углерод Повышенное содержание глерода приводит к меньшению прочности, твердости и величению пластичности; глерод лучшает литейные свойства чугуна Увеличенное содержание глерода лучшает литейные свойства чугуна Углерод - основной регулятор механических свойств ковкого чугуна; чугун обладает низкой жидкотекучестью и требует высокого перегрева Кремний Кремний (с четом содержания глерода) способствует выделению графита и снижает твердость, также меньшает садку; повышенное содержание кремния снижает пластичность и несколько величивает твердость С повышением содержания кремния возрастает предел прочности при растяжении, при дальнейшем величении содержания - меньшаются предел прочности при растяжении и относительное длинение Для ферритного ковкового чугуна суммарное содержание кремния и глерода должно быть 3,7-4,1%. Содержание кремния зависит от количества глерода и толщины стенки. При содержании кремния до 1,5% механические свойства сплава повышаются Химический элемент Серый чугун Высокопрочный чугун Ковкий чугун Марганец Марганец тормозит выделение графита, способствует размельчению перлита и отбеливанию чугуна; взаимодействуя с серой, нейтрализует ее вредное действие. Механические свойства чугуна повышаются при содержании марганца до 0,7-1,3 %, при дальнейшем величении - снижаются. Марганец величивает садку сплава С повышением содержания марганца меньшается доля феррита и величивается количество перлита; при этом повышается предел прочности при растяжении и меньшается относительное длинение. Для повышения износостойкости содержание марганца величивают до 1,0- 1,3% Марганец величивает количество связанного глерода, повышает прочность феррита. При повышении содержания марганца до 0,8-1,4% величивается количество перлита, прочность сплава повышается, но резко падает пластичность и дарная вязкость. В ферритном чугуне содержание марганца не должно превышать 0,6%, в перлитном - 1,0%
Магний
- Для образования графита шаровидной формы содержание магния должно быть не ниже 0,03%, церия не ниже 0,02% (остаточное содержание). При более низком содержании не весь графит получает шаровидную форму; часть его содержится в виде пластинок, что снижает механические свойства сплава. При повышенном содержании магния (и церия) в структуре сплава образуется цементит и, следовательно, снижаются механические свойства. Оптимальное содержание остаточного магния - 0,04-0,08% -
Химический элемент Серый чугун Высокопрочный чугун Ковкий чугун Сера Сера снижает прочность и пластичность, но несколько повышает износостойкость сплава, считается вредной примесью, придает чугуну красноломкость (образование трещин при высоких температурах), препятствует выделению графита Чем выше содержание серы в исходном чугуне, тем труднее получить полностью шаровидную форму графита и, следовательно, высокие механические свойства Содержание серы в ферритном ковком чугуне, модифицированном алюминием, может быть повышено до 0,2 %; при этом механические свойства возрастают за счет лучшения формы графита. Определяющее влияние на механические свойства чугуна оказывает отношение содержания марганца и серы, которое должно быть в пределах 0,8-3,0
Фосфор Фосфор на процесс графитизации глерода влияет слабо, но повышает жидкотекучесть сплава, придает чугуну хладноломкость, т. е. хрупкость Фосфор оказывает существенное влияние на структуру и механические свойства. Чтобы получить чугун с высокой пластичностью, содержание фосфора не должно превышать 0,08%. Для получения чугуна с невысокой пластичностью содержание фосфора величивают до 0,12-0,15% Фосфор оказывает такое же, как для серого чугуна влияние на структуру и механические свойства сплава Химический элемент Серый чугун Высокопрочный чугун Ковкий чугун Никель Никель - легирующий элемент, благоприятно влияет на выравнивание механических свойств в отливках с различной толщиной стенок, повышает твердость на 10 НВ. С величением содержания никеля возрастает коррозионная стойкость и лучшается обрабатываемость сплава Никель влияет на тепло- и электропроводность, также на коррозионную стойкость и жаростойкость сплава. С величением содержания никеля эти свойства