Читайте данную работу прямо на сайте или скачайте
Коррозия металлов и методы защиты от неё
Содержание
Глава 1 Коррозия металл....1
1. Основы теории коррозии.Е...1
1,1 классификация коррозийных процессов.ЕЕ.Е.1
1,2 Показатель скорости коррозии..Е....2
2а Электрохимическая коррозия.Е..4
2,1 Термодинамика электрохимической коррозии металлов...Е.4
2,2 Гомогенные и гетерогенные пути электрохимической коррозииЕЕ..5
2,3 Анодные процессы при электрохимической коррозии металлов ЕЕ.6
2,4 Причины анодного растворения.ЕЕ..6
2,6 Анодная пассивность металлов.7
3 Депомеризация ...Е..8
3,1 Термодинамические возможности кислородной депомеризацииЕЕ..8
3,2 Перенапряжение ионизации кислорода.ЕЕ10
Глава 2 Электрохимические методы защиты металлов от коррозии
1. Методы защиты металлов от коррозии...11
2. Катодная защита..ЕЕ.12
3. Явление пассивности..ЕЕ..14
4. Анодная защита. Использования пассивности в практике от коррозии..15
5. Покрытия, как методы защиты металлов от коррозии...Е.18
6. Ингибиторы ...20
Глава 3 Обработка резанием.
1. Сущность и схемы способов обработки22
2. Параметры технологического процесса..25
Глава 4 Коррозийное растрескивание.
1. Явление коррозийного растрескивания....29
2. Коррозионная стрела...30
3. Структура и состав.....30
4. Напряжение .30
5. Характер ..30
6. Предотвращение коррозионного растрескивания..Е.ЕЕ31
7. Механизм коррозийного растрескивания.Е.Е..31
8. Начальная стадия локализованной коррозии.Е....Е..33
9. Система сплавов, подверженных межкриталлитному растрескиванию.....Е..34
10. Системы сплавов, подвеженных внутрикристаллическому растрескиванию...ЕЕ35
11. Развитие трещин..35
12. Общие закономерности я вления коррозийного растрескивания ..ЕЕ.38
Глава 1
Коррозия металла
1. Основы теории коррозии
Термин коррозия происходит ота латинского "corrosio", что означает разъедать, разрушать. Этота термина характеризуета как процесс разрушения , так и результат.
Среда в которой металл подвергается коррозии (коррозирует) называется коррозионной или агрессивной средой.
В случае с металлами, говоря об их коррозии, имеют ввиду нежелательный процесс взаимодействия металл со средой. Физико-химическая сущность изменений, которые претерпевает металл при коррозии я вля ется окисление металла.
Любой коррозионный процесс я вля ется многостадийным:
1) Необходим подвод коррозионной среды или отдельныха ее компонентов к поверхности металла.
2) Взаимодействие среды с металлом.
3) Полный илиа частичный отвода продуктова от поверхности металла (в объем жидкости, если среда жидкая ).
Известно что большинство металлова (а кромеа Ag,Pt,Cu,Au) встречаются ва природе ва ионнома состоя нии:а оксиды, сульфиды, карбонаты и др., называемые обычно руды металлов.
Ионное состоя ние более выгодно, оно характеризуется а более меньшей внутренней энергией. Это заметно при получение металлов из руд и иха коррозии. Поглощенная а энергия а приа восстановлении металла иза соединенийа свидетельствуета о тома , что свободный металл обладаета болееа высокой энергией, чем металлическое соединение. Это приводита к тому, что металла находя щийся а в контакте c коррозионно-активной средой стремится а перейтиа в энергетически выгодное состоя ние с меньшим запасом энергии.
Коррозионный процесс я вля ется самопроизвольным, следовательно G=G-Gа (Gа и G относя тся к начальному и конечному состоя нию соответственно). Если G>G то G<0, т.е. коррозионный процесс возможен; G>0а коррозионный процесса невозможен; G=0 система металл-продукт находится а ва равновесии. То есть можно сказать, что апервопричиной коррозии металл я вля ется термодинамическая неустойчивость металлов в заданной среде.
1.1а Классификация коррозионных процессов.
1. По механизму процесс различают химическую и электрохимическую коррозию металла.
Химическая коррозия - это взаимодействие металлова с коррозионной средой, при котором окисля ется металл и восстанавливается окислительные компоненты коррозионной среды протекают ва однома акте. Така протекаета окислениеа большинств металлов в газовых средаха содержащиха окислитель (например, окисление в воздухе при повышении температуры)
Электрохимическая коррозия а -а это взаимодействие металла са коррозионной средой, при которома ионизация а атомова металл и восстановление окислительной компоненты среды происходита не водном акте, и их скорости завися та ота электродного потенциала
металла. По такому процессу протекают, например, взаимодействие металла с кислотами:
эта суммарная реакция состоит из двух актов:
2. По характеру коррозионного разрушения .
Общая или сплошная коррозия а при которойа коррозируета вся поверхность металла. Он соответственно делится на равномерную (1а), не равномерную (1б)а и избирательную (1в), при которой коррозионный процесс распространя ется преимущественно по какой-либо структурной составля ющей сплава.
Местная коррозия при которой коррозируюта определенные участки металла:
а) коррозия я звами - коррозионные разрушения ва виде отдельных средних и больших пя тен (коррозия латуни в морской воде)
б) межкристаллическая коррозия при ней процесс коррозии распространя ется по границе металл-сплав (алюминий сплавля ется с хромоникелем) и другие виды коррозии.
а3. По словия м протекания процесса.
а) Газовая коррозия - это коррозия а ва газовой среде при высоких температурах. (жидкий металл, приа горя чей прокатке, штамповке и др.)
б) Атмосферная коррозия - это коррозия металл в естественной атмосфере или атмосфереа цех (ржавление кровли, коррозия обшивки самолета).
в) Жидкостная коррозия - это коррозия в жидких средах:а как в растворах электролитов, так и в растворах не электролитов.
г) Подземная коррозия - это коррозия металла в почве
д) Структурная коррозия -а коррозия а из-з структурной неоднородности металла.
е) Микробиологическая коррозия - результат действия бактерий
ж) Коррозия внешним током - воздействие внешнего источник тока (анодное или катодное заземление)
з) Коррозия а блуждающимиа токами -а прохождениеа ток по непредусмотренным путя м по проекту.
и) Контактная коррозия - сопря жение разнородных электрохимических металлов в электропроводя щей среде.
к) Коррозия пода напря жениема -а одновременное воздействие коррозионной среды и механического напря жения .
1.2 Показатель скорости коррозии.
Для установления скорости коррозии металла ва данной среде обычно ведута наблюдения а з изменениема во времени какой-либо характеристики, объективно отражающей изменение свойства металла.
Чаще всего в коррозионной практике используют следующие показатели.
1) Показатель изменения массы - изменение массы образца в результате коррозии отнесенный к единице поверхности металла S и к единице времени (например, г/м ч) в зависимости от словий коррозии различают:
а) отрицательный показатель изменения массы
К-m
=m / S
m=m/st
гдеа m -а быль массы металл з время а коррозииа после даления продуктов коррозии.
б) положительный показатель изменения массы
К+m
=m / S
где mа - величение массы металла за время вследствие рост пленки продуктов коррозии.
Если состава продуктов коррозии известен, то можно сделать пересчет от К к К и наоборот
К-m=К+m (nok A Me / n Me Aok)
где А и М - атомная и молекуля рная масс Меа и окислителя соответственно; n и nа валентность металл и окислителя а в окислительной среде.
2) Объемный показатель коррозии
К - объем поглощенного или выделившегося в процессе газ V отнесенный к единице поверхностиа металл и единицеа времени (например, см/см ч).
К= объ.V/ S
объем газа обычно приводя т к нормальным словия м.
Применительно к электрохимической коррозииа когда процесс катодной деполя ризацииа осуществля ется а з счета разря д ионов водорода, например, по схеме Н + 2е = Н, или ионизация молекул кислорода О + 4е +НО = ОН;а вводя тся соответственно кислородный (К ) и водородный (К ) показатель соответственно.
Водородный показатель коррозии - это объем выделившегося а На в процессе коррозии, отнесенный к Suа.
Кислородный показатель коррозии - это объем поглощенного в процессе О, отнесенный к Suа .
3)а Показатель сопротивления .
Изменение электрического сопротивления образц металл з определенное время а испытанийа также может быть использован в качестве показания коррозии (К).
КR = (/Ro)100%
за время t
где Ro и соответственно до и после коррозии.
У этого способа есть некоторый недостатока толщин металл во все время а испытаний должна быть одинаковой и по этой причине чаще всего определя юта дельноеа сопротивление, т.е. изменение электрического сопротивления а н единицу площади образца (см, мм) при длине равной единице. Этот метод имеет ограничения применения (для листового металл неа более 3мм). Наиболее точные данные получают для проволочных образцов. Этот метода не пригодена для сварных соединений.
4) Механический показатель коррозии.
Изменение какого-либо свойства металла за время коррозии. Сравнительно часто пользуются а изменением предел прочности. Прочностной показатель при этом выражается :
Кo= (в/
во) 100% за время
t
где o изменение предел прочности приа растя жении после коррозии образц ва теченииа времени ;
во предела прочности до коррозии.
5) Глубинный показатель коррозии.
К - глубин разрушения а металл Па ва единицу времени (например, мм/год)
КП = п/
Глубина коррозионного разрушения П может быть средней или максимальной. Глубинныйа показатель коррозии можно использовать для характеристики как равномерной., так и неравномерной коррозии (в том числе и местной) металлов. Он добен для сравнения скорости коррозии металла с различными плотностя ми. Переход от массового, токового и объемного к глубинномуа возможена при равномерной коррозии.
2. Электрохимическая коррозия .
Электрохимическая коррозия я вля ется наиболее распространенным типом коррозии металлов. По электрохимическому механизму коррозируют металлы в контакте с растворами электролитов (морская вода, растворы кислот, щелочей, солей). В обычных атмосферныха словия х и в земле металлы коррозируют также по электрохимическому механизму, т.к. на их поверхности имеются капли влаги с растворенными компонентами воздуха и земли. Электрохимическая коррозия я вля ется гетерогенным и
многостадийным процессом. Ее причиной я вля ется термодинамическая неустойчивость металлов в данной коррозионной среде.
чение о электрохимической коррозии ставит главный вопрос - вопрос о скорости коррозии и тех факторов, которые влия ют на нее. С электрохимической точки зрения коррозия а металл это не просто процесса окисления а металла, т.к. этота переход должен
сопровождаться сопря женно идущим восстановительным процессом. В результате ионизации освобождаются электроны и роль второго восстановительного процесс состоит в их ассимиля ции подходя щима окислителема (Д), образующима стойчивое соединение.
Ионизация и процесса ассимиля ции электронова какима либо элементома среды (обычно На ионы или о )представля ет собой В отличии химического, электрохимические процессы контролируются (завися т)а не только от концентрации реагирующих веществ, но и, главным образом, завися т от потенциала поверхности металла.
Потенциал.
На границе раздела двух разнородных фаз происходита переход заря женных частица - ионов или электронов из одной фазы в другую, следовательно, возникаета разность электрических потенциалов, распределения упоря доченных электрических заря дов, т.е.
образование двойного электрического слоя . Возникновение межфазового скачка потенциала можно объя снить следующими основными причинами;а но рассмотрим только те, которые приводя т к коррозии металлов, точнее переход катионов металл из электролит н металл (электродный потенциал) адсорбция анионов аэлектролит н металле (адсорбционный потенциал) возникновение ионно-адсорбционного потенциал з счет одновременной адсорбции поля ризуемого атома кислорода и перехода
катионов из металла в электролит.
По известныма причинам, абсолютное значение межфазовой разности потенциалов измерить нельзя , эту величину можно измерить относительно другойа величины и з точку отсчет принимается стандартный водородный потенциал.
Наличие на межфазовой границеа металл-раствора электролит двойного электрического слоя а оказываета существенное влия ние н процесс,, в частности, на скорость коррозииа металлов. При изменении концентрации (плотности) положительных или отрицательных частиц ва растворе или металлеа можета измениться скорость процесса растворения металла. Именно их этих соображений электродный потенциал я вля ется одной из важнейшиха характеристик, определя ющих скорость коррозии металла.
2.1а Термодинамика электрохимической коррозии металлов.
Стремлением металлов переходить из металлического состоя ния в ионное для а различныха металлова различно. Вероя тность такого перехода зависит также ота природы коррозионной среды. Такую вероя тность можно выразить меньшениема свободной энергии при протекании реакции перехода ва заданной среде приа определенных словия х.
