
Технологическое обеспечение точности профильного шлифования алмазными кругами, упроченными пластическим деформированием
Автореферат кандидатской диссертации
На правах рукописи
СОКОЛОВ Алексей Владимирович
Технологическое обеспечение точности
профильного шлифования алмазными кругами,
аупрочненными пластическим деформированием
Специальности: 05.02.08 - Технология машиностроения;
05.02.07а - Технология и оборудование механической
и физико-технической обработки
А в т о р е ф е р а т
диссертации на соискание ученой степени
кандидата технических наук
ПЕНЗА 2012
Работа выполнена в ФГБОУ ВПО Пензенский государственный университет.
Научный руководитель: |
доктор технических наук, профессор ЗВЕРОВЩИКОВ Владимир Зиновьевич |
Официальные оппоненты: |
САВИЦКИЙ Владимир Яковлевич, доктор технических наук, профессор, Военный учебно-научный центр сухопутных войск Общевойсковая академия вооруженных сил Российской Федерации (филиал в г. Пензе), профессор кафедры Общепрофессиональные дисциплины; БРЖОЗОВСКИЙ Борис Максович, доктор технических наук, профессор, ФГБОУ ВПО Саратовский государственный технический университет, заведующий кафедрой Конструирование и компьютерное моделирование технологического оборудования в машино- и приборостроении |
Ведущее предприятие: |
ФГУП ФНП - ПО ?Старт? им. М. В. Проценко |
Защита диссертации состоитсяа 11 мая 2012 г., в 12 часов, на заседании диссертационного совета Д 212.186.03 в ФГБОУ ВПО Пензенский государственный университет по адресу: 440026, г. Пенза,
ул. Красная, 40.
С диссертацией можно ознакомиться в библиотеке ФГБОУ ВПО Пензенский государственный университет.
Автореферат разослан л___ апреля 2012 г.
Ученый секретарь
диссертационного совета Воячек Игорь Иванович
ОБЩАЯ ХАРАКТЕРИСТИКА РАБОТЫ
Актуальность темы. Быстрое развитие техники стимулирует применение в машиностроении деталей из твердых сплавов, ферритов, композиционных и других труднообрабатываемых материалов. Изготовление таких твердосплавных инструментов, как фасонные резцы, протяжки, метчики, а также шлифование деталей из неметаллических материалов - ферритов, керамики - невозможно без широкого использования различных алмазных инструментов.
Детали из труднообрабатываемых материалов со сложным профилем поверхности изготавляются преимущественно путем последовательной обработки отдельных участков профиля на копировально-шлифовальных и оптико-шлифовальных станках, а также методом врезного шлифования с применением алмазных профильных кругов. Применение метода врезного шлифования фасонными алмазными кругами вместо шлифованияа путем последовательного обхода обрабатываемого контура шлифовальным кругом позволяет стабилизировать точность и повысить производительность шлифования до 10Е50 раз.
При шлифовании фасонных поверхностей задача повышения стойкости и сохранения профиля кругов выдвигается на первый план. В процессе шлифования потеря формы рабочей поверхности возможна как в результате неравномерного износа круга на различных участках вследствие выкрашивания зерен и вырывания их из связки, так и в результате забивания пор круга шламом, что приводит к засаливанию и потере режущей способности на отдельных участках профиля.
Для повышения стойкости кругов приа профильном шлифовании используют связки с повышенным алмазоудержанием, к которым относятся, в первую очередь, металлические связки. Явление засаливания при этом возникает наиболее часто и ведет к снижению режущей способности круга, что отрицательно сказывается на производительности шлифования и качестве шлифованной поверхности.
Восстановление профиля шлифовального круга путем частых правок со значительным удалением материала связки приводит к увеличению операционного времени и сокращению срока службы инструмента.
Доминирующее влияние на точностные параметры детали оказывает форма режущего контура фасонного круга, зависящая от технологических возможностей метода профилирования его рабочей поверхности.
Следовательно, при врезном шлифовании поверхностей деталей авесьма актуальной является задача повышения точности профилирования алмазных кругов на металлических связках, стабилизация режущих свойств и размерной стойкости фасонных акругов.
Цель работы заключается в повышении точности профильного шлифования фасонными алмазными кругами на металлической связке путем упрочнения материала связки пластическим деформированием и периодической электроэрозионной правки круга в процессе обработки.
Для достижения поставленной цели сформулированы следующие
задачи:
- разработать способ врезного шлифования деталей фасонными алмазными кругами с периодическим электроэрозионным воздействием на связку для сохранения формы профиля;
- разработать способ профилирования алмазных кругов при комбинированном воздействии на алмазоносный слой электрическими разрядами и поверхностным пластическим деформированием для окончательного формирования фасонного профиля;
- установить в виде аналитических зависимостей влияние технологических факторов на деформируемость металлической связки алмазоносного слоя и величину напряжения при электроэрозионной правке круга для достижения точностных параметров при шлифовании сложнопрофильных поверхностей деталей;
- выполнить экспериментальные исследования точностных параметров фасонного профиля круга и качественных характеристик поверхности послеа врезного шлифования с периодической электроэрозионной правкой;
- разработать рекомендации по регламентированию технологических режимов врезного шлифования и профилированию кругов;
- внедрить результаты исследований в производство.
Объект исследования: технологические операции профилирования алмазных кругов и врезного шлифования фасонными кругами.
Предмет исследования: взаимосвязи технологических факторов профилирования алмазных кругов и режимов шлифования деталей фасонными кругами, стабильно обеспечивающие точностные параметры обрабатываемой поверхности.