повышаются Никель способствует графитизации глерода и величивает количество перлита в металлической основе сплава Хром Хром - карбидообразующий элемент. С величением хрома растет прочность и твердость отливок, замедляется процесс графитизации глерода С величением содержания хрома в определенных пределах повышается жаростойкость, коррозионная стойкость и износостойкость сплава Хром замедляет процесс графитизации глерода. Содержание хрома в сплаве не превышает 0,06-0,08%; повышение содержания до 0,1 -0,12% приводит к образованию в структуре сплава стойких карбидов Химический элемент Серый чугун Высокопрочный чугун Ковкий чугун Молибден Молибден - легирующий элемент; замедляет процесс графитизации глерода и способствует карбидообразованию. С величением содержания молибдена повышается твердость без худшения обрабатываемости и возрастает сопротивление износу - Молибден способствует измельчению перлита и графитовых включений, величивает предел прочности на 3-7 кгс/мм2 при содержании молибдена 0,5%; замедляет процесс графитизации глерода Медь Медь способствует графитизации глерода, величивает жидкотекучесть, повышает прочность и твердость сплава При содержании в сплаве 1 % меди прочность при растяжении повышается до 40%, текучесть - до 50 % и соответственно при 2% меди - до 65% и до 70%. Содержание меди более 2% препятствует образованию в структуре сплава шаровидного графита Медь способствует графитизации глерода и величивает содержание в сплаве перлита
№4Серые чугуны разделяют по структуре металлической основы и по размерам, форме и расположению графитных включений.
Количество химически связанного глерода в серых чугунах не превышает 2%, поэтому их металлическая основа аналогична сталям доэвтектоидной, эвтектоид-ной или заэвтектоидной.
По структуре металлической основы различают чугуны: на ферритной основе (феррит+графит); на фер-ритно-перлитной основе (феррит + перлит + графит); на перлитной основе (перлит+графит); на перлитно-це-ментнтной основе (перлит+цементит+графит).
Следовательно, структура серых литейных чугунов представляет собой сталистую металлическую основу с рассеянными в ней графитными включениями.
Микроструктура серых чугунов с различной металлической основой.По размерам, форме и расположению графита
различают чугуны с крупными, средними и мелкими графитными включениями; с
прямолинейными и завихренными включениями; с равномерным, гнездовым и эвтектическим расположением графита.
№46 Обыкновенный серый чугун имеет высокие литейные свойства, хорошо обрабатывается, но вязкость его низкая; отливки из этого чугуна не выдерживают дарной нагрузки. Это связано с тем, что выделившийся в чугуне свободный глерод имеет форму пластинок, которые действуют на металлическую основу чугуна как надрезы (трещины).
В настоящее время для получения высокопрочного чугуна применяют модифицирование - введение в жидкий расплав небольших количеств модификаторов - магния, кальция и др. Модифицированный серый чугун называют высокопрочным. Высокая прочность обеспечивается благодаря шаровидной форме графита, не пластинчатой, как в сером чугуне.
№4Высокопрочный чугун - чугун, имеющий графитные включения сфероидальной формы.
Графит сфероидальной формы имеет меньшее отношение его поверхностик объему, что определяет наибольшую сплошность металлической основы, следовательно, и прочность чугуна. Структура металлической основы чугунов с шаровидным (сфероидальным) графитом такая же, как и в обычном сером чугуне, то есть, в зависимости от химического состава чугуна, скорости охлаждения (толщины стенки отливки) могут быть получены чугуны со следующей структурой: феррит + шаровидный графит (ферритный высокопрочный чугун), феррит + перлит + шаровидный графит (феррито-перлитный высокопрочный чугун), перлит + шаровидный графит (перлитный высокопрочный чугун).
Наиболее часто применяется для изготовления изделий ответственного назначения в машиностроении, также для производства высокопрочных труб (водоснабжение,
водоотведение, газо-, нефте-проводы). Изделия и трубы из Высокопрочного чугуна отличаются высокой прочностью, долговечностью, высокими эксплуатационными свойствами.