Но пря мой свя зи между термодинамическим ря дома и коррозией металлов нет. Это объя сня ется тем, что термодинамические данные получены для идеально чистой поверхности металла, в то время как в реальныха словия ха коррозирующий металл покрыт слоем (пленкой) продуктов взаимодействия металла со средой.
Для расчетов изменения свободнойа энергии реакции при электрохимической коррозии металл используют величины электродных потенциалов. В соответствии с неравенством процесс электрохимической коррозии возможен, если
GT = - n ET F
< 0
где - э.д.с. гальванического элемента, в котором обратимо осуществля ется данный коррозионный процесс, В
- обратный потенциал катодной реакции, В
- обратный потенциал металла в данных условия х.
Следовательно, для а электрохимического растворения металл необходимо присутствие ва раствореа окислителя а (деполя ризатора, который бы осуществля л катодную реакцию ассимиля ции электронов), обратимый окислительно-восстановительный потенциал которого положительнее обратимого потенциала металла в данных словия х.
Катодные процессы приа электрохимической коррозии могут осуществля ться различными веществами.
1) ионами
2) молекулами
3) оксидами и гидрооксидами (кака правило малорастворимыми продуктами коррозии, образованными на поверхности металлов)
4) органическими соединения ми
Обратимые окислительно-восстановительные потенциалы катодных
процессов можно рассчитать по равнения м:
(Vk)обр
= (Vk)0обр
+ (RT/nF)
2,303 lg
(apok/agв)
где (Vk)обр = (Vk)0обр стандартный окислительно-восстановительныйа потенциал при apok/agв=1,
аu, -а активность (приближенно концентрация окислителя и
восстановителя )
pu, q -а стехиометрические коэффициенты аокислителя а и восстановителя в реакции
В коррозионной практике в качестве окислителей-деполя ризаторов, осуществля ющиха коррозию, выступают ионы водород иа молекулы растворенного в электролите кислорода.
Электродная реакция анодного растворения металл (собственно коррозионные потери металла) в общем случае протекают по схеме Me -> Me + ne
При величении активности ионов металл (повышение концентрации ионов металл в растворе), потенциал анод возрастает, что приводит к торможению растворения а металла. Понижение активности металла, напротив, способствует растворению
металла. Ва ходе коррозионного процесса изменя ются не только свойства металлической поверхности, но и контактирующего раствора (изменение концентрации отдельных его компонентов). При меньшении, например, концентрации деполя ризатора, у катодной зоны можета оказаться , что катодная реакция деполя ризации термодинамически невозможна.
2.2 Гомогенные и гетерогенные пути электрохимической коррозии.
Причину коррозии металлова ва растворах, не содержащих одноименных ионов, объя сня ет теория необратимых потенциалов. Эт теория рассматривает поверхность металлов как однородную, гомогенную. Основной и единственной причиной растворения (коррозии) таких металлов я вля ется термодинамическая а возможность протекания анодного иа катодного актов. Скорость растворения (коррозии) будет определя ться кинетическими факторами. Но гомогенную поверхность металлов можно рассматривать как предельный случай, который может быть реализован, например, в жидких металлах. (ртуть и амальгамы металлов). Для а твердых металлов такое допущение будета ошибочным, хотя а бы потомуа что различные атомы сплав (и чистого металла) занимают различное положение в кристаллической решетке. Наиболее сильное отклонение от гомогенной конструкции будет наблюдаться при наличии в металле инородных включений, интерметаллидов, границ зерен и т.д. В этом случае, разумеется , поверхность я вля ется гетерогенной. становлено, что даже при наличии н поверхности металл неоднородностей в целом поверхность остается а эквипотенциальной.
Таким образом неоднородность поверхностей сплав не может я вля ться основной причиной общей коррозииа металла. Наиболее существенной в подобных случая ха я вля ется а ионизация а растворения анодной составля ющей вблизи катодной составля ющей, это возможно, если н поверхности металлической конструкции возникают гальванические элементы. Рассмотрим некоторые из них:
) неоднородность металлическойа фазы, обусловленная неоднородностью сплава, такжеа в результате микро и макровключений.
б) неоднородность поверхностиа металла в следствие наличия а границ блоков и зерен кристаллов, выхода дислокацийа н поверхность, анизотропность кристаллов.
в), г)а неоднородность защитныха пленок н поверхности за счета микро и макропор пленки (в), з счет неравномерного образования а на поверхности вторичныха продуктов коррозии (г) и др.
Мы рассмотрели дв крайних механизм саморастворения металлов: равномерное растворение идеально гомогенной поверхности и растворения (в основном локальное) микроэлементов при пространственном разделении катодных и анодных зон (процессов).
В общема случае, необходимо считаться с возможностьюа протекания а н анодныха часткаха наря ду c основными анодными процессами катодных процессов, н катодныха же часткаха могута протекать с пониженной скоростью анодные процессы растворения .
Можно сделать вывод, что нета оснований противопоставля ть "гомогенный" и "гетерогенный" пути протекания а коррозионных процессов. Правильнее будет их рассматривать как факторы, взаимно дополня ющие друга друга. Основнойа же причиной коррозии металлов остается по-прежнему термодинамическая вероя тность протекания а в данных словия ха на металле анодных процессов ионизации металла и сопря женного с ним катодного процесса деполя ризации.
2.3а Анодные процессы при электрохимической коррозии металлов.
Термодинамические основы.
Для протекания коррозионного процесса существенным я вля ется состоя ние форма соединения , в котором находится катион металла в растворе. Ионизация а металл са последующим переходом в раствор простых компонентов металла представля ет лишь одно иза возможных направлений анодныха процессов. Форма их конкретного состоя ния во многом определя ется как природой металла и контактирующей c ним средойа, так и направлением и величиной поля ризующего тока (или электродного потенциала). Переходя а ва раствор, коррозирующий металл вступает в свя зь либо с растворителем, либо с компонентами раствора. При этом могут образовываться а простыеа и комплексные соединения а c различной растворимостью и с различной адгезией к поверхности металла. При высоких положительных значения х потенциал на аноде возможен процесс окисления воды с выделением кислорода. В зависимости от того, какие процессы или их сочетания протекаюта н аноде, ониа могут в значительной мере (а иногда и полностью) контролировать суммарный процесс коррозии.
2.4 Причины анодного растворения металлов.
Простейшими анодными реакция ми я вля ются такие , в результате которых образуются растворимыеа гидратированные и комплексные катионы,. которые отводя тся от анода путем диффузии, миграции (перенос за счет электрического поля ) или конвекции.
Поля рные молекулы жидкости электростатически взаимодействуют са заря женными ионами, образуюта сольватные (в случае воды-гидратные) комплексы. Обладающие значительно меньшим запасом энергии чем ионы в кристаллической решетки металла. Величину этого понижения а можно оценить, исходя а иза соображений предложенных Борном. Полный электрический заря да в вакууме обладает энергией, равной потенциальной энергии. Для определения величины энергии заря да представим, что проводя щая сфера радиусома r имеет заря д q. Внесение еще одной части заря д dq в сферу должно быть встречено отталкивающими силами df=qdq/r. Поистине огромное меньшение энергии иона в водном растворе казывает на стойчивость такого состоя ния в нем. Таким образом, причиной переход атомов металл с поверхности и их ионизация я вля ется электростатическое взаимодействие (сольватация ) ионов металла с поля рными молекулами растворителя . Следовательно, схему реакции ионизации в контакте с растворителем правильнее записать в виде:
Me + mHO -> Me + mHO +ne.
2.6 Анодная пассивность металлов.
При значительнома торможении анодной реакции ионизации металла скорость коррозионного процесс можета понизится а н несколько поря дков. Такоеа состоя ние металл приня то называть анодной пассивностью. Пассивность можно определить следующим образом: пассивность - состоя ние повышенной коррозионной стойчивости металл или сплав (в словия х, когд термодинамически она я вля ется а реакционно способным), Вызванное преимущественным торможением анодного процесса т.е. может произойти так, что в реальных словия х скорость коррозии "активных" элементова оказывается весьма незначительной в следствии наступления а пассивного состоя ния . Например, титан расположенный левее цинка, и хром, расположенный ря дом с цинком, в следствии наступления пассивности оказываются более коррозионностойкими в большинстве водных сред, чем цинк. Н склонность к пассивному состоя нию влия ет природ системы металл-раствор. Наибольшую склонность к переходу ва пассивное состоя ние проя вля ют Ti,Ni,Al,Mg,Fe,Co и др.
Наступление пассивного состоя ния а приводит к значительному изменению формы анодной поля ризационной кривой. Кривая может быть разбита на несколько характерных частков:
Вначале скорость анодного растворения металлова возрастает в соответствии с равнением Тафеля (а =a + blgi)-участок АВ.
Но начиная с В становится возможным процесс образования защитного слоя (фазового или адсорбционного), скорость которого растет при смещении потенциала в положительную сторону. Это приводит к торможению анодного растворения (BD). В точке D, соответствующей потенциалу ( потенциала начал пассивации) скорость образования защитного слоя равна скорости его растворения . Далееа идета роста защитного слоя , экранирующего поверхность, скорость анодного растворения резко понижается (DE). Ва точке Е, соответствующей потенциалуа полной пассивации металла оказывается ва пассивном состоя нии. На частке EF (область пассивного состоя ния )а скорость анодного процесс неа зависита ота потенциала, определя ется скоростью химического растворения защитной пленки. Ток соответствующий области пассивного состоя ния , называется а током пассивного состоя ния (i ). Положительнее Fа возможна ( -потенциал перепассивации) новая аветвь активного растворения с образованием катионов более высокой валентности.
При высокиха положительныха потенциалаха возможена локализованный пробой оксидной пленки -а металла начинаета растворя тся а по типу питтинга (PP') называют потенциалом питтингообразования .
Металл запассивированный в данной среде, может сохраня ться в пассивном состоя нии некоторое время в непассивирующей среде.
3. Депомеризация .
При наличии ва растворе газообразного кислород и не возможностью протекания процесс коррозии с водородной деполя ризацией основную роль деполя ризатор исполня ета кислород коррозионные процессы, у которых катодная деполя ризация
осуществля ется растворенным ва электролите кислородом, называют процессами коррозии металлова с кислородной деполя ризацией. Это наиболее распространенныйа типа коррозии металл в воде, в нейтральных и даже ва слабокислых солевых растворах, в морской воде, в земле, в атмосфере воздуха.
Общая схем кислородной деполя ризации сводится к восстановлению молекуля рного кислорода до иона гидроокисла:
O + 4e +2HO -> 4OH
3.1а Термодинамические возможности кислородной деполя ризации.
Протекание процесс коррозии металл с кислородной деполя ризацией согласно уравнения возможно при словии:
(Me)обр < (VO2)обр
где (VO2)обр -а обратимый потенциала кислородного электрода,
равный: (VO2)0обр + (RT/4F)2,303 lg(PO2/OH)
Из последнего равнения следует, что ( ) зависит от рН среды (а ) и парциального давления кислорода.
Значение обратимых потенциалов кислородного электрод при
различных рН среды и Р
P (атм) |
,B, при рН среды |
||
рН=0 |
рН=7 |
рН=14 |
|
0,21 |
+1,218 |
+0,805 |
+0,381 |
1 |
+1,229 |
+0,815 |
+0,400 |
Коррозия металла с кислородной деполя ризацией в большинстве практических случаев происходит в электролитах, соприкасающихся с атмосферой, парциальное давление кислорода в которой Р=0,21 атм. Следовательно, при определении термодинамической возможности протекания коррозионного процесс са кислороднойа деполя ризацией следует производить учитывая реальное парциальное давление кислорода ва воздухе (см. табл.). Т.к. значения (Vа ) очень аположительны, то словия а соблюдаются в очень многих случая х. В следующей таблице приведены значения ЭДС и изменения изобарно-изотермических потенциалов коррозионных процессова с кислородной деполя ризацией:
Me + n/2HO + n/4O = Me(OH)
Металлы |
Твердый продукт (E)обр = (VO2)-(VMe)обр |
|
|
коррозии |
(VO2)-(VMe)обр |
||
Mn MnO +2,488 -25,6 Zn Zn(OH) +1,636 -37,7 Fe Fe(OH) +1,268 -29,3 Fe Fe(OH) +1,164 -26,3 Cu CuO +0,648 -17,3 Cu Cu(OH) +0,615 -14,2 Ag AgO +0,047 -1,1 |
|||
Сопоставля я эти данные с данными по водороду
![]() |
![]() |
![]() |
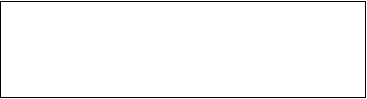
Ра (атм) рН=0 рН=7 рН=14
5*10 +0,186 -0,288 -0,642
1 0, -0,414 -0,828
позволя ет казать на, то что кислородная а деполя ризация а более термодинамически возможна чем водородная деполя ризация .