Методы исследования. Теоретические исследования выполнены с использованием научных положений технологии машиностроения, теории резания, теории упругости и пластичности материалов, теоретической физики, методов математического моделирования и планирования экспериментов.
Экспериментальные исследования выполнены в лабораторных и производственных условиях с использованием аттестованной контрольно-измерительной аппаратуры. Результаты экспериментальных исследований обработаны с применением программных пакетов Microsoft Office Excel,а Mathsoft Mathcad и других программ.
Достоверность и обоснованность научных результатов обеспечивается корректной математической формулировкой задач для описания физических закономерностей процессов износа шлифовальных кругов и упрочнения материала связки, сходимостью теоретических результатов и экспериментальных данных, а также результатами внедрения в производство.
Основные результаты, выносимые на защиту:
- новый способ профилирования алмазных шлифовальных кругов на металлических связках с комбинированным воздействием на алмазоносный слой электрической эрозией и упрочнением связки накатыванием;
- новый способ шлифования профильными алмазными кругами с периодическим восстановлением режущих свойств рабочей поверхности электрическими разрядами в процессе обработки;
- аналитическое обоснование силы деформирования при поверхностном упрочнении алмазоносного слоя круга накатыванием и величины напряжения при электроэрозионной правке круга для восстановления фасонного профиля круга и удаления продуктов шлифования из межзернового пространства без интенсивного воздействия на материал связки;
- результаты экспериментальных исследований производительности профильного шлифования и шероховатости поверхности по параметру Ra адля образцов из твердого сплава, феррита и конструкционной стали, упрочненной борированием, представленные в виде полиномиальных моделей, устанавливающих связи между режимами шлифования;
- теоретическое обоснование возможности управления качественными характеристиками поверхностного слоя ферритовых деталей при алмазном шлифовании путем активации технологической жидкости с ультрадисперсными добавками (наночастицами) ультразвуковым воздействием;
- рекомендации по определению рациональных режимов профилирования алмазных шлифовальных кругов и врезного шлифования фасонными алмазными кругами с периодической электроэрозионной правкой в процессе обработки.
Научная новизна
По специальности 05.02.08:
- Получена аналитическая зависимость радиальной составляющей силы резанияа от глубины резания, твердости обрабатываемого материала и объема межзернового пространства при врезном шлифовании, позволяющая ограничить ее предельные значения и предотвратить засаливание алмазного круга между правками.
- Получены эмпирические полиномиальные модели влияния режимов предлагаемого способа шлифования на производительность обработки, необходимые для проектирования технологической операции.
- Теоретически обоснована и экспериментально подтверждена возможность управления качественными характеристиками поверхностного слоя при шлифовании ферритов путем активации технологической жидкости с ультрадисперсными добавками (наночастицами) на основе ультразвукового капиллярного эффекта.
По специальности 05.02.07:
- Установлены взаимосвязи технологических факторов и получено выражение для определения предельной силы деформирования алмазоносного слоя связки круга накатным роликом, при превышении которой происходит разрушение алмазоносного слоя.
- Предложена зависимость, устанавливающая связь напряжения источника постоянного тока с технологическими факторами, на основе которой реализуется режим правки с удалением минимальной толщины алмазоносного слоя, достаточной для восстановления режущей способности и коррекции профиля круга.
Практическая ценность:
- предложен новый способ шлифования с периодическим восстановлением профиля круга и его режущей способности путем электроэрозионного воздействия в процессе обработки, позволяющий снизить трудоемкость изготовления деталей;а
- разработан новый способ окончательного профилирования фасонных алмазных шлифовальных кругов пластическим деформированием металлической связки, обеспечивающий повышение стойкости инструмента;
- обоснована технология шлифования ферритовых деталей с добавлением наночастиц в состав технологической жидкости для заращивания микротрещин на поверхности после шлифования, позволяющая повысить эксплуатационные характеристики изделий.
Соответствие паспорту научной специальности.
Выполненная диссертационная работа соответствует паспортам специальностей 05.02.08 - Технология машиностроения и 05.02.07 - Технология и оборудование механической и физико-технической обработки по следующим областям исследований.
По специальности 05.02.08:
- совершенствование существующих и разработка новых методов обработки и сборки с целью повышения качества изделий машиностроения и снижения себестоимости их выпуска;
- технологическое обеспечение и повышение качества поверхностного слоя, точности и долговечности деталей машин.
По специальности 05.02.07:
- исследование механических и физико-технических процессов в целях определения параметров оборудования, агрегатов,а механизмов и других комплектующих, обеспечивающих выполнение заданных технологических операций и повышение производительности, качества, экологичности и экономичности обработки;
- новые технологические процессы механической и физико-техни-ческой обработки и создание оборудования и инструментов для их реалии-зации.
Реализация результатов работы. Результаты исследований внедрены на ОАО Пензадизельмаш (г. Пенза) и ФГУП ФНП - ПО ?Старт?
им. М. В. Проценко (г. Заречный, Пензенская обл.). Достигнуто повышение качества поверхности на финишных операциях шлифования твердосплавных деталей, увеличение размерной стойкости алмазных шлифовальных кругов и снижение трудоемкости изготовления изделий. Годовой экономический эффект составил 255 000 руб.
Материалы диссертации использовались при выполнении госбюджетных научно-исследовательских работ по заказу Министерства образования и науки Российской Федерации по темам: Научные основы наноструктурирования для обеспечения качества поверхностного слоя ответственных деталей машиностроения и Разработка теоретических основ акустостимулированного изменения физико-механических свойств поверхностного слоя при абразивном диспергировании хрупких материалов.