№4Ковкий чугун - словное название мягкого и вязкого чугуна, получаемого из белого чугуна отливкой и дальнейшей термической обработкой. Используется длительный отжиг, в результате которого происходит распад цементита с образованием графита, то есть процесс графитизации, и поэтому такой отжиг называют графитизирующим.
Ковкий чугун, как и серый, состоит из сталистой основы и содержитуглерод в виде графита, однако графитовые включения в ковком чугуне иные, чем в обычном сером чугуне. Разница в том, что включения графита в ковком чугуне расположены в форме хлопьев, которые получаются при отжиге, и изолированны друг от друга, в результате чего металлическая основа менее разобщена, и чугун обладает некоторой вязкостью ипластичностью. Из-за своей хлопьевидной формы и способа получения (отжиг) графит в ковком чугуне часто называют глеродом отжига.
По составу белый чугун, подвергающийся отжигу на ковкий чугун, является доэвтектическим и имеет структуру ледебурит + цементит (вторичный) + перлит. Для получения структуры феррит + глерод отжига в процессе отжига должен быть разложен цементит ледебурита, вторичный цементит и цементит эвтектоидный, то есть входящий в перлит. Разложение цементита ледебурита и цементита вторичного (частично) происходит на первой стадии графитизации, которую проводят притемпературе выше критической (95Ч1 С); разложение эвтектоидного цементита происходит на второй стадии графитизации, которую проводят путём выдержки при температуре ниже критической (74Ч720 C), или при медленном охлаждении в интервале критических температур (76Ч720 C).
№4Классификация легирующих элементов Легирующие элементы по их влиянию на полиморфизм железа подразделяются на две группы:
1) легирующие элементы, расширяющие область стойчивости Y-модификации железа (группа никеля). К ним относятся никель, марганец, медь, кобальт и др. Часть диаграммы состояний сплавов железо - никель. Как видно из диаграммы, величение содержания никеля расширяет область стойчивости легированного аустенита и при значительном содержании никеля в сплаве легированный аустенит сохраняется до комнатных температур;
2) легирующие элементы, сужающие область стойчивости у-мо-дификации железа (группа хрома). Такими элементами являются хром, алюминий, молибден, вольфрам, ванадий, титан, кремний, бор, цирконий и др. Так, например, при большом содержании в стали хрома у-мо-дификация железа не образуется и при температурах ниже линии солидуса сталь состоит только из легированного феррита.
По отношению к глероду легирующие элементы также подразделяются на группу никеля и группу хрома. Легирующие элементы группы никеля (Ni, Co, Cu, Si, N) в словиях получения стали не образуют с глеродом стойчивых карбидов. Легирующие элементы группы хрома (Ti, V, Mn, Zr, Nb, Mo, W) образуют с глеродом стойчивые карбиды, как простые, например СгСз, так и сложные типа (FeCr)7C3.
№51
Кроме известного разделения легированных сталей по их химическому составу и по способу выплавки (кислая и основная электросталь, основная и кислая мартеновская сталь), отметим классификации, основанные на следующих признаках:
1) по структуре (состоянию), получаемой при скоренном охлаждении - на воздухе, т. е. после нормализации;
2) по структуре, получаемой при медленном охлаждении (в равновесном состоянии);
3) по назначению (применению).
Классификация по структуре, получаемой при охлаждении на воздухе. Эта классификация основывается на величении закаливаемости сталей по мере повышения в них содержания легирующих элементов.
Представим теперь, что образцы (одного и того же размера) сталей А, Б и В, нагретые до состояния аустенита, охлаждаются до атмосферной температуры на воздухе.
Lg времени
Это значит, что в стали будет образовываться сорбит или троостит закалки с пластинчатым строением цементита, подобно пластинчатому перлиту. Охлаждение стали Б с той же скоростью приведет к получению мартенсита, так как здесь кривая пересечет диаграмму изотермических превращений данной стали ниже линии М, т. е. в области мартенситного распада.
Наконец, у стали В переохлажденный аустенит имеет наибольшую стойчивость и при атмосферной температуре не распадается совершенно, мартенситная точка М у этой стали лежит ниже нормальной температуры.
