
Интенсификация и стабилизация электроэрозионного профилирования алмазных шлифовальных кругов путем автоматизированного управления режимами обработки
Автореферат кандидатской диссертации
На правах рукописи
НИКИТКИН Александр Сергеевич
ИНТЕНСИФИКАЦИЯ И СТАБИЛИЗАЦИЯ
ЭЛЕКТРОЭРОЗИОННОГО ПРОФИЛИРОВАНИЯ АЛМАЗНЫХ
ШЛИФОВАЛЬНЫХ КРУГОВ
ПУТЕМ АВТОМАТИЗИРОВАННОГО УПРАВЛЕНИЯ
РЕЖИМАМИ ОБРАБОТКИ
Специальности:
05.13.06 - Автоматизация и управление технологическими
процессами и производствами (промышленность);
05.02.07 - Технология и оборудование механической
и физико-технической обработки
А в т о р е ф е р а т
диссертации на соискание ученой степени
кандидата технических наук
ПЕНЗА-2012
Работа выполнена в ФГБОУ ВПО Пензенский государственный университет.
Научные руководители: |
доктор технических наук, доцент СЕМЕНОВ Анатолий Дмитриевич; доктор технических наук, профессор
|
Официальные оппоненты: |
ДЬЯЧКОВ Юрий Алексеевич, доктор технических наук, профессор, ФГБОУ ВПО Пензенский государственный университет, заведующий кафедрой Транспортные машины. ЧЕРНИКОВ Владислав Сергеевич, кандидат технических наук, ООО Научно-производственное предприятие Технопроект, главный контролер качества. |
Ведущая организация - |
ФГУП ФНПЦ ПО ?Старт? им. М. В. Проценко. |
Защита состоится 5 июля 2012 г., в 12 часов, на заседании диссертационного совета Д 212.186.03 в ФГБОУ ВПО Пензенский государственный университет по адресу: 440026, Пенза, ул. Красная, 40.
С диссертацией можно ознакомиться в библиотеке ФГБОУ ВПО Пензенский государственный университет.
Автореферат разослан л____ _____________ 2012 г.
Ученый секретарь
диссертационного совета аВоячек Игорь Иванович
ОБЩАЯ ХАРАКТЕРИСТИКА РАБОТЫ
Актуальность темы. При обработке изделий сложной конфигурации, изготовленных из таких материалов, как керамика, ситаллы, твердые сплавы и т.д., широко применяется профильное алмазное шлифование высокостойкими кругами на металлических связках.
Наиболее эффективным методом получения фасонных алмазных шлифовальных кругов на металлических связках является глубинный электроэрозионный метод.
На эффективность процесса электроэрозионного профилирования алмазного инструмента оказывает влияние большое количество факторов, поэтому для достижения максимальной производительности профилирования, обеспечения заданной точности и стабильности необходимо управлять параметрами, от которых в большей степени зависит качество рассматриваемого процесса. Наряду с этим существующие системы управления электроэрозионной обработкой не обеспечивают заданных показателей качества процесса глубинного электроэрозионного профилирования, так как не учитывается ряд важных факторов, например наличие в обрабатываемой детали нетокопроводящих включений (алмазных зерен), оказывающих существенное влияние на данный процесс.
Таким образом, задача повышения эффективности операций профильного алмазного шлифования путем управления качеством формообразования алмазно-абразивного инструмента является актуальной.
Цель работы - повышение стабильности и производительности процесса электроэрозионного профилирования алмазных шлифовальных кругов путем автоматизированного экстремального управления режимами обработки.
Для достижения поставленной в работе цели необходимо решить следующие задачи:
1) построить математические модели процесса электроэрозионного профилирования и провести их верификацию по результатам экспериментов;
2) установить закономерности процесса профилирования, оказывающие влияние на его стабильность и производительность, а также позволяющие осуществлять автоматизированное управление его параметрами;
3) обосновать выбор алгоритмов управления процессом электроэрозионного профилирования и разработать методики расчета технологических режимов этого процесса, позволяющие повысить его стабильность и производительность;
4) провести экспериментальные исследования влияния предлагаемых режимов электроэрозионного профилирования алмазно-абранзивного инструмента и алгоритмов управления на эффективность пронфильного алмазного шлифования;
5) на основе проведенных теоретических и экспериментальных исследований модернизировать технологическое оборудование и разработать автоматизированную систему управления.
Объект исследования - процесс глубинного электроэрозионного профилирования алмазных шлифовальных кругов.
Предмет исследования - моделирование, алгоритмизация и автоматизация управления процессом электроэрозионного профилирования алмазных шлифовальных кругов с целью его интенсификации и стабилизации.
Методы исследований. Исследования проводились на базе современной теории управления и автоматизации технологических процессов, технологии машиностроения, теории шлифования и электроэрозионной обработки, теории вероятностей и математической статистики, моделирования, численных и экспериментальных методов.
Достоверность полученных результатов и выводов подтвержндена математическими доказательствами, цифровым моделированием, сходимостью теоретических и экспериментальных исследований, а также практической реализацией разработанных систем управления.