Апробация работы. Основные положения работы докладывались на Международной научно-технической конференции Современные проблемы машиностроения (Томск, 2008); Всероссийском форуме Наука и инновации в технических университетах (Санкт-Петербург, 2008); Всероссийской научно-технической конференции Повышение эффективности механообработки на основе моделирования физических явлений (Рыбинск, 2009); научно-технической конференции Шлифабразив-2009 (Волгоград, 2009); Международной научно-технической конференции Ассоциации автомобиль-ных инженеров Автомобиле- и тракторостроение в России: приоритеты развития и подготовка кадров (Москва, 2010); Международной научной заочной конференции Актуальные вопросы современной техники и технологии (Липецк, 2011); Международной научно-практической конференции Ресурсы модернизации страны: творческая личность и изобретательство (Пенза, 2011); молодежном научно-инновационном конкурсе У.М.Н.И.К. (Пенза, 2011); ежегодных научно-технических конференциях профессорско-преподавательского состава Пензенского государственного университета (Пенза, 2008Ц2011).
Публикации. Основные положения диссертации опубликованы в
18 печатных работах, из них 3 - в изданиях, рекомендованных ВАК РФ; получено два патента РФ на изобретения.
Структура и объем работы. Диссертационная работа состоит из введения, пяти глав, заключения, списка литературы из 104 наименований
и пяти приложений. Работа изложена на 145 страницах основного текста, включает 56 рисунков и 35 таблиц.
СОДЕРЖАНИЕ РАБОТЫ
Во введении обоснована актуальность темы, рассмотрены существующие направления повышения эффективности профильного врезного шлифования фасонными алмазными кругами и методы профилирования алмазных инструментов на металлических связках. Приведены цель, задачи, объект, предмет исследования, научная новизна и показана практическая значимость работы.
В первой главе выполнен обзор литературных источников и анализ технологических способов профилирования алмазных шлифовальных кругов на металлических связках. Показана перспективность совершенствования формообразования профильного инструмента и точности врезного шлифования за счет повышения размерной стойкости фасонных кругов.
Существенный вклад в развитие теории и практики врезного шлифования внесли отечественные ученые В. Н. Бакуль, А. К. Байкалов, Д. Г. Евсеев, А. В. Королев, С. Н. Корчак, Е. Н. Маслов, А. Н. Резников, Л. Н. Филимонов, Л. В. Худобин и др. Исследованию профильного шлифования посвящены работы А. И. Исаева, В. А. Сипайлова, А. Н. Филина, А. В. Якимова, П. И. Ящерицына и зарубежных ученых.
На решение задачи повышения точности механической обработки и формообразования на основе стабилизации динамического состояния технологического оборудования и управления станочными системами направлены исследования ученых Саратовского государственного технического университета Б. М. Бржозовского,а И. Н. Янкина, аВ. В. Мартынова и др.
Выполненный обзор литературных источников и опыта промышленности показал, что перспективным направлением для достижения высокой точности и эффективности при изготовлении деталей сложной формы из труднообрабатываемых материалов является применение профильных алмазных шлифовальных инструментов.
Для профилирования алмазных инструментов на металлических связках наиболее эффективно использовать электроэрозионный метод формообразования рабочей поверхности. Исследования этого метода наиболее полно освещены в работах П. И. Ящерицына, В. Д. Дорофееева, В. В. Коломийца, Ю. А. Пахалина, Н. К. Фотеева и др.
Вместе с тем остаются нерешенными многие вопросы, связанные с обеспечением точности профилирования шлифовальных инструментов и повышением их размерной стойкости.
Показана актуальность дальнейших исследований для совершенствования врезного алмазного шлифования спрофилированными алмазными кругами. Сформулированы задачи исследования.
Во второй главе приведены результаты теоретических исследований по повышению стойкости профильных алмазных шлифовальных кругов на металлических связках и обеспечению точности шлифуемых деталей.
Для получения профильных шлифовальных кругов предложен новый способ, позволяющий существенно повысить их размерную стойкость. Сущность способа заключается в том, что профиль фасонного круга формируют за две технологические операции. На первой операции производят предварительное профилирование круга электроэрозионным методом. При этом конфигурация профиля рабочей поверхности шлифовального инструмента будет отличаться от требуемой на величину припуска ?R для поверхностного пластического деформирования алмазоносного слоя накатным роликом (рисунок 1).
Рисунок 1 - Схема профилирования алмазного круга
накатным роликом с усилием P:
1 - шлифовальный круг; 2 - накатной ролик
аНа второй операции выполняют окончательное формирование профиля круга путем деформирования алмазоносного слоя роликом. Процесс деформации сопровождается упрочнением связки и образованием наклепанного слоя с повышенной твердостью, а следовательно, и износостойкостью. Поэтому в процессе шлифования износ инструмента по фасонному профилю будет происходить более равномерно, что позволяет сохранить конфигурацию рабочей поверхности круга, близкую к исходной, и обеспечить стабильность точностных характеристик шлифуемых деталей в течение достаточно длительного времени.
Окончательное формообразование круга накатным роликом обеспечивает точностные параметры на различных участках сложного профиля круга до 5Е10 мкм вследствие выравнивания режущего контура из алмазных зерен поверхностью накатного ролика.
Чтобы избежать разрушения металлической связки круга, усилие накатывания P предложено ограничивать соотношением
аа (1)
где Dк - наибольший наружный диаметр профильного шлифовального
круга, мм; b - ширина контакта круга с накатным роликом, мм; q - (1,8Е2,2)?т - максимальное давление при накатывании (?т - предел текучести материала связки), МПа; k - коэффициент, учитывающий зону деформации связки круга для принятой схемы контакта с роликом; k = 0,1Е0,15 (меньшее значение принимается при b ? 10 мм); dp - наружный диаметр накатного ролика, мм; E - модуль упругости материала связки круга, МПа.