Изучение восстановления кислорода на неблагородных металлах (а именно они представля юта наибольший интереса с точки зрения коррозии) затрудня ется а тем, что при катодной поля ризации электрода металла может иметь потенциал более положительный, чем равновесный и, следовательно, подвергается окислению (ионизации).
При катодной поля ризацииа ва определеннома интервале потенциалов будут происходить одновременно дв процесс восстановление кислорода иа окисление металла. Окислениеа металл прекратится когда потенциал металл будета равена или станета отрицательнее равновесного потенциал металла. Эти обстоя тельства затрудня ют изучение процессов кислородной деполя ризации.
Схема кислородной деполя ризации.
Каждый процесс с кислородной деполя ризациейа включает следующие последовательные стадии:
1) Растворение кислорода воздуха в растворе электролита.
2) Транспортировк растворенного кислород в растворе электролита (за счет диффузии или перемешивания ) к слою Прандтля .
3) Перенос кислород в части слоя а Прандтля а П(а)в результате движения
электролита.
4) Переноса кислород ва диффузионном слое электролит толщиной или ва пленке продуктова коррозииа металл к катодным часткам поверхности.
5) Ионизация кислорода:
а) в нейтральных и щелочных растворах
O2 + 4e + 2 H2O = 4OH- (водн)
б) в кислых растворах
O2 + 4e + 4 H+(водн) = Н2O
6) Диффузионный или конвектный перенос ионов ОН от катодных частков поверхности корродирующего металла в глубь электролита.
В реальных словия х коррозии металла наиболее затрудненными стадия ми процесса я вля ются :
а) реакция а ионизации кислорода на катоде. Возникающую при этом поля ризацию называют перенапря жением кислорода. Говоря т, что процесс идет с кинетическим контролем.
б) Диффузия а кислород к катоду, либо перенапря жение диффузии. В этом случае, говоря т, что процесс идет с диффузионным контролем.
Возможны случаи когд обе стадии - ионизация кислорода и диффузия кислорода оказывают влия ние на процесс. Тогда говоря т, о кинетически-диффузионном контроле.
3.2а Перенапря жение ионизации кислорода.
Перенапря жение ионизации кислорода чаще всего поя вля ется а в сильно перемешанныха растворах, при интенсивной аэрации раствор (баротаж воздуха и др.), при наличии н металлеа тонкой пленки электролита (влаги)а кака и ва случаеа са любой другой катодной реакцией восстановление перенапря жение ионизации кислород зависит от катодной плотности тока, материала катода, температуры и некоторых других факторов.
Если плотность ток достаточно высок i> А/м то перенапря жение ионизации кислорода я вля ется линейной функцией lgi т.е. имеет место зависимость тапа равнения Тафеля
= - (Vk)э=х = a+b lg ik
где -а постоя нная азавися щая а ота моля рностиа катода его состоя ния , Т и пр., численно а=h при i=1; b постоя нная завися щая от механизм возникновения а перенапря жения . При заторможенности только реакции взаимодействия кислорода с электроном
b=(RT/BnF)n 2,303 = 0,118/ n
Зависимость перенапря жения ионизации кислорода на металлах ва растворе: 0,5NaCl + 0,005MNaCO + 0,005MNaHCO (pH=9,2) в атмосфере кислорода при 20 С, раствор перемешивался а) в координатах б) в координатах.
Катодная реакция а ионизацииа кислород состоит из цепи последовательных элементарных реакций, т.е. протекает стадийно:
а) образование молекуля рного иона кислорода
O2+e = O2-
б) образование пергидроксила
O2- + H+ = HO2
в) образование пергидроксила иона
HO2 + e = HO2-
г) образование перекиси водорода.
HO2- + H+ = H2O2
д) восстановление перекиси водород до гидроксила ион и гидроксил-радикала
H2O2 +e = OH- + OH
е) Восстановление гидроксил-радикала до гидроксил иона
OH + e = OH-
Для ря де металлов (Fe,Cu,Au,Pt) при 25 С const b=0.10..0.13.
Это свидетельствует о том, что причиной перенапря жения ионизации кислорода я вля ется замедленность элементарной реакции ассимиля ции одного электрон (n=1). Для а кислыха растворова такой реакцией я вля ется , по видимому, образование молекуля рного иона кислорода
(а), для щелочных сред - образование пергидроксил-иона (в).
Глава 2
Электрохимические методы защиты металлов от коррозии.
2 Катодная защита
Из всех методов защиты основанных на изменении электрохимических свойств металла под действием поля ризующего тока,
наибольшее распространение получила защита металлов при наложении на них катодной поля ризации (катодная защита). При смещении потенциала металла в сторону более электроотрицательных значений (по сравнению с величиной стационарного потенциала коррозии) скорость катодной реакции величивается , скорость анодной падает (см. рис. 1). Если при стационарном потенциале равенство
,
то при более отрицательном значении я :
причем
.
Рис. аSEQ Рис. \* ARABIC 1я ризационная диаграмма коррозионного процесса.
меньшение скорости анодной реакции при катодной поля ризации эквивалентно меньшению скорости коррозии. Коэффициент торможения при выбранном потенциале j/ (см.рис.4) будет равен двум
степень защиты достигает 50%
а=
Внешний ток , необходимый для
смещения потенциала до значения
я ет собой разницу между катодным и анодным токами
(его величина на рис.4 выражена пря мой ав). По мере величения внешнего тока потенциал смещается в более отрицательную сторону, и скорость коррозии должна непрерывно падать. Когда потенциал корродирующего металла достигает равновесного потенциала анодного процесса я
равной нулю (
), коэффициент торможения
Ц бесконечности, степень защиты 100%. Плотность тока, обеспечивающая полную катодную защиту, называется защитным током
. Его величине на рис.4 соответствует отрезок cd.
Величина защитного тока не зависит от особенностей протекания данной анодной реакции, в частности от величины сопровождающей ее поля ризации, целиком определя ется
катодной поля ризационной кривой.
Так, например, при переходе от водородной деполя ризации к кислородной сила защитного тока меньшается
и становится равной предельному диффузному току (отрезок cd /а на рис.4).
Защита металла катодной поля ризацией применя ется для повышения стойкости металлических сооружений в словия х подземной (почвенной) и морской коррозии, также при контакте металлов с агрессивными химическими средами. Она я вля ется экономически оправданной в тех случая х, когда коррозионная среда обладает достаточной электропроводностью, и потери напря жения (свя занные с протеканием защитного тока), следовательно, и расхода электроэнергии сравнительно невелик. Катодная поля ризация защищаемого металла достигается либо наложением тока от внешнего источника (катодная защита), либо созданием макрогальванической пары с менее благородным металлом (обычно применя ются алюминий, магний, цинк и их сплавы). Он играет здесь роль анода и растворя ется со скоростью, достаточной для создания в системе электрического тока необходимой силы (протекторная защита). Растворимый анод при протекторной защите часто называют жертвенным анодом.
Катодная защита обычно свя зана с защитой черных металлов, так как из них изготавливается а подавля ющая часть объектов работающих под землей и при погружении в воду, например трубопроводы, свайные основания , пирсы, эстакады, суда и др. В качестве материала для расходуемых анодов-протекторов во всем мире широко применя ется магний. Обычно он используется в виде сплавов с содержанием 6% алюминия , 3% цинка и 0,2% марганца; эти добавки предотвращают образование пленок, которые снижают скорость растворения а металла. Выход защитного тока всегда меньше 100%, так как магний корродирует и на нем выделя ется водород. Применя ется также алюминий, легированный 5% цинка, но разность потенциалов с железом для сплава значительно меньше, чем для магниевого сплава. Она близка к разности потенциалов для металлического цинка, который также применя ется для защиты при словии, что путем соответствующего легирования на анодах предотвращается пленкообразование, свя занное с обычным для цинка загря знением примеся ми железа Выбор материала для анодов - сложная задача. В почвах или других средах низкой проводимости необходима большая разность потенциалов, поскольку падение iR между электродами весьма велико, в то время как в средах высокой проводимости возможна более экономичная для использования малая разность потенциалов. Важными переменными я вля ются расположение электродов, рассеивающая способность среды, т. е. ее способность обеспечить одинаковую плотность тока на всех частках защищаемой поверхности, также поля ризационные характеристики электродов. Если электроды погружены в почву, которая по каким - либо причинам неприемлема, например агрессивна по отношению к анодам, то обычно практикуется окружать последние ложем из нейтрального пористого проводя щего материала, называемого засыпкой.
Применение для катодной защиты метода приложения тока облегчает регулирование системы и часто дешевле, чем использование анодов - протекторов, которые, конечно, нуждаются в регуля рных заменах.
На практике катодная защита редко применя ется без дополнительных мероприя тий. Требуемый для полной защиты ток обычно бывает чрезмерно велик, и помимо дорогостоя щих электрических становок для его обеспечения следует иметь в виду, что такой ток часто будет вызывать вредный побочный эффект, например чрезмерное защелачивание. Поэтому катодная защита применя ется в сочетании с некоторыми видами покрытий. Требуемый при этом ток мал и служит только для защиты обнаженных частков поверхности металла.
5 Покрытия , как метод защиты металлов от коррозии.
Защита металлов, основанная на изменение их свойств, осуществля ется или специальной обработкой их поверхности, или легированием. Обработка поверхности металла с целью меньшения коррозии проводится одним из следующих способов: покрытием металла поверхностными пассивирующими пленками из его трудно растворимых соединений (окислы, фосфаты, сульфаты, вольфраматы или их комбинации), созданием защитных слоев из смазок, битумов, красок, эмалей и т.п. и нанесением покрытий из других металлов, более стойких в данных конкретных словия х, чем защищаемый металл (лужение, цинкование, меднение, никелирование, хромирование, свинцование, родирование и т.д.).
Защитное действие большинства поверхностных пленок можно отнести за счет вызванной ими механической изоля ции металла от окружающей среды. По теории локальных элементов, их эффект следует рассматривать как результат величения электрического сопротивления (рис. 8).
Рис. аSEQ Рис. \* ARABIC 3я диаграмма, показывающая , что меньшение скорости коррозии при нанесении поверхностных защитных слоёв может быть объя снено как величением омического сопротивления (а), так и повышением частных коррозионных реакций (б).
Повышение устойчивости железных и стальных изделий при покрытии их поверхности осадками других металлов обусловлено и механической изоля цией поверхности, и изменением ее электрохимических свойств. При этом может наблюдаться или смещение обратимого потенциала анодной реакции в сторону более положительных значений (покрытия медью, никелем, родием), или величение поля ризации катодной реакции - повышение водородного перенапря жения (цинк, олово, свинец). Как следует из диаграмм (рис.8), все эти изменения меньшают скорость коррозии.
Обработку поверхности металлов применя ют для предохранения машин, оборудования , аппаратов и предметов домашнего обихода при временной защите в словия х транспортировки, хранения и консервации (смазка, пассивирующие пленки) и для более длительной защиты при их эксплуатации (лаки, краски, эмали, металлические покрытия ). Общим недостатком этих металлов я вля ется то, что при далении (например, вследствие износа или повреждения ) поверхностного слоя скорость коррозии на поврежденном месте резко возрастает, повторное нанесение защитного покрытия не всегда бывает возможно.
В этом отношении легирование я вля ется
значительно более эффективным (хотя
и более дорогим) методом повышения
коррозионной стойкости металлов. Примером повышения
коррозийной стойкости металла легированием я вля ются
сплавы меди с золотом. Для надежной защиты меди необходимо добавля ть к ней значительное количество золота (не менее 52,2 ат.%). Атомы золота механически защищают атомы меди от их взаимодействия
с окружающей средой. Несравненно меньше количество легирующих компонентов требуется для
повышения стойчивости металла, если эти компоненты способны образовывать с кислородом защитные пассивирующие пленки. Так, введение хрома в количестве нескольких процентов резко величивает коррозионную стойкость сталей. Теоретический и практический интерес представля ет повышение коррозионной стойкости легированием катодными добавками (Томашов). Для
выя снения
принципов, на которых основан этот метод, можно, следуя
Колотыркину, рассмотреть потенциостатические кривые. В отсутствие внешнего поля ризующего тока металл находится при стационарном потенциале я (до легирования ).