Научная новизна:
по специальности 05.13.06:
1) установлена экстремальная зависимость средней мощности от величины межэлектродного промежутка, позволяющая обоснованно выбрать алгоритм управления подачей профилирующего электрода, для достижения максимальной величины средней мощности, что обеспечивает интенсификацию и стабилизацию процесса электроэрозионного профилирования;
2) разработаны математические модели процесса электроэрозионного профилирования, учитывающие его электродинамические и технологические особенности, используемые для алгоритмизации и автоматизации управления этим процессом;
по специальности 05.02.07:
1) установлено квазипериодическое расположение алмазных зерен на рабочей поверхности алмазного круга и предложен алгоритм фазовой синхронизации частоты вращения круга с частотой генератора технологических импульсов, позволивший стабилизировать процесс электроэрозионного профилирования;
2) разработана методика расчета параметров технологических импульсов на основе вычисления среднего расстояния между алмазными зернами по характеристикам шлифовальных кругов и даны рекомендации по выбору режимов процесса профилирования, обеспечивающие повышение режущих свойств у алмазно-абразивного инструмента.
Практическая ценность.
- Предложенный алгоритм экстремального управления подачей профилирующего электрода из условия достижения максимальной величины средней мощности, выделяемой в межэлектродном промежутке, позволяет повысить производительность процесса электроэрозионного профилирования.
- Предложенный алгоритм фазовой синхронизации частоты генератора технологических импульсов с частотой вращения алмазного круга стабилизирует технологические параметры процесса электроэрозионной обработки алмазных кругов.
- Разработанная модель процесса электроэрозионного профилирования алмазных шлифовальных кругов позволяет осуществить выбор режимов профилирования, обеспечивающих повышение точности и производительности процесса обработки.
- Разработанная система автоматизированного управления установкой для глубинного электроэрозионного профилирования алмазных шлифовальных кругов позволяет стабилизировать и интенсифицировать процесс глубинного электроэрозионного профилирования.
Реализация и внедрение результатов работы. Результаты
работы внедрены в производство на ФГУП ФНПЦ ПО ?Старт?
им. М. В. Проценко, что позволило повысить производительность изготовления фасонных твердосплавных инструментов в 1,2-1,5 раза, а фасонных деталей основного производства из керамики и магнитных сплавов - в 1,3-1,8 раза за счет достижения высоких режущих свойств алмазного инструмента после его профилирования и повышения точности и стойкости алмазного круга.
Работа выполнена в рамках аналитической ведомственной целевой программы Министерства образования и науки РФ Развитие научного потенциала высшей школы 2009-2012 г. № 01200952070 в соответствии с планами госбюджетной научно-исслендовательской работы Пензенского государственного университета и поддержана грантом У.М.Н.И.К. (в 2010 г.) Фонда содействия развитию малых форм предприятий в научно-технической сфере.
На защиту выносятся:
по специальности 05.13.06:
1) экстремальная зависимость средней мощности от величины межэлектродного промежутка, которая обеспечивает увеличение скорости профилирования, а также интенсификацию и стабилизацию процесса путем экстремального управления;
2) математические модели процесса электроэрозионного профилирования, учитывающие его электродинамические и технологические особенности, используемые для алгоритмизации и автоматизации управления этим процессом;
по специальности 05.02.07:
1) квазипериодическое расположение алмазных зерен на рабочей поверхности алмазного круга, позволяющее обоснованно подойти к выбору параметров разрядных импульсов, синхронизируя их частоту и длительность с частотой вращения алмазного круга;
2) методика расчета параметров технологических импульсов на основе вычисления среднего расстояния между алмазными зернами по характеристикам шлифовальных кругов и рекомендации по выбору режимов процесса профилирования, обеспечивающие повышение режущих свойств у алмазно-абразивного инструмента.
Апробация работы. Основные положения и результаты диссертационной работы докладывались и обсуждались на девяти конференциях различного уровня, в том числе на Всероссийском форуме Наука и инновации в технических университетах (Санкт-Петернбург, 2008, 2011), Международной научно-технической конференции Проблемы автоматизации и управления в технических системах (Пенза, 2009), Международном симпозиуме Надежность и качество (Пенза, 2009, 2010, 2012), Международной научно-практической конференции Формообразование и обеспечение качества техногенных систем (Пенза, 2009), XXIX Всероссийской научно-практической конференции молодых ученых и специалистов Датчики и системы (Пеннза, 2010), Молодежном научно-инновационном конкурсе У.М.Н.И.К. (Пенза, 2009), ежегодных научно-технинчеснких конференциях профессорско-преподавательского состава и студентов Пензенского государственного университета (2008Ц2011).
Публикации. По теме диссертации опубликовано 17 печатных работ, в том числе 3 статьи в журналах, входящих в перечень ВАК РФ (без соавторов 4 работы).
Структура и объем работы. Диссертационная работа состоит из введения, пяти глав, общих выводов, списка литературы, включающего 115 наименований, и приложения. Объем работы - 207 страниц машинописного текста, включая 97 рисунков и 19 таблиц.
СОДЕРЖАНИЕ РАБОТЫ
Во введении обоснована актуальность темы диссертационной работы, сформулированы цель и задачи исследования, научная новизна, практическая ценность, а также положения, выносимые на защиту.