Для круга с наружным диаметромDк = 150 мм на металлической связке М2-01 с ?т = 63,7 МПа и E = 105 911 МПа при ширине контакта аb = 20 мм и диаметре накатного ролика dp = 90 мм допустимое усилие P составит 1325 Н.
Для повышения точности профилирования и уменьшения величины упругого возврата материала связки при накатывании роликом количество циклов деформирования должно быть таким, чтобы приращение пластической деформации после определенного числа циклов прекращалось. Установлено, что количество циклов накатывания следует ограничивать диапазоном от 10 до 15. Дальнейшее увеличение числа циклов может привести к перенаклепу материала связки и нарушению целостности алмазоносного слоя вследствие его локального разрушения, которое проявляется в отслаивании от корпуса круга.
Для повышения эффективности упрочнения связки профилирование накатным роликом рекомендуется производить с применением жировых смазок, которые позволяют уменьшить трение между контактирующими поверхностями ролика и рабочего слоя шлифовального круга. Введение в смазку поверхностно-активных веществ, например 0,2 %-го раствора олеиновой кислоты в вазелиновом масле, приводит к проявлению эффекта адсорбционного пластифицирования, который позволяет понизить прочность и облегчить деформацию материала связки.
На основе анализа рабочей поверхностиа шлифовального круга было произведено моделирование алмазоносного слоя, что позволило определить объем межзернового пространства шлифовального круга в виде
, (2)
где Fк - площадь контакта алмазного круга с заготовкой, мм2; lм - средневероятное расстояние между зернами в глубине слоя, мм; ? - массовое содержание зерен в алмазоносном слое, мг/мм3; N? - среднее количество зерен
в 1 мг алмазоносного слоя, шт/мг; dср - эквивалентный (усредненный) диаметр алмазных зерен, мм; ep p - разновысотность выступания зерен из связки после накатывания алмазоносного слоя роликом, мм; eр о - величина максимального осаживания алмазных зерен в связку при деформировании роликом (при условии сохранения их целостности), мм.
Для обеспечения нормальных условий работы шлифовального круга необходимо, чтобы объем возникающей при резании стружки был меньше объема межзернового пространства на поверхности алмазоносного слоя круга. В противном случае будет происходить засаливание круга, его режущая способность будет снижаться, а на шлифуемой поверхности могут появиться прижоги.
Величину радиальной составляющей силы резания PY, для врезного шлифования, при которой будут обеспечиваться наиболее благоприятные условия резания, найдем по выражению
,а аа(3)
где HV - твердость обрабатываемого материала по Виккерсу; Dк - наибольший наружный диаметр профильного шлифовального круга, мм;t - глубина резания, мм.
С учетом величины PY, можно назначить технологические режимы, при которых процесс врезного шлифования будет наиболее производительным для обрабатываемого материала.
Однако вследствие неравномерного износа круга отдельные участки профиля могут подвергаться засаливанию. Поэтому для обеспечения постоянства режущих свойств шлифовального круга следует удалять возникающий при резании шлам из межзернового пространства. Для очистки рабочей поверхности круга можно обеспечить подвод электрической энергии в зону контакта круга с обрабатываемой деталью до появления электрических разрядов, т.е. создать условия для электроэрозионного шлифования. В процессе электрической эрозии будет происходить непрерывное вскрытие зерен в алмазоносном слое, стабилизация режущих свойств алмазного круга и уменьшение локального нагрева зоны резания, который может приводить к возникновению напряжений в металле и появлению прижогов, сколов, макро- и микротрещин в поверхностном слое. При этом на обрабатываемой поверхности детали формируется дефектный слой в виде лунок оплавленного металла.
Поэтому для сохранения высоких режущих свойств алмазного круга и повышения качества обрабатываемой поверхности предлагается производить периодическое электроэрозионное воздействие на рабочую поверхность инструмента вне зоны шлифования.
На рисунке 2 приведена принципиальная схема нового способа шлифования.
а)
а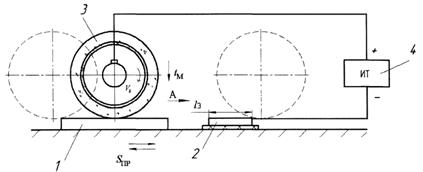
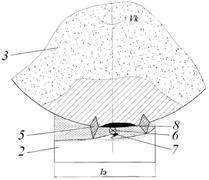
б)
Рисунок 2 - Схема алмазного шлифования (а) с электроэрозионным воздействием
на рабочую поверхность (б) круга вне зоны обработки:
1 - обрабатываемая деталь; 2 - корректирующий электрод-инструмент;
3 - алмазный шлифовальный круг; 4 - источник постоянного тока; 5 - алмазные зерна;
6 - микродуговой разряд; 7 - стружки обрабатываемого материала;
8 - эрозионная лунка
Способ шлифования осуществляют следующим образом. Обрабатываемую деталь 1 устанавливают на стол станка, на котором вне зоны обработки закрепляют изолированный от стола корректирующий электрод-инструмент 2. Алмазный шлифовальный круг 3 на токопроводящей связкеа и электрод-инструмент 2 подключают к соответствующим полюсам источника постоянного тока 4 и устанавливают допустимую условиями выполнения операции величину напряжения U. Шлифовальному кругу 3 задают вращение, а столу станка с обрабатываемой деталью 1 и электродом-инструмен-том 2 сообщают возвратно-поступательное перемещение Sпр. Подачу на глубину шлифования tм круга 3 осуществляют за каждый двойной ход стола, т.е. обработку производят по схеме врезного шлифования.