Скорость коррозии определя ется при этом пересечением кривых
аи соответствует току
я (или другого металла с низким перенапря жением водорода) поля ризационная
кривая выделения водорода будет отвечать пря мой
я
пересечет анодную кривую же в области пассивного состоя ния . В результате этого стационарный потенциал сместится в положительную сторону до некоторого значения
я
до величины
я
металла в пассивном состоя нии. Таким образом, снижение скорости коррозии достигается
за счет меньшения торможений катодного процесса. Такой механизм защиты возможен лишь в том случае, если обратимый потенциал водородного электрода в данных словия х положительнее, чем Фладе - потенциал, и если точка пересечения катодной и анодной поля ризационных кривых лежит в области пассивного состоя ния металла (рис.9).
Рис. аSEQ Рис. \* ARABIC 4я ризационная диаграмма, показывающая возможность защиты пассивирующегося металла от коррозии при величении скорости катодного процесса.
6 Ингибиторы.
Скорость коррозии можно снизить также изменением свойств коррозионной среды. Это достигается или соответствующей обработкой среды, в результате которой меньшается ее агрессивность, или введением в коррозионную среду небольших добавок специальных веществ, так называемых замедлителей или ингибиторов коррозии.
Обработка среды включает в себя все способы, уменьшающие концентрацию ее компонентов, особенно опасных в коррозионном отношении. Так, например, в нейтральных солевых средах и пресной воде одним из самых агрессивных компонентов я вля ется кислород. Его даля ют деаэрацией (кипя чение, дистилля ция , барботаж инертного газа) или смазывают при помощи соответствующих реагентов (сульфиты, гидразин и т.п.). меньшение концентрации кислорода должно почти линейно снижать предельный ток его восстановления , а следовательно, и скорость коррозии металла. Агрессивность среды меньшается также при ее подщелачивании, снижение общего содержания солей и замене более агрессивных ионов менее агрессивными. При противокоррозионной подготовке воды для уменьшения накипеобразования широко применя ется ее очистка ионнообменными смолами.
Ингибиторы коррозии разделя ют, в зависимости от условий их применения , на жидкофазные и парофазные или летучие. Жидкофазные ингибиторы деля т в свою очередь на ингибиторы коррозии в нейтральных, щелочных и кислых средах. В качестве ингибиторов для нейтральных растворов чаще всего применя ются неорганические вещества анионного типа. Их тормозя щее действие свя зано, по-видимому, или с окислением поверхности металла (нитриты, хроматы), или с образованием пленки труднорастворимого соединения между металлом, данным анионом и, возможно, кислородом (фосфаты, гидрофосфаты). Исключение представля ют в этом отношении соли бензойной кислоты, ингибирующий эффект которых свя зан, главным образом, с адсорбционными я вления ми. Все ингибиторы для нейтральных сред тормозя т преимущественно анодную реакцию, смещая стационарный потенциал в положительную сторону. До настоя щего времени еще не далось найти эффективных ингибиторов коррозии металлов в щелочных растворах. Некоторым тормозя щим действием обладают лишь высокомолекуля рные соединения .
В качестве ингибиторов кислотной коррозии применя ются почти исключительно органические вещества, содержащие азот, серу или кислород в виде амино-, имино-, тиогрупп, также в виде карбоксильных, карбонильных и некоторых других групп. Согласно наиболее распространенному мнению, действие ингибиторов кислотной коррозии свя зано с их адсорбцией на границе раздела металл - кислота. В результате адсорбции ингибиторов наблюдается торможение катодного и анодного процессов, снижающие скорость коррозии.
В свя зи с преобладающим адсорбционным эффектом органических ингибиторов кислотной коррозии особое значение для
понимания механизма их действия и для
рационального подхода к созданию новых ингибиторов приобретает величина заря да поверхности корродирующего металла, т.е.
величина его я ет использовать данные электрокапилля рных измерений на ртути в растворах, содержащих органические соединения , для оченки их эффективности в качестве ингибиторов при кислотной коррозии железа и других металлов. Значение
я ет не только предсказать, какие вещества могут быть ингибиторами, но и рассчитать коэффициенты торможения .
Экспериментальные значения
коэффициентов торможения кислотной коррозии железа в присутствии различных количеств диэтиламина, сопоставление с расчетной пря мой приведены на рис.
10. Расчетная пря мая
вычерчена по равнению
где я нная для
любого члена гомологических ря дов аминов и пиридинов,
анайдены из электрокапилля рных измерений по ртути.
Рис. аSEQ Рис. \* ARABIC 5l- и -¡- - данные двух авторов) и расчётных (пря мая линия ) коэффициентов торможения кислотной коррозии железа при введении разных количеств диэтиланилина.
Адсорбция , однако, я вля ется лишь необходимым словием проя вления ингибирующего действия органических веществ, но не определя ет полностью фактического эффекта ингибиторов. Последний зависит также от многих других факторов - электрохимических особенностей протекания данного коррозионного процесса, характера катодной реакции, величины и природы перенапря жения водорода (при коррозии с водородной деполя ризацией), возможных химических превращений ингибитора в ходе коррозии и т.д.
Действие большинства ингибиторов кислотной коррозии силивается при одновременном введении добавок поверхностно - активных анионов: галогенидов, сульфидов и роданидов.
Парофазные ингибиторы применя ются для защиты машин, аппаратов и других металлических изделий во время их эксплуатации в воздушной атмосфере, при транспортировке и хранении. Парофазные ингибиторы вводя тся в конвейеры, в паковочные материалы или помещают в непосредственной близости от работающего агрегата. Благодаря достаточно высокой пругости паров, летучие ингибиторы достигают границы раздела металл - воздух и растворя ются в пленке влаги, покрывающей металл. Далее они адсорбируются из раствора на поверхности металла. Тормозя щие эффекты в этом случае подобны тем, какие наблюдаются при применение жидкофозных ингибиторов. В качестве парофазных ингибиторов используют обычно амины с небольшим молекуля рным весом, в которые введены соответствующие группы, например NО2 или СО2 . В свя зи с особенностя ми использования парофазных ингибиторов к ним предъя вля ются повышенные требования в отношении их токсичности.
Ингибирование - сложный способ защиты, и его спешное применение в различных словия х требует широких познаний.
Глава 3
Обработка резанием.
Обработка резанием я вля ется универсальным методом размерной обранботки. Метод позволя ет обрабатывать поверхности деталей различной формы и размеров с высокой точностью из наиболее используемых конструкционных мантериалов. Он обладает малой энергоемкостью и высокой производительностью. Вследствие этого обработка резанием я вля ется основным, наиболее используенмым в промышленности процессом размерной обработки деталей.
1. Сущность и схемы способов обработки
Обработка резанием - это процесс получения детали требуемой геонметрической формы, точности размеров, взаиморасположения и шероховантости поверхностей за счет механического срезания с поверхностей заготовнки режущим инструментом материала технологического припуска в виде стружки (рис. 1.1).
Основным режущим элементом любого инструмента я вля ется режунщий клин (рис. 1.1, а). Его твердость и прочность должны существенно превосходить твердость и прочность обрабатываемого материала, обеснпечивая его режущие свойства. К инструменту прикладывается силие резания , равное силе сопротивления материала резанию, и сообщается перемещение относительно заготовки со скоростью ν. Под действием приложенного силия режущий клин врезается в заготовку и, разрушая обрабатываемый материал, срезает с поверхности заготовки стружку. Стружка образуется в результате интенсивной пругопластической дефорнмации сжатия материала, приводя щей к его разрушению у режущей кромнки, и сдвигу в зоне действия максимальных касательных напря жений под глом φ. Величина φ зависит от параметров резания и свойств обрабатываемого материала. Она составля ет ~30
Внешний вид стружки характеризует процессы деформирования и разнрушения материала, происходя щие при резании. Различают четыре возможнных типа образующихся стружек: сливная , суставчатая , элементная и стружнка надлома (рис. 6).
Рис. 6. словная схема процесса резания :
- 1 Ц обрабатываемый материал; 2 - стружка; 3 - подача смазочно-охлаждающих средств; 4 - режущий клин; 5 - режущая кромка; φ - гол сдвига, характеризующий положение словной плоскости сдвига (П) относительно плоскости резания ; γ - главный передний гол режущего клина; Рz - сила резания ; Рy - сила нормального давления инструмента на материал; Сγu, Сγl - длины пластичного и пругого контактов; Сγ, Сa - длина зон контактного взаимодействия по передней и задней поверхностя м инструмента; LOM - область главного пругопластичного деформирования при стружкообразовании; FKPT Ц область вторичной контактной пругоЦпластичнеской деформации металла; h - глубина резания ; Н - толщина зоны пластического деформирования (наклепа) металла.
В процессе резания режущий клин, испытывая интенсивное трение, контактирует с материанлом стружки и обработанной понверхностью в контактных зонах. Для снижения сил трения и нангрева инструмента применя ют принудительное охлаждение зонны резания смазочно-охлаждающими средами (СОС), подавая их в зону резания специальными устройствами.
Детали и инструменты занкрепля ются в специальных органнах станка или приспособления х. Станок, приспособление, инструнмент и деталь образуют силовую систему (СПИД), передающую силие и движение резания от привода станка режущему инстнрументу и детали.
Реальные схемы различнных способов обработки резанинем, используемый инструмент, также виды движения инструменнта и заготовки в процессе обранботки приведены на рис. 7. В зависимости от используемого типа инструмента способы механнической обработки подразделя нются на лезвийную и абразивную.
Рис. 7. Схемы способов обработки резанием:
- точение; б - сверление; в - фрезерование; г - строгание; д - протя гивание; е - шлифование; ж - хонингование; з - суперфиниширование; Dr - главное движение резания ; Ds - движение подачи; Ro - обрабатываемая поверхность; R - поверхность резания ; Rоп - обработанная поверхность; 1 - токарный резец; 2 - сверло; 3 - фреза; 4 - строгальный резец; 5 - протя жка; 6 - абразивный круг; 7 - хон; 8 - бруски; 9 - головка.
Отличительной особеннонстью лезвийной обработки я вля нется наличие у обрабатываемого инструмента острой режущей кромки определенной геометрической формы, для абразивной обработки - наличие различным образом ориентированных режущих зерен абразивного инструмента, каждое из которых представля ет собой микроклин.
Рис. 8 Конструкция и элементы лезвийных режущих инструментов:
- токарного резца; б - фрезы; в - сверла;
1 - главная режущая кромка; 2 - главная задня я поверхность; 3 - вершина лезвия ; 4 - вспомогательная задня я поверхность лезвия ; 5 - вспомогательная режущая кромка; 6 - передня я поверхность; 7 Ц крепежная часть инструмента.
Рассмотрим конструкцию лезвийных инструментов, используемых при резании (рис. 8). Инструмент состоит из рабочей части, включающей ренжущие лезвия , образующие их поверхности, режущие кромки и крепежной части, предназначенной для установки и закрепления в рабочих органах станка.
Основными способами лезвийной обработки я вля ются точение, сверленние, фрезерование, строгание и протя гивание. К абразивной обработке относя тся процессы шлифования , хонингования и суперфиниша. В основу классификации способов механической обработки заложен вид используемого инструмента и кинематика движений. Так, в качестве инструмента при точении используются токарные резцы, при сверлении - сверла, при фрезеровании - фрезы, при строгании - строгальные резцы, при протя гивании - протя жки, при шлифовании - шлифовальные круги, при хонинговании - хоны, при суперфинише - абразивные бруски. Любой способ обработки включает два движения (рис. 1.2.): главное - движене резания Dr Ц и вспомогательное - движение подачи Ds. Главное движение обеспечивает съем металла, а вспомогательное - подачу в зону обработки следующего необработанного частка заготовки. Эти движения осуществля ются за счет перемещения заготовки или инструмента. Поэтому при оценках движение инструмента во всех процессах резания добно рассматривать при неподвижной заготовке как сумнмарное (рис. 9).
Рис. 9 Схемы определения максимальной скорости режущей кромки инструмента υе, формы поверхности резания R и глубины резания h при обработке:
- точением; б - сверлением; в - фрезерованием; г - строганием; дЦ протя гиванием; е - хонингованием; ж - суперфинишированием.