В первой главе выполнен обзор научных публикаций, посвященных вопросам повышения эффективности электроэрозионного пронфилирования алмазных шлифовальных кругов, оказывающего существенное влияние на технологические показатели профильного шлифования деталей.
Наиболее эффективным методом получения фасонных высокостойких алмазных шлифовальных кругов на металлических связках является электроэрозионный метод.
Изучению различных вопросов профилирования и правки алмазно-абразивных инструментов электроэрозионным методом посвящены работы В. Д. Дорофеева, Ю. А. Пахалина, Н. К. Беззубенко, В. Н. Чанчина, В. В. Авакяна, В. Л. Касьяна, В. В. Коломиеца, А. Л. Лившица, В. О. Соколова, М. Ф. Семко, В. А. Дресвянникова, Н. К. Фотеева
Анализ различных технологических схем электроэрозионного профилирования алмазных шлифовальных кругов показал, что наибольшими потенциальными возможностями для подготовки фасонного алмазного инструмента обладает схема глубинного электроэрозионного профилирования. Вместе с этим вопрос управления ходом процесса профилирования с целью повышения точности и производительности обработки является практически не изученным.
Существующие системы управления электроэрозионной обработкой построены на основе моделей процесса, не учитывающих ряд важных факторов. В большинстве этих систем используются косвенные показатели, которые не в полной мере отражают состояние процесса обработки.
Наиболее информативным показателем процесса электроэрозионной обработки является величина средней мощности, выделяемой в межэлектродном промежутке. Однако до сих пор остаются неизученными возможности данного показателя при глубинном электроэрозионном профилировании, поскольку этот процесс отличается от традиционной электроэрозионной обработки наличием нетокопроводящих включений (алмазных зерен) в обрабатываемой детали, оказывающих механическое воздействие на профилирующий электрод и теряющих свои режущие свойства при воздействии на них электрических раз-рядов.
Вместе с этим нет определенности относительно выбора рациональных режимов глубинного профилирования, так как увеличение энергии разрядных импульсов с целью повышения производительности обработки приводит не только к снижению точности профилирования, но и к графитизации алмазных зерен, что оказывает существенное влияние на размерную стойкость алмазно-абразивного инструмента.
В связи с этим необходимо обосновать выбор алгоритмов, позволяющих управлять качеством формообразования рабочей поверхности алмазных шлифовальных кругов и создать систему автоматизированного управления процессом глубинного электроэрозионного профилирования, а также дать рекомендации по выбору рациональных режимов обработки.
Вторая глава посвящена математическому описанию процесса электроэрозионного профилирования алмазных шлифовальных кругов, разработке математических моделей этого процесса и обоснованному выбору методов автоматизированного управления, обеспечивающих интенсификацию и стабилизацию данного процесса.
Математическое описание процесса электроэрозионного профилирования связано с построением ряда математических моделей, таких как модель межэлектродного промежутка, модель электроприводов подач, а также модель рабочей поверхности алмазных шлифовальных кругов.
С целью обоснованного выбора типа и параметров схемы замещения межэлектродного промежутка экспериментально были получены осциллограммы токов и напряжений технологических импульсов при различных величинах этого промежутка.
Поскольку ток в межэлектродном промежутке имеет ярко выраженную колебательную составляющую, то схема замещения включает в себя колебательный RLC-контур. Функциональная и параметрическая идентификация параметров этого контура по экспериментально снятым импульсам разрядного тока и напряжения позволила остановиться на Т-образной схеме замещения, в которой колебательный контур подключен на активно-индуктивную нагрузку.
По результатам идентификации средствами Matlab были получены значения параметров схемы замещения. Установлено, что сопротивление межэлектродного промежутка R2 (Ом) нелинейно зависит от его величины, плавно изменяясь от 0 (короткое замыкание) до ? (холостой ход).
С достаточной для практики точностью эту зависимость можно аппроксимировать выражением
, (1)
где a и b- коэффициенты, зависящие от амплитуды импульсов напряжения генератора технологических импульсов; S - величина межэлектродного промежутка, мкм.
С учетом общепринятых допущений были разработаны одномассовая и двухмассовая модели электроприводов круговой и поперечной подач профилирующего электрода с линеаризованными характеристиками приводного двигателя.
По профилограммам рабочей поверхности алмазных шлифовальных кругов проведена оценка параметров случайной функции, воспроизводящей эту поверхность, и построена ее имитационная модель. Установлено, что закон распределения этой случайной функции подчиняется закону Пуассона.
В результате моделирования установлена экстремальная зависимость величины средней мощности, выделяемой в межэлектродном промежутке, от величины этого промежутка (рис. 1).
Sотн
аSотн
а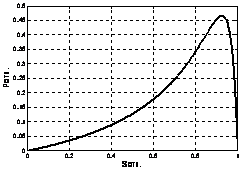
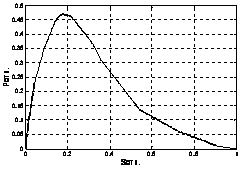
аа а) аа б)
Рис. 1. Экстремальная зависимость величины средней мощности,
выделяемой в межэлектродном промежутке,
от величины этого промежутка:
а - для идеально ровной рабочей поверхности шлифовального круга;
б - с учетом неровностей поверхности
Смещение экстремальной характеристики средней мощности с учетом неровностей рабочей поверхности алмазных кругов объясняется наличием режимов холостого хода и короткого замыкания, при которых рассматриваемая мощность равна нулю.
