Обработка металлов резанием
Вид материала | Документы |
- Шифр специальности: 05. 16. 01 Металловедение и термическая обработка металлов и сплавов, 25.46kb.
- Обработка металлов давлением при обработке металлов давлением, 131.9kb.
- Программа профессиональной переподготовки мтф п/п-1 «металловедение и термическая обработка, 34.45kb.
- Лекция 7 термическая обработка металлов, 136.74kb.
- Научные основы и технологические способы обработки гетерофазных сплавов с высоким уровнем, 572.64kb.
- Программа вступительного испытания по направлению «Металлургия», 51.65kb.
- 05. 16. 01 Металловедение и термическая обработка металлов, 25.25kb.
- Развитие научных основ и разработка совмещенных методов обработки металлов давлением,, 606kb.
- Реферат по теме: «Металлы. Свойства металлов.», 196.2kb.
- Закономерности превращения, 589.18kb.
Химико-термическая обработка металлов, совокупность технологических процессов, приводящих к изменению химического состава, структуры и свойств поверхности металла без изменения состава, структуры и свойств его сердцевидных зон. Осуществляется с помощью диффузионного насыщения поверхности различными элементами при повышенных температурах. Выбор элемента (или комплекса элементов) определяется требуемыми свойствами поверхности детали. Насыщение производят углеродом (цементация), азотом (азотирование), азотом и углеродом (нитроцементация, цианирование), металлами (см. Диффузионная металлизация), бором (борирование), кремнием (силицирование) и т.д.
В зависимости от физико-химического состояния среды, содержащей диффундирующий элемент, различают Х.-т. о. из газовой, жидкой, твёрдой или паровой фазы (чаще применяются первые 2 метода). Х.-т. о. проводится в газовых, вакуумных или в ванных печах. Х.-т. о. подвергаются изделия из стали, чугуна, чистых металлов, сплавов на основе никеля, молибдена, вольфрама, кобальта, ниобия, меди, алюминия и др.
Физико-химические процессы, происходящие вблизи поверхности при Х.-т. о., заключаются в образовании диффундирующего элемента в атомарном состоянии вследствие химических реакций в насыщающей среде или на границе раздела среды с поверхностью металла (при насыщении из газовой или жидкой фазы), сублимации диффундирующего элемента (насыщение из паровой фазы), последующей сорбции атомов элемента поверхностью металла и их диффузии в поверхностные слои металла. Концентрация диффундирующего элемента на поверхности металла, а также структура и свойства диффузионного слоя зависят от метода Х.-т. о. Глубина диффузии элемента возрастает с повышением температуры (по экспоненциальному закону) и с увеличением продолжительности процесса (по параболическому закону). Диффузионный слой, образующийся при Х.-т. о. деталей, изменяя структурно-энергетическое состояние поверхности, оказывает положительное влияние не только на физико-химические свойства поверхности, но и на объёмные свойства деталей. Х.-т. о. позволяет сообщить изделиям повышенную износостойкость, жаростойкость, коррозионную стойкость, усталостную прочность и т.д. (см. статьи о конкретных процессах Х.-т. о.).
Лит.: Минкевич А. Н., Химико-термическая обработка металлов и сплавов, 2 изд., М., 1965; Райцес В. Б., Технология химико-термической обработки на машиностроительных заводах, М., 1965; Самсонов Г. В., Эпик А. П., Тугоплавкие покрытия, 2 изд., М., 1973; Дубинин Г. Н., О механизме формирования диффузионного слоя, в сборнике: Защитные покрытия на металлах, в. 10, К., 1976.
Г. Н. Дубинин.
Наклёп металлов и сплавов, изменение структуры и соответственно свойств металлов и сплавов, вызванное пластической деформацией при температуре ниже температуры рекристаллизации. Н. называется также технологический процесс создания упрочнённого состояния материала холодной поверхностной пластической деформацией. Явление Н. объясняется накапливанием в металле части энергии деформации, которая расходуется на искажение кристаллической решётки, образование преимущественно ориентированных кристаллов (текстур), изменение дислокационных структуры, а также на увеличение удельного объёма металла в слое. Н. может быть результатом действия внешних деформирующих сил (деформационный Н.) или, реже, фазовых превращений (фазовый Н.). Н. сопровождается увеличением прочности и твёрдости и снижением пластичности материала.
В технике Н. используется для поверхностного упрочнения деталей. Кроме того Н. приводит к возникновению в поверхностном слое детали благоприятной системы остаточных напряжений, влияние которых главным образом и определяет высокий упрочняющий эффект поверхностной пластической деформации, выражающийся в повышении усталостной прочности, а иногда и износостойкости. Н. осуществляют специальными способами и на специальном оборудовании, например, производят обкатку цилиндрических поверхностей роликами, зубьев зубчатых колёс роликами или зубчатыми накатниками, дробеструйную обработку фасонных поверхностей, обработку ударными инструментами и др.
Лит.: Кудрявцев И. В., Поверхностный наклеп для повышения прочности и долговечности деталей машин, 2 изд. М., 1969; Бернштейн М. Л., Займовский В. А., Структура и механические свойства металлов, М., 1970
Г. З. Зайцев.
Отжиг, вид термической обработки металлов и сплавов, главным образом сталей и чугунов, заключающийся в нагреве до определённой температуры, выдержке и последующем, обычно медленном, охлаждении. При О. осуществляются процессы возврата (отдыха металлов), рекристаллизации и гомогенизации. Цели О. — снижение твёрдости для повышения обрабатываемости, улучшение структуры и достижение большей однородности металла, снятие внутренних напряжений.
По классификации А. А. Бочвара различают 2 вида отжига. О. 1-го вида — без фазовой перекристаллизации — применяется для приведения металла в более равновесное структурное состояние: снимается наклёп, понижается твёрдость, возрастают пластичность и ударная вязкость, снимаются внутренние напряжения (в связи с процессами отдыха и рекристаллизации). О. 2-го вида осуществляется с фазовой перекристаллизацией: сталь нагревается до температуры выше критических точек, затем следует выдержка различной продолжительности и последующее сравнительно медленное охлаждение.
Полный О. заключается в нагреве стали на 30—50 С выше верхней критической точки для полного превращения структуры стали в аустенит и последующем медленном охлаждении до 500—600 С для образования феррита и перлита. Скорость охлаждения для углеродистых сталей около 50—100 С/ч. Если охлаждение ведётся на воздухе, происходит нормализация. Неполный О. заключается в нагреве до температур между нижней и верхней критической точками и последующем медленном охлаждении; чаще всего он применяется для получения структуры зернистого перлита, что приводит к снижению твёрдости и улучшению обрабатываемости резанием.
Для легированных сталей применяют изотермический О., состоящий в нагреве выше верхней критической точки, выдержке, охлаждении до температуры ниже нижней критической точки, выдержке, достаточной для полного превращения аустенита в перлит, и охлаждении до комнатной температуры. Диффузионный О. состоит в нагреве до температур, значительно превосходящих критические точки, и продолжительной выдержке; используется для выравнивания неоднородностей распределения элементов по объёму изделия. Диффузионный О. приводит к достижению более однородных свойств по объёму изделия и особенно улучшению механических свойств в поперечном (по отношению к прокатке) направлении. В необходимых случаях для предотвращения обезуглероживания стали производят О. в защитных атмосферах.
Лит.: Бочвар А. А., Металловедение, 5 изд., М., 1956; Гуляев А. П., Термическая обработка стали, 2 изд., М. 1960.
Р. И. Энтин.
Отпуск металлов, вид термической обработки, заключающийся в нагреве закалённого сплава до температуры ниже нижней критической точки, выдержке и последующем охлаждении. Термин «О.» применяют главным образом к сталям. Процессы распада зафиксированного закалкой состояния других сплавов чаще называют старением (см. Старение металлов). Основное назначение О.— достижение необходимых свойств стали, в особенности оптимального сочетания прочности, пластичности и ударной вязкости. С повышением температуры свойства стали изменяются постепенно, однако наблюдаются сравнительно узкие интервалы температур резкого их изменения. В соответствии с этими интервалами различают первое (100—150° С), второе (250—300° С) и третье (325—400° С) превращения. При первом происходит уменьшение, при втором — увеличение, при третьем — значительное уменьшение объёма металла.
Большую роль в выяснении сущности процессов О. сыграли рентгеноструктурные исследования Г. В. Курдюмова, показавшие, что первое и третье превращения связаны с распадом мартенсита, а второе — остаточного аустенита. Распад мартенсита в процессе О. при 100—150° С имеет двухфазный характер; наряду с твёрдым раствором исходной концентрации появляется раствор, содержащий 0,25—0,3% углерода. При О. в интервале температур до 200—300° С из твёрдого раствора выделяется низкотемпературный карбид железа, а при более высоких температурах — цементит. Традиционная классификация превращений при О. имеет относительную ценность. В низкоуглеродистых сталях (до 0,2% углерода) отсутствует первое превращение. Легирование Cr, Mo, W, V, Со, Si сдвигает второе превращение при О. к более высоким температурам. В сталях, легированных Mo, W, V, при О. в интервале температур 450—550° С наблюдается выделение частиц карбидов этих элементов в дисперсной форме, что вызывает так называемое вторичное твердение. В конечном счёте высокий О. приводит к превращению структуры стали в феррито-карбидную смесь.
Процессы, происходящие в закалённой стали при вылёживании и нагреве, на основании современных экспериментальных данных представляются следующим образом: перераспределение атомов углерода в мартенсите — сток некоторой части атомов углерода к дислокациям и к границам мартенситных кристаллов, перемещения их в порах кристаллической решётки; распад мартенсита с образованием выделений той или иной карбидной фазы в зависимости от температуры О., легирования, реальной структуры кристаллов мартенсита; релаксация внутренних микронапряжений в результате микропластической деформации; превращения остаточного аустенита в зависимости от легирования и температурного интервала — бейнитное и перлитное; превращение остаточного аустенита при охлаждении после О. (вторичная закалка).
С повышением температуры О. твёрдость и прочность понижаются, пластичность и ударная вязкость повышаются; понижается критическая температура хладноломкости (Ткр). При О. до 300° С повышается сопротивление малым пластическим деформациям. При О. в интервалах температур 300—400° С и 500—600° С, особенно в легированных сталях, наблюдается падение ударной вязкости и повышение Ткр — явления необратимой и обратимой отпускной хрупкости. Быстрое охлаждение после О. при 600—650° С и легирование Mo, W подавляют обратимую хрупкость. Низкий О. (120—250° С) главным образом уменьшает склонность к хрупкому разрушению и используется при термообработке инструментальных, цементуемых и высокопрочных конструкционных сталей, О. при 300—400° С применяется при термообработке пружин и рессор, высокий О. (450—650° С) — при термообработке деталей машин, испытывающих динамические и вибрационные нагрузки.
Лит.: Курдюмов Г. В., Явления закалки и отпуска стали, М., 1960; его же, О кристаллической структуре закаленной стали, в сборнике: Проблемы металловедения и физики металлов, сб. 9, М., 1968; Гуляев А. П., Термическая обработка стали, 2 изд., М., 1960.
Р. И. Энтин.
Аустенит, одна из структурных составляющих железоуглеродистых сплавов, твёрдый раствор углерода (до 2%)и легирующих элементов в железе (см. Железо). А. получил название по имени английского учёного У. Робертса-Остена (W. Roberts-Austen, 1843—1902). Кристаллическая решётка — куб с центрированными гранями. А. немагнитен, плотность его больше, чем других структурных составляющих стали. В углеродистых сталях и чугунах А. устойчив выше 723°C. В процессе охлаждения стали А. превращается в другие структурные составляющие. В железоуглеродистых сплавах, содержащих никель, марганец, хром в значительных количествах, А. может полностью сохраниться после охлаждения до комнатной температуры (например, нержавеющие хромоникелевые стали). В зависимости от состава стали и условий охлаждения А. может сохраниться частично в углеродистых или легированных сталях (т. н. остаточный А.).
Учение о превращениях А. берёт начало с открытий Д. К. Чернова (1868), впервые указавшего на их связь с критическими точками стали. При охлаждении ниже этих точек образуются фазы с иным взаимным расположением атомов в кристаллической решётке и, в некоторых случаях, с измененным химическим составом. Различают три области превращений А. В верхнем районе температур (723—550°С) А. распадается с образованием перлита — эвтектоидной смеси, состоящей из перемежающихся пластин феррита (массовая концентрация углерода 0,02%) и цементита (концентрация углерода 6,7%). Перлитное превращение начинается после некоторой выдержки и при достаточном времени завершается полным распадом А. Ниже определенной температуры (Мн), зависящей от содержания углерода (для стали с 0,8% углерода около 240°C), происходит мартенситное превращение А. (см. Мартенсит). Оно состоит в закономерной перестройке кристаллической решётки, при которой атомы не обмениваются местами. В интервале температур 550°С — Мн происходит промежуточное (бейнитное) превращение А. Это превращение, как и перлитное, начинается после инкубационного периода и может быть подавлено быстрым охлаждением; оно, как и мартенситное, прекращается при постоянной температуре (некоторая часть А. сохраняется непревращённой) и сопровождается образованием характерного рельефа на поверхности шлифа. При промежуточном превращении упорядоченные перемещения металлических атомов сочетаются с диффузионным перераспределением атомов углерода в А. В результате образуется феррито-цементитная смесь, а часто и остаточный А. с измененным по сравнению со средним содержанием углерода. Цементит при промежуточном превращении может выделяться как из А. непосредственно, так и из пересыщенного углеродом феррита (см. Бейнит).
Превращение А. в сплавах с содержанием углерода св. 2%, в связи с наличием первичных образований цементита или графита, вызывает своеобразие получающихся структур (см. Чугун). Представление о кинетике превращений А. дают диаграммы, указывающие долю превратившегося А. в координатах температура — время. На диаграмме превращений легиров. А. четко разделены области перлитного (640—520°C) и промежуточного (480—300°C) превращений и имеется температурная зона высокой устойчивости А. (рис.). При перлитном превращении легированного А. во многих случаях образуется смесь феррита и специальных карбидов.
Легирующие элементы, за исключением кобальта, увеличивают продолжительность инкубационного периода перлитного превращения.
Закономерности превращений А. используют при разработке легированных сталей различного назначения процессов термической и термомехалической обработки. Диаграммы превращений А. позволяют устанавливать режимы отжига сталей, охлаждения изделий, изотермической закалки и т. д.
Лит.: Курдюмов Г. В., Явления закалки и отпуска стали, М., 1960; Энтин Р. И., Превращения аустенита в стали, М., 1960.
Р. И. Энтин.

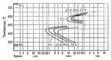
Диаграмма изотермического превращения аустенита стали, содержащей 0,4% углерода, 2% марганца и 0,1% ванадия.
Мартенсит, структура кристаллических твёрдых тел, возникающая в результате сдвигового бездиффузионного полиморфного превращения при охлаждении (см. Мартенситное превращение). Назван по имени немецкого металловеда А. Мартенса (A. Martens; 1850—1914). В результате деформации решётки при этом превращении (так называемого кооперативного сдвига) на поверхности металла появляется рельеф; в объёме же возникают внутренние напряжения и происходит пластическая деформация, которые и ограничивают рост кристалла. Скорость роста достигает 103 м/сек и не зависит от температуры, поэтому скорость образования М. обычно лимитирует зарождение кристаллов. Противодействие внутренних напряжений смещает зарождение кристаллов много ниже точки термодинамического равновесия фаз и может остановить превращение при постоянной температуре; в связи с этим количество возникшего М. обычно растет с увеличением переохлаждения. Поскольку упругая энергия должна быть минимальной, кристаллы М. принимают форму пластин (на шлифе — иголок), правильно ориентированных относительно исходной решётки. Внутренние напряжения снимаются также пластической деформацией, поэтому кристалл содержит много дислокаций (до 1012 см-2) либо разбит на двойники толщиной 10—100 нм (100—1000

М. в стали — пересыщенный раствор Fe—C, получающийся при закалке из аустенита. Упорядоченное размещение атомов углерода (в результате мартенситного сдвига) превращает объёмноцентрированную решётку -железа из кубической в тетрагональную. Её искажения около внедрённых атомов вызывают упрочнение. Тетрагональность и упрочнение растут с концентрацией углерода (твёрдость — до 1000 HV). Углеродистый М. — основная структурная составляющая большинства высокопрочных сталей. Концентрация углерода в твёрдом растворе и субзёренная структура М. изменяются при отпуске, используемом для повышения пластичности стали. Углерод — важнейший фактор прочности М. в стали; прочность безуглеродистой мартенситно-стареющей стали обусловлена выделениями интерметаллидов при старении (см. Старение металлов). Физическая природа М. Fe—С как раствора внедрения, происхождение его высокой прочности, сущность механизма и закономерности кинетики образования М. установлены Г. В. Курдюмовым.
Лит. см. при статье Мартенситное превращение.
М. А. Штремель.