Тогда полная скорость перемещения (ve) произвольной точки Мрежунщей кромки складывается из скорости главного движения (v) и скорости подачи (vs):
e = v + vs (1.1)
Поверхность резания R представля ет собой поверхность, которую описывает режущая кромка или зерно при осуществлении суммарного движения , включающего главное движение и движение подачи. При точении, сверлении, фрезеровании, шлифовании поверхности резания Ч пространственные линейчатые, при строгании и протя гивании Ч плонские, совпадающие с поверхностя ми главного движения ; при хонин-говании и суперфинишировании они совпадают с поверхностя ми главнного движения .
Поверхности Ro и Roп называются , соответственно, обрабатываенмой поверхностью заготовки и обработанной поверхностью детали
В процессах точения , сверления , фрезерования и шлифования главнное движение и движение подачи выполня ются одновременно, в пронцессах строгания , хонингования движение подачи выполня ется после главного движения .
2. Параметры технологического процесса резания
К основным параметрам режима резания относя тся скорость главного движения резания , скорость подачи и глубина резания .
Скорость главного движения резания (или скорость рензания ) определя ется максимальной линейной скоростью главного движения режущей кромки инструмента. Эта скорость выражается в м/с.
Если главное движение резания вращательное, как при точении, сверлении, фрезеровании и шлифовании, то скорость резания будет определя ться линейной скоростью главного движения наиболее даленной от оси вращения точки режунщей кромки - максимальной линейной скоростью главного движения .
= ωD/2 (2.1)
где D - максимальный диаметр обрабатываемой поверхности заготовки, определя ющий положение наиболее удаленной от оси вращения точки режущей кромки, м; ω - гловая скорость, рад/с.
Выразив гловую скорость ω через частоту вращения шпинделя станка, получим:
= πnD (2.2)
При строгании и протя гивании скорость резания v определя ется скоронстью перемещения строгального резца и протя жки в процессе резания отнонсительно заготовки.
При хонинговании и суперфинишировании скорость резания определя нется с учетом осевого перемещения (см. рис. 1.4, е, ж) инструмента.
Скорость резания оказывает наибольшее влия ние на производительность процесса, стойкость инструмента и качество обработанной поверхности.
Подача инструмента определя ется ее скоростью vs. В технологических расчетах параметров режима при точении, сверлении, фрезеровании и шлифовании используется поня тие подачи на один оборот заготовки So и выражается в мм/об. Подача на оборот численно соответствунет перемещению инструмента за время одного оборота:
So = vs / n (2.3)
При строгании подача определя ется на ход резца. При шлифовании пондача может казываться на ход или двойной ход инструмента. Подача на зуб при фрезеровании определя ется числом зубьев Z инструмента и подачей на оборот:
Sz = So / Z (2.4)
Глубина резания А определя ется расстоя нием по нормали от обработаой поверхности заготовки до обрабатываемой, мм. Глубину резания задают на каждый рабочий ход инструмента. При точении цилиндрической поверхнности глубину резания определя ют как полуразность диаметров до г: после обработки:
h = (Dur - d) / 2 (2.5)
где d - диаметр обработанной поверхности заготовки, мм. Величина подачи и глубина резания определя ют производительность пронцесса и оказывают большое влия ние на качество обрабатываемой поверхности.
К технологическим параметрам процесса относя тся геометрия режущего иннструмента, силы резания , производительность обработки и стойкость инструмента.
Геометрические параметры режущего инструмента определя ются углами, образуемыми пересечением поверхностей лезвия , а также положением поверхностей режущих лезвий относительно обрабатынваемой поверхности и направлением главного движения . Указанные паранметры идентичны для различных видов инструмента, что позволя ет рассмотнреть их на примере резца, используемого при точении.
Углы резца по передним и задним поверхностя м измеря ют в определеых координатных плоскостя х. На рис.10 изображены координатные плоскости при точении, на рис. 2.1, б углы резца в статике.
Главный передний гол γ - гол между передней поверхностью лезвия и плоскостью, перпендикуля рной к плоскости резания ; главный задний угол α - гол между задней поверхностью лезвия и плоскостью резания ; гол заострения β - гол между передней и задней поверхностя ми. Из принципа построения углов следует, что
α + β + γ = π/2.
Угол наклона режущей кромки X - гол в плоскости резания между режущей кромкой и основной плоскостью.
Углы в плане: главный гол в плане φ - гол в основной плоскости менжду следом плоскости резания и направлением продольной подачи; вспомо-
гательный гол в плане φ' - гол в основной плоскости между вспомогантельной режущей кромкой и обработанной поверхностью.
Рис. 10 Геометрические парамеры токарного резца:
- координатные плоскости; б - глы резца в статике;
1 - плоскость резания Рп; 2 - рабочая плоскость Рs; 3 - главная несущая плоскость Рt; 4 - основная плоскость Pv
Геометрические параметры режущего инструмента оказывают сущестнвенное влия ние на усилие резания , качество поверхности и износ инструменнта. Так, с величением гла у инструмент легче врезается в материал, снинжаются силы резания , улучшается качество поверхности, но повышается износ инструмента. Наличие гла снижает трение инструмента о поверхнность резания , меньшая его износ, но чрезмерное его величение ослабля ет режущую кромку, способствуя ее разрушению при дарных нагрузках.
Силы резания Р представля ют собой силы, действующие на ренжущий инструмент в процессе пругопластической деформации и разрушенния срезаемой стружки.
Силы резания приводя т к вершине лезвия или к точке режущей кромки и раскладывают по координатным ося м пря моугольной системы координат xyz (рис.11). В этой системе координат ось z направлена по скорости главнного движения и ее положительное направление соответствует направлению действия обрабатываемого материала на инструмент. Ось у направлена по радиусу окружности главного движения вершины. Ее положительное нанправление также соответствует направлению действия металла на инструнмент. Направление оси х выбирается из словия образования правой системы координат. Значение силия резания определя ется несколькими факторами. Оно растет с величением глубины h резания и скорости подачи s (сечения срезаемой стружки), скорости резания ν, снижением переднего гла γ режунщего инструмента. Поэтому расчет силия резания производится по эмпиринческим формулам, становленным для каждого способа обработки (см. спранвочники по обработке резанием). Например, для строгания эта формула имеет вид Р = СphXpsYpXn где коэффициенты Ср, Хр, Yp, n характеризуют материал заготовки, резца и вид обработки.
Мощность процесса резания определя ется скаля рным пронизведением:
N = Pve (2.6)
Выразив это произведение через проекции по координнатным ося м, получим:
N = Pz vz + Pyvy + Pxvx (2.7)
где vx, vy, vz - проекции на оси координат скорости движения точки приложения равнодействующей сил резания . В практических расчетах используется приближенная зависимость N = Pzv. Это прощение обусловлено тем, что составля ющие Ру и Рх полной силы резания малы по сравнению с Р2, а скорость подачи относительно сконрости резания составля ет всего 1 - 0,1%.
Рис. 11 Схема действия сил резания на режущую кромку инструмента в точке, имеющую максимальную скорость перемещения νе, при обработке: - точением; б - сверлением; в - фрезерованием; г - строганием; дЦ протя гиванием; е - хонингованием; ж - суперфинишированием.
Производительность обработки при резании определя ется числом деталей, изготовля емых в единицу времени: Q = \/Тт. Время изготовления одной детали равно Тт = Тд + Тт + Ткп, где То Ч машинное время обработки, затрачиваемое на процесс резания , определя ется для каждого технологического способа; Тт - время подвода и отвода инструмента при обработке одной детали; Гвсп - вспомогательное время установки и нанстройки инструмента.
Таким образом, производительность обработки резанием в первую оченредь определя ется машинным временем То. При токарной обработке, мин: То = La/(nsoh), где L а- расчетная длина хода резца, мм; - величина принпуска на обработку, мм.
Отношение a/h характеризует требуемое число проходов инструмента при обработке с глубиной резания И. Поэтому наибольшая производительнность будет при обработке с глубиной резания h = а, наибольшей подачей s0 и максимальной скоростью резания . Однако при увеличениипроизводительности снижается качесто поверхности и повышается износ инструмента. Поэтому при обработке резанием решается задача по становлению максимально допустимой производительности при сохранении требуемого качества поверхности и стойкости инструмента.
Глава 4
Коррозионное растрескивание.
1 Явление коррозийного растрескивания
В металле, подверженном коррозионному растрескиванию, при отсутствии внешних напря жений обычно происходит очень незнанчительное коррозионное разрушение, при отсутствии коррозиоой среды под воздействием напря жений почти не происходит изнменения прочности или пластичности металла. Таким.образом, в процессе коррозионного растрескивания , т. е. при одновремеом воздействии статических напря жений и коррозионной среды, наблюдается существенно большее худшение механических свойств металла, чем это имело бы место в результате раздельного, но аддитивного действия этих факторов. Коррозионное растренскивание я вля ется характерным случаем, когда взаимодействует химическая реакция и механические силы, что приводит к структурному разрушению. Такое разрушение носит хрупкий характер и возникает в обычных пластичных металлах, также в медных, никелевых сплавах, нержавеющих сталя х и др. в присутствии аопределенной коррозионной среды. При исследовании процесса хрупнкого разрушения в результате коррозионного растрескиванир особое значение имеет исследование раздельного воздействия на металл напря жений и коррозионной среды, а также их одновременное воздействие. Однако в процессе коррозионного растрескивания первостепенное значение имеют следующие стадии: 1) зарождение и возникновение трещин и 2) последующее развитие коррозионных трещин. Обе стадии, как будет показано ниже, я вля ются индивидуальными ступеня ми в процессе коррозионного растрескивания .
2 Коррозионная среда
Средами, в которых происходит коррозионное растрескивание металлов, я вля ются такие среды, в которых процессы коррозии сильно локализованы обычно при отсутствии заметной общей понверхностной коррозии. Интенсивность локализованной коррозии-может быть весьма значительной, в результате чего прогрессирует процесс развития очень зких углублений, достигая , вероя тно, нанибольшей величины на дне глублений, имеющих радиусы понря дка одного междуатомного расстоя ния . Тщательное изучение линтературы показывает, что во многих случая х процесс начальной коррозии может иметь место и при отсутствии напря жений, хотя такое коррозионное разрушение может быть совсем незначительнным. Некоторые вонпросы, относя щиеся к роли напря жений в развитии этих чувствинтельных зон в определенных системах сплавов, еще остаются нея снными, но в общем случае это я сно. Кроме того, большинство экспенриментальных работ показывает, что в том случае, когда начальнные локализованные коррозионные глубления межкристаллигаы,. то при последующем растрескивании преобладает также межкри-сталлитное разрушение. Если начальная коррозия происходит внунтри зерен металла, то последующее растрескивание имеет внутри-кристаллитный характер. Нет определенных казаний о том, что межкристаллитная трещина будет развиваться из внутрикристаллитного коррозионного глубления , и наоборот. Смешанный тип растрескивания , который иногда наблюдается , может быть обусловлен побочным процессом, свя занным с динамикой быстро развинвающейся трещины.
При воздействии на материал коррозионной среды, которая влиня ет на склонность сплава к коррозионному растрескиванию и характер разрушения , основными факторами я вля ются следуюнщие:
1) относительная разность потенциалов микроструктурных фаз, присутствующих в сплаве, что вызывает вероя тность местного разнрушения
2)а поля ризационные процессы на анодных и катодных частках
3)а образование продуктов коррозии, которые оказывают влия ние на коррозионный процесс.
3 Структура и состав
Если локализованная коррозия я вля ется важным фактором в обнщем процессе растрескивания , то вполне очевидно, что микрострукнтура металла должна иметь еще большее значение, определя ющее вероя тность возникновения такого коррозионного разрушения . Опыты со всей очевидностью показывают, что изменения в составе, термообработке, механической обработке и способах изготовления приводя т к изменению микроструктуры, а, следовательно, влия ют и на стойчивость металла против коррозионного растрескивания . Опыты показывают, что структура металла влия ет не только на ханрактер начального местного разрушения , но также определя ет путь и скорость коррозионного растрескивания .
Кроме того, небольшие изменения в составе сплава, без какого-либо очевидного изменения микроструктуры, приводя т к заметному изменению стойчивости сплава против коррозионного растрескинвания . Например, чистая медь в аммиачных средах не подвержена растрескиванию, но примесь менее чем 0,1 % фосфора, мышья к или сурьмы в однородном твердом растворе делает ее подверженной разрушению. Добавление 0,3% хрома защищает от коррозиоого растрескивания алюминиевый сплав марки 755, что важно в промышленном отношении и что еще раз подчеркивает значение изменений состава сплава на стойчивость против коррозионного растрескивания .
4 Напря жения
Для того чтобы произошел процесс коррозионного растрескиванния , необходимо наличие поверхностных или внутренних растя гинвающих напря жений. Обычно встречающиеся на практике разрушенния обусловлены наличием остаточных напря жений, возникающих, при производстве и обработке металла, но в целя х исследования не следует делать разграничения между остаточными напря жения ми и напря жения ми, возникшими в результате приложенных внешних нагрузок. Коррозионное растрескивание никогда не наблюдалось в результате действия поверхностных сжимащих напря жений; наоборот, сжиающие поверхностные напря жения разрушения а могут использоваться для защиты от коррозионного растрескивания .
При величении величины приложенных напря жений меньншается время до полного разрушения металла. Для корнрозионного растрескивания обычно необходимы высокие напря женния , приближающиеся к пределу текучести, однако, часто разрушенние может наступить и при напря жения х, значительно меньших предела текучести. Для многих систем сплавов наблюдается какой-то лпорог или лпредел напря жений, т. е. напря жения , ниже котонрых коррозионное растрескивание не происходит за определенный период времени. Такая зависимость, наблюдавшая ся , например, при замедленном растрескивании сталей, указывает, что основную роль в процессе разрушения играют напря жения .
Имеются доказательства, что основное влия ние при коррозионном растрескивании напря жения оказывают незадолго до полного разрушения , т. е. эффективность напря жений не сказывается до определенного периода времени, после чего наступает внезапное разрушение. Этот вывод в дальнейшем подчеркивается ря дом нанблюдений, в которых казывается на зависимость времени до полнного разрушения от времени приложения напря жений. Показано, что время до полного разрушения ,не зависит от того, приложены ли напря жения в начале испытания или на последующих стадия х его.
5 Характер коррозионных трещин
Коррозионные трещины развиваются в плоскости, перпендикунля рной плоскости растя гивающих напря жений, независимо от ханрактера приложенных или остаточных напря жений. С точки зрения микроструктуры коррозионные трещины могут иметь как внутрикристаллитный, так и межкристаллитный характер. Можно предположить, что направление и характер развития трещин в металле до некоторой степени завися т от формы и размера зерен, поскольку эти факторы влия ют на распределение внутренних напря жений.
Одно из наиболее важных исследований, относя щихся к изученнию характера развития трещин, устанавливает, что этот процесс не я вля ется непрерывным. На прерывистый характер развития тренщин казано в работах Джильберта и Хаддена, Эделеану и Фармери. Обнаружено, что в алюминиево-магкиевых сплавах развитие трещин я вля ется ступенчатым процессом, разнвивающимся путем ря да отдельных механических изломов. Более новое доказательство прерывистого характера развития трещин показано в кинофильме, подготовленном Престом, Беком и Фоннтана, занимающимися коррозионным растрескиванием магниенвых сплавов.
6 Предотвращение коррозионного растрескивания
Наиболее эффективный метод повышения стойчивости металнлов против коррозионного растрескивания состоит в использовании соответствующих конструктивных мероприя тий и способов обранботки, сокращающих до минимума величину остаточных напря женний. Если остаточные напря жения неизбежны, спешно может быть применена термообработка, снимающая эти напря жения . Если понзволя ют словия , может быть использована, например, дробеструйнная обработка, вызывающая сжимающие поверхностные напря женния , которые впоследствии дают возможность нагружать материал, не вызывая напря женного состоя ния поверхности. Одним из метондов, который получает все большее признание и который свя зан с электрохимическим фактором процесса растрескивания , я вля ется применение катодной защиты.
Одним из интересных методов исследования взаимодействия нанпря жений и химических факторов я вля ется изучение зависимости величины катодного тока, необходимого для защиты, от величины механических напря жений.
Кроме того, ря д исследований показывает, что начавшееся раснтрескивание может быть остановлено путем применения катодной защиты.
7 Механизм коррозийного растрескивания
Для объя снения характерных особенностей процесса коррозиоого растрескивания необходим обобщенный механизм этого я вленния , который можно было бы применить для всех металлических систем с четом всех особенностей в каждом индивидуальном слунчае разрушения .
Первые объя снения механизма коррозионного растрескивания свя зывались либо с химическим, либо с механическим фактором и были недостаточны, так как не учитывалось совместное химическое и механическое действие. Большой вклад в вопрос понимания менханизма коррозионного растрескивания внесен Диксом и совтонрами. Их опыты бедительно показали основную электрохиминческую природу коррозионного разрушения , а в обобщенном ими механизме коррозионного растрескивания указывается на роль менханических факторов в процессе общего разрушения . Согласно этому механизму, процесс коррозионного растрескивания тракнтуется следующим образом.
Если в металле происходит развитие местного коррозионного разрушения в виде очень зких глублений, то вполне очевидно, что растя гивающие напря жения , перпендикуля рные к направлению этих углублений, будут способствовать возникновению концентранции напря жений на дне их, причем чем больше глубления и меньше радиус дна глублений, тем больше будет концентрация напря женний. При таком состоя нии металла создаются все словия для разнрушения его вдоль этих более или менее протя женных локальных коррозионных разрушений, и поэтому при достаточной концентранции напря жений металл может начать разрушаться за счет механинческого воздействия . В результате механического разрушения будет обнажаться свежая , незащищенная окисной пленкой поверхность металла, которая , будучи более анодной, подвергается интенсивнному воздействию коррозионной среды, что приведет к величению тока между дном глублений и неповрежденной поверхностью менталла, а, следовательно, и к скорению коррозии. скорение корнрозионного процесса вызовет дальнейшее механическое разрушенние, и, как результат, величится скорость развития трещин блангодаря совместному действию коррозионной среды и растя гиваюнщих напря жений.
Эта общая картина процесса коррозионного растрескивания серьезно не изменилась при последующих исследования х, и в нанстоя щее время можно дать более детальную оценку механического действия концентратора напря жений и его роли в процессе разнрушения .
Существует мнение, что главная функция напря жений состоит в нарушении поверхностных пленок без разрушения металла и что скоренное развитие и распространение трещин в основном имеет электрохимическую природу. В пленочных теория х корнрозионного растрескивания отмечается , что вопрос о том, будет ли иметь место быстрое развитие трещины, зависит от соотношения скоростей образования пленки и увеличения концентрации напря нжений. Если образование пленки может остановить коррозию до того, как концентрация напря жений достигнет значительной велинчины, то быстрое развитие трещин будет предотвращено, но если концентрация напря жений достигнет критического значения до обнразования пленки, то- произойдет разрушение.
Несмотря на то, что высокие напря жения и деформация могут разрушать поверхностную пленку и тем самым способствовать лонкализованной ускоренной коррозии, нет достаточных доказательств, что они играют основную роль или что разрушение пленки я вля ется главным фактором, приводя щим к развитию трещин. Однако вознможно, что разрушение поверхностной пленки, если оно имеет менсто, может играть важную роль в процессе хрупкого разрушения .
Весьма маловероя тно, что наблюдаемое в некоторых случая х очень быстрое развитие трещин и последующее разрушение металла может быть причиной протекания коррозионного процесса. Очень быстрое (почти моментальное) растрескивание может быть воспроизведено в лабораторных словия х при соответствующем вынборе состава сплава, термообработки и коррозионной среды. Нанблюдения за характером развития трещин показывают, что тренщины развиваются преимущественно механическим путем. Сконрость развития трещин, хрупкий характер разрушения и другие факторы казывают на основную роль напря жений в общем пронцессе взаимодействия механических и химических факторов, кроме тех случаев, когда происходит разрушение поверхностной пленки, обеспечивающей доступ коррозионной среды. Новые представления о механизме хрупкого разрушения пластичных металлов и исследонвание влия ния поверхностных пленок на ползучесть и пластическую деформацию казывают на основную роль напря жений в процессе развития трещин и хрупкого разрушения . Вполне вероя тно, что. в результате совместного действия напря жений и коррозии происходит процесс пластической деформации, что приводит к хрупкому разрушению металла.
Основные характерные черты такого представления о механизме коррозионного растрескивания содержатся в теория х Дикса и совнторов, а также в работах Киттинга. Впоследствии Джильберт и Хадден развили эти представления более пондробно для сплавов Аl - 7% Мg, что дало возможность расширить представления о механизме коррозионного растрескивания , пригоднного для всех систем сплавов. Полагают, что такой механизм позвонля ет объя сня ть многие наблюдаемые я вления , ранее трудно со-гласуемые.
Наиболее вероя тными процессами, при которых происходит корнрозионное растрескивание, я вля ются следующие:
1. Локализованная электрохимическая коррозия вызывает обранзование небольших зких трещин в виде отдельных глублений, развивающиеся края которых имеют радиусы кривизны поря дка атомных размеров. Трещины могут проходить по границам зерен, как, например, в алюминиевых сплаваха или латуни, или через-зерна, как, например, в аустенитных нержавеющих сталя х или в магниевых сплавах. Количество образующихся трещин может быть различным, но обычно одна трещин развивается в большей степени, чем другие.
2. По мере развития трещины у ее вершины создается конценнтрация напря жений. Для пластичных сплавов эта концентрация напря жений не превышает максимальной величины, которая принблизительно в 3 раза больше предела текучести. При достаточно высоких напря жения х у вершины трещины происходит местная пластическая деформация , которая предшествует хрупкому разруншению. В настоя щее время становлено, что в пластичных металнлах хрупкое разрушение не может иметь места без предшествуюнщей пластической деформации. Действительно, именно деформация металла у развивающегося края трещины вызывает хрупкое разрушение за счета действующих у вершины трещины напря жений.
3. В зависимости от формы образца, способа приложения нангрузки, словий испытания и определенного энергетического состоя нния металла, свойственного процессу развития хрупкого разрушенния , трещина может распространиться через весь образец, вызвав-мгновенное разрушение его, или, распространившись на определеое расстоя ние, развитие ее может прекратиться . Развитие тренщины может быть приостановлено при неблагоприя тной для пронцесса растрескивания ориентации границ зерен, при неоднороднонсти кристаллической решетки или приа наличии неметаллических включений; развитие ее может остановиться в результате релаксанции напря жений при развитии трещины или при определенном энернгетическом состоя нии, когда производимая работа деформации бундет больше, чем величение поверхностной энергии, как отмечено у Ирвин и Орована.
4. Развитие трещины за счет механического разрушения обнанжает свежую поверхность металла, и коррозионная среда быстро засасывается в трещину под действием капилля рныха сил, в результате чего наступает период интенсивной коррозии. Вполне возможно, что эта стадия интенсивной коррозии способствует развитию; трещины, причем коррозия развивается таким образом, что вызывает разветвление трещины. Однако следует считать, что главным фактором в развитии трещины я вля ется механическое воздействие не электрохимические процессы.
5. скоренный процесс коррозии, вызванный действием коррозинонной среды на не защищенную пленкой поверхность металла, бынстро замедля ется вследствие поля ризации и повторного образованния защитной пленки, что свя зано с изменением концентрации: электролита внутри трещины.
6. После этого опя ть преобладают условия , медленно развивающая ся локализованная коррозия продолжается до тех пор, пока не возникнет достаточно высокая концентрация , напря жений, которая вызовет деформацию и развитие трещины. Полный цикл процессов повторя ется до тех пор, пока не наступит разрушение вследствие развития трещины или меньшения попенречного сечения напря женного образца.
Вопрос о том, разрушается ли образец сразу после того как обнразовалась первая трещина или в результате развития нескольких трещин в течение какого-то периода времени, не я вля ется сущестнвенным в механизме растрескивания и зависит от формы, размеров и толщины образца, а также от величины напря жений и условий испытания .
Таким образом, представленный выше механизм включает две основные стадии процесса коррозионного растрескивания : период; локализованной электрохимической коррозии и последующий пенриод развития трещин. Если разрушение не происходит очень быcтро, процесс растрескивания включает непродолжительный период интенсивной коррозии. Ниже подробно рассматривается кажндая из стадий процесса растрескивания , а также факторы, опреденля ющие эти стадии, и экспериментальные данные, подтверждаюнщие изложенные ранее гипотезы.
8 Начальная стадия локализованной коррозии
Состоя ние поверхности металла, обеспечивающее развитие иннтенсивной локализованной коррозии, вероя тно, подобно тому сонстоя нию, при котором происходит питтинговая коррозия . Локальнное коррозионное разрушение происходит обычно при наличии кантодных и анодных микроэлементов, которые способствуют конценнтрации и скорению электрохимического процесса. Источниками местных анодных частков могут быть: 1) состав и микроструктурные неоднородности сплава, как, например, многофазные сплавы или включения по границам зерен; 2) значительное искажение гранниц зерен или других субструктурных границ, по которым могут выделя ться растворенные атомы; 3) частки границ зерен, возникншие благодаря местной концентрации напря жений; 4) локальнное разрушение поверхностной пленки под действием нанпря жений; 5) частки, возникшие за счет пластической денформации.
9 Системы сплавов, подверженных межкристаллитному растрескиванию
люминиево-медные сплавы. Браун и совторы показали, что, в результате выделения по границам зерен CuAl2 примыкающие к границам зерен зоны обедня ются медью, в результате чего в растворе хлористого натрия между границами зерен и зернами существует разность потенциалов в 200 мв. Эти обедненные медью зоны, анодны по отношению к выделившейся фазе CuAl2 и по отношению к самим зернам.
Сплавы А1 - 7% Мg. Джильберт и Хадден показали, что соендинение Мg2А13, которое выделя ется по границам зерен, в нейтральных и кислых растворах хлористого натрия я вля ется анодом по отношению к зернам и к обедненным зонам границ зенрен. В этих растворах b-фаза подвержена избирательной коррозии. В водном растворе едкого натра b-фаза катодна по отношению к телу зерен, и в этом случае не происходит ни избирательной корнрозии, ни коррозионного растрескивания , имеет место только общая коррозия . Эделеану предположил, что подверженность интенсивной избирательной коррозии не обусловлена выделя юнщейся по границам зерен равновесной фазой, свя зана с одним из переходных состоя ний в процессе старения - выделением или адсорбцией растворенных атомов по границам зерен.
Таким образом, в структуре сплавов, прочня ющихся с выденлением второй фазы и подверженных межкристаллитному растренскиванию, имеется три частка с различными электрохимическими характеристиками.
1. Зерна твердого раствора.
2. Выделившая ся по границам зерен фаз (или переходное состоя ние этой фазы или адсорбированных растворенных атонмов).
3. Обедненные каким-либо компонентом частки твердого раснтвора, примыкающие к границам зерен.
Мя гкие стали. Паркинс показал, что выделя ющиеся по гранинцам зерен карбиды вызывают искажение этих границ. В растворах нитратов искаженные границы зерен феррита анодны по отношению к зернам, в результате чего границы служат местом интенсивной межкристаллитной коррозии. Действие напря жений может еще больше исказить эти границы и сделать эту область более аноднной.
Медные сплавы в аммиачных средах. Чистая медь в аммиачных средах не подвержена растрескиванию, но добавление небольших количеств фосфора, мышья ка, сурьмы, цинка, алюминия , кремния или никеля в качестве легирующих элементов, входя щих в однонродный твердый раствор, вызывает межкристаллитное растрескинвание меди. Оказывается , что наблюдаемая разность потенцианлов между границами зерен и зернами и местная межкристаллитная коррозия а могут быть обусловлены искажением границ зерен в результате различной ориентации смежных зерен. Робертсон, показал, что концентрация легирующего компонента в меди, вызывающая беспоря дочную рекристаллизованную структуру, соотнветствует концентрации, которая делает сплав подверженным кор-озионному растрескиванию. В однородных системах причиной развития местной межкристаллитной коррозии может быть химическая активность границ зерен, которая зависит от искажения границ и действия напря жений и деформации. Выделение или адсорбция по раницам зерен растворенных атомов будет значительно влия ть на искажение и активность границ зерен.
В работе Томпсона и Трэси выведено соотношение между концентрацией легирующего компонента, необходимой для полученния подверженного коррозионному растрескиванию сплава, и количеством компонента, которое вызывает межкристаллитную коррозию сплава при отсутствии напря жений. Ни в одном случае не наблюдалось коррозионного растрескивания при легировании компонентами, которые не вызывают первоначальной межкристаллитной коррозии. Интересно отметить, что при значительном величении концентрации легирующих компонентов алюминия и кремния (но не выходя из области твердых растворов) сопротивление растрескинванию величивается и наблюдается смешанный характер растренскивания - и межкристаллитный и внутрикристаллитный, что ненсомненно свя зано с изменением активности границ зерен.
10 Системы сплавов, подверженных внутрикристаллитному растрескиванию
Магниевые сплавы. На основании изучения зависимости между содержанием железа в магниевых сплавах и их стойчивостью пронтив внутрикристаллитного коррозионного растрескивания было вынсказано предположение, что железо-алюминиевая составля ющая , преимущественно выделя ющая ся параллельно определенным кринсталлографическим плоскостя м, в частности плоскости базиса, может быть катодной фазой. Было показано, что разнность потенциалов между соединением FeЧА1 и твердым раствором МgЧА1 в соля нохроматных растворах составля ет 1в. Наблюдаемое межкристаллитное растрескивание некоторых магниевых, сплавов в дистиллированной воде, в растворах хроматов и фторидов, возможно, обусловлено присутствием незначительных примесей по границам зерен. Как известно, сопротивление магния общей корронзии зависит от наличия некоторых примесей - таких, как железо, медь, никель и кобальт, которые в этом отношении особенно активны.
устенитные нержавеющие стали типа 18-8. Стабильность аустенитной фазы в нержавеющих сталя х зависит в основном от содернжания в сплаве никеля и азота. Однако, в сталя х типа 18-8 в рензультате холодной обработки или деформации какая -то часть аустенита может превратиться в мартенсит. Было высказано преднположение, что пластинки мартенсита я вля ются анодной фазой в процессе местной коррозии. Это предположение подверглось критике на основании того, что некоторые аустенитные нержавеюнщие стали, которые даже под влия нием значительной холодной обработки не претерпевают мартенситного превращения , подвернжены коррозионному растрескиванию. Кроме того, нержавеющая сталь типа 18-8 подвержена коррозионному растрескиванию в атнмосфере пара, содержащего хлориды, при температурах, слишком высоких для мартенситных превращений.
Существенным доказательством электрохимического характера локального коррозионного разрушения , т. е. первой стадии процесса коррозионного растрескивания , я вля ется возможность предотвранщения растрескивания при катодной поля ризации и при деаэрации коррозионной среды для некоторых алюминиево-магниевых сплавов. даление кислорода из раствора понижает скорость катодного процесса и тем самым препя тствует электрохимическому разрушеннию.
11 Развитие трещин
Существенным подтверждением гипотез механизма коррозиоого растрескивания я вля ется более подробное изучение харакнтера развития трещин, в частности, микрокиноскопическое исслендование процесса развития трещин. Фильм, засня тый Престом, Беком и Фонтана, показывает, что развитию внутрикристаллитной трещины в магниево-алюминиевых сплавах предшествует волна пластической деформации. Как ранее становлено, для возникнонвения пластической деформации необходимо наличие небольшой трещины, как источника развития хрупкого разрушения . Кроме того, в результате деформации металла у вершины первоначально образовавшейся трещины должно происходить дальнейшее ее глубление и расширение, что наблюдается в действительности. Степень развития трещины в результате деформации определя ется , несомненно, пластическими характеристиками материала, и слендует ожидать, что при наличии непрерывной хрупкой фазы для разнвития трещины потребуется небольшая деформация и расширения трещины совсем не произойдет или будет весьма незначительным.
В результате пластической деформации обычно происходит разнрушение защитных поверхностных пленок в трещине, что вызывает ускорение коррозионного процесса. Но разрушение пленки может играть и более существенную роль в процессе деформации. Было показано, что защитные пленки на монокристаллах и в некоторых поликристаллических материалах препя тствуют протеканию пронцессов ползучести и деформации. Было высказано предположенние, что такие пленки действуют как барьер при передвижении дислокаций и, следовательно, препя тствуют деформации. Коннцентрация дислокаций под поверхностной пленкой вызывает высонкую концентрацию напря жений. Когда пленка разрушается или страня ется химическим путем, дислокации стремя тся к передвиженнию по своему первоначальному направлению, вызывая тем самым самопроизвольную деформацию. Если это передвижение происходит в плоскости развития трещины, должно происходить ее глубление и расширение. Деформация , которая происходит у верншины трещины, очень локализована и трудно обнаруживается обычными методами металлографического анализа. Кроме того, cледует честь, что деформированные частки и поверхности образующихся трещин подвержены интенсивной коррозии, которая может легко ничтожить все признаки существования деформации.
Имеются данные о том, что напря женные и деформированные металлы более активны, чем ненапря женные. Таким образом, часткам с коррозионными трещинами свойственна большая электрохимическая активность, что приводит к скорению процесса трещинообразования . Не может быть сомнения , что скоренный коррозионный процесс вызван разрушением поверхностной пленки и наличием напря женных анодных участков, но мало вероя тно, что эти факторы способствуют общему процессу развития трещин. Если они оказывают влия ние, то только в основном на возникновение небольших местных трещин, необходимых для создания концентранции напря жений и последующего трещинообразования .
Развитие трещины, которая вызывает разрушение металла, не обя зательно происходит в том же месте, где поя вилась первая мелнкая трещина. Форма образца и характер деформации могут быть такими, что основная трещина развивается на некотором расстоя ннии от первоначально поя вившейся небольшой трещины.
Ирвин и совторы характеризуют процесс развития тренщины следующим образом. Первоначальное зарождение трещин происходит на разрозненных, не свя занных между собой частках с большими растя гивающими напря жения ми. Мелкие разрознеые трещины, соединя я сь, образуют одну трещину. Как отмечается , процесс трещинообразования начинается на ослабленных частках металла, и первые стадии его сопровождаются пластической дефорнмацией. Развитие трещины носит прерывистый характер, и это я вля ется основным свойством быстрого трещинообразования .
Быстрое начало и прекращение отдельных процессов прерывинстого трещинообразования производит на металл сильное механинческое воздействие, что может вызвать дальнейшее развитие и разнветвление трещины. Развитие трещины приостановится , когда она достигнет области, где нет достаточных растя гивающих напря женний, направление которых перпендикуля рно направлению развития трещины. Следовательно, для последующего развития трещины ненобходима дальнейшая деформация . Большие трещины обладают способностью развиваться быстрее, чем мелкие. По мере роста мелких трещин крупные трещины развиваются значительно бынстрее, и вскоре начинает преобладать только одна трещина, котонрая останавливает развитие других. Характер развития трещин в пластичных металлах обеспечивает возникновение ря да быстро развивающихся трещин, так как новые трещины образуются по ходу .продвижения основной трещины и соединя ются с ней. Когда энергия деформации, выделя ющая ся при развитии основной тренщины, становится равной работе деформации, происходит процесс быстрого саморастрескивания . В эту главу не входит подробное обсуждение работ Ирвина и Орована об относительном равновесии между совершённой работой и энергией, освобождаюнщейся при развитии трещины. Следует казать, что если энергия деформации, выделя ющая ся при развитии трещины, больше энернгии, необходимой для нового разрушения поверхности, трещина будет развиваться самопроизвольно. Ирвин также показал, что сконрость развития трещины будет величиваться до тех пор, пока не будет достигнуто неустойчивое состоя ние, после чего произойдет быстрое разрушение.
Изложенное рассмотрение процесса возникновения и развития трещины более точно характеризует природу коррозионного растренскивания . На прерывистый характер развития трещин казывают Эделеану, Джильберт и Хадден, Фармери для алюминиенвых сплавов, также Преет, Бек и Фонтана для магниевых спланвов. Очевидно, нет сомнения , что при растрескивании материал подвергается серии отдельных механических разрушений, которые, соединя я сь вместе, образуют трещину. Кроме того, фильмы и микрофотографии, имеющиеся а в литературе, показывают, что растрескивание происходит путем продвижения развивающейся трещины. Можно ожидать, что изложенный механико-электрохимический механизм коррозионного растрескивания может достаточно точно объя снить наблюдаемые я вления процесса коррозионного растрескивания , среди которых основнными я вля ются а следующие:
1. Трещины не возникают и не развиваются под действием сжинмающих напря жений.
2. Более высокие напря жения , особенно напря жения , близкие к пределу текучести, вызывают более высокую концентрацию нанпря жений и соответственно меньшают стойчивость металла протнив растрескивания .
3. Для создания достаточной концентрации напря жений и послендующей деформации необходим какой-то минимума напря жений, тот минимальный предел напря жений не я вля ется абсолютной величиной и зависит от формы образца и словий испытания . Следует также казать, что предел пругости или текучести на отдельных микроскопических частках может быть значительно ниже, чем тенкучесть сплава.
4. В том случае, когда разрушение металла происходит почти сразу после образования первоначальной трещины, время до раснтрескивания зависит от времени, необходимого для зарождения мелких коррозионных трещин. Важным фактором я вля ется также состоя ние поверхности. При разрушении, включающем ря д повторнных циклов процесса растрескивания , общее время до разрушения определя ется как суммарное время образования серии коррозиоых трещин. Не наблюдается значительного отличия во времени до разрушения образцов, нагруженных в течение всего испытания , и образцов, нагруженных незадолго до разрушения ; время , необхондимое для коррозионного растрескивания , не зависит существенно от словий создания напря женного состоя ния металла.
5. Доказательством того, что наибольшее влия ние приложеые напря жения оказывают незадолго до разрушения , служит самопроизвольное растрескивание металла после зарождения пернвоначальной трещины. Если процесс растрескивания происходит за счет образования серии мелких трещин и по мере развития трещины металл приближается к неустойчивому состоя нию, то при нанличии деформированных частков металлапроизойдет самопроизнвольное развитие трещины и полное разрушение металла.
6. Катодная защита препя тствует развитию локальных корронзионных разрушений. При наложении катодного тока величинваются радиусы возникающих коррозионных глублений, в резульнтате чего коррозионный процесс может происходить только при величении напря жений. Поэтому для предотвращения коррозиоого растрескивания при повышенных напря жения х должна примення ться более эффективная защита, которая будет препя тствовать возникновению локальных коррозионных разрушений и созданию концентраторов напря жений.
Полагают, что если развитие трещины достигнет такого знанчения , что создаются словия для самопроизвольного растренскивания , то применение кантодной защиты не окажет нинкакого влия ния .
7. Если время до растрескинвания относительно мало и разнвивается только одна или ненсколько трещин, то не наблюндается существенного отличия в коррозии (в количестве менталла, переходя щего в раствор) напря женных и ненапря женных образцов, как показал, например, Эделеану для сплава АЧ7% Мg, так как развитие трещин идет практически только за счет механического разрушения . С другой стонроны, процесс химического разрушения приводит к переходу в раснтвор измеримого количества металла, но переход металла в раствор не будет существенно зависеть от времени до разрушения .
8. Предложенный механизм растрескивания а согласуется а с наблюдаемым я влением, обнаруживающим одинаковую скорость развития образовавшихся трещин в материале, подверженном коррозионному растрескиванию, и в сравнительно стойчивом материале. Зависимость стойчивости металла против коррозионного растренскивания от его структуры и коррозионной среды в значительно мольшей степени проя вля ется в первый период зарождения локальнного разрушения , чем при последующей стадии развития трещин.
9. Чем меньше размер зерна металла, тем больше его стойчинвость против коррозионного растрескивания . При величении разнмера зерна меньшается время до разрушения . Казалось бы, что чем больше число зерен, тем больше число границ зерен, имеющих высокую электрохимическую активность, в результате чего более вероя тен процесс локального коррозионного разрушения ; однако при мелкозернистой структуре условия а для зарождения трещин довольно неблагоприя тные. Доказано, что сопротивление хрупкому разрушению поликристаллических металлов обратно пропорционально квадратному корню размера зерна. Слендовательно, для разрушения мелкозернистого поликристалличенского материала требуются повышенные напря жения . Поэтому крупнозернистые металлы с благоприя тной ориентацией границ зерен очень неустойчивы против коррозионного растрескивания .
В случае межкристаллитного растрескивания большое значение имеет выделение растворенных атомов по границам зерен, так как предполагается , что адсорбция растворенных атомов по границам зерен меньшает энергию границ зерен и снижает напря жения , необходимые для того, чтобы вызвать хрупкое разрушение (т. е. снижает работу, необходимую для образования новой поверхности). Любой адсорбционный процесс на частках металла с несонвершенной структурой, который меньшает работу, необходимую для образования новой поверхности, значительно величивает теннденцию таких частков к трещинообразованию при наличии напря нжений.
Очевидно, следует предположить, что хрупкое межкристаллитное растрескивание сплавов вызвано содержанием по границам зерен интерметаллических фаз; в этом случае существуют очень благонприя тные словия для развития по границам зерен местной корронзии, развитие хрупкого разрушения происходит за счет интерметаллической фазы. Для однородных твердых растворов, в которых имеет место межкристаллитное растрескивание (напринмер, в а-латуни), определя ющим фактором я вля ется адсорбция или выделение растворенных атомов по границам зерен.
12 Общие закономерности я вления коррозийного растрескивания
Вполне очевидно, что сплавы, основу которых составля ют благонродные металлы, я вля ются наиболее стойчивыми против коррозинонного растрескивания , так как легирующие компоненты таких сплавов всегда менее благородий. Кроме того, для таких сплавов ограничено число коррозионных сред, в которых может происхондить растрескивание. С другой стороны, для такого очень активнного металла, как магний, все легирующие компоненты более блангородны, поэтому магниевые сплавы сильно подвержены коррозиоому растрескиванию. Для магния даже вода я вля ется активной коррозионной средой.
Среди специальных групп сплавов, не подверженных коррозиоому растрескиванию, можно отметить сплавы золота, палладия и платины.
Однако для сплавов серебра словия для коррозионного растренскивания более благоприя тны. Во-первых, серебро часто испольнзуется в виде сплава с более благородными металлами, такими, как золото, палладий и платина; во-вторых, серебро быстро вступает.в реакцию с сильными окислителя ми, такими, как азотная и хромовая кислоты, также с соля ной кислотой и хлорным железом. Прендел устойчивости для этих сред лежит примерно при 40 ат. % Аu, так что коррозионное растрескивание будет иметь место во всех сплавах с золотом, содержащих менее 58,5 вес. % золота. В свя зи с этим имеются многочисленные примеры коррозионного растрескинвания сплавов серебра, содержащих золото и палладий, применя юнщихся в зубоврачебном деле. Коррозионное растрескивание этих сплавов наблюдалось после очистки их в соля ной кислоте в пронцессе производства. С другой стороны, сплавы серебра, содержащие менее благородные компоненты, не подвержены коррозионному раснтрескиванию. Это подтвердилось при испытании однородных сплавов системы АuЧZn, содержащих 25 ат. % Zn, и сплавов системы AgЧА1, содержащих 13 ат. % А1. Образцы из этих сплавов, испынтываемые под напря жением в 2%-ном растворе FeС3, не подверганлись коррозионному растрескиванию даже в течение продолжительнного времени испытания .
Медные сплавы более подвержены коррозионному растрескинванию. Число более благородных легирующих компонентов для меди не меньше, чем для серебра, но основная опасность обусловнлена тем, что в любой среде, содержащей хотя бы незначительное количество аммиака, происходит коррозионное растрескивание меднных сплавов. Все сплавы, содержащие небольшое количество зонлота, использующиеся в производстве ювелирных изделий, я вля нются сплавами на медной основе. Из всех использующихся сплавов меди с золотом только один сплав, содержащий 75 вес.% золота, не подвержен коррозионному растрескиванию. Для остальных сплавов их стойчивость зависит от коррозионной среды и предела устойчинвости.
Предел стойчивости для сплавов системы СuЧАu в растворе аммиак составля ет примерно 20 ат.% Аu, так что сплавы, содержащие 50 вес. % золота, не подвержены коррозиоому растрескиванию в этой среде. Но в 2 %-ом растворе FeС3 танкие сплавы, содержащие меньше 35 ат.% Аu, подвержены коррозинонному растрескиванию. Поэтому в ювелирном деле следует принменя ть сплавы, содержащие не менее 58,5 вес.% золота, с использованием их при возможно более низких напря жения х. Однако в случае технического использования , включающего наличие в сплаве внутренних напря жений и воздействие коррозионной среды (например, изготовление перьев для авторучек), такие сплавы нендостаточно устойчивы. Но если часть меди в этих сплавах заменя ть серебром (по весу), как это часто делается на пракнтике, то атомная доля золота в сплаве величивается и соответнственно величивается сопротивление коррозионному растрескиваннию.
Особое внимание следует делить такому важному сплаву, как латунь, где медь легирована менее благородным компонентом (циннком) и поэтому, согласно правилам, не должна подвергаться корнрозионному растрескиванию. Однако практически очень часто пронисходит сезонное растрескивание латуни. Тщательное исследование показывает, что коррозионное растрескивание латуни происходит только в аммиачных средах, тогда как раствор FeС3, концентрированные кислоты НС1 и НNОз вызывают только общую поверхнонстную коррозию.
Это отклонение от правил вызвано особым поведением меди в аммиачной среде, в которой образуются комплексные ионы с медью, что вызывает характерный тип коррозии, не свойственной другим средам. В растворах цианистого калия также образуются комплексные ионы, но в отличие от аммиака эта среда не вызывает коррозионного растрескивания сплавов систем СuЧАu и СuЧAu, хотя она, подобно царской водке, вызывает коррозию золота.
Все остальные технически пригодные металлы менее благородны, чем водород. Из всех технических металлов наименее благородным я вля ется магний, в результате чего все легирующие компоненты всегда более благородны, что и обусловливает сильную поднверженность магниевых сплавов коррозионному растрескиванию Даже вода, я вля ющая ся для магния активной коррозионной cредой, при наличии внутренних напря жений может вызвать коррозинонное растрескивание магниевых сплавов. Поэтому использование таких сплавов в технике в значительной степени ограничено. В рензультате небольшой растворимости алюминия и цинка в магнии сплавы магния с этими компонентами пересыщены при комнатной температуре, вследствие чего всегда приходится решать вопрос о том, преобладает ли совершенно однородное состоя ние сплава или в сплаве имеются субмикроскопические выделения второй фазы, вызывающие коррозионное растрескивание. Однако исследования автора, проводимые с магниевыми сплавами, содержащими принмерно 1 ат. % А1 и имеющими совершенно однородную структуру, показали, что, несмотря на отсутствие выделений второй фазы, пронисходит коррозионное растрескивание сплавов.
Более стойкими против коррозионного растрескивания я вля ются алюминиевые сплавы, особенно если они легированы менее благонродным элементом - магнием. Согласно общим правилам, коррозинонному растрескиванию подвержены только те алюминиевые сплавы, которые содержат цинк и медь, сплавы системы АЧMg не растрескиваются даже в пересыщенном состоя нии, что неоднонкратно подтверждалось исследования ми.
Литература
В основу реферата был взя т сборник статей зарубежных авторов: Коррозионное растрескивание и хрупкость (1962г.)
Список авторов и их статьи:
1. D. K. Priest, F. H. Beck and M. G. F o n t a n a, Trans. ASM* 47, 473 (1955).
2. A. Morris, Trans. AIME, 89, 256 (1930).
3. C. Edeleanu, J. Inst. Metals, 80, 187 (1952).
4. P. T. Gilbertа and S. E. Madden, J. Inst. Metals, 77, 237 (1950).
5. U. R. Evans, Symposium on Properties ofа Metallic Surfaces, p. 264, Inst. of Metals, London 1953.
6. F. A. Champion, Symposium on Internal Stressesа in Metals and Alloys p. 468, Inst. of Metals, London 1948.
7. H L. Logan, J. Research Natl. Bur. Standards, 48, 99 (1952).
8. G. R. Irwin and J. A. Kies, Welding J., 31, 95(1952); G. R. Irwin, Conference on Brittle Fracture Mechanics, p. 169, Natl. Research Council Rept., May, 17, 1954.
9. W. D. Robertson, Trans. AIME, 188, 791 (1Q50).
10. D. H. Thompson and A. W. T r a c y, J. Metals, 1, 100 (1942).
11. R. D. Heidenreich, R. McNulty and R. C. Gerould, Trans. AIME, 166, 15 (1946).
12. M. R. Pick us and E. R. Parker, J. Metals, 3, 792 (1951).
S. Harperа and A. H. Cottrell, Proc. Phys. Soc.. B63, 331 (1950).
E. N. da C. Andrade and R. F. Y. Randall, Nature, 162, 890
(1948).
J. W. Menter and Hall E. O., Nature, 165, 611 (1950).
13. J. J. Harwood, Corrosion, 6, 249 (1950).
14. F. D. Coffin and S. L. Simon, J. Appl. Phys., 24, 1 (1953).
15. A. H. Cottrell, Dislocations and Plastic Flowа in Crystals, p. 55,. Oxford 19
так же
15 Исаев Коррозия металлов
16 Жук Курс коррозии и защиты металлов
17а Материаловедение и технология металлов. Под ред. Г.П.Фетисова
М.: Высшая школа, 2001