Величина удаляемого при правке круга материала связки зависит от времени электроэрозионного воздействия на поверхность алмазного круга, а следовательно, от длины lэ шлифуемого участка электрода-инструмента 2 при прочих равных условиях.
Для уменьшения износа алмазоносного слоя круга при правке электроэрозионным методом максимальную величину напряжения U (В) источника постоянного тока ограничивают соотношением
,аа (4)
где kc - коэффициент, характеризующий величину напряжения электрических импульсов и интенсивность разрушения материала связки электрической эрозией для вскрытия алмазных зерен и восстановления режущих свойств круга при шлифовании (для связки М2-01, обладающей минимальной эрозионной стойкостью, принимают kc = 1, а для других связок эти значения установлены экспериментально и приведены в таблице 1); Dк - наибольший наружный диаметр фасонного шлифовального круга, мм;
? = (4Е7) % Zmax - толщина алмазоносного слоя, удаляемого с поверхности круга при однократном воздействии за один двойной ход стола, мкм (Zmaxа - наибольший размер алмазных зерен, зависящих от зернистости круга, мкм);
lэ - длина правящего электрода-инструмента; Nз - количество алмазных зерен, приходящихся на 1 мм2 рабочей поверхности круга; ? - коэффициент, определяющий количество зерен, участвующих в резании, составляющий 10Е12 % от общего числа зерен, находящихся на поверхности круга; ? = 0,85Е0,95 - коэффициент, учитывающий вероятность возникновения электрических разрядов при стружечном замыкании; K - концентрация алмазов в алмазоносном слое круга, %.
Таблица 1 - Значения коэффициента kc для различных металлических связок
алмазных кругов
М2-09 |
||||||
Значения kc |
В таблице 2 приведены рекомендуемые значения напряжения U для алмазного шлифования кругами разной зернистости на металлической связке М2-01.
Таблица 2 - Рекомендуемые значения напряжения для электроэрозионной правки круга
Зернистость алмазов |
Напряжение U, В, при концентрации алмазов в круге, % |
||
50 |
100 |
200 |
|
63/50 |
10 |
7 |
6 |
100/80 |
13 |
10 |
7 |
160/125 |
14 |
12 |
10 |
250/200 |
18 |
14 |
12 |
В третьей главе приведены результаты экспериментальных исследований влияния технологических факторов на эффективность профильного врезного шлифования различных труднообрабатываемых материалов алмазными кругами, упрочненными накатыванием.
Для выделения факторов, оказывающих наибольшее влияние на стойкость кругов, был поставлен отсеивающий эксперимент методом случайного баланса.
Основными факторами,а влияющими на расход алмазов при шлифовании, являются X1 - зернистость шлифовального материала, мкм; X2 - подача на глубину шлифования, мм/дв. ход; X3 - скорость детали, м/мин; X4 - концентрация алмазов в алмазоносном слое инструмента, %;а X5 - материал, обрабатываемый шлифованием; X6 - скорость круга, м/с; X7 - марка металлической связки.
В качестве параметра оптимизации, характеризующего стойкость круга, был принят удельный расход алмазов q, мг/г.
Общий вид экспериментального стенда на базе плоскошлифовального станка приведен на рисунке 3.
Рисунок 3 - Стенд для исследования шлифования
с электроэрозионной правкой круга вне зоны обработки:
1 - обрабатываемая деталь; 2 - корректирующий электрод-инструмент;
3 - алмазный шлифовальный круг; 4 - источник постоянного тока
Анализ результатов отсеивающего эксперимента показал, что анаибольшее влияние на износ круга оказывают зернистость Z, подача S и скорость детали V.
Для оценки влияния выявленных факторов на износ алмазных шлифовальных кругов, на производительность обработки и шероховатость поверхности после шлифования были выполнены экспериментальные исследования на образцах из твердого сплава Т14К8, феррита марки 10 000 НМ и конструкционной стали, упрочненной борированием, путем врезного шлифования на станке мод. 3Г71.
При проведении исследований был реализован полный факторный эксперимент типа 23 по методике ротатабельного композиционного униформ-планирования.
Обработка результатов опыта осуществлялась с применением ЭВМ по специальной разработанной программе.
После проверки значимости коэффициентов и перехода от кодовых обозначений факторов к натуральным были получены математические модели, характеризующие влияние основных технологических факторов на удельный расход алмазов q, мг/г, при шлифовании образцов из трех различных материалов:
для твердого сплава Т14К8
qтс = 1,14 + 13,5ХS - 0,03ХV - 0,016ХZ - 0,8ХSХV а+ 0,007ХV 2 + 0,00005ХZ 2; а(5)
для феррита 10 000 НМ
qф = 0,4 + 1,3S + 0,0145V - 0,0013Z;(6)
для конструкционной стали, упрочненной борированием,
qбс = 1,9 - 3ХS + 0,002ХV - 0,01ХZ + 95ХS^2 + 0,004ХV 2 + 0,00004ХZ 2. а(7)
Математические модели, описывающие влияние этих же факторов на шероховатость шлифованной поверхности по параметру Ra, мкм, получаемую при шлифовании:
для твердого сплава Т14К8
Raтс = 1,1 + 4,8ХS - 0,08ХV - 0,016ХZ + 0,001ХVХZ а+ 0,00005ХZ 2; а(8)
для феррита 10 000 НМ
Raф = 1,7 - 2,3ХS - 0,085ХV - 0,02145ХZ + 37,5ХS 2 + 0,00525ХV 2 + 0,00014ХZ 2; а(9)
для конструкционной стали, упрочненной борированием,
Raбс = 0,9 - 1,7ХS + 0,03ХV - 0,014ХZ + 30ХS 2 + 0,0001ХZ 2. а(10)
Математические модели, описывающие влияние технологических факторов на производительность шлифования Q, мм3/мин:
для твердого сплава Т14К8
Qтс= Ц1558 + 12901S + 105V + 14,2Z - 41,1SZ + 0,5VZ Ц
- 44330S 2 - 4,8V 2 - 0,06Z 2;аа (11)
для феррита 10 000 НМ
Qф = 911 + 22,75S - 99V - 2Z а+ 24,3SZ + 0,54VZ + 3,9V 2; (12)
для конструкционной стали, упрочненной борированием,
Qбс = Ц286 + 577,15S + 57,33V + 5,57Z - 2,14V 2 - 0,02Z 2.а (13)
Проверка моделейа (5)Ц(13) по критерию Фишера показала, что они являются адекватными с доверительной вероятностью 95 %.
