Проектирование режущего инструмента
Оглавление.
1. Задание - 3.
2. Расчет фасонного резца - 4.
2.1 Расчет диаметра заготовки.
2.2 Расчет координат зловых и промежуточных точек фасонного профиля резца - 6.
3. Технология изготовления детали на шести шпиндельном токарном автомате модели 1265-6 - 8.
4. становка фасонного резца на станке - 10.
4.1 Спецификация - 11.
5. Проектирование спирального сверла - 12.
6. Проектирования зенкера - 14.
7. Проектирование зенковки - 16.
8. Проектирования развёртки - 16.
9. Проектирование резца - 18.
10. Проектирование фрез - 18.
10.1. Проектирование торцевой насадной фрезы - 19.
10.2. Проектирование концевой фрезы - 19.
10.3. Проектирование дисковой трёхсторонней фрезы - 20.
11. Литературные источники - 21.
Рассчитать размер фасонного профиля и конструктивные размеры резца для обработки детали №79168 в словиях массового производства. Сталь А12, HB 207, проектирование режущего инструмента.
2. Расчет фасонного резца.
Деталь изготавливаем из сортового проката круглого поперечного сечения по ГОСТ 2590-71.
2.1 Расчет диаметра заготовки.
dзаг = dдет max+2zmin ,
где dзаг - диаметр заготовки; dдет max - максимальный диаметр обрабатываемой детали; zmin - минимальный припуск на обработку.
Расчет минимального припуска на обработку.
2Zmin=2[(Rz+h)i-1+Ö D2åi-1+2i],
Расчет слагаемых входящих в формулу минимального припуска.
Качество поверхности сортового проката.
Rz = 160 мкм
h = 250 мкм
Суммарное отклонение расположения поверхности:
Då=Ö D2åк+D2ц,
где Dåк Ц общее отклонение оси от прямолинейности; Dц Ц смещение оси заготовки в результате погрешности центрирования (стр.41 таб.12)
Dåк= а
D2к+0.25
где Dк Цкривизна профиля сортового проката (1, стр.180, таб.4) Dк= 0.5 мкм;
Dåк = 60(0.5/0.5) = 60 мкм
Dц = 20 мкм,
Då = 63,2 мкм.
Погрешность становки заготовки (1, стр.42, таб.13):
e<=280 мкм;
тогда min припуск на обработку равен:
2zmin = 2[(Rz+h)i-1+ÖD2åi-1+
тогда диаметр заготовки равен:
dзаг=40+1.39=41.39 мм.
В качестве заготовки выбираем сортовой прокат диаметром 42мм по (1, стр.69 таб.62) ГОСТ 2590-71.
Обоснование типа фасонного резца.
Выбираю призматический резец с базовой точкой на высоте линии центров, так как на обрабатываемой детали есть протяженная сферическая поверхность.
Призматический радиальный резец с базовой точкой на линии центров имеет меньшую погрешность по сравнению с круглыми резцами.
Обоснование выбора материала режущей части и корпуса фасонного резца (2, стр.115 таб.2).
При обработке сталей экономически выгодно использовать резцы из следующих марок быстрорежущих сталей Р18, РМФ3, РМ5, РК10, Р1КФ5 и т.д. Выбираем марку быстрорежущей стали, РМ5. Для экономии быстрорежущей стали, резец делаем составным неразъемным, сваренным, с помощью контактной сварки оплавлением. Крепежную часть призматического резца изготавливают из стали - 4Х.
Обоснование выбора геометрических параметров фасонного резца.
Принимаем по таблице для стали - А12 твердостью НВ=207 (4, стр.112,113) a<=10
Расчет координат зловых и промежуточных точек фасонного профиля детали.
Определим координаты точки 3. Для этого запишем равнения окружности (l-28)2+r2=202 и равнения прямой r=18. Совместное решение этих равнений даёт координаты точки l3= 9.2822; r3=18.
Определим координаты точки 4. Они получаются из равнений окружностиа (l-28)2+r2=202 и равнения наклонной прямой (r=kl+b) r=-tg165o+27, где b=27 из равнения для точки 5: 11=60tg165о+b. Совместное решение этих равнений даёт координаты точки l4= 16.415; r4=39.191.
Возьмём вспомогательную точку на коническом частке детали для этого запишем 2 равнения прямой: r7= -tg165ol7 +27 и r4=16.415; откуда получим координаты точки 7: r7=16.415, l7=49.879.
![]() |
№точки фас. Профиля детали |
ri(y) |
li(x) |
1 |
15.0 |
0 |
2 |
18.0 |
3 |
3 |
18.0 |
19.282 |
4 |
16.415 |
39.191 |
5 |
11.0 |
60 |
6 |
20.0 |
28 |
7 |
13.634 |
49.879 |
2.2 Расчет координат зловых и промежуточных точек фасонного профиля резца.
а
M5=r5*Sin5=11sin23 A5=r5*Cos5=11cos23<<=10.126;
Sini=M5/ri;
Ei=ri*Cosi;
Ci=Ei-A5;
sin1=M5/r1=4.298/15.0=0.287
Þ 1=16.651 E1=r1*Cos1=15.0cos16.651 C1=E1-A5=14.371-10.126=4.245.
1
2
3
4
5
6
7
Ri
15
18
18
16.415
11
20
13.634
gi
16.651
13.814
13.814
15.178
23
12.409
18.376
Ei
14.371
17.479
17.479
15.842
10.126
19.533
12.939
Ci
4.245
7.353
7.353
5.716
0
9.407
2.813
Hi
3.560
6.167
6.167
4.795
0
7.889
2.359
Значения Hi находим из треугольников
рис. 6
4. становка фасонного резца на станок.
Фасонные резцы для обработки наружных поверхностей с радиальным направлением подачи станавливают в специальных державках на поперечных суппортах станков.
Конструкция державки должна обеспечивать возможность смены и регулеровки резца и минимально допустимый вылет прутка из зажимной цанги.
На листе 1 данного курсового проекта показана державка призматического резца для позиций 2 и 5 шести шпиндельного автомата 1265 - 6.
Регулировка размера 65+/-0.02 осуществляется при помощи ослабления винтов 15 и регулировки вылета резца винтом 16, затем затягиванием винтами 15.
Осевая регулировка резца осуществляется следующим образом: отпускаются крепёжные винты 12 и 13, винтом 7 регулируется осевой размер, и затем затягиваются крепёжные винты.
При регулировки резца в радиальном направлении отпускаются крепёжные винты 12, положение опоры фиксируется винтом 13. Для более точной регулировки предусмотрен винт 6 (см. спецификацию).
Фасонные резцы для обработки наружных поверхностей с радиальным направлением подачи станавливают в специальных державках на поперечных суппортах станков.
Конструкция державки должна обеспечивать возможность смены и регулировки резца и минимально допустимый вылет прутка из зажимной цанги.
5.
Проектирование спирального сверла.
Обоснование использования инструмента.
Спиральное сверло Æ12 предназначено для сверления глухого отверстия диаметра
12 мм на глубину 65мм в заготовке детали №79168.
Обоснование выбора материала режущей и хвостовой части сверла.
Для экономии быстрорежущей стали все сверла с цилиндрическим хвостовиком диаметром более 8
мм и сверла с коническим хвостовиком более 6 мм изготовляются сварными.
В основном, сверла делают из быстрорежущих сталей. Твердосплавные сверла делают для обработке конструкционных сталей высокой твердости (45...56HRC), обработке чугуна и пластмасс. Исходя из твердости обрабатываемого материала - 207 НВ, принимаем решение об изготовлении сверла из быстрорежущей стали РМ5 ГОСТ 19265-73.
Крепежную часть сверла изготовим из стали 4Х (ГОСТ 454-74).
Обоснование выбора геометрических параметров сверла.
Задний гол .= 8
Передний гол. Также является величиной переменной вдоль режущего лезвия и зависит, кроме того, от гла наклона винтовых канавок
Угол при вершине сверла. Значение глов 2Угол наклона винтовых канавок. гол наклона винтовых канавок определяет жесткость сверла, величину переднего угла, свободу выхода стружки и др. Он выбирается в зависимости от обрабатываемого материала и диаметра сверла. По (6,табл.5) назначаем Угол наклона поперечной кромки. При одном и том же гле Расчет, назначение конструктивных размеров сверла.
Спиральные сверла одного и того же диаметра в зависимости от серии бывают различной длины. Длина сверла характеризуется его серией. В связи с тем, что длина рабочей части сверла определяет его стойкость,
жесткость, прочность и виброустойчивость, желательно во всех случаях выбирать сверло минимальной длины. Серия сверла должна быть выбрана таким образом, чтобы
lо ГОСТ ≥ lо расч.
Расчетная длина рабочей части сверла lо ,
равна расстоянию от вершины сверла до конца стружечной канавки, может быть определена по формуле:
lо = lр
+ lвых + lд + lв + lп + lк
+ lф,
агде
lр - длина режущей части сверла lр
= 0.3*dсв = 0.3*12 = 3.6 мм;
lвых - величина выхода сверла из отверстия lвых = 0 (т.к. отверстие глухое);
lд - толщина детали или глубина сверления, если отверстие глухое lд = 65 мм;
lв - толщина кондукторной втулки lв
= 0 ;
lп - запас на переточку lп = D l * (i +1), где
D l - величина, срезаемая за одну переточку,
измеренная в направлении оси, D l = 1 мм.;
i - число переточек i = 40;
lп = 1*(40+1) =
41 мм;
lк - величина,
характеризующая величение длины сверла для возможности свободного выхода стружки при полностью сточенном сверле;
lф - величина, характеризующая меньшение глубины канавки, полученной при работе канавочной фрезы
lк + lф
= 1.5*dсв = 1.5*12 = 18 мм,
тогда
l0 = 3.6 + 0 +65
+ 0 + 41 + 18 = 127.6 мм.
В соответствии с ГОСТ
12121-77 (" Сверла спиральные из быстрорежущей стали с коническим хвостовиком ") точняем значения l0 и общей длины L :
l0 ГОСТ = 140 мм;
L = 220 мм.
Положение сварного шва на сверле : lс = l0 + (2...3) = 143 мм.
Диаметр сердцевины сверла dс
выбирается в зависимости от диаметра сверла и инструментального материала (6,
стр.12):
dс = 0.15*dсв
= 0.15 * 12 = 1.8 мм.
Ширина ленточки fл
= (0.45...0.32)*sqrt(dс) = 0.7 мм.
Высот ленточки hл
= (0.05...0.025)*dс = 0.4 мм.
Хвостовик сверла выполняется коническим - конус Морзе №1 АТ8 ГОСТ 2848 - 75 (6, табл.2 и 3).
Центровые отверстия на сверлах изготовляются в соответствии с ГОСТ 14034-74 (6, рис.5).
Определение количества переточек.
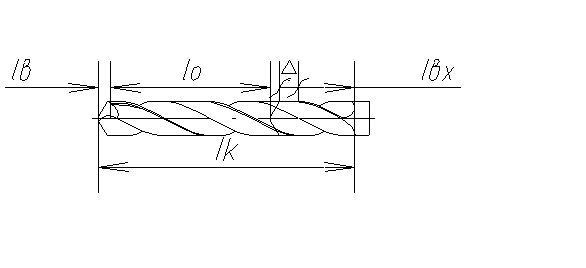
Общая длина стачивания:
lо = lk - lвых -
Δ - lр, где
lвsх Ц величина, характеризующая увеличение длины сверла для возможности свободного выхода стружки при полностью сточенном сверле;
lр Ц длина режущей части сверла lр = 0.3dсв = 0.312 = 3,6 мм;
lк Ц длина стружечной канавки;
D = 10 мм;
lо = 130-30-10-3,6=86,4 мм.
Число переточек: n = lo/D
D
6. Проектирования зенкера.
Обоснование использования инструмента.
Зенкер предназначен для обработки отверстия в литых деталях или штампованных деталей, также предварительно просверленных отверстий с целью повышения точности и величения шероховатости поверхности отверстия. В техническом процессе зенкер, как правило, выполняет промежуточную операцию между сверлением и развёртыванием.
Зенкерованием получают отверстие точностью Н11 с шероховатостью до Rz=2,5мкм.
Зенкерованием можно исправить искривление оси отверстия.
Обоснование выбора материала режущей части резца.
В металлообработке используется большое количество различных типов зенкеров. Рассмотри зенкер из быстрорежущей стали, с коническим хвостовиком,
диаметр D=17.9мм, ГОСТ12489-71, тип зенкера №1 (7, Табл.2).
Выбора материала режущей части и хвостовика зенкера (2, стр.115 таб.2),
при обработке сталей, экономически выгодно использовать зенкер из следующих марок быстрорежущих сталей Р18, РМФ3, РМ5, РК10, Р1КФ5 и т.д. Выбираем марку быстрорежущей стали РМ5, ГОСТ 19256-73. Для экономии быстрорежущей стали, зенкер делаем составным неразъемным, сваренным, с помощью контактной сварки оплавлением. Хвостовик изготавливают из стали 4Х ГОСТ 454-74.
Геометрические параметры режущей части.
Задний гол 1 <= 8o, что обуславливает неблагоприятные условия резанья для вспомогательной режущей кромки.
Передний гол
Главный гол в плане o.
Угол наклона канавок o
Угол наклона главной режущей кромки Расчет, назначение конструктивных размеров зенкера.
Конструкция зенкера имеет много общего с конструкцией сверла, особенно это, относится к зенкерам типа 1, 3. Более высокая жёсткость конструкции,
увеличение по сравнению со сверлом числа зубьев и соответственно центрующих ленточек обеспечивают лучшее направление зенкера в процессе работы и более высокое качество обработанной поверхности.
Количество зубьев зенкера Z зависит от типа зенкера и его диаметра, в данном случае Z=3 (7, Табл. 3).
Хвостовые зенкеры изготавливаются сварными, положение сварного шва задаётся размером lc=60мм. Хвостовик для зенкеров типа 1, 3 и 6
состоит из конической базовой поверхности, служащей для центрирования зенкера и передачи крутящего момента, и лапки. Лапка предохраняет хвостовик зенкера от проворачивания в шпинделе станка в случае, когда момент сил трения на конической поверхности оказываются меньше сил резанья. Такая ситуация возникает при врезание зенкера в заготовку.
Хвостовик выполнен в форме конуса Морзе №2 (7, Табл.5), его размер выбирается по АТ8 ГОСТ 2848-75.
Для изготовления последующих переточек хвостовой зенкер снабжён центровым отверстием формы В по ГОСТ 14034-75.
Допуск на изготовление конических базовых поверхностей зенкера выбираются по ГОСТ 2848-75.
Исполнительный размер диаметра зенкера D станавливается с ГОСТ
12509-75. Предельные отклонения для D=17,9мм: верхнее - -0,210, нижнее - -0,237
(7, Табл.6).
Допуск на диаметр зенкера рассчитывается из словия обработки отверстия по одиннадцатому квалитету.
D=d0+T0-P,
где
D - диаметр зенкера;
d0 Ц номинальный диаметр отверстия;
T0 Ц допуск изготовление отверстия;
Р - разбивка отверстия;
Tз Ц допуск на изготовление зенкера.
Длина стружечной канавки:
lк = l1 +
l2 + l3 + l4 + l5, где
l1- допустимое стачивание l1 = D
где D1
= 1.3 * 45 = 58.5 мм;
l2 - выход зенкера из обрабатываемого отверстия l2 = 3 мм (7,стр.8);
l3 - длина отверстия l3 = 40 мм;
l4 - длина кондукторной втулки l4 = 0;
l5 - минимально допустимая длина канавки для свободного выхода стружки (7,стр.8)
l5 = 1.5 * d =
1.5 * 20 = 30 мм;
lк = 58.5 + 3 +
40 + 30 = 131.5 мм.
Уточняем lк по ГОСТ 12489-71: lк = lк ГОСТ = 80 мм, общая длина сверла
L = 174мм.
Положение места сварки lс
= 60мм.
Профиль стружечных канавок. Форма и размеры стружечных канавок зенкеров должны, с одной стороны, обеспечивать размещение и свободный отвод стружки, с другой, - достаточную жесткость зенкеров. Кроме того, форма и расположение стружечной канавки, определяют форму передней поверхности и значение переднего гла. При выборе стружечной канавки необходимо учитывать ее технологичность.
По рекомендациям (7, стр.24-25) выбираем трех радиусную форму канавки. Этот профиль обеспечивает благоприятные словия для образования и завивания стружки, он также достаточно технологичен.
7. Проектирование зенковки.
Одной из разновидностей операции зенкерования является операция образования цилиндрических ступенчатых,
конических и торцевых поверхностей, выполняемых специальным осевым инструментом - зенковками.
Зенковка коническая предназначена для изготовления фаски 2х45
Обоснование выбора геометрических параметров зенковки.
M5=r5*Sin Ei=ri*Cos Ci=Ei-A5; sin E1=r1*Cos C1=E1-A5=14.371-10.126=4.245. 2 3 4 5 6 7 Ri 15 18 18 16.415 11 20 13.634 gi 16.651 13.814 13.814 15.178 23 12.409 18.376 14.371 17.479 17.479 15.842 10.126 19.533 12.939 Ci 4.245 7.353 7.353 5.716 0 9.407 2.813 Hi 3.560 6.167 6.167 4.795 0 7.889 2.359 Значения Hi находим из треугольников рис. 6 4. становка фасонного резца на станок. Фасонные резцы для обработки наружных поверхностей с радиальным направлением подачи станавливают в специальных державках на поперечных суппортах станков. Конструкция державки должна обеспечивать возможность смены и регулеровки резца и минимально допустимый вылет прутка из зажимной цанги. На листе 1 данного курсового проекта показана державка призматического резца для позиций 2 и 5 шести шпиндельного автомата 1265 - 6. Регулировка размера 65+/-0.02 осуществляется при помощи ослабления винтов 15 и регулировки вылета резца винтом 16, затем затягиванием винтами 15. Осевая регулировка резца осуществляется следующим образом: отпускаются крепёжные винты 12 и 13, винтом 7 регулируется осевой размер, и затем затягиваются крепёжные винты. При регулировки резца в радиальном направлении отпускаются крепёжные винты 12, положение опоры фиксируется винтом 13. Для более точной регулировки предусмотрен винт 6 (см. спецификацию). Фасонные резцы для обработки наружных поверхностей с радиальным направлением подачи станавливают в специальных державках на поперечных суппортах станков. Конструкция державки должна обеспечивать возможность смены и регулировки резца и минимально допустимый вылет прутка из зажимной цанги. 5.
Проектирование спирального сверла. Обоснование использования инструмента. Спиральное сверло Æ12 предназначено для сверления глухого отверстия диаметра
12 мм на глубину 65мм в заготовке детали №79168. Обоснование выбора материала режущей и хвостовой части сверла. Для экономии быстрорежущей стали все сверла с цилиндрическим хвостовиком диаметром более 8
мм и сверла с коническим хвостовиком более 6 мм изготовляются сварными. В основном, сверла делают из быстрорежущих сталей. Твердосплавные сверла делают для обработке конструкционных сталей высокой твердости (45...56HRC), обработке чугуна и пластмасс. Исходя из твердости обрабатываемого материала - 207 НВ, принимаем решение об изготовлении сверла из быстрорежущей стали РМ5 ГОСТ 19265-73.
Крепежную часть сверла изготовим из стали 4Х (ГОСТ 454-74). Обоснование выбора геометрических параметров сверла. Задний гол Передний гол. Также является величиной переменной вдоль режущего лезвия и зависит, кроме того, от гла наклона винтовых канавок Угол при вершине сверла. Значение глов 2 Спиральные сверла одного и того же диаметра в зависимости от серии бывают различной длины. Длина сверла характеризуется его серией. В связи с тем, что длина рабочей части сверла определяет его стойкость,
жесткость, прочность и виброустойчивость, желательно во всех случаях выбирать сверло минимальной длины. Серия сверла должна быть выбрана таким образом, чтобы
lо ГОСТ ≥ lо расч. Расчетная длина рабочей части сверла lо ,
равна расстоянию от вершины сверла до конца стружечной канавки, может быть определена по формуле: lо = lр
+ lвых + lд + lв + lп + lк
+ lф, агде lр - длина режущей части сверла lр
= 0.3*dсв = 0.3*12 = 3.6 мм; lвых - величина выхода сверла из отверстия lвых = 0 (т.к. отверстие глухое); lд - толщина детали или глубина сверления, если отверстие глухое lд = 65 мм; lв - толщина кондукторной втулки lв
= 0 ; lп - запас на переточку lп = D l * (i +1), где D l - величина, срезаемая за одну переточку,
измеренная в направлении оси, D l = 1 мм.; i - число переточек i = 40; lп = 1*(40+1) =
41 мм; lк - величина,
характеризующая величение длины сверла для возможности свободного выхода стружки при полностью сточенном сверле; lф - величина, характеризующая меньшение глубины канавки, полученной при работе канавочной фрезы lк + lф
= 1.5*dсв = 1.5*12 = 18 мм, тогда l0 = 3.6 + 0 +65
+ 0 + 41 + 18 = 127.6 мм. В соответствии с ГОСТ
12121-77 (" Сверла спиральные из быстрорежущей стали с коническим хвостовиком ") точняем значения l0 и общей длины L : l0 ГОСТ = 140 мм;
L = 220 мм. Положение сварного шва на сверле : lс = l0 + (2...3) = 143 мм. Диаметр сердцевины сверла dс
выбирается в зависимости от диаметра сверла и инструментального материала (6,
стр.12): dс = 0.15*dсв
= 0.15 * 12 = 1.8 мм. Ширина ленточки fл
= (0.45...0.32)*sqrt(dс) = 0.7 мм. Высот ленточки hл
= (0.05...0.025)*dс = 0.4 мм. Хвостовик сверла выполняется коническим - конус Морзе №1 АТ8 ГОСТ 2848 - 75 (6, табл.2 и 3). Центровые отверстия на сверлах изготовляются в соответствии с ГОСТ 14034-74 (6, рис.5). Определение количества переточек.
Общая длина стачивания: lо = lk - lвых -
Δ - lр, где lвsх Ц величина, характеризующая увеличение длины сверла для возможности свободного выхода стружки при полностью сточенном сверле; lр Ц длина режущей части сверла lр = 0.3dсв = 0.312 = 3,6 мм; lк Ц длина стружечной канавки; D = 10 мм; lо = 130-30-10-3,6=86,4 мм. Число переточек: n = lo/D D 6. Проектирования зенкера. Обоснование использования инструмента. Зенкер предназначен для обработки отверстия в литых деталях или штампованных деталей, также предварительно просверленных отверстий с целью повышения точности и величения шероховатости поверхности отверстия. В техническом процессе зенкер, как правило, выполняет промежуточную операцию между сверлением и развёртыванием. Зенкерованием получают отверстие точностью Н11 с шероховатостью до Rz=2,5мкм.
Зенкерованием можно исправить искривление оси отверстия. Обоснование выбора материала режущей части резца. В металлообработке используется большое количество различных типов зенкеров. Рассмотри зенкер из быстрорежущей стали, с коническим хвостовиком,
диаметр D=17.9мм, ГОСТ12489-71, тип зенкера №1 (7, Табл.2). Выбора материала режущей части и хвостовика зенкера (2, стр.115 таб.2),
при обработке сталей, экономически выгодно использовать зенкер из следующих марок быстрорежущих сталей Р18, РМФ3, РМ5, РК10, Р1КФ5 и т.д. Выбираем марку быстрорежущей стали РМ5, ГОСТ 19256-73. Для экономии быстрорежущей стали, зенкер делаем составным неразъемным, сваренным, с помощью контактной сварки оплавлением. Хвостовик изготавливают из стали 4Х ГОСТ 454-74. Геометрические параметры режущей части. Задний гол 1 <= 8o, что обуславливает неблагоприятные условия резанья для вспомогательной режущей кромки. Передний гол Главный гол в плане Угол наклона канавок Угол наклона главной режущей кромки Конструкция зенкера имеет много общего с конструкцией сверла, особенно это, относится к зенкерам типа 1, 3. Более высокая жёсткость конструкции,
увеличение по сравнению со сверлом числа зубьев и соответственно центрующих ленточек обеспечивают лучшее направление зенкера в процессе работы и более высокое качество обработанной поверхности. Количество зубьев зенкера Z зависит от типа зенкера и его диаметра, в данном случае Z=3 (7, Табл. 3). Хвостовые зенкеры изготавливаются сварными, положение сварного шва задаётся размером lc=60мм. Хвостовик для зенкеров типа 1, 3 и 6
состоит из конической базовой поверхности, служащей для центрирования зенкера и передачи крутящего момента, и лапки. Лапка предохраняет хвостовик зенкера от проворачивания в шпинделе станка в случае, когда момент сил трения на конической поверхности оказываются меньше сил резанья. Такая ситуация возникает при врезание зенкера в заготовку. Хвостовик выполнен в форме конуса Морзе №2 (7, Табл.5), его размер выбирается по АТ8 ГОСТ 2848-75. Для изготовления последующих переточек хвостовой зенкер снабжён центровым отверстием формы В по ГОСТ 14034-75. Допуск на изготовление конических базовых поверхностей зенкера выбираются по ГОСТ 2848-75. Исполнительный размер диаметра зенкера D станавливается с ГОСТ
12509-75. Предельные отклонения для D=17,9мм: верхнее - -0,210, нижнее - -0,237
(7, Табл.6). D=d0+T0-P,
где D - диаметр зенкера; d0 Ц номинальный диаметр отверстия; T0 Ц допуск изготовление отверстия; Р - разбивка отверстия; Tз Ц допуск на изготовление зенкера. Длина стружечной канавки: lк = l1 +
l2 + l3 + l4 + l5, где l1- допустимое стачивание l1 = D где D l2 - выход зенкера из обрабатываемого отверстия l2 = 3 мм (7,стр.8); l3 - длина отверстия l3 = 40 мм; l4 - длина кондукторной втулки l4 = 0; l5 - минимально допустимая длина канавки для свободного выхода стружки (7,стр.8) l5 = 1.5 * d =
1.5 * 20 = 30 мм; lк = 58.5 + 3 +
40 + 30 = 131.5 мм. Уточняем lк по ГОСТ 12489-71: lк = lк ГОСТ = 80 мм, общая длина сверла
L = 174мм. Положение места сварки lс
= 60мм. Профиль стружечных канавок. Форма и размеры стружечных канавок зенкеров должны, с одной стороны, обеспечивать размещение и свободный отвод стружки, с другой, - достаточную жесткость зенкеров. Кроме того, форма и расположение стружечной канавки, определяют форму передней поверхности и значение переднего гла. При выборе стружечной канавки необходимо учитывать ее технологичность. По рекомендациям (7, стр.24-25) выбираем трех радиусную форму канавки. Этот профиль обеспечивает благоприятные словия для образования и завивания стружки, он также достаточно технологичен. 7. Проектирование зенковки. Одной из разновидностей операции зенкерования является операция образования цилиндрических ступенчатых,
конических и торцевых поверхностей, выполняемых специальным осевым инструментом - зенковками. Зенковка коническая предназначена для изготовления фаски 2х45
Обоснование выбора геометрических параметров зенковки.A5=r5*Cos
Sin
1
Ei
Допуск на диаметр зенкера рассчитывается из словия обработки отверстия по одиннадцатому квалитету.