Другими словами, охлаждение на воздухе стали В приведет к получению стойчивого при атмосферной температуре аустенита. Таким образом, при одной и той же скорости охлаждения (на воздухе), по мере величения в составе стали легирующих элементов, могут быть получены различные структуры и состояния стали: при небольшом содержании легирующих элементов - перлитообразные структуры различной дисперсности (перлит, сорбит, троостит), при большем - мартенсит и, наконец, аустенит.
С повышением в составе стали глерода содержание необходимого легирующего элемента для получения того или иного состояния и структуры может быть меньше, так как глерод также несколько способствует повышению стойчивости переохлажденного аустенита.
На этих принципах и построена классификация стали по структуре, получаемой при охлаждении на воздухе, предложенная французским ченым Гийе. По этой классификации сталь разделяют на три основных класса: аустенитный, мартенситный и перлитный. Для определения принадлежности стали к тому или иному классу ее в виде образцов толщиной 15-20 мм нагревают до состояния аустенита и затем охлаждают на воздухе.
Если испытуемая сталь приобретает структуру аустенита или мартенсита, ее соответственно относят к аустенитному или мар-тенситпому классу. К перлитному классу по этой классификации относят словно сталь, которая в результате охлаждения на воздухе испытывает любое диффузионное превращение аустенита, т. е. приобретает структуру перлита, сорбита или троостита-закалки.
Гийе привел также диаграммы,, которые приблизительно показывают, при каких составах, т. е. количестве глерода и легирующих элементов, можно получать
Здесь видно, что при наименьших добавках никеля и соответствующем содержании глерода сначала получаются стали перлитного класса, с дальнейшим повышением содержания никеля - стали мартенситного класса, при наибольшем содержании никеля - аустенитного класса.
Так как всегда возможны и такие состояния, когда наряду с мартенситом наблюдается аустенит или троостит (его мы относим к классу перлита), то могут существовать и стали промежуточных классов мартенсито-трооститных или мартенсито-аустенитных, отмеченных также на диаграмме промежуточными полями.
Кроме трех казанных основных классов стали, характеризуемых по закаливаемости, т. е. структуре, получаемой при охлаждении на воздухе, Гийе становил еще четвертый так называемый карбидный класс для стали, легированной карбидообразующими элементами. словным признаком его является же не основная структура охлажденного образца, присутствие значительного количества легированных карбидов, которые могут образоваться лишь при наличии в стали большого количества карбидообразующих элементов и глерода.
Наконец, в легированной стали может содержаться значительное количество элементов, замыкающих область 7-твердых растворов (группа хрома, з 129). При пониженном содержании в стали глерода (углерод расширяет область 7) может оказаться, что в стали будут отсутствовать аллотропические превращения, и сталь при любых температурах до расплавления будет находиться в состоянии а, т. е. представлять легированный феррит. Такие стали составляют класс, называемый ферритным.
Итак, легированную сталь по структуре и состоянию, получаемому при охлаждении на воздухе, делят на пять классов: перлитный, мартенсит-ный, аустенитный, ферритный, карбидный.
Классификация легированных сталей по структуре, получаемой после медленного охлаждения (в равновесном состоянии). Этой классификацией предусматривается разделение на классы: доэвтектоидный, заэвтек-тоидный, ледебуритный и ферритный.
Эта классификация подобна классификации нелегированной стали, которую, как известно, тоже разделяют на доэвтектоидную и заэвтектоидную в связи с содержанием глерода и структурой, получаемой в равновесном состоянии, соответственно диаграмме Fe-Fe3C.
Границей, определяющей принадлежность стали к тому и другому классу, является содержание глерода в эвтектоиде (0,83%). При легировании стали, как известно, это количество глерода обычно снижается и, следовательно, граница между доэвтектоидным и заэв-тектоидным классами будет изменяться соответственно действию каждого добавляемого элемента.
показывают границу между доэвтектоидными и заэвтектоидными сталями при добавках хрома (а) или вольфрама (б). По мере величения процента Сг или W эта граница непрерывно снижается, так что содержание глерода в эвтектоиде может доходить до 0,2% и ниже.