Установлено, что для обеспечения требуемых значений шероховатости при низких значениях расхода алмазов на операциях чистового шлифования профильными алмазными кругами рекомендуется выбирать величину подачи на глубину tм ? 0,03 мм/дв. ход при скорости поступательного перемещения детали до 9 м/мин и зернистости шлифовального материала кругов 80/63 или 63/50.
В четвертой главе приведены результаты исследования по технологическому обеспечению качества поверхностного слоя ферритовых деталей при алмазном врезном шлифовании профильными кругами.
Шлифование характеризуется высокой тепловой напряженностью, поэтому в поверхностных слоях ферритовых деталей велика вероятность появления сетки микротрещин, которая приводит к снижению эксплуатационных свойств.
Теоретически рассмотрено взаимодействие наночастиц, введенных в состав технологической жидкости, в условиях возникающего при вращении шлифовального круга ультразвукового капиллярного эффекта и получено выражение для определения силы их взаимодействия, усредненной по периоду ультразвуковой волны T, дисперсии u размеров наночастиц и углу ?, образованному направлением скоростей осциллирующих сферических частиц и линией, соединяющей их центры:
аа (14)
где а - усредненная сила взаимодействия двух наночастиц, Н;
?с - плотность технологической жидкости, г/см3; R0 - средний радиус наночастицы, нм; Lн - расстояние между наночастицами, нм; ? - угол, образованный направлением скоростей осциллирующих сферических частиц с линией, соединяющей их центры; us = u0cХcos?t (u0c - амплитуда скорости колеблющихся частиц);аu - дисперсия размеров наночастиц; umax,а umin - максимальная и минимальная дисперсии радиуса наночастиц, u0 = (umax+ umin)/2.
Обоснована возможность управления качеством поверхности путем изменения локального значения модуля Юнга поверхностного слоя материала в условиях кавитационного режима, обусловленного ультразвуковым капиллярным эффектом при шлифовании ферритов с охлаждением зоны резания технологической жидкостью с ультрадисперсными частицами металла (наночастицами) вследствие заращивания микротрещин кластерами наночастиц металла.
Предложена математическая модель поверхностного слоя ферритовых деталей с сеткой микротрещин, которая позволила получить выражение для среднего значения модуля Юнга аповерхностного слоя обрабатываемой детали в виде
аа
а (15)
где E1 - модуль Юнга материала обрабатываемой детали с учетом пористости; E2 - модуль Юнга материала наночастиц; a - среднее расстояние между микротрещинами на поверхности детали, мкм; l - длина поверхности шлифуемой детали, мм;
Проведенные эксперименты показали уменьшение числа микротрещин на поверхности деталей из ферритов после шлифования с применением ультрадисперсных частиц металла в составе технологической жидкости. Изучение поверхности проводилось на металлографическом микроскопе МЕТАМ ЛВ-3 с 500-кратным увеличением, а топографии участка поверхности (размер участка 2?2 мкм) были получены с использованием атомно-силового микроскопа SFM. Фотографии представлены на рисунках 4, 5 и 6.
а
а)а б)
Рисунок 4 - Фотография (а) аисходного микрорельефа и топография (б)
фрагмента поверхности образца из феррита до шлифования
а) аа б)
Рисунок 5 - Фотография (а) аисходного микрорельефа и топография (б)
фрагмента поверхности образца из феррита после шлифованияа
с применением мыльно-содового водного раствора
а аа
аа а)а б)
Рисунок 6 - Фотография (а) исходного микрорельефа поверхности
и топография (б) фрагмента поверхности образца из феррита после шлифования
с охлаждением зоны резания технологической жидкостью с наночастицами
Анализ выполненных исследований поверхностей образцов показывает, что число микротрещин на поверхности ферритовых образцов после шлифования с использованием наночастиц меди в составе технологической жидкости снижается. Установлено также, что применение ультрадисперсных частиц при шлифовании деталей из ферритов обеспечило снижение мощности шлифования на 15 % за счет уменьшения коэффициента трения и позволило повысить эксплуатационные характеристики изделий, что подтверждено увеличением напряжения во вторичной обмотке магнитного контура до 30 % при использовании токов высокой частоты, а это косвенно подтверждает уменьшение магнитных потерь в месте контакта вследствие заращивания микротрещин на поверхности ферритовых сердечников.
В пятой главе приведены рекомендации по определению припуска под накатывание, необходимого для пластической деформации, которая обеспечит требуемую степень упрочнения металлический связки круга.
Приведен пример расчета профиля радиального фасонного резца для восстановления исходной конфигурации рабочей поверхности электрода-инструмента после износа в процессе эксплуатации.
