Расчет и проектирование одноступенчатого, цилиндрического, шевронного редуктора общего назначения
Пинский государственный индустриально-
педагогический колледж
Пояснительная записка
по предмету: Техническая механика
Тема: Рассчитать и спроектировать одноступенчатый, цилиндрический, шевронный аредуктор общего назначения
/p>
Выполнил: Лепесевич Антон
Проверила: Цинкель Т.Н.
Пинск 2005
3 |

1 |

2 |






























м а |




















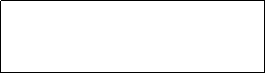
Позиция |
Элемент схемы |
Исходные данные |
Значение |
1 |
Цилиндрический редуктор |
Мощность,квт |
1,8 |
2 |
Клиноременная передача |
Частота вращения, п об/мин |
120 |
3 |
Двигатель |
АМ90LУ3 |
|
Содержание:
1. Введени......стр 2
2. Выбор электродвигателя. Кинематический расчет приводЕстр(3 -5)
3. Выбор материала зубчатой передачи. Определение допускаемых напряжений....стр(6 - 9)
4. Расчёт закрытой цилиндрической зубчатой передачистр(10 - 14)
5. Проектный расчет валов редуктора..стр(15 Ц 19)
6.Определение реакций в подшипниках. Построение эпюр изгибающих и крутящих моментов...стр(20 - 24)
7. Проверочный расчет подшипников..стр(25 Ц 27)
8. Конструктивная компоновка привода..стр(28 Ц 30)
9. Смазывани...стр 31
10. Проверочный расчет шпонокстр 32
11. Технический уровень редуктора...стр 33
12. Список литературыстр 34
1. Введение
Редуктором называется механизм, понижающий гловую скорость и величивающий вращающий момент в приводах от электродвигателя к рабочей машине.
Редуктор состоит из зубчатых или червячных передач, становленных в отдельном герметичном корпусе, что принципиально отличает его от зубчатой или червячной передачи, встраиваемой в исполнительный механизм или машину.
Редукторы широко применяют в различных отраслях машиностроения, поэтому число разновидностей их велико.
Редукторы применяют также и в других отраслях промышленности.
Редукторы определяются составом передач, порядком их размещения в направлении от быстроходного вала к тихоходному валу и положением осей валов в пространстве.
Типоразмер редуктора определяется типом и главным параметром тихоходной ступени.
Исполнение редуктора определяется передаточным числом, вариантом сборки и формой концевых частков вала.
Основная энергетическая характеристика редуктора - номинальный вращающий момент Т на его тихоходном валу при постоянной нагрузке.
Цилиндрические редукторы благодаря широкому диапазону передаваемых мощностей, долговечности, простоте изготовления и обслуживания получили широкое распространение в машиностроении.
2. Выбор электродвигателя. Кинематический расчет привода.
2.1 Определяем общий КПД привода:
ηобщ = ηрп * ηпк² * ηзп
где ηрп - коэффициент полезного действия клиноременной передачи;
ηрп <= 0,9Е0,97 (табл. 2.2, стр.41 [1]);
принимаем ηрп <= 0,97;
ηзп - коэффициент полезного действия закрытой зубчатой
цилиндрической шевронной передачи;
ηзп = 0,9Е0,97(табл. 2.2, стр.40 [1]);
принимаем ηзп = 0,96;
ηпк - коэффициент полезного действия подшипников качения;
ηпк = 0,9Е0,995 (табл. 3, стр.41 [1]);
принимаем ηпк = 0,98;
ηобщ = 0,97*0,96*0,98² = 0,894
2.2 Определяем требуемую мощность рабочей машины.
Ррм <= Р3 <= 1,8 квт
2.3 Определяем требуемую мощность двигателя Рдв., квт:
Рдв = Ррма ηобщ <= 1,8 / 0,894 = 2,013 квт
2.4 Определяем номинальную мощность двигателя Рном., квт:
Рном ≥ Рдв а
Из таблицы 2.1 стр. 39 [1] выбираем тип двигателя
1. АМ8ВУ3 (п = 2850 об/мин.) Рном = 2,2 квт;
2. АМ90LУ3 (п = 1425 об/мин.) Рном = 2,2 квт;
3. АМ100LУ3 (п = 950 об/мин.) Рном = 2,2 квт;
4. аАМ11МАУ3 (п = 700 об/мин.) Рном = 2,2 квт;
Т.к. двигатели с большой частотой вращения имеют низкий рабочий ресурс, двигатели с низкими частотами весьма металлоемки, поэтому их нежелательно применять без особой необходимости в приводах общего назначения малой мощности.
Следовательно в данной ситуации подходит трехфазный асинхронный двигатель серии А типа 90L: АМ90LУ3
Характеристики двигателя следующие:
Рном = 2,2 квт; пном = 1425 об/мин. (табл. к9, стр. 384 [1])
2.5 Определяем передаточные числа привода и его ступеней. Передаточное число привода определяется отношением номинальной частоты вращения двигателя пнома к частоте вращения приводного вала рабочей машины прм (п3) при номинальной нагрузке.
U = пном / прма
1.U = 2850 / 120 = 23,75
2.U <= 1425 / 120 = 11,875
3.U = 950 / 120 = 7,916
4.U = 700 / 120 = 5,833
Общее передаточное число U: аU = Uрп * Uзп
где Uрп - передаточное число ременной передачи, которое должно быть ва пределах Е4 (табл. 2.3, стр. 43 [1]);
Uзп - передаточное число зубчатой передачи.
Приняв передаточное число зубчатой передачи за 4 (табл. 2.3, стр. 43 [1]) получим передаточное число ременной передачи: Uрп <= U Uзп
1.Uрп <= 23,75 / 4 = 5,937
2.Uрп <= 11,875 / 4 = 2,968
3.Uрп <= 7,916 / 4 = 1,979
4.Uрп <= 5,833 / 4 = 1,458
2.6 Определяем мощность каждой ступени:
РI а<= Рраб.м = 2,013 квт
РII = РI * ηрп = 2,013 * 0,97 = 1,952 квт
Р< <= РII * ηпк² * ηзп <= 1,952 * 0,98² * 0,96 = 1,799 квт
2.7 Определяем гловые скорости на каждой ступени привода:
nI = пдв = 1425 об/мин.
nII = n< <= 2.8 Определяем моменты ступеней привода. ТI <= wI = wII = w< = ТI = ТII <= Т < = тая теля машины Быстро- ходный Тихо- ходный Точное число, U 4 2,968 Расчетная мощность,
2,013 1,952 1,799 1,799 Угловая скорость,
w 149,15 50,252 12,563 12,563 η 0,96 0,97 Частота вращения, 1425 480,121 120,03 12,03 Вращающийся момент, Т 13,496 38,844 143,198 143,198 3. Выбор материала зубчатой передачи.
Определение допускаемых напряжений. Поскольку, в проектном задании к редуктору не предъявляется жёстких требований в отношении габаритов передачи, изготовление колёс осуществляется в словиях мелкосерийного производства, то выбираем материалы со средними механическими качествами. В проектном задании казано, что редуктор должен быть общего назначения, кроме того передаваемая мощность невелика (1,8 квт). Для таких редукторов экономически целесообразно применять колёса с твёрдостью ≤ 350 НВ, при этом достигается лучшая прирабатываемость зубьев колеса, обеспечивается чистовое нарезание зубьев колёс после термообработки, высокая точность их изготовления. учитывая, что число нагружений в единицу времени зубьев шестерни в передаточное число раз (2,5) больше нагружений зубьев колеса, для достижения одинаковой контактной сталости обеспечиваем механические характеристики материала шестерни выше, чем материала колеса. Для равномерного изнашивания зубьев и лучшей их прирабатываемости твердость шестерни НВ1 назначаем больше твёрдости колеса НВ2
(стр. 48 [1]);
НВ1-НВ2=2Е50 Мощность на рабочем валу Р< = 1,8 квт; передаточное число редуктора аUзп =4; частота вращения рабочего вала передача нереверсивная. 3.1.Пользуясь таблицей
3.2, стр.50 [1], подбираем подходящий материал. Сталь 45, которой присущи следующие характеристики: Dпред. - любой; Sпред. - любая; Твёрдость заготовки
17Е207 НВ; Gв = 600 Н/мм²; Gт = 320 Н/мм²; G<-1 = 260 Н/мм²; Данный материал подходит для изготовления колеса редуктора, в качестве термообработки используют нормализацию. Сталь 45, которой присущи следующие характеристики: Dпред. =125 мм; Sпред. =80 мм; Твёрдость заготовки
33Е262 НВ; Gв = 780 Н/мм²; Gт = 540 Н/мм²; G<-1 = 335 Н/мм²; Данный материал подходит для изготовления шестерни редуктора, в качестве термообработки используют улучшение. 3.2 Допускаемые контактные напряжения при расчётах на прочность определяются отдельно для зубьев шестерни
[G<]н1 и колёса [G<]н2. Определяем коэффициент долговечности KнL : KнL = где, Nно - число циклов перемены напряжений, соответствующее пределу выносливости; N - число циклов перемены напряжений за весь срок службы. Если N> Nно , то принимаем KнL = 1 (стр. 51[1]). По таблице 3.1, стр. 49
[1] определяем допускаемое контактное напряжение [G<]но,
соответствующее пределу контактной выносливости при числе циклов перемены напряжений Nно. [G<]но <=
1,8 Вср<+67 Вср1 = (235+262)/2 = 248,5 [G<]но1 =
1,8*248,5+67 = 514,3 Н/мм² Вср2 <= (179+207)/2 = 193 [G<]но2 =
1,8*193+67 = 414,4 Н/мм² Определяем адопускаемые контактные напряжения для зубьев шестерни [G<]н1 и колеса [G<]н2 (стр. 51 [1]): [G<]н1 = KнL1*[G<]но1 = 1*514,3 Н/мм² [G<]н2 = KнL2*[G<]но2 = 1*414,4 Н/мм² Среднее допускаемое контактное напряжение (стр. 51 [1]): [G<]н =
0,45* ( [G<]н1<+[G<]н2 ) =
0,45* (514,3+414,4) = 0,45*928,7 = 418 Н/мм² 3.3 Определяю допускаемое напряжение изгиба [G<]F. Проверочный расчёт зубчатых передач на изгиб выполняется отдельно для зубьев шестерни и колеса по допускаемым напряжениям изгиба [G<]F1 и [G<]F2. Определяю коэффициент долговечности (стр. 52, [1]): KнL где, NFO = 4*10 N - число циклов перемены напряжений за весь срок службы. Т.к. N> NFOа
(стр. 52, [1]),
то принимаем КFL = 1. Допускаемое напряжение изгиба [G<]F0, соответствующее пределу изгибной выносливости при числе циклов перемены напряжений NFO. [G<]F0 = 1,03 Вср (табл. 3.1,
стр. 49 [1]) Вср1 = 248,5 ; Вср2 = 193 [G<]F01 = 1,03*248,5 = 256 Н/мм² [G<]F02 = 1,03*293 = 199 Н/мм² Расчёт модуля зацепления для цилиндрических передач с прямыми и непрямыми зубьями выполняют по меньшему значению [G<]F из полученных для шестерни [G<]F1 и колеса [G<]F2, то есть по менее прочным зубьям. Составляем табличный ответ: передачи стали Sпред, мм; работка НRCэ1ср НВ2ср [G<]н NF Шестерня Колесо 45 45 125 80 У Н 248,5 193 514,3 414,4 256 199 4. Расчёт закрытой цилиндрической зубчатой передачи. 4.1 Проектный расчёт. 4.1.1. Определяю главный параметр - межосевое расстояние а где к - вспомогательный коэффициент. Для шевронных передач к = 43 (стр. 58 [1]); аΨа - коэффициент ширины венца колеса, равный 0,2Е0,36 (стр.58[1]) - для шестерни,
расположенной симметрично относительно опор в проектируемых нестандартных одноступенчатых редукторах; U - передаточное число редуктора; Т< - вращающий момент на тихоходном валу редуктора или на приводном валу рабочей машины для открытой передачи, Нм; [G<]н - допускаемое контактное напряжение колеса с менее прочным зубом или среднее допускаемое контактное напряжение, Н/мм². Kнв - коэффициент неравномерности нагрузки по длине зуба. Для прирабатывающихся зубьев Kнв <= 1(табл. 3.1, стр. 49 [1]). Полученное межосевое расстояние округлить до ближайшего значения из ряда нормальных линейных размеров (табл. 13.15, стр. 313 [1]). 4.1.2 Определяю модуль зацепления М, мм: М≥ Км - для косозубых передач равен 5,8 (стр. 59 [1]). М ≥ Если модуль получили меньше 2 мм, то, несмотря на полученное значение, принимаем за 2 мм., т.к в силовых передачах значение модуля меньше 2 мм. не рекомендуется из-за опасности большого понижения несущей способности в результате износа, повышенного влияния неоднородности материала, опасности разрушения при перегородках ( ч. Решетов Детали машин, стр. 266). М = 2 мм. 4.1.3 Определяю гол наклона зубьев β β 4.1.4 Определяю суммарное число зубьев шестерни и колеса: Z∑ = Z1 <+
Z2 = 2 а Полученное значение Z∑ округляем в меньшую сторону до целого числа. Z∑ = 114 4.1.5 точняем действительную величину гла наклона зубьев для шевронных передач: β =
arccos Z∑ М / (2 а Z1 <= Z∑ / (1+U) = 114 / 5 = 22,8 Значение Z1 округляю до ближайшего целого числа: Z1 = 23 4.1.7 Определяю число зубьев колеса: Z2 <= Z∑ - Z1 = 114 - 23 = 91а 4.1.8а Определяю фактическое передаточное число Uф и проверяю его отклонение ∆U от заданного U: Uф = Z2 Z1 <= 91 / 23 =
3,956; ∆U = ∆U = Полученное значение отклонения довлетворяет словию: ∆U ≤ 4% 4.1.9 Определяю фактическое межосевое расстояние: 4.1.10 Определяем основные геометрические параметры передачи: d1 = M* Z1 / d2 = M*Z2 / dа1 = d1+М = 46,747+2*2 = 50,747 мм. dа2 = d2+М = 184,959+2*2 = 188,954 мм. df1 = d1 - 2,М = 46,747 - 4,8 = 41,947 мм. df2 = d2 - 2,М = 184,959 - 4,8 = 180,159
мм. b2 а<= Ψа * а У шевронных передач Составляем табличный ответ: Параметр, мм. Шестерня Колесо Делительный диаметр, d 46 184 Диаметр вершин зубьев, dа 50 188 Диаметр впадин зубьев, df 42 180 Ширина венца, b 39 39 4.2 Проверочный расчет: 4.2.1 Проверяем межосевое расстояние: 4.2.2 Проверяем пригодность заготовок колес: Условие пригодности заготовок колес: Dзаг ≤ Dпред.; Сзаг (Sзаг) ≤ Sпред. Dзаг1 = dа1+ 6 мм. = 50,747+6 = 56,747 мм.,
т.к аDпред = 125 мм. выполняется словие: 56,747≤125,
заготовка пригодна. Sзаг2 = 4.2.3 Проверяю контактные напряжения Gн, Н/мм²: Gн = К* где К - вспомогательный коэффициент. Для шевронных передач К = 376 (стр. 61 [1]). FT <= 2 Т < * 10 Кнα - коэффициент, учитывающий распределение нагрузки между зубьями. Для шевронных передач Кнα определяют по графику (рис. 4.2., стр. 63 [1]) в зависимости от окружной скорости колес V и степени точности передач. = W< * d2 / 2*10 Степень точности передачи - 9 (табл. 4.2., стр. 62 [1]) Кнα = 1,12. Кнβ = 1 (стр. 59 [1]) - коэффициент неравномерности нагрузки по длине зуба. Кнν - коэффициент динамической нагрузки, зависящий от окружной скорости колес V и степени точности передач. Кнν = 1,01(табл. 4.3., стр. 62 [1]) Gн =376 В данном случае [Gн<] = 418 Н/мм². Наблюдается недогрузка передачи на 1,4%.
Допускаемая недогрузка 10%, словие выполнено. 4.2.4 Проверяем напряжение изгиба зубьев шестерни GF1 и колеса GF2, Н/мм². GF2 = YF2*Yβ GF1 = GF2 * YF1 /
YF2 ≤ [G]F1 где М - модуль зацепления, мм. b2 - ширина зубчатого венца колеса, мм. FT - окружная сила зацеплений, Н. КFα - коэффициент, учитывающий распределение нагрузки между зубьями, для шевронных передач КFα =1(стр. 63 [1]). КFβ Цкоэффициент неравномерности нагрузки по длине зуба.
КFβ =1(стр. 63 [1]). КFV - коэффициент динамической нагрузки.
КFV = 1,01(табл.
4.3., стр. 62 [1]). YF1 и YF2 - коэффициенты формы зуба шестерни и колеса. Определяются по таблице 4.4, стр. 64[1] в зависимости от эквивалентного числа зубьев шестерни Z1 , и колеса Z2. ZV1 = Z1 / ZV2 <= Z2 / Yβ <= 1 -
β /140 = 1 - 10 / 140 = 0,929 - коэффициент, учитывающий наклон зуба. GF2 = 3,62*0,929 GF1 = 69,327*3,7 /
3,62 = 70,859 Н/мм² Если GF значительно меньше [G<]F, то это допустимо, т.к. нагрузочная способность большинства зубчатых передач ограничивается контактной прочностью.
Условие выполнено. 4.2.5 Составляем табличный ответ: Параметры зубчатой цилиндрической передачи, мм. Проверочный расчет: Параметр Допускаемые значения Расчетные значения Примечания Контактные напряжения, Gн 418 Н/мм² 412 Н/мм² -1,4% Напряжения изгиба, GF1 256 Н/мм² 70,859 Н/мм² -72% Напряжения изгиба, GF2 199 Н/мм² 69,327 Н/мм² -65% Проектный расчет: Параметр Значения Межосевое расстояние, а Модуль зацепления, мм. Ширина зубчатого венца: шестерни, колеса, Угол наклона зубьев, β Диаметр делительной окружности: шестерни, d1 колеса, d2 Число зубьев шестерни, Z1 Число зубьев колеса, Z2 Диаметр окружности вершин шестерни, dа1 колеса, dа2 Диаметр окружности впадин шестерни, df1 колеса, df2 Вид зубьев 116 2 39 39 10
46,747 184,959 23 91 50,747 188,959 41,947 180,159 Шевронные 5. Проектный расчет валов редуктора 5.Выбор материала валов. Для валов в проектируемом редукторе рекомендуют применять сталь 45. 5.2 Выбор допускаемых напряжений. Проектный расчет валов выполняется по напряжениям кручения. Поэтому допускаемое напряжение: [τ<]ка <= 10 Е 20 Н/мм². При этом меньшее [τ]к <= 10 Н/мм² -
для быстроходного вала, большее [τ]к <= 20 Н/мм² - для тихоходного вала. 5.3
Определение сила в зацеплении закрытых передач: Силы в зацеплении закрытой передачи На шестерни На колесе Цилиндрическая Окружная, FT 1546,155 1546,155 Шевронная Радиальная, FR 567,339 567,339 FT1 = FT2 FT2 = 2*Т *
10 FR1 <= FR2 FR2 = FT2 Угол зацепления α
принят за 20
5.4 Определяем консольные силы: Консольные силы Вид открытой передачи Характер силы по направлению Значение силы, Н Клиноременная Радиальная 874,051 Fоп = 2Fо * где Fо - сила предварительного натяжения ремня; Fо = 110,357 Н (результат расчета ременной передачи). α1 - гол обхвата ремнем ведущего шкива. α1 = 163,672 (результат расчета ременной передачи). Fоп = 2*110,375* 5.5 Определяем размеры ступеней валов одноступенчатого редуктора: 5.5.1 1-я ступень валов d1 = где Мк = Т - крутящий момент равен вращающему моменту на валу, Нм. [τ<] [τ<] [τ<] Быстроходный вал: d1 = Тихоходный вал: d1 = Быстроходный вал: L1 = (1,Е1,5) d1 = 1,2*26,88 = 32,256 = 32 мм. Тихоходный вал: L1 = (1,Е1,5) d1 = 1,2*32,957 = 39,548 = 40 мм. 5.5.2 2-я ступень валов: Быстроходный вал: d2 = d1+2 где d2 = 26,88+2*2,2
= 31,28 мм. Диаметр под подшипник округляем до ближайшего стандартного значения диаметра внутреннего кольца подшипника d. d2 = 30 мм. Тихоходный вал: d2 = d1+2 где d2 = 32,957+2*2,2
= 37,334 мм. Следовательно, d2 = 35 мм. Быстроходный вал: L2 ≈ 1,5*d2 ≈ 1,5*30 ≈ 45 мм. Тихоходный вал: L2 ≈ 1,25*d2 ≈ 1,25*35 ≈ 43,75 мм. Округляем до ближайшего стандартного значения из ряда Ra40: L2 ≈ 45 мм. 5.5.3 3-я ступень валов: Быстроходный вал: d3 = d2+3,2r где r = 2 (примечание 1, стр.109 [1]). d3 = 30+3,2*2 =
36,4 мм. Округлив принимаема d3 = 36 мм. Тихоходный вал: d3 = d2+3,2*r = 35+3,2*2 = 41,4 мм. Округлив принимаема d3 = 42 мм. 5.5.4 4-я ступень валов: Быстроходный вал: d4 = d2 = 30 мм. Тихоходный вал: d4 = d2 = 35 мм. Быстроходный вал: L4 = В - ширина подшипника, где В = 19
мм. ( табл. К27, стр.410 [1]). L4 = 19 мм. Тихоходный вал: L4 = В, где В = 17 мм. ( табл. К27,
стр.410 [1]). L4 = 17 мм. 5.5.5 5-я ступень валов: Тихоходный вал: d5 = d3+3 d5 = 42+3*1,6 =
42+4,8 = 46,5 мм. Округлив принимаема d5 = 48 мм. 5.5.6 Составляем табличный ответ по определению размеров ступеней валов редуктора: Размеры ступеней, мм. Ступени вала Вал-шестерня Вал-колесо 1-я под элемент открытой передачи d1 = 26 мм. L1 = 32 мм. d1 = 32 мм. L1 = 40 мм. 2-я под плотнение крышки с отверстием
и подшипник d2 = 30 мм. L2 = 45 мм. d2 = 35 мм. L2 = 45 мм. 3-я под шестерню, колесо d3 = 36 мм. определяют графически d3 = 42 мм. определяют графически 4-я под подшипник d4 = 30 мм. L4 = 19 мм. d4 = 35 мм. L4 = 17 мм. 5-я упорная или под резьбу d5 = 48 мм. определяют графически Схема нагружения валов цилиндрического одноступенчатого редуктора SHAPEа
* MERGEFORMAT Параметр Шестерня Колесо Ft, H Fr, H Fa, H Foп,Н 874,051 Т,
Нм 38,844 143,198 W,с 50,252 12,563 SHAPEа
* MERGEFORMAT 6.Определение реакций в подшипниках.
Построение эпюр изгибающих и крутящих моментов ( быстроходный вал ) SHAPEа * MERGEFORMAT Быстроходный вал: Дано: Ft = 1546,155 H, Fr = 567,339 H, Foп = 874,051 Н, Lоп = 0,052 м, Lв/2 = 0,039 м, Lв = 0,078 м, Fy = Foп*
sin20 = 874,051*0,342 = 298,925 H Fx = Foп*cos20
=874,051*0,94 = 821,607 H 1. Определение реакции в подшипниках в вертикальной плоскости: ∑М4 = 0 - Fy(Lоп+ Lв) +Ray* Lв - Fr * Lв/2 = 0 - 298,925*0,13+ Ray*0,078-567,339*0,039 = 0 -38,860+ Ray*0,078-22,126 = 0 Ray*0,078 = 60,986 Ray = 60,986/0,078 = 781,871 Н ∑М2
= 0 - Fy* Lоп<+ Fr*
Lв2+
Rв -298,925*0,052+567,339*0,039+
Rв -15,544+22,126+ Rв Rв Проверка: ∑Fnyа
<= 0 Fy<- Ray<+ Fr<- Rв Строим эпюры изгибающих моментов. М1 = 0 М2лева <= Fy* Lоп = 298,925*0,052 = 15,544 Нм М2пр = М2лев = 15,544 Нм М3лев = Fy(Lоп+ Lв/2)- Ray* Lв/2=298,925*0,091-781,871*0,039=-3,29
Нм М3пр = М3лев = -3,29а Нм М4лев = Fy (Lоп+ Lв)- Ray* Lв+ Fr* Lв/2 =
298,925*0,13-781,871*0,078+567,339*0,039 = 38,86-60,985+22,126 = 0 2. Определение реакции в подшипниках в горизонтальной плоскости: ∑М4 = 0 - Fx(Lоп+ Lв) +Raх* Lв + Ft * Lв/2 = 0 -821,607*0,13+ Raх*0,078+1546,155*0,039 = 0 -106,808+ Raх*0,078+60,3 = 0 Raх =
46,508/0,078 = 596,236 Н ∑М2 = 0 - Fх* Lоп - Ft* Lв/2+ Rвх* Lв = 0 -821,607*0,052-1546,155*0,039+
Rвх*0,078 = 0 -42,723-60,3+ Rвх*0,078 = 0 Rвх =
103,023/0,078 = 1320,807 Н Проверка: ∑Fnха
<= 0 Fх- Raх- Ft<+ Rвх = 0 ;
821,607-596,236-1546,155+1320,807 = 0 ; 0 = 0 Строим эпюры изгибающих моментов. М1 = 0 М2лева <= Fх* Lоп = 821,607*0,052 = 42,723 Нм М2пр = М2лев =а 42,723 Нм М3лев=Fх(Lоп+Lв/2)- Raх* Lв/2=821,607*0,091-596,236*0,039=51,513
Нм М3пр = М3лев = 51,513 Нм М4лев = Fх (Lоп+ Lв)- Raх* Lв - Ft* Lв/2 =
821,607*0,13-596,236*0,078-1546,155*0,039 = 106,808-46,506-60,3 = 0 3. Строим эпюры крутящих моментов. Мк = М2 = Ft*d1/2 = 1546,155*46,747/2 = 36,139 Нм 4. Определяем суммарные радиальные реакции: Ra = Rв = 5. Определяем суммарные изгибающие моменты. М2 = М3 = Определение реакций в подшипниках. Построение эпюр изгибающих и крутящих моментов ( тихоходный вал ) SHAPEа
* MERGEFORMAT Тихоходный вал: Дано: Ft = 1546,155 H, Fr = 567,339 H, Lт = 0,093 м, Lт/2 = 0,0465 м, 1. Определение реакции в подшипниках в горизонтальной плоскости: ∑М3 = 0 - Rсх*Lт + Ft * Lт/2 = 0 - Rсх*0,093+1546,155*0,0465 = 0 - Rсх*0,093 = -71,896 Rсх = 71,896/0,093 = 773,075 Н ∑М1 = 0 - Ft* Lт/2+Rдх* Lт = 0 -1546,155*0,0465+ Rдх *0,093 = 0 Rдх =
71,896/0,093 = 773,075 Н Проверка: ∑Fnха
<= 0 Rдх + Rсх - Ft = 0 ; 773,075+773,075-1546,155 = 0 ;
0 = 0 Строим эпюры изгибающих моментов. М1 = 0 М2лева <= Rсх * Lт/2а
<= 773,075*0,0465 = 35,947 Нм М2пр = М2лев = 35,947 Нм М3лев = Rсх * Lт- Ft* Lт/2а
<= 71,895-71,895 = 0 2. Определение реакции в подшипниках в вертикальной плоскости: ∑М3 = 0 - Rсу*Lт + Fr * Lт/2 = 0 - Rсу*0,093+567,339*0,0465 = 0 Rсу = 26,381/0,093 = 283,669 Н ∑М1 = 0 - Fr* Lт/2+Rду* Lт = 0 567,339*0,0465+ Rду *0,093 = 0 Rду = 26,38/0,093
= 283,669 Н Проверка: ∑Fnуа
<= 0 Rсу - Fr<+ Rду = 0 ;а 283,669 - 567,339+283,669 = 0 ; 0 = 0 Строим эпюры изгибающих моментов. М1 = 0 М2лева <= Rсу * Lт/2а
<= 283,669 *0,0465 = 13,19 Нм М2пр = М2лев = 13,19 Нм М3лев = Rсу * Lт- Fr* Lт/2а
<= 26,381-26,381 = 0 3. Строим эпюры крутящих моментов. Мк = М2 = Ft*d2/2 = 1546,155*184,959/2 = 145,13 Нм 4. Определяем суммарные радиальные реакции: Rс = Rд = 5. Определяем суммарные изгибающие моменты. М2 = 7. Проверочный расчет подшипников: 7.1 Базовая динамическая грузоподъемность подшипника Сr представляет собой постоянную радиальную нагрузку, которую подшипник может воспринять при базовой долговечности, составляющей 10 Сr = 29100 Н для быстроходного вала
(табл. К27, стр.410 [1]), подшипник 306. Сr = 25500 Н для тихоходного вала
(табл. К27, стр.410 [1]), подшипник 207. Требуемая долговечность подшипника Lh составляет для зубчатых редукторов Lh ≥ 6 часов. Пригодность подшипников определяется сопоставлением расчетной динамической грузоподъемности Crp, Н с базовой долговечностью L10 Расчетная динамическая грузоподъемность Crp, Н и базовая долговечность L10 Crp = где RE - эквивалентная динамическая нагрузка, Н; ω - гловая скорость соответствующего вала, с М - показатель степени: М
= 3 для шариковых подшипников (стр.128 [1]). 7.1.1 Определяем эквивалентную нагрузку RE = V* Rr*Кв*Кт, где - коэффициент вращения. V = 1 при вращающемся внутреннем кольце подшипника (стр.130 [1]). Rr - радиальная нагрузка подшипника, Н. Rr = R - суммарная реакция подшипника. Кв - коэффициент безопасности. Кв = 1,7 (табл. 9.4, стр.133 [1]). Кт - температурный коэффициент. Кт = 1(табл. 9.5, стр.135 [1]). Быстроходный вал: RE = 1*1,7*1323,499*1 = 2249,448 Н Тихоходный вал: RE = 1*1,7*823,746*1 = 1399,909 Н 7.1.2 Рассчитываем динамическую грузоподъемность Crp и долговечность L10 Быстроходный вал: Crp =2249,448 L10 75123,783 ≥ 6 -
условие выполнено. Тихоходный вал: Crp = 1399,909 L10 848550,469 ≥ 6 -а словие выполнено. Проверочный расчет показал рентабельность выбранных подшипников. 7.1.3 Составляем табличный ответ: Основные размеры и эксплуатационные размеры подшипников: d×D×T мм. Crp Cr L10 Lh Б 306 30×72×19 26991,126 29100 75123,783 6 Т 207 35×72×17 10581,912 25500 848550,469 6 8. Конструктивная компоновка привода: 8.1 Конструирование зубчатых колес: Зубчатое колесо: Элемент колеса Параметр Значения параметра Обод Диаметр Толщина Ширина da
= 184,959 мм S
= 2,2м<+0,05b2
=2,2*2+0,05*39=6,35 мм b2
= 39 мм Ступица Диаметр внутренний Толщина Длина d = d3 = 42 мм δст = 0,3 d = 0,3*42 = 13,6 мм Lст = d = 42 мм Диск Толщина Радиусы закруглений Отверстия С = 0,5 (S<+ δст)≥0,25 b2 С = 0,5(6,35+13,6)≥0,25*39 С = 9,975≥9,75 Принимаем С = 10 мм R≥6 ;Принимаем R = 6 Не предусмотрены На торцах зубьев выполняют фаски размером Для передачи вращающегося момента редукторной парой применяют шпоночное соединение посадкой Н7/r6. 8.1.2 При использовании в качестве редукторной пары шевронных колес заботится об осевом фиксировании колеса нет необходимости, однако для предотвращения осевого смещения подшипникова в сторону колеса устанавливаем две втулки по обе стороны колеса. 8.2 Конструирование валов: Переходный часток валов между двумя смежными ступенями разных диаметров выполняют канавкой: d Свыше 10 до 50мм b 3 мм h 0,25 мм r 1 мм (табл.
10.7, стр.173 [1]) 8.2.1 На первой ступени быстроходного вала используется шпоночное соединение со шпонкой, имеющей следующие размеры: b h 26 8 7 0,5 4 18 8.2.2 На первой и третей ступени тихоходного вала применяем шпоночное соединение со шпонками, имеющими следующие размеры: b h 1-я 32 10 8 0,5 5 24 3-я 42 10 8 0,5 5 34 8.3 Конструирование корпуса редуктора: Корпус изготовлен литьем из чугуна марки СЧ 15. Корпус разъемный. Состоит из основания и крышки. Имеет прямоугольную форму, с гладкими наружными стенками без выступающих конструктивных элементов. В верхней части крышки корпуса имеется смотровое окно, закрытое крышкой с отдушиной. В нижней части основания расположены две пробки - сливная и контрольная. Толщина стенок и ребер жесткости δ, мм.:δ=1,12 Для выполнения словия
δ≥6 мм., принимаем δ = 10 мм. 8.3.1 Крепление редуктора к фундаментальной раме (плите), осуществляется четырьмя шпильками М12. Ширина фланса 32 мм., координата оси отверстия под шпильку 14 мм. Соединение крышки и основания корпуса осуществляется шестью винтами М8. Крышка смотрового окна крепится четырьмя винтами М6. 8.4 Проверочный расчет валов 8.4.1. Определяем эквивалентный момент по формуле для валов:
Быстроходный вал: Мэкв = Тихоходный вал: Мэкв = 8.4.2. Определяем расчетные эквивалентные напряжения δэкв и сравниваем их с допустимым значением [δ] Для быстроходного вала: δэкв =
где : Wнетто = 0,1d d = 36 - диаметр быстроходного вала в опасном сечении. Для тихоходного вала: δэкв = где: Wнетто = 0,1d d = 42 - диаметр тихоходного вала в опасном сечении. Вывод: прочность быстроходного и тихоходного вала обеспечена. 9. Смазывание 9.1 Для редукторов общего назначения применяют непрерывное смазывание жидким маслом картерным непроточным способом (окунанием). Этот способ применяется для зубчатых передач с окружными скоростями от 0,3 до 12,5 м/сек. 9.2 Выбор сорта масла зависит от значения расчетного контактного напряжения в зубьях GН аи фактической окружной скорости колес U. Сорт масла выбирается по таблице 10.29, стр.241. В данном редукторе при
U = 1,161 м/сек,
GНа
<= 412 применяется масло сорта И-Г-А-68. 9.3 Для одноступенчатых редукторов объем масла определяют из расчета 0,Е0,8 л. на 1 квт передаваемой мощности.= 2,2 квт, U = 2,2*0,5 = 1,100 л. Объем масла в проектируемом редукторе составляет 1,100 л. Заполнение редуктора маслом осуществляется через смотровое окно. Контроль уровня масла осуществляется с помощью контрольной пробки. Слив масла производят через сливную пробку. 9.4 Смазывание подшипников: В проектируемых редукторах для смазывания подшипников качения применяют жидкие и пластичные смазочные материалы. Смазочный материал набивают в подшипник вручную при снятой крышке подшипникового зла. Наиболее распространенной для подшипников качения - пластичной смазки типа солидол жировой (ГОСТ 1033-79), консталин ажировой Т-1
(ГОСТ 1957-75). 10. Проверочный расчет шпонок 10.1 Призматические шпонки проверяют на смятие, проверки подлежат две шпонки тихоходного вала. Условие прочности Gсм = Ft / Aсм ≤
[G<]см где Ft - окружная сила на колесе, Н Aсм - площадь смятия, мм² Aсм = (0,94 Lp = L -
[G<]см - допускаемое напряжение на смятие, Н/мм² [G<]см =
110 Н/мм² (стр.252 [1]) 10.2 Проверяем шпонку на первой ступени вала: L = 24 Lp = 24 - 10 = 14
мм. Aсм = (0,94*8 - 5)*14 = 35,28 мм² Gсм = 1546,155 / 35,28 = 42,617
Н/мм² 42,617≤110 Н/мм²
- словие прочности выполнено, шпонка пригодна. Проверяем шпонку на третей ступени вала: L = 34 Lp = 34 - 10 = 24
мм. Aсм = (0,94*8 - 5)*24 = 60,48 мм² Gсм = 1546,155 / 60,48 = 25,564
Н/мм² 25,564 ≤110 Н/мм²
- словие прочности выполнено, шпонка пригодна. 11. Технический уровень редуктора Результатом для редуктора является его нагрузочная способность, в качестве характеристики которой можно принять вращающий момент на его тихоходном валу. Объективной мерой затраченных средств является масса редуктора м, кг., в которой практически интегрирован весь процесс его проектирования. Поэтому за критерий технического уровня можно принять относительную массу γ = м / Т, т.е.
отношение массы редуктора (кг.) к вращающему моменту на его тихоходном валу
(Нм). Этот критерий характеризует расход материалов на передачу момента и легок для сравнения. 11.1 Определяем массу редуктора: м = φρV*10 где φ - коэффициент заполнения (рис. 12.1) φ = 0,43 (стр.263 [1]) ρ = 7300 кг/м - словный объем редуктора, мм = L*B*H
= 265*76*238 = 4793320 мм м = 0,43*7300*4793320*10 11.2 Определяем критерий технического уровня редуктора: γ = м / Т < = 15 / 143,198 = 0,1 11.3 Составляем табличный ответ: Технический уровень редуктора: Тип редуктора Масса, кг Момент, Нм Критерий, γ Вывод Цилиндрический одноступенчатый горизонтальный шевронный 15 143,198 0,1 Технический уровень редуктора
высокий, редуктор соответствует современным мировым образцам Список литературы: 1. А.Е. Шейнблит Курсовое проектирование деталей машин // Москва, Высшая школа, 1991 г. 2. Н.Г. Куклин, Г.С.
Куклина Детали машин // Москва, Высшая школа, 1987 г. 3. Решетов Детали машин
// Москва, Высшая школа, 1975 г.а
а<=
а<=
а<= 149,15 (рад/с)
а<=а 50,252 (рад/с)
а<= 12,563 (рад/с)
<=
13,496 (Нм)
а<=
а<= 38,844 а(Нм)
а<=
а<= 143,198 (Нм)
Параметр
Передача
Параметр
Вал
Закры-тая
Откры-
Двига-
Редуктора
Приводной рабочей
Переда-
КПД
а<- число циклов перемены напряжений для всех сталей,
соответствующее пределу выносливости;
Элемент
Марка
Dпред, мм;
Термооб-
Н/мм²
116,53 мм.
а
а<= Ψа * а
Gн<]
d2 = 2*143198 / 185,231 = 1546,155 - окружная сила зацеплений, Н.
* КFα* КFβ*
КFV≤ [G<]F2
Вид передачи
Силы в зацеплении
Значение силы, Н
d2 = 2*143198 / 185,231 = 1546,155 Н
26
мм.
а<= 32,957 = 32 мм.
1546,155
567,339
0
<
<
а<= 823,476 Н
а<= 823,476а Н
аоборотов внутреннего кольца.
L10
а <- словие выполнено.
а словие выполнено.
Вал
Подшипник
Размеры
Динамическая грузоподъемность, Н
Долговечность, ч
Диаметр вала, d
Сечение шпонки
Фаска
Глубина паза вала,
Длина
Ступень
Диаметр вала, d
Сечение шпонки
Фаска
Глубина паза вала,
Длина
а
а<=
а<= 13,505 мПа ≤ [δ]
а<= 0,1*36
а<=
а<= 20,259 мПа ≤ [δ]
а<= 0,1*42
а
а<- плотность чугуна