Обработка металлов резанием
Вид материала | Документы |
Р. И. Энтин. А. Я. Стомахин. |
- Шифр специальности: 05. 16. 01 Металловедение и термическая обработка металлов и сплавов, 25.46kb.
- Обработка металлов давлением при обработке металлов давлением, 131.9kb.
- Программа профессиональной переподготовки мтф п/п-1 «металловедение и термическая обработка, 34.45kb.
- Лекция 7 термическая обработка металлов, 136.74kb.
- Научные основы и технологические способы обработки гетерофазных сплавов с высоким уровнем, 572.64kb.
- Программа вступительного испытания по направлению «Металлургия», 51.65kb.
- 05. 16. 01 Металловедение и термическая обработка металлов, 25.25kb.
- Развитие научных основ и разработка совмещенных методов обработки металлов давлением,, 606kb.
- Реферат по теме: «Металлы. Свойства металлов.», 196.2kb.
- Закономерности превращения, 589.18kb.
Перлит в металловедении, одна из структурных составляющих железоуглеродистых сплавов — сталей и чугунов: представляет собой эвтектоидную (см. Эвтектоид) смесь двух фаз — феррита и цементита (в легированных сталях — карбидов). П.— продукт эвтектоидного распада аустенита при сравнительно медленном охлаждении железоуглеродистых сплавов ниже 723 °С. При этом -железо переходит в -железо, растворимость углерода в котором составляет лишь около 0,02%; избыточный углерод выделяется в форме цементита или карбидов. В зависимости от формы различают П. пластинчатый (основной вид П.; обе фазы имеют форму пластинок) и зернистый (округлые зёрнышки, или глобули, цементита располагаются на фоне зёрен феррита). С увеличением переохлаждения растет число колоний П., то есть участков с однообразной ориентацией пластинок феррита и цементита (карбидов), а сами пластинки становятся более тонкими. Механические свойства П. зависят в первую очередь от межпластиночного расстояния (суммарная толщина пластинок обеих фаз): чем оно меньше, тем выше значение предела прочности и предела текучести и ниже критическая температура хладноломкости. При перлитной структуре облегчается механическая обработка стали. Дисперсные разновидности П. иногда называют сорбитом и трооститом.
Лит.: Бунин К. П., Баранов А. А., Металлография, М., 1970.
Р. И. Энтин.
Цементит, карбид железа Fe3C, фазовая и структурная составляющая железоуглеродистых сплавов. Ц. имеет орторомбическую кристаллическую решётку, очень твёрд и хрупок, слабо магнитен до 210 °С. Ц. — метастабильная фаза; образование стабильной фазы — графита во многих случаях затруднено. Ц. выделяется из расплава, из аустенита и феррита. В зависимости от условий кристаллизации и последующей обработки Ц. может иметь различную форму — равноосных зёрен, сетки по границам зёрен, пластин, а также видманштеттову структуру. Ц. — составная часть структурных составляющих стали и чугуна — ледебурита, перлита, бейнита, сорбита отпуска.
Лит.: Бунин К. П.. Баранов А. А., Металлография, М., 1970.
Феррит (от лат. ferrum – железо), структурная составляющая сплавов железа, представляющая собой твёрдый раствор углерода и легирующих элементов в -железе. Кристаллическая решётка – объёмноцентрированный куб (ОЦК). Растворимость углерода в Ф. 0,02–0,03% (по массе) при 723 °С, а при комнатной температуре 10-6–10-7%. Растворимость легирующих элементов может быть весьма значительной или неограниченной. Легирование Ф. в большинстве случаев приводит к его упрочнению. Нелегированный Ф. относительно мягок, пластичен, сильно ферромагнитен до 768–770 °С. Микростроение, размеры зерна и субструктура Ф. зависят от условий его образования при полиморфном -превращении. При небольшом переохлаждении образуются приблизительно равноосные, полиэдрические зёрна; при больших переохлаждениях и наличии легирующих элементов (Cr, Mn, Ni) Ф. возникает по мартенситному механизму и вследствие этого упрочняется. Укрупнение зёрен аустенита часто приводит к образованию при охлаждении видманштеттова Ф. (см. Видманштеттова структура), особенно в литых и перегретых сталях. Выделение доэвтектоидного Ф. происходит преимущественно на границах аустенитных зёрен. При температурах выше 1390 °С в железоуглеродистых сплавах образуется твёрдый раствор углерода в -железе, имеющий также кристаллическую решётку (ОЦК); растворимость углерода в -железе 0,1%. Эту фазу можно рассматривать как высокотемпературный Ф. См. также Железоуглеродистые сплавы.
Лит.: Вочвар А. А,, Металловедение, 5 изд., М., 1956; Бунин К, П., Баранов А. А., Металлография, М., 1970.
Р. И. Энтин.
Ликвация (от лат. liquatio — разжижение, плавление), сегрегация (от позднелат. segregatio — отделение) в металлургии, неоднородность химического состава сплавов, возникающая при их кристаллизации. Особое значение имеет Л. в стали, впервые обнаруженная русскими металлургами Н. В. Калакуцким и А. С. Лавровым в 1866.
Л. возникает в результате того, что сплавы, в отличие от чистых металлов, кристаллизуются не при одной температуре, а в интервале температур. При этом состав кристаллов, образующихся в начале затвердевания, может существенно отличаться от состава последних порций кристаллизующегося маточного раствора. Чем шире температурный интервал кристаллизации сплава, тем большее развитие получает Л., причём наибольшую склонность к ней проявляют те компоненты сплава, которые наиболее сильно влияют на ширину интервала кристаллизации (для стали, например, сера, кислород, фосфор, углерод). Л. оказывает, как правило, вредное влияние на качество металла, т. к. приводит к неравномерности его свойств.
Различают дендритную Л., которая проявляется в микрообъёмах сплава, близких к размеру зёрен, и зональную Л., наблюдаемую во всём объёме слитка. Дендритная Л. выражается в том, что оси дендритных кристаллов отличаются по химическому составу от межосных пространств. Этот вид Л. может быть в значительной степени устранён при длительном отжиге металла (так называемая гомогенизация) в результате диффузии примесей. Зональная Л. выражается в наличии в слитке нескольких зон с различным химическим составом, которые в зависимости от характера отклонений от среднего состава сплава называются зонами положительной или отрицательной Л. Различают осевую и внеосевую Л. Для уменьшения зональной Л. ограничивают размеры слитков, а также применяют специальные металлургические процессы: непрерывную разливку, переплав в водоохлаждаемом кристаллизаторе (электрошлаковый или вакуумный) и т. п.
Лит.: Голиков И. Н., Дендритная ликвация в стали, М., 1958; Штейнберг С. С., Металловедение, Свердловск, 1961; Вайнгард У., Введение в физику кристаллизации металлов, пер. с англ., М., 1967.
А. Я. Стомахин.
Внутреннее трение в твёрдых телах, свойство твёрдых тел необратимо превращать в теплоту механическую энергию, сообщенную телу в процессе его деформирования. В. т. связано с двумя различными группами явлений — неупругостью и пластической деформацией.
Неупругость представляет собой отклонение от свойств упругости при деформировании тела в условиях, когда остаточные деформации практически отсутствуют. При деформировании с конечной скоростью в теле возникает отклонение от теплового равновесия. Например, при изгибе равномерно нагретой тонкой пластинки, материал которой расширяется при нагревании, растянутые волокна охладятся, сжатые — нагреются, вследствие чего возникнет поперечный перепад температуры, т. е. упругое деформирование вызовет нарушение теплового равновесия. Последующее выравнивание температуры путём теплопроводности представляет собой процесс, сопровождаемый необратимым переходом части упругой энергии в тепловую. Этим объясняется наблюдаемое на опыте затухание свободных изгибных колебаний пластинки —так называемый термоупругий эффект. Такой процесс восстановления нарушенного равновесия называется релаксацией.
При упругом деформировании сплава с равномерным распределением атомов различных компонентов может произойти перераспределение атомов в веществе, связанное с различием их размеров. Восстановление равновесного распределения атомов путём диффузии также представляет собой релаксационный процесс. Проявлениями неупругих, или релаксационных, свойств, кроме упомянутых, являются упругое последействие в чистых металлах и сплавах, упругий гистерезис и др.
Деформация, возникающая в упругом теле, зависит не только от приложенных к нему внешних механических сил, но и от температуры тела, его химического состава, внешних магнитных и электрических полей (магнито- и электрострикция), величины зерна и т.д. Это приводит к многообразию релаксационных явлений, каждое из которых вносит свой вклад во В. т. Если в теле одновременно происходит несколько релаксационных процессов, каждый из которых можно характеризовать своим временем релаксации i, то совокупность всех времён релаксации отдельных релаксационных процессов образует так называемый релаксационный спектр данного материала (рис.), характеризующий данный материал при данных условиях; каждое структурное изменение в образце меняет релаксационный спектр.
В качестве методов измерения В. т. применяются: изучение затухания свободных колебаний (продольных, поперечных, крутильных, изгибных); изучение резонансной кривой для вынужденных колебаний; относительное рассеяние упругой энергии за один период колебаний. Изучение В. т. твёрдых тел представляет собой новую быстро развивающуюся область физики твёрдого тела, является источником важных сведений о процессах, возникающих в твёрдых телах, в частности в чистых металлах и сплавах, подвергнутых различным механическим и тепловым обработкам.
В. т. при пластической деформации. Если силы, действующие на твёрдое тело, превосходят предел упругости и возникает пластическое течение, то можно говорить о квазивязком сопротивлении течению (по аналогии с вязкой жидкостью). Механизм В. т. при пластической деформации существенно отличается от механизма В. т. при неупругости (см. Пластичность, Ползучесть). Различие в механизмах рассеяния энергии определяет и разницу в значениях вязкости, отличающихся на 5—7 порядков (вязкость пластического течения, достигающая величин 1013—108 н·сек/м2, всегда значительно выше вязкости, вычисляемой из упругих колебаний и равной 107—108 н·сек/м2). По мере роста амплитуды упругих колебаний всё большую роль в затухании этих колебаний начинают играть пластические сдвиги, и величина вязкости растёт, приближаясь к значениям пластической вязкости.
Лит.: Новик А. С., Внутреннее трение в металлах, в кн.: Успехи физики металлов. Сб. статей, пер. с англ., ч. 1, М., 1956; Постников В. С., Релаксационные явления в металлах и сплавах, подвергнутых деформированию, «Успехи физических наук», 1954, т. 53, в. 1, с. 87; его же, Температурная зависимость внутреннего трения чистых металлов и сплавов, там же, 1958, т. 66, в. 1, с. 43.


Пример релаксационного спектра твёрдого тела, обусловленного различными релаксационными процессами.
Сверление, 1) в металлообработке — процесс получения сквозных и глухих отверстий в сплошном материале на сверлильных, токарных, револьверных, расточных, агрегатных и других станках, а также при помощи сверлильных ручных машин. Точность изготовления отверстий при С. — 4—5-й класс. Отверстия более высокой точности получают после С. растачиванием, зенкерованием или развёртыванием.
Главное движение при С. — вращательное, движение подачи — поступательное. При работе на сверлильных станках оба движения осуществляет сверло, при работе на других станках вращение совершает обрабатываемая заготовка, поступательное осевое движение — сверло.
Режим резания при С. определяется скоростью резания v и подачей s. Скорость резания (теоретическая) — окружная скорость наиболее удалённой от оси сверла точки режущей кромки: = Dn/1000 м/мин, где D — диаметр сверла (по ленточкам) в мм; n — частота вращения сверла в об/мин. Допускаемая скорость резания при С.:
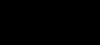

Производительность С. характеризуется основным технологическим временем: To= L/ns мин, где L — длина прохода сверла в мм в направлении подачи.
Д. Л. Юдин.
2) В деревообработке — процесс получения сквозных отверстий в сплошной древесине или древесных материалах сверлом, а также обработка пазов, гнёзд под шипы и т. п. Точность обработки — 2—3-й класс (по диаметру), 3—4-й класс (по глубине). Частота вращения сверла по дереву достигает 3000—12000 об/мин, подача 0,1—0,5 мм/об (для твёрдых материалов) и 0,7—2,2 мм/об (для мягких материалов).
В. С. Рыбалко.
Лит.: Бершадский А. Л., Расчет режимов резания древесины, М., 1967. См. также лит. при ст. Обработка металлов резанием.
Станки
Зубообрабатывающий станок, металлорежущий станок для обработки зубчатых колёс, червяков и зубчатых реек. В зависимости от применяемого инструмента (см. Зуборезный инструмент) различают зубофрезерные, зубодолбёжные, зубострогальные, зубоотделочные (зубошевинговальные, зубошлифовальные, зубохонинговальные, зубопритирочные, зубообкаточные и зубозакругляющие) станки.
На З. с. осуществляют: черновую обработку зубьев, чистовую обработку зубьев, приработку зубчатых колёс, доводку зубьев, закругление торцов зубьев.
На зубофрезерных станках нарезают цилиндрические прямозубые, косозубые и с шевронными зубьями колёса, червячные зубчатые колёса. Наиболее распространённые в промышленности вертикальные зубофрезерные станки выпускаются с подвижным столом и неподвижной стойкой и с подвижной стойкой и неподвижным столом (рис. 1). При нарезании зубчатых колёс заготовка жестко связана с делительным червячным колесом, получающим вращение от делительного червяка, который сменными зубчатыми колёсами кинематически связан с червячной фрезой. Соотношение частоты вращения червячной фрезы и заготовки определяется передаточным отношением набора сменных зубчатых колёс.
Наиболее широко применяются зубофрезерные станки, обеспечивающие нарезание зубчатых колёс с модулем от 0,05 до 10 мм и диаметром от 2 до 750 мм.
На зубодолбёжных станках нарезают цилиндрические зубчатые колёса наружного и внутреннего зацепления с прямыми и косыми зубьями, блоки зубчатых колёс, колёса с буртами, зубчатые секторы, шлицевые валики, зубчатые рейки, храповые колёса и т. п. Обычно нарезание производится методом обкатки, реже — методом копирования (см. Зубонарезание). Наибольшее применение в промышленности имеют вертикальные зубодолбёжные станки (рис. 2). Режущим инструментом является долбяк, который движется возвратно-поступательно параллельно оси заготовки. Главное (рабочее) движение — Vp, при обратном (холостом) ходе Vx резание не совершается. Движение круговой подачи Sвр осуществляют, сообщая вращательное движение и долбяку, и заготовке в направлениях V1 и V2 с тем, чтобы они вращались так, как вращались бы, будучи в зацеплении, два зубчатых колеса. Для этого долбяк и заготовку соединяют жёсткой кинематической цепью со сменными зубчатыми колёсами и реверсивным устройством. При долблении зубьев колёс с наружным зацеплением направление вращения долбяка противоположно направлению вращения заготовки (как это показано на схеме), а при долблении колёс с внутренним зацеплением эти направления совпадают. Шевронные зубчатые колёса обычно нарезают на горизонтальных зубодолбёжных станках поочерёдно работающими долбяками с косыми зубьями правого и левого направления. Наиболее распространены зубодолбёжные станки для нарезания зубчатых колёс с модулем от 0,2 до 6 мм и диаметром от 15 до 500 мм; для нарезания зубчатых колёс с модулем от 8 до 12 мм, диаметром от 800 до 1600 мм. Обработка по методу копирования осуществляется одновременным долблением всех впадин зубчатого колеса фасонными зуборезными головками (рис. 3). Принцип действия таких головок состоит в том, что фасонные резцы, число которых соответствует числу впадин (зубьев) обрабатываемого зубчатого колеса, укрепленные в головке, производят одновременно (за один проход) долбление всех впадин, после чего разводящее кольцо отводит резцы.
На зубострогальных станках (рис. 4) обрабатывают конические зубчатые колёса с прямыми зубьями по методу обкатки одним или чаще двумя резцами. На этих станках воспроизводится зацепление нарезаемого зубчатого колеса с воображаемым плоским производящим зубчатым колесом; при этом два зуба последнего представляют собой зубострогальные резцы, совершающие возвратно-поступательное движение. Т. о., боковые поверхности каждого из зубьев нарезаемого зубчатого колеса формируются в результате движения резцов и обработки находящихся в зацеплении плоского и нарезаемого зубчатых колёс. Процесс нарезания зубьев происходит при движении резцов к вершине конуса заготовки, а обратный ход является холостым (в этот период резцы отводятся от заготовки). Нарезание конических зубчатых колёс с круговыми зубьями осуществляется методом обкатки на специальных станках с применением зуборезной резцовой головки, представляющей собой диск с вставленными по его периферии резцами, обрабатывающими профиль зуба с двух сторон (первая половина резцов обрабатывает одну сторону, вторая половина — другую). Наиболее распространены зубострогальные станки для нарезания конических зубчатых колёс с модулем от 2,5 до 25 мм и длиной зуба от 20 до 285 мм, для чернового нарезания и чистовой обработки крупногабаритных конических прямозубых колёс с модулем до 16 мм, для чернового и чистового нарезания конических колёс с винтовыми зубьями с модулем до 25 мм.
Зубошевингование (бреющее резание) производится на зубошевинговальных станках. Основано на взаимном скольжении находящихся в зацеплении зубьев инструмента и обрабатываемого зубчатого колеса при встречном движении (рис. 5). По направлению подачи различают три метода зубошевингования: параллельный, диагональный и касательный. Инструментом является шевер — дисковый, реечный и червячный. Первые два типа — для обработки цилиндрических зубчатых колёс, последний — для червячных.
На зубошлифовальных станках производят обработку зубчатых колёс обкаткой и профильным копированием при помощи фасонного шлифовального круга (рис. 6, а). По исполнению различают зубошлифовальные станки с вертикальным и горизонтальным расположением обрабатываемого зубчатого колеса. В процессе шлифования методом обкатки воспроизводят зубчатое зацепление пары рейка — зубчатое колесо (рис. 6, б, в), в котором инструментом является шлифовальный круг (или круги), имитирующий рейку. Шлифовальные круги совершают вращательное и возвратно-поступательное движения; последнее — аналогично воображаемой производящей рейке. Обкатываясь по поворачивающемуся (в обе стороны) обрабатываемому зубчатому колесу, шлифовальные круги своими торцами шлифуют поверхности зубьев. По методу обкатки работают также станки с использованием в качестве инструмента абразивного червяка (рис. 6, г).
На зубохонинговальных станках осуществляют обработку прямозубых и косозубых колёс с модулем 1,25—6 мм, а также зубчатых колёс с фланкированными и бочкообразными зубьями для уменьшения шероховатости поверхности профиля зубьев. Зубохонингование производят на станке, аналогичном шевинговальному, при скрещивающихся осях инструмента (зубчатого хона) и обрабатываемого зубчатого колеса, но не имеющем механизма радиальной подачи. Устанавливаемое в центрах станка зубчатое колесо совершает, кроме вращательного (реверсируемого), также и возвратно-поступательное движение вдоль своей оси. Зубчатый хон представляет собой зубчатое колесо с геликоидальным профилем, изготовленное из пластмассы и шаржированное абразивным порошком, зернистость которого выбирается в зависимости от величины припуска (0,025—0,05 мм) и требований к шероховатости поверхности. Зубохонингование производят при постоянном давлении между зубьями обрабатываемого зубчатого колеса и хона («в распор») или при их беззазорном зацеплении, при постоянном межцентровом расстоянии. Первый способ обеспечивает изготовление зубчатых колёс более высокой точности. Необходимым условием зубохонингования является обильное охлаждение и эффективное удаление металлической пыли с обрабатываемой поверхности.
На зубопритирочных станках после термической обработки зубчатых колёс производят операцию зубопритирки. Инструментом служат притиры — чугунные зубчатые колёса, находящиеся в зацеплении с обрабатываемым зубчатым колесом. Притиры смазывают смесью мелкого абразивного порошка с маслом. Обрабатываемое зубчатое колесо (рис.7) обкатывают тремя притирами. Оси притиров со спиральными или прямыми зубьями наклонены к оси обрабатывающего зубчатого колеса; ось третьего притира параллельна оси обрабатываемого зубчатого колеса и вращается попеременно в разных направлениях для обеспечения равномерной обработки зуба с обеих сторон. Притиры также совершают возвратно-поступательное движение в осевом направлении на длине около 25 мм.
На зубообкаточных станках обрабатывают незакалённые зубчатые колёса в масляной среде без абразивного порошка. Обрабатываемое колесо работает в паре с одним или несколькими закалёнными колёсами-эталонами, изготовленными с высокой точностью. В результате давления зубьев колёс-эталонов в процессе обкатывания и возникающего при этом наклёпа на поверхностях обрабатываемых зубьев сглаживаются неровности. Этот способ отделки применим лишь для зубчатых колёс, не требующих высокой точности, а также не подвергающихся термической обработке.
На зубозакругляющих станках обрабатывают зубья пальцевой конической фрезой, вращающейся и совершающей возвратно-поступательное движение. За один двойной ход фрезы зубчатое колесо поворачивается на один угловой шаг. Перемещение инструмента вдоль зуба (рис. 8) осуществляется под действием вращающегося фасонного кулачка. На станках осуществляют закругление прямых и косых зубьев зубчатых колёс наружного и внутреннего зацепления диаметром до 320 мм, а также снимают фаски и заусенцы с торцов зубьев после их нарезки. Во время работы ось инструмента находится в вертикальном положении, а заготовка наклонена к этой оси под углом 30—45°. Станок работает по автоматическому циклу: быстрый подвод инструмента к заготовке, рабочая подача и возврат инструмента в исходное положение. Заготовка закрепляется в приспособлении на оправке.
Лит.: Балакшин Б. С., Основы технологии машиностроения, М., 1969; Яхин А. Б., Ефимов В. П., Технология приборостроения, М., 1955; Технология электроприборостроения, М. — Л., 1959; Гаврилов А. Н., Технология авиационного приборостроения, 2 изд., М., 1962; Соколовский А. П., Научные основы технологии машиностроения, М. — Л., 1955; Чарнко Д. В., Основы выбора технологического процесса механической обработки, М., 1963.
В. В. Данилевский.

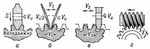
Рис. 6. Схемы зубошлифования: а — по методу профильного копирования фасонным шлифовальным кругом; б — по методу обкатки двумя тарельчатыми шлифовальными кругами; в — по методу обкатки одним дисковым шлифовальным кругом, имеющим профиль зуба рейки; г — по методу обкатки абразивным червяком; Vu и Vg — скорости вращения соответственно инструмента (шлифовального круга) и детали (зубчатого колеса); S — поперечная подача шлифовального круга; V2 — скорость возвратно-поступательного движения шлифовальных кругов.

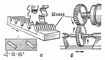
Рис. 5. Схемы шевингования цилиндрических зубчатых колёс: а — реечным шевером; б — дисковым шевером.


Рис. 3. Нарезание зубьев фасонной зуборезной головкой.


Рис. 7. Схема притирки зубчатых колёс: 1, 2, 4 — притиры; 3 — обрабатываемое колесо.

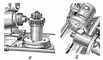
Рис. 8. Схемы зубозакругления наружных (а) и внутренних (б) зубьев.


Рис. 4a. Зубострогальный станок. Общий вид.


Рис. 4б. Зубострогальный станок. Схема нарезания зубьев на коническом зубчатом колесе: 1 — обрабатываемое зубчатое колесо; 2 — производящее зубчатое колесо; 3 — зубострогальные резцы производящего колеса.


Рис. 1. Зубофрезерный станок.


Рис. 2. Принципиальная схема работы вертикального зубодолбёжного станка.