Здесь же показана и другая линия, ограничивающая область заэвтектоидных сталей и представляющая смещение предельной точки насыщения аустенита (Е; см. фиг. 88) по мере величения количества W или Сг.
Как известно, в простых сталях за этой точкой получаются же белые чугуны, содержащие в структуре ледебурит.
В легированных сталях при составах, находящихся за линией, в структуре тоже появляется ледебурит (легированный), почему класс таких сталей и называют ледебуритным.
По структуре их следовало бы рассматривать как белые чугуны. Но так как в них обычно бывает низкое, необычное для чугуна, содержание глерода (меньше 1,7%) и по свойствам они не (лответствуют хрупкому белому чугуну,то их словно называют сталями ледебуритного класса.
Поскольку в ледебурите содержится значительное количество карбида, класс ледебуритных сталей, по другой рассмотренной выше классификации (Гийе) должен соответствовать карбидному классу. Четвертый -ф е р р и т н ы й- класс классификации по структуре в равновесном состоянии совершенно совпадает с таким же классом по классификации Гийе; область его также располагается в левом верхнем глу диаграммы, т. е. отвечает минимальному содержанию глерода при высоком количестве легирующего элемента, расширяющего область а-железа (феррита).
В таких сплавах, независимо от скорости охлаждения, получается зернистая структура легированного феррита, не имеющего превращений в твердом состоянии.
Классификация по назначению. Согласно этой классификации, основанной на применении стали в практике, различается:
1) конструкционная сталь (машииоподелочная и строительная), применяемая для изготовления деталей машин и механизмов, также для различных металлических конструкций;
2) инструментальная сталь, применяемая для изготовления высококачественного режущего, дарно-штампового и мерительного инструментов;
3) сталь с особыми физическими и химическими свойствами ив связи с этим имеющая особое специальное назначение в каждом отдельном случае.
Сопоставляя эту классификацию с классификацией стали по Гийе, можно также отметите некоторую связь между ними. Конструкционная сталь, в подавляющем большинстве случаев, относится к перлитному классу; сталь с особыми свойствами - к аустенитному или ферритиому классу; инструментальная - чаще к карбидному классу и т. п.
№5В соответствии с ГОТом для обозначения легирующих элементов приняты следующие буквы: X - хром, Н - никель, Г - марганец, С - кремний, В - вольфрам, М - молибден, Ф - ванадий, К - кобальт, Т - титан, Ю - алюминий, Д - медь, П - фосфор,- бор, Б - ниобий, А - азот (ставить в конце маркировки запрещается), Е - селен, - - цирконий. Для обозначения легированной стали той или иной марки применяют определенное сочетание цифр и букв.
Для стали конструкционной легированной принята маркировка, по которой первые две цифры казывают среднее массовое содержание глерода в сотых долях процента, если сталь содержит менее 0,1 % глерода, то первая цифра ноль, например 08, 05. Буквы в маркировке казывают наличие соответствующих легирующих элементов, цифры, следующие за буквами, - процентное массовое содержание этих элементов в стали. Если за какой-либо буквой отсутствует цифра, то это значит, что сталь содержит данный элемент в количестве до 1,5 %, кроме элементов, присутствующих в малых количествах (для комплексно-легированных сталей). Например, марка 3Х обозначает хромовую сталь с массовым содержанием С около 0,35 % и Сг до 1,5 %; 4Г2 - марганцевую сталь с массовым содержанием С около 0,45 % и Мп около 2 %; марка 3ХНЗМФА - сталь, содержащую 0,33-0,4 % С, 1,2-1,6 % Сг, 3,0-3,5 % Ni, 0,35-0,45 % Mo, 0,1-0,18 % V, также 0,25-0,5 % Мп, не казанного по маркировке, букву А в конце маркировки используют для обозначения высококачественной стали. Для обозначения особовысококачественной стали в конце маркировки ставят букву Ш (через дефис), например, ЗОХГС-Ш.