В результате объединения приведенных выше моделей получена модель процесса электроэрозионного профилирования алмазных шлифовальных кругов с автоматизированным экстремальным управлением подачей профилирующего электрода.
На рис. 2 приведена структурная схема данной модели, реализованной в среде имитационного моделирования Simulink, где Б1 - полупроводниковый преобразователь; Б2 - электропривод подачи профилирующего электрода; Б3 - блок вычисления величины межэлектродного промежутка и его активного сопротивления; Б4 - блок, реализующий работу схемы замещения межэлектродного промежутка; Б5 - блок переключения между режимом холостого хода и рабочим режимом; Б6 - блок, вычисляющий интенсивность съема алмазосодержащего слоя алмазного шлифовального круга; Б7 - блок, реализующий алгоритм экстремального управления на основе нечеткой процедуры поиска экстремума.
Рис. 2. Структурная схема Simulink-модели управляемого процесса
электроэрозионного профилирования
Среднеквадратическое отклонение между расчетными, полученными в Simulink-модели и экспериментальными значениями импульсов тока и напряжения, отнесенное к их установившимся значениям, не превышает 10 %.
В третьей главе приведены результаты экспериментальных исследований закономерностей процесса электроэрозионного профилирования алмазных шлифовальных кругов, доказывающих экстремальную зависимость величины средней мощности от межэлектродного промежутка и существенное влияние неровностей рабочей поверхности алмазно-абразивного инструмента на эту зависимость.
Экспериментальные исследования выполнялись на специальной установке, созданной на базе модернизированного токарно-фрезерного станка АМ-171, позволяющей производить электроэрозионное профилирование и правку алмазных шлифовальных кругов.
Использовались специальные безалмазные круги прямого профиля, изготовленные из различных металлических связок, а также алмазные шлифовальные круги с той же формой профиля на металлической связке М1.
Определена вероятность появления рабочих импульсов в зависимости от средней величины межэлектродного промежутка. На рис. 3 показаны законы распределения неровностей рабочих поверхностей профилирующего электрода и алмазного шлифовального круга.
Рис. 3. Законы распределения неровностей рабочих поверхностей
профилирующего электрода (f1(x)) и алмазного круга (f2(x+ S))
Вероятность появления рабочих импульсов Pp равна незаштрихованной площади законов распределения.
На рис. 4 приведено изменение этой вероятности от средней величины межэлектродного промежутка.
S, мкм
аS, мкм
а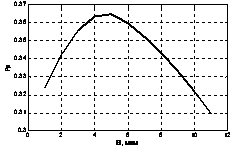
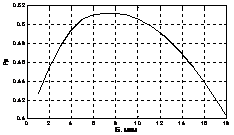
а)а б)
Рис. 4. Зависимость вероятности появления рабочих импульсов
от величины межэлектродного промежутка (U = 100 В; J = 4 А):
а - q = 3; б - q = 2
Наличие неровностей рабочих поверхностей электрода и алмазного круга смещает точку экстремума в сторону меньших значений межэлектродного промежутка, что подтверждает результаты моделирования на Simulink-модели.
Экспериментально установлено, что зависимость величины средней мощности, выделяемой в межэлектродном промежутке, от величины этого промежутка также носит экстремальный характер (рис. 5).
Рис. 5. Экспериментально полученные зависимости
относительной величины средней мощности, выделяемой
в межэлектродном промежутке, от величины этого промежутка
С увеличением величины средней мощности пропорционально растет интенсивность съема алмазосодержащего слоя шлифовального круга, характеризующая производительность обработки.
В связи с этим для интенсификации процесса профилирования предложено осуществлять подачу профилирующего электрода из условия выделения в межэлектродном промежутке максимальной величины средней мощности. С этой целью предложено использовать систему автоматизированного управления приводом подач профилируюнщего электрода на основе экстремального регулирования.
Экстремальное регулирование мощности также обеспечивает проведение электроэрозионной обработки алмазно-абразивного инструмента с оптимальной величиной межэлектродного промежутка, при которой значительно снижается вероятность возникновения режимов холостого хода и короткого замыкания, а также механического воздействия алмазных зерен на профилирующий электрод, что повышает стабильность профилирования.
Поскольку разработанная Simulink-модель процесса электроэрозионного профилирования алмазных шлифовальных кругов не учитывает теплофизические свойства связки алмазного инструмента и износ профилирующего электрода, то для определения влияния режимов профилирования на основные параметры этого процесса проведен эксперимент с использованием методики планирования эксперимента.
В качестве варьируемых факторов были выбраны: f - частота технологических импульсов, кГц; q - скважность технологических импульсов; U - амплитуда импульсов напряжения генератора технологических импульсов, В; А - зернистость алмазного порошка, мкм; K - концентрация алмазов в алмазосодержащем слое шлифовального круга, %.
При определении коэффициентов полинома применялось центральное ротатабельное униформ-планирование второго порядка с ядром в виде полного факторного эксперимента типа 25.
