В. А. Хандожко модернизация автоматизированной системы научных исследований контактной жесткости на основе усовершенствованной нормализованной методики испытаний
Вид материала | Документы |
- М. И. Прудников Метод триботехнических испытаний цилиндрических поверхностей трения, 168.82kb.
- Ix всероссийская заочная научно-практическая конференция модернизация системы, 119.71kb.
- Секция автоматизированные системы обработки информации и управления, 62.56kb.
- Аннотация дисциплины «методология научных исследований», 17.31kb.
- Правила этической экспертизы инициативных научных исследований методическое пособие, 681.68kb.
- Казанского Государственного Технического Университета (кгту им. А. Н. Туполева) и Казанского, 110.87kb.
- А. Ф. Рочев Начальник Управления организации муниципальных закупок Е. Н. Мисбахова, 722.05kb.
- Пояснительная записка к проекту первой редакции типовой методики сертификационных испытаний, 10.88kb.
- Инструкция пользователю автоматизированной системы общие обязанности сотрудников организации, 73.18kb.
- "Краны грузоподъемные. Типовые программы и методики испытаний" согласован письмом Госгортехнадзора, 1319.49kb.
Вестник Брянского государственного технического университета. 2006. № 2 (10)
УДК 621.9
В.А. Хандожко
МОДЕРНИЗАЦИЯ АВТОМАТИЗИРОВАННОЙ СИСТЕМЫ НАУЧНЫХ ИССЛЕДОВАНИЙ КОНТАКТНОЙ ЖЕСТКОСТИ НА ОСНОВЕ УСОВЕРШЕНСТВОВАННОЙ НОРМАЛИЗОВАННОЙ МЕТОДИКИ ИСПЫТАНИЙ
Предложен вариант модернизации АСНИ контактной жесткости на базе современной платы сбора данных PCI-1202.
При проведении экспериментальных исследований в последние годы широкое применение находят автоматизированные системы научных исследований. В кандидатской диссертации А.Е. Захарова была разработана автоматизированная установка для измерения контактной жесткости в соответствии с методическими указаниями [1]. В указанном источнике предлагается измерять контактную жесткость стыка, в котором одна из поверхностей принята идеальной (гладкой и недеформируемой), с использованием конкретных нагрузок, определяемых в зависимости от твердости и высотного параметра шероховатости Rz (по ГОСТ 2789-73) поверхности. При этом указания [1] распространяются на поверхности с шероховатостью от Ra = 0,32 до Rz = 320 мкм при изменении твердости от 20 до 300 НВ. Ограничение по твердости объясняется допущением, что индентор гладкий и недеформируемый. Для этого он подвергается термообработке (цементации) с последующими шлифованием и доводкой.
Согласно литературным данным, упругая деформация волнистости и подложки в несколько раз меньше пластической деформации.
Согласно [2] пластическая деформация поверхностных слоев определяется по формуле (1), упругая – по формуле (2).
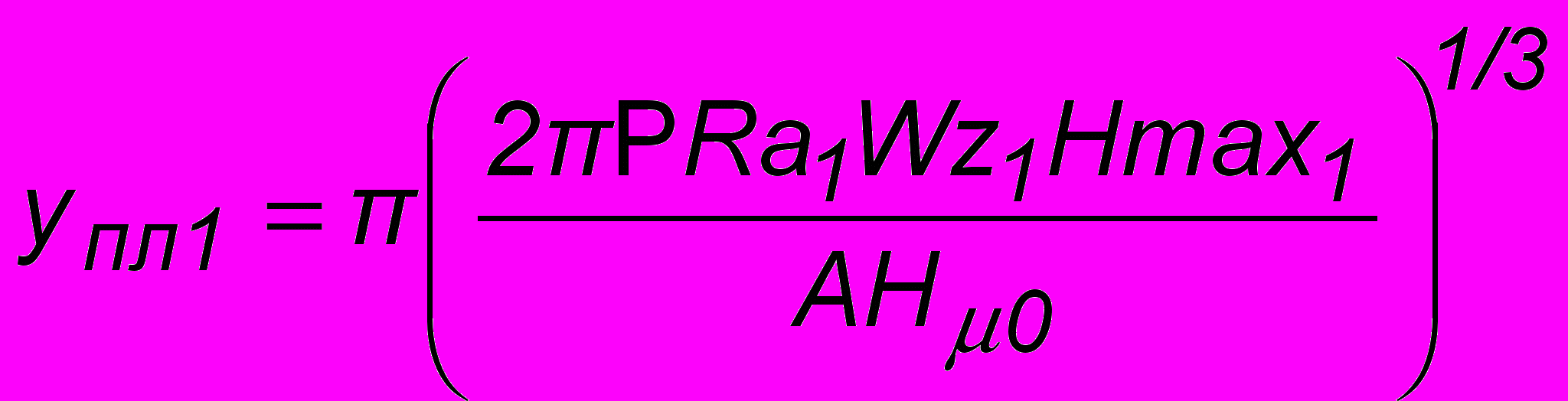
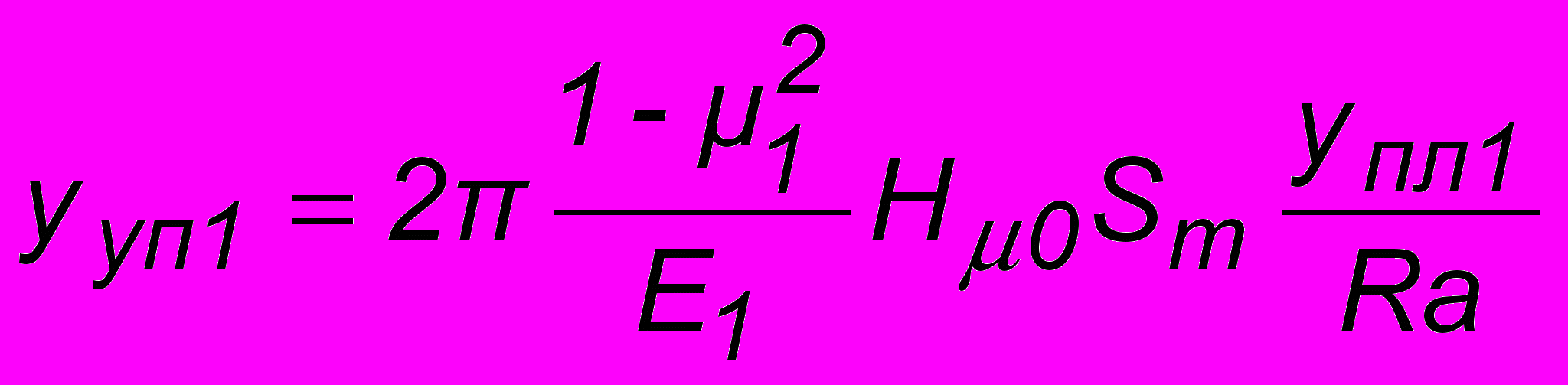
где yпл1 – пластическая деформация одной из поверхностей в контакте; yуп1 - упругая деформация одной из поверхностей в контакте.
И
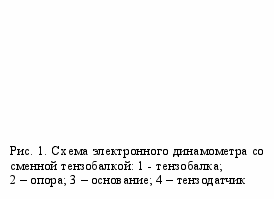
Анализ поверхностей, для которых имеет значение контактная жесткость (в первую очередь, детали станков: привалочные плоскости корпусных деталей; торцовые поверхности гильз, стаканов, фланцев, регулировочных колец; детали универсально-сборных приспособлений и т.д.[3]), показал, что их шероховатость изменяется от Ra = 0,04 до Ra = 3,2 мкм. Все эти детали подвергаются термообработке, и твердость их рабочих поверхностей составляет 30-55 HRC.
Однако для таких условий рекомендации [2] неприменимы, поскольку допущение о недеформируемости индентора вызовет погрешность, сопоставимую с измеряемой величиной.
В существующую АСНИ контактной жесткости входит электрический привод постоянного тока с высокомоментным двигателем, управляемый от платы сбора данных и управления NVL-03. Данная плата также выполняет оцифровку сигнала с усилителей тензодатчиков и индуктивного датчика перемещений. Для программирования данной платы поставляются драйверы, программируемые в операционной системе MS-DOS на языках С и С++.
В настоящее время существуют SCADA-системы, такие как LabVIEW, которые позволяют создавать виртуальные инструменты специально для работы с платами сбора данных. Такие системы позволяют быстро создавать программу для считывания информации с датчиков с удобным графическим оформлением. В дальнейшем возможна передача результатов эксперимента в файл с их статистической обработкой в системах Mathcad или Statistica.
При модернизации АСНИ планируется применение современной платы сбора данных PCI-1202 фирмы ICP DAS. Плата представляет собой низкочастотный (110 кГц) 12-разрядный 16-канальный аналого-цифровой преобразователь. Помимо этого, имеются два цифроаналоговых преобразователя и по 16 цифровых входов и выходов. С платой поставляются драйвера-функции для программирования каналов сбора данных и управления в LabVIEW.
Модернизация АСНИ также необходима и в отношении точности измерений силы и контактных перемещений.
Анализ систем электронных динамометров показал, что для заданного диапазона нагрузок (от 10 г до 300 кг) нет серийно выпускаемых динамометров сжатия. Возможно их изготовление на заказ или собственными силами. Предлагаемая схема измерений (рис.1) достаточно проста, а динамометр несложно изготовить.
Тензодатчики соединены в полномостовую схему. Для усиления сигнала с тензомоста динамометра используется серийно изготовляемый тензометрический модуль I7016P. Для изменения диапазона измерений применяется сменная тензобалка.
Заданная точность измерения перемещений – 0,1 мкм - принципиально недостижима в базовой конструкции узла измерения перемещений, так как только теоретическая точность датчика составляет 0,1 мкм. Анализ современных датчиков перемещений показывает, что требуемой точности можно достичь с помощью индуктивных и емкостных датчиков, причем наиболее высокую точность обеспечивают емкостные датчики. Так, фирма MicroEpsilon предлагает высокоточный емкостной датчик DT6630 с точностью измерения 0,1 нм. Недостатком его применения является необходимость поддержания идеальной чистоты в контакте между электродами.
Предлагается индуктивный датчик перемещений transSENSOR фирмы MicroEpsilon с точностью 2 мкм. Заданная точность будет обеспечиваться установкой промежуточной балки (рис. 2).
Принципиальным его отличием от индуктивного датчика линейных перемещений М-30 с Ш-образной системой завода «Калибр», применяемого в базовой АСНИ, является отсутствие изнашивающихся частей. Контроллер transCON содержит генератор питания первичной обмотки датчика, выпрямитель и усилитель сигнала.
На рис. 3 представлена структурная схема модернизированного варианта АСНИ.
П
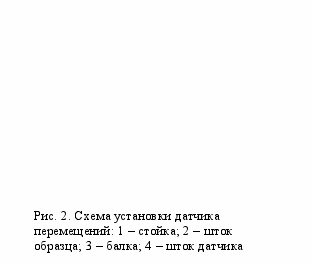
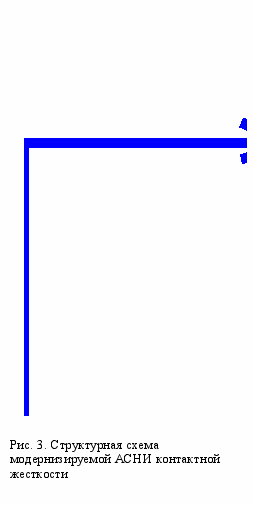
о программе от ПЭВМ цифро-аналоговый преобразователь (ЦАП) управляет двигателем посредством комплектного электропривода. Механизм нагружения включает червячный редуктор, в червячном колесе которого перемещается винт. При нагружении индентор упирается в образец, деформируя его. В это время датчик перемещений transSENSOR измеряет контактное сближение, а электронный динамометр – нагрузку. Программа, имея исходные данные об эксперименте – вид поверхностей в контакте «плоскость-плоскость», «плоскость-сфера», «цилиндр-сфера» и др.), размеры контактирующих площадок, количество инденторов, - определяет давление и контактную жесткость, формируя протокол эксперимента. В реальном времени программа сравнивает текущую нагрузку с заданной и в момент их совпадения реверсирует двигатель. Процесс нагружения происходит 6 раз. Программой фиксируется контактная жесткость при первом (пластическая + упругая деформация) и при повторных нагружениях (только упругая деформация).
СПИСОК ЛИТЕРАТУРЫ
- Метод определения нормальной контактной жесткости неподвижных стыков: метод. рекомендации. – М.:ВНИИМАШ, 1982.
- Суслов, А.Г. Технологическое обеспечение параметров состояния поверхностного слоя деталей машин/ А.Г. Суслов. – М.:Машиностроение, 1987.- 208 с.
- ЭНИМС. Основные нормы. Нормали станкостроения и руководящие материалы.- М., 1969.
Материал поступил в редколлегию 20.02.06.