Для инструментальной легированной стали порядок маркировки по легирующим компонентам тот же, что и для конструкционных сталей, но содержание глерода казывается первой цифрой в десятых долях процента. Если цифра отсутствует, то сталь содержит около 1 % глерода.
Некоторые стали специального назначения имеют особую маркировку из букв, которые ставятся впереди цифр: А - автоматная, - шарикоподшипниковая,- быстрорежущая, Е - магнитотвердая, Э - электротехническая, Св - сварочная, Нп - наплавочная и др.
№5Твердые растворы. В данной системе имеются твердые растворы железа с глеродом на основе двух кристаллических модификаций железа. Они являются твердыми растворами внедрения, т.е. атомы железа занимают злы пространственной решетки, атомы глерода размещаются в междоузлиях.
Твердый раствор глерода в a -железе называется ферритом. В феррите сохраняется кристаллическая решетка a -железа - объемно-центрированный куб. Феррит занимает на диаграмме зкую область, примыкающую к железуQPG. Максимальная растворимость глерода в нем не более 0,025 %, при комнатной температуре она равна 0,006%. Твердость феррита около 800-1 Па, предел прочности s в~ 250 Па; s т~ 120 Па, относительное длинение (d ) до 50 %, поперечное сужение Y -до 80 %. До температуры 770 С феррит ферромагнитен, выше Цпарамагнитен. Значительно большую область на диаграмме железо-углерод занимает твердый раствор глерода в g -железе с гранецентрированной кубической решеткой, который называется аустенитом.
В аустените предел растворимости достигает 2,14 %. Твердость его равна 1700 - 2 Па, s в - 50 - 80 Па. Аустенит обладает и малой склонностью к хрупкому разрушению. Как в феррите, так и в аустените осуществляется металлический тип связи.
№5Карбиды - соединения металлов и неметаллов с глеродом. Традиционно к карбидам относят соединения где глерод имеет большую электроотрицательность, чем второй элемент (таким образом из карбидов исключаются такие соединения глерода, как оксиды, галогениды и т.п.)
Карбиды - тугоплавкие твёрдые вещества, не растворимы[источник не казан 1069 дней] ни в одном из известных растидов исключаются такие соединения глерода, как оксиды, галогениды и т.п.)
Карбиды - тугоплавкие твёрдые вещества, не растворимы[источник не казан 1069 дней] ни в одном из известных растворителей. Карбиды бора и кремния (ВС и SiC), титана, вольфрама, циркония (TiC, WC и ZrC соответственно) обладают высокой твёрдостью, жаростойкостью, химической инертностью. Нитриды - соединения азота с менее электроотрицательными элементами, например, с металлами (AlN;TiNx;Na3N;Ca3N2;Zn3N2; и т. д.) и с рядом неметаллов (NH3, BN, Si3N4).
Соединения азота с металлами чаще всего являются тугоплавкими и стойчивыми при высоких температурах веществами, например, эльбор. Нитридные покрытия придают изделиям твёрдость, коррозионную стойкость; находят применение в энергетике, космической технике.
Интерметаллид (интерметаллическое соединение) - химическое соединение из двух или более металлов. Интерметаллиды, как и другие химические соединения, имеют фиксированное соотношение между компонентами. Интерметаллиды обладают, как правило, высокой твёрдостью и высокой химической стойкостью. Очень часто интерметаллиды имеют более высокую температуру плавления, чем исходные металлы. Почти все интерметаллиды хрупки, так как связь между атомами в решётке становится ковалентной или ионной (например, в ауриде цезия CsAu), не металлической. Некоторые из них имеют полупроводниковые свойства, причём, чем ближе к стехиометрии соотношение элементов, тем выше электрическое сопротивление. Никелид титана, известный под маркой нитинол, обладает памятью формы - после закалки изделие может быть деформировано механически, но примет исходную форму при небольшом нагреве.
Некоторые из металлов могут реагировать друг с другом очень активно. Например, реакция цинка и никеля при температурах выше 1 C носит взрывной характер.