В процессе эксперимента поддерживалось экстремальное значение средней мощности, выделяемой в межэлектродном промежутке, путем регулирования величины этого промежутка.
В результате было получено уравнение регрессии, связывающее интенсивность съема связки М1 mМ1 (мм3/мин) с исследуемыми факторами:
. а(2)
Для обобщения результатов регрессионного анализа экспериментально был получен поправочный коэффициент kс, учитывающий интенсивность съема для различных видов металлических связок, значения которого приведены в табл. 1.
Таблица 1
Значения коэффициента kс
Связка |
М1 |
МС1 |
МК |
МЖ |
Ж1 |
М04 |
М05 |
М016 |
ТМ2 |
kc |
1,0 |
0,81 |
0,69 |
0,82 |
0,42 |
0,71 |
0,83 |
0,70 |
0,88 |
Установлено, что с повышением частоты и скважности разрядных импульсов интенсивность съема падает, а с повышением амплитуды импульсов напряжения - растет. Выявлено, что присутствующие в связках наполнители и легирующие элементы снижают интенсивность съема алмазосодержащего слоя.
Расхождение величины интенсивности съема между экспериментальными и расчетными данными, полученными в разработанной Simulink-модели, не превышает 15 %.
На основе величины объемной интенсивности съема связки получены выражения для определения припусков на чистовой и доводочный технологические переходы.
Получено уравнение регрессии для определения линейного относительного износа профилирующего электрода:
а а(3)
Установлено, что повышение частоты и скважности разрядных импульсов, а также зернистости и концентрации алмазных зерен приводит к росту линейного относительного износа. При повышении амплитуды импульсов напряжения, генератора технологических импульсов, линейный относительный износ профилирующего электрода снижается.
В четвертой главе приведены результаты исследования рабочей поверхности алмазных шлифовальных кругов и практические рекомендации по обеспечению стабильности и производительности процесса электроэрозионного профилирования, разработанные на основе этого исследования. Представлены результаты влияния предложенных алгоритмов и режимов автоматизированного электроэрозионного профилирования шлифовальных кругов на точность этого процесса и приводятся технологические показатели профильного шлифования, которые подтверждают обоснованность предложенных алгоритмов и режимов.
При исследовании рабочей поверхности алмазных шлифовальных кругов с помощью профилографа выявлено наличие периодической составляющей в профилях неровностей, зависящей от зернистости и концентрации алмазного порошка.
На рис. 6 приведены характерные спектральные плотности профилей неровностей рабочей поверхности алмазных кругов с различной зернистостью.
F, 1/мкм
аF, 1/мкм
а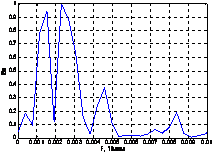
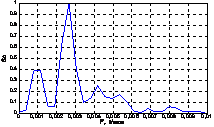
а)а аа б)
Рис. 6. Спектральные плотности профилей неровностей
рабочей поверхности алмазных кругов:
а - зернистость - 80/63 мкм; б - зернистость - 50/40 мкм
Из графика на рис. 6,б видно, что максимум этой плотности находится на частоте 0,0026 1/мкм, которая соответствует периоду, равному 385 мкм.
Сделано предположение, что периодическая составляющая рабочей поверхности шлифовального круга вызвана наличием алмазных зерен, выступающих над поверхностью связки.
Поскольку геометрия рабочей поверхности алмазных кругов является случайной функцией, удовлетворяющей условиям стационарности и эргодичности, то нет необходимости рассматривать ее всю целиком. Достаточно определить средний шаг алмазных зерен на
локальном участке этой поверхности.
Фотографирование локального участка рабочей поверхности алмазного шлифовального круга (1840?840 мкм) с зернистостью алмазного порошка 50/40 мкм 100 % концентрации (рис. 7) подтвердило, что расстояние между алмазными зернами близко к расстоянию, определенному по спектральным плотностям (см. рис. 6).
Рис. 7. Фотография рабочей поверхности
алмазного шлифовального круга
Для дополнительного подтверждения данного обстоятельства был проведен вычислительный эксперимент. На рассматриваемом
локальном участке тех же размеров случайным образом по равномерному закону распределения размещалось столько же точек, сколько алмазных зерен на фотографии (см. рис. 7). Затем строилась триангуляция Делоне и определялось среднее геометрическое значение расстояния между этими точками, которое оказалось равным 410 мкм.
Сопоставление расчетной и экспериментально найденной величины среднего расстояния между алмазными зернами показало, что расхождение не превышает 9 %.
Наличие периодичности расположения алмазных зерен обусловливает необходимость синхронизации частоты вращения алмазного круга с частотой генератора технологических импульсов. Предлагается граничные значения частоты fг (кГц) и длительности разрядных импульсов tи (мс) вычислять с учетом скорости вращения алмазного круга V (м/с) и среднего расстояния между алмазными зернами lз (мм):
;а (4)
, аа(5)
где dср - средний диаметр алмазных зерен, мм.
Синхронизация вращения алмазного круга с частотой генератора технологических импульсов стабилизирует процесс электроэрозионного профилирования, поскольку обеспечивается равномерное размещение эрозионных лунок в промежутке между алмазными зернами, значительно снижается термическое воздействие разрядных импульсов на алмазные зерна и, как следствие, обеспечивается неизменность их физико-механических свойств.