Описана методика расчета величины напряжения U при шлифовании с периодической правкой круга воздействием электрических разрядов вне зоны обработки для эффективного удаления продуктов шлифования из межзернового пространства круга при минимальном воздействии на связку. Установлено, что для обеспечения наибольшей производительности шлифования с периодической электроэрозионной правкой круга при снижении расхода алмазов следует назначать величины напряжения U в диапазоне от 6
до 18 В с ограничением времени электроэрозионного воздействия от 0,2
до 2 с за один двойной ход в зависимости от зернистости алмазного круга и материала обрабатываемой заготовки.
Разработана методика определения режимов профилирования алмазного круга и режимов шлифования, представленная в виде алгоритма, позволяющего назначать эффективные значения параметров технологических факторов и повышать эффективность нового способа шлифования. Внедрение этой методики на промышленных предприятиях при изготовлении твердосплавных режущих инструментов с фасонным профилем рабочей поверхности позволило снизить трудоемкость выполнения технологической операции, повысить качество поверхности и стойкость шлифовального инструмента.
Приведен расчет экономической эффективности инвестиционного проекта при внедрении предлагаемой технологии врезного шлифования в производство. Годовой экономический эффект на двух предприятиях составил 255 000 руб.
ОСНОВНЫЕ РЕЗУЛЬТАТЫ И ВЫВОДЫ
- Выполнен аналитический обзор литературных источников и опыта промышленности, который показал актуальность совершенствования врезного шлифования фасонными кругами и повышения размерной стойкости профильных алмазных шлифовальных кругов на металлических связках.
- Предложены новые способы профильного шлифования с периодическим восстановлением режущих свойств круга электроэрозионным воздействием на рабочую поверхность алмазоносного слоя в процессе обработки и профилирования фасонных кругов пластическим деформированием, которое повышает стойкость круга в среднем на 25 %.
- Теоретически определен объем межзернового пространства рабочей поверхности круга, спрофилированного пластическим деформированием, и определена величина напряжения электроэрозионного воздействия, при котором достигается удаление продуктов шлифования из межзернового пространства без интенсивного разрушающего воздействия электрических разрядов на связку круга. Установлено, что для кругов с концентрацией алмазов от 50 до 200 % и зернистости шлифовального материала от 63/50 до 250/200 мкм допустимая величина напряжения источника постоянного тока составляет от 6 до 18 В, при которой предотвращается засаливание кругов на металлических связках между правками.
- Аналитически определена сила, достаточная для деформирования алмазоносного слоя накатным роликом при окончательном профилировании фасонного круга. Стабильно достигается заданная точность размеров профиля, а диапазон рассеяния размеров на различных участках фасонного круга не превышает 10 мкм. Рациональное число циклов нагружения при накатывании роликом составляет от 10 до 15.
- Установлены эмпирические полиномиальные модели влияния технологических факторов на удельный расход алмазов; производительность обработки и шероховатость поверхности при профильном врезном шлифовании алмазными кругами, упрочненными накатыванием, для различных труднообрабатываемых материалов. На операциях чистового шлифования профильными алмазными кругами, упрочненными пластическим деформированием, рекомендуется выбирать значения подачи на глубину шлифования до 0,03 мм/дв. ход и скорости детали до 9 м/мин при зернистости кругов 80/63 или 63/50.
- Теоретически обоснована возможность управления локальным модулем Юнга поверхностного слоя ферритовых пластин путем ультразвуковой активации кавитационного процесса в технологической жидкости с ультрадисперсными частицами (наночастицами) металла при врезном алмазном шлифовании. Экспериментально подтверждено заращивание сетки микротрещин на поверхности ферритовых пластин кластерами наночастиц меди, что приводит к изменению локального модуля Юнга (уменьшению хрупкости) и позволяет повысить эффективность шлифования материалов, склонных к трещинообразованию.
- Разработанная технология профильного алмазного шлифования фасонными кругами с повышенной размерной стойкостью после упрочнения материала связки поверхностным пластическим деформированием внедрена при изготовлении твердосплавных режущих инструментов с фасонным профилем рабочей поверхности на двух промышленных предприятиях с годовым экономическим эффектом 255 000 руб.
ОСНОВНЫЕ ПУБЛИКАЦИИ ПО ТЕМЕ ДИССЕРТАЦИИ
Публикации в изданиях, рекомендованных ВАК РФ
- Соколов, А. В. Новый способ профилирования алмазных кругов на металлических связках для шлифования деталей из труднообрабатываемых материалов / А. В. Соколов, В. З. Зверовщиков // Вестник СГТУ. - 2011. -
№ 1 (52). - С. 61Ц67.
- Соколов, А. В. Повышение качественных характеристик поверхности при профильном алмазном шлифовании / А. В. Соколов, В. З. Зверовщиков // Известия высших учебных заведений. Поволжский регион. Технические науки. - 2011. - № 3 (19). - С. 167Ц175.
- Соколов, А. В. Кавитационный механизм управления качеством поверхностного слоя деталей при использовании смазывающе-охлаждающих жидкостей с нанодобавками в условиях звукокапиллярного эффекта /
А. В. Соколов, В. Д. Кревчик, Н. П. Симонов // Известия высших учебных заведений. Поволжский регион. Технические науки. - 2011. - № 4 (20). -
С. 180Ц191.
Публикации в других изданиях
- Соколов, А. В. Обеспечение точности шлифования изделий сложной конфигурации / А. В. Соколов, В. О. Соколов // Процессы абразивной обработки, абразивные инструменты и материалы. Шлифабразив-2005 : сб. ст. Междунар. науч.-техн.конф. ЦВолжский, 2005. - С. 114Ц117.
