
Эффективный метод получения синтез-газа паровой и пароуглекислотной конверсией метана
Автореферат кандидатской диссертации
ООО ЮРД - Центр и акафедра газохимииа Российского Государственного Университета нефти и газа имени И.М. Губкина.
аа На правах рукописи
ГЕРАЩЕНКО ИГОРЬ ОЛЕГОВИЧ
ЭФФЕКТИВНЫЙ МЕТОД ПОЛУЧЕНИЯ СИНТЕЗ-ГАЗА ПАРОВОЙ И ПАРОУГЛЕКИСЛОТНОЙ КОНВЕРСИЕЙ МЕТАНА.
05.17.07 - Химическая технология топлива и
высокоэнергетических веществ
АВТОРЕФЕРАТ
диссертации на соискание ученой степени
кандидата технических наук
Москва 2012
а
Работа выполнена в ООО ЮРД - Центр и на кафедре Газохимии Российского государственного Университета нефти и газа имени И.М.Губкина.
Научный руководитель: член-корреспондент РАН,
доктор химических наук, профессор
Лапидус Альберт Львович
Официальные оппоненты:аа доктор технических наук, профессор
Туманяна Борис Петрович
кандидат технических наук
Антонюк Сергей Николаевич
Ведущая организация: ООО ВНИИГАЗ
Защита состоится 24 апреля 2012 г. в 15-00 часов в ауд. 541 на заседании Диссертационного совета Д 212.200.04 при Российском государственном университете нефти и газа имени И.М.Губкина по адресу 119991, ГСП-1, Москва, Ленинский проспект, 65
С диссертацией можно ознакомиться в библиотеке РГУ нефти и газа имени И.М.Губкина.
Автореферат разослана л__а март 2012 г.
Ученый секретарь диссертационного совета Д 212.200.04,
доктор технических наук, профессор Р.З. Сафиеваа
Общая характеристика работы
Актуальность работы. аСовременные требования к экологическим нормам при добыче нефти препятствуют сжиганию попутного нефтяного газа на факелах. Все увеличивающиеся масштабы добычи природного газа приводят к снижению давления в газоносных пластах и возникновению низконапорных месторождений, добыча газа на которых становится нерентабельной. В результате возникает необходимость создания современных технологий утилизации природного и попутного нефтяного газа посредством переработки его в жидкие углеводороды а(GTL).
На первых этапах таких разработок априменяются лабораторные реакторы синтеза жидких углеводородов малого размера, которые могут использовать синтез-газ из баллонов. Однако последующие этапы разработки технологий GTL требуют использования лабораторных, а впоследствии и опытно-промышленных реакторов с объемом зоны реакции от нескольких сотен миллилитров до нескольких десятков литров. Необходимость проведения лабораторных и аопытно-промышленных аисследований на больших реакторах определяется тем, что процесс синтеза жидких углеводородов сопровождаетсяа значительным выделением тепла, а используемые катализаторы имеют узкий диапазон рабочей температуры и, при перегреве, теряют активность. Проектирование промышленных реакторов синтеза жидких углеводородов сводится к определению таких геометрических размеров реактора и параметров его работы, при которых перепады температуры в зоне реакции не будут превышать максимально допустимых.
Математическое моделирование процесса теплопередачи в слое катализатора всегда базируется на экспериментальных данных, для получения которых необходимо использовать лабораторные и аопытно-промышленные реакторы достаточно больших размеров.
При работе с такими реакторами потребление синтез-газа может составлять от нескольких сотен литрова до нескольких десятков кубометров в час, что проблематично при использовании газа из баллонов.
Получение синтез-газа в поршневых или реактивных двигателях имеет существенный недостаток,а поскольку принцип их работы основан на парциальном окислении метана воздухом, то содержание синтез-газа в получаемом продукте не может превышать 60%.
Из всего этого очевидна актуальность разработки лабораторного и ааопытно-промышленного метода аполучения синтез-газа паровой и пароуглекислотной конверсией метана с достаточной апроизводительностью по синтез-газу.
Получаемый при этом синтез-газ должен быть, по своему составу, пригоден для синтеза жидких углеводородов без дополнительной корректировки его состава.
Актуальным является изучение влияния параметров работы ааустановки паровой и пароуглекислотной конверсии метана на состав получаемого синтез-газа, а также отклонения значения этих параметров от теоретически арассчитаных.
Цель и задачи работы. ааЦелью работы являетсяа усовершенствование метода получения синтез-газа путем паровой и пароуглекислотной конверсией метана.
Для достижения этой цели в диссертации необходимо было решить следующие задачи:
- усовершенствовать схему установки для эффективного метода получения синтез-газа паровой и пароуглекислотной конверсией метана;
- оптимизировать схему движения материальных потоков в системе для достижения гомогенности исходной газовой смеси поступающей в зону конверсии;
- разработать конструкцию реактора паровой и пароуглекислотной конверсии метана, позволяющую аполучать синтез-газ, по составу пригодный для синтеза жидких углеводородов без дополнительной корректировки его состава;
- изучить влияние состава исходной газовой смеси и температурных режимов процесса на состав получаемого синтез-газа;
- оптимизировать параметры процесса.
Научная новизна работы:
- усовершенствована схема движения материальных потоков в системе для достижения гомогенности исходной газовой смесиа позволяющая сократить время от момента нагрева углеродосодержащих газов до их входа в слой катализатора конверсии до 0,1 - 0,2 секунды, что снижает сажеобразование,
- установлено, что усовершенствованный метода получения синтез-газа позволяет обеспечить производительность, достаточную для обеспечения работы как лабораторных, так и опытно-промышленныха установок GTL при составе синтез-газа не нуждающемся в дополнительной корректировке,
- впервые сконструирован и испытана реактор паровой и пароуглекислотной конверсии метана со встроенным в него прямоточным парогенератором.
Практическая значимость работы. а
Практическое значение работы заключается в том, что ва результате разработан усовершенствованный метод аполучения синтез-газа паровой и пароуглекислотной конверсии метана с составом пригодным для широкого спектра углеводородного синтеза. аа
Разработан лабораторный иа опытно-промышленный метод получения синтез-газа са широким диапазоном соотношенийа Н2 : СО от 1,6 до 4,6 при низком содержании (менее 8,5%) суммарного количестве СО2 и СН4 в получаемом синтез-газе.
Разработанный метод, приаа его масштабировании, позволит создавать установки с производительностью по синтез-газу от 200 до 100 000 литров в час, что позволит применять его в лабораторных и опытно-промышленных установках GTL. Состав получаемого синтез-газа позволяет использовать его для синтеза жидких углеводородова из Н2 и СО без дополнительной корректировки.
а Апробация работы. Результаты работы докладывались на:
- Втором международном газохимическом форуме IGCF'10.а Ханты-Мансийск, аамарт 2010 года г.;
- Научном семинаре по газохимии аав Российскома Государственном Университете нефти и газа им. И.М. Губкина,а июнь 2010г.
а аПубликации. аПо теме диссертации опубликовано 3 научных статьи в журналах, входящих в список ВАК России, 2 тезиса докладов, 1 патент на изобретение Российской Федерации.
Структура и объем работы. Диссертация состоит из введения, 4-х глав, основных выводов, списка использованной литературы, насчитывающего 145 наименования. Работа изложена на 126 стр, включает 23 рис. и 24 табл.
ОСНОВНОЕ СОДЕРЖАНИЕ РАБОТЫ.
Во введении аобоснована актуальность темы, определены цель и задачи диссертационной работы, ее новизна и практическая значимость, сформулированы положения, выносимые на защиту.
В первой главе (литобзор) представлен обзор современных процессов промышленного и лабораторного получения синтез-газа. Проведено сравнениеа процессов паровой, углекислотной конверсии метана и его парциального окисления.
Проанализированы газохимические процессы, потребляющие синтез-газ. Отмечено, что для лабораторных иа аопытно-промышленных аустановок аполучения синтез-газа, наиболее перспективным ааявляется пароуглекислотная конверсияа метана, поскольку она позволяет, изменяя соотношение СН4, СО2 и Н2О в исходной газовой смеси, аполучать синтез-газ с заданным соотношением аН2 : СО в диапазоне от 3 до 1.
Сделан анализ получения синтез-газа в лабораторных и опытно-промышленных аусловиях с помощью дизельных двигателей внутреннего сгорания. Показано, что такая методикаа подходит далеко не для всех аапроцессов синтеза жидких углеводородов из-за большого (более 40%) содержания азота в получаемом синтез-газе.
Изложено описание парциального окисления метана с использованием газоплотных керамических ферритовых кислородопроводящих мембран.
Приведен расчет, показывающий недостаточную эффективность газоплотных кислородопроводящих мембран в промышленных установках парциального окисления.
Описана схема Тандем для процесса двухступенчатой паронвоздушной или парокислородной конверсии, построенной по принципу авто-термичности процесса.
Приведено описание получения синтез-газа в плазме СВЧ - разряда, основанное на использовании низкотемпературной плазмы.
Представлено описание получение синтез-газа в реактивном (ракетном) двигателе.
Освещен ряд проблем, связанных с получением синтез-газа в лабораторных и опытно-промышленных условиях.а
Литературный обзор показывает, что лабораторные и опытно-промышленные технологии получения синтез-газа отработаны недостаточно.
Во второй аглаве а
Изображенаа схема установки пароуглекислотной конверсии метана.
В работе приведены расчеты, на основании которых была сконструированаа установка паровой и пароуглекислотной конверсии метана, а именно:
- скорости движения газов в каналах реактора (на основании которых определялись геометрические размеры, необходимые для создания оптимального режима смешения газов);
- прочности различных деталей реактора, с определением геометрических размеров и выбором материалов для изготовления деталей;
- системы обогрева, необходимые для конструирования нагревателей и блоков питания;
- процесса теплопередачи, определяющие тепловые потокиа и температурные перепады в слое катализатора и деталях реактора.
Обоснован выбор катализатора конверсии и приведены его характеристики.
В качестве катализатора использовался промышленный катализатор НИАП-03-01 (ТУ 113-03-00209510-93-2002).
Поскольку размеры гранулы катализатора НИАП-03-01 рассчитаны на использование в промышленных реакторах с внутренним диаметром труб не менее 100 мм, а испытуемыйа реактор имеет диаметр трубы 22 мм, то перед загрузкой в реактор конверсии метана гранулы катализатора измельчали, продували от пыли и измеряли их насыпную плотность. Фракционирование проводили с использованием сит № 4 (размер ячеек 4,75 мм), № 8 (2,36 мм) и № 14 (1,40 мм).
Принципиальная схема лабораторного блока пароуглекислотной конверсии метана представлена на рис. 1, а общий вид установки на рис. 2.а
Синтез-газ
а5
а1
а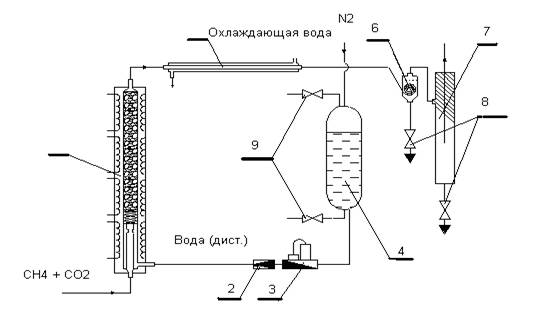
Рис. 1. Схема блока пароуглекисотной конверсии метана: 1 - реактор конверсии, 2 - обратный клапан, 3 - расходомер, 4 - баллон с водой, 5 - холодильник, 6 - циклон, 7 - сепаратор, 8, 9 - вентили.
Рис. 2. Общий вид установки.
Конструкция реактора конверсии приведена на рис. 3
Рис. 3. аКонструкция реактора конверсии
1 - Корпус реактора
2 - Корпус прямоточного парогенератора с винтовым каналом подачи воды и пара
3 - Зона смешения
4 - Патрубок подвода воды
5 - Патрубок подвода смеси метана и углекислого газа
6 - Карман для термопар
7 - Зона конверсии, заполненная катализатором
8 - Патрубок выхода продуктов реакции
9 - Нагреватель камеры смешения
10 - Нагреватели зоны реакции
На основании тепловых расчетов и расчетов на прочность были подобраны материалы для изготовления деталей реактора: корпуса, патрубка выхода продуктов реакции, накидной гайки и кармана для термопар. Они изготовлены из жаропрочного сплава ХН78Т, остальные детали, работающие при меньших нагрузках и температурах - из нержавеющей стали 12Х18Н10Т.
В третьей главе (методика проведения эксперимента) описана методика проведения лабораторных экспериментов.
Исследования заключались в изучении влияния температурного режима паровой и пароуглекислотной конверсии метана и состава исходной газовой смеси ана состав получаемого в результате конверсии синтез-газа.
Температурный режим поддерживался при помощи регуляторов температуры Термодат-25-Е1-ЗВ/12УВ/12Т/12Р, и силового блока СБ15М1. аВ качестве регулирующих и измеряющих термопар использовались хромель-алюмелевые термопарыа КТХА 01.02-100-к-1-И-Т600-1-800 .
Контроль и измерения давления на входе/выходе газова осуществлялся с помощью регуляторов давления Industrial Pressure Gauge, Adj Pointer, 63 mm, 0 to 400 psi, bar secondary, Lower Mount, 1/4 in. MNPT - 10 шт, PGI-63B-PG400-LAOX-J.
Регулирование расходов подаваемых в реактор метана, углекислого газа и воды осуществлялось с помощью регуляторов расхода EL-FLOWа Bronkhorst High-Tech.
Анализ состава получаемого синтез-газа проводился с помощью Хроматографаа Кристаллюкс-400М. В работе применялись колонки длиной 3 м и внутренним диаметром 3 мм. В качестве газа-носителя использовался гелий. Фазы в колонках - молекулярные сита 5А и Haysep Q.
Градуировка хроматографа производилась на 2х градуировочных смесяхаа с помощью градуировочных газовых смесей с известным составом.
В четвертой главе (Экспериментальные данные) представлены формулы для расчета основных показателей процесса (табл. 1).
Таблица 1 - Расчет основных показателей процесса конверсии метана.
Параметр |
Условное обозначение |
Расчетная формула |
Конверсияа метана |
К(СН4) |
|
Выход водорода |
В(Н2) |
|
Выход монооксида углерода |
В(СО) |
|
Селективность по водороду |
С(Н2) |
|
Селективность по оксиду углерода |
С(СО) |
|
n(CH4) - количество метана, подаваемого в ареактор конверсии, моль; nТ(CH4) - количество метана на выходе из реактора конверсии, моль; n(H2) - количество образовавшегося водорода, моль; n(H2O) - количествоа воды, аподаваемой в ареактор, моль; n(CO) - количество образовавшегося монооксида углерода, моль; n(CO2) - количествоа углекислого газа, подаваемого в ареактор, моль. |
а
Оценка параметрова процесса пароуглекислотной конверсии метана проводилась поа термодинамическим арасчетам, сделанным ведущим научным сотрудником лаборатории Газохимии ООО ОЦИР М.Н. Михайловым , арезультаты которых представлены в табл. 2 и 3.
Таблица 2 - Данные термодинамического расчета состава смеси, получаемой в процессе пароуглекислотной конверсии метана, при давлении 5 атм. и составе сырьевого газа CH4 : H2O : CO2= 1,0 : 1,13 : 0,4.
T,C |
H2, об.% |
CO, об.% |
H2 : CO |
CO2, об.% |
H2O, об.% |
CH4, об.% |
500 |
16.2 |
1.1 |
14,7 |
13.8 |
41.1 |
27.9 |
550 |
22.9 |
2.4 |
9,5 |
13.9 |
36.4 |
24.4 |
600 |
30.2 |
4.9 |
6,2 |
13.4 |
31.2 |
20.4 |
650 |
37.4 |
8.8 |
4,25 |
12.2 |
25.4 |
16.2 |
700 |
43.8 |
14.3 |
3,00 |
10.2 |
19.4 |
12.3 |
750 |
49.4 |
20.0 |
2,47 |
7.7 |
14.5 |
8.5 |
800 |
54.3 |
23.5 |
2,3 |
5.6 |
11.9 |
4.7 |
850 |
57.4 |
25.8 |
2,22 |
4.2 |
10.3 |
2.3 |
900 |
59.0 |
27.1 |
2,18 |
3.4 |
9.5 |
1.0 |
950 |
59.6 |
27.8 |
2,14 |
3.0 |
9.3 |
0.4 |
1000 |
59.7 |
28.2 |
2,12 |
2.6 |
9.3 |
0.2 |
1050 |
59.7 |
28.5 |
2,1 |
2.4 |
9.4 |
0.1 |
1100 |
59.6 |
28.7 |
2,08 |
2.2 |
9.5 |
0.0 |
1150 |
59.4 |
28.8 |
2,06 |
2.1 |
9.7 |
0.0 |
1200 |
59.3 |
29.0 |
2,04 |
1.9 |
9.8 |
0.0 |
На рис. 4 представлена зависимость соотношенияа H2 : CO в получаемом синтез-газе, от температуры пароуглекислотной конверсии метана. аИз табл. 2 и рис. 4 видно, что минимальное значение температуры конверсии для получения синтез-газа, приемлемого для синтеза жидких углеводородов, составляет 800 оС. Максимальное допустимое значение температуры конверсии определяется жаростойкостью материала реактора, и соответствует 1000 оС.
Рис. 4.
Зависимость соотношения H2 : CO в получаемом синтез-газе от температуры проведения пароуглекислотной конверсии метана.
В табл. 3 приведены данные термодинамического расчета мольных соотношений CH4/ H2O/ CO2а для процесса пароуглекислотной конверсии метана при 5 атм. в температурном диапазоне от 800 до 1000 оС.
Таблица 3 - Диапазоны термодинамического расчета мольных соотношений CH4/ H2O/ CO2а для процесса пароуглекислотной конверсии метана при 5 атм.
T, С |
CH4/ H2O / CO2 |
800 |
1/1.05-1.3/0.42-0.53 |
900 |
1/0.8-1.18/0.25-0.4 |
1000 |
1/0.8-1.05/0.26-0.36 |
а
Были проведены ааэксперименты при температурном режиме 450оС в камере смешения исходных газовых компонентов и 900оС в зоне реакции при различных составах газовой смеси. Температура в камере смешения выставлялась такой, при которой конверсия метана еще не происходит.
Температура в зоне реакции определялась прочностными характеристиками жаропрочного сплава корпуса реактора.
Испытание установки паровой и пароуглекислотной конверсии метана проводили в режиме stop and go в течение 5 дней. Время выхода установки на необходимый температурный режим составляло 3 - 3,5 часа. Время работы в стабильном режиме, в каждом эксперименте, было 6 часов.
В табл. 4 представлены показатели процесса паровой и пароуглекислотной конверсии метана, при различных соотношениях СН4, СО2 и Н2О в исходной газовой смеси. Целью данных экспериментов было определение состава исходной газовой смеси при котором, в результате конверсии, будет получаться синтез-газ с соотношением Н2 к СО в диапазоне 2 - 2,2.
а
Таблица 4 - Состав синтез-газа и основные показатели процесса паровой и апароуглекислотной конверсии метана (Ткамеры смешения =450С, Тконверсии=900С, р=5 атм, объемная скорость 1000ч-1, продолжительность опыта =6 ч)
Исходная смесь, мольные соотношения |
Отношение H2 : CO |
Показатели процесса, % |
||||||
CH4 |
CO2 |
H2O |
К(CH4) |
В(H2) |
В(CO) |
C(H2) |
C(CO) |
|
1,00 |
0,00 |
1,16 |
4,6 |
82,52 |
72,2 |
54,9 |
87,4 |
66,5 |
1,00 |
0,10 |
1,16 |
4,2 |
87,4 |
76,1 |
66,3 |
87,1 |
75,9 |
1,00 |
0,40 |
1,16 |
2,5 |
91,8 |
78,6 |
71,1 |
85,6 |
77,5 |
1,00 |
0,70 |
1,16 |
1,8 |
92,9 |
78,7 |
75,4 |
84,7 |
81,1 |
1,00 |
1,00 |
1,16 |
1,6 |
90,7 |
82,8 |
71,2 |
91,4 |
78,5 |
Данные экспериментов этого этапа показывают, что предлагаемаяаа технология конверсии метана позволяет получать синтез-газ с диапазоном соотношения Н2 :СО от 1,6 до 4,6. Такой диапазон состава синтез-газа позволяет его использование в широком спектре газохимическихаа процессов.
При синтезе жидких углеводородов по методу Фишера-Тропша требуемое соотношение Н2 к СО в синтез-газе составляет 2 - 2,2.
По табл.4 видно, ачто синтез-газ такого состава может быть получен при соотношении компонентов в исходной газовой смеси в диапазоне:
CH4 : H2O : CO2= 1,0 : 1,16: 0,4.аа H2 : CO = 2,5
CH4 : H2O : CO2= 1,0 : 1,16: 0,7. ааH2 : CO = 1,8
Поэтому был проведен ряд экспериментов с целью получения синтез-газа вышеуказанного состава при соотношении компонентов исходной газовой смеси CH4 : H2O : CO2= 1,0 : 1,0 : 0,4.аа а
Результаты экспериментов представлены в аатабл. 5.
Табл. 5 - Экспериментальные данныеа пароуглекислотной конверсии
метана (Т=900С, р=5 атм), ( CH4 : H2O : CO2 = 1 : 1: 0,4)
№ опыта |
Состав синтез-газа, % мольные |
||||
|
Н2 |
СО |
СН4 |
СО2 |
Н2 : СО |
1 |
61,99 |
30,14 |
3,76 |
4,11 |
2,06 |
2 |
62,22 |
30,04 |
3,22 |
4,52 |
2,07 |
3 |
61,56 |
30.56 |
2,97 |
4,91 |
2,01 |
4 |
62,45 |
29,71 |
2,8 |
5,04 |
2,12 |
5 |
63,05 |
29,25 |
2,63 |
5,07 |
2,15 |
6 |
63,21 |
29,07 |
2,56 |
5,16 |
2,17 |
7 |
60,34 |
31,25 |
2,49 |
5,92 |
1,93 |
Состав получаемого синтез-газа, как по соотношению Н2 : СО, так и по содержанию СО2 и СН4 приемлем дляа использования в процессах аGTL без дополнительной корректировки состава.
Сравнение экспериментально полученных данных с термодинамически рассчитанными показывает, что соотношение Н2 : СО в получаемом синтез-газе на 4 - 5% ниже, чем теоретически рассчитанное. Такое отклонение можно объяснить погрешностями в определении состава газа, а также погрешностями измерения температуры в зоне реакции.
Содержание СО2 и СН4 в газе превышает теоретически рассчитанное. При этом общее содержание этих компонентов остается незначительным (от 7,7 до 8,4%), и не может существенно повлиять на возможность использования получаемого синтез-газа для лабораторных и опытно-промышленных установок синтеза жидких углеводородов.
Были проведены эксперименты при температуре конверсии 800оС, 850 оС и 900 оС в режиме паровой конверсии, результаты которых, включающие материальный баланс, представлены в табл.6. Соотношение СН4 : Н2О в исходной газовой смеси составляло 1 : 1,1. Материальный баланс составлялся по показателям замеров в течение 1 часа. Расход газа измерялся с помощью газовых часов Ritter TG 3. аМатериальный баланс во всех экспериментах удовлетворительный. Содержание СН4 в получаемой газовой смеси не превышает 4%. Соотношение Н2 : СО находится в диапазоне 3,5 - 3,7.
Таблица 6 - Материальный баланс паровой конверсии метанаа
(СН4 : Н2Оа = 1 : 1,1)
Компонент |
Т = 800оС |
Т = 850оС |
Т = 900оС |
|||||||||
m,г |
% |
mC,г |
% |
m,г |
% |
mC,г |
% |
m,г |
% |
mC,г |
% |
|
Вход |
|
|
|
|||||||||
СН4 |
49,70 |
44,69 |
37,27 |
100 |
49,29 |
44,69 |
36,69 |
100 |
49,29 |
46,69 |
36,96 |
100 |
Н2О |
61,51 |
55,31 |
- |
0 |
61,00 |
53,31 |
- |
0 |
61,00 |
53,31 |
- |
0 |
ИТОГО: |
111,20 |
100 |
37,27 |
100 |
110,29 |
100 |
36,69 |
100 |
110,29 |
100 |
36,96 |
100 |
Выход |
|
|
|
|||||||||
СН4 |
1,86 |
1,67 |
1,40 |
3,76 |
0,27 |
0,24 |
0,20 |
0,55 |
1,75 |
1,59 |
1,31 |
3,57 |
Н2 |
19,24 |
17,30 |
- |
0 |
18,36 |
16,65 |
- |
0 |
18,60 |
18,86 |
- |
0 |
СО |
78,08 |
70,22 |
33,46 |
89,78 |
70,49 |
63,91 |
30,21 |
82,34 |
81,82 |
74,19 |
35,07 |
95,58 |
СО2 |
5,40 |
4,86 |
1,47 |
3,94 |
15,29 |
13,86 |
4,17 |
11,35 |
0 |
0 |
0 |
0 |
Н2О |
4,00 |
3,60 |
- |
0 |
2,20 |
19,95 |
- |
0 |
5,00 |
4,53 |
- |
0 |
ИТОГО: |
108,58 |
97,65 |
36,33 |
94,48 |
106,62 |
96,67 |
34,58 |
94,25 |
107,18 |
97,18 |
36,38 |
99,16 |
С+ потери |
2,62 |
2,35 |
0,94 |
2,52 |
3,67 |
3,33 |
2,11 |
5,75 |
3,11 |
2,82 |
0,31 |
0,84 |
Всего: |
111,2 |
100 |
37,27 |
100 |
110,29 |
100 |
36,69 |
100 |
110,29 |
100 |
36,96 |
100 |
В табл. 7 представленыаосновные характеристики паровой конверсии метана при соотношении компонентов в исходной газовой смеси
СН4 : Н2О = 1 : 1,1.
Таблица 7 - Основные характеристики паровой конверсии метанаа
(СН4 : Н2О = 1 : 1,1).аа
Температура, С |
Конверсия, СН4 а% |
Выход Н2, % |
Выход СО, % |
Селективность по Н2, % |
Селективность по СО, % |
Н2:СО |
800 |
96,3 |
96,2 |
89,8 |
99,9 |
93,3 |
3,5 |
850 |
99,5 |
99,1 |
81,7 |
99,6 |
100,0 |
3,7 |
900 |
99,9 |
99,9 |
99,9 |
99,9 |
100,0 |
3,5 |
Как видно из табл. 6 и 7, основные характеристики паровой конверсии метана в диапазоне температуры 800 - 900 оС изменяются незначительно.
Были проведены эксперименты при температуре конверсии 800оС, 850 оС и 900 оС в режиме пароуглекислотной конверсии метана, результаты которых, включающие материальный баланс, представлены в Табл.8 и 9. Соотношение СН4 : Н2О : СО2а в исходной газовой смесиа асоставляло 1 : 0,73 : 0,33аи 1 : 0,73 : 0,17 . ааМатериальный баланс составлялся по показателям замеров в течении 1 часа. Материальный баланс во всех экспериментах удовлетворительный.
Таблица 8 - Материальный баланс пароуглекислотнойа конверсии метана
(СН4 : Н2О : СО2а = 1 : 0,73 : 0,33)
Компо-нент |
Т = 800оС |
Т = 850оС |
Т = 900оС |
|||||||||
m,г |
% |
mC,г |
% |
m,г |
% |
mC,г |
% |
m,г |
% |
mC,г |
% |
|
Вход |
|
|
|
|||||||||
СН4 |
49,29 |
34,12 |
36,96 |
74,98 |
49,29а |
34,12 |
36,69 |
74,98 |
50,93 |
34,12 |
38,20 |
75,00 |
Н2О |
а50,00 |
34,61 |
а- |
а0 |
50,00 |
34,61 |
а- |
а0 |
а51,67 |
34,61 |
- |
а0 |
СО2 |
45,18 |
31,27 |
12,33 |
25,01 |
45,18 |
31,27 |
12,32 |
25,01 |
46,68 |
31,27 |
12,73 |
25,00 |
ИТОГО: |
144,46 |
100 |
49,29 |
100 |
144,46 |
100 |
49,29 |
100 |
149,28 |
100 |
50,93 |
100 |
Выход |
|
|
|
|||||||||
СН4 |
1,03 |
0,71 |
0,77 |
1,56 |
0,54 |
0,37 |
0,41 |
а0,83 |
0,50 |
0,33 |
0,37 |
0,73 |
Н2 |
а14,81 |
10,25 |
а- |
а0 |
а17,08 |
11,82 |
а- |
а0 |
а17,61 |
11,80 |
а- |
а0 |
СО |
а88,62 |
61,35 |
37,98 |
77,05 |
101,02 |
69,93 |
43,29 |
87,83 |
102,13 |
68,42 |
43,77 |
85,94 |
СО2 |
а10,97 |
а7,59 |
а2,99 |
а6,07 |
а15,32 |
10,61 |
а4,18 |
а8,48 |
а20,88 |
13,99 |
а5,70 |
11,19 |
Н2О |
а15,20 |
10,52 |
а- |
а0 |
а4,20 |
а2,91 |
а- |
а0 |
а4,50 |
а3,01 |
а- |
а0 |
ИТОГО: |
130,63 |
90,42 |
41,74 |
84,68 |
138,16 |
95,64 |
47,88 |
97,14 |
145,62 |
97,55 |
49,84 |
97,86 |
С+ потери |
а13,48 |
а9,33 |
7,55 |
а15,3 |
а6,3 |
4,36 |
а1,41 |
2,86 |
а3,66 |
а2,45 |
а1,09 |
а2,14 |
Всего: |
144,46 |
100 |
49,29 |
100 |
144,46 |
100 |
49,29 |
100 |
149,28 |
100 |
50,93 |
100 |
аа
Таблица 9 - Материальный баланс аапароуглекислотнойа конверсии метана
(СН4 : Н2О : СО2а = 1 : 0,73 : 0,17)
Компонент |
Т = 800оС |
Т = 850оС |
Т = 900оС |
||||||||||||
м,г |
% |
мC,г |
% |
м,г |
% |
м C,г |
% |
м,г |
% |
мC,г |
% |
||||
Вход |
|
|
|
||||||||||||
СН4 |
73,93 |
40,44 |
55,45 |
85,72 |
103,91 |
40,44 |
77,93 |
85,71 |
78,04 |
40,44 |
58,53 |
85,72 |
|||
Н2О |
а75,00 |
41,03 |
а- |
а0 |
105,42 |
41,02 |
а- |
а0 |
а79,17 |
41,02 |
- |
а0 |
|||
СО2 |
а33,88 |
18,53 |
а9,24 |
14,28 |
а47,63 |
18,54 |
12,99 |
14,29 |
а35,77 |
18,54 |
а9,75 |
14,28 |
|||
ИТОГО: |
182,81 |
100 |
64,69 |
100 |
256,95 |
100 |
90,92 |
100 |
192,97 |
100 |
68,28 |
100 |
|||
Выход |
|
|
|
||||||||||||
СН4 |
а3,94 |
2,16 |
а2,95 |
4,56 |
а5,34 |
2,08 |
а4,01 |
а4,41 |
а2,16 |
1,12 |
1,62 |
а2,37 |
|||
Н2 |
а24,61 |
13,46 |
а- |
а0 |
а36,36 |
14,15 |
а- |
а0 |
а27,29 |
14,14 |
а- |
а0 |
|||
СО |
132,51 |
72,49 |
56,79 |
87,79 |
192,67 |
74,98 |
82,57 |
90,82 |
141,36 |
73,25 |
60,58 |
88,72 |
|||
СО2 |
а10,70 |
а5,85 |
а2,75 |
а4,25 |
а12,43 |
а4,84 |
а3,39 |
а3,73 |
а19,50 |
10,11 |
5,32 |
а7,79 |
|||
Н2О |
а4,20 |
а2,30 |
а- |
а0 |
а5,20 |
а2,02 |
а- |
а0 |
а0 |
а0 |
а- |
а0 |
|||
ИТОГО: |
175,33 |
95,91 |
62,49 |
96,60 |
251,32 |
97,81 |
89,97 |
98,95 |
190,30 |
98,62 |
67,52 |
98,89 |
|||
С+ потери |
а7,48 |
а4,09 |
а2,20 |
3,4 |
а5,63 |
а2,19 |
а0,96 |
а1,05 |
а2,67 |
а1,38 |
0,76 |
а1,11 |
|||
Всего: |
182,81 |
100 |
64,69 |
100 |
256,95 |
100 |
90,92 |
100 |
192,97 |
100 |
68,28 |
100 |
В Табл. 10 и 11 представленыа основные характеристики пароуглекислотной конверсии метана.
Таблица 10 - Основные характеристики пароуглекислотной конверсии метанаа а
(СН4 : Н2О : СО2 = 1 : 0,73 : 0,33).
Температура, С |
Конверсия, СН4 , а% |
Выход Н2, % |
Выход СО, % |
Селективность по Н2, % |
Селективность по СО, % |
Н2 :СО |
800 |
97,9 |
82,9 |
77,1 |
84,6 |
78,7 |
2,3 |
850 |
98,9 |
95,5 |
87,8 |
96,6 |
88,8 |
2,4 |
900 |
99,0 |
95,3 |
85,9 |
96,3 |
86,8 |
2,4 |
аа
Как видно из табл. 10 что ас увеличением температуры конверсии с 800 до 850оС аселективность по Н2 и СО возрастает более чем на 10%, а при увеличении температуры ас 850 до 900оС остается практически неизменной. Выход Н2 и СО возрастает с повышением температуры аот 800 до 850оС и остается практически постоянным при повышении температуры от 850 до 900оС. Показатели конверсии СН4 ав диапазоне температуры от 800 до 900оС
остаются практически неизменными.
Таблица 11 - Основные характеристики пароуглекислотной конверсии метана
(СН4 : Н2О : СО2 = 1 : 0,73 : 0,17).
Температура, С |
Конверсия, СН4 , а% |
Выход Н2, % |
Выход СО, % |
Селективность по Н2, % |
Селективность по СО, % |
Н2 :СО |
800 |
94,7 |
91,8 |
87,8 |
96,9 |
92,7 |
2,6 |
850 |
94,9 |
94,7 |
90,8 |
99,8 |
95,7 |
2,6 |
900 |
97,2 |
96,4 |
88,7 |
99,1 |
91,2 |
2,7 |
Из табл. 11 и 10а видно, что с уменьшением содержания СО2 в исходной газовой смеси показатели процесса становятся менее зависимыми от температуры конверсии, при этом значение соотношения Н2 :СО возрастает.
Последним этапом экспериментов было проведение ресурсных испытаний с целью выяснения возможности работы сконструированной установки пароуглекислотной конверсии метана в непрерывном режиме. Испытания проходили в течение 300 часов в непрерывном режиме работы. аЗамеры производились дважды в сутки. Результаты ресурсных испытаний представлены в табл. 12 и 13. Испытания показали стабильность работы установки пароуглекислотной конверсии метана в течение 300 часов.
Таблица 12.
Основные характеристики пароуглекислотной конверсия метана
(СН4 : Н2О : СО2 = 1,00 : 1,00 : 0,4), Т = 900 оС.
№ |
Состав синтез-газа апосле реактора конверсии, |
Показатели процесса, % мольные |
||||||||||||
об % |
моль |
Н2:СО |
К (CH4) |
В (H2) |
В (CO) |
C (H2) |
C (CO) |
|||||||
H2 |
CO |
CO2 |
CH4 |
H2 |
CO |
CO2 |
CH4 |
|||||||
1 |
60,6 |
28,3 |
2,3 |
5,8 |
2,14 |
1,00 |
0,1 |
0,20 |
2,1:1 |
82,4 |
60,0 |
73,5 |
72,3 |
89,2 |
2 |
61,4 |
28,1 |
5,5 |
4,9 |
2,18 |
1,00 |
0,20 |
0,17 |
2,2:1 |
85,9 |
60,8 |
73,2 |
71,4 |
86,0 |
3 |
60,9 |
28,2 |
6,1 |
4,8 |
2,16 |
1,00 |
0,22 |
0,17 |
2,2:1 |
85,4 |
60,3 |
73,2 |
70,6 |
85,7 |
4 |
60,2 |
26,9 |
8,0 |
4,9 |
2,24 |
1,00 |
0,30 |
0,18 |
2,2:1 |
85,1 |
59,6 |
69,8 |
70,0 |
82,1 |
Эксперимент был продолжен с измененным составом исходной смеси. (табл.13)
Таблица 13 - Основные характеристики пароуглекислотной конверсии метана
(СН4 : Н2О : СО2 = 1,00 : 1,06 : 0,3), Т = 900 оС.
№ |
Состав синтез-газа после реактора конверсии |
Показатели процесса, % |
||||||||||||
об % |
моль |
Н2:СО |
К (CH) |
В (H2) |
В (CO) |
C (H2) |
C (CO) |
|||||||
H2 |
CO |
CO2 |
CH4 |
H2 |
CO |
CO2 |
CH4 |
|||||||
1 |
63,7 |
25,4 |
5,3 |
5,6 |
2,51 |
1,00 |
0,21 |
0,22 |
2,5:1 |
79,7 |
75,1 |
78,5 |
94,2 |
98,5 |
2 |
63,8 |
25,7 |
5,5 |
5,0 |
2,48 |
1,00 |
0,21 |
0,21 |
2,5:1 |
80,8 |
75,2 |
78,8 |
93,0 |
97,5 |
3 |
63,9 |
25,4 |
5,5 |
5,2 |
2,50 |
1,00 |
0,22 |
0,20 |
2,5:1 |
81,2 |
75,2 |
78,8 |
92,6 |
97,1 |
4 |
64,1 |
25,8 |
5,0 |
5,1 |
2,48 |
1,00 |
0,19 |
0,20 |
2,5:1 |
81,5 |
75,5 |
79,7 |
92,6 |
97,8 |
5 |
64,0 |
25,5 |
5,5 |
5,0 |
2,51 |
1,00 |
0,22 |
0,20 |
2,5:1 |
81,9 |
75,4 |
78,8 |
92,1 |
96,2 |
6 |
63,6 |
25,2 |
6,0 |
5,2 |
2,52 |
1,00 |
0,24 |
0,21 |
2,5:1 |
81,2 |
74,9 |
77,9 |
92,3 |
96,0 |
7 |
64,2 |
25,0 |
5,3 |
5,5 |
2,55 |
1,00 |
0,21 |
0,22 |
2,6:1 |
80,1 |
75,5 |
77,6 |
94,3 |
96,9 |
8 |
63,7 |
25,2 |
5,5 |
5,6 |
2,53 |
1,00 |
0,22 |
0,22 |
2,5:1 |
79,7 |
75,1 |
77,9 |
94,2 |
97,7 |
9 |
64,1 |
25,5 |
4,6 |
5,8 |
2,51 |
1,00 |
0,18 |
0,23 |
2,5:1 |
79,0 |
75,5 |
78,8 |
95,6 |
99,8 |
10 |
63,9 |
25,5 |
4,7 |
5,9 |
2,51 |
1,00 |
0,18 |
0,23 |
2,5:1 |
78,6 |
75,3 |
78,8 |
95,8 |
99,9 |
11 |
64,0 |
25,3 |
5,4 |
5,3 |
2,53 |
1,00 |
0,21 |
0,21 |
2,5:1 |
80,8 |
75,4 |
78,2 |
93,3 |
96,8 |
12 |
64,1 |
26,0 |
4,5 |
5,4 |
2,47 |
1,00 |
0,17 |
0,21 |
2,5:1 |
80,4 |
75,5 |
80,3 |
93,9 |
99,9 |
13 |
64,2 |
26,5 |
4,1 |
5,2 |
2,42 |
1,00 |
0,15 |
0,20 |
2,4:1 |
81,2 |
75,6 |
81,9 |
93,2 |
99,9 |
14 |
63,9 |
25,7 |
4,9 |
5,5 |
2,49 |
1,00 |
0,19 |
0,21 |
2,5:1 |
80,1 |
75,3 |
79,4 |
94,0 |
99,2 |
15 |
64,2 |
25,9 |
4,5 |
5,4 |
2,48 |
1,00 |
0,17 |
0,21 |
2,5:1 |
80,4 |
75,6 |
80,0 |
94,0 |
99,5 |
16 |
63,9 |
25,1 |
5,7 |
5,3 |
2,55 |
1,00 |
0,23 |
0,21 |
2,6:1 |
80,8 |
75,3 |
77,6 |
93,2 |
96,0 |
17 |
63,8 |
25,0 |
5,6 |
5,7 |
2,55 |
1,00 |
0,21 |
0,22 |
2,5:1 |
80,1 |
75,5 |
77,9 |
94,3 |
97,3 |
18 |
64,0 |
25,3 |
5,1 |
5,6 |
2,53 |
1,00 |
0,20 |
0,22 |
2,5:1 |
79,7 |
75,4 |
78,2 |
94,6 |
98,1 |
Из данных, приведенных ва таблицах а12 и 13 видно, что в течение 300 часов ресурсных испытаний установки основные показатели процесса оставались практически без изменений. Отклонения показателей незначительны.
Выводы
- Разработана технологическая схема установки для паровой и пароуглекислотной конверсии метана в синтез-газ на основании принципиально новой конструкции реактора со встроенным в него прямоточным парогенератором.
- Установлено, что разработанный метода позволяет:
- получать синтез-газ с диапазоном мольных соотношения Н2 : СОа от 1,6 до 4,6 при температуре конверсии 800 - 900оС и давлении 5 атм;
- достигать производительность по синтез-газуа от 200 - 400 л/час, а при масштабировании до 100 000 л/час;
- получать синтез-газ с суммарным содержанием СО2 и СН4 менее 8,5%, что позволяет использовать синтез-газ в процессах GTL без дополнительной корректировки его состава;
- астабильно работать как в режиме stop and go, так и в непрерывном режиме в течение 300 часов.аа
- Показано, что разработанный метод конверсии метана позволяет получить синтез-газ с мольным соотношением Н2 : СОа (2 - 2.2), необходимом для процессов синтеза жидких углеводородов.
- Исследовано влияние состава исходной смеси и температурного режима на состав получаемого синтез-газа.
а
а
Основные положения диссертации опубликованы:
- Геращенко И.О., Лапидус А.Л. Лабораторный реактор пароуглекислотной конверсии природногогаза. // Газохимия. № 4-5 (14-15) октябрь - ноябрь 2010 года.
- Геращенко И.О., Лапидус А.Л. О влиянии промышленных выбросов углекислого газа на климатические изменения.// Вестник Самарского государственного технического университета. № 1, а2011 года.
- Геращенко И.О., Лапидус А.Л. аРасчет процесса теплоотдачи при синтезе Фишера-Тропша. // Технологии нефти и газа. № а5 октябрь 2011 года.
- Геращенко И.О. Результаты разработки отечественной технологии глубокой переработки природного или попутного газа в синтетические жидкие углеводороды (СЖУ) // Тезисы докладов.// Второй международный газохимический форум IGCF'10.а Ханты-Мансийск,а 12 марта, сессия 1, 2010 года г.;
- И.О.Геращенко. а//а Лабораторный реактор пароуглекислотной конверсии природного газа// Тезисы докладов.а Научный семинар по газохимии аав Российскома Государственном Университете нефти и газа им. И.М. Губкина,а 11 июня 2010г.
- И.О.Геращенко. // Реактор паровой и пароуглекислотной конверсии легких углеводородов для получения газа, содержащего водород и окись углерода (синтез-газа)//. Патент на изобретение.а Заявка № 2010134600/05(049120). Решение о выдаче патента на изобретение 06.12.2011г.
а