Разработана методика расчета параметров импульсов напряжения, формируемых генератором по характеристикам алмазных шлифовальных кругов, которая заключается в следующем.
Рассчитывается количество алмазных зерен, приходящихся на единицу площади рабочей поверхности алмазного круга:
,а (6)
где Va - относительный объем, занимаемый алмазами в алмазосодержащем слое; dср - средний диаметр алмазных зерен; kр = 0,4 - поправочный коэффициент.
Исходя из заданной достоверности задается число алмазных зерен и вычисляется площадь участка рабочей поверхности алмазного круга, на котором случайным образом по равномерному закону распределения размещаются эти зерна. Строится триангуляция Делоне и вычисляется среднее геометрическое значение расстояния между алмазными зернами. По формулам (4) и (5) определяются граничные значения частоты и длительности разрядных импульсов.
На основе механизма электрического пробоя жидкостей и допустимой энергии разрядных импульсов проведен расчет формы и амплитуды этих импульсов.
Амплитуда поджигающих Uп (В) и силовых импульсов Uс (В) определяется по следующим формулам:
а аа(7)
где Eпр - предельная электрическая прочность жидкой среды в меж-электродном промежутке, определяемая по формуле Мартина, В/мкм; S - величина межэлектродного промежутка, мкм;
,а аа8)
где Pи - мощность единичного разрядного импульса, Вт; Rср - среднее сопротивление межэлектродного промежутка во время импульсного разряда, определяемое по осциллограммам тока и напряжения разрядных импульсов, Ом.
Максимальная мощность единичного разрядного импульса Pи (Вт) определяется из условия непревышения оптимальной величины энергии разрядных импульсов:
,аа а(9)
где Wопт - оптимальная энергия разрядного импульса, Дж; tи - длительность разрядных импульсов, с.
Рассчитанные по зависимостям (4), (5), (7)-(9) предельные (sup, inf) режимы электроэрозионного профилирования для алмазных кругов 100 % концентрации приведены в табл. 2.
Таблица 2
sup-, inf-режимы профилирования алмазных кругов
Зернис-тость, мкм |
Режимы профилирования |
|||||||||
Чистовой переход |
Доводочный переход |
|||||||||
supU, В |
supUc, В |
supPи, Вт |
suptи, мкс |
inf fг, кГц |
supUп, В |
supUc, В |
supPи, Вт |
suptи, мкс |
inf fг, кГц |
|
250/200 |
730 |
70 |
300 |
150 |
2,2 |
730 |
100 |
110 |
150 |
2,2 |
200/160 |
590 |
70 |
300 |
150 |
2,7 |
590 |
100 |
80 |
150 |
2,7 |
160/125 |
480 |
70 |
300 |
150 |
3,6 |
480 |
80 |
50 |
150 |
3,6 |
125/100 |
390 |
70 |
300 |
150 |
4,1 |
390 |
70 |
40 |
150 |
4,1 |
100/80 |
330 |
70 |
300 |
140 |
4,7 |
330 |
60 |
30 |
140 |
4,7 |
80/63 |
280 |
75 |
300 |
130 |
6,2 |
280 |
50 |
20 |
130 |
6,2 |
63/50 |
220 |
75 |
300 |
130 |
6,9 |
220 |
40 |
15 |
130 |
6,9 |
50/40 |
200 |
100 |
300 |
100 |
9,8 |
200 |
30 |
10 |
100 |
9,8 |
С целью проверки адекватности предложенных режимов обработки проводились экспериментальные исследования точности глубинного электроэрозионного профилирования на алмазных шлифовальных кругах различной зернистости 100 % концентрации на металлической связке М1.
Экспериментальные исследования проводились на предложенных режимах с круговой подачей профилирующего электрода из условия достижения максимальной величины средней мощности, выделяемой в межэлектродном промежутке, а также со средним значением круговой подачи. Средняя величина круговой подачи электрода определялась экспериментально для алмазного круга с определенной зернистостью путем усреднения значений круговой подачи электрода при ее экстремальном регулировании.
Исследования показали, что при прочих равных условиях профилирование с экстремальным регулированием круговой подачи электрода обеспечивает повышение точности обработки до 30 % за счет стабильного поддержания параметров технологического процесса (рис. 8).
Рис. 8. Зависимость погрешности профилирования алмазных кругов различной зернистости 100 % концентрации от угла наклона местной
нормали профиля:
1 - с круговой подачей электрода из условия достижения максимальной
величины средней мощности; 2 - со средней величиной круговой подачи
Для оценки влияния предложенных режимов на эффективность профильного алмазного шлифования были проведены экспериментальные исследования удельного расхода алмазов и шероховатости обработанной поверхности в зависимости от режимов шлифования.
Исследования показали, что при прочих равных условиях удельный расход алмазов у шлифовальных кругов, спрофилированных с экстремальным регулированием величины круговой подачи профилирующего электрода, уменьшается на 12-17 %, а шероховатость обработанной поверхности снижается на 15-20 %.
В пятой главе приведена разработанная система автоматизированного управления глубинным электроэрозионным профилированием, а также представлены практические рекомендации по модернизации оборудования.
В крупносерийном и массовом производстве, когда применяется большое количество алмазных шлифовальных кругов, профилирование алмазного инструмента непосредственно на рабочем месте экономически нецелесообразно. В связи с этим разработана и изготовлена установка для глубинного электроэрозионного профилирования на базе токарно-фрезерного станка модели АМ-171 (рис. 9).
|
|
Рис. 9. Установка для глубинного электроэрозионного профилирования
Для повышения эффективности процесса профилирования разработана система автоматизированного управления установкой для глубинного электроэрозионного профилирования алмазных шлифовальных кругов, состоящая из микропроцессорного устройства управления приводами подач профилирующего электрода, реализованного на базе микроконтроллера ATmega128, и персонального компьютера.
Разработаны алгоритм работы микропроцессорного устройства управления, а также программы нижнего и верхнего уровня для осуществления работы системы автоматизированного управления установкой.
Результаты работы внедрены в производство на ФГУП ФНПЦ ПО ?Старт? им. М. В. Проценко, что позволило повысить производительность изготовления фасонных твердосплавных инструментов в 1,2-1,5 раза, а также изделий основного производства из магнитных сплавов и керамики - в 1,3-1,8 раза.
ОСНОВНЫЕ РЕЗУЛЬТАТЫ И ВЫВОДЫ
- Разработана Simulink-модель управляемого процесса электроэрозионного профилирования алмазных шлифовальных кругов, которая позволяет учитывать влияние межэлектродной среды на параметры разрядных импульсов, динамические характеристики электроприводов подач, а также технологические особенности процесса профилирования. Установлено, что расхождение между расчетными, полученными в Simulink-модели, и экспериментальными значениями импульсов тока и напряжения не превышает 10 %, а расхождение величины интенсивности съема - 15 %.
- Доказано существование экстремальной зависимости средней мощности, выделяемой в межэлектродном промежутке, от его величины, а также значительное влияние на характер этой зависимости неровностей рабочих поверхностей шлифовального круга и электрода. Данная зависимость позволяет реализовать процесс автоматизированного экстремального управления профилированием.
- Предложено использовать алгоритм экстремального управления на основе нечеткой процедуры поиска экстремума, обеспечивающий подачу профилирующего электрода из условия достижения максимальной величины средней мощности, выделяемой в межэлектродном промежутке, и позволяющий интенсифицировать на 20-40 % и стабилизировать процесс электроэрозионного профилирования.
- Проведена оценка параметров случайной функции неровностей рабочей поверхности, построена ее имитационная модель и установлено, что закон распределения этой случайной функции соответствует закону Пуассона.
- В результате анализа спектрограмм случайной функции неровностей рабочей поверхности алмазных шлифовальных кругов выявлено квазипериодическое расположение алмазных зерен на их рабочей поверхности, что позволило стабилизировать процесс электроэрозионного профилирования путем фазовой синхронизации частоты разрядных импульсов с частотой вращения алмазного круга.
- Разработана методика расчета параметров разрядных импульсов по характеристикам алмазных шлифовальных кругов, обеспечивающая повышение режущих свойств у алмазно-абразивного инструмента после электроэрозионного профилирования.
- Получены экспериментальные зависимости, отражающие влинянние режимов профилирования на объемную интенсивность съема алмазосодержащего слоя и линейный относительный износ электрода.
- Экспериментально подтверждена эффективность предложенных экстремальных алгоритмов управления и режимов автоматизированного электроэрозионного профилирования, что дало возможность снизить удельный расход алмазов на 12-17 %, уменьшить шероховатость обработанной поверхности на 15Е20 % по параметру Ra при повышении точности обработки до 30 %.
- аРазработана система автоматизированного управления глубинным электроэрозионным профилированием, а также предложены практические рекомендации по модернизации оборудования.
- Никиткин, А. С. Модель процесса электроэрозионного профилирования алмазных шлифовальных кругов / А. Д. Семенов, А. С. Никиткин // Новые промышленные технологии. - 2009. - № 3. - С. 14-16.
- Никиткин, А. С. Алгоритм экстремального регулирования на основе рекуррентной процедуры метода наименьших квадратов / А. Д. Семенов, О. В. Авдеева, А. С. Никиткин // Известия высших учебных заведений. Поволжский регион. Технические науки. - 2012. - № 1. - С. 3-11.
- Никиткин, А. С. Определение режимов генератора технологических импульсов для электроэрозионного профилирования алмазных шлифовальных кругов / А. Д. Семенов, А. С. Никиткин, О. В. Авдеева // Инженернный вестник Дона (электронный журнал). - 2012. - № 2. - URL: /n2y2012/826.
- Никиткин, А. С. Моделирование процесса электроэрозионного профилирования алмазных шлифовальных кругов / В. О. Соколов, А. С. Нинкитнкин // Системы проектирования, моделирования, подготовки производства и управление проектами CAD/CAM/CAE/PDM : сб. ст. II Междунар. науч.-практ. конф. - Пенза : Приволж. Дом знаний, 2008. - С. 51-54.