- Соколов, А. В. Повышение размерной стойкости профильных алмазных кругов / А. В. Соколов, В. О. Соколов // Процессы абразивной обработки, абразивные инструменты и материалы. Шлифабразив-2006 : сб. ст. Междунар. науч.-техн. конф. ЦВолжский, 2006. - С. 6Ц9.
- Соколов, А. В. Управление точностью профильного шлифования изделий сложной формы / А. В. Соколов, В. О. Соколов // Вестник Курганского государственного университета. Серия: Технические науки. - 2006. Ц
N 1. - Вып. 2, ч. 1. - С. 115, 116.
- Соколов, А. В. О повышении размерной стойкости профильных шлифовальных кругов / А. В. Соколов, Н. А. Миронычев // Материаловедение и технология конструкционных материалов - важнейшие составляющие компетенции современного инженера. Проблемы качества технологической подготовки. - Волжский, 2007. - С. 131Ц134.
- Соколов, А. В. Технология профилирования шлифовальных кругов на металлических связках / А. В. Соколов // Наука и инновации в технических университетах : материалы Всерос. форума студентов, аспирантов и молодых ученых. - Санкт-Петербург : Изд-во политехнического университета, 2008. - С. 114, 115.
- Соколов, А. В. Повышение износостойкости алмазных шлифовальных кругов на металлических связках / А. В. Соколов,а В. З. Зверовщиков // Современные проблемы машиностроения : тр. четвертой Междунар. науч.-техн. конф. - Томск : Изд-во ТПУ, 2008. - С. 563Ц565.
- Соколов, А. В. Стабилизация геометрии рабочей поверхности алмазных кругов сложного профиля / А. В. Соколов, В. О. Соколов // Повышение эффективности механообработки на основе моделирования физических явлений : материалы Всерос. науч.-техн. конф. - Рыбинск : РГАТА, 2009. - Ч. 1. - С. 192Ц195.
- Соколов, А. В. Профилирование алмазных шлифовальных кругов комбинированным методом / А. В. Соколов, В. О. Соколов // Процессы абразивной обработки, абразивные инструменты и материалы. Шлифабразив-2009 : сб ст. Междунар. науч.-техн. конф. - Волжский, 2010. - С. 121Ц123.
- Соколов, А. В. Получение профильных алмазных шлифовальных кругов на металлических связках с повышенной размерной стойкостью /
А. В. Соколов // Автомобиле- и тракторостроение в России: приоритеты развития и подготовка кадров : материалы Междунар. науч.-техн. конф. Ассоциации автомобильных инженеров. - М. : МАМИ, 2010. - С. 218Ц222.
- Соколов, А. В. Повышение эффективности алмазного шлифования ферритовых деталей путем ультразвукового воздействия / А. В. Соколов,
В. Д. Кревчик, С. Б. Меньшова // Актуальные вопросы современной техники и технологии : сб. докл. III Междунар. науч. заоч. конф. - Липецк : Издательский центр Гравис, 2011. - Ч. 1. - С. 103Ц105.
- Соколов, А. В. Моделирование шлифования для повышения стойкости профильных алмазных шлифовальных кругов / А. В. Соколов,
В. З. Зверовщиков // Системы проектирования, моделирования, подготовки производства и управление проектами CAD/CAM/CAE/PDM : сб. ст. V Междунар. науч.-практ. конф. - Пенза : Приволжский дом знаний, 2011. -
С. 32Ц34.
- Соколов, А. В. Разработка новых технических решений для шлифования труднообрабатываемых материалов алмазными кругами / А. В. Соколов, В. З. Зверовщиков // Ресурсы модернизации страны: творческая личность и изобретательство : сб. ст. Междунар. науч.-практ. конф. - Пенза : Приволжский дом знаний, 2011. - С. 46-49.
- Соколов, А. В. Инновационная технология шлифования фасонных поверхностей деталей алмазными кругами / А. В. Соколов // Молодежьа иа наука:а модернизацияа иа инновационное развитие страны : материалы
Междунар. науч.-практ. конф. : в 3 ч. - Пенза : Изд-во ПГУ, 2011. - аЧ. 3. -
С. 91, 92.
Патенты РФ
- Пат. 2364497 Российская Федерация, МПК B24D18/00. Способ изготовления профильных шлифовальных кругов / Соколов А. В. и др.; заявитель и патентообладатель Пенз. гос. ун-т. - № 2008116945/02; заявл. 28.04.08; опубл. 20.08.09, Бюл. № 23. - 8 с.
Пат. 2432239 Российская Федерация, МПК B23H5/04 B24B53/00. Способ шлифования сложнопрофильных поверхностей деталей / Соко-
лов В. О. и др.; заявитель и патентообладатель Пенз. гос. ун-т. - № 2010105449/02; заявл. 15.02.10; опубл. 27.10.11, Бюл. № 30. - 9 с.
Научное издание
СОКОЛОВ Алексей Владимирович
Технологическое обеспечение точности
профильного шлифования алмазными кругами,
упрочненными пластическим деформированием
Специальности: 05.02.08 - Технология машиностроения;
05.02.07а - Технология и оборудование механической
и физико-технической обработки
Редактор Т. В. Веденеева
Технический редактор М. Б. Жучкова
Компьютерная верстка М. Б. Жучковой
Распоряжение № 14/2012 от 06.04.2012 г.
Подписано в печать 05.04.12.
Формат 60?841/16. Усл. печ. л. 1,16.
Тираж 100. Заказ № 002036.
Издательство ПГУ.
440026, Пенза, Красная, 40.
Тел./факс: (8412) 56-47-33; e-mail:pnzgu.ru
Авторефераты по темам >>
Разные специальности - [часть 1] [часть 2]