- Никиткин, А. С. Профилирование алмазных шлифовальных кругов на токопроводящих связках / А. С. Никиткин // Наука и инновации в технических университетах : материалы Всерос. форума студентов, аспи-рантов и молодых ученых. - СПб. : Изд-во Политехн. ун-та, 2008. - С. 45-46.
- Никиткин, А. С. Экспериментальное определение параметров схемы замещения межэлектродного зазора при электроэрозионной обработке / А. Д. Семенов, А. С. Никиткин, О. В. Авдеева // Проблемы автоматизации и управления в технических системах : тр. Междунар. науч.-техн. конф. - Пенза : Изд-во ПГУ, 2009. - С. 294-298.
- Никиткин, А. С. Моделирование системы автоматического регулирования межэлектродного зазора при электроэрозионном профилировании алмазных кругов / А. Д. Семенов, А. С. Никиткин // Надежность и качество - 2009 : тр. Междунар. симп. : в 2 т. - Пенза : Изд-во ПГУ, 2009. -
Т. 1. - С. 270-273.
- Никиткин, А. С. К вопросу об управлении формообразованием профиля алмазных шлифовальных кругов на токопроводящих связках / А. С. Никиткин // Формообразование и обеспечение качества техногенных систем : сб. ст. Междунар. науч.-практ. конф. - Пенза : Приволж. Дом знаний, 2009. - С. 74-77.
- Никиткин, А. С. Рекуррентный алгоритм поиска экстремума статической характеристики инерционного объекта / А. С. Никиткин, О. В. Авнденева // Датчики и системы : тр. XXIX Всерос. науч.-пракнт. конф. молодых ученых и специалистов. - Пенза : ОАО НИИФИ, 2010. - С. 180-182.
- Никиткин, А. С. К вопросу о построении автоматических систем управления для станков электроэрозионного профилирования алмазных шлифовальных кругов на токопроводящих связках / А. С. Никиткин, О. В. Авденева // Датчики и системы : тр. XXIX Всерос. науч.-пракнт. конф. молодых ученых и специалистов. - Пенза : ОАО НИИФИ, а2010. - С. 201-203.
- Никиткин, А. С. Алгоритм экстремального регулирования автоматической системы управления процессом электроэрозионной обработки / А. Д. Семенов, О. В. Авдеева, А. С. Никиткин // Надежность и качество - 2010 : тр. Междунар. симп. : в 2 т. - Пенза : аИзд-во ПГУ, 2010. -
Т. 2. - С. 191-192.
- Никиткин, А. С. Помехоустойчивый алгоритм экстремального регулирования инерционными объектами / А. Д. Семенов, О. В. Авдеева, А. С. Никиткин // Автоматизация & IT в энергетике. - 2011. - № 11. - С. 18-21.
- Никиткин, А. С. Моделирование экстремального регулятора производительности / А. Д. Семенов, О. В. Авдеева, А. С. Никиткин // Новые промышленные технологии. - 2011. - № 3. - С. 46-49.
- Никиткин, А. С. Конструкция системы управления электроэрозионным профилированием алмазных шлифовальных кругов / А. Д. Семенов, А. С. Никиткин, О. В. Авдеева // Наукоемкие технологии в машиностроении. - 2011. - № 5. - С. 17-22.
- Никиткин, А. С. Программное управление автоматизированной установкой для глубинного электроэрозионного профилирования шлифовальных кругов / А. Д. Семенов, А. С. Никиткин, О. В. Авдеева // Новые промышленные технологии. - 2011. - № 6. - С. 5-8.
- Никиткин, А. С. Влияние электрических режимов и характеристик рабочей поверхности алмазных шлифовальных кругов на производительность процесса обработки при их электроэрозионном профилировании / А. С. Никиткин // Наука и инновации в технических университетах : материалы Всерос. форума студентов, аспирантов и молодых ученых. - СПб. : Изд-во Политехн. ун-та, 2011. - С. 20-22.
- Никиткин, А. С. Разработка эффективного технологического процесса глубинного электроэрозионного профилирования алмазных шлифовальных кругов / А. С. Никиткин // Надежность и качество - 2012 : тр.
Междунар. симп. : в 2 т. - Пенза : Изд-во ПГУ, 2012. - Т. 2. - С. 221-223.
ОСНОВНЫЕ ПУБЛИКАЦИИ ПО ТЕМЕ ДИССЕРТАЦИИ
Публикации в изданиях, рекомендованных ВАК
Публикации в других изданиях
Научное издание
НИКИТКИН Александр Сергеевич
Интенсификация и стабилизация
электроэрозионного профилирования алмазных
шлифовальных кругов
путем автоматизированного управления
режимами обработки
Специальности:
05.13.06 - Автоматизация и управление технологическими
процессами и производствами (промышленность);
05.02.07 - Технология и оборудование механической
и физико-технической обработки
Редактор Е. П. Мухина
Технический редактор Н. В. Иванова
Компьютерная верстка Н. В. Ивановой
Распоряжение № 26/2012 от 29.05.2012.
Подписано в печать 04.06.12. Формат 60x841/16.
Усл. печ. л. 1,16. Заказ № 420. Тираж 100.
_______________________________________________________
Издательство ПГУ.
440026, Пенза, Красная, 40.
Тел./факс: (8412) 56-47-33